Table of Contents
-
ПРОЕКТИPАНЕ, ИЗРАБОТКА И ЕКСПЛОАТАЦИЯ НА ИНСТРУМЕНТАЛНА ЕКИПИРОВКА ЗА ПРЕСОВА ОБРАБОТКА НА ЛИСТОВ МАТЕРИАЛ
- Д-р инж. Петър Димитров Димитров
- РЕЗЮМЕ
- ВЪВЕДЕНИЕ
- ГЛАВА 1. ОСНОВНИ ФАЗИ В СЪЗДАВАНЕТО, ЕКСПЛОАТАЦИЯТА И ЗАМЯНАТА НА МАШИНИТЕ, СЪОРЪЖЕНИЯТА И ИНСТРУМЕНТИТЕ (ПЕРИОД НА ЖИЗНЕНИЯ ЦИКЪЛ НА ИЗДЕЛИЕТО)
- ГЛАВА 2. ОСНОВНИ ТЕХНОЛОГИЧНИ ПРОЦЕСИ И ОПЕРАЦИИ ПРИ ОБРАБОТКА НА ЛИСТОВ МАТЕРИАЛ
- ГЛАВА 3. ТЕХНОЛОГИЧНИ ИЗИСКВАНИЯ КЪМ ДЕТАЙЛИТЕ ОТ ЛИСТОВ МАТЕРИАЛ, ПОЛУЧАВАНИ ЧРЕЗ ПРЕСОВА ОБРАБОТКА
- ГЛАВА 4. ИДЕЕН ПРОЕКТ НА ИНСТРУМЕНТИ ЗА ЩАНЦОВАНЕ - ИЗБОР И ОЦЕНКА НА ИКОНОМИЧЕСКИ ИЗГОДЕН ВАРИАНТ
- ГЛАВА 5. РАБОТЕН (ТЕХНИЧЕСКИ) ПРОЕКТ - ПРОЕКТИРАНЕ НА ТЕХНОЛОГИЧНИ ПРОЦЕСИ И СХЕМИ НА РАБОТА, ТЕХНОЛОГИЧНО - СИЛОВО - ЯКОСТНО ИЗЧИСЛЯВАНЕ, КОНСТРУИРАНЕ И ИЗЧЕРТАВАНЕ НА СБОРНИ И ДЕТАЙЛНИ ЧЕРТЕЖИ НА ИНСТРУМЕНТИ ЗА ЩАНЦОВАНЕ, ТЕХНОЛОГИЧНО ОСИГУРЯВАНЕ НА ИЗРАБОТКАТА ИМ
- ГЛАВА 6. КОНСТРУКЦИИ НА ИНСТРУМЕНТИТЕ ЗА ОБРАБОТКА НА ЛИСТОВ МАТЕРИАЛ (ЩАНЦИ, ЩАМПИ ЗА ЛИСТОВО ЩАМПОВАНЕ)
- ГЛАВА 7. АКТИВНИ (РАБОТНИ) ЧАСТИ НА ЩАНЦИТЕ
- ГЛАВА 8. ТЕХНОЛОГИЧНО НЕОБХОДИМИ (НОСЕЩИ, ВОДЕЩИ, ПОЗИЦИОНИРАЩИ) И СПОМАГАТЕЛНИ ЧАСТИ НА ЩАНЦИТЕ
- ГЛАВА 9. ИЗБОР НА ПРЕСОВО ОБОРУДВАНЕ
- ГЛАВА 10. МЕТОДИ И ТЕХНОЛОГИЧНИ ПРОЦЕСИ, ИЗПОЛЗВАНИ ПРИ ИЗРАБОТКАТА НА ИНСТРУМЕНТИ ЗА ЛИСТОВ МАТЕРИАЛ (ЩАНЦИ)
- ГЛАВА 11. ТИПОВИ ТЕХНОЛОГИЧНИ МАРШРУТИ ЗА ИЗРАБОТКА НА АКТИВНИТЕ, НА ТЕХНОЛОГИЧНО НЕОБХОДИМИТЕ И СПОМАГАТЕЛНИ ЧАСТИ НА ИНСТРУМЕНТИ ЗА ПРЕСОВАНЕ НА ЛИСТОВ МАТЕРИАЛ (ЩАНЦИ)
- ГЛАВА 12. ОРГАНИЗАЦИЯ НА ИНСТРУМЕНТАЛНОТО ПРОИЗВОДСТВО, ИЗРАБОТКАТА, МОНТАЖА И КОНТРОЛА НА ИНСТРУМЕНТАЛНАТА ЕКИПИРОВКА ЗА ПРЕСОВА ОБРАБОТКА НА ЛИСТОВ МАТЕРИАЛ
- ГЛАВА 13. НАСТРОЙКА И ПРОБА (ТЕСТ) НА НОВИ ИНСТРУМЕНТИ ЗА ЩАНЦОВАНЕ – ОЦЕНКА НА КОНСТРУКЦИЯТА, КАЧЕСТВОТО НА ТЯХНАТА ИЗРАБОТКА И ТОЧНОСТТА НА ПРОИЗВЕДЕНОТО ИЗДЕЛИЕ
- ГЛАВА 14 . БЕЗОПАСНА ЕКСПЛОАТАЦИЯ, ПОДДРЪЖКА И РЕМОНТ НА ИНСТРУМЕНТАЛНАТА ЕКИПИРОВКА ЗА ЩАНЦОВАНЕ
- ПРИЛОЖЕНИЕ 1. СПИСЪК НА ПРОЕКТИРАНИ И ВНЕДРЕНИ ИНСТРУМЕНТАЛНИ ЕКИПИРОВКИ ЗА ЩАНЦОВАНЕ, СРЕД КОИТО СА ИЗБРАНИ ИЗПОЛЗВАНИТЕ ПРИМЕРИ
- ИЗПОЛЗВАНА ЛИТЕРАТУРА:
ПРОЕКТИPАНЕ, ИЗРАБОТКА И ЕКСПЛОАТАЦИЯ НА ИНСТРУМЕНТАЛНА ЕКИПИРОВКА ЗА ПРЕСОВА ОБРАБОТКА НА ЛИСТОВ МАТЕРИАЛ
Д-р инж. Петър Димитров Димитров
РЕЗЮМЕ
Разгледани са основните инженерни задачи, решавани при производството на детайли от листов метал, видовете технологични процеси за пресова обработка на листови материали, типови конструкции на инструменти и пресово оборудване, методите за проектиране и оценка, използувани процеси за изработка на инструменталната екипировка за щанцоване, особености на нейната експлоатация и поддръжка. Използваните примери са на инструменти, реално внедрени в производството от автора.
Предназначена е за специалисти в областта на студената пластична обработка на металите - инженери, конструктори, технолози, студенти, майстори в инструментални цехове.
ВЪВЕДЕНИЕ
С навлизането на пластмаси и нови композиционни материали в конструкциите, традиционните части, изработени от листов метал постепенно намалявят своя дял в производството на нови изделия. Все пак, остават много области, където метални конструкции от листов материал са незаменими. Най-икономичния начин за тяхното масово производство е студеното листово щамповане или щанцоване. Независимо от разликата в терминологията, двете наименования означават идентични процеси на обработка. Инструментите използвани в процеса на пресова обработка на листов материал се наричат щампи за листово щамповане или щанци (за разлика от термина щампи, който обичайно се използва за инструменти при обемна пресова обработка на металите). И двата термина са използвани в настоящата публикация.
Наличната техническа литература за щампи за листов материал или щанци, на български език е оскъдна - едва няколко заглавия за последните 30 години. При това, тя е насочена към отделни аспекти, предимно към технологичните процесите за щанцоване, отчасти към проектирането на самите инструменти или тяхната изработка. С навлизането на компютърните системи, инструменталното производство коренно промени своя облик и старите технологии се замениха с CAD-CAM производство (проектиране и производство с помоща на компютърни системи).
Все повече се използва термина “управление на жизнения цикъл на изделието”, планиращ всички етапи на съществане на даден продукт - от неговото замисляне, през производството до излизането му от употреба и замяната с нов.
В настоящата публикация е възприет комплексен подход на разглеждане на всички основни етапи от жизнения цикъл на инструменталната екипировка за пресова обработка на листов материал в тяхното единство. Това означава, че при проектирането се отчита влиянието на всяко едно решение върху изработката и експлоатацията на инструментите. Голямо внимание е отделено на връзката “технологичен процес за щанцоване - конструкция на инструмент - изработка - експлоатация и поддръжка” със серийността на щанцования детайл и икономически обосновано решение, на база себестойност на детайла, цена на инструмента и прогнозен срок за изработка. Разгледаните примери са на внедрени в производството процеси и инструменти за щанцоване, избрани от списъка в приложение 1. За техния избор основни критерии са били наличието на характерни особеностти, на оригинални нестандартни решения и на подходящи информационни носители в електронен вид (за част от инструментите са налични само копия на хартия). Рагледаните проблеми, предлаганите решения и отправените препоръки са на базата на реалния опит от проектиране, изработка и внедряване в производството на над 400 инструмента. Предложените методи и модели за икономическа оценка на инструменталната екипировка за щанцоване са разработени и изпробвани от автора в практиката, където са доказали своята пригодност. Естествено, посочените данни се отнасят за конкретни условия на инструментално производство и за други условия трябва да се проверят - може да са необходими някои корекции.
Публикуваните материали са с практическа и информационна насоченост и нямат за цел да заместят справочната литература за процесите на студено пресова обработка на металите чрез пластична деформация. Книгата е структорирана в 14 глави, разглеждащи различни етапи (или части от тях) от жизнения цикъл на инструментите за щанцоване. Текста е илюстриран с над 300 схеми, таблици, диаграми, чертежи и снимки.
ГЛАВА 1. ОСНОВНИ ФАЗИ В СЪЗДАВАНЕТО, ЕКСПЛОАТАЦИЯТА И ЗАМЯНАТА НА МАШИНИТЕ, СЪОРЪЖЕНИЯТА И ИНСТРУМЕНТИТЕ (ПЕРИОД НА ЖИЗНЕНИЯ ЦИКЪЛ НА ИЗДЕЛИЕТО)
Всичко материално в заобикалящия свят, създадено от човечеството, преминава през фази на създаване, съществуване и замяна с ново, по-съвършено. Тези три основни фази са наречени жизнен цикъл. На него човечеството дължи постигнатия технически напредък.
Основните фази, през които преминават машините, са показани на Фиг.1-1.
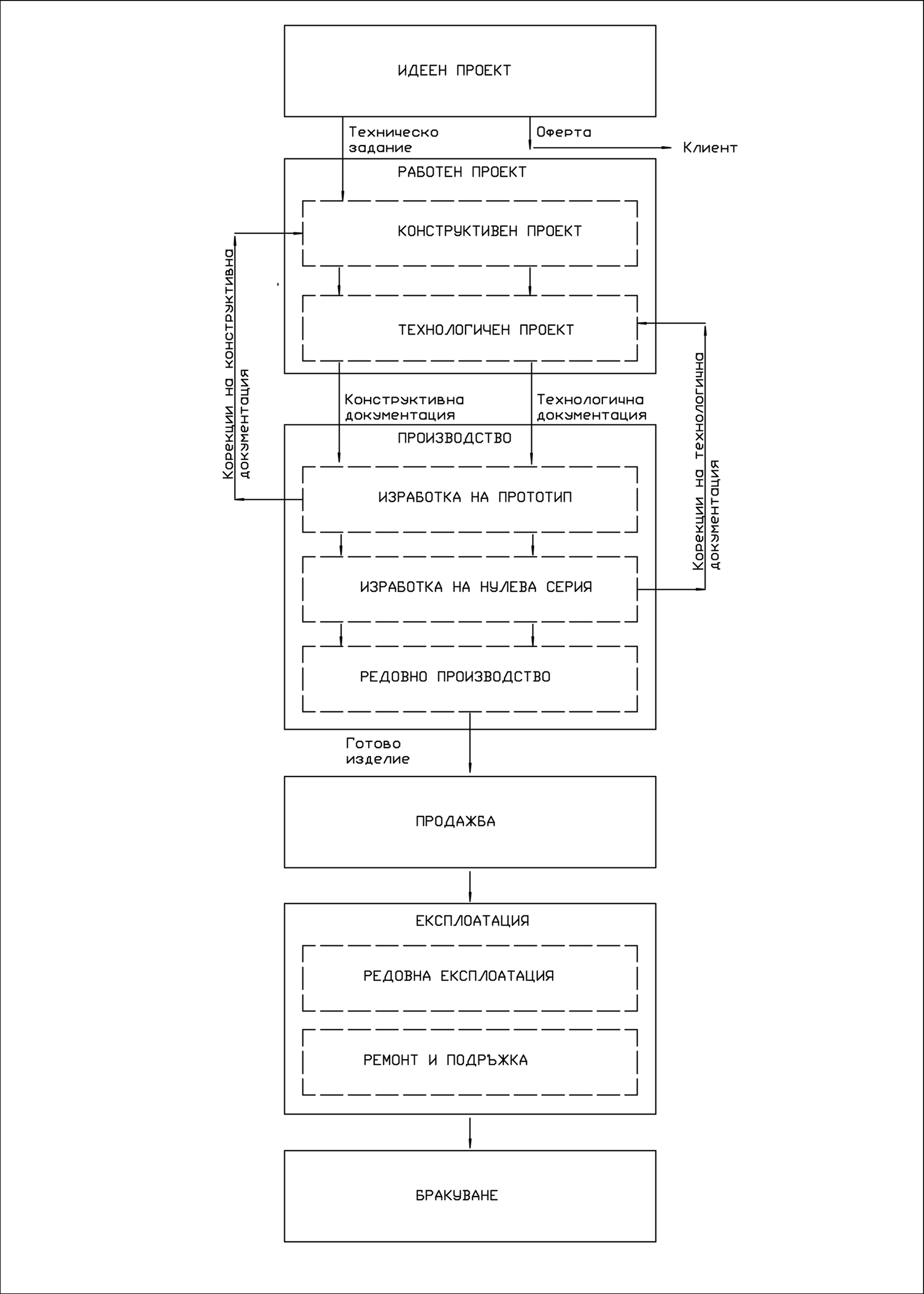
Фиг.1-1
1. Разработка на ИДЕЕН ПРОЕКТ.
1.1. Формулиране на целта на идейния проект (обекта) и уточняване на общите задачи – създаване нова конструкция на машина, възел, детал, инструмент, или конструкция на обекта, работещи на различен принцип на действие (патент).
1.2. Предварително проучване на нивото на съществуващите технически решения – техническа и научна литература, фирмени проспекти, отраслови и заводски нормали, съществуващи стандарти, патенти и полезни модели, интернет сайтове, симпозиуми, изложби, панаири, радио, телевизия, периодични издания и други достъпни източници.
1.3. Избор на аналог сред известните технически решения – базов модел (конструкция, схема), който ще се усъвършенства и с който ще се сравняват параметрите на обекта. Определяне на предимствата и недостатъците на базовия модел.
1.4. Извършване на предварителни технически изчисления – кинематични, якостни, деформационни, топлинни, к.п.д., електрически, технологични, икономически. Изчисленията трябва да докажат работоспособност и икономическа целесъобразност на новия обект.
1.5. Сравнение на възможнте варианти (конструкции, схеми) и избор на оптималния за обекта чрез анализ на предимствата и недостатъците – целта е увеличаване на предимствата и намаляване (избягване) на недостатъците в новия обект. Уточняване на техническите характеристики на обекта.
1.6. Изготвяне на кинематични, електрически, принципни, технологични, компановачни схеми, габаритни и монтажни сборни чертежи, спецификации на техническите параметри, производствени и икономически показатели.
1.7. Съставяне на техническо задание или оферта за обекта – всеки от посочените документи трябва да включва техническа и икономическа части, които да дефинират ясно обекта с неговите характеристики и да прогнозират неговата цена. Обикновено, техническото задание и офертата се одобряват от съответното ръководство или клиент преди началото на следващата фаза.
2. Разработка на РАБОТЕН ПРОЕКТ.
2.1. Уточняване на техническо задание – допълване на схемите, габаритни чертежи, спецификациите с технически параметри на обекта.
2.2. Конструктивни изчисления на обекта – пълни кинематични, якостни, деформациони и други необходими изчисления на съствните части. Изчисленията се оформят като обяснителна записка.
2.3. Създаване на 3D (обемни) модели на обекта. Тази фаза обикновено се изпълнява паралелно с изчисленията. В някои случаи дори ги предшества (на пример използване на метод на крайни елементи).
2.4. Разработка на сборни чертежи и спецификации на машини, сглобени единици (възли и групи детайли) – изясняване на съставните части, техния брой, взаимно разположение и връзки между тях, важни функционални и присъединителни размери, тегло, материали на оригиналните детайли, използвани стандартни или покупни части.
2.5. Разработка на детайлни (работни) чертежи на всички оригинални детайли – изясняване на геометрията, материала, качеството и точността на повърхнините, наличие на термична обработка или покрития, допустими отклонения на размерите, геометричната форма и взаимното разположение на повърхнините.
2.6. Подготовка на инструкции за експлоатация, за изпитване, за настройка или паспорт на продукта.
2.7. Съгласуване и одобрение на конструктивната документация.
2.8. Кореция на конструктивната документация – утвърждаване на различни изменения, наложени от технологични причини или произлезли от тестване на опитен образец. Обикновено, тази фаза се изпънява паралелно на авторския контрол по време на производството.
2.9. Избор на технологични процеси за изработка на обекта – в зависимост от големината на партидата и наличното оборудване.
2.10. Проектиране на технологичен маршрут за всеки оригинален детайл на обекта – създаване на последователност от технологични операции, описваща превъщането на изходната суровина (заготовка) в готов продукт. В тази фаза се попълват маршрутни технологични (работни) карти, определящи името на операцията, машината на която се извършва обработката, използваните работни (режещи, измервателни, монтажни, спомагателни) инструменти и приспособления, броя на едновремено обработваните заготовки, големината на серията за обработка, квалификацията на работника и времето за завършване на серията или за обработка на една заготовка.
2.11. Разработване на операционна технология за всеки оригинален детайл на обекта – създаване на последователност от технологични установки, работни преходи и похвати, извършващи се на една машина с един или няколко инструмента върху единична заготовка или група заготовки. В тази фаза се попълват операционни технологични (работни) карти, в които се описват преходи и установки, технологичните режими на работа, работните норми (време за обработка на една заготовка), прилагат се технологични схеми за установяване на детайлите върху машините, скици на получената заготовка и размерите, които трябва да се контролират.
2.12. Съставяне на технологични задания за проектиране на специални и контрони приспособления и инструменти – уточняват се изискванията, вида и основните технически данни на приспособления и инструменти, които трябва да се проектират и изработят за производството на даден обект.
2.13. Подготовка на управляващи програми за машини с ЦПУ.
2.14. Подготовка на заявки за доставка на изходни материали, стандартни и покупни детайли – уточняване на съответни спецификации и избор на доставчици.
2.15. Съгласуване и одобрение на технологичната документация.
2.16. Планиране на производството и формиране на себестойност на продукта – създаване на линейни мрежови графици за натоварването на производственото оборудване, на което ще се изпълнява обекта и подготовка на точна калкулация за себестойността на изделието.
2.17. Корекция на технологичната документация – утвърждаване на различни изменения на операции, режими и норми, наложени при изработката опитна (нулева) серия.
3. Стадии на ПРОИЗВОДСТВО.
3.1. Изработка на опитен образец (прототип) – обикновено се изработва модел на обекта, като се използват технологии за единично производство и ковенционални машини. Целта е да се провери работоспособността и техническите характеристики на обекта.
3.2. Изработка на нулева серия – проверка на годността на избраните технологични процеси, маршрут и технологични операции за производство на годен продукт, да се провери точността на заложените норми, които в последствие ще залегнат в определяне на себестойността на изделието.
3.3. Доставка на материали, покупни и стандартни части за производство.
3.4. Производство на заготовки за обекта – изработване на отливки, изковки, щамповани или заварени части, отрязани от валцуван прокат парчета.
3.5. Механичнна обработка на заготовките – обработка чрез стружко отнемане (струговане, фрезоване, пробиване, райбероване, дълбане, шлифоване, полиране, зъбообработване, нарязване на резби и други) на всички или на присъединителните повърхнини.
3.6. Други обработки на заготовките – физични (елетро-ерозийна или лазерна обработка), химични (цементация) процеси, пластична обработка (валцуване), термобработка (отгряване, закаляване, отвръщане, ТВЧ).
3.7. Довършителни обработки на детайлите – повърхностни покрития (хромиране, анодиране, титаново-нитритно покритие и др.), боядисване (обикновено или прахово), почистване (обезмасляване).
3.8. Монтаж на изделието – сглобяване на оригиналните и стандартни части (детайлите) във възли, сглобени единици, отделни машини и комплексни линии.
3.9. Качествен контрол и изпитване – проверка на съответствието между произведените части и конструктивната документация на всяка фаза от тяхната изработка. Тест на произведеното изделие съгласно методиката за изпитване, за да се сертифицира и поеме на гаранция за него.
3.10. Опаковане и складиране на готовия обект – комлектоване и подготовка на изделието за доставка на клиента.
4. ПРОДАЖБА на изделието.
4.1. Транспорт на обекта до търговеца или клиента.
4.2. Складиране при търговеца.
4.3. Продажба на клиента.
5. ЕКСПЛОАТАЦИЯ.
5.1. Пускане в редовна експлоатация – извършване на всички дейности по монтаж и настройка в условията на клиента (ако е необходимо). Първоначално изпитване чрез изрършване на 72 часова проба, която да потвърди работоспособността, правилната настройка, възможността за поемане на гаранция за обекта, обучение на персонал.
5.2. Редовна експлоатация на обекта – изпълнение на основните функции, за които е предназначен.
5.3. Ремонт и поддръка – извършване на текущи и планови ремонти съгласно инстукцията за експлоатация на обекта, доставка на резервни части и замяна на износени, изпълнение на аварийни ремонти.
6. Извеждане от експоатация – БРАКУВАНЕ
6.1. Извеждане на обекта от редовна експлоатация – извършва се когато е изтекъл предвидения от производителя ресурс, или ако честотата на аварийните ремонти и тяхната цена (физическо остаряване) е много висока и по-нататъчната експлоатация е финансово неизгодна. Възможно е също, обекта да се изведе от редовна експлоатация, защото неговите технически характеристики са много по-ниски от съществуващите на пазара (морално остаряване), което прави неговата по-нататъчната експлоатация финансово неизгодна.
6.2. Бракуване на обекта – може да се извършва частично или пълно бракуване. Най-често за това се съставя специален документ с описание на причините за бракуване.
Иструментите за обработка на листов материал (щанци) преминават през същите фази, както машините. Особеностите при тях са показани на Фиг.1-2.
Важен фактор е серийността на тяхното производство – единично производство на уникални изделия. Поради тази причина, някои от описаните етапи от идейния и работен проект може да са непълни или изобщо да липсват.
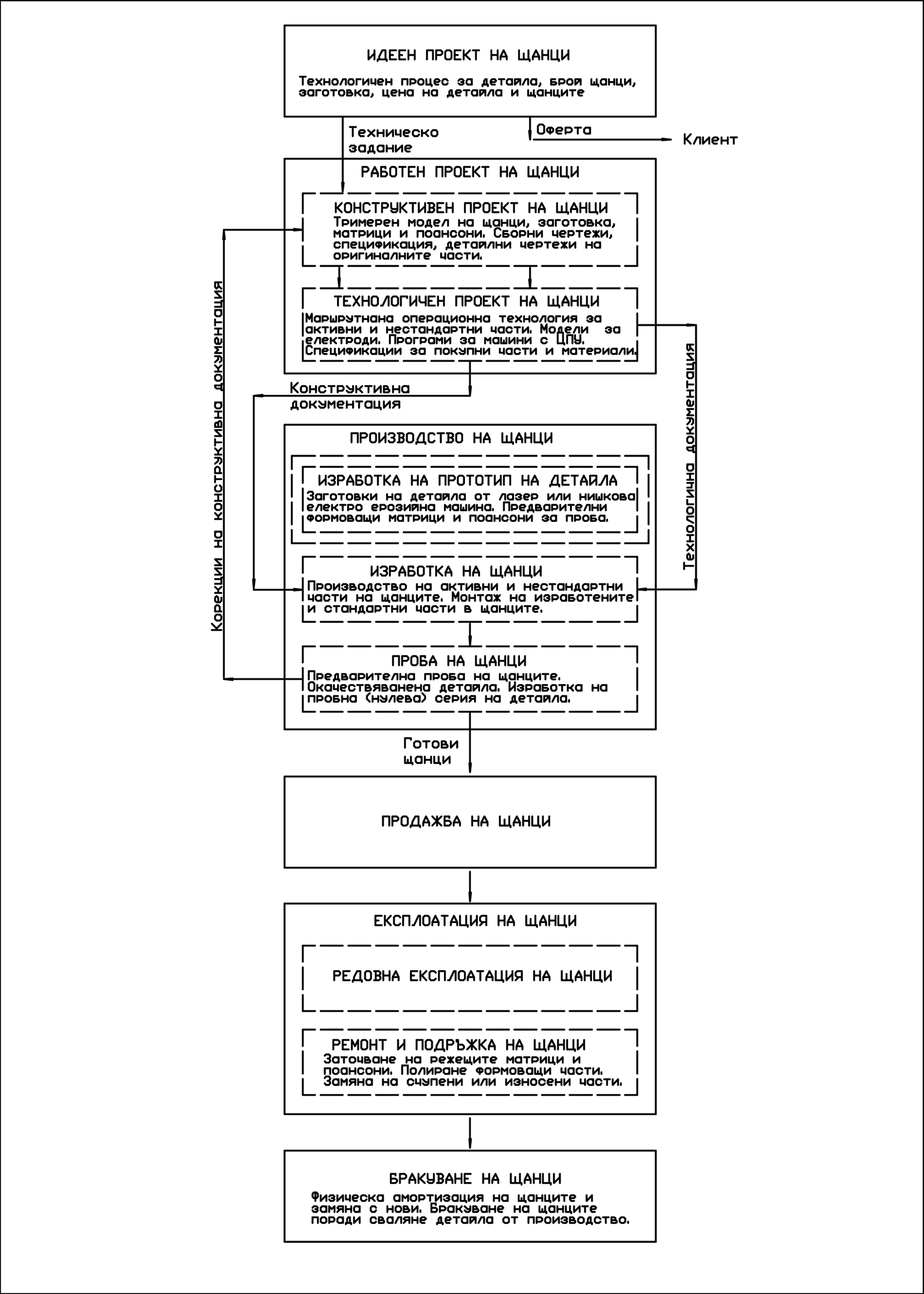
Фиг.1-2
ГЛАВА 2. ОСНОВНИ ТЕХНОЛОГИЧНИ ПРОЦЕСИ И ОПЕРАЦИИ ПРИ ОБРАБОТКА НА ЛИСТОВ МАТЕРИАЛ
В специализираната литература [1] е приведена класификация на различните видове технологични операции, прилагани при обработка на листов метал. На основата на характера и степента на деформацията, която претърпява заготовката по време на обработка, процесите условно могат да се разделят на две основни групи:
– Разделителни операции, при които деформацията последователно преминава през еластичен, пластичен и разрушаващ стадий;
– Формоизменящи операции, при които деформацията последователно преминава през еластичен и пластичен стадий без да се достига разрушение на материала.
По долу ще бъдат разгледани основни сведения само за някой от най-разпространените процеси. Няма да бъдат влючени монтажни операци, които също могат да се изпъляват с инструментална екипировка, но по своята същност най-често са формоизменящи или комбинация от разделителни и формоизменящи операции.
1. Разделителни операции.
1.1.Изрязване и пробиване – процес на разделяне на изходната заготовка по затворен контур на две части – детайл и отпадък. Когато външната част от заготовката с изрязания профил е отпадък, а материала от изрязания профил е детайла, процеса се нарича ИЗРЯЗВАНЕ. Обратно, когато външната част от заготовката с изрязания профил е детайла, а материала от изрязания профил е отпадък, процеса се нарича ПРОБИВАНЕ.
Използваните инструменти за осъществяване на процеса са поансон (обхващана от материала част) и матрица (обхващаща материала част). Заготовката се раполага между тях и при взаимно им движение се извършва разделянето на детайл и отпадък.
При ИЗРЯЗВАНЕ детайлът е тази част, която остава в отвора на матрицата и това определя основното правило, че РАЗМЕРИТЕ НА МАТРИЦАТА са определящи за точността.
При ПРОБИВАНЕ детайлът е тази част, която остава над матрицата и това определя основното правило, че РАЗМЕРИТЕ НА ПОАНСОНА са определящи за точността.
Последователността на процесите на изрязване и пробиване е показана на Фиг.2-1.
Първия стадий 1 е свързан с еластично деформиране на заготовката, което постепенно с по-нататъчното преместване на поансона спрямо матрицата, преминава в стадий 2 на пластично деформиране с ясно изразени зони на смачкване с широчина „b” на заготовката и видимо отпечатване в отвора на матрицата. По-нататък стадия продължава с все по-дълбоко потъване на поансона в заготовката и избутване на част от материала под него в матрицата. Изчерпването на възможността за пластична деформация на материала (достигане границата на якостта) води до стадий 3, при който над режещия ръб на матрицата се зараждат пукнатини в заготовката. При следващия стадий 4 тези пукнатините от страна на матрицата се разширяват и подобни се зараждат при режещите ръбове на поансона. Пукнатините могат да се срещнат при оптимална хлабина между матрицата и поансона (Z1) или да се разминат при недостатъчна хлабина (Z2), което определя и разликите в протичане стадия на разрушение 5 и формата на получения детайл – „а“ при оптимална и „б“ и недостатъчна хлабина.
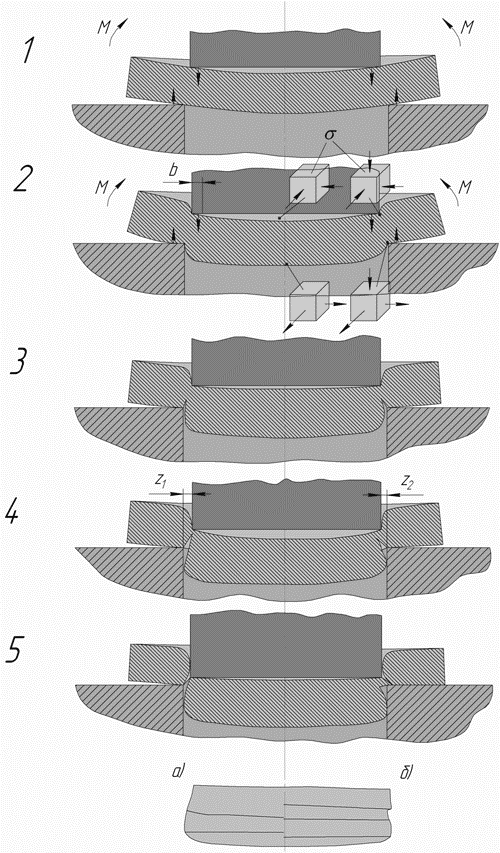
Фиг.2-1
Срязаната повърхност на детайла (или отпадъка) и в двата случая включва 3 основни части:
– закръгление, съответстващо на края на еластичните деформации и началото на пластичните;
– гладък (блестящ) пояс, отговарящ на увеличението на пластичните деформации (изтичане на заготовката под въздействие на поансона в матрицата) до изчерпване възможностите на материала;
– грапава повърхност, резултат на разрушението на материала.
При недостатъчна хлабина се получава вторично срязване на блестящия пояс и характерна форма „б“.
Процесите изрязване и пробиване са придружени с неравномерно разпределено натоварване на режещите ръбове на матрицата и поансона Фиг.2-2.
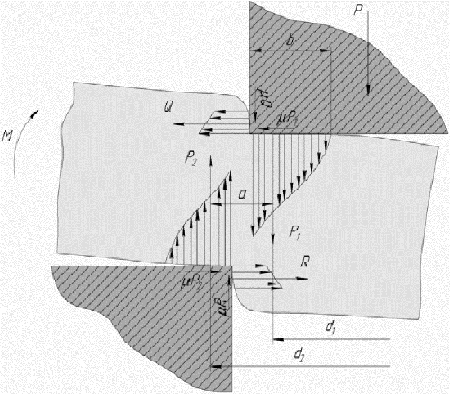
Фиг.2-2
Силата, която трябва да се приложи за изпълнение на процеса, се променя от нула до максимална стойност за много кратък период – практически за времето необходимо на поансона да проникне в заготовката на дълбочина hп (на пример за стомана от 1/5 до 3/4 от нейната дебелина) - Фиг.2-3.

Фиг.2-3
Максималната сила се изчислява като произведение на дължината на срязвания контур, дебелината на материала, якостта на материала и коефициент на условията. Този коефициент отчита влиянието на вида на материала, хлабината между матрицата и поансона, отношението между диаметъра (или най-малкия размер) и дебелината, скоростта на движение на поансона, разположението спрямо други отвори или края на материала, смазване, износване на режещите ръбове и други фактори, някои от които свързани с конструкцията на матрицата, поансона и самия инструмент. В справочниците най-често е приведено произведението на коефициента с якоста на различни материали и условно е наречено спротивление на срязване за даден материал (условно, защото не отчита влиянието на всички описани фактори за всеки конкретен случай).
За избутването на детайла (отпадъка) през отвора на матрицата, както се вижда от Фиг.2-3,
е необходима допълнителна сила за преодоляване на триенето със стените на отвора. При цилиндрична матрица тя е от 5% до 10% от стойността на максималната сила [1].
Изваждането на поансона от обработвания материал е съпроводено от триене, за чието преодоляване е необходима сила за събуване, представляваща от 2% до 20% от стойността на максималната сила [1].
Намаляване на необходимата сила може да се постигне чрез скосяване под ъгъл на матрицата и поансона [1] - Фиг.2-4.
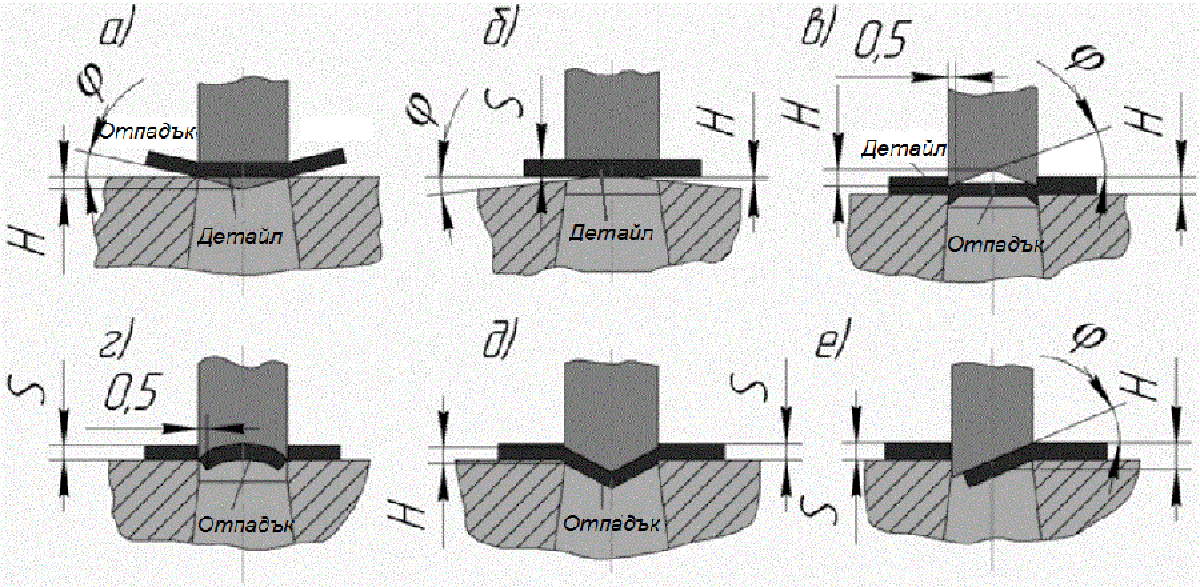
Фиг.2-4
При ИЗРЯЗВАНЕ се скосява МАТРИЦАТА (показана на „a“ и „б“) за да остане плосък детайла, а при ПРОБОВАНЕ се скосява ПОАНСОНА (показан на „в“ „г“ и „д“). Височината на скосяване „Н“ спрямо дебелината „s“ определя с колко ще се намали максималната сила - Фиг.2-5.
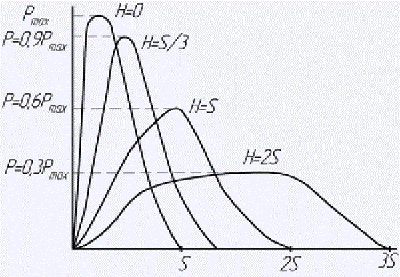
Фиг.2-5
Хлабината между матрицата и поансона е най-важния фактор за качеството на детайла. С нейното увеличаване по срязаните краища се образуват остри издатъци, наречени „чепак“ - Фиг.2-6,
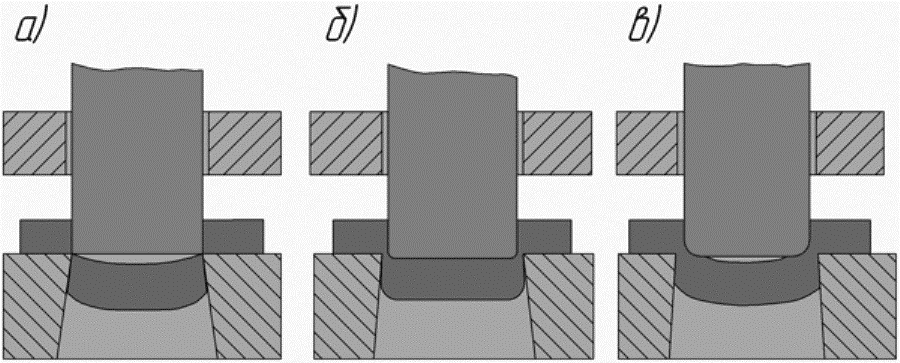
Фиг.2-6
като най-големи са при голям хлабина и износени режещи ръбове (случай „в“) . Чепак при ИЗРЯЗВАНЕ се получава от ПОАНСОНА и той трябва по-често да се проверява за износване на режещия ръб. При ПРОБИВАНЕ чепак се получава от МАТРИЦАТА и нейния режещ ръб трябва да се проверява и заточва.
1.2.Чисто изрязване и пробиване – процес на разделяне на изходната заготовка по затворен контур на две части – детайл и отпадък, при който вследствие промененото напрегнато състояние в зоната на срязване до обемен натиск, се получава детайл с гладки и перпендикулярни на основата срязани стени. Процесът изисква специални преси и инструменти, осигуряващи допълнително притискане на лентата и детайла при щанцоване - Фиг.2-7.
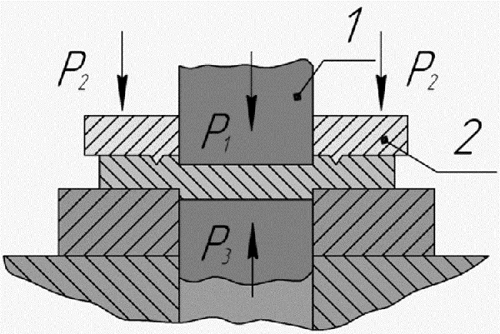
Фиг.2-7
Най-разпространеният метод за получаване на обемен натик в зоната срязаване, е използване на притискачи с клинови ребра от страните на матрицата и на поансоан - Фиг.2-8.
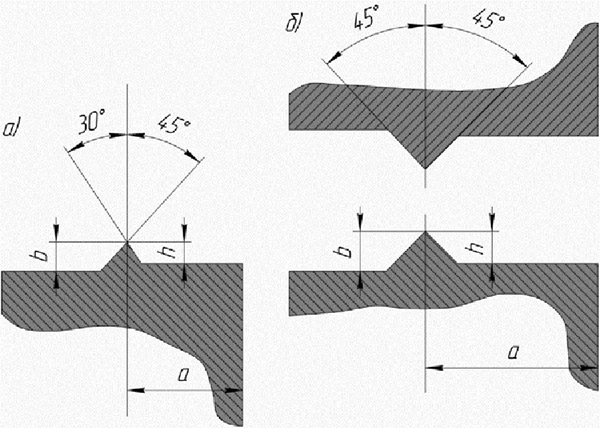
Фиг.2-8
Силата, необходима за осъществяване на процеса е 2.5-3 пъти по-голяма от тази, за обичайно щанцоване на същия детайл.
Като цяло, процесът се характеризира с ограничения по отношение на използвания материал, по голям разход на материал заради зоните, необходими за клиновите ребра, и необходимост от допълнително шлифоване на плоската страна за премахване на оставащия чепак.
1.3. Зачистване – процес на получаване на детайл с гладки и перпендикулярни на основата срязани стени чрез стружко отнемане на дефектния слой на предварително изрязани или пробити заготовки. Процесът може да се изпълни с хлабина между матрицата и поансона (лява половина) или с по-голям от матрицата поансон (дясна половина) - Фиг.2-9.
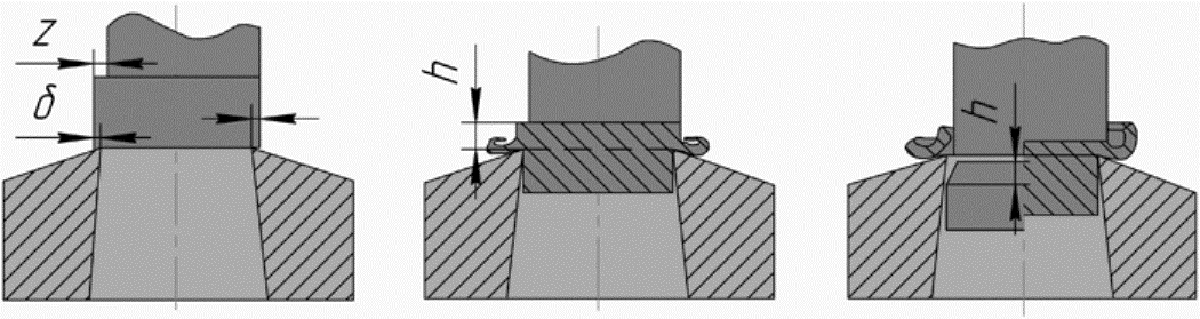
Фиг.2-9
Подходящ е за точни отвори с малък диаметър (а) и може да се комбинира в една операция с пробиване (б) - Фиг.2-10.
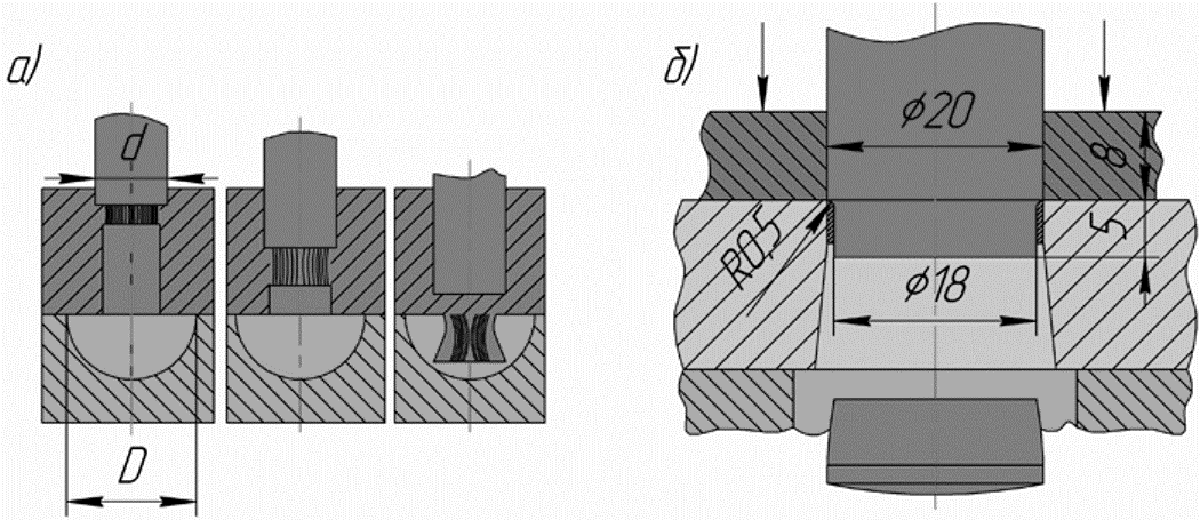
Фиг.2-10
1.4. Просичане – процес на разделяне на изходната заготовка от неметален материал по затворен контур на две части – детайл и отпадък.
1.5. Обрязване – процес на разделяне фланеца на изтеглена заготовка по затворен контур на две части (детайл и отпадък) - Фиг.2-11.
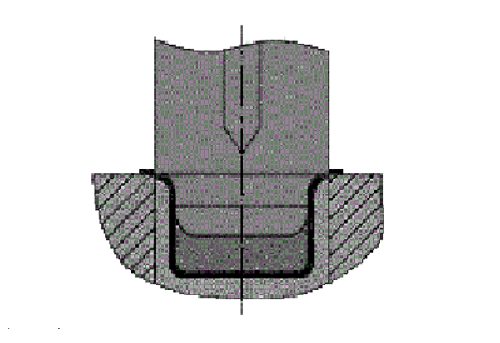
Фиг.2-11
2. Формоизменящи операции.
2.1. Огъване – процес на превръщане на плоска изходната заготовка в обемен детайл чрез пластично деформиране на отделни участъци. В резултат на дефрормацията, вътрешните слоеве по дължина на материала се свиват, външните се разпъват и огънатия учатък се деформира напречно – правоъгълното напречно сечение се превъща в трапец - Фиг.2-12.
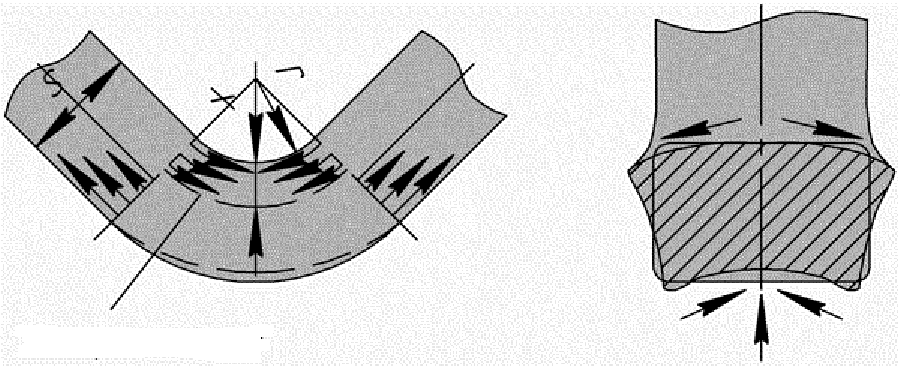
Фиг.2-12
С увеличаване широчината на огъвания детайл, напречната деформация рязко намалява. Практически при 3-5 пъти по-голяма широчина от дебелината на материала, тя може да се пренебрегне. Процесът на огъване при едноъглово – ”V“ образна форма (а) и двуъглово – ”П“ образна форма (б) - Фиг.2-13
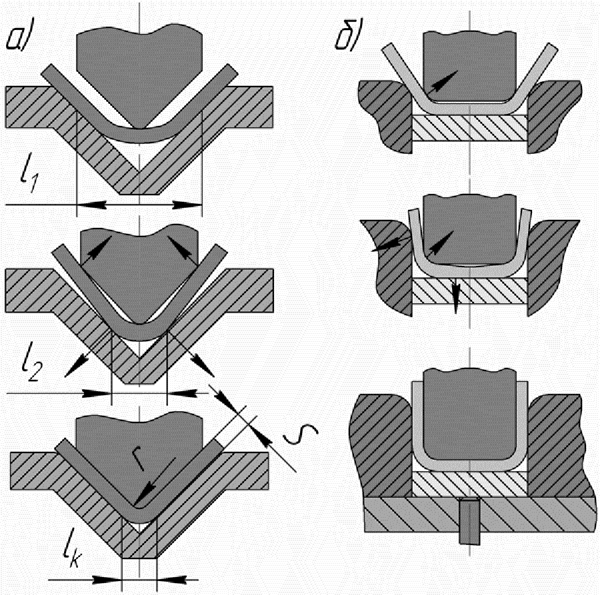
Фиг.2-13
преминава през три основни етапа:
– Еластични деформации в контактните зони на ъглите;
– Пластична деформация около зоната на радиуса на поансона, която в хода на процеса се стеснява (рамото между действащите сили се намалява);
– Калиброване на рамената и контактната зона на ъглите.
Промяната на необходимата сила за извършване на процеса за ”V“ образна форма (а) и двуъглово - ”П“ образна форма (б) на огъване е показана на Фиг.2-14.
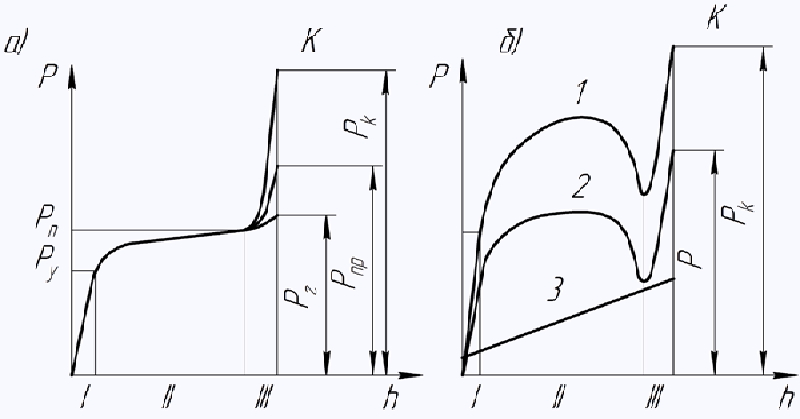
Фиг.2-14
В края на калиброването силата рязко нараства и зависи от настройката на пресата. Поради тази причина, с един и същ инструмент, на една преса могат да са налице различни резултати, вследствие различната настройка на крайното положение на поансона спрямо матрицата.
Максималната сила се изчислява като произведение на дължината на линията на огъване, дебелината на материала, якостта на материала и корекционен коефициент [1]. Този коефициент отчита вида на огъвката. Към максималната сила се добавят силата за предварително притискане на буфер и силата за калибровка, представляваща произведение на калибрована площ и специфично налягане за калибровка.
Еластичните деформации след завършване на процеса довеждат до пружиниране и промяна в ъгъла между рамената и радиуса на огъване - Фиг.2-15,
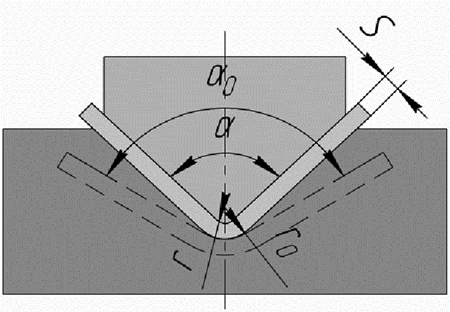
Фиг.2-15
които трябва да се коригират в инструмента.
Използват се различни методи за намаляване на пружинирането при двуъглово огъване с ”П“ образната форма - Фиг.2-16.
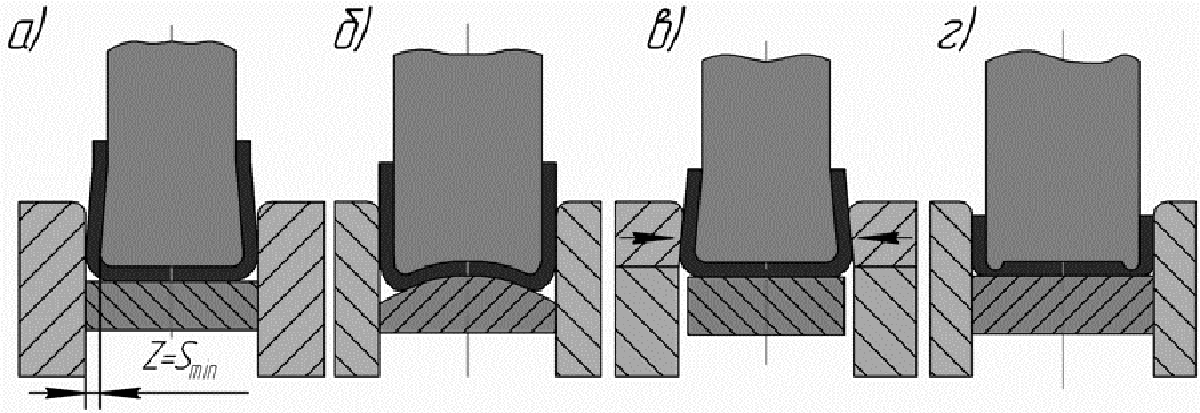
Фиг.2-16
Важно ограничение за процеса е минималния радиус на огъване, специфичен за различните материали, и зависещ от разположението на линията на огъване спрямо посоката на валцуване на листа [1]. Огъване с по-малък от допустимия радиус предизвиква пукнатини по външната изтънена част - Фиг.2-17
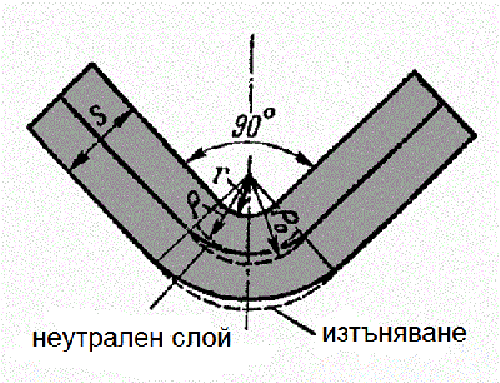
Фиг.2-17
и може да доведе до разрушение на детайла.
За да се произведе детайл със зададени размери, е необхомо да се определи дължината на изправената изходна заготовка. За тази цел се използва неутрален слой на деформациите, който включва участъци с нулева стойност на деформация. Неутралния слой в зоната на радиуса е изместен към неговия център Фиг.2-17. Общата дължина на огънатите рамена се изчислява като сума от дължините на правите участъци и дължините на неутралния слой в зоните на радиуса. Понеже точното определяне е затруднено, в практиката се прилага изчисление с дължината на дъга от окръжност с радиус, представляващ сумата на вътрешния радиус на детайла и произведението на дебелината с коефициент на изместване „х“ [1] (в някои източници се нарича „К-фактор“).
Инструмента за огъване се състои от две основни част – поансон (обхващана от материала част) и матрица (обхващаща материала част). При единично производство понякога вместо матрица се използва еластична среда (полеуретан). Коя част от инструмента е определяща за точноста – матрица или поансон, зависи от мястото на посочените допуски на детайла. Ако е зададен допуск на ВЪТРЕШЕН РАЗМЕР, то се оразмерява ПОАНСОНА. При зададен допуск на ВЪНШЕН РАЗМЕР се оразмерява МАТРИЦАТА. Винаги обаче трябва да се съобразява посоката и големината на еластичното пружиниране на рамената след края на процеса.
Огъване с предварителен опън е разновидност на процес на огъване на профилни детайли с много голям радиус. В резултат на формата, при тях еластичните деформации са много големи и след края на процеса, детайла и напречното сечение на профила се деформира, поради което трябва да се вземат специални мерки. Разтягането на заготовката с 2-5% преди и при огъване, измества неутралния слой и позволява да се намали пружинирането.
Огъване на профили и тръби е друга разновидност на процес на огъване. Съществува голямо разнообразие от форми и геометрични размери на профилите, поради което няма общ подход към всички. Като правило при този процес се използват ролки.
2.2. Изтегляне – процес на превръщане на плоска изходната заготовка с кръгла или друга форма в кух обемен детайл (чаша, кутия) чрез пластично деформиране. В хода на процеса диаметърът на равнината заготовка D постепено намалява до диаметъра на изтегления детайл d за сметка на увеличението на височината h - Фиг.2-18,
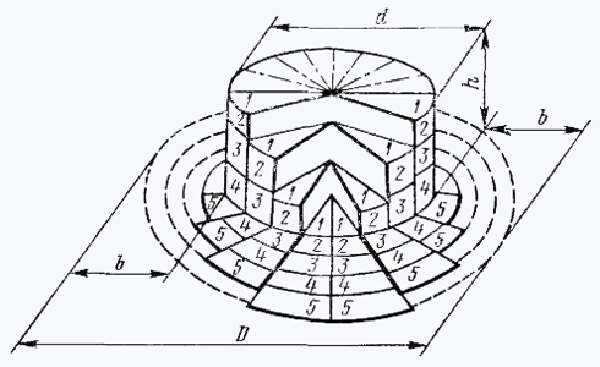
Фиг.2-18
като част от равнините участъци (2, 3, 4) получават цилиндрична форма. Важно условие за правилно протичане на изтеглянето е РАВЕНСТВО НА ОБЕМА НА ИЗХОДНАТА ЗАГОТОВКА С ОБЕМА НА ИЗТЕГЛЕНИЯ ДЕТАЙЛ. В противен случай ще настъпи разкъсване в най-натоварената част – зоната на радиус между дъното и цилиндричния участък. Протичането на отделните етапи на дълбоко изтегляне - Фиг.2-19
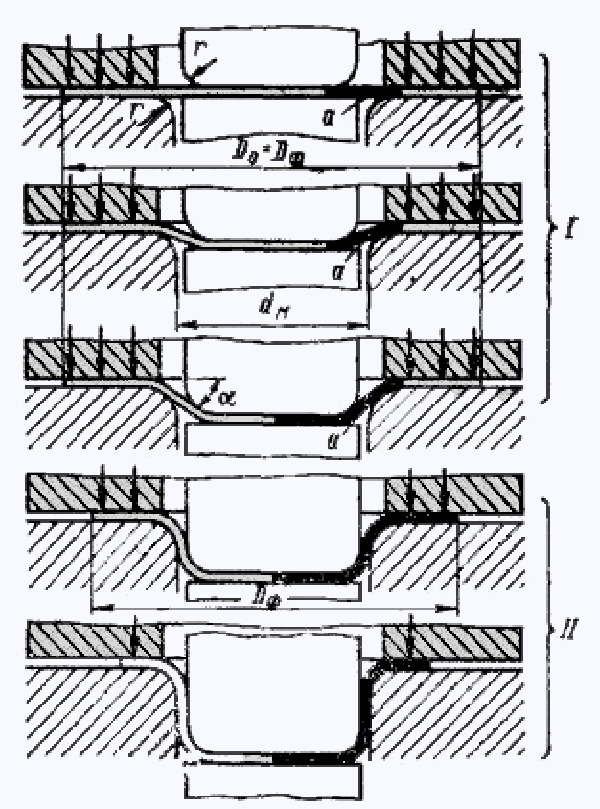
Фиг.2-19
започва с преминаване на еластичните деформаци в пластични първоначално в пръстеновидната зона между радиусите на поансона и матрицата, която постепено се разширява към дъното и фланеца (стадий I). При това, настъпва известно местно удължаване и изтъняване на участъка около радиуса на поансона, силата непрекъснато нараства до достигане на съпротивителната сила на фланеца. От този момент започва пластичното преобразуване на плоски участъци от фланеца в цилиндрични (стадий II). Фланецът започва да намаля своя диаметър D, който при цилиндрично изтегляне без фланец става равен на изтегления диаметър d, височината на изтеглената част нараства.
Деформациите на елемент от фланеца (а) - Фиг.2-20
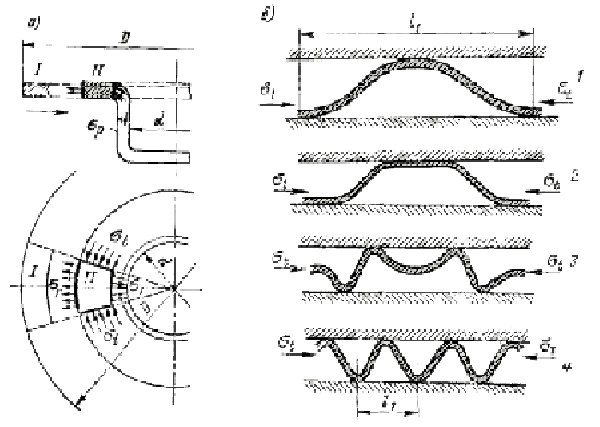
Фиг.2-20
са радиално удължаване и тангенциално свиване (вследствие взаимодействието със съседни участъци). Последното води до удебеляване на фланеца и при недостатъчно притискане действащите тангенциални напрежения предизвикват загуба на устоичивост на фланеца (б) и поява на гънки или „гофри“ (вълнообразност). Крайния резултат при образуване на гофри е рязко покачване съпотивлението на фланеца срещу изтегляне и местно изтъняване в зоната на радиуса на дъното – цилиндрична част, където след изчерпване на пластичните свойства на материала, започва откъсване на дъното. Това изисква да се вземат специални мерки за оптимално притискане на фланеца при дълбоко изтегляне на заготовки с малка дебелина – прекалено силното притискане също увеличава триенето и съпротивата на фланеца и може да доведе до откъсване на дъното.
Необходимата сила за протичане на процеса се изменя плавно от нула до максималната си стойност и пак до нула с увеличаване на изтеглената височина на детайла - Фиг.2-21.
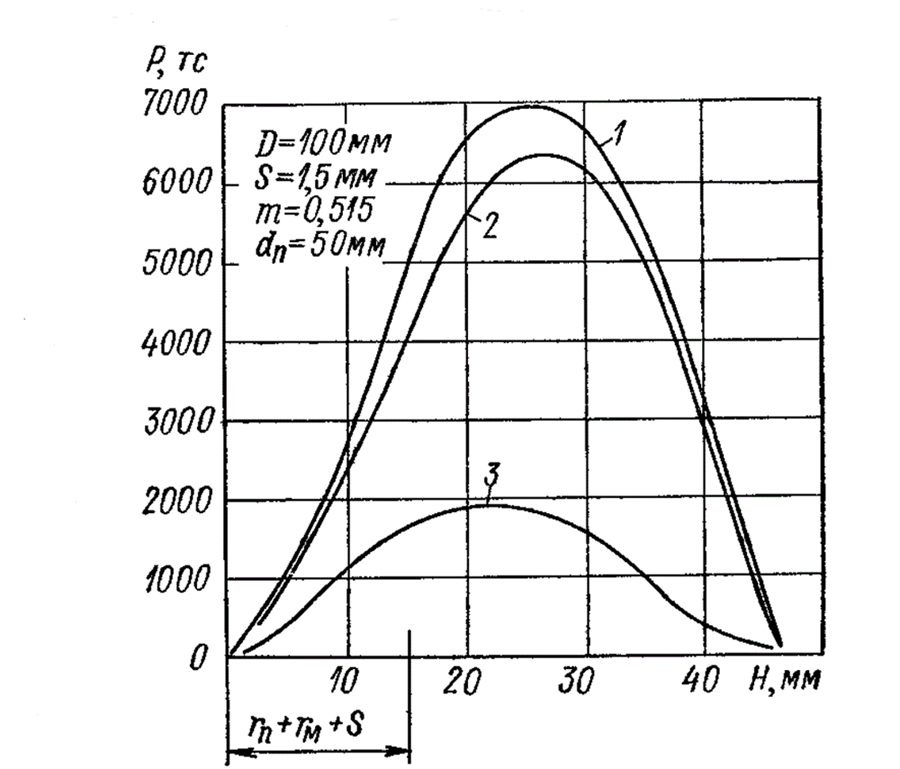
Фиг.2-21
Максималната сила е различна при изтегляне на един и същ детайл от различни материали (1-стомана; 2- месинг; 3-мек алуминий) и достига най-висока стойност около средата на изтеглената височина. Тя се изчислява като произведение на диаметъра на поансона, дебелината на детайла, якостта на материала, числото „пи“ и корекционен коефицинет, зависещ от вида на изтегляне [1].
Необходимостта от притискане на фланеца и нужната сила зависи главно от отношението на дебелината към диаметъра на изходната заготовка и дълбочината на изтегляне (височината на детайла). При заготовка с голяма относителна дебелина и не голяма дълбочина на изтегляне, е възможен устойчив процес без притискане. Силата на притискане се изчислява като произведение на притисканата площ с опитно определено специфично налягане, достатъчно за да не възникват гънки (примерно за стомана с дебелина над 0.5 mm около 2 MPa).
Границата на приложение на процеса изтегляне за определен детайл, зависи от свойствата на материала и допустимата деформация. За оценка и сравнение на последната се използват два критерия – степен на изтегляне и коефициент на изтегляне. Степента на изтегляне (число по-голямо от 1) се определя като отношение на диаметъра на изходната заготовка към диаметъра на изтегляне, а коефициентът на изтегляне (число по-малко от 1) е отношение на диаметъра на изтегляне към диаметъра на изходната заготовка (реципрочна стойност на степента на изтегляне). Практически установените допустими стойности на тези критерии са посочени в специализираната литература и зависят от редица други параметри, като относителната дебелина на заготовката, големина на радиусите на матрицата и поансона, вида на изтегления детайл (с или без фланец след изтегляне) и отношението между диаметрите на фланеца и на изтегляне, наличие и вид на смазка, скоростта на изтегляне.
По-голяма дълбочина на изтегляне (степен на изтегляне) се постига чрез разделяне на процеса на няколко операции (или прехода):
– пръво изтегляне от плоска заготовка;
– второ изтегляне на получената куха заготовка на първата операция (или преход);
– трето изтегляне на получената куха заготовка на втората операция (или преход) и така нататък.
При такъв много операционен процес се подобрява равномерността на разпределение на деформацията по височина и се намалява вероятността от скъсване на дъното, вследствие на силно изтъняване на радиуса между дъното и цилиндричната част. Диаметърът на поансона за произволна поредна операция (или преход) на изтегляне е произведение на диаметъра на поансона от предишната с допустимия коефициент на изтегляне (за второ изтегляне се взема диаметъра на плоската заготовка). Общият коефициент на възможното изтегляне за детайла е произведение от коефициентите на отделните операции. Важно правило е, че за всяка следваща операция (или преход), коефициента на изтегляне е по-малък от предходния и не по-голям от допустимия. В някои случаи, при силно уякчаващи се при деформация материали (топлоустойчиви неръждаеми стомани, мед, алуминий) след 2-3 операци на изтегляне, е необходимо отгряване на заготовката за премахване на вътрешните напрежения, след което може да се премине към следващо изтегляне. За други материали е характерна способност за промяна на свойствата във времето – например 3 последователнo извършени операции на изтегляне са напълно възможни, но 3-та операция не може да се изпълни след престой от 3 месеца върху заготовка от 2-ро изтегляне, поради скъсване на дъното.
За да се определят размерите (в случай на цилиндрично изтегляне диаметъра) на изходната плоска заготовка, се изхожда от равенство на обемите преди и след изтегляне. Наличието на неравномерни свойства на реалните материали в различни посоки (анизотропия), води до получаване на неравномерност в изтеглената височина на цилиндричен детайл, наречени „фестони“ (четири по-ниски зони под 45 градуса спрямо посоката на валцуване на стоманен лист). По тази причина изтеглените детайли се нуждаят от допълнителна операция – обрязване, за която диаметъра на изходната заготовка се увеличава с определена прибавка. В някои случаи е възможно, вместо прибавка да се промени формата на изходната заготовка – на пример от кръгла на квадратна с отчитане реалната анизотропия, с което при дълбоко изтегляне в матрици с променлив радиус може да се постигне значителна икономия на материал.
Много операционият процес на изтегляне изисква изключително прецизно изчисляване на размерите и допустимата степен на изтегляне за всяка операция (или преход) на основа на равенството на обемите. Основното правило е, че на първата операция (или преход) трябва да се изтегли целия необходим за детайла обем (с малък запас от 1-3%, за да компенсира местното изтъняване), а на всяка следваща, изтегленото количество трабва само да се преразпределя чрез равенство на обемите на изходните и крайните форми. Това означава, че на пример при много операционо изтегляне на детайл с широк фланец, неговия диаметър трябва да се получи след първа операция, а размерите при следващите трябва да са определени от условието диаметъра да остане постоянен. Изключение от това правило е случая на изтеглен детайл с фланец до 10% по-голям диаметъра на изтеглената част за няколко операции (или преходи), където първоначално се изтегля в цилиндър целия фланец, а на последната операция (или преход) част от материала на цилиндричната заготовка се връща обратно във фланеца и се калиброва.
Наличието на радиуси на закръгление на дъното или фланеца по-малки от 3-4 дебелини изискват допълнителна операция (или преход) калибровка, при която се извършва само местно деформиране на зоните до зададения радиус за сметка на намаляване на височината с 43% от разликата между изходните и крайните радиуси. С калибровка е възможно получаване на радиуси от 0.5-1 дебелината на материала. Избраните радиуси на матрицата и поансона за междинните операции (преходи) трябва постепенно да намаляват и на последната да отговарят на зададените. Увеличаването на радиусите (особено на матрицата) облекчават процеса на изтегляне, но много голям радиус на матрицата може да доведе до прекалено рано излизане на фланеца от притискане и образуване на гънки – „гофри“.
При тънкостени детайли с конична, сферична или неправилна форма, допълнително се оформят възпиращи ребра или прагове, целящи допълнително затрудняване на изтичането на материала от фланеца, с което намалява опасността за образуване на гънки - „гофри“.
Конструктивното оформяне на изтеглящите матрици и поансони изискват осигуряване на достатъчна хлабина между тях, за да може да преминават дори удебелените участъци на фланеца, да намалят натиска върху стените на матрицата и да остане място за прилагане на смазка, с което се намалява триенето и преждевременото износване. Обикновено, препоръчаната хлабина е най-голяма на първата операция (или преход) – примерно 1.3 пъти дебелината на материала и постепено намалява за да достигне до 1.05-1.1 пъти дебелината при калиброване.
Изтеглените детайли могат да се разделят условно според геометричната си форма на три основни групи:
– осево симетрични ротациони детайли (симетрично равномерно поле на деформация);
– детайли с форма на квадратни, правоъгълни, елептични кутии (от части симетрично, не равномерно разпределено поле на деформации);
– детайли с произволна не симетрична форма (не симетрично, не равномерно поле на деформации).
Методите за определяне на изходната заготовка и построяване на процеса за всяка от основните групи са различни, но условието за равенство на обема и оценка на допустимата деформация остават в сила за всеки един от тях.
Процесите на изтегляне според дебелината на стената са два основни вида:
– без изтъняване, при което дебелината на заготовката и изтегления детайл остава равна на изходната (с изключение на незначително изтънения участък на радиуса между дъното и цилиндричната част и слабо удебеления участък на фланеца);
– с изтъняване, при което дебелината на стената на изтегления детайл е по-малка от тази на заготовката, като в този случай се постига значително по-голяма височина на изтегляне.
Като пример за много операционен процес на изтегляне може да се посочи последователното изтегляне в лента - Фиг.2-22,
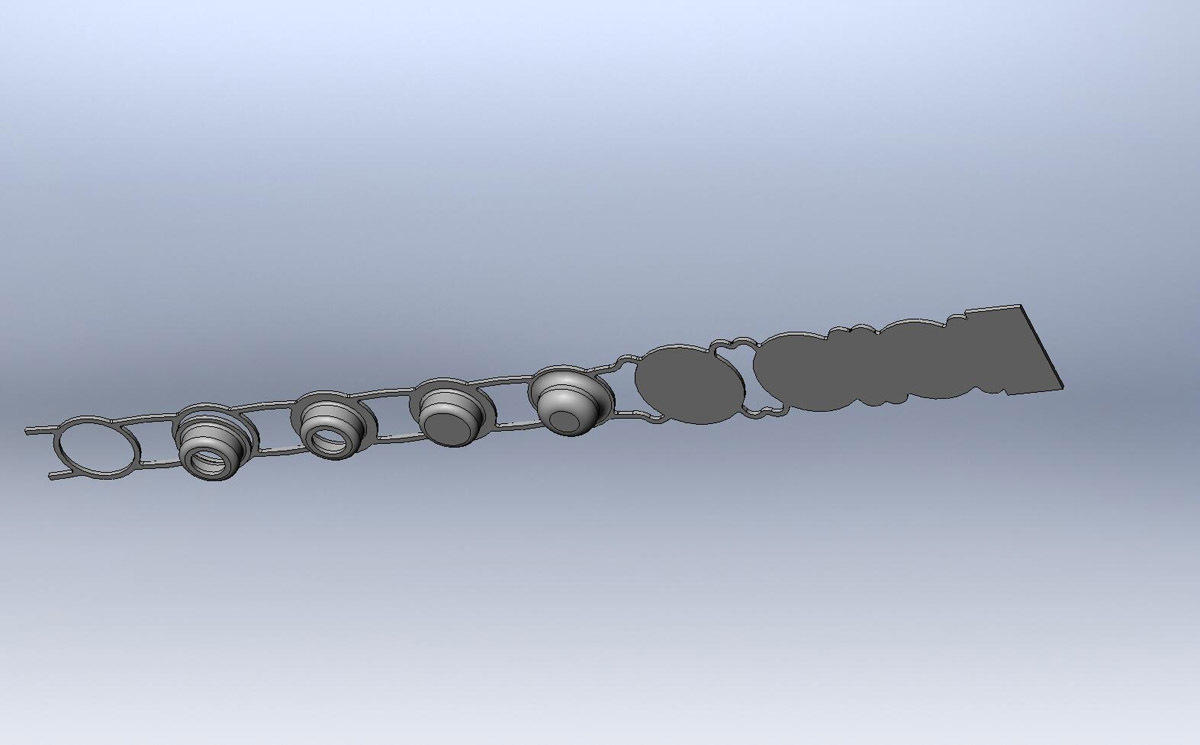
Фиг.2-22
където на всяка позиция (стъпка) се извършва един преход на обработка, вклочително пробиване на отвор и обрязване на готовия детайл.
2.3. Отбортоване – процес на получаване на борд по периферията на предварително пробит отвор (ВЪТРЕШНО ОТБОРТОВАНЕ) или изрязан контур (ВЪНШНО ОТБОРТОВАНЕ) в плоска изходната заготовка чрез пластично деформиране на материала. В хода на процеса диаметъра на пробития отвор d постепено се увеличава до диаметъра на отбортоване D, за сметка на увеличението на височината Н - Фиг.2-23.
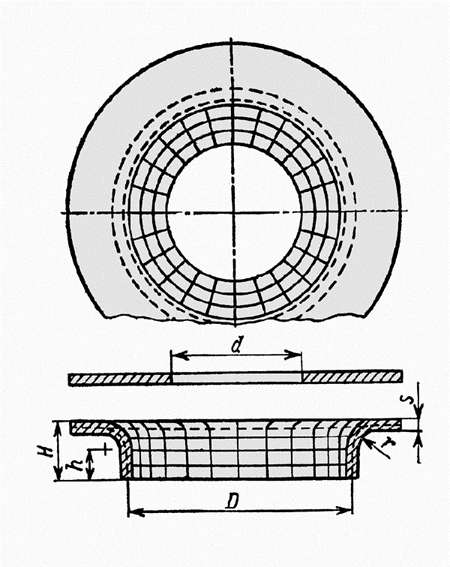
Фиг.2-23
Равнините участъците, разположени между диаметрите D и d получават цилиндрична форма, с което местно се увеличава коравината на детайла. Увеличаването на диаметъра е съпроодено с значително удължаване на повърхностните слоеве на отвора и намаляване на изходната дебелина, което може да предизвика пукнатини по външния ръб на борда. Максимално допустимата деформация се оценява с коефициент на отбортоване, представляващ отношението на диаметъра на пробития отвор към диаметъра на отбртовка. В някои литературни източници се използва степен на отбортовка, която е число, реципрочно на коефициент на отбортоване. Освен от материала, допустимия с коефициент на отбортоване зависи от отношението на дебелината към диаметъра на отвора, метода на пробиване и формата на отбортоващия поансон.
Необходимата сила за отбортоване се изменя от нула до максимална стойност и плавно намалява към края на хода на отбортоващия поансон - Фиг.2-24.
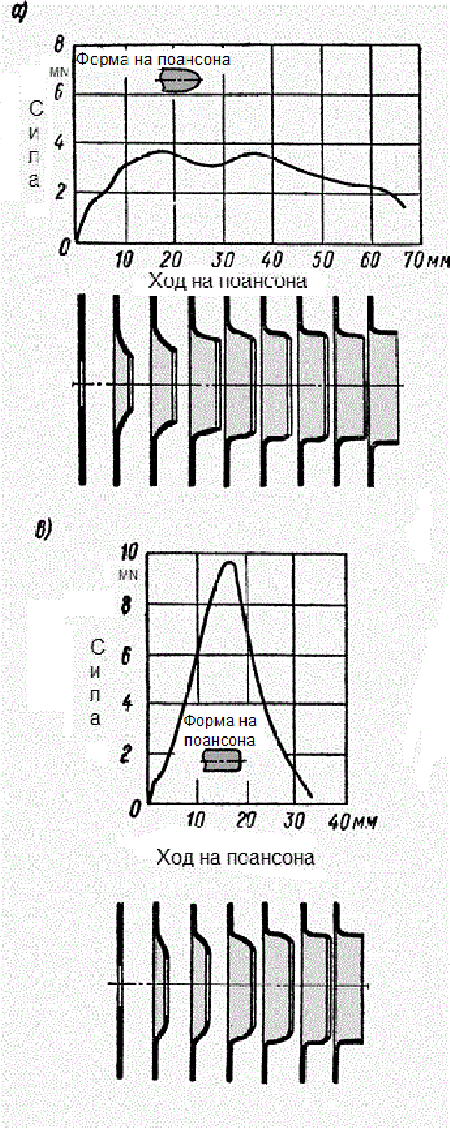
Фиг.2-24
Максималната стойност зависи от формата на отбортоващия поансон – при криволинейна форма (а) тя е над два пъти по-ниска от тази при цилиндрична форма (в).
Максималната сила в общия случай на вътрешно или външно отбортоване се изчислява като произведение на дължината на отбортования контур, дебелината на детайла, якостта на материала и корекционен коефицинет, зависещ от условията.
Построяването на процес за вътрешно отбортоване обикновено изисква определяне на диаметъра на пробития отвор по зададени крайни размери. Може да се използва равенството на обемите преди и след отбортоване, но трябва да се има в предвид неравномерното изтъняване на дебелината на стената до 30-45% в края. Съществуват емпиричи формули за определяне на диаметъра на пробития отвор за случаи на отбортоване на детайл с резба до М5 [1]. При този вид може да се използва и отбортоване без предварително пробит отвор.
Допустимата деформация (коефициент на отбортоване) ограничава височината на получавания борд. За известно увеличение на височината се препоръчва увеличаване на радиуса на матрицата, когато е възможно (на пример за увеличаване на местната коравина), или отбортоване с изтъняване на стената (за по-дълга цилиндрична част) чрез намаляване диаметъра на отвора в матрицата. Когато тези методи не дават желания резултат се прилага комбиниран метод, съчетаващ три операции (прехода) – на първо изтегляне, следващо пробиване на предварителен отвор в дъното и същинско отбортоване - Фиг.2-25
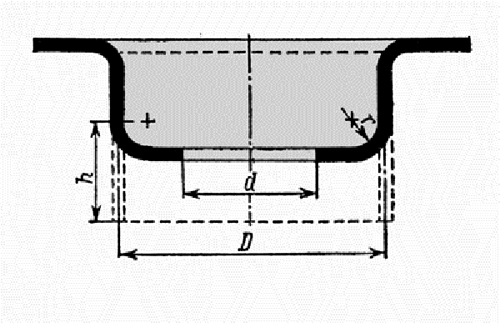
Фиг.2-25
с което към височината на отбортоване h се прибавя висичината на изтегления участък.
Важно правило за избягване на пукнатини при отбортоването е, заготовката с предварително пробит отвор да се поставя обратно на посоката на пробиване (чепака от пробиване да е към отбортоващия поансон). Така остатъчните опънови напрежения от пробиване на отвора ще се разположат в по-слабо деформираната вътрешна част на стената.
Външното отбортоване е най-използвания метод за увеличаване на коравината на сложни детайли от автомобилната, авиационата промишлености и техниката за дома. Според формата се дели на два вида - Фиг.2-26
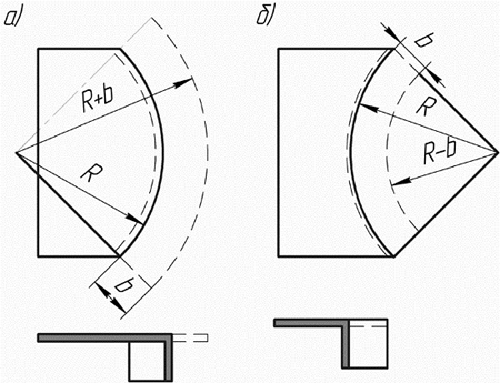
Фиг.2-26
– изпъкнала (а) и вдлъбната (б). Характерът на деформация на първия вид е подобна на изтегляне с малка височина и може да се използват съответните изчислителни методи. Втория вид е аналогичен на вътрешно отбортоване на отвор и методите на изчисление са подобни.
2.4. Релефно формоване – процес на получаване на местен пространствен релеф (изпъкналост или вдлъбнатост) върху плоска повърхност на детайла чрез локално пластично деформиране (удължаване) на прилежащите зони. Най-разпостранените приложения са усилващи ребра (а), опорни крачета и пъпки (б) за контактно електросъпротивително заваряване на детайлите - Фиг.2-27.
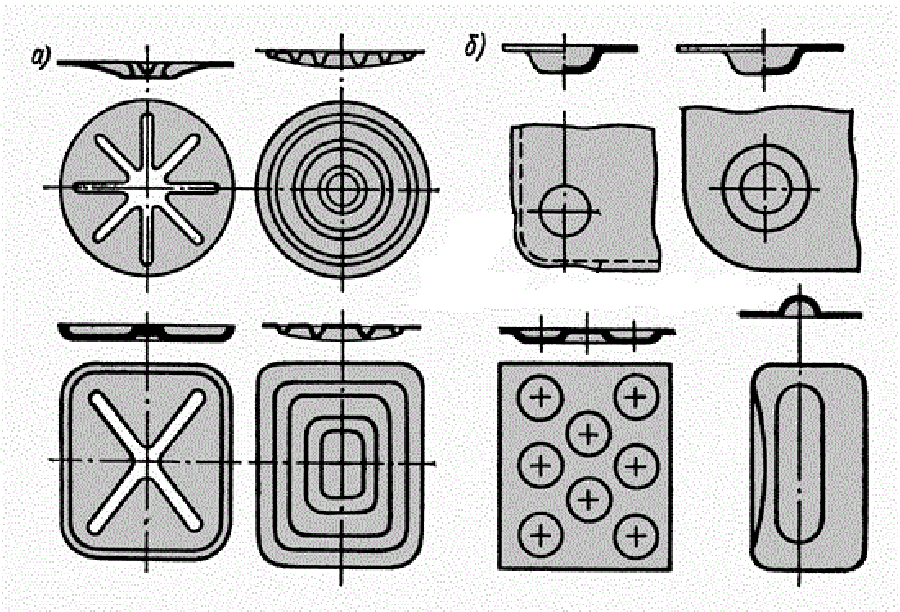
Фиг.2-27
Височината на релефа зависи от материала и геометрията на инструмента (радиусите на закръгление на матрицата, поансона и хлабината между тях). При заготовки с големи размери (разтоянието от формования участък до края детайла е повече от 10 пъти широчината на формоване) е прието, че пластичната зона обхваща област около 1,65 пъти по-голяма от широчината на формоване. Важно практическо правило е, релефното формоване да се извърши преди изрязване, пробиване или обрязване, за да се избегнат нежелани деформации на контура.
2.5. Планиране и калиброване – процес на получаване на равнинен детайл или такъв с правилна форма. При много детайли, поради остатъчни напрежения от извършени различни щамповъчни операции, се нарушава равниността на плоските повърхности.
Тяхното изправяне (планиране) се извършва чрез притискане между гладки или назъбени матрици и поансони. Процес на калиброване се изпълнява върху огънати, изтеглени или формовани повърхности чрез притискане на заготовката между матрица и поансон с подходяща форма. И при двата процеса необходимата сила е произведение на съответната площ по специвично налягане, зависещо от материала и вида на процеса.
ГЛАВА 3. ТЕХНОЛОГИЧНИ ИЗИСКВАНИЯ КЪМ ДЕТАЙЛИТЕ ОТ ЛИСТОВ МАТЕРИАЛ, ПОЛУЧАВАНИ ЧРЕЗ ПРЕСОВА ОБРАБОТКА
1. Технологичност на детайл от листов материал – съчетание на такъв набор от технически характеристики и експлотациони свойства (якост, твърдост, износоустойчивост, геометрични форми и размери, точност, възможност за заваряване, тегло и други), който позволява най-бързо, най-просто и най-евтино изработване в определени производствени условия. Главен фактор за технологичност е серийността на производство – технологичен детайл за голяма серия (скъпи и сложни инструменти) често е не технологичен за единични детайли (евтини и прости или универсални инструменти) и обратно. Заедно със серийността, детайлът трябва да се оцени и по отношение на ограниченията, характерни за използваните материали и възможните методи за производство.
2. Показатели за оценка на технологичността на детайл от листов материал – тяхното изпълнение позволява производсто с най-ниска себестойност:
2.1. Минимален разход на материал – избраната форма и размери да гарантират най-малко отпадъчен материал (най-висок коефициент на използване на изxодния материал).
2.2. Минимален брой технологични операции за производство – избраната форма, размери и точност да се постигат чрез технологични процеси с ниска трудоемкост за най-малък брой операции. По възможност, да не е необходима допълнителна механична обработка чрез стружко отделяне.
2.3. Минимален брой необходими специално оборудване и инструменти – избраната форма, размери и точност да позволяват използване на минимален брой най-прости специални инструменти, с къси срокове за изработка и ниска цена.
2.4. Максимална производителност – избраната форма, размери, точност и материал да позволяват използване на високо ефективни производствени процеси (на пример последователно комбинирано щанцоване в лента - Фиг.3-1 и Фиг.3-2).
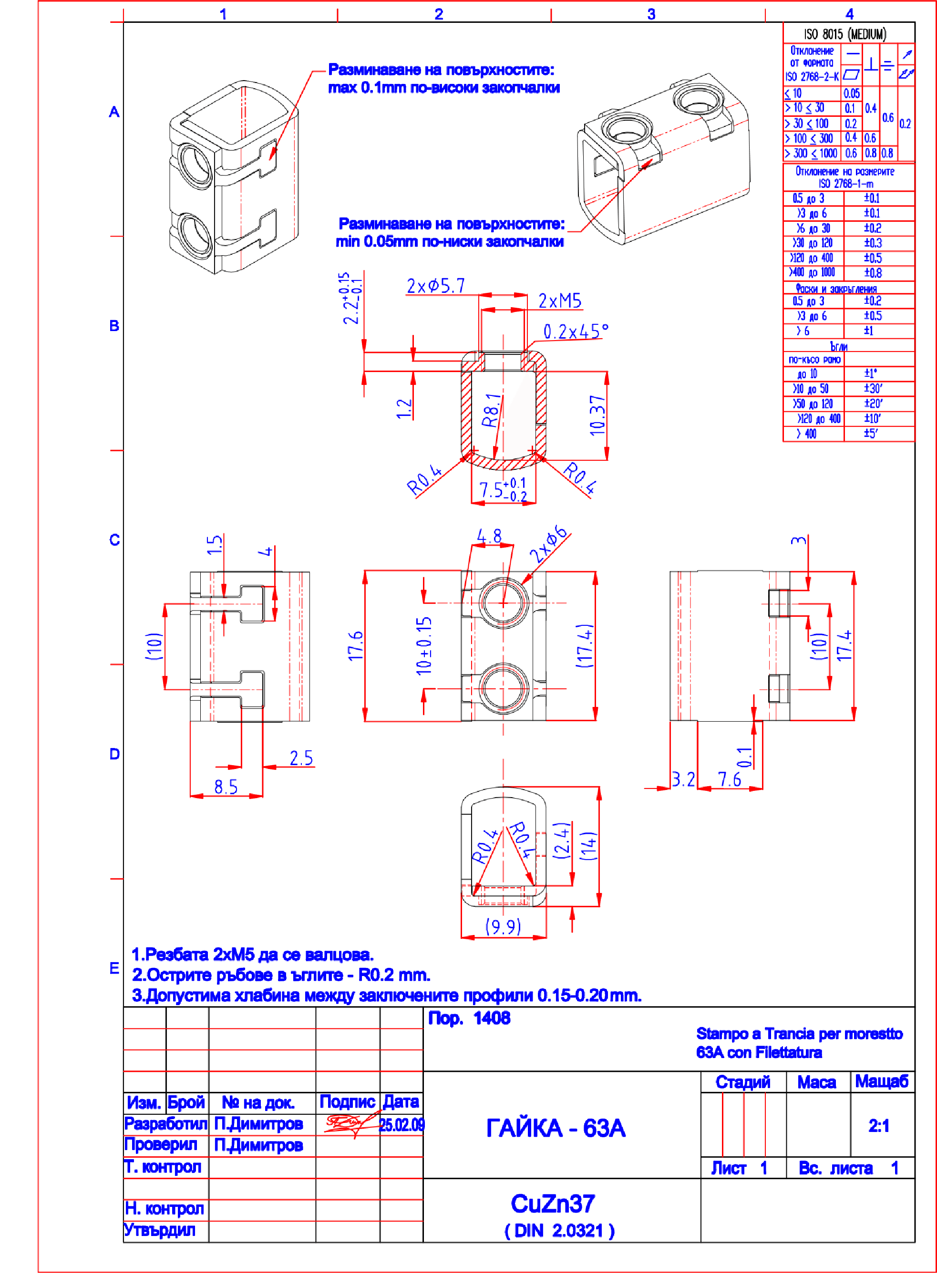
Фиг.3-1
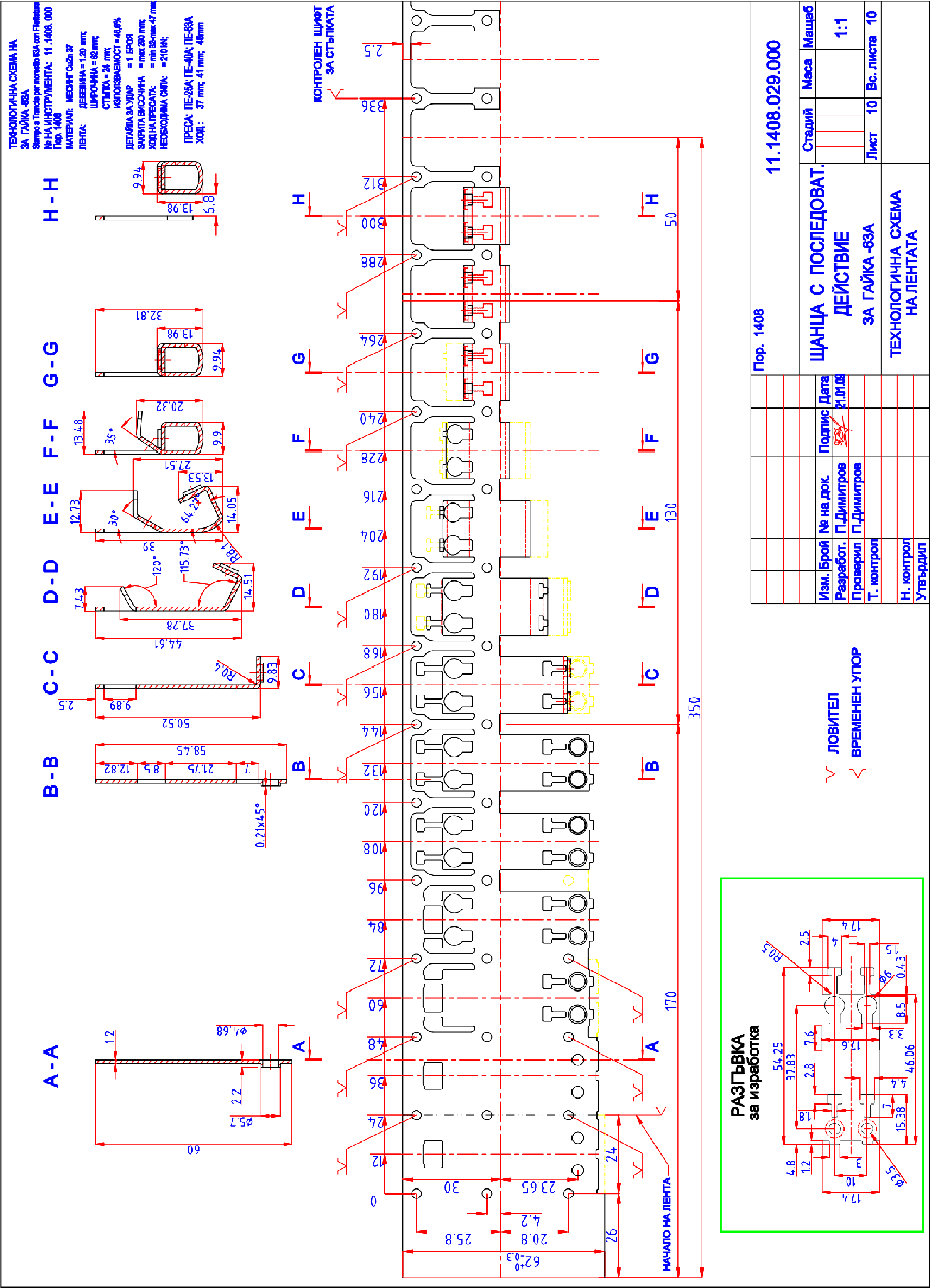
Фиг.3-2
3. Себестойност на детайл от листов материал – обобщен комплексен показател за оценка на технологичността на детайла при определени условия на производство. Тя има числова стойност (лева / евро) и показва разходите за производство на един детайл. Включва три основни вида разходи:
– за материали (основни и спомагателни);
– за труд и общозаводски разходи (разпределени върху единица пряко вложен труд за производство);
– за изработка, поддръжка и експлоатация (амортизация) на иструменти.
При серийно производство, вследствие на голямото количество детайли и прилагането на високо производителни методи, цената на материала е от 50-90% от общите разходи и е много по-ефективно да се търси намаляване на себестойността чрез икономия на матерал. Това важи най-силно при големи габарити и използване на скъп материал. Обратният случай е при малки серии или единични детайли. При тях разходите за специални инструменти се разпределят върху малък брой детайли и водят до мнокократно по-големи стойности (десетки, стотици, хиляди пъти) от тези за материали и труд. Затова, ефективния метод тук е увеличение на разходите за труд и материали за сметка на опростяване и минимизиране на броя на специалните инструменти (намалява цената за инструментите).
4. Технологични изисквания към детайл от листов материал, получен чрез изрязване и пробиване – ще бъдат изброени основните ограничения, не позволяващи прилагане на надежден технологичен процес за производство и на инструменти с достатъчна трайност.
4.1. Формата на детайла да не включва дълги и тесни прорези с широчина по-малка от 3 пъти дебелината на материала и дължина по-голяма от 3 пъти широчината. Такива прорези водят до недостатъчна здравина на матрицата, следователно до не траен инструмент и не надежден производствен процес. В най-добрият случай, те изискват сложен и скъп инструмент. Правилото важи и за изработка чрез изрязване на дълги и тесни детайли.
4.2. Размерите на пробитите отвори в детайла да не са по-малки от 1 (кръгли) и 0,7 (правоъгълни) пъти дебелината на материала (за мека стомана и месинг). По-малките отвори водят до високо натоварване на поансона и загуба на усточивост, задръстване на отворите в матрицата, следователно до не траен и скъп инструмент и не надежден производствен процес. Такива отвори се допускат като изключение при използване на скъпи пробиващи инструменти със специална конструкция за водене на поансоните.
4.3. Разстоянието между пробитите отвори в детайла да не е по-малко от 3 пъти дебелината на материала, а до края на детайла да не е по-малко от 2 пъти дебелината. В противен случай, отворите не могат да се пробиват едновремено или ще предизвикат остатъчни деформации на изрязани (пробити) повърхнини. По-малкото разстояние изисква допълнителна операция с ново позициониране и резултата е по-ниска точност и по-скъп инструмент.
4.4. Детайла да не включва радиуси на закръгление, по-малки от 0,5 пъти дебелината на материала и като абсолютен размер по-малки от 0,25 mm. Малките радиуси водят до високо натоварване и бързо износване на матриците и поансоните, следователно до не траен инструмент и не надежден производствен процес. Радиуси под 0.2 mm са изключително трудни за изработка. Най-често в този случай се прилагат съставни конструкции на матрици и поансони (радиуса може да е нула), които са значително по-скъпи. Изключение се допуска само за външни контури на детайли, получавани чрез безотпадни схеми ща изрязване - Фиг.3-3.
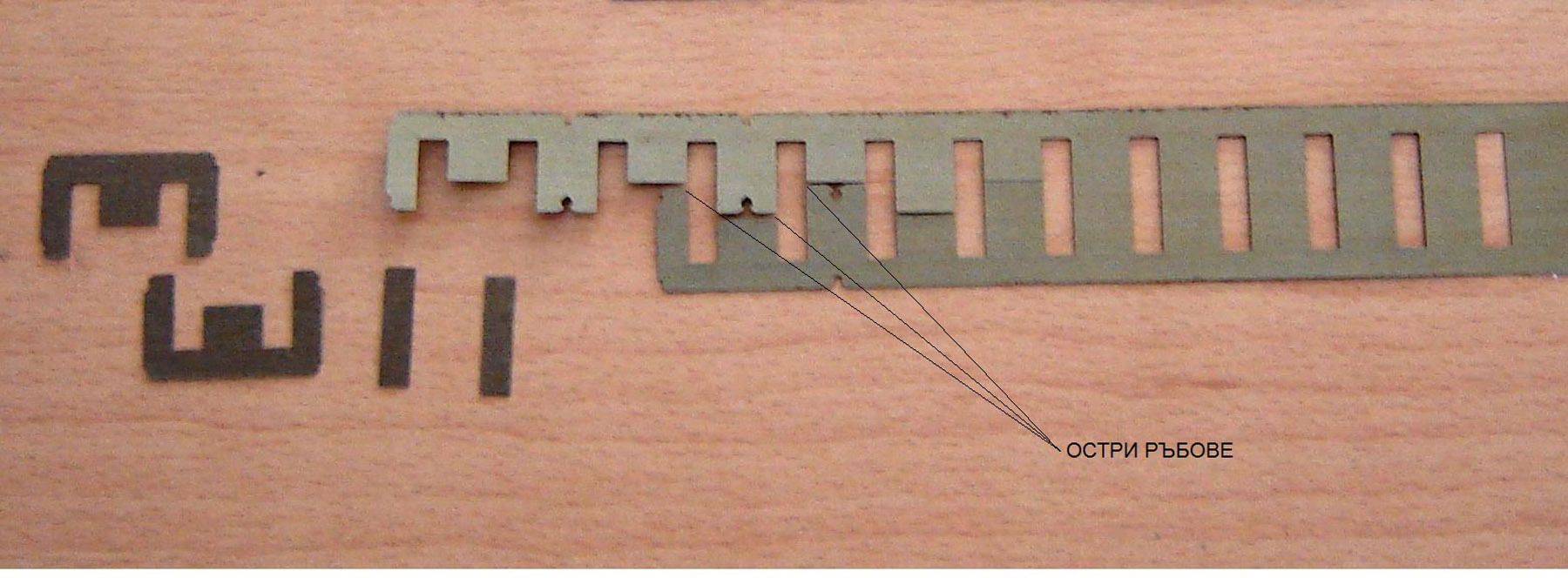
Фиг.3-3
4.5. Разгъвките на огънати детайли да не включват отвори, разположени на разстояние от центъра на радиуса по-малко 2 пъти дебелината на материала. В противен случай е неизбежна деформация на отвора след огъване.
4.6. Отворите в дъното или фланеца на изтеглени детайли, да са разположени на разстояние от центъра на радиуса не по-малко от 0,5 пъти дебелината на материала - Фиг.3-4.
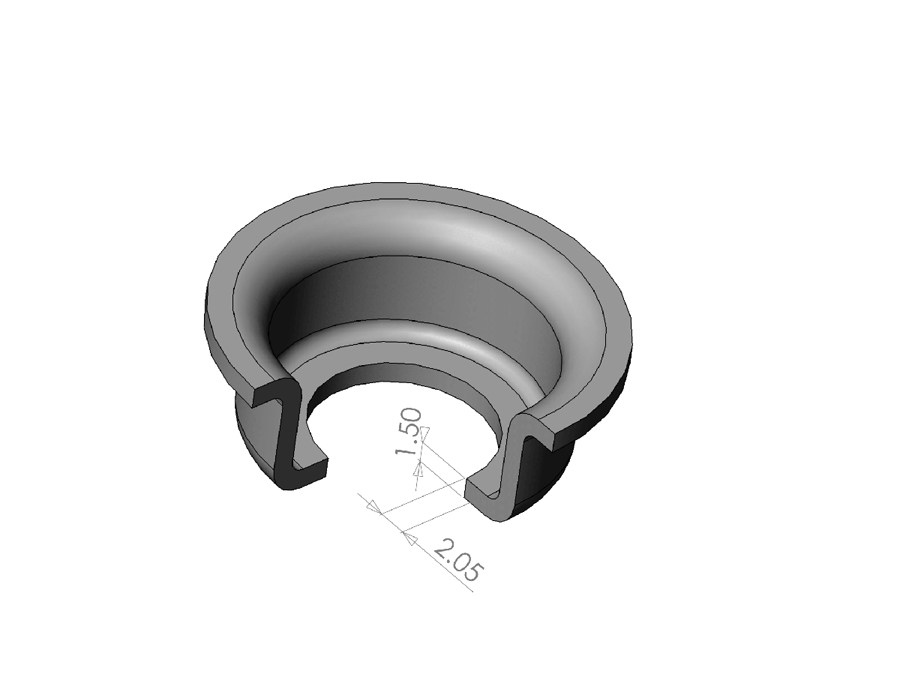
Фиг.3-4
Те задължително да се пробиват след изтегляне, за да се избегне деформация на отвора и откъсване на дъното пpи изтегляне.
4.7. Точността на размерите да не включва допуски по-малки от 0.05 mm. Поансоните и матриците при експлоатация се износват и тяхното заточване не може изцяло да го компенсира. Възникват също еластични деформации след края на изрязване или пробиване. Това означава не достатъчна трайност на инструмента. Изключение е допустимо само за пробиване кръгли отвори със стандартен цилиндричен поансон.
4.8. Детайлите да не включват повишени изисквания за грапавост и точност на формата на изрязаните и пробити повърхнини. Обичайните повърхности от изрязване и пробиване се състоят от закръгление, гладка блестяща част и грапава наклонена зона. Високи изисквания за точност на формата и грапавост изискват допълнителна обработка – зачистване или други операции чрез стружко oтнемaне, което оскъпява детайла. Чисто изрязване или пробиване да се прилагат по изключение при обосновани случаи, съобразено с техническите изисквания към тях, посочени в [1].
4.9. Детайлите да включват изисквания за посоката на чепака само на отвори или само на външните контури. В противен случай се усложняват и оскъпяват инструментите и производствените процеси.
5. Технологични изисквания към детайл от листов материал, получен чрез огъване:
5.1. Минималният вътрешен радиус на огънат детайл да не по-малък от 0,5 пъти дебелината на материала (за мека стомана и месинг, линията на огъване напречно на посоката на влакната) и по-малък от 3 пъти (за твърда стомана, наклепан месинг, бронз). Не спазването на тези правила води до поява на пукнатини от страната на външния радиус на огънатия детайл. Минималният радиус трябва да е 2 пъти по-голям от посочените при разполагане линията на огъване надлъжно на посоката на влакната от валцоване на листа.
5.2. Минималната височина на огънатото рамо на детайла над радиуса да не по-малка от 3 пъти дебелината на материала . По-малка височина не позволява да се получи желания ъгъл и е придружена с деформации на рамото.
5.3. Радиусът на огъване при детайли с голяма разлика между широчината на огънатите рамената да не започва на разстояние по-малко от 0,5 пъти дебелината на материала от началото на по-широката част. Ако това не е изпълнено, в зоните на широкото рамо да са предвидени освобождаващи изрязани участъци с широчина по-голяма от дебелината на материала, които да подминават началото на радиуса минимум с 0,5 пъти дебелината - Фиг.3-5.
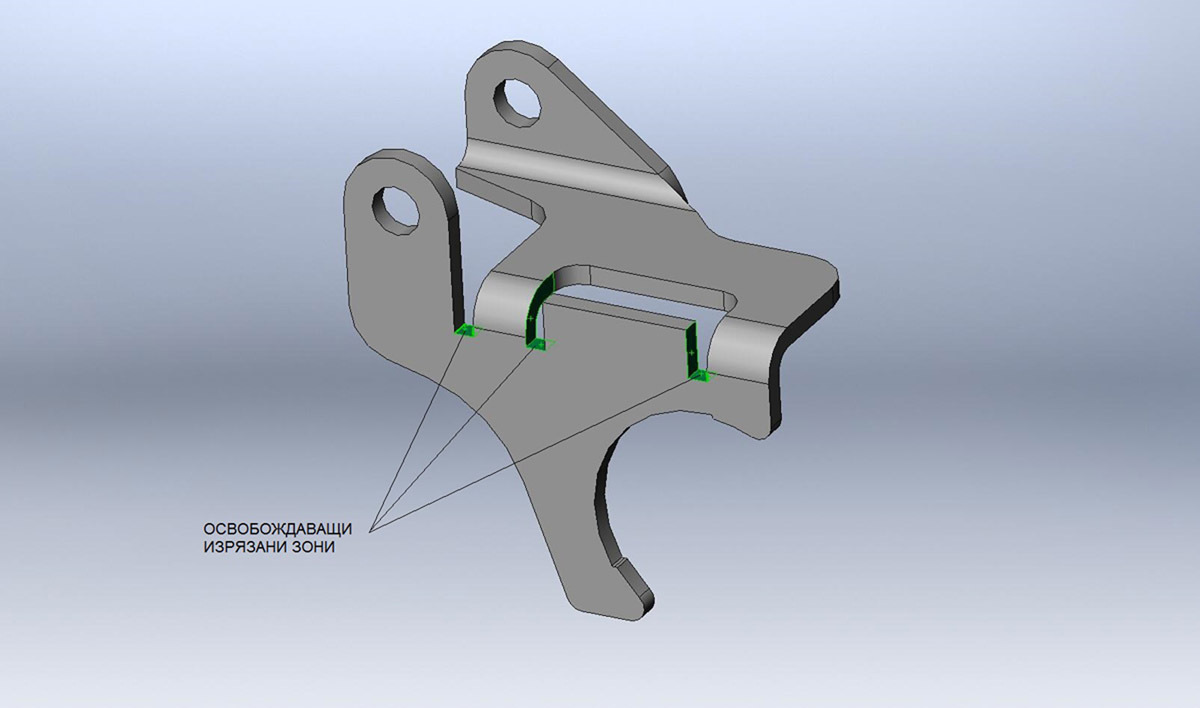
Фиг.3-5
5.4. На огънатите детайли да се задава само вътрешния радиус на огъване. Поради наличие на деформации, външния радиус не може да се получи точно (не цилиндрична форма на повърхнината). Изключение е случай на огъване с радиус по-голям от 10 пъти дебелината на материала. Тогава може да се зададе само външния радиус.
5.5. Точността на размерите на огънатите детайли да не е по-малка от 0,2-0,3 пъти дебелината на материала, в абсолютна стойност по-малка от 0.1 mm. Наличието на част от пластичната деформация в правите участъци на рамената и различното пружиниране при повече огъвки ще доведе до трудно подържане на по-малък допуск при експлоатация. Освен това, ще са необходими много опити и пробно уточняване на разгъвката, което ще оскъпи инструмента.
5.6. Допуските за широчината на рамената да не се отнасят за зоната на огъване (осбено при рамена по-тесни от 3 пъти дебелината на материала – виж Фиг.2-12. Ако това е невъзможно, зоната на огъване трябва да е изпълнена с по-малък размер от широчината на рамото.
5.7. На огънатите детайли с повече от една огъвка да са предвидени технологични бази, които да се използват при следващите операции на огъване - Фиг.3-6.
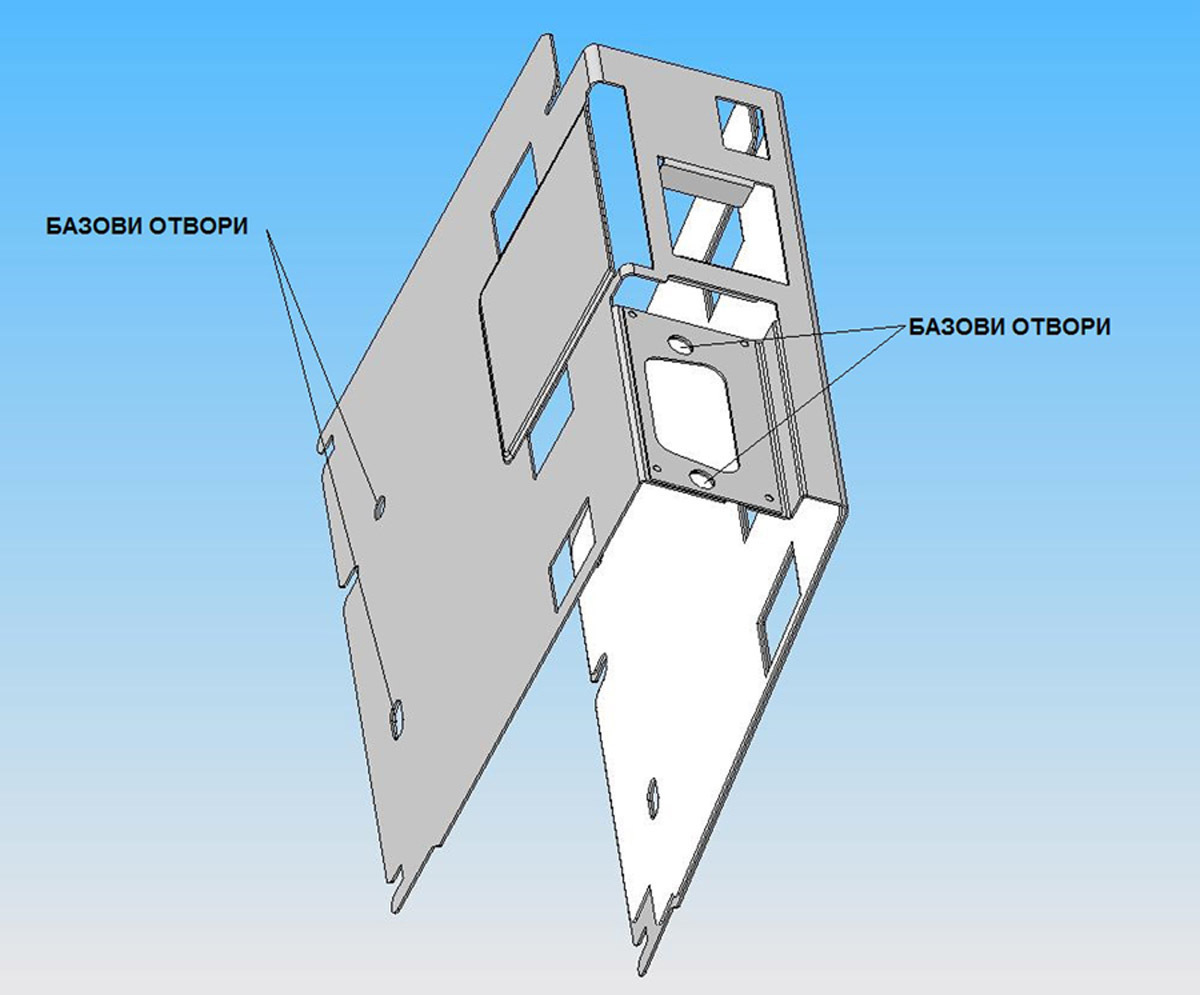
Фиг.3-6
6. Технологични изисквания към детайл от листов материал, получен чрез дълбоко изтегляне:
6.1. Изтегляните детайли да нямат сложна не симетрична форма. Ако детайлите са не симетрични, то формата да позволява получаването им чрез разделяне на симетрична заготовка на сътветен брой части - Фиг.3-7.
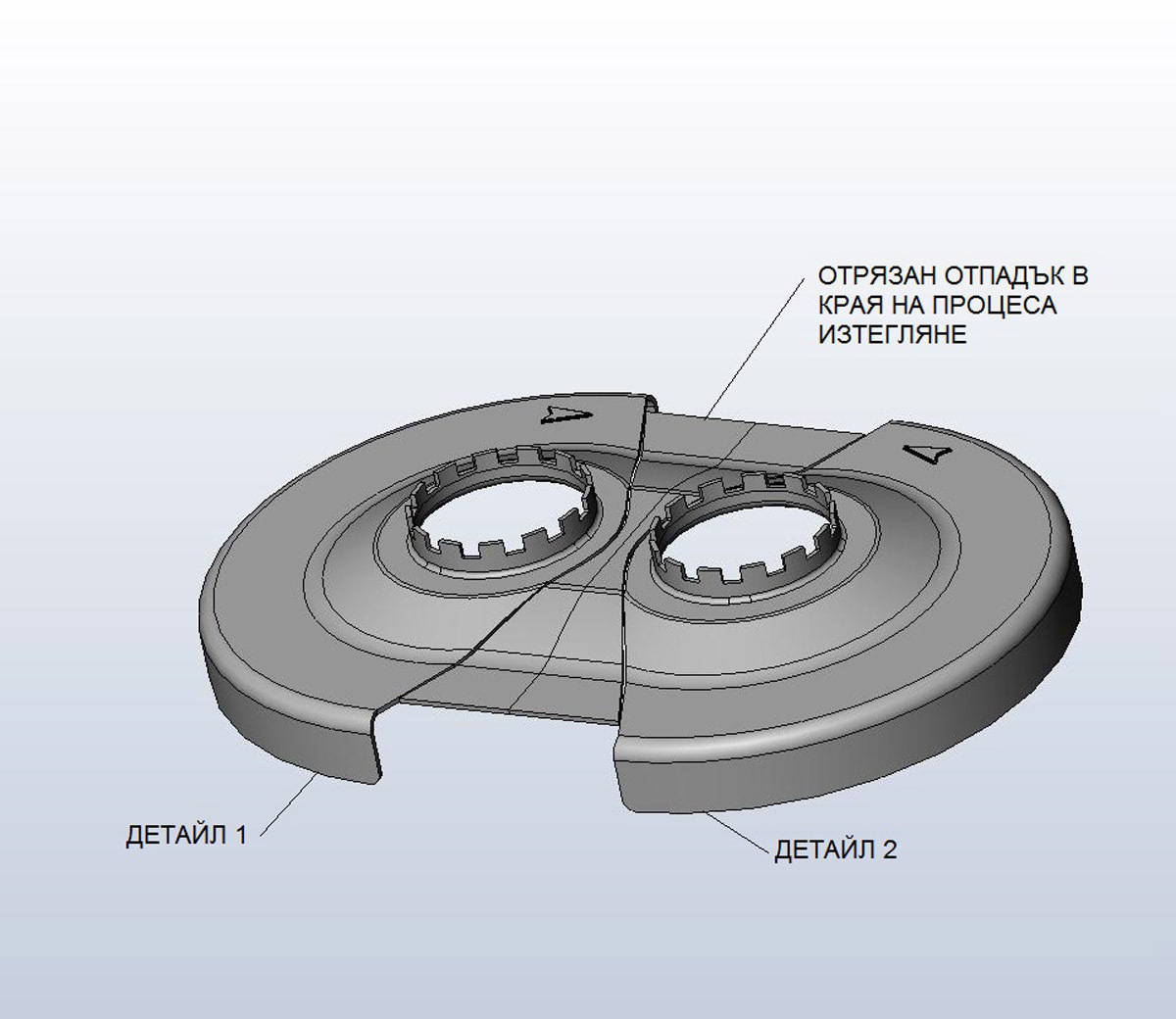
Фиг.3-7
Не спазването на тези условия водят до еднострано издърпане на материала и невъзможност за получаване на устойчив процес.
6.2. Изтегляните цилиндрични детайли да нямат височина по-голяма от 1,5-2 пъти диаметъра на изтеглената част. За детайли с фланец, последния да е с диаметър по-малък от 3 пъти диаметъра на изтеглената част, а нейната височина да е по-малка от 1.5 пъти диаметъра на изтеглената част. Това са ориентировъчни ограничения за процеса, на база максимална допустима деформация, без разрушение на детайла. Точната оценка изисква изчисления за всеки конкретен случай.
6.3. Радиусите на дъното и на фланеца да не са по-малки от 3-5 пъти дебелината на материала. За получаване на минимални радиуси от 1 път дебелината на материала са необходими допълнителни операции за калиброване, което усложнява и оскъпява процеса - Фиг.3-8.
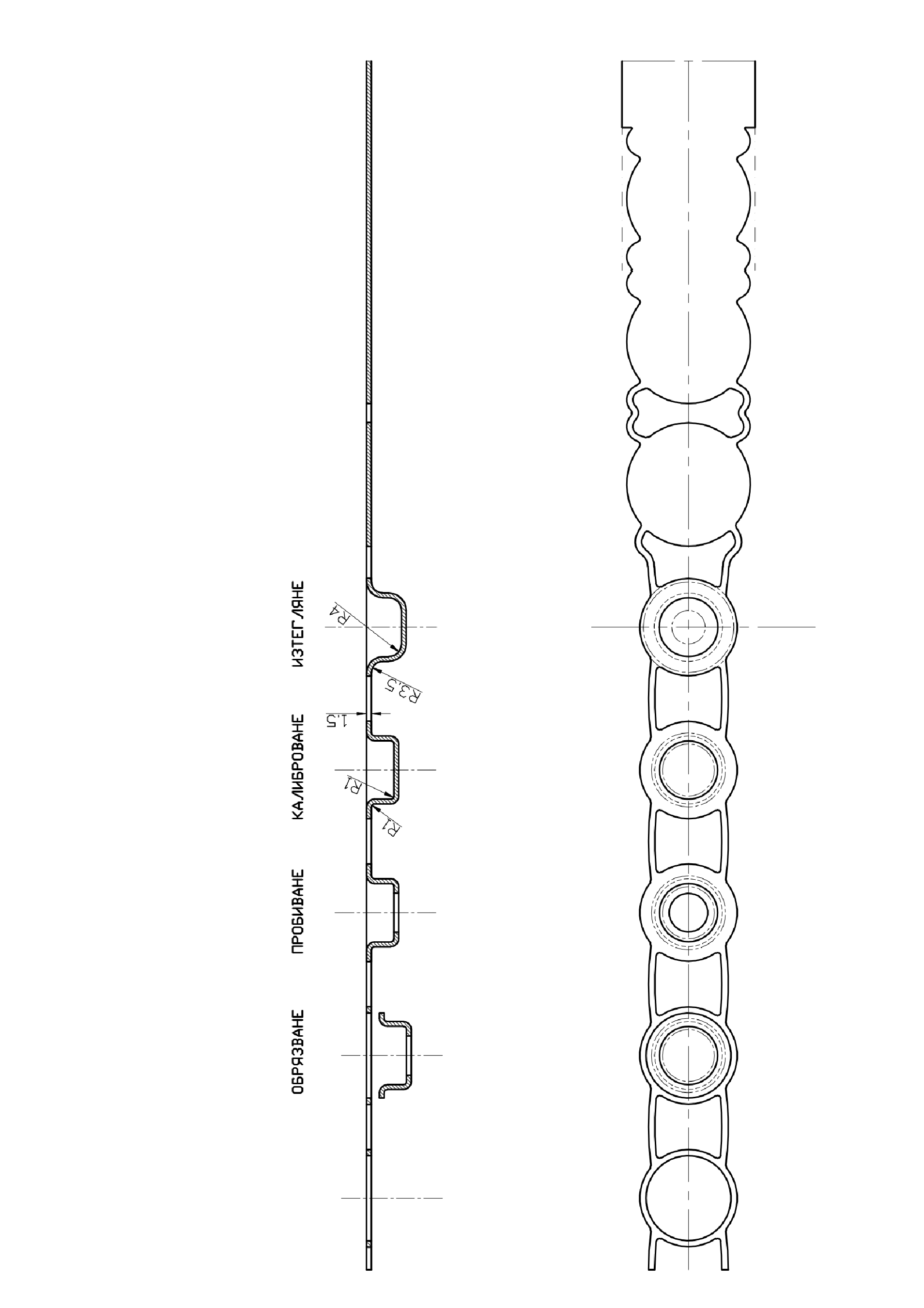
Фиг.3-8
6.4. Изтегляните детайли с форма на паралелепипед да имат радиуси на закръгление между стените и между тях и дъното не по-малки от посочените по-горе.
6.5. Допуските на размерите на изтегляните детайли да са по-големи от 0.5 пъти дебелината на материала, в абсолютна стойност по-големи от 0.2 mm. При това да са регламентирани само за вътрешния или само за външения диаметър.
6.6. Материалът на детайла да е подходящ за дълбоко изтегляне – с голяма разлика между граница на провлачане и якост на опън и висока стойност на относителното удължение. Повърхността да е подложена на специална обработка – „дресиране“ за премахване опасноста от поява на мрежа от видими следи след изтегляне („портокалова кора“).
6.7. В детайли със сложна форма, изискващи много операционно изтегляне, да са предвидени технологични бази за следващите операции.
7. Технологични изисквания към детайл от листов материал, получен чрез отбортоване:
7.1. Максималната височина при вътрешно отбортоване да не превишава 2,5-3 пъти дебелината на материала. Посочената стойност е ориентировъчна, допустимата височина се проверява за всеки конкретен случай. В противен случай ще се увеличи тройно броя на операциите и себестойността на детайла.
7.2. На отбортованите детайли да се задава само вътрешния диаметър. Поради наличие на неравномерно изтъняване на стената, външния диаметър се задава от конструктора на инструмента.
8. Технологични изисквания към детайл от листов материал, получен чрез релефно формоване:
8.1. Максималната височина на ребра, пъпки и формовани профили да не превишава 2,5 пъти дебелината на материала.
8.2. Краищата на усилващите ребра да не са разпложени на разстояние по-малко 3 пъти дебелината на материала от точни отвори или външия контур.
ГЛАВА 4. ИДЕЕН ПРОЕКТ НА ИНСТРУМЕНТИ ЗА ЩАНЦОВАНЕ - ИЗБОР И ОЦЕНКА НА ИКОНОМИЧЕСКИ ИЗГОДЕН ВАРИАНТ
1. Цел на идейния проект и задачи.
1.1. Целта на идейния проект на инструмента е избор (създаване) на подходящ технологичен процес за щанцоване и рационална конструкция на щанца (инструмента), позволяващи производство на детайли с оптимални за конкретните условия разходи.
1.2. Задачите, които трябва да се решат в идейния проект на инструмента са:
– избор на технологията на щанцоване – едно опeрационна, много операционна (последователна, съвместна, комбинирана);
– избор на последователност на щанцовите операции;
– избор на вида на изходна заготовка – лист, ивици от лист, лента на руло;
– изчисляване на разгъвка или изходна заготовка за изтегляне;
– създаване възможни схеми за щанцоване и избор на оптимална, на база максималното използване на материала от лентата или листа;
– избор на вида и конструкцията на щанцата;
– изчисляване на производствената и икономическата ефиктивност – предварителна себестойност (цена) на щанцования детайл;
– прогнозиране на разходите за изработка и пускане в експлоатация на инструменталната екипировка;
– подготовка на технико-икономическо задание или оферта за инструменталната екипировка и щанцования детайл.
2. Предварително проучване на съществуващите технически решения за щанцоване на подобни детайли.
Проучване на техническа и спpавочна литература – (виж препоръчана литература):
– чертежи на предишни щанци за близки по форма детайли;
– фирмени проспекти;
– отраслови и заводски нормали за типови схеми и конструкции;
– публикувани патенти;
– интернет сайтове;
– други общо достъпни източници (преса, радио, телевизаия).
3. Избор на аналози сред известните технически решения и създаване на базов вариант.
3.1. Избор на технологията на щанцоване.
3.1.1. Едно опeрационна – изпълнява се с прости инструменти, всеки от които е предназначен само за една операция (на пример за изрязрване на контура, за пробиване на отвори, за огъване, за изтегляне, за обрязване на фланец, за отбортоване на отвор и други).
Предимствата са проста конструкция и ниска цена на щанците. Недостатъците са ниска производителност, висока цена на щанцования детайл, не винаги може да се гарантира 100% качеството на продукцията. Подходаща е за малки серии на произвежданите детайли.
3.1.2. Много операционна – изпълнява се със сложни инструменти, всеки от които е предназначен за няколко операции (на пример за изрязрване на контура, пробиване на отвори и огъване на детайла):
– последователна – последоватено изпълнение на операциите на отделни позиции – стъпки (на пример пробиване на отвори за фиксиране на лентата, изрязване на две дъги по контура, първо изтегляне, второ изтегляне с калиброване, пробиване на отвор в дъното, обрязване на фланеца и отделяне на готовия детайл от лентата, отрязване на остатъка от лентата на парчета) - Фиг. 4-1:
– съвместна – едновременно изпълнение на операциите на една позиция – стъпка (на пример изрязване на контура на заготовката за изтегляне, първо изтегляне на детайла) - Фиг. 4-2;
– комбинирана – последоватено изпълнение на част от операциите на отделни стъпки, а някои от тях се изпълняват едновременно в една стъпка (комбинация между описаните по-горе видове).
Предимствата са висока производителност, ниска цена на щанцования детайл, високо качество на продукцията. Недостатъците са сложна конструкция, трудна подръжка и висока цена на щанците. Подходяща е за много големи серии на произвежданите детайли.
3.1.3. Система за изпълнение на операциите и подаване на заготовката.
– прогресивна (в лента) – отделните операции се извършват последователно или съвместно върху заготовката на отделни позиции, като предвижването на заготовката между позициите се извършва от самата лента чрез носещи мостчета (представляват технологичен отпадък), свързващи множество заготовки – например Фиг. 4-1;
– трансферна – отделните операции се извършват последователно или съвместно върху заготовката на отделни позиции, като предвижването на заготовката между позициите се извършва от специално подаващо устройство (грейферно или манипулатор на многопозиционни преси) - Фиг. 4-3;
– координатна – отделните операции се изпълняват последователно върху заготовката (най-често цял лист), която се позиционира спрямо инструмента (координатно) от масата на пресата (координатни преси с ЦПУ);
– ръчна – отделните операции се извършват последователно или съвместно върху заготовката на отделни инструменти, най-често монтирани върху различни преси.
Правилния избор на технология зависи от серийността на детайла и конкретните условия на производителя (налично пресово оборудване).
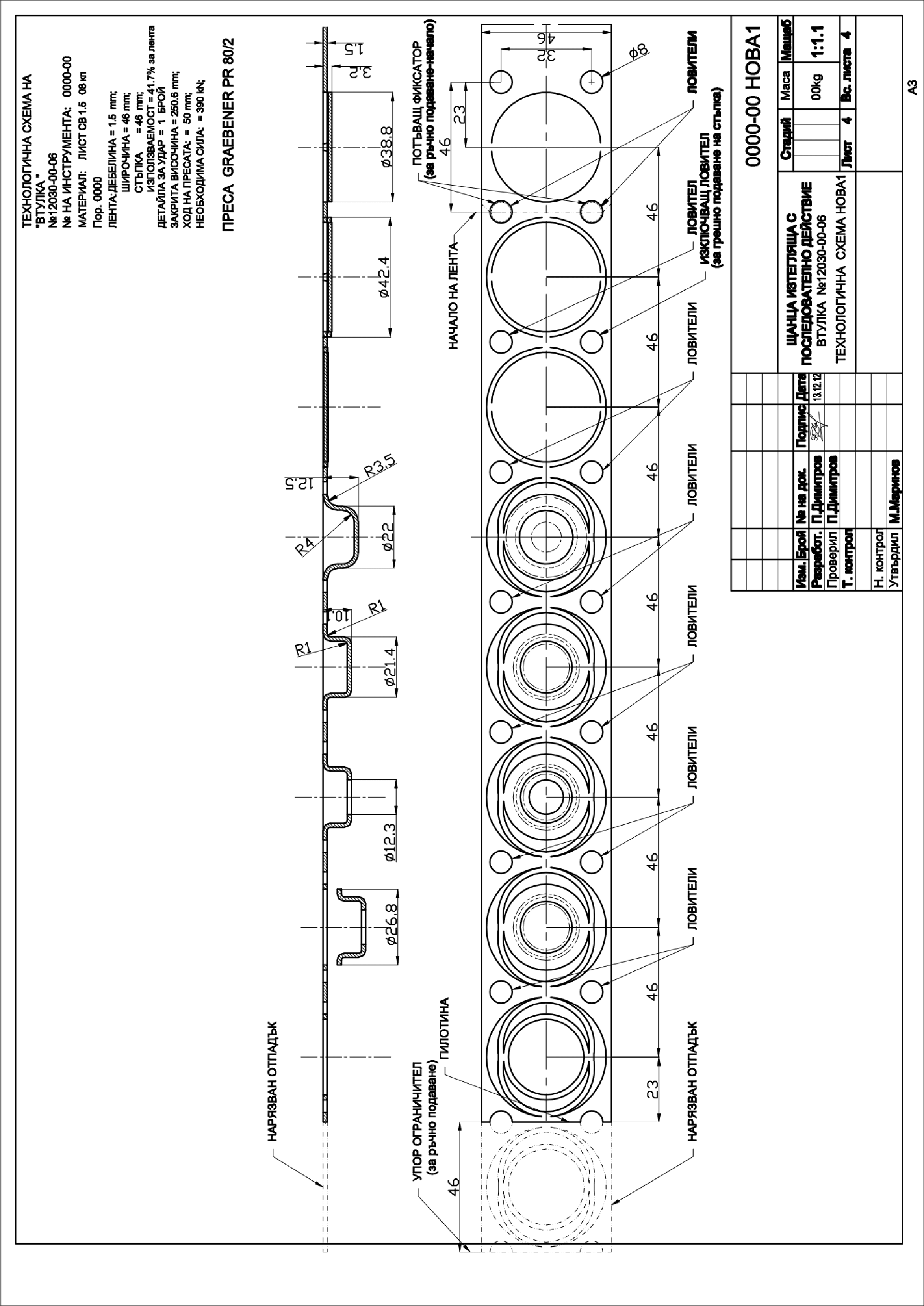
Фиг. 4-1
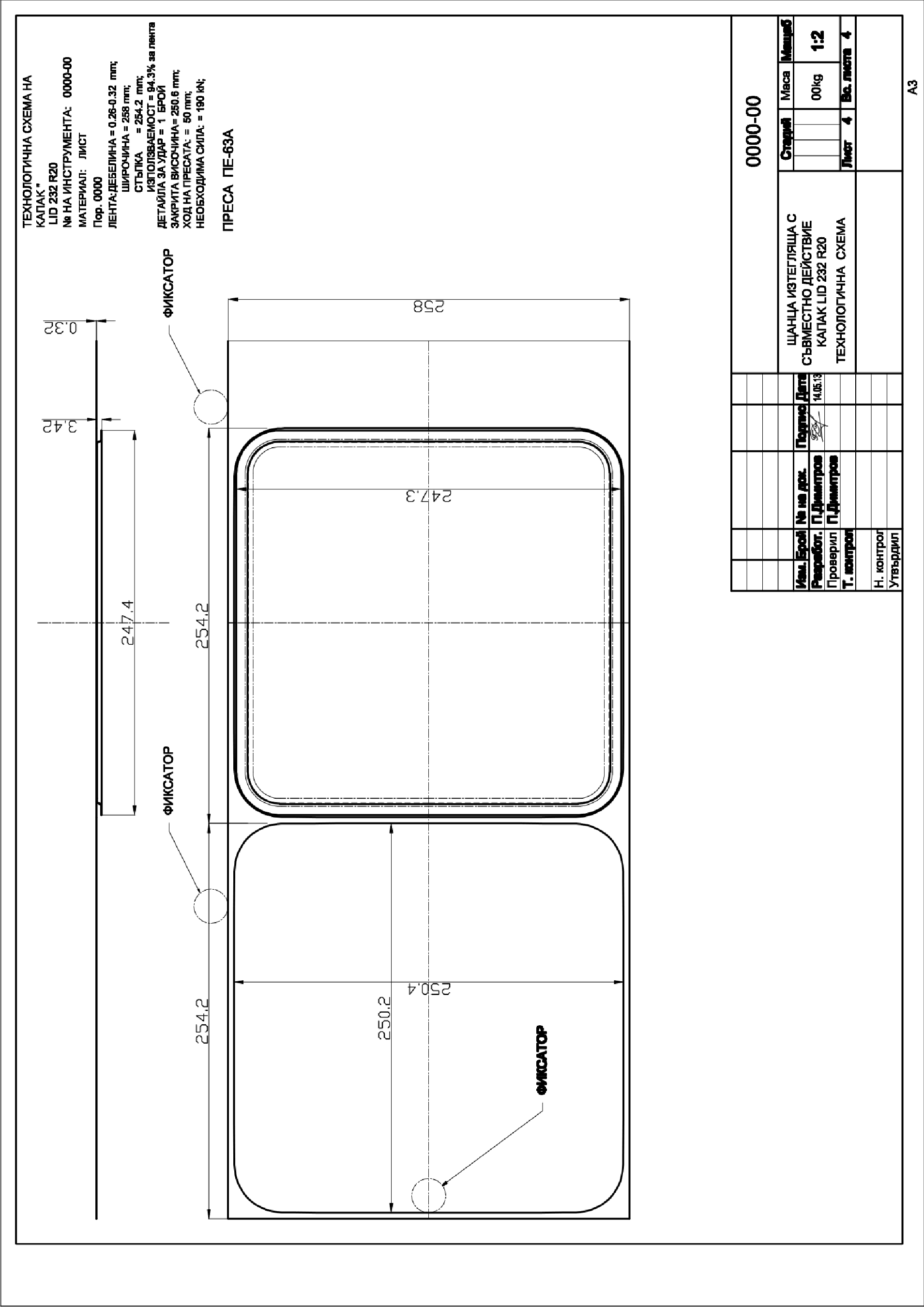
Фиг. 4-2
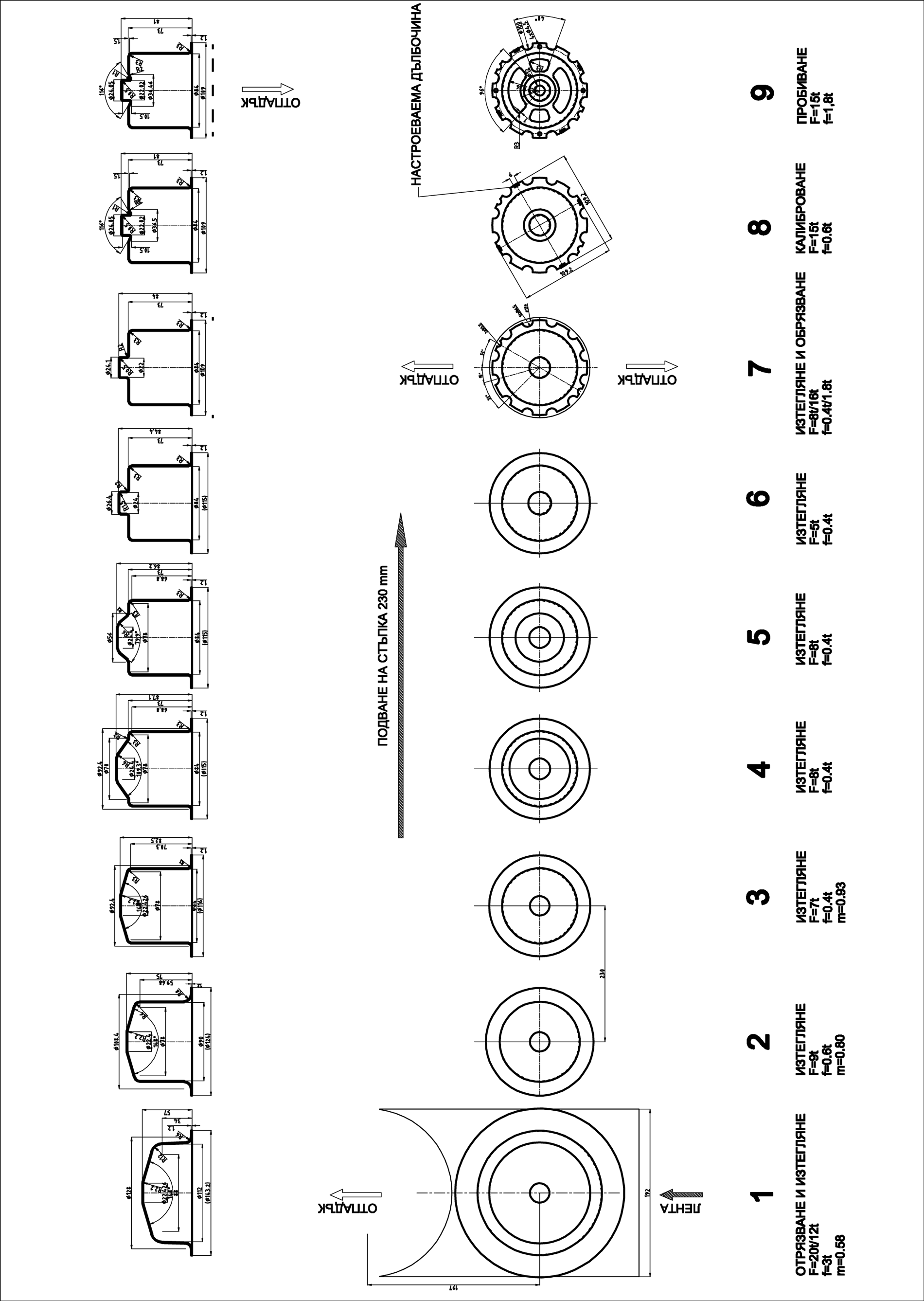
Фиг. 4-3
3.2. Избор на вида на изходния материал (заготовка).
3.2.1. Лента на руло;
3.2.2. Ленти, получени от разкрояването на листов материал на ивици с необходимата широчина;
3.2.3. Лист;
3.2.4. Единични заготовки, разкроени на гилотина или чрез други медоди (например лазерно изрязани).
Правилния избор зависи от серийността на детайла, наличното пресово оборудване и възможностите за доставка на конкретния материал.
3.3. Избор на последователност за щанцовите операции.
3.3.1. Определяне на необходимите щанцови операции за детайла;
3.3.2. Определяне на ограниченията за всяка операция на щанцоване – нейната изпълнимост и зависимост (на пример не трябва да се пробива точен отвор в област от заготовката, която впоследствие се огъва, изтегля, формова);
3.3.3. Определяне на реда (последователността) на щанцовите операции за детайла.
4. Извършване на предварителни технически и икономически изчисления.
4.1. Определяне на формата и размерите на разгъвката за щанцования детайл – при наличие на огънати части се пресмятят дължините при тяхното изправяне (състоянието преди огъване).
– разделяне на огъвките на прави участъци и дъги;
– изчисляване на дължините на дъгите, при отчитане изместването на неутралния слой (например с прилагане „К-фактор“);
– построяване на разгъвката за щанцования детайл.
4.2. Определяне на формата и размерите на изходната заготовка при изтеглен детайл – при наличие на изтеглени или отбортовани части се пресмятят размерите преди изпълнение на операцията (равнинно състоянието на заготовката).
– изчисляване на площта (за изтегляне без изтъняване на стената) или нa обема на щанцования детайл;
– добавяне на площта (за изтегляне без изтъняване на стената) или обема на технологичната прибавка за обрязване (ако е предвидена такова);
– изчисляване на размерите на равнинна заготовка от същата дебелина на материала, при отчитане равенството на площта или обема преди и след изтегляне;
– построяване на изходната заготовка за изтеглен или отбортован детайл.
4.3. Определяне на основните размери на лентата.
4.3.1. Изчисляване на широчината на лентата – към максималния размер на разгъвката или изходната заготовка (напречно на лентата) се прибавя минимално допустимата ширина на двете надлъжни носещите мостчета (необходим технологичен отпадък, гарантиращ здравина и устойчивост на лентата).
4.3.2. Изчисляване на стъпката на лентата – към максималния размер на разгъвката или изходната заготовка (надлъжно на лентата) се прибавя минимално допустимата ширина на напречното носещо мостче (необходим технологичен отпадък, гарантиращ здравина и устйчивост на лентата).
4.3.3. Определяне на разходната норма за детайла – представлява площта или обема от лентата, които са необходими за производство на един детайл. Изчисляват се като произведение на широчината на лентата по стъпката на лентата (за площта) или произведение на широчината по стъпката по дебелината на лентата (за обема). Теглото на разходната норма е обема по специфичното тегло на използвания материал. При многоредно разположение, разходната норма се разделя на броя на получаваните детайли в една стъпка на лентата.
4.4. Изчисляване на използваемостта на материала.
4.4.1. Изчисляване на коефициента на използване на материала за лента – площта, обема или теглото на детайла, разделени на площта, на обема или теглото на разходната норма;
4.4.2. Изчисляване на коефициента на използване на материала за лист – площта, обема или теглото на детайла, умножен по общия брой детайли от един лист, разделени на площта, обема или теглото на целия лист.
4.4.3. Анализ на коефициентите на използване на материала и избор на оптималния вариант – този с максимален брой детайли от един лист или лента има най-висока стойност - Фиг. 4-4.
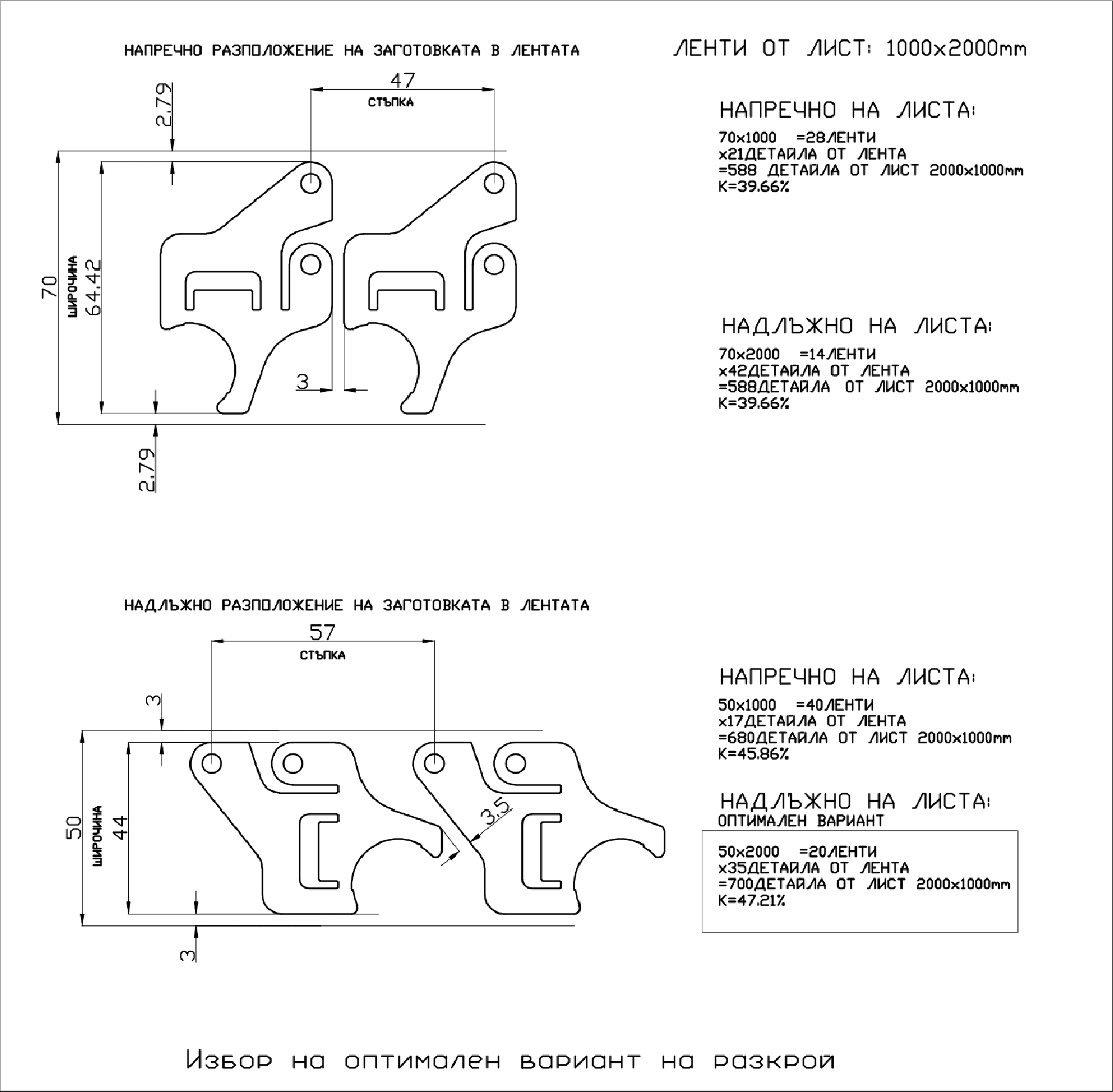
Фиг. 4-4
4.5. Изчисляване на себестойността на щанцования детайл.
4.5.1. Изчисляване на цената на материала – теглото на разходната норма умножена по цената на материала за килограм;
4.5.2. Изчисляване на средната производителност на щанцоване и цената за труд – средната производителност на инструмента за час умножена по часовата тарифна ставка, заплащана на работника.
4.5.3. Изчисляване на цената за покрития и термообработки (ако има) – околната повърхност на детайла умножена по специфична цена за единица площ на покритието.
4.5.4. Определяне на цената за кооперирани операции – обикновено са резултат на допълнителни запитвания към евентуални подизпълнители.
4.5.5. Изчисляване на цената за опаковка и транспорт – цената на опаковката (на пример картонена кутия) и разходите за нейното запълване и транспорт се разделят на броя детайли в нея.
4.5.6. Определяне на цената за общо заводски разходи – обикновенно те са определени като процент от общите производствени разходи на дадено звено (участък, цех, фирма) и отразяват всички не пряко включвани разходи, необходими за нормално производство. В този случай, със същия процент трябва да се увеличи изчислената себестойност.
4.5.7. Изчисляване на цената за амортизация на инструмента и пресата – цената на инструмента, разделена на необходимото количество детали за година, умножено по броя на годините за производство на този детайл. Ако произведението на количество детали за година и броя на годините за производство е по-голямо от ресурса на живот на инструмента (общия брой произведени детайли до бракуване на инструмента), то е необходимо да се включи цената на два или повече инструмента. Амортизацията на пресата се изчислява като се раздели счетоводно заложената годишна стойност на необходимото количество детали за година.
4.6. Изчисляване на максималните сили и работни ходове за щанцоване – те са необходими за избора на подходящи преси за всяка операция. Принципно, максималните сили се определят за всяка операция като произведение на якостта (или специфично налягане) на обработваемия материал и срязвана, огъвана, изтеляна, формована и т. н. площи, корегирани с поправъчни коефициенти за различните операции. Максималната сила е сума от максималните сили на отделните операци, извършвани в един същ момент, увеличена със спомагателни сили (пружини, буфери и други). Работните ходове ориентировъчно могат да се определят като височината на детайла се умножи по 3 (за огъване, изтеглене).
5. Изготвяне на технологични схеми на щанцоване.
Подготвя се чертеж на технологичната схема за щанцоване и спецификация на основните техническите параметри - Фиг. 4-5.
При едно операционна технология се съставя маршрут на операциите и технологични схеми на заготовките за всяка от тях - Фиг. 4-6.
6. Избор на конструкцията на щанцата.
Подготвят се габаритни монтажни чертежи на инструментите - Фиг. 4-7.
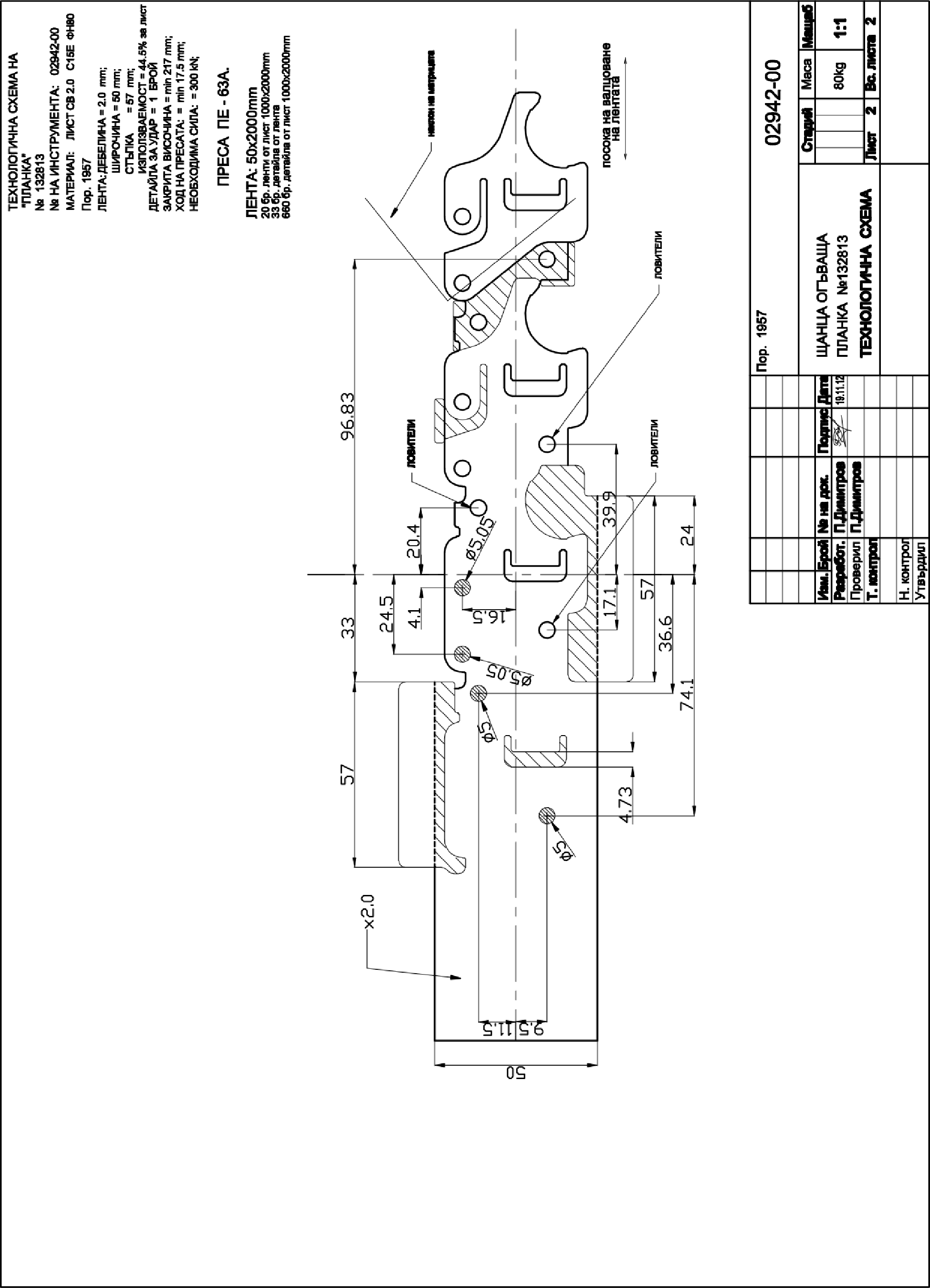
Фиг. 4-5
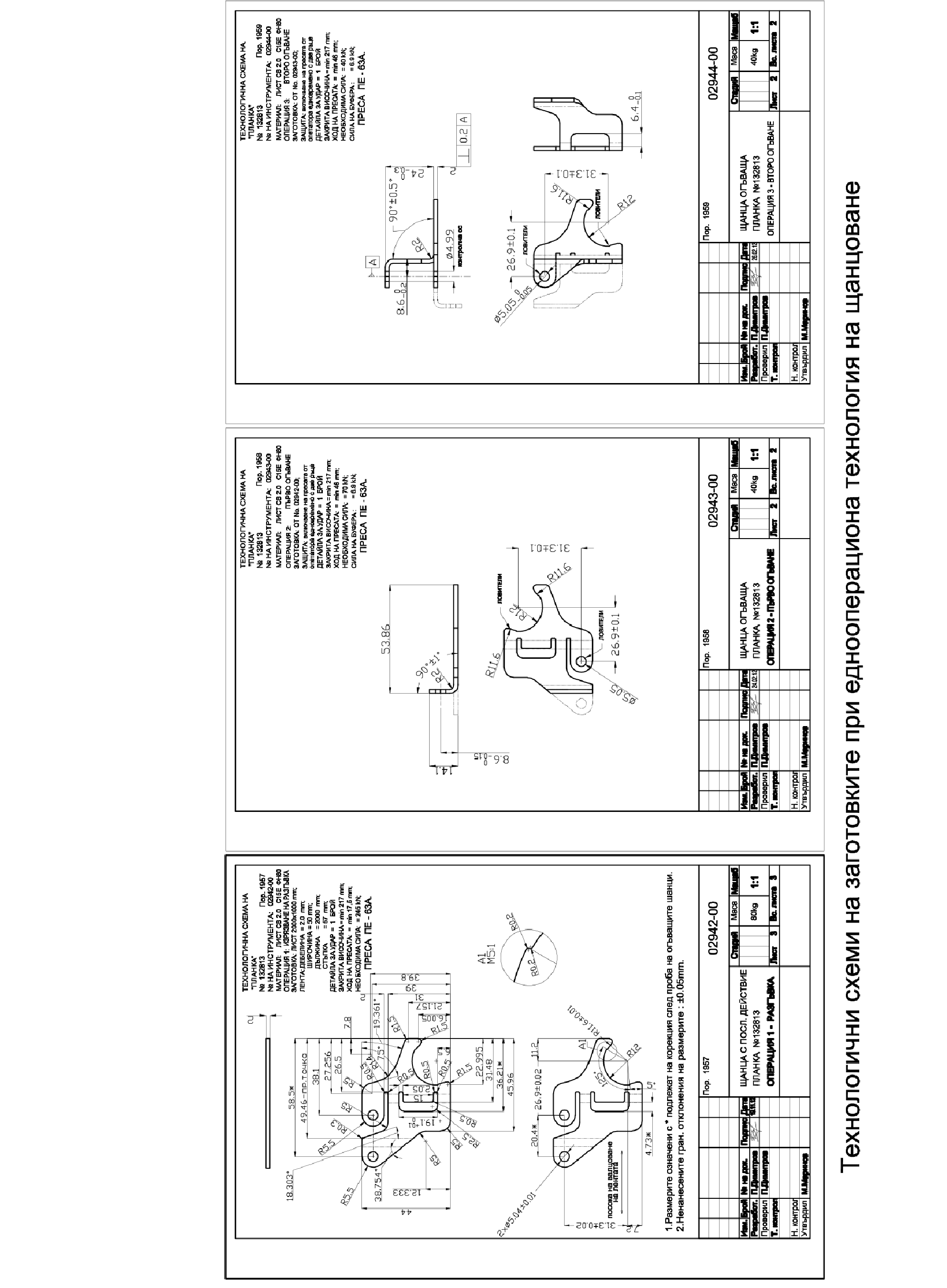
Фиг. 4-6
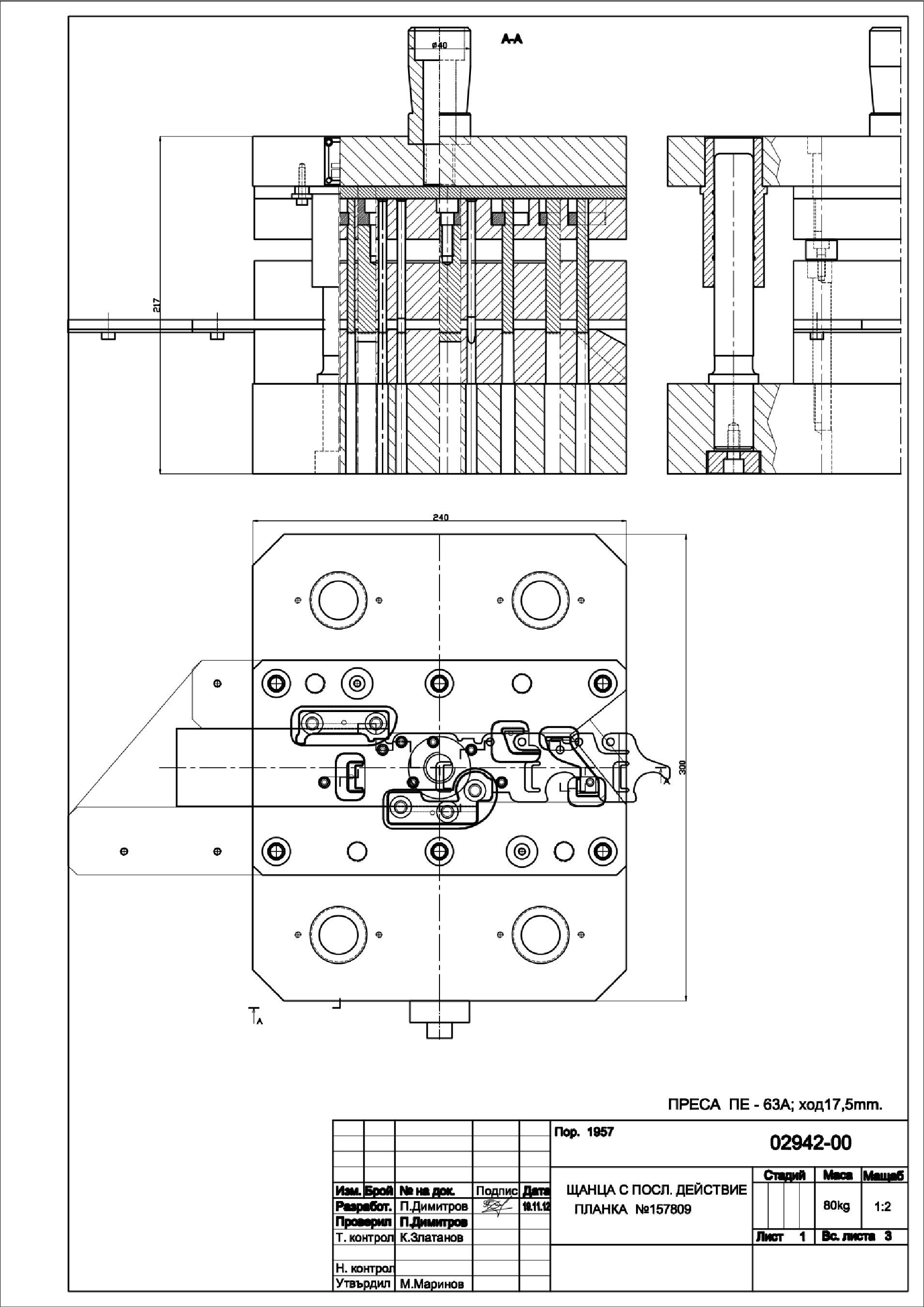
Фиг. 4-7
7. Предварителна оценка на разходите за проектиране и изработка на инструментите.
7.1. Определяне на приблизителната трудоемкост на инструментите в часове.
Тя се умножава по средната цена за час (средната часова тарифна ставка, увеличена с процента на общите производствени разходи).
7.2. Определяне на стойноста на вложените материали в инструментите.
Тук се включва и цена на всички готови или кооперирани части, възли, услуги.
7.3. Прогнозиране на цените на инструментите.
Цените на инструментите и разходите за тяхното пускане в производство (те ще се включат в изчисленията по т.4.5.7) - Фиг. 4-8 .

Фиг. 4-8
8. Съставяне на техническо задание или оферта за щанцоване на детайла и цена на инструменталната екипировка.
Техническото задание за щанцоване на детайла уточнява технологичната последователност на операциите, размери и вид на изходните заготовки или лента с разходна норма за производство, количеството едновременно произвеждани детайли, възможните производителности и трайност на инструментите, вида на пресите и режима на работа (ръчен, автоматичен), вида и конструктивни особености на инструментите (щанците), наличие на резервни части, обема и вида на комплектоващата конструктивна, технологична и експлоатационна документация. Подготовката на технологични схеми с основни данни и чертежи на заготовки улеснява разработката и допълва техническото задание. Техническото задание и офертата позволяват да се дефинира еднозначно технологичния процес, използваните щанцови инструменти и цената на произвежданите с тях детайли - Фиг. 4-9. Mного често идейният проект на инструмента не се изпълнява в пълния обем, разгледан по-горе, поради единичния характер на инструменталното производство, липса на време и компетентност, или несигурността, дали ще се стигне до поръчка. Минималното съдържание на техническото задание или офертата се свежда до броя, вида на инструментите и тяхната цена. В такъв случай всички действия от т. 2 до т. 6 (без т. 4.5) трябва да се изпълнят при работния проект, защото са необходими за конструирането на инструмента.
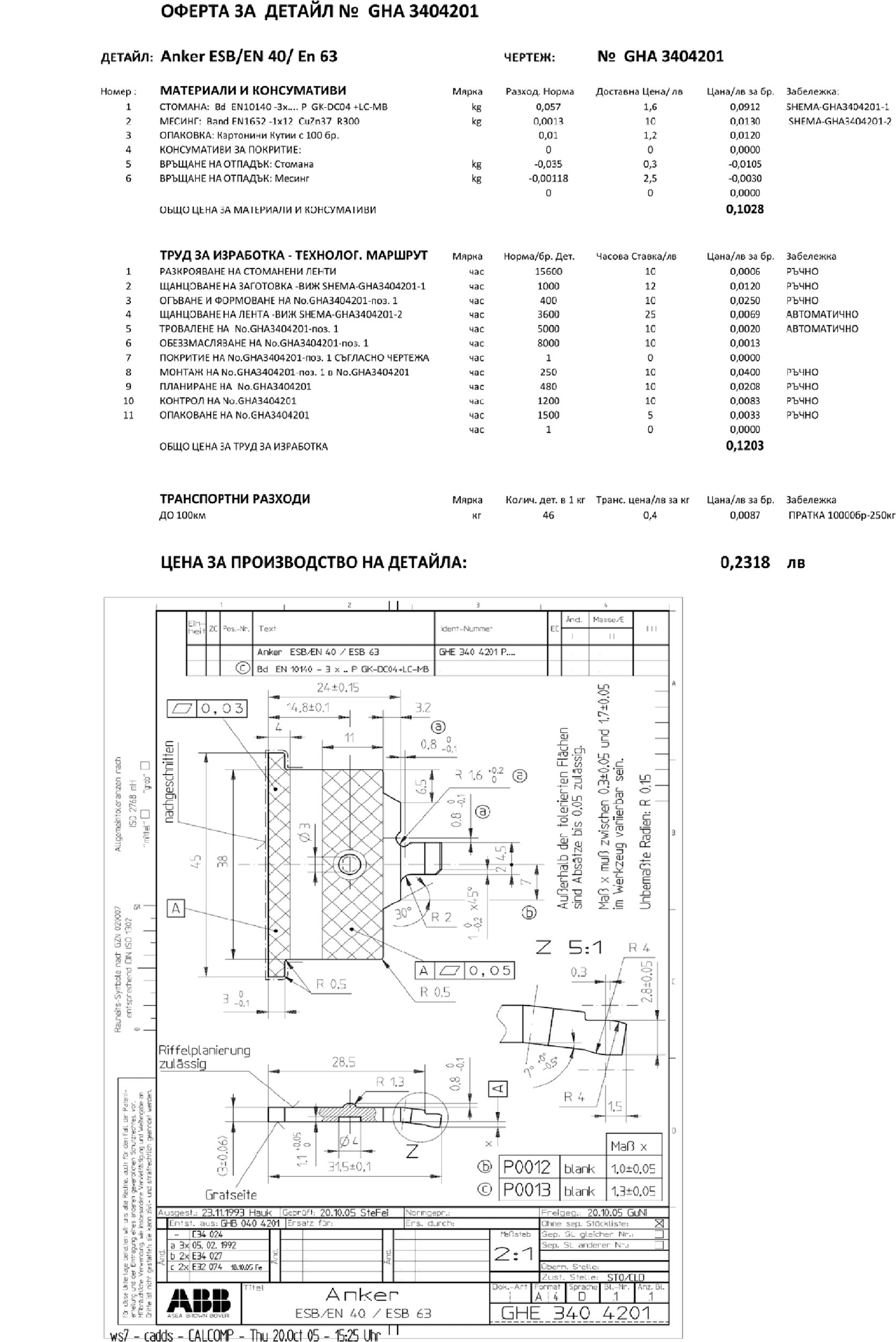
Фиг. 4-9
ГЛАВА 5. РАБОТЕН (ТЕХНИЧЕСКИ) ПРОЕКТ - ПРОЕКТИРАНЕ НА ТЕХНОЛОГИЧНИ ПРОЦЕСИ И СХЕМИ НА РАБОТА, ТЕХНОЛОГИЧНО - СИЛОВО - ЯКОСТНО ИЗЧИСЛЯВАНЕ, КОНСТРУИРАНЕ И ИЗЧЕРТАВАНЕ НА СБОРНИ И ДЕТАЙЛНИ ЧЕРТЕЖИ НА ИНСТРУМЕНТИ ЗА ЩАНЦОВАНЕ, ТЕХНОЛОГИЧНО ОСИГУРЯВАНЕ НА ИЗРАБОТКАТА ИМ
1. Цел и задачи на работния проект.
1.1. Целта на работния проект на инструмента:
Създаване необходимите модели, конструктивна, технологична и експлотационна документация на щанците, позволяващи тяхната изработка и правилна експлоатация.
1.2. Задачите, които трябва да се решат в работния проект на инструмента са:
– проверка, допълване или частична промяна на технологичния процес на щанцоване – необходими операции, последователност, технологични схеми и заготовки, ракрояване на материала, изчисление на възникващи сили и необходими ходове, уточняване необходимостта от притискащи, подаващи, пакетиращи, отделящи или други допълнителни устройства (в някои случаи тяхното проектиране), окончателен избор на преси;
– създаване модел на конструкция на щанцата – избор и разработка на активни, технологично необходими и спомагателни части, геометрични, кинематични, якостни и деформационни изчисления, точностни анализи на допуски на затварящи звена;
– разработка на конструктивна документация за изработка – сборни чертежи, спецификации на оригинални и покупни детайли, работни чертежи на оригиналните части;
– технологична подготовка за изработка – анализ на технологичността и изпълнимостта на конструкцията и отделните детайли в конкретните условия (наличен машинен парк и квалификация на персонала), избор на технологични процеси и създаване маршрутна операционна технология за активните части (желателно за всички оригинални детайли от чертежа), разработка на управляващи програми за използваните металообработващи машини, създаване на три или дву – измерни модели за електроди или други инструменти и приспособления от втори порядък, необходими за изработката с маршрутна операционна технология за тях;
– създаване инструкции за правилна експлоатация и техника на безопасност на щанцата, инструкции и схеми за настойка и проби (когато е необходимо).
Важно условие за съдаване на добри инструменти е многопластовото разглеждането на всяка от решаваните задачи за технологичен процес на щанцоване, за конструкции на щанците, за възможностите на тяхната изработка, отчитайки очакваното въздействие върху останалите задачи и промяна на подхода или решението, когато е необходимо. Задачите на работния проект обикновено предлагат многовариантни решения. От тях трябва да се изберат тези, които позволяват съвмесно решение на всичките задачи. На пример, добре създадени процес на щанцоване и инструменти не трябва да влизат в противоречие с възможностите за изработка на щанците или за тяхната поддръжка при експлоатация.
2. Проверка и допълване на технологичния процес на щанцоване.
2.1. Проверка и анализ на технологичните операции.
Разработката на технологичен процес при идейния проект обикновенно е предварителна. При нея не могат да се предвидят фактори, зависещи от конструкцията на самия инструмент. На пример, в технологичната схема при конструктивно решение за вложкова матрица е възможно, заложеното разтояние между позициите на предвидените операции, да не е достаъчно за вложки с необходимата дебелина на стената - Фиг.5-1.
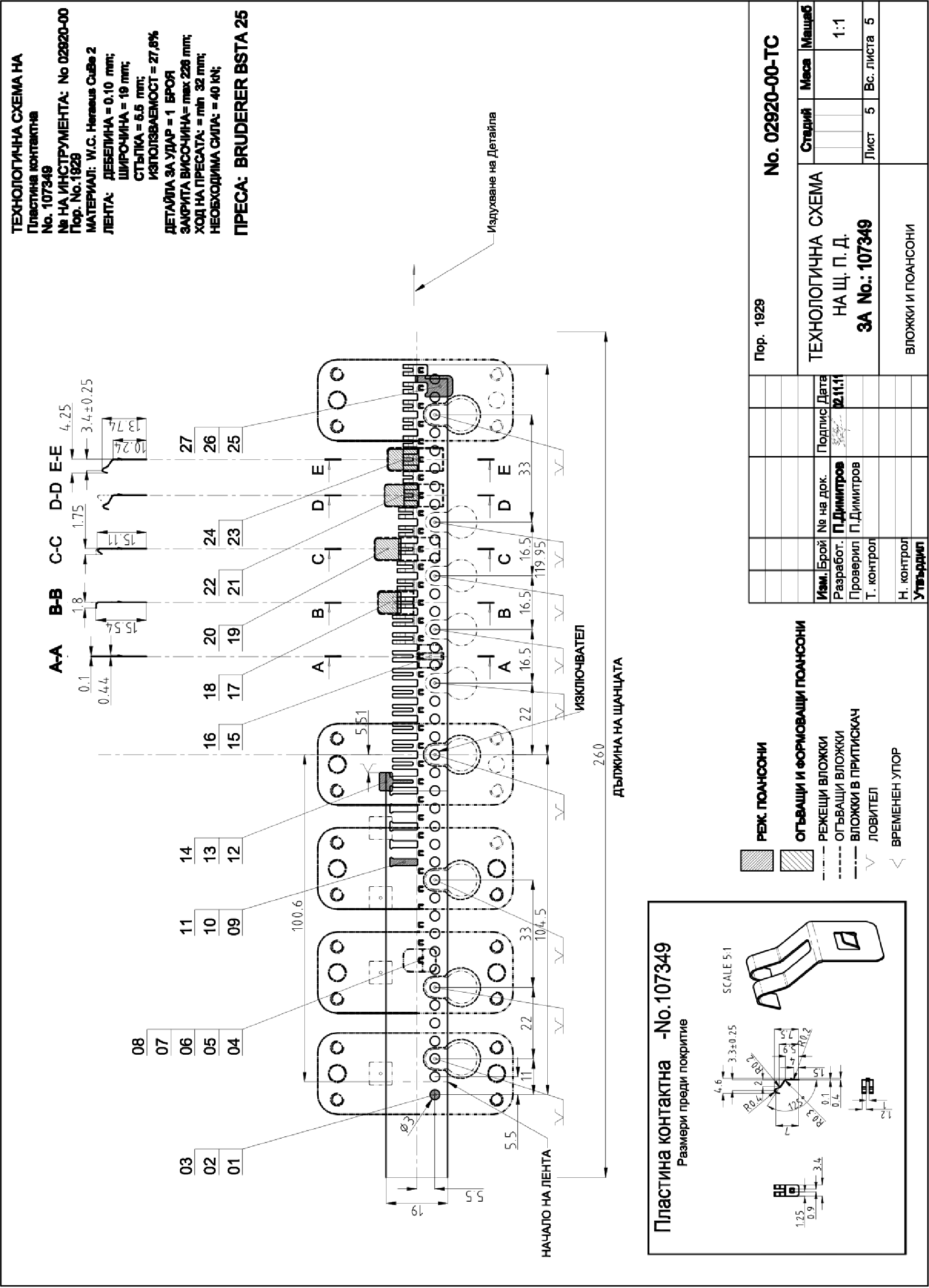
Фиг.5-1
Затова е важно, технологичните операции, схеми и заготовки да се допълват и променят преди изграждането на конструкция на инструмента. Чрез извършения анализ може да се разкрият рискови ситуации, които изискват промяна в технологичния процес. Като пример за необходимост от промяна е технологичният процес, предвиждащ получаване на готов огънат детайл Фиг.5-2
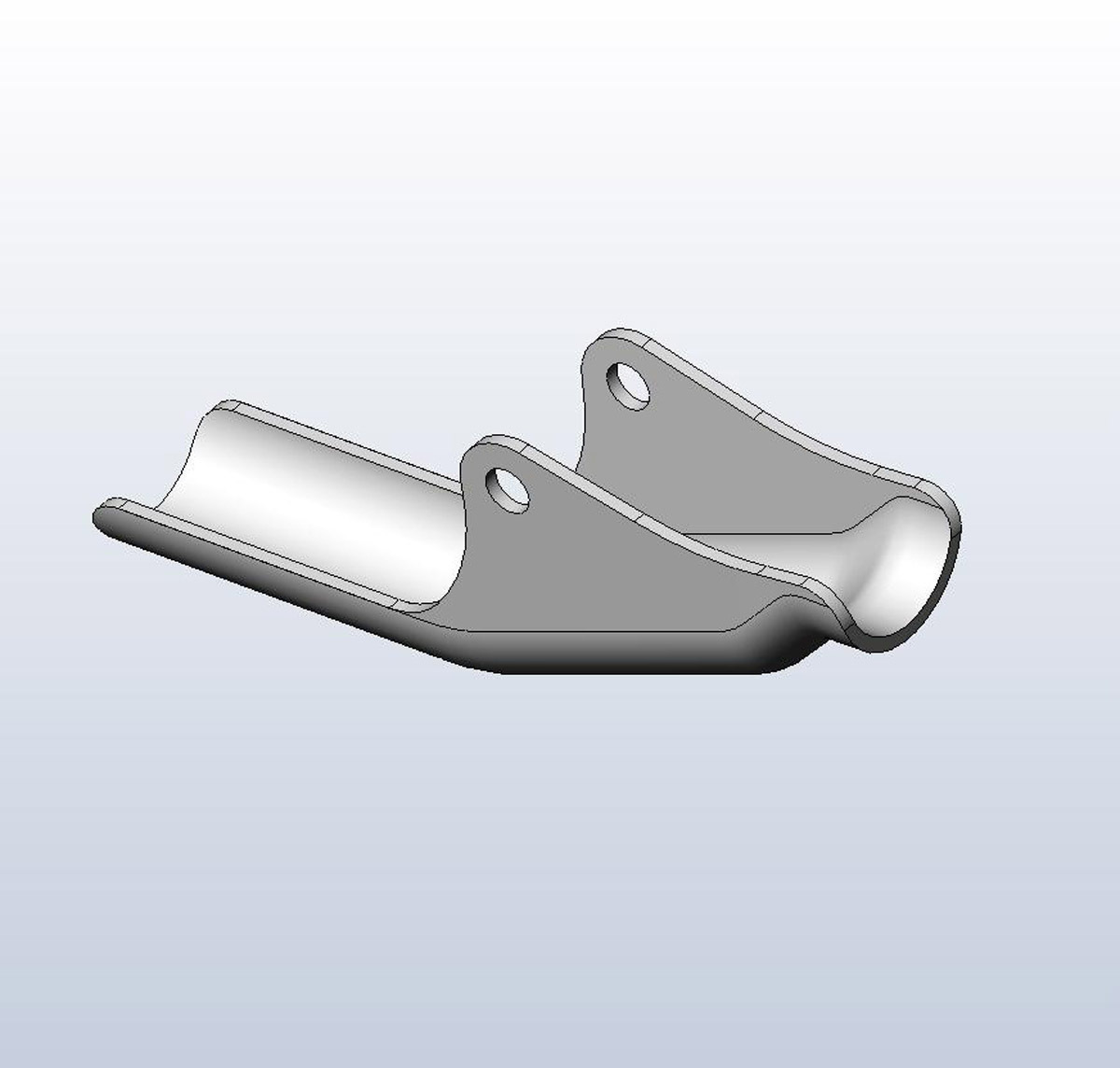
Фиг.5-2
от плоска заготовка Фиг.5-3.
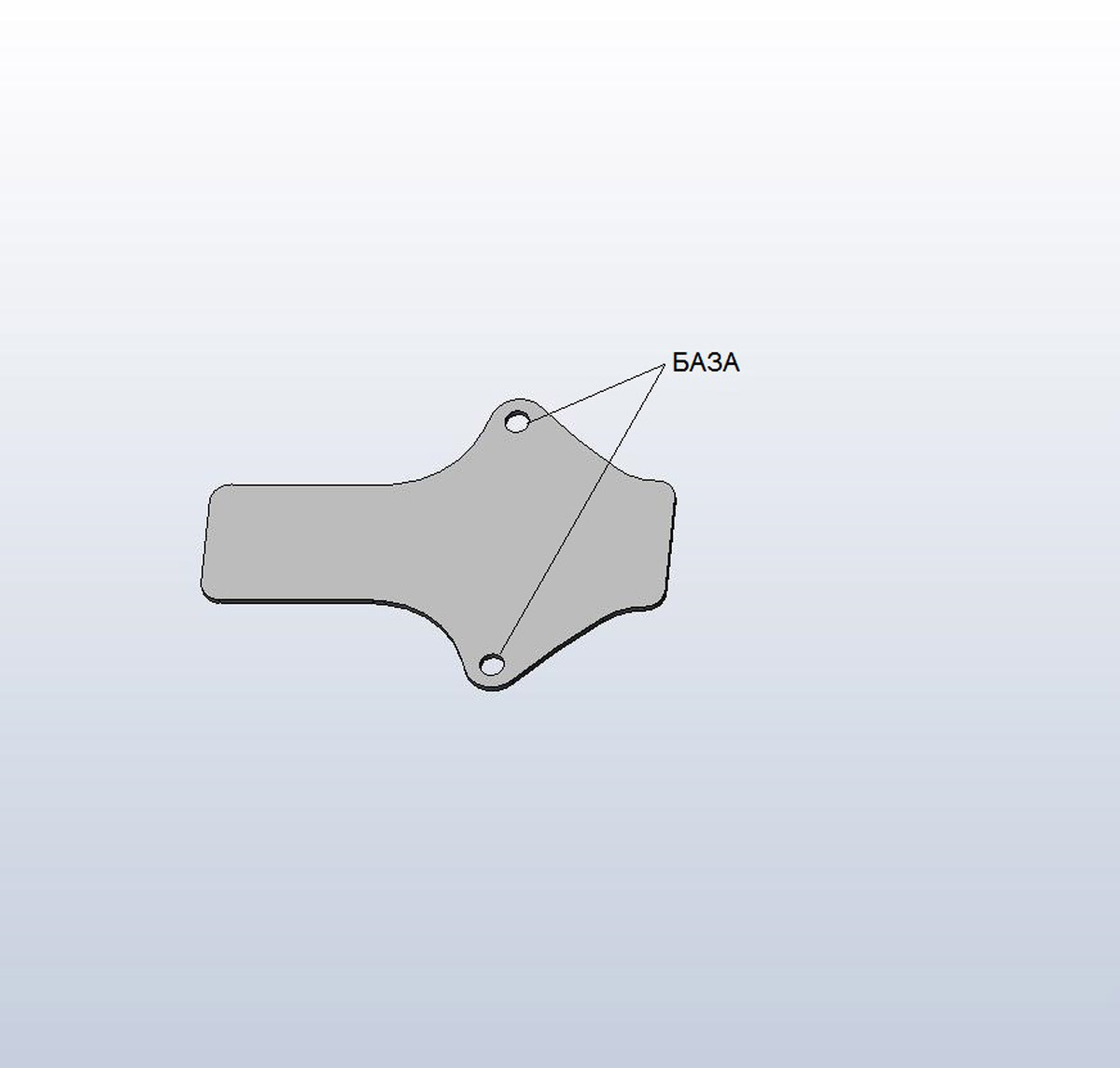
Фиг.5-3
Заложено е за бази да се използват двата отвора. Формата на детайла обаче, изисква пространствено огъване в две равнини, надлъжното от които е не симетрично. Анализът показва, че при огъването на рамената отворите ще излязат от контакт с базиращите части малко след началото, поради което е задължително добро притискане през целия процес. Такова не може да се осигури при използване на плоска заготовка. Извършването на несиметричното надлъжно огъване едновременно с напречното, след освобождаване от базиращите части ще доведе до изместване и не съосие на отворите. Това налага промяна на технологичния процес чрез въвеждане на допълнителна операция за предварително огъване - Фиг.5-4,
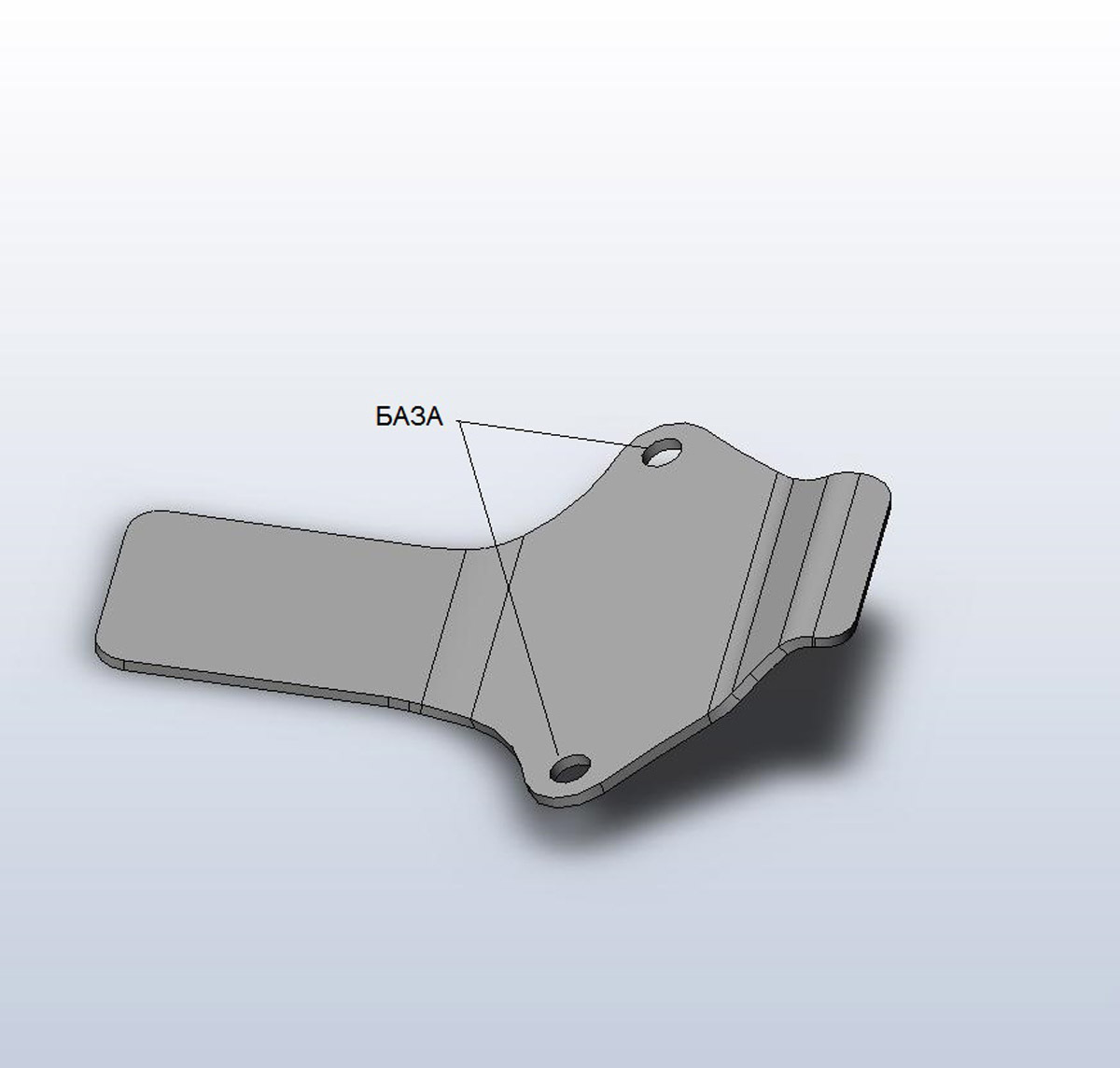
Фиг.5-4
което ще се изпълни при непрекъснат контакт на отворите с базиращите части. Наслагването на предварително огънатата заготовка с крайния детайл показва, че е възможно притискане през целия процес на окончателно огъване - Фиг.5-5.
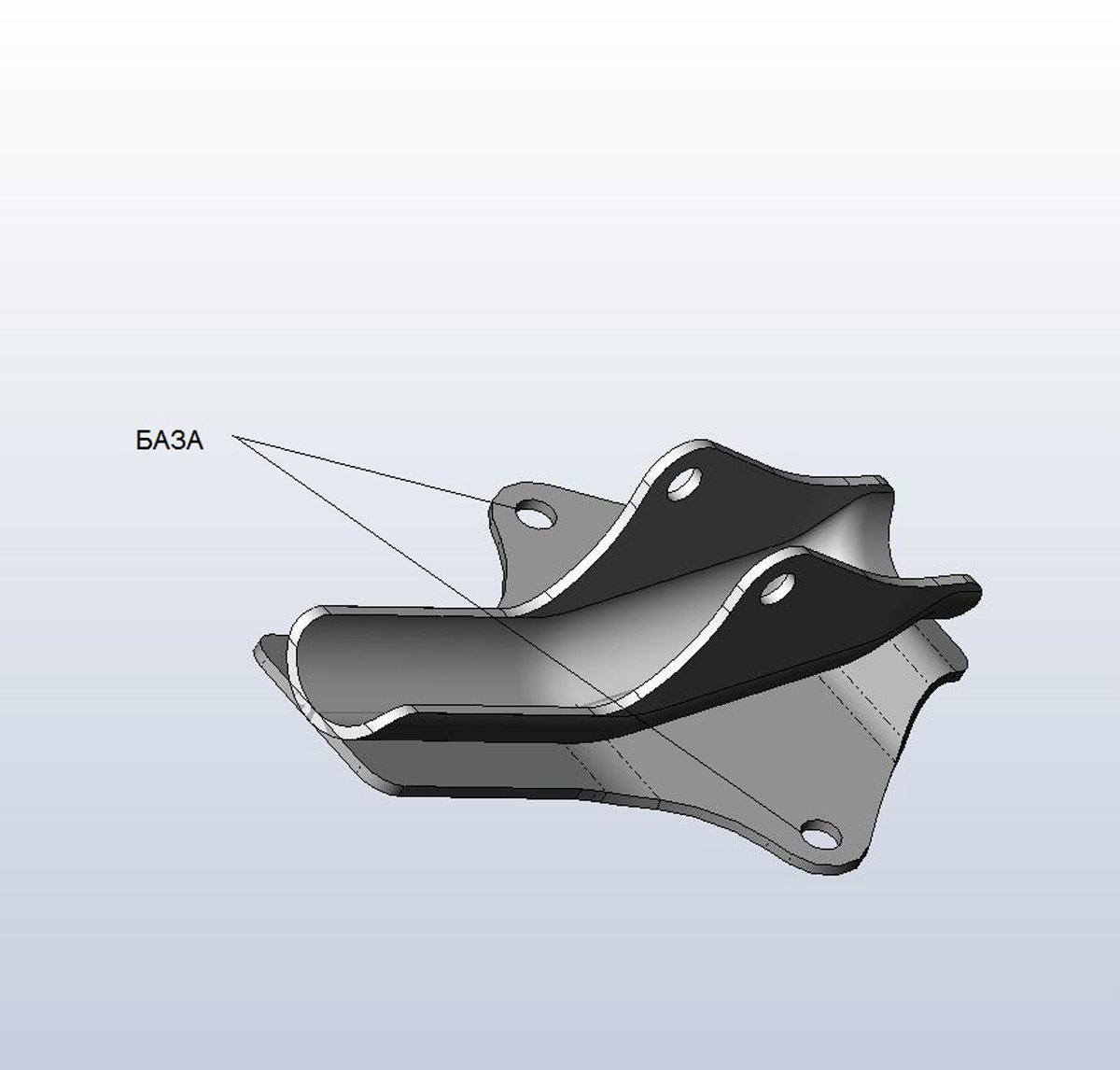
Фиг.5-5
2.2. Последователност при разработка на технологичните схеми.
Избраният технологичен процес, разделен на операции и използвани инструменти и заготовки, е известен от идейния проект. Предстои избор на технологична схема за получаване на изходната заготовка. Основните принципи при разработка на технологична схема са:
– Равниност на лентата от начало до край на технологичните преходи;
– Единство на базите за всеки технологичен преход, когато е възможно;
– Сигурно водене, позициониране, фиксиране, технологично въздействие и изваждане на заготовката за всеки технологичен преход;
– Гарантирано извеждане от инструмента на отпадъците от лентата;
– Разделяне на отпадъка от готовите детайли.
За пример на последователността при получаване на плоска заготовка - Фиг.5-6 е избран детайл „Планка“ от Фиг.3-5.
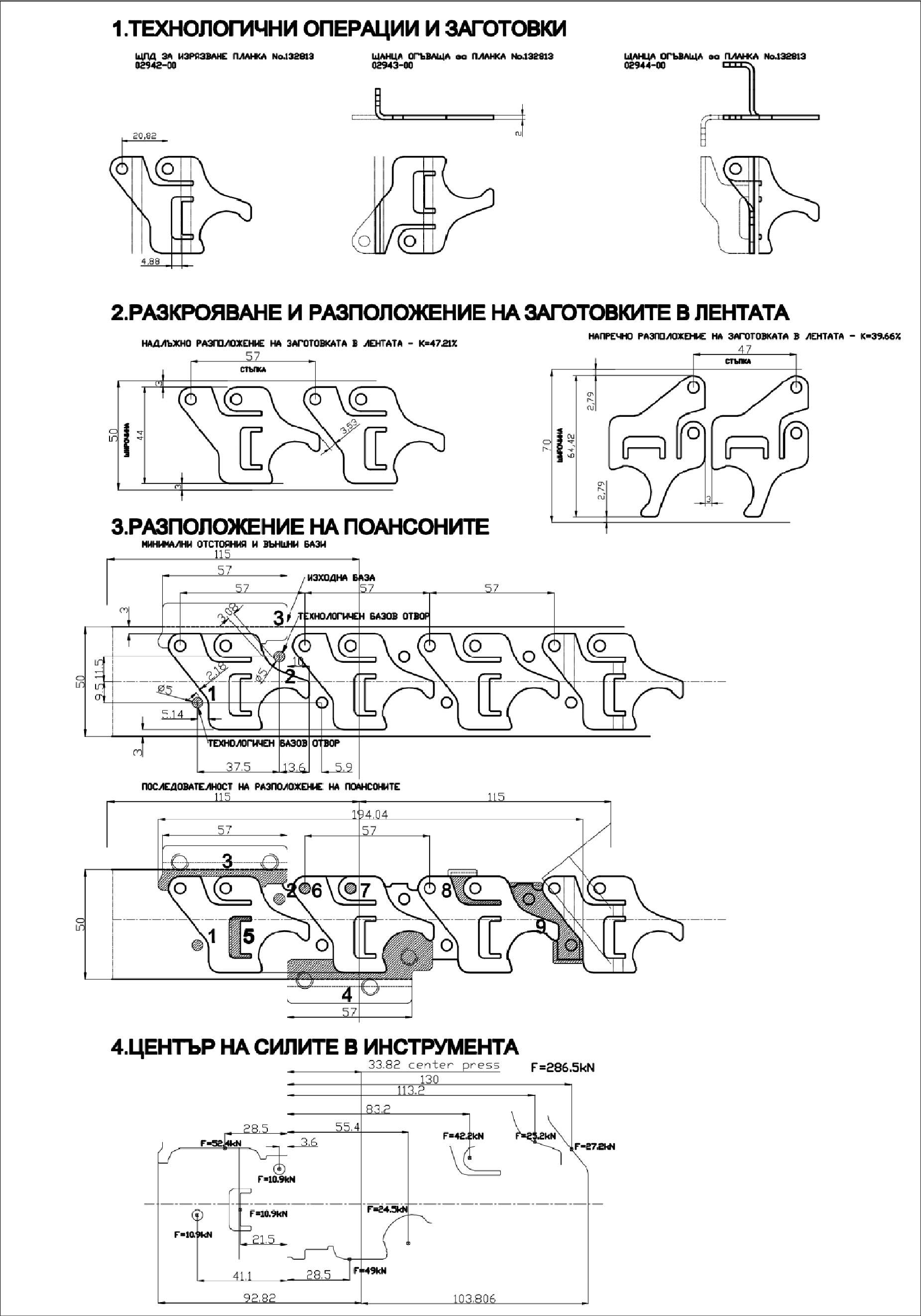
Фиг.5-6
Задачите се решават в в следния ред:
2.2.1 Изходни данни за разработка на технологичната схема са заготовките за отделните технологични операции.
2.2.2. Следващата задача при разработка на технологичната схема е избор на материал и разположение на заготовките в лентата. Големината на серията и дебелината на детайла определят използване на стандартен лист, разкроен на ленти. Съществуат много възможни решения за разположението на детайла в лентата и размерите на самите ленти.
В случая, избора на оптимален вариант е извършен на база получаване на максимален брой годни детайли от един лист (виж Фиг.4-4). Разположението може да се опише математически с коефициента на използване на материала за лента или лист Ако всички възможни разположения на детайла и техните коефициенти на използване описват някъква непрекъсната функция, то нейния максимум определя оптималното разположение. Коефициента на използване достига най-висока стойност. Разбира се, не е оправдано да се изчисляват всички възможни стойности. В практиката е достатъчно да се разгледат основните възможни разположения и от тях да се избере този с най-висок коефициент на използване на материала. С това са определени широчината, стъпката и дължината на лентите за оптималния вариант.
2.2.3. Определяне на формата и раложението на поансоните е следваща стъпка при разработка на технологичната схема. Тя определя последователноста на технологичните преходи, точноста на получената заготовка, силовото натоварване в конструкцията, нейната надеждност и удобство при експлоатация. Първоначално се избират бази – възможно е да се използват отвори или участъци от самата заготовка (вътрешни) или да се предвидят допълнителни в отпадъчната част на лентатата (външни). Избраните бази ще определят точността на центроване на заготовката във всяка позиция. Затова е задължително да се използват едни и същи бази винаги, когато е възможно. Така избраните елементи се проверяват за отсъствие на критично малки разстояния до други профили, които ще доведат до неустойчива лента или слаби сечения в матрицата. Следва избор на изрязван контур или част от него, избор на форма на поансона и разположение в технологичната схема. Избраното разположение определя физическата последователност на преобразуване на лентата в готов детайл или заготовка.
За разгледания пример Фиг.5-6 са избрани външни бази – отвори за ловител и издаден участък от лентата, изрязван с профилен поансон-стъпков нож. Избора на външни отвори тук не е случаен. Вътрешните отвори са в двете огънати рамена и получаването на съосие между тях е малко вероятно да стане още с първата проба. Вероятността да се наложи промяна на разтоянието между тях и съответна корекция в инструмента ще доведе до много повече труд, ако те са използвани за база. В съответствие с принипа за единство на базите, са предвидени нови отвори, които ще се използват до изпълнение на посления технологичен преход в лентата. Изходната база е профилен поансон-стъпков нож, изрязващ част от детайла и оформящ стъпало в лентата, което ще ограничава до упор ръчно подаваната лента, без да увеличава отпадъка. Готовият детайл (заготовка за следващите операции) ще се отделя от лентата чрез изрязване на свързващия отпадък с поансон №9 и ще се плъзга по наклонена част от матрицата. Тази схема е подходяща поради размерите и теглото на детайла. Тя запазва равниността и не позволява да се смесват готови детайли с отпадъци.
2.2.4. Определяне на центъра на равнодействащата сила. Това е точката, около която сумата на моментите от всички сили е равна на нула. Практически, в нея или близо до нея, трябва да е разположен центъра на пресата (равнодействащата сила), за да се минимизира страничното натоварванне от огъващи моменти върху поансони, водещи части на инструмента и плъзгача на пресата. При технологична схема само с разделителни операции, този център може да се определи графично като център на тежест на система от линии или площи. Такова опростено определяне е приблизително и е изградено на допусканията, че силите възникват в един и същ момент (при една и съща дълбочина на проникване на поансоните) и са еднакви за единица дължина на режещия ръб за всички поансони. В действителност, силите и дълбочината зависят в голяма степен от отношението на дебелината на материала и размера на конкретния детайл и затова трябва много внимателно да се използва това опростяване.
Крайният вариант на технолочна схема за плоската заготовка на детайл „Планка“ е показан на Фиг.4-5.
Последователността при разработка на технологичните схеми на комбинирани инструменти с последователно действие за разделителни и формоизменящи оперции добавя допълнителни задачи към разгледаните по-горе:
2.2.5. Определяне плоските разгъвки на огъващи, изтегляващи, отбортоващи преходи. Избира се броя на преходите за огъване или изтегляне и се оределят техните размери. Освен размерите се приемат и подходящи форми на изрязване, за да се гарантира свободна деформация в необходимата посока.
2.2.6. Определяне на възможната последователност на формоизменящите преходи на огънати, изтеглени, отбортовани части в общата технологична схема и оптималното им местоположение. Правилната последователност изисква изпълнението им да се извършва след приключване на режещи преходи, освобождаващи деформираните зони. Препоръчително е, тези режещи преходи да се извършват в плоската лента (ако е възможно), за да се опростят матриците и притискачите.
2.2.7. Избор на свързващи части с лентата, носещи зони за повдигане, водене и притискане, които не създават конфликти за никой от технологичните преходи. На пример, зони за повдигане и водене не трябва пресичат огънати на долу рамена, защото конструктивните елементи в тях (повдигачи и водачи) няма да позволят свободно преминаване на рамената.
2.2.8. Нарязване на отпадъчната част от лентата, ако е необходимо (ленти на руло). Това условие е характерно за работа в автоматичен режим и е единствената алтернатива, когато отпадъчната лента не се навива на ролка (дебел материал или липса на такава възможност на пресовото оборудване).
Пример за технологична схема на комбиниран инструмент с последователно действие за разделителни, огъващи и маркиращи оперции за изработка на детайл INCISIVO, е показан на Фиг.5-7.
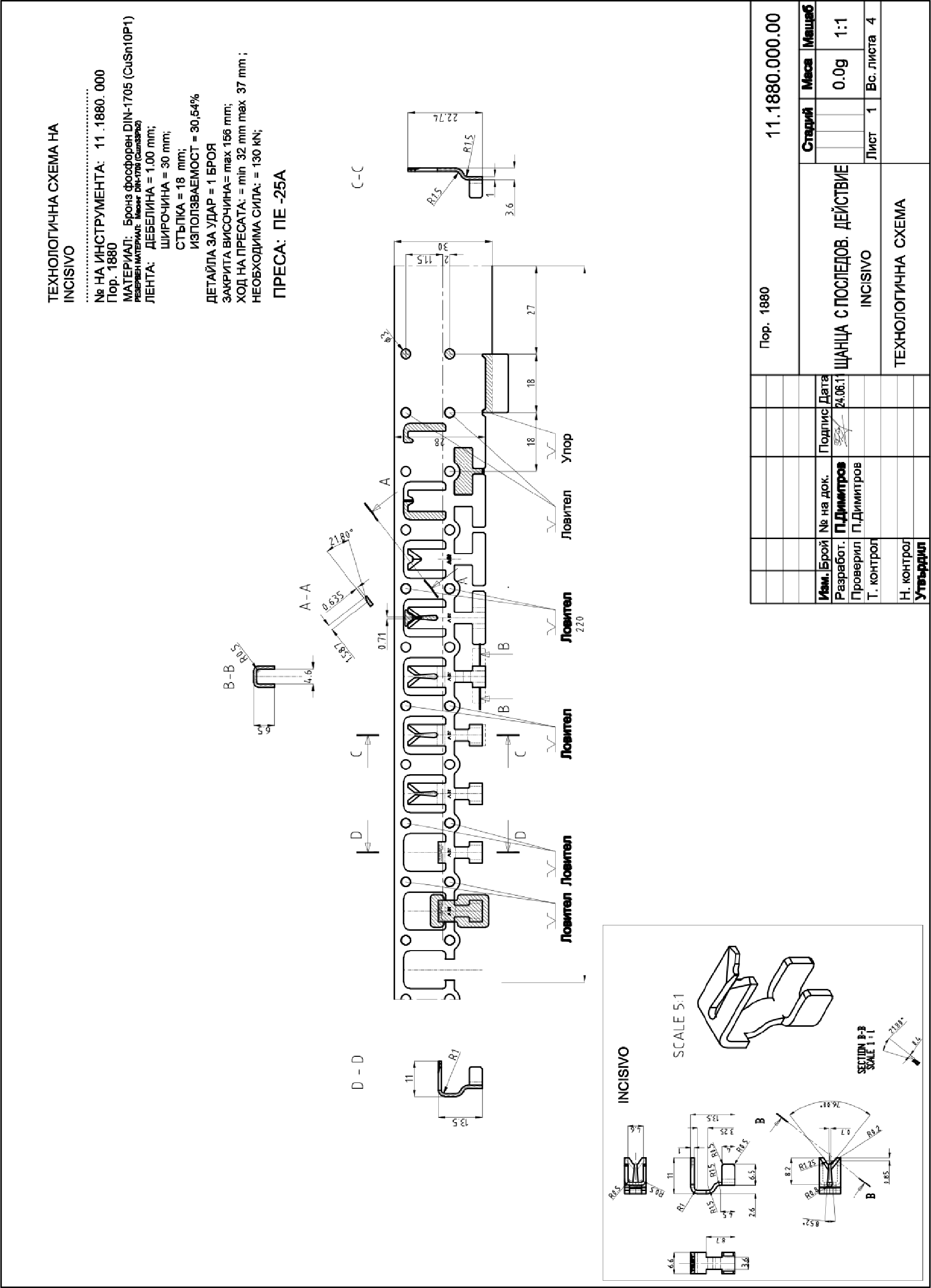
Фиг.5-7
Тук готовия детайл се отделя от лентата през отвора на матрицата надолу, а отпадъка от лентата под форма на свързващи мостчета, се извежда над матрицата. Изведената лента с отпадък не се нарязва. Така могат да се използват отворите за ловител на изхода от матрицата за ръчно центроване при работа с нарязани от лист ленти. В лентата преди огъване се прави заостряне чрез смачкване (разрез А-А) и маркировка от долната страна. Този преход е възможен само след осигурена възможност за свободно изтичане на материала чрез предварително пробит отвор с подходяща форма. За да преминават свободно огънатите на долу части (разрез D-D), лентата се повдига на 11 mm, а зоните за повдигане и водене са избрани от двете страни по дължина на лентата, преди огъващите преходи (разрези B-B, C-C, D-D).
Последователността при разработката на технологична схема за комбиниран инструмент с последователно действие за изтегляне в лента на детайл ВТУЛКА е показана на Фиг.5-8.
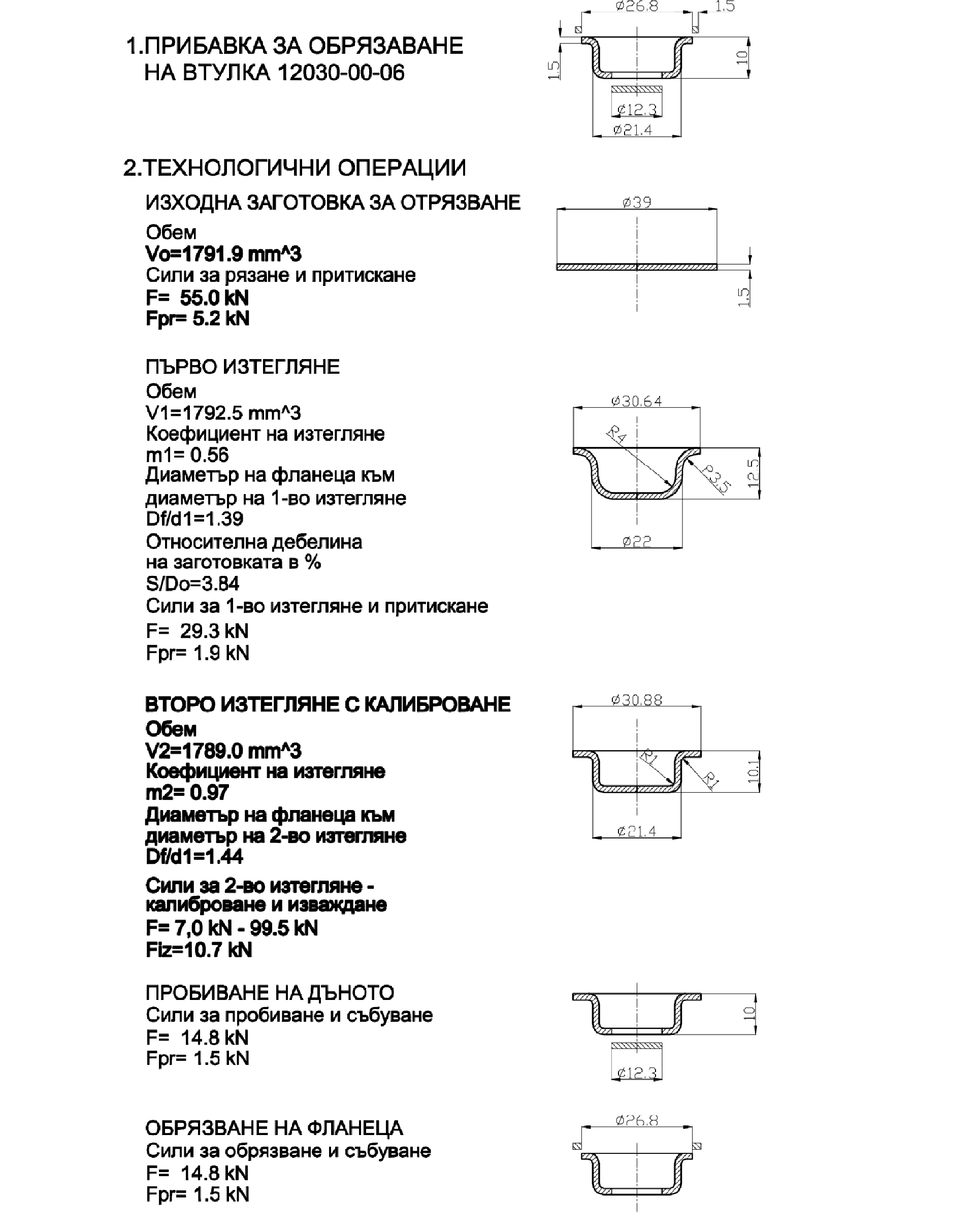
Фиг.5-8
Изходни дани за разработка на преходите са скица на детайла и необходимата прибавка за обрязване на фланеца.
Приет е изчислителен модел на крайна заготовка за изтегляне, без отвор и увеличен с прибавката диаметър на фланеца. В следващите стъпки са определени последователно необходимите технологични операции за получаване на готов детайл ВТУЛКА, които могат да се изпълнят на отделни иструменти. Понеже операциите ще бъдат обединени в един инструмент, те ще са само част от основните технологични преходи, чрез които лентата ще се трансформира в готов детайл. За определяне диаметъра на изходната плоска заготовка за отрязване, е използвано условието за постоянство на обема. Предвиден е процес на изтегляне без изтъняване, което означава постоянна дебелина преди и след изтегляне. Предположението е теоретично, защото в реалния процес на изтегляне в зависимост от степента на деформация, ще има местно изтъняване в областта на дънния радиус и страничната стена и местно удебеляване на фланеца и прилежащия му радиус. Ако се разработва технологичен процес за съществуващ детайл, от който да се измерят местните деформации, обемът може да се определи много точно. На практика обаче съществуват сили на триене, които не могат да се изчислят точно при проектирането и следователно, винаги заготовката изтънява повече от предвиденото, а фланеца остава по-голям от очакваното. Като се добави съществуването на анизотропия (не еднакви свойства в различни направления), ефектът от по-точнoтo изчисление на обема не отговаря на очакванията. По тази причина, някои специалисти препоръчват при критична степен на деформация да се увеличи обема с 2-3% (следователно и дълбочината на изтегляне), за да се намали опасността от скъсване на дъното.
След намиране на диаметъра на изходната заготовката, при известен обем и дебелина, са изчислени коефициентът на изтегляне m2 за приетия изчислителен модел на крайна заготовка, съотношението между диаметрите на фланеца и на изтегляне Df/d1 и относителната дебелина S/Do. Неизвестната променлива е диаметъра на фланеца, който е определен от условието за постоянен обем, равен на този на изходната заготовка. Най-лесното решение е чрез задаване на последователни дискретни стойности за промяна на фланеца, построяване на модела, изчисление на получения обем и повтаряне тази процедура неколкократно, до приближение на резултата към този на изходната заготовка с определена точност. В повечето случаи са достатъчни само 5-8 процедури на промени и изчисления. Може да се използва който и да е CАD продукт, позволяващ изчисление на обем на пространствения модел. Понеже радиусите са по-малки от препоръчваните, прието е, че този детайл ще се получи след калиброване и това е втори изтеглящ преход.
По избран допустим коефициент на първо изтегляне m1, за детайл с фланец при зададено съотношение спрямо изтегления диаметър и относителната дебелина, е изчислен диаметър за първо изтегляне и са приети увеличени радиуси. Диаметърът на фланеца след първото изтегляне трябва да остане постоянен за всяко следващо, включително и при калиброване. Построена е формата на заготовката след първо изтегляне, чрез която е определена дълбочината на изтегляне от условието за постоянен обем с този на изходната заготовка. Използван е същия метод на последователни приближения – чрез задаване на дискретни стойности на промяна на дълбочината, построяване на формата и изчисляване с компютър на получения обем до приближаването му към този на изходната заготовка с зададена точност (грешка под 0,5% е напълно приемлива). Определената дълбочина е сравнена с допустимата за първо изтегляне [1].
Определени са размерите на заготовката за всички технологични преходи, които са необходими за избор на работни ходове и височина на повдигане. За всички преходи са изчислени максималните технологични сили, необходимите сили на притискане, събуване на поансона или избутване от матрицата, които ще са необходими при конструирането на инструмента.
За построяване на технологичната схема за изтегляне в лента, трябва да се изберат формата на изрязване на плоската заготовка, свързващи части с лентата, носещи зони за повдигане, водене, центроване и притискане. Първия възможен вариант (виж Фиг.2-22) е на външно профилно обрязване на лентата и профилно пробиване на междината, за да останат две мостчета, свързващи отделните заготовки (виж Фиг.3-8). Главният недостатък на тозаи вариант е свиване на лентата и трудности при центроване, повдигане, водене. Подходящ е за ръчно подаване на детайли с не висока точност. Препоръчителният вариант при работа с автоматично подаване или детайли с по-висока точност е чрез пробиване на две двойки дъги, разположени перпендикулярно една спрямо друга, които след първото изтегляне оформят четири мостчета, свързващи отделните заготовки (виж Фиг.4-1). Той решава удовлетворително задачите, свързани с носещи зони за повдигане, водене, отвори за центроване на всеки преход и притискане. Лентата остава не деформирана. При него обаче, отпадъка от лентата е голям (коефициент на използване 41.7%). По тази причина е избран видоизменен вариант с пробиване на една двойка дъги, разположени напречно на лентата Фиг.5-9.
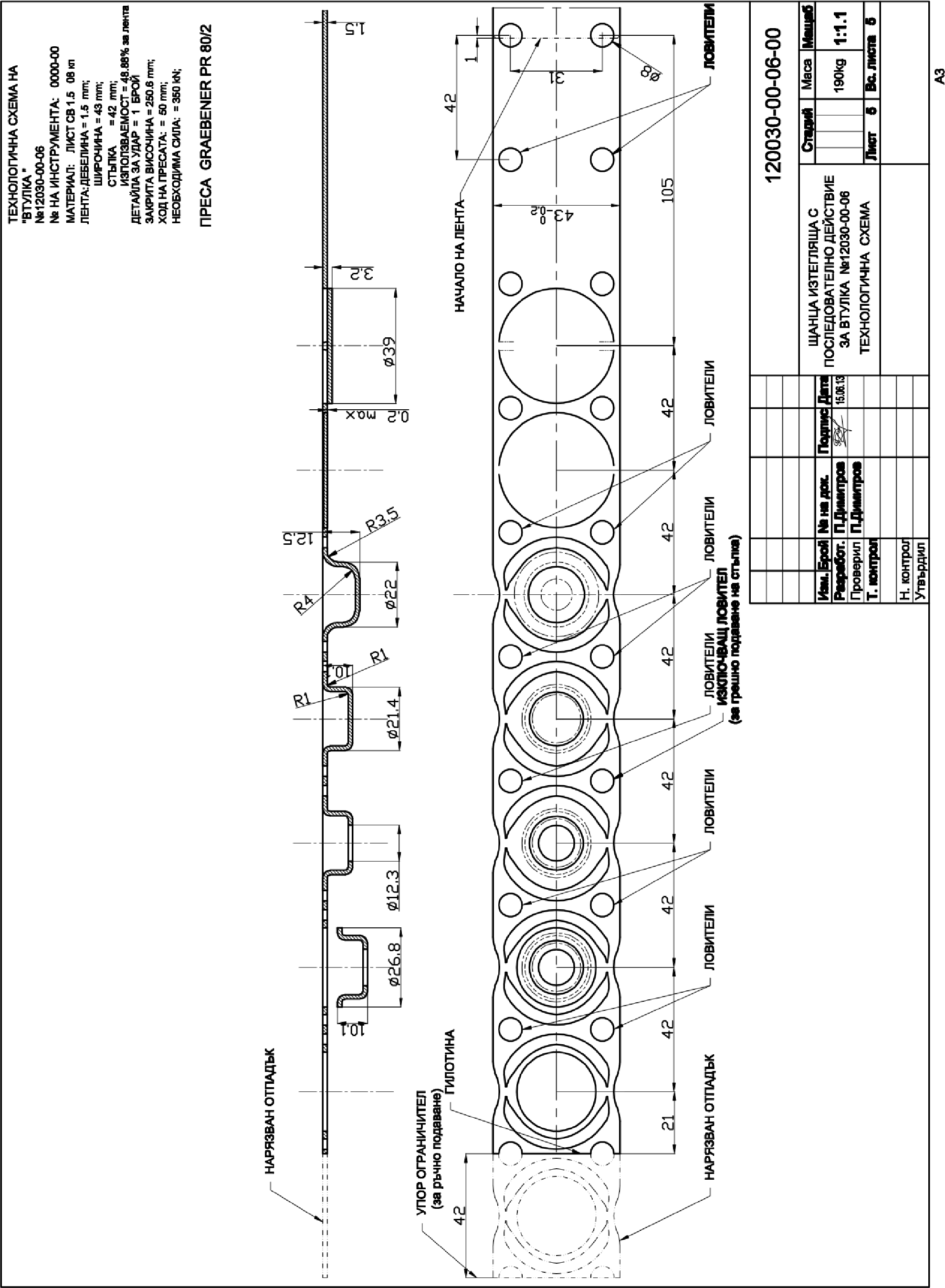
Фиг.5-9
Независимо от известна деформация на лентата, този вариант е по-икономичен (коефициент на използване 48.9%).
От разгледания пример може да се обобщи последователноста за решаване на задачите при определяне на формата и размерите на заготовките за изтеглящи операции или преходи:
– Прибавки за обрязване към изтегляния детайл и премахване на всички отвори;
– Обем на изтегления модел;
– Диаметрър на изходната заготовка за обем еднакъв с изтегления модел;
– Размер на изтегления фланец (ако има) или височина на изтегления модел за същия обем;
– Коефициент на изтегляне, относителна дебелина, отношение на диаметрите на фланеца и на изтегляне (ако има фланец);
– Допустим коефициент на изтегляне и решение за едно или много операционен процес;
– Диаметри на изтегляне за всеки преход при много операционен процес;
– Височина на заготовка за първо изтегляне при известни диаметри на първо изтегляне и постоянен фланец, за приетите радиуси;
– Коефициент на изтегляне, относителна дебелина, отношение на диаметрите на фланеца и на изтегляне, сравнение с допустимия коефициент на първо изтегляне;
– Конусна форма на изтегления фланец при първо изтегляне, ако обема не позволява получаване на същия диаметър. В този случай, по-малкия диаметър на фланеца и по-голямата дълбочина на заготовката от първия преход, на последния се оформят във фланеца на изтегления модел чрез преразпределяне и връщане на материал от цилиндричната част и конусния фланец;
– Форма и височина на заготовка за второ изтегляне при известни диаметри на второ изтегляне и постоянен фланец, за приетите радиуси;
– Коефициент на изтегляне и сравнение с допустимия за второ изтегляне;
– Форма и височина на заготовка за следващо изтегляне и така до получаване на изтегления модел.
2.3. Изчисление на технологичните сили.
Познаването на действащите сили е необходимо за вземане на правилни рашения при конструиране. Интерес представляват не само силите в резултат на извършваната технологична операция, но също сили за събуване на поансоните от лентата или заготовката, сили за избутване заготовката през отвора на матрицата или за нейното изваждане, сили на притискане на заготовкатите при огъване, изтегляне, отбортоване, формоване, сили на триене между подвижни части и заготовката, сили от теглото на заготовката, лентата, отпадъка, сили от възможно подналягане или вакум, сили от остатъчен магнетизъм в работните части на инструмента и други. Разнообразието на листови детайли и конструкции е много голямо и не може да се обобщат всички възможности на необходими сили. По-долу ще се посочат само основните сили, които трябва да се определят задължително при различните технологични операции и целта, за която ще се използват:
– Сили при изрязване и пробиване – технологично необходимата максимална сила, която трябва да се приложи за изпълнение на процеса се изчислява като произведение на дължината на срязвания контур, дебелината на материала и условното съпротивление на срязване на обработваемия материал [1]. Тя се използва за определяне максималното натоварване на режещите ръбове и на опорните им части, определяне центъра на равнодействащата сила на инструмента и за избор на подходяща преса. Тази сила обикновено се съпровожда от сила на събуване, необходима за преодоляване на триенето и изваждане на поансона от заготовката или лентата. Изчислява се като зададен процент от технологично необходимата максимална сила (до 20%) . Този вид сила се използва за изчисляване закрепващите части на матриците и поансоните, избор на пружини и буферни притискащи елементи, закрепването за събуващии лента или заготовката детайли. В матрицата се получава сила за избутване или изваждане на отпадъка или детайла от нея. Тя се изчислява като процент от технологично необходимата максимална сила (5-10%). По характер, тя е сила на триене и задавайки коефициент на триене, може да се прогнозира нормалното налягане в отвора на матрицата. Прилага се за изчисляване закрепване на матрични вложки, здравина на матрицата в най-слабото сечение, избор на пружинни или друг вид изваждащи механизми.
– Сили при огъване – технологично необходимата максимална сила, която трябва да се приложи за изпълнение на процеса, се изчислява като произведение на дължината на линиите на огъване, дебелината и якостта на обработваемия материал и корекционен коефициент [1]. При калибровка в края на процеса силата е средно 2 – 4 пъти по-голяма (зависи от настройката на пресата). Тя се използва за определяне натоварването на поансони, матриции, на опорните им части, за определяне центъра на равнодействащата сила на инструмента и за избор на подходяща преса. За да остане неподвижна заготовката при огъване, се препоръчва прилагане на сила на притискане, противодействаща на възникналия огъващ момент. Изчислява се като произведение на препоръчано повърхностно налягане и площа на притискане. За опростяване може да се използва изчисляване като процент от силата на огъване (до 25%). Прецизното изчисление обаче, изисква определянето и от условието за равновесие с момента от огъващата сила за рамото на нейното приложение. Този вид сила се използва за изчисляване на пружини и буферни притискащи елементи или за изваждане на заготовката от матрицата. В някои случаи може да е необходима сила за изваждане на заготовката от поансона. По характер тя също е сила на триене и може да се приеме като зададен процент от технологично необходимата максимална сила на огъване (2-5%). Използва се за изчисляване на събуващи пружини.
– Сили при изтегляне – технологично необходимата максимална сила, която трябва да се приложи за изпълнение на процеса. Тя се изчислява като произведение на дължината на изтегления контур, дебелината и якостата на материала и корекционен коефициент за вида на изтеглянето [1]. Използва се за определяне максималното натоварване на матрици, поансони и на опорните им части, за определяне центъра на равнодействащата сила на инструмента и избор на подходяща преса. В някои случаи е необходима за оценка на съпротивлението на заготовката срещу изкълчване. При изтегляне на заготовката с недостатъчна относителна дебелина (100xS/d < 2) се препоръчва прилагане на сила на притискане, затрудняваща образуването на гънки (гофри). Изчислява се като произведение на допустимо повърхностно налягане и площа на притискане на фланеца [1]. Този вид сила се използва за изчисляване на буферни притискащи елементи или за изваждане на заготовката от поансона. Необходима е също и сила за изваждане на заготовката от матрицата. По характер тя е сила на триене и също може да се приеме като зададен процент от необходимата максимална сила на изтегляне (3-6%). При малка хлабини в калиброващи операции този процент е до 2 пъти по-висок. Използва се за изчисляване на събуващи пружини и изхвъргачи.
– Сили при отбортоване – технологично необходимата максимална сила, която трябва да се приложи за изпълнение на процеса. Тя се изчислява като произведение на дължината на отбортования контур, дебелината на материала и корекционен коефициент [1]. Използва се за определяне натоварването на поансони, матрици и опорните им части, за определяне центъра на равнодействащата сила на инструмента и за избор на подходяща преса. Необходими са и сили за изваждане на поансона от заготовката и на последната от матрицата. Те са сили на триене и също могат да се приемат като зададен процент от необходимата максимална сила на отбортоване (до 10%). Прилагат се за изчисляване на закрепване на поансони и матрици, избор на пружинни или изхвъргачи.
– Сили при релефно формоване – необходимата максимална сила, която трябва да се приложи за изпълнение на процеса. Тя се изчислява като произведение на формованата площ и специфично налягане, зависещо от якостата на материала [1]. Използва се за определяне натоварването на поансони, матриции, на опорните им части, за определяне центъра на равнодействащата сила на инструмента и избор на подходяща преса.
2.4. Определяне на необходимите работни ходове.
Тук е важно да се определят всички необходими ходове, които трябва да се гарантират от инструмента. Скиците на технологичните преходи се анализират, за да се определят какви работни ходове трябва да извърши всеки поансон, включително и с колко трябва да се подмине заготовката надолу и нагоре. Към най-големия ход се добавя максималната стойност на повдигане на заготовката или лентата за безпрепятствено преместване. Добавя се необходимия ход за свиване на пружините от момента на контакт с най-високата част на заготовката до нейното притискане. В зависимост от начина на работа се добавя допълнително разстояние, необходимо за сигурно предвижване на лентата или ръчно поставяне и снемане на заготовка. Получената обща стойност е минимално необходимия ход на инструмента. Максимално допустимия ход се ограничава от съображения за излизане на поансоните или колоните от водене, или поради големите инерционни натоварвания при високо скоростни преси. Той трябва да е съобразен с наличните ходове на пресата. За разгледания пример от Фиг.5-8 максималния работен ход на поансона е при първо изтегляне. С отчитане на дебелината той е 11 mm плюс 0.5 mm превишаване над заготовката. На такава стойност трябва да се повдигне заготовката за излизане от матрицата и безпрепятствено преместване на лентата. За пробиване на отвора и събуване на поансона е необходимо притискащата част да навлезе в лентата до дъното на 8,5 mm, която също ще се прибави към необходимия ход – едва след това може да започне пробиване на отвора и свиване на пружините. След добавяне на 10 mm за гарантиране достаъчно разстояние между най-ниската подвижна част и лентата, минималния необходим ход е 41,5 mm. Приет е най-близкия по-голям ход на пресата от 50 mm.
2.5. Подаване и водене на заготовката.
Важно условие при изготвяне на технологична схема е сигурно водене на лентата във всеки един момент на подаване до достигане на позиция за нейното фиксиране при изпълнение на технологичен преход. За да е възможно свободно движение на лентата, е необходима минимална хлабина, която да гарантира, че възможните грешки в широчината на лентата и възникналите деформации в някои от технологичните преходи, няма да предизвикат заклинване. В разгледания случай на профилно изрязана лента от Фиг.4-5, сигурното водене във всеки един момент на подаване ще се постигне с цели направляващи планки – лентоводачи с едностранна хлабина от 0,2 mm. Случаят за лентата от Фиг.5-9 е по-сложен, защото освен водене, във всеки един момент на подаване е необходимо и повдигане на височина минимум 11.5 mm. Използвания по-икономичен вариант има съществен недостатък – деформиране навътре на част от страничния край на лентата след първото изтегляне, което затруднява условието за сигурно и непрекъснато водене на лентата. Тук решението се търси за такова разположение на водещите и повдигащи части, при което излизането на лентата от една двойка да е предшествано от нейното влизане в контакт с друга. Чрез по-голям брой подходящо разположени водещите и повдигащи части се осигурява сигурно водене, подобно на цели направляващи планки.
2.6. Позициониране и фиксиране на заготовката – уточняване на използваните бази.
Това е основен етап, чието правилно решаване определя точността на детайла не само за технологичната схема, но и за всяка операция и преход. Важно изискване е прилагането на принципа на единство на базите (когато е възможно се използват едни и същи повърхнини). Прилагат се различни методи за позициониране и фиксиране на заготовката, които зависят основно от два фактора – конфигурацията на заготовката (включително и лентата) и начина на подаване. За ръчно позициониране на лентата от Фиг.4-5 са използвани изрязаните части от стъпкови поансони, които опират в упор на лентоводачите. Окочателното фиксиране на лентата в работно положение се извършва при хода на пресата надолу по пробити в първа позиция отвори ф5 mm чрез ловители. Така се извършва първоначално позициониране на лентата с точност, зависеща от хлабината на водене и следващо прецизно центроване и фиксиране с временна сглобка с минимална хлабина по време на работния ход. Автоматичното позициониране на лентата от Фиг.5-9 се извършва от подаващо устройство на пресата. Окочателното фиксиране на лентата в работно положение се извършва при хода на пресата надолу по пробити в първа позиция отвори ф8 mm чрез ловители. За позициите на пробиване и обрязване се използва и центроване по вътрешните изтеглени повърхнини на заготовката. Предвидена е възможност за ръчно позициониране на лентата до упор на изхода от матрицата. Работата с автоматична преса изисква прилагане на защитни устройства за грешно позициониране. За тази цел е използван един от ловителите, който изключва пресата ако не попадне в съответния отвор и не позволява ново включване преди намеса на оператора.
Трябва да се има в предвид, че използване на ловители за фиксиране на лентата при хода на пресата надолу, изисква да се осигури безпроблемното им изваждане от нея при обратния ход. Най-лесното решение е механично ограничаване на възможностите за повдигане на лентата чрез стъпало в направляващите планки - лентоводачи или повдигащите части, при което тя принудително се събува от ловителите. В други случаи (лесно деформираща се лента) се използват подпружинени отлепвачи, разположени близо до ловителите, които избутват лентата на малка величина, достатъчна за понататъчното и отделяне под действие на гравитационните сили.
2.7. Извеждане на заготовката от работната позиция.
Заготовката остава в отвора на матрицата (гнездото) след края на работния ход на пресата надолу при огъване, изтегляне, отбортоване и в някои случаи дори при операция изрязване (щанци със съвместно действие при едновременно пробиване и изрязване на контур). В зависимост от вида на технологичната операция и условията, нейното изваждане изисква прилагане на по-голяма или по-малка сила за преодоляване на съпротивлението от триене. При последователно изпълняваните технологични преходи в лента, обикновенно изваждането трябва да стане съгласувано (едновременно) с обратния ход на поансоните. Най-разпространеното и достъпно решение е използване на буфери или пружини, които посредством специални изхвъргачи изваждат заготовката от съответното гнездо. По-рядко се използват избивачи, които се задействат механично при движението на пресата или от специални устройства. При тях обикновенно не се търси съгласуване с обратния ход на поансоните. Закъснението на момента на изваждане на заготовката в отделни случаи се търси преднамерено, за да може лентата да се е преместила и извадената заготовка да падне върху нея и така да се изведе от работната позиция. Типичен пример за такъв подход е едновременно пробиване и изрязване на контура на леки детайли (неметални уплътнения, гарнитури, изолиращи планки) в щанци със съвместно действие с горно разположение на изрязваща матрица и пробиващи поансони и долно разположена поансон-матрица. Падането на заготовката върху преместената лента позволява нейното извеждане от самата лента или чрез издухване с въздушна струя, което е по-безопасно от ръчното изваждане.
За лентата от Фиг.5-9 принудителното изваждане на изтеглената и калибрована заготовка е задължително – свързващите отделните заготовки отпадъчни лентички са тънки и лесно деформируеми. Те не могат да се използват за изваждане (издърпване) на заготовката. За схемата е характрно, че при калиброването заготовка с по-долям диаметър принудително се вкарва в по-малкото гнездо на матрицата, което води до по-големи сили на триене при изваждане. Затова за тази позиция е предвидено използване на пружинен буфер с две сили – голяма в началния момент на изваждане и незначителна (за преодоляване на теглото на заготовката) до края на повдигане.
Има случаи, когато изваждането на заготовката не може да се изпълни в посока, обратна на вкарването. Такъв е показан при лентата от Фиг.5-2 – разрези Е-Е, F-F, G-G. Затворената форма на заготовката. определя единствено възможна посока за изваждане от работна позиция, движението напред с лентата. По необходимост, оформящата огъвките матрична огъваща вложка, изпълнява едновременно всички допълнителни функции за водене, повдигане и изваждане.
2.8. Отделяне на отпадъка.
Отделянето на отпадъка и извеждането му от работната зона е много важен момент за всички разделителни операции. Разработката на технологична схема не трябва да допуска смесване на готовия детайл с отпадък на никъкъв етап. Сигурното извеждането на отпадъка е особено актуалено при работа на автоматична преса, където дори няколко минути са достатъчни за да настъпи задръстване с отпадък и повреда в инструмента.
Най-разпространените начини за отделяне на отпадъка от пробиване или отрязване са:
– надолу през инструмента и масата на пресата, показан на Фиг.4-5 (защрихованите зони);
– странично на матрицата по улеи извеждащи го извън инструмента, показани на Фиг.5-9 (последния преход след обрязване фланеца на детайла) и на Фиг.4-3 (технологичен преход изтегляне и обрязване №7).
Отделянето и извеждането му на долу е надежден и сравнително прост метод за разделяне на ненужната част от лентата със заготовките. Тук обаче, възникват редица затруднения при отпадък от пробиване на отвори с малък диаметър или изрязване на сравнително малки отпадъци с отворен профил. Те често се заклинват в отвеждащите отвори, с което предизвикват задръстване и повреда на режещите ръбове на матрицата. Причина за това е недостатъчна или прекомерно голяма хлабина между тях и отвора. В единият случай, след завъртане на ъгъл, по-малък от ъгъла на триене, те се заклинват, а в другия, някои от тях се завъртат перпеникулярно на посоката на извеждане и контактувайки с нормално разположените отпадъци отново предизвикват заклинване и задръстване. По тази причина, изборът на хлабина и форма на отвеждащите отвори, е изключително важен за надеждната работа на инструмента, но често се подценява от конструкторите. Хлабината трябва да е по-малка от половината дебелина на отпадъка, а формата на извеждащия отвор да е конусна, разширяваща се на долу. Отпадъците с отворен профил често се залепват към челата на поансоните и се изваждат от матрицата, с което възпрепятстват свободното преместване на лентата и оставят белези или деформации по крайния детайл. Причина за това е малкото тегло, наличието на остатъчни магнитни сили по поансоните (при стоманен отпадък), смазка по челната повърхност на поансона (увеличава адхезиата). Отвореният профил не позволява заклинване на отпадъка вследствие на деформациите, защото той се изместава и силите на триене отсъстват. Това явление на вдигане на отпадък се наблюдава понякога и при малки отвори със затворен профил. Не е напълно ясен механизма на поява и причините, които го предизвикват. Безспорно, една от тях е по-голямата хлабина между матрица и поансон и състоянието на режещите ръбове. Проблемът в този случай е, че за един и същ затворен профил, понякога отпадъкът се вдига, а друг път остава в матрицата. Решението при по-големи отворени профили е поставяне на пружинни отлепватели в поансона или използване на отвори за въздух под налягане. Единствената възможност за малките отпадъци по затворен контур е създаване на подналягане или частичен вакум в отвора на матрицата. За съжаление, това не винаги е конструктивно осъществимо, поради което е задължително да се анализира тази възможност още при разработка на технологичната схема. Когато не е предвидено използване на частичен вакум в отвора на матрицата, може да се опита частично затъпяване ръбовете на поансона или матрицата, в зависимост от това, коя част ще е отпадък. В затъпеният участък възникват чепак или дефекти, които помагат на задържане на отпадъка в матрицата, но този ефект е временен и не дава 100% сигурност.
2.9. Уточняване необходимостта от допълнителни устройства.
Всеки щанцов детайл има особености, които понякога изискват използване на допълнителни устройства. Те не са включени в конструкцията на инструмента или пресата и трябва да се изработят. На пример магнитопроводите в тарнсформатори и електродвигатели изискват ориентиране и отделяне на определен брой пластините в пакети, което е целесъобразно да се извършва при излизането им от инструмента. Показаната технологична схема за Лист роторен и Лист статорен предвижда изработка на допълнителни ориентиращи улеи за двата - Фиг. 5-10.
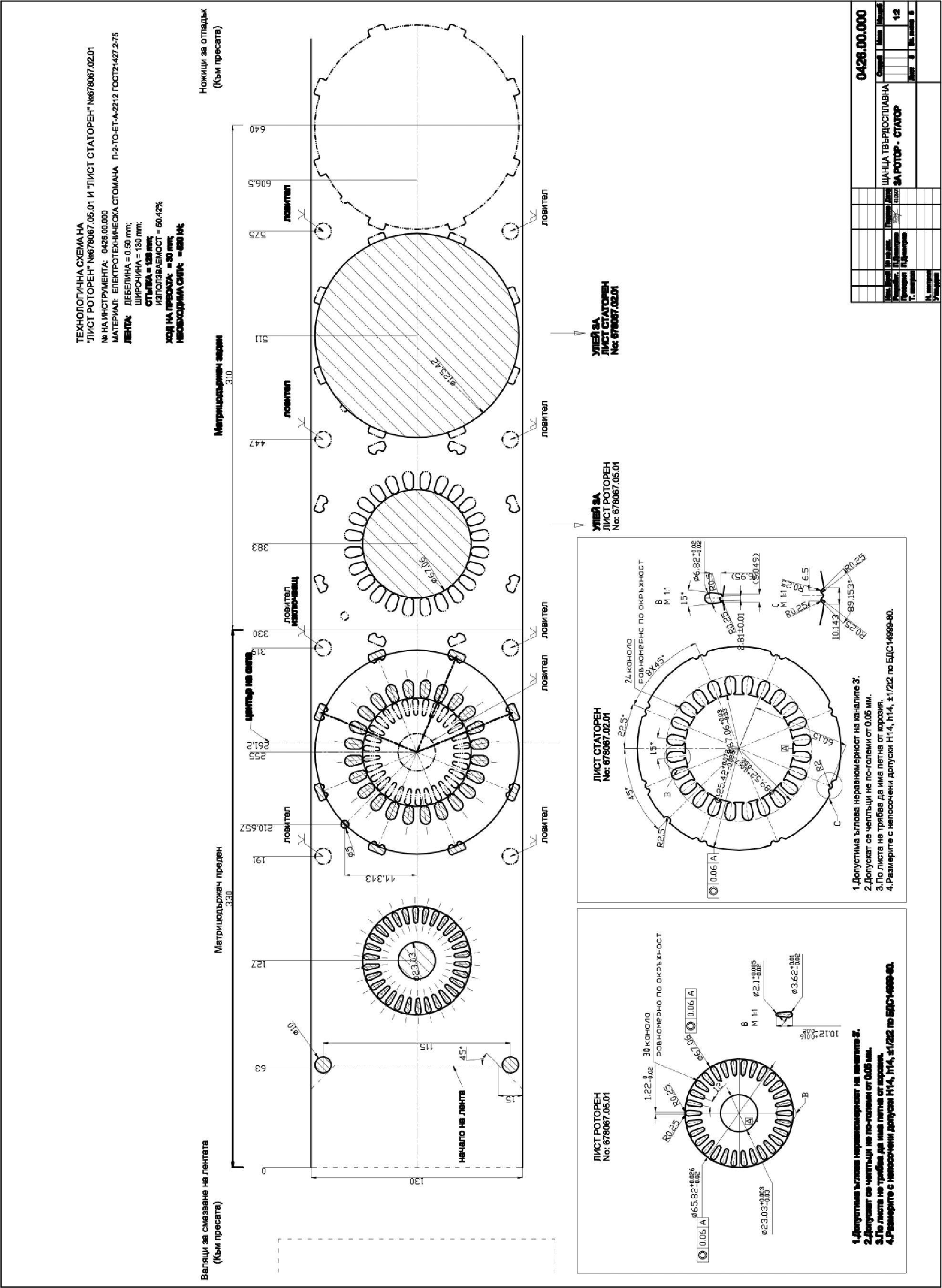
Фиг. 5-10
Към щанцата за Лист роторен и Лист статорен е предвидена изработка на допълнителен лентоводач на входа със смазване на лентата от двете страни.
Допълнителни устройства са притискащите буфери за пресата, които е предвидено да се изработят. На пример, за огъващите инструменти на детайл от Фиг.5-2 се е наложило изработка на специален буфер за масата на пресата с променлива сила и ъглово позициониране - Фиг.5-11 и Фиг. 5-12.
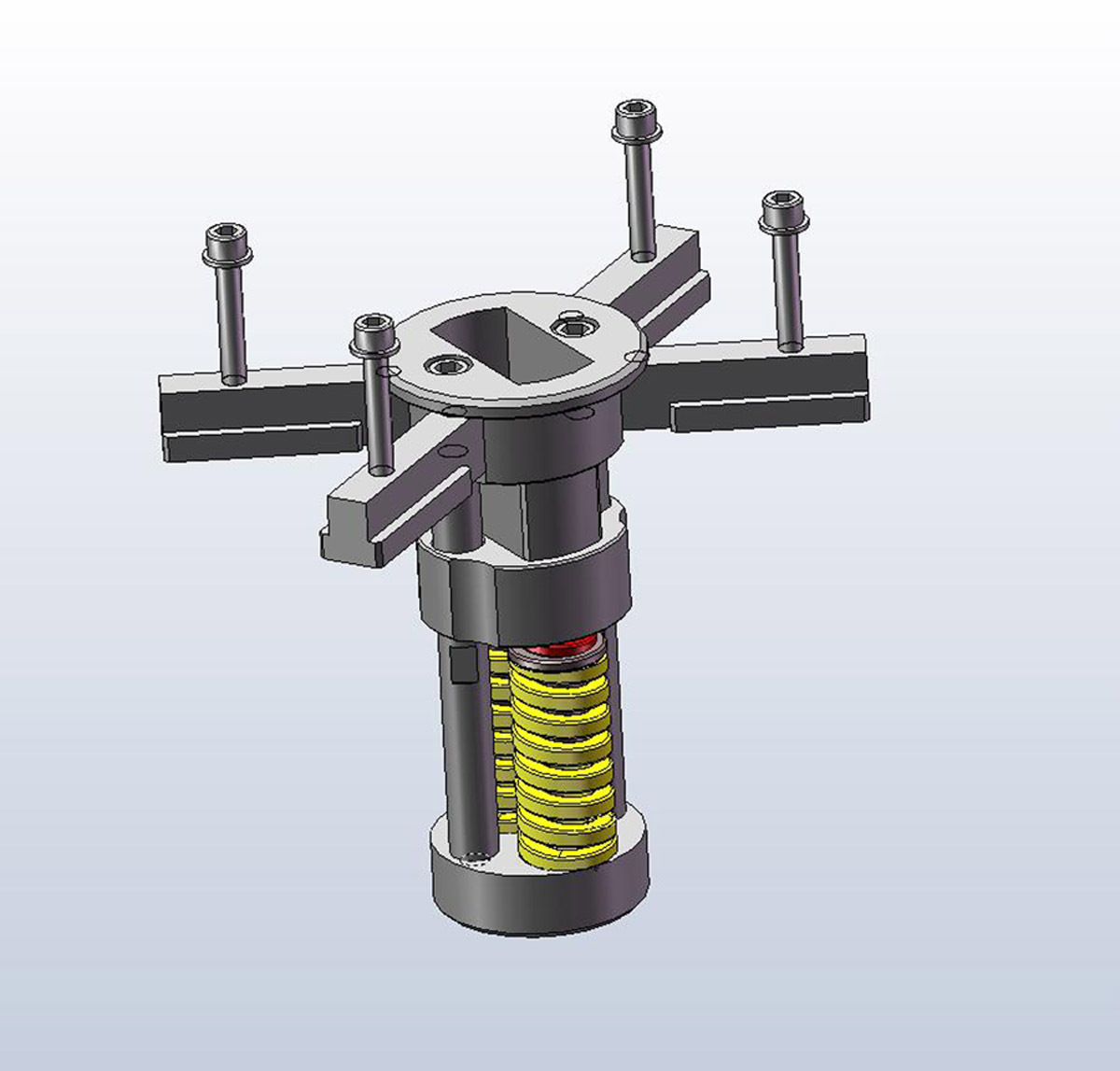
Фиг.5-11
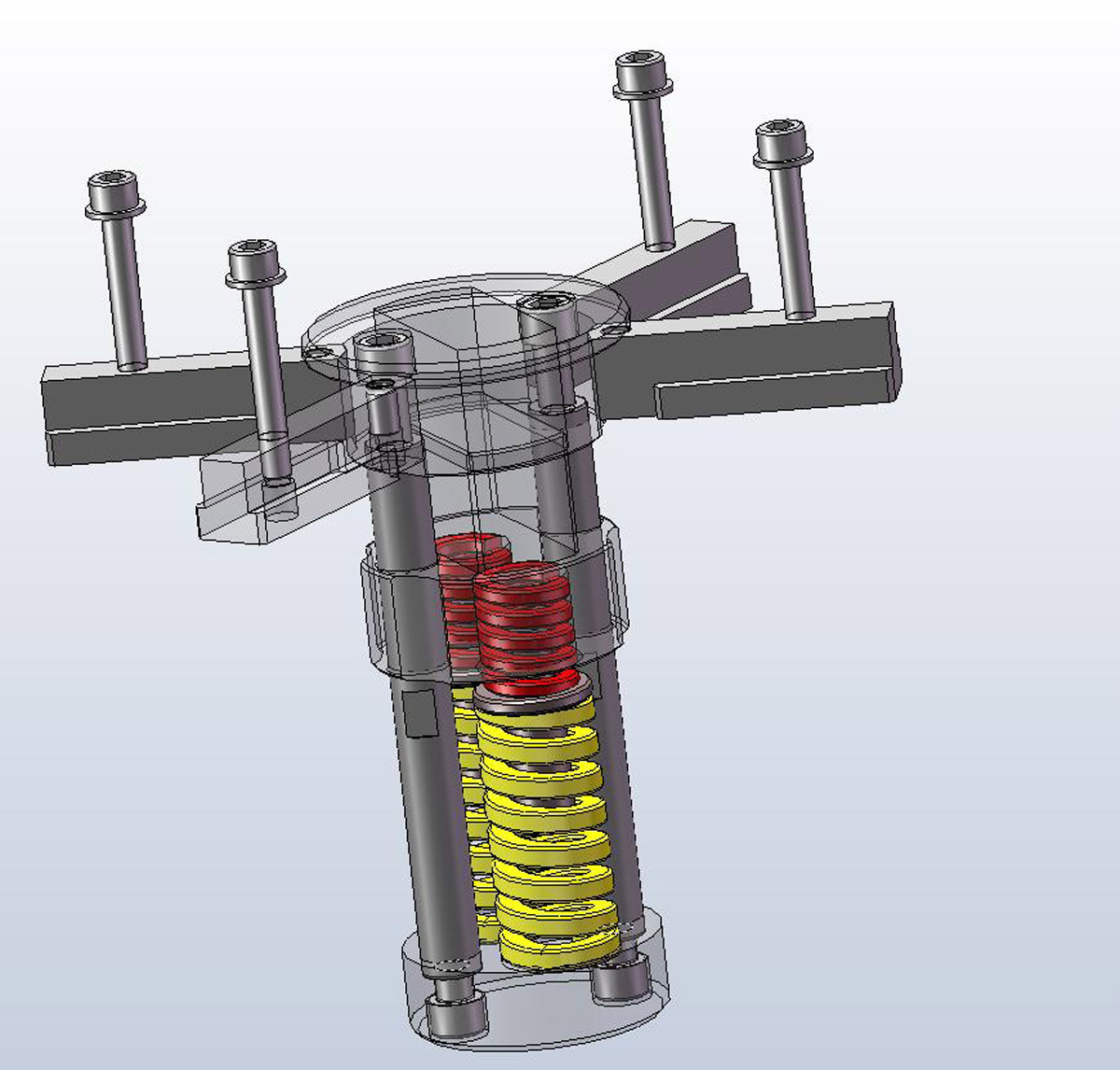
Фиг. 5-12
2.10. Окончателен избор на преса.
След определяне на технологичните сили за всяка операция или преход, общата сила по т.2.3. и необходимия ход на пресата по т. 2.4., може да се извърши окончателен избор на преса. Желателно е, да се провери момента на тяхното възникване, спрямо кривата на допустимо на натоварване на пресата - Фиг.5-13.
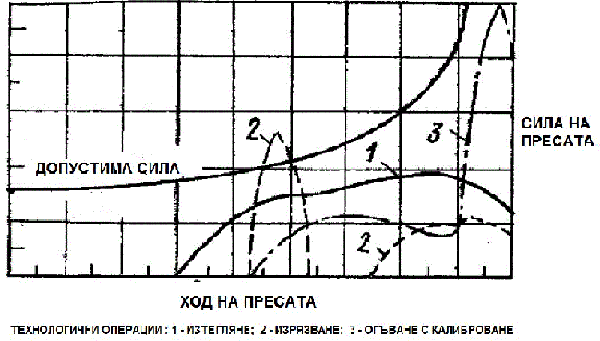
Фиг.5-13
Така ще се избегнат случаи, когато максималната технологична сила е по-малка от номиналната на пресата, но се прилага в неподходящ момент от хода (крива 2).
Пресата трябва да се провери за претоварване по мощност [1] при работа в автоматичен режим и при технологичен процес за многопозиционни преси с грейферно или манипулаторно подаване на отделните заготовки (виж Фиг.4-3). Напълно реална е възможността, отговаряща по допустимо натоварване преса, да е не подходяща за работа в автоматичен режим, заради претоварване по мощност. Вследствие на това претоварване се нарушава закона за съхранение на енергията (полезната работа на пресата не покрива технологично необходимата работа за протичане на процеса) и след някъкъв период от време пресата аварира поради прегряване на двигателя. Същата преса при проби с единични удъри, с достаъчен интервал между тях, може да работи напълно нормално, защото маховика има време да възстанови загубената енергия. Трябва да се има в предвид, че работата при технологичните операции се интерпретира графично с площа на графиките им от Фиг.5-13. При повечето процеси на щанцоване, намаляване на максималната сила най-често е свързано с по-дълъг ход, а следователно с повече работа (заради по-дългото въздействие на силите на триене).
Изборът на преса и нейната комплектност ще помогне да се уточнят необходимите допълнителни устройства по т. 2.10.
При разработката на технологичен процес за единични операции, извършвани с отделни инсрументи, се прилагат частино или изцяло същите действия и правила. Някои от изброените основни принципи, обаче, загубват значението си при конкретните условия. На пример изискванията за равниност на лентата, сигурното водене, гарантирано извеждане на отпадъка или разделянето му от детайла при огъваща щанца. Други, свързани със сигурно позициониране, центроване, фиксиране и извеждане на заготовката от работната позиция остават, независимо от вида на технологичния процес и конкретната операция или инструмент.
Разработката на технологичен процес за многопозиционна преса с грейферно подаване на отделните заготовки (трансферна система на подаване) от Фиг.4-3 е много близка до изложеното за технологични схеми на инструменти с последователно действие. Операциите се проектират както едно операционни за отделни инструменти. Особеното е, че вместо да се спазват изисквания за равниност на лентата, свързващи мостчета, водене на лентата, трябва да се изберат и гарантират зони за сигурно захващане на заготовката за всяка работна позиция и нейното надеждно позициониране и центроване спрямо матрици и поансони преди и след работния ход. Изборът на тези зони е свързан с формата на конкретния детайл и се базира на избрания модел преса и особеностите на нейното грейферно подаващо устройство – 2 или 3 координатно, максимални ходове по съответните оси (на захващане, повдигане и подаване), пределно тегло на заготовката. Изключително важно е самото позициониране и центроване да става плавно, а изваждането от работната зона да гарантира очакваното разположение на заготовката. Всички проверки за свободно преминаване на заготовката между позициите и възможни сблъсъци (колизии), се извършват за системата заготовка – грейферно устройство –инструмент за всяка работна позиция. При откриване на конфликти от колизия, най-често се променя избраната зона за захващане на заготовката в съответната позиция.
Големите размери на този вид преси ги прави податливи по направление на работния ход. Затова е трудно да се получат точни по височина детайли или части от тях без предвиждане на специални мерки за настройка, позволяващи да се компенсира силовото влияние на съседни позиции. За проверките по мощност и по допустимите силови натоварвания чрез сумарната графика, беше споменато по горе. Обичайно при многопозиционните преси е отделянето на отпадъка извън пресата странично по улеи. По същия начин се отделя и готовия детайл.
3. Разработка на конструкция на щанците.
Всяка конструкция на щанцов инструмент съдържа три основни групи от взаимно свързани части.
Най-важната от тях е на АКТИВНИТЕ ЧАСТИ, която включва детайли, влизащи в контакт с обработваемия материал и определящи формата и размера на получения детайл. Конструктивното им изпълнение е различно – матрици (обхващащи продукта), поансони (обхващани от продукта), поансон-матрици и вложки (могат да са и матрични и поансонни).
Друга основна група е ТЕХНОЛОГИЧНО НЕОБХОДИМИТЕ ЧАСТИ, позволяващи правилна работа на инструмента. Техните функции са от една страна да осигурят водене, центроване, фиксиране, притискане, изваждане на заготовката, а от друга да гарантират правилно взаимно разположение на активните части. Технологично необходимите части, които контактуват с обработваемия материал и осигуряват необходимото разположение и точност на заготовката при обработка са конструктивно изпълнени като лентоводачи, ловители, фиксатори, упори, ограничители, притискачи, събувачи, повдигачи, отлепвачи. Конструктивните части, осигуряващи необходимото разположение на матрици, поансони и вложки спрямо заготовката, са носещите плочи (горни, долни, водещи), водещите втулки и колонки. Тази носеща конструкция се нарича блок и може да се изработи като оригинална за дадена щанца или да се използва готова.
Много фирми доставят нормализирани блокове за щанци с различни размери с по 2 или 4 водещи колонки, разположени осово, диагонално или зад работната площ („FIBRO Normalien“, „DME“, „RABORDIN INDUSTRE“, „AGATHON“, „STRACK Normalien“, „MEUSBURGER“, „DANLY“, „DEYTON LAMINA“, „SUPERIOR“). Нормализираните блокове са с различно изпълнение на водещите колонки и втулки – с триене при плъзгане или триене при търкаляне. Могат да включват и водещи плоча, а фирмите „FIBRO Normalien“ и „DME“ доставят конструкция на нормализирани блокове за щанци с последователно действие, включващи и поансонодържач с опорна плоча с закрепващи винтове и щифтове.
Последната основна група са СПОМАГАТЕЛНИТЕ ЧАСТИ, които не влизат с контакт с обработваемия материал, но облекчават и подпомагат работата с инструмента. Това са държачи за преса, транспортни палци, ограничители за хода или закритата височина, улеи, защитни ограждения, информационни табели, подложни пластини. Към тази група може да се отнесат стандартни буферни елементи (винтови пружини, тарелчати пружини, полеуретанови или гумени елементи, газови пружини), скрепителни елементи и щифтове.
Ако се използва нормализиран блок, той трябва да се избере от каталог по вид, размери на работната площ, дебелна на плочите, дължина на колонките и да се преработи съобразно конкретния инструмент. На практика тези блокове са полуфабрикати, в чиито плочи допълнително се изработват необходимите работни профили и скрепителни отвори.
3.1. Проектиране на активни части.
Tехнологичната схема на лентата или на заготовката от инструмента са задължително условие за начало на проектиране на матриците и поансоните. Успоредно с тяхното оформяне се проектират технологично необходимите части, които контактуват с обработваемия материал и осигуряват необходимото разположение и точност на заготовката. Това са лентоводачи, ловители или фиксатори, упори, притискачи, повдигачи. Ако се използват стандартни или нормализирани части, достатъчно е да се оформят необходимите отвори за тях. При създаването на обемни модели на активните и технологично необходимите части, контактуващи с лентата, тяхното наслагване дава много добра нагледност и визуализация на възможните грешки и проблеми. Често срещан проблем при ръчното проектиране е липса на освобождаващо легло за направени на предишна позиция огъвки или формовки, което се открива след тяхното смачкване при проба на инструмента. Този проблем се рашава много лесно от съвремените CAD системи чрез проверка за контакт между съответния 3D модел и лентатa. Обикновено такива проблеми се откриват и визуално.
Пример за последователността на 3D проектиране на активните части за щанца с последователно действие е показан за лентата oт Фиг.5-14.
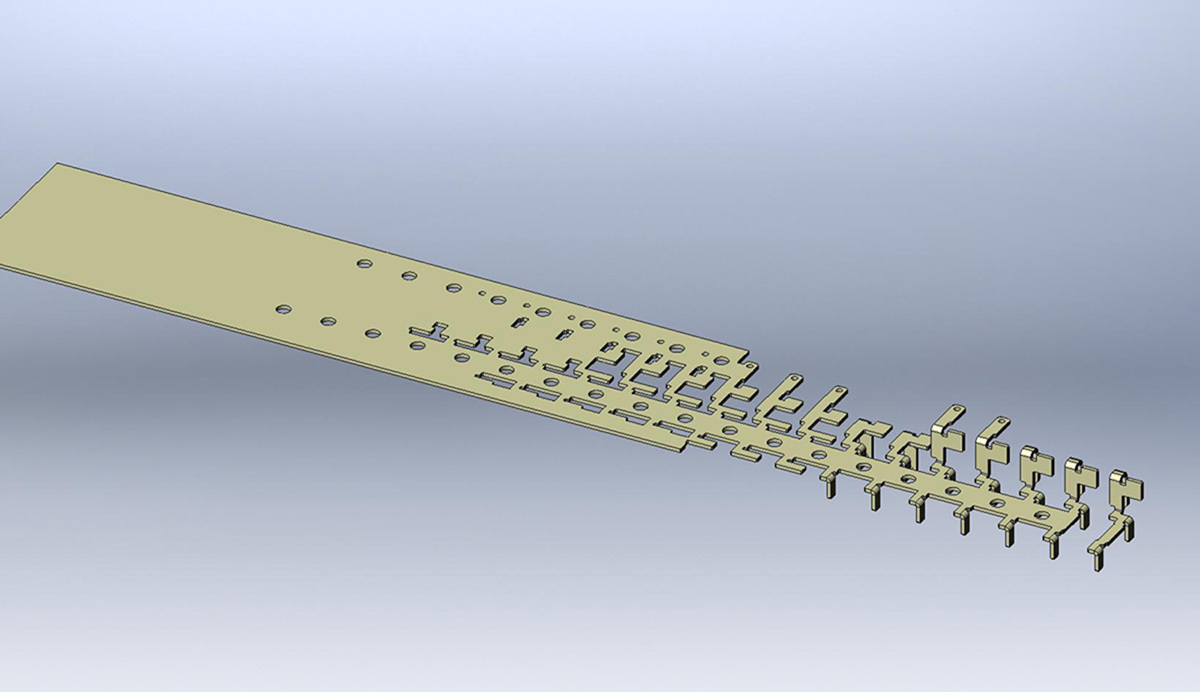
Фиг.5-14
Крайният детайл с огъвки в противоположни посоки (надолу и нагоре), се получава след 18 стъпки – последователни преходи на пробиване, изрязване, огъване, оформяне на фаски. Инструмента е предназначен за работа в автоматичен режим върху преса с подаващо устройство, осигуряващо заложената стъпка и точно фиксиране по пробити в отпадъка от лентата отвори. Същевремено, лентата е необходимо да се повдига за да се извадят огънатите надолу зони от матрицата. Местата за повдигане не трябва да пречат на преместването и по дължина на матрицата, но трябва да са достаъчно близо до отворите за фиксиране, за да се избегне огъване на лентата. Трябва да се гарантира и безпроблемното изваждане на фиксиращите ловители от отворите, без деформация на лентата. В разгледания случай, инструмента е с вложкова съставна матрица - Фиг.5-15.
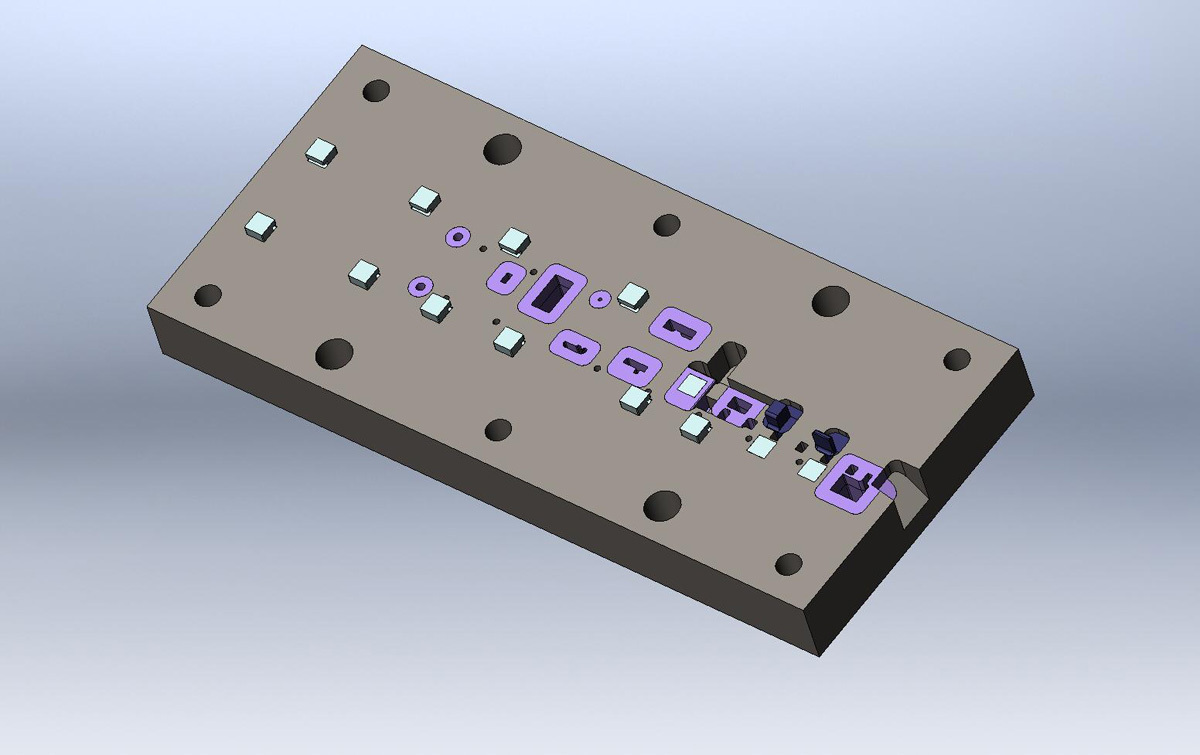
Фиг.5-15
Това позволява матричните вложки да се изработят от различен материал, според предназначението им – режещите от металокерамика или бързорезна стомана, огъващите и формоващите от високо легирана инструментална стомана. Така се оптимизира износоустойчивостта в зависимост от местното натоварване, подобрява се технологичността за изработка (особено за огъващите вложки) и се подобряват експлотационните показатели чрез улесняване на подръжката при заточване. Режещите вложки и матрицата могат да се заточват по работната страна отделно от огъващите, които просто ще се извадят. След заточване на режещите, извадените огъващи вложки могат да се намалят от не работна страна със същата стойност, с което да се възстанови размерната верига. Режещите вложки от матрицата на от Фиг.5-15 са оцветени в лилав цвят, а огъващите вложки в тъмно син. В матрицата са показани и технолочихо необходимите части за повдигане на лентата в светло син цвят. Конструкцията и разположението на част от тези повдигачи са проектирани да съчетаят функциите по водене на лентата, нейното повдигане и събуване от ловителите - Фиг.5-16.
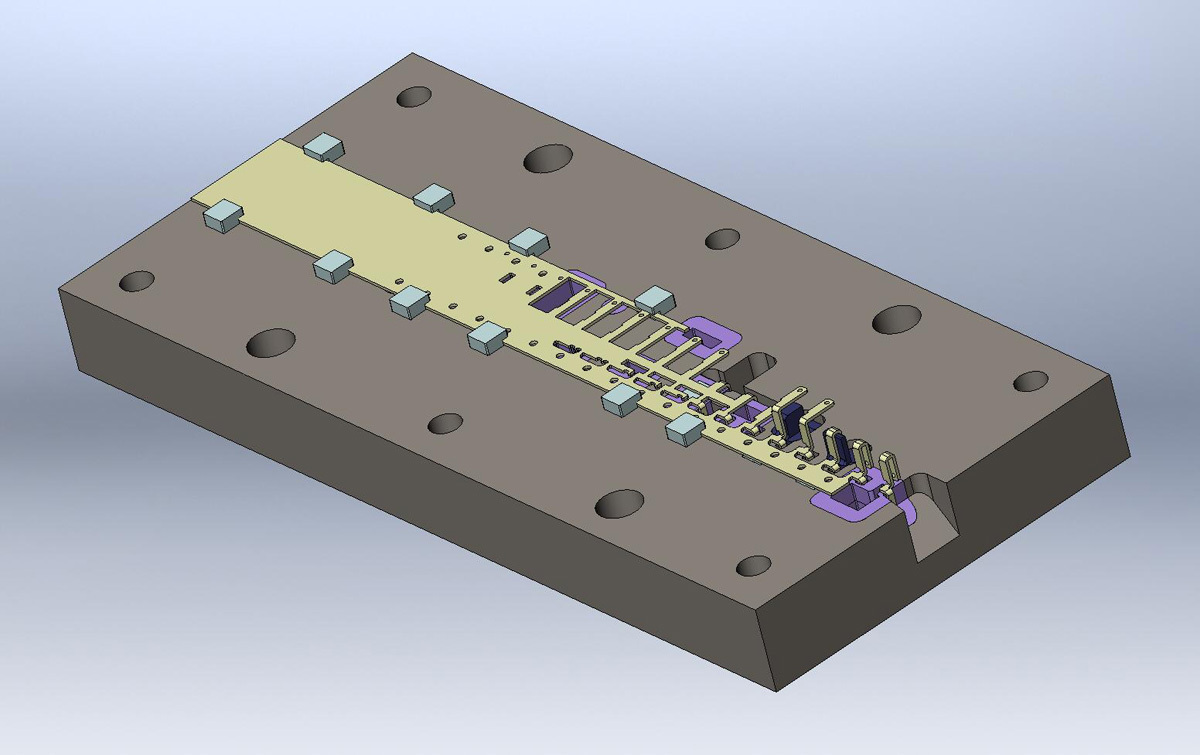
Фиг.5-16
Решението е постичнато с оформяне на страничен канал в тях. Така долната страна на канала ще повдига лентата, страничната страна ще я води, а горната ще събува лентата от ловителите. Тяхното разположение не пречи на свободното движение на огънатите зони. Горната страна на повдигачите ще се използва за принудителното им прибиране при хода на долу, с което ще се отстрани опасността от деформация на лентата. След проверка за освобождаващи легла под огънатите части на лентата, се проектират формата и разполочението на пробиващи и изрязващи поансони - Фиг.5-17.
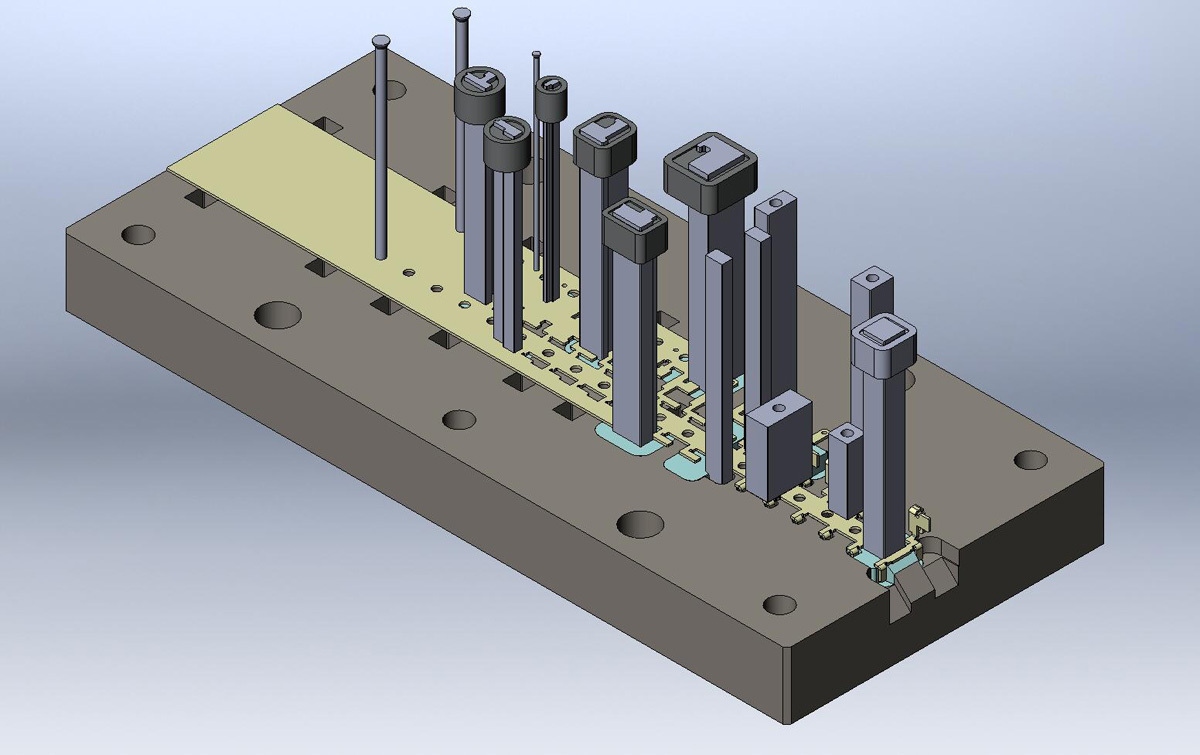
Фиг.5-17
За преодоляване силата на събуване при изваждането им от лентата, те са проектирани със запоени глави, които осигуряват необходимата площ за задържане в поансонодържача. Огъващите поансони са оформени без глави или стъпала, защото при заточване на режещите части те трябва да се скъсяват от горната страна. Тяхното задържане към поансонодържача се осъществява чрез изпълнени резбови отвори в горните им части, където ще се завият подходящи винтове. Това решение позволява безпроблено скъсяване на огъващите поансони от неработната (горната) страна. Окончателната проверка за необходимите освобождения се извършва след проектиране на водача за поансоните, който също е от технологично необходимите части, които контактуват с лентата и осигуряват необходимото разположение и точност - Фиг.5-18.
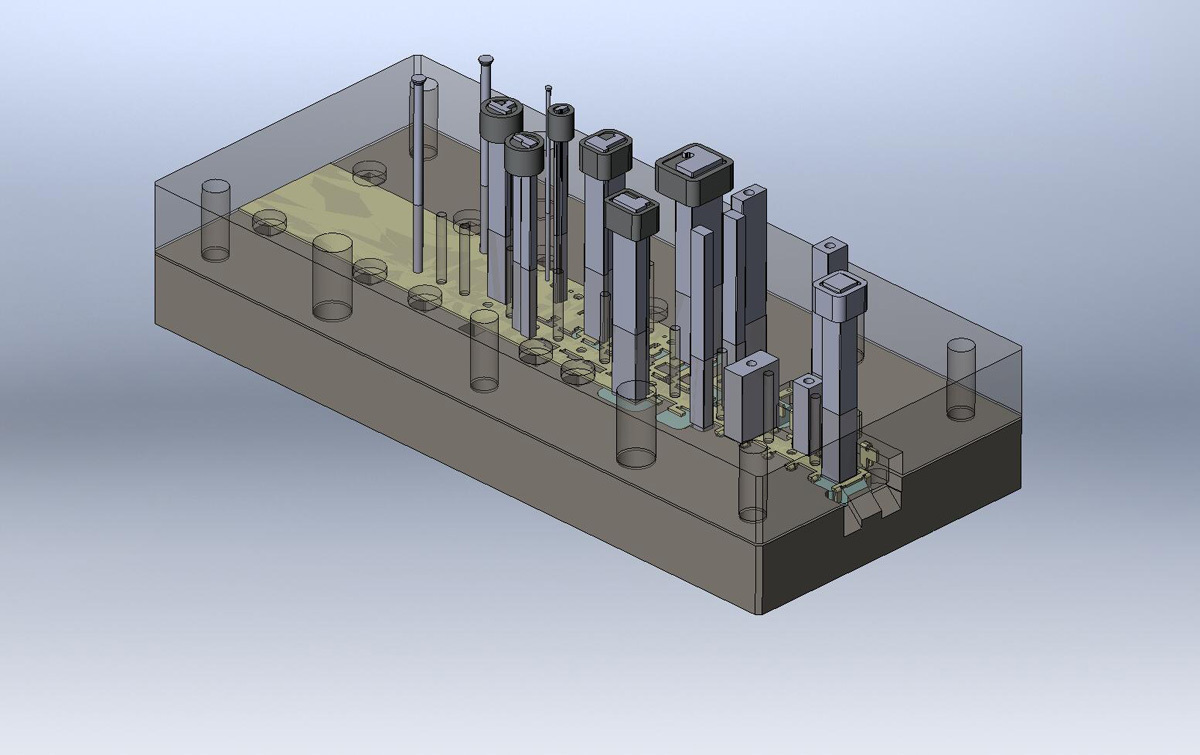
Фиг.5-18
Същата последователност се използва за проектиране на активните части за едно операционни инструменти (на пример пробиващи, огъващи, изтеглящи). Първоначално се конструира матрицата и към нея се добавят притискачи, фиксатори, избутвачи. След това се оформя поансона с включени към него ловители, притискачи, изхвъгачи (ако са неоходими). Проверяват се за освобождаващи легла, за възможно поставяне и изваждане на заготовката.
3.2. Проектиране на технологично необходими части.
Разработката на технологично необходимите части задължително включва оформяне на носещи детайли – плоча долна, плоча горна, плоча водеща (ако е необходима), на водещи колонки и втулки - Фиг.5-19.
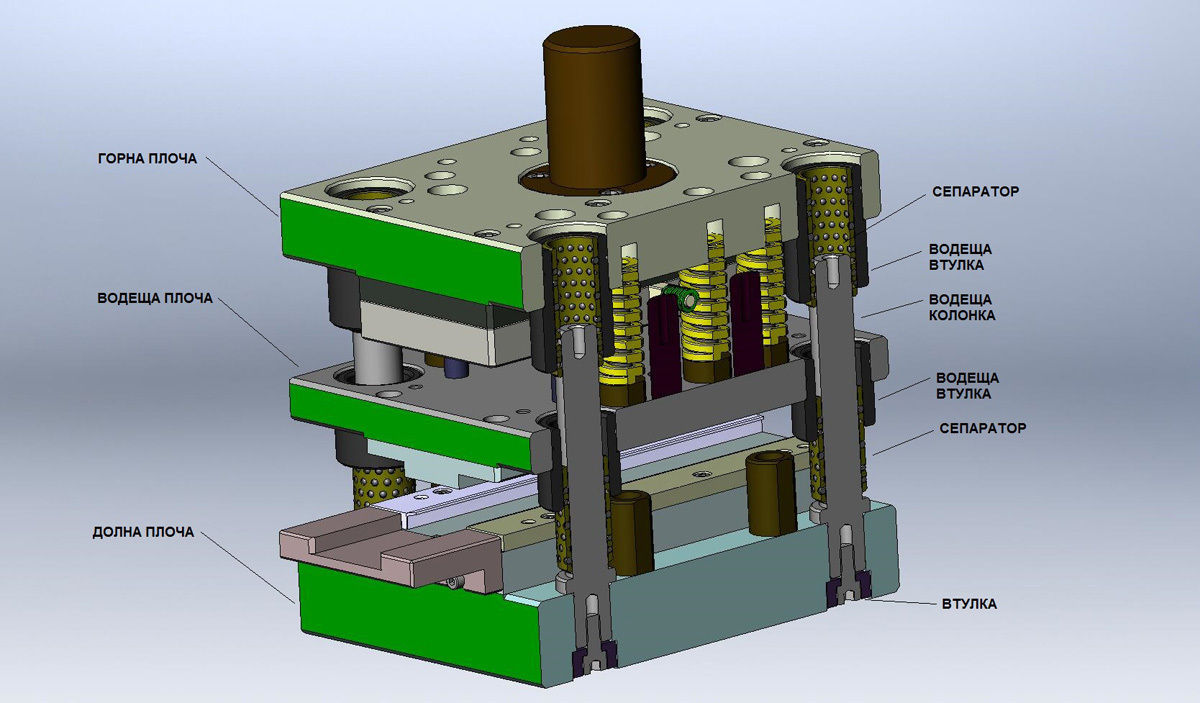
Фиг.5-19
При дебелина на материала под 1 mm и при щанци с последователно действие е препоръчително да се използват сачмени сепаратори за по-висока точност и по-лесно движение на подвижната част на инструмента. Дали ще се използва нормализиран блок, или ще се разработи оригинална конструкция, плочите трябва да се конструират с всички необходими отвори. Плочите от блока с водещи колонки и втулки трябва да се сглобят с матрицата и другите технологично необходими части, като притискачи, поансонодържачи, опорни или подложни плочи, лентоводачи, дорици, ограничители на хода и други в долен пакет - Фиг.5-20
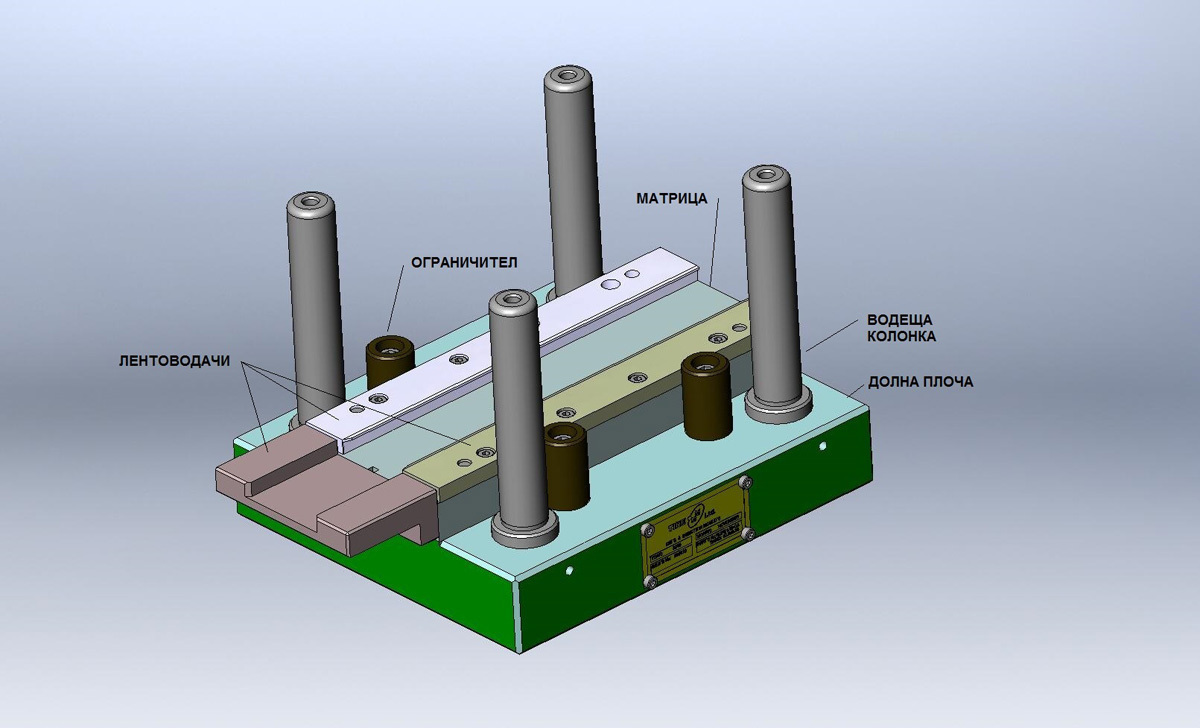
Фиг.5-20
и горен пакет на интрумента - Фиг.5-21.
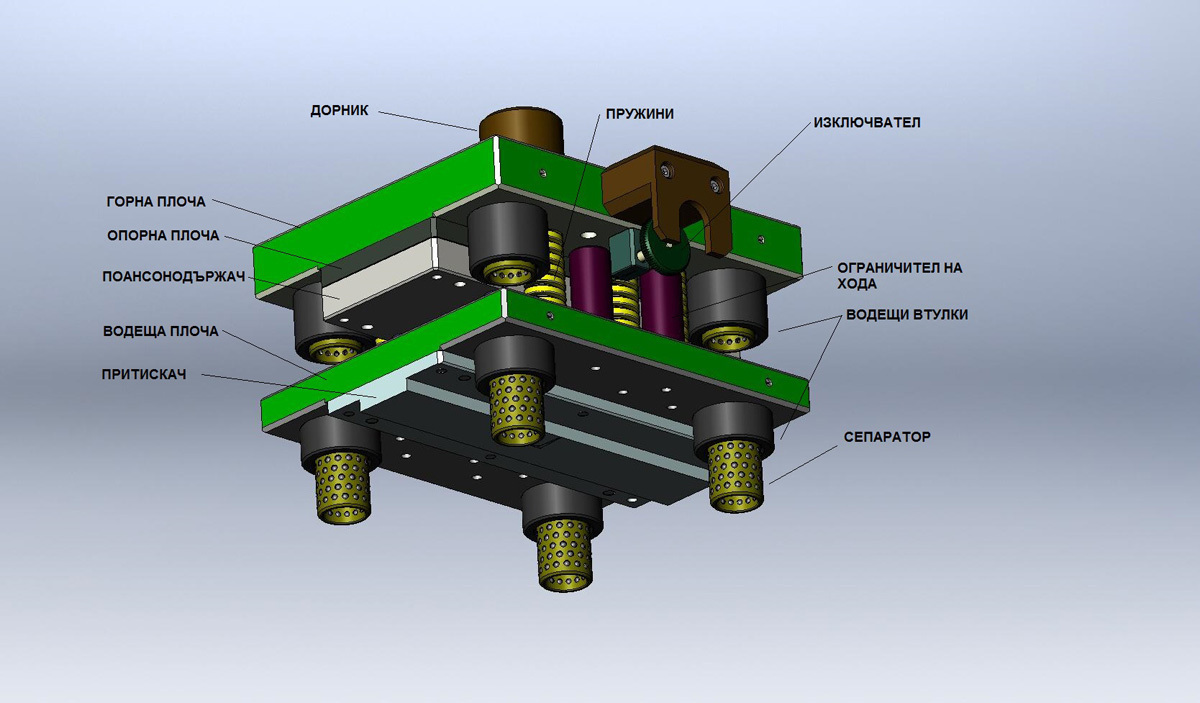
Фиг.5-21
Оригинално разработена конструкция на блок със заготовки за матрицата, притискача, поансонодържача и опорна плоча над поансоните, пружини и ограничители на хода е показана на Фиг.5-22.
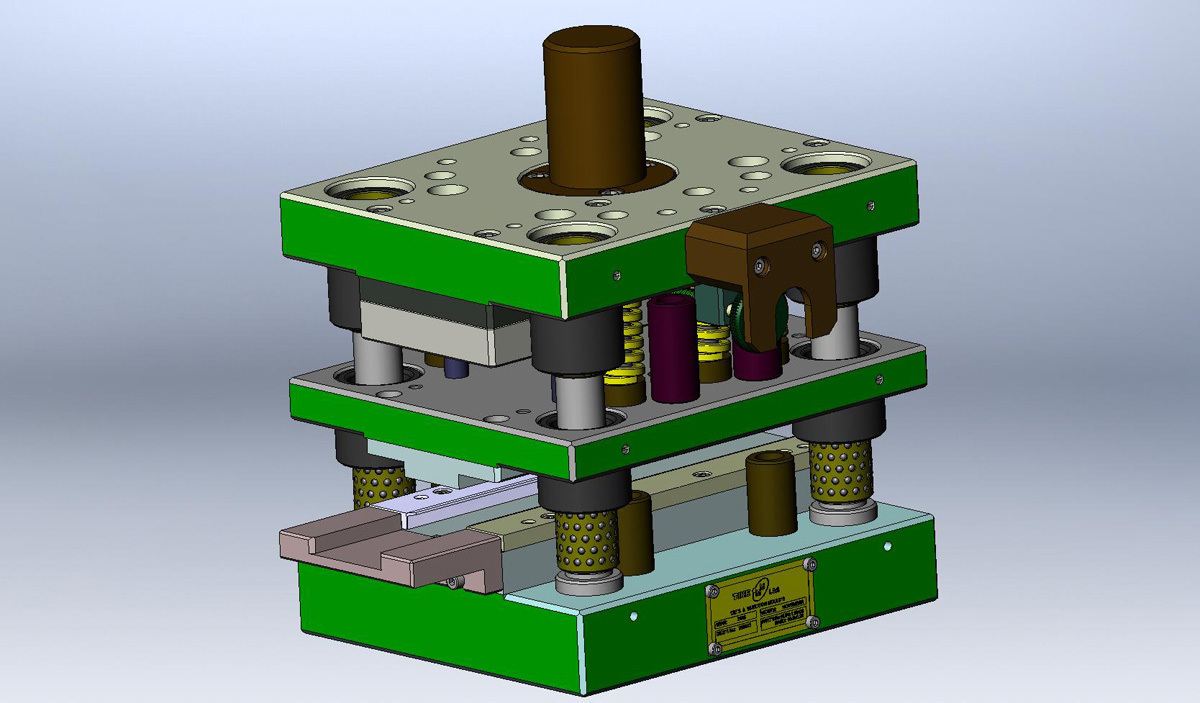
Фиг.5-22
Такъв подход позволява значително да се съкрати времето за разработка на блока, защото всички независими от активните части за конкретния детайл елементи, са оформени и включени в спецификацията на конструкцията. За плочите са създадени 3D модели и асоциативни 2D чертежи, които просто се допълват. Чрез промяна само на 5 параметра се извършва съгласуването на конструкцията за конкретен детайл:
– височините на ограничителите – за зададена дебелина на лентата;
– височините на втулки дистанционни под главите на винт дистанционен – за зададен ход на поансоните;
– височините ограничителите на хода – за зададен ход на поансоните;
– дебелината на шайбите под пружините – за желана сила на притискане;
– широчината на лентоводачите – за зададена широчина на лентата.
При проектиране на едно операционни инструменти (например пробиващи, огъващи, изтеглящи) най-често се ползват нормализирани блокове и плочи, които трябва да се сглобят в обща конструкция с активните части по описания начин за проверка на работоспособността и наличието на проблеми.
3.3. Проектиране или избор на спомагателни части.
Разработката на спомагателни части, като дорник за центроване и закрепване на подвижния пакет към пресата, ограничители на хода на поансоните, транспортни части, улеи, информационни табели или избора на буферни пружини и на скрепителни елементи са завършващ етап в оформяне на конструкцията на инструмента. Макар и посочен на последно място, този етап в много случаи трябва да се изпълнява успоредно с проектиране на технологично необходими части, поне доколкото се отнася до избора на пружини и скрепителни елементи. В противен случай, може да се стигне до парадокс – да са небходими винтове и пружини, за които в конструцията не е предвидено достатъчно място. При разработената конструкция от Фиг.5-22 предварително са заложени местата, броя и вида на буферните пружини за блока, показани на Фиг.5-23
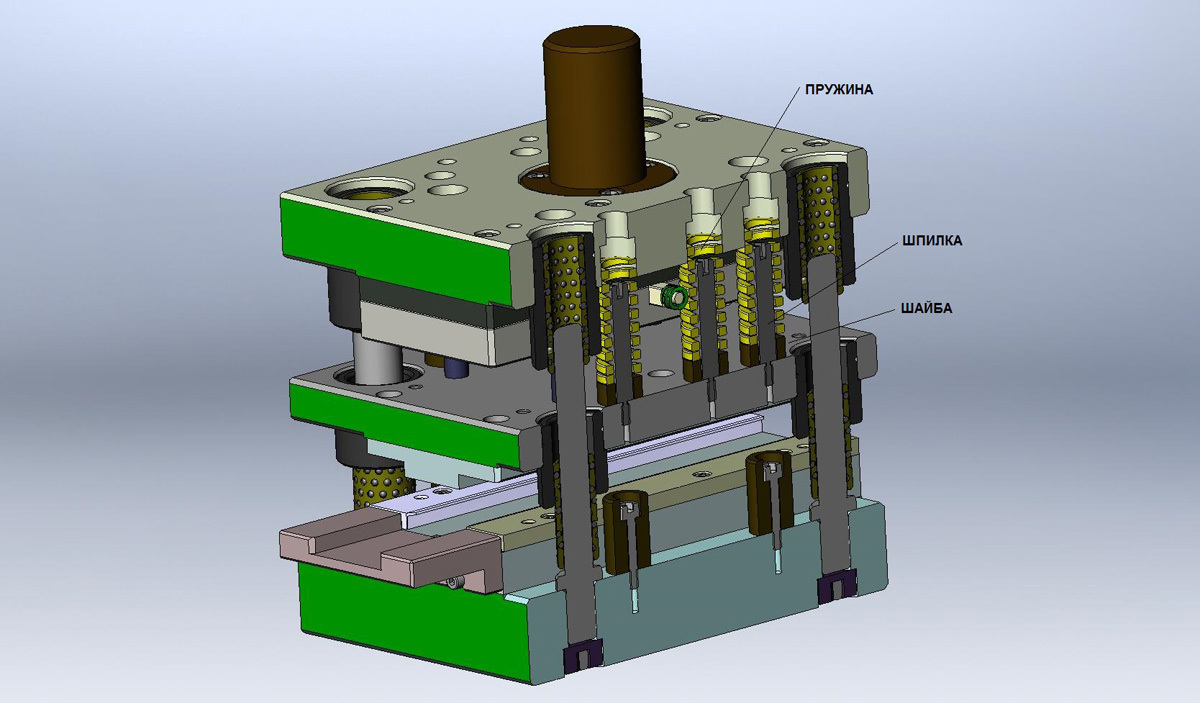
Фиг.5-23
с частите за тяхното прилагане – шпилка за центроване на пружината и подложна шайба за регулране предварителната сила на пружината и компенсиране на намалението на дължината на поансоните след заточване. Предварително са заложени също местата, броя и вида на дистанционните винтове и втулки, ограничаващи максималното разстояние между плочите при отваряне на блока (избрания ход на поансоните) - Фиг.5-24,
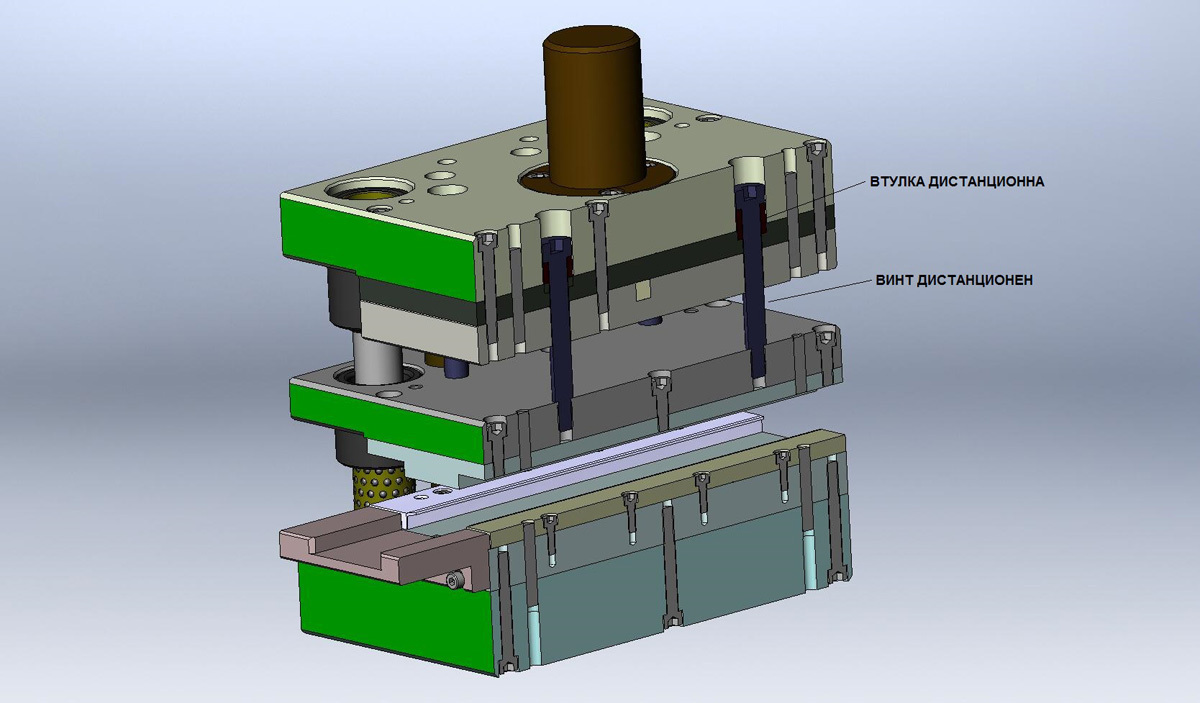
Фиг.5-24
а също и скрепителните елементи и местата на ограничителите. Използването на нормализира конструкция на блок изисква от конструктора да се съобрази с нейните ограничения и диапазаон на приложение още преди разработването на активните части и да избере друга, ако първата е неподходяща. Всички пружини под повдигачи или над ловители с тяхните части и скрепителни елементи, изключвателя за грешка в подаване на лентата - Фиг.5-25
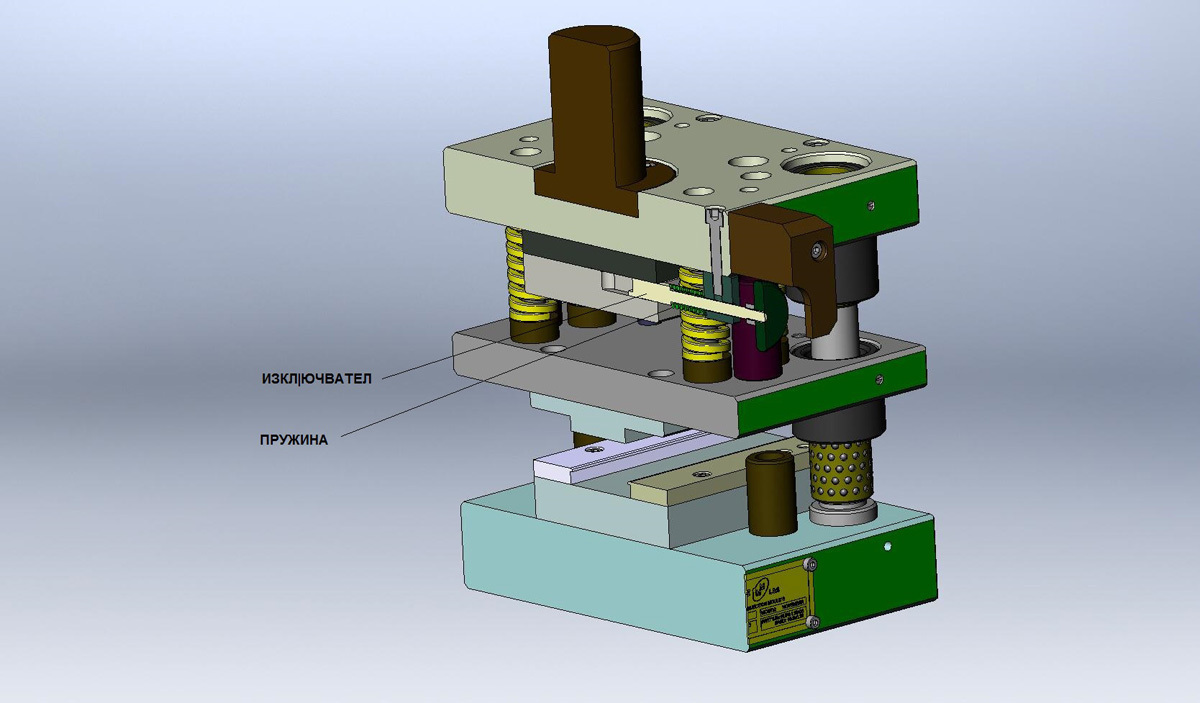
Фиг.5-25
се проектират инивидуално за конкретната технологична схема и се проверяват за проблеми между тях или с конструкцията на блока. Пружините се избират на база на техните размери, коравина и максимално допустима деформация. Задължително се осигурява предварително свиване (за пружини по ISO 10243 минимум 5% от свободната дължина) при което пружинната сила е по-голяма от минимално необходимата (например сила на притискане или събуване). След предварителното свиване, пружината трябва да осигури необходимия ход, без да е достигнала да максимално допустимата си деформация.
3.4. Изпълнение на необходимите изчисления.
Всички изчисления се извършват преди или паралелно с конструирането на съответнята част, при условие, че са извести необходимите изходни данни. Когато има непълнота в тях, след конструирането и уточняването им, се извършват проверочни изчисления, оценяващи допустимостта на приетите решения. Изчисленията са разнообразни и няма стандартни изисквания за тях – на практика зависят от квалификацията, от разполагаемото времето и желание на конструктора. Тяхната цел в много от случаите е да докажат, че субективно избраните размери на база натрупан опит, са преоразмерени. Изпълняваните изчисления условно се разделят на три основни типа:
– геометрични или кинематични;
– якостни и деформационни;
– точностни.
3.4.1. Кинематични изчисления – те определят връзката между задвижващия и предаващия край на гърбичен, лостов или клинов механизъм. Пример за такива изчисления на лостовия преобразуващ механизъм за детайла от Фиг.3-1 с технологична схема от Фиг.3-2 е показан на Фиг.5-26.
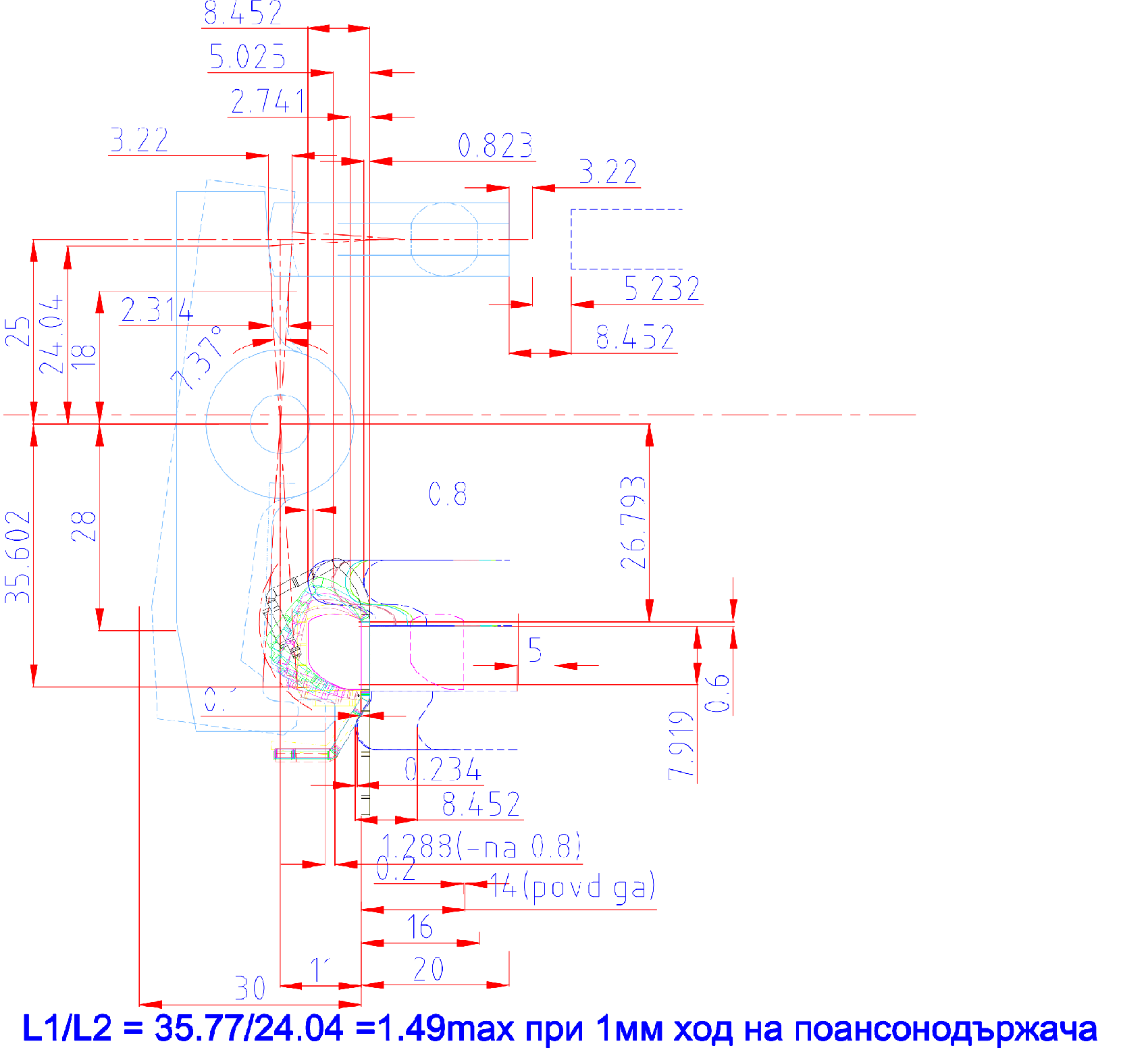
Фиг.5-26
Друг пример за кинематично свързани изчисления е определяне на преместването на сепаратора спрямо водещата втулка при зададен ход на горния пакет на инструмента (виж Фиг.5-21). То е равно на половината от хода на водещите втулки.
3.4.2. Геометрични изчисления – те най-често са свързани с определяне ходовете на повдигачи, избутвачи, притискачи.
3.4.3. Якостни изчисления – те са свързани главно с проверка на активните части като:
– проверка на тънки поансони за загуба на устойчивост под действието на силите на рязане;
– проверка на тънки режещи поансони за максимално допустимо налягане на режещите ръбове под действието на силите на рязане и избор на инструментален материал;
– проверка на опорните повърхнини на поансоните и вложките на смачкване под действието на технологичните сили;
– проверка на задържащите повърхнини на поансони и вложки на смачкване под действието на силите на събуване или избутване;
– проверка на критични сечения на вложки на огъване под действието на технологичните сили;
– проверка за центъра на технологичните сили на инструмента – принципа е същия, като описания за силите от пробиване и изрязване в т. 2.2.4, но тук трябва да се разгледа равновесието на всички технологични сили в различни моменти от работния ход;
– проверка на допустимите сили и деформации за избраните винтови, тарелчати или полеуретанови пружини.
3.4.4. Деформационни изчисления – те са свързани с определяне на максималните деформации, предимно на части от блока – долна плоча, водеща плоча, притискач, под действието на технологичните сили или на водещи колонки от странично натоварване. Понякога на такива изчисления трябва да се подлагат и тънки огъващи вложки и поансони. Поради сложността на задачата и отсъствието на точни аналитични формули, най-добрия подход за решение е използването компютърни програмни пакети, прилагащи метода на крайните елементи (Finite Element Analysis). Практическото използване на метода често налага известно опростяване в 3D моделите и много внимателно дефиниране на граничните условия, но получените резултати позволяват да се избере оптимално решение.
3.4.5. Точностни изчисления – те определят точността на щанцования детайл или допускa на определено затварящо звено в размерни вериги. Пример за необходимост от такова изчисление, е определената стойност за корегиране на разгъвката на огънатия детайл ПЛАНКА след пружиниране, за да се получи в зададените граници размера на процепа 6.4 mm - Фиг.5-27.
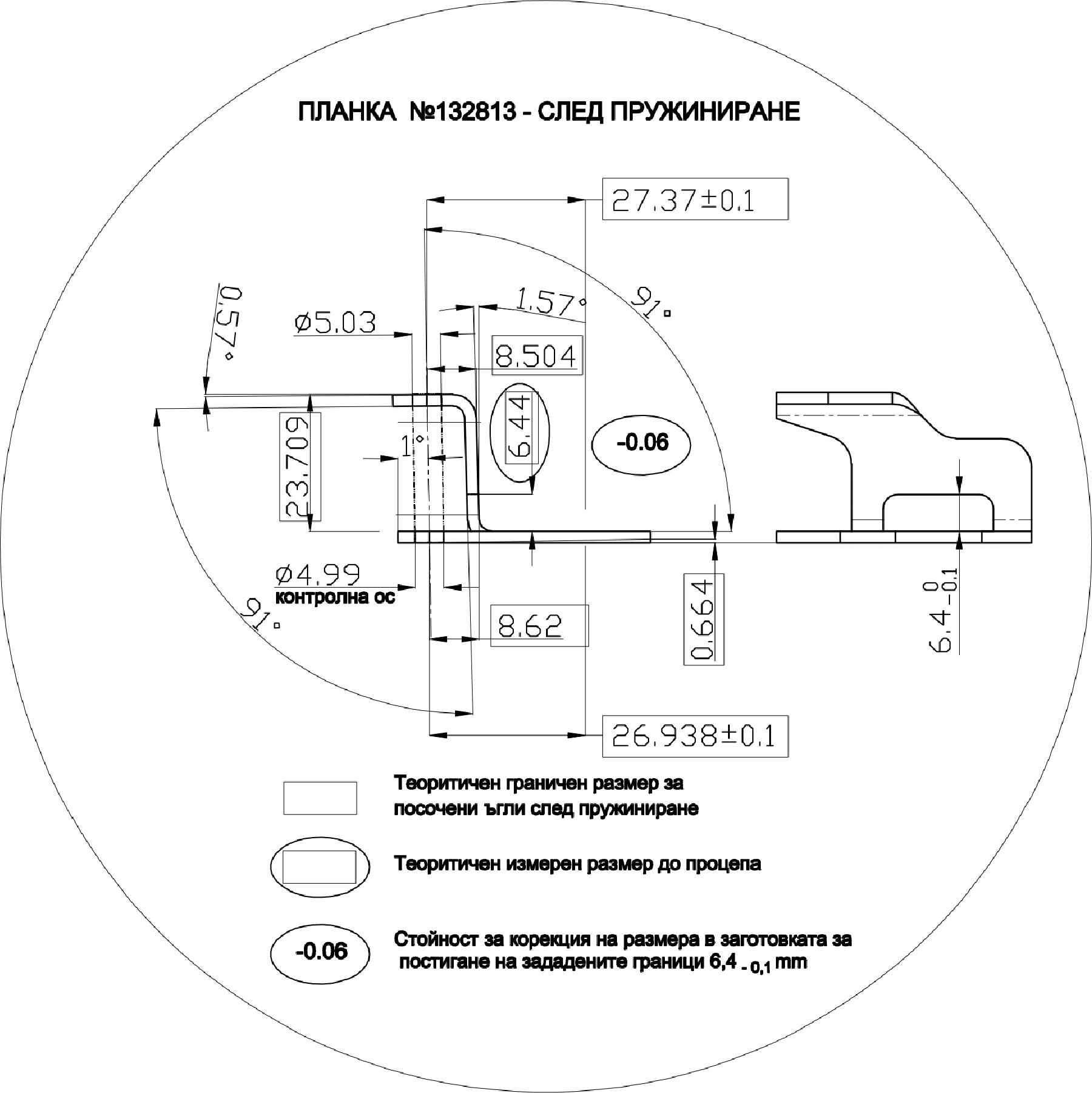
Фиг.5-27
3.5. Разработване на конструктивна документация.
Създаването и размножаването на 2D чертежи все още е основен момент при изработката на инструменти за щанцоване. До голяма степен това е резултат на висок процент на универсални металорежещи машини без ЦПУ, използвани при тяхната изработка и на голямото разнообразие от процеси на щанцоване. В съответствие със съществувщите стандарти и практика, конструктивната документация включва:
3.5.1. Сборни чертежи – те представят инструмента в 3 проекции заедно с необходимите разрези, сечения и изнесени увеличени елементи. Задължително, всички детайли (или възли и групи) са номерирани с отделни позици, позволяващи недвусмисленто им идентифициране и описание, като наименование, количество, материал, номер на означение, стандарт или доставчик. Доколкото щанците са обект на единично производство, много фирми са възприели сборните чертежи като основен и единствен коструктивен документ. Това предполага, че освен необходимите сглобки, присъединителни и габаритни размери, на сборните чертежи трябва да се нанесат всички размери, достатъчни за изработка на изграждащите конструкцията части. Такова решение е приемливо за инструменти, съдържащи много висок процент на стандартизирани елементи и нормализирани блокове, които ще се изработват от един инструменталчик в сравнително малка, тясно специализирана фирма, или бригада от няколко човека. Подобно решение обаче, е не приемливо за голяма фирма без тясна специализация в областта на инструменталната екипировка за щанцоване, или при изполването на коопериране на детайли и обработки с външни под доставчици.
Пример за сборен чертеж за детайл INCISIVO е показан на - Фиг.5-28 (поглед от горе и частични разрези С-С и D-D), Фиг.5-29 (напречен разрез А-А) и Фиг.5-30 (надлъжен разрез В-В).
Щанцата използва конструкцията на блока от Фиг.5-22.
3.5.2. Спецификации на използваните детайли – те описват всички налични оригинални, стандартни, нормализирани и покупни детайли, техните наименования, коструктивни номера, или означение по стандарт, или от каталога на съответния доставчик, количеството им в инструмента. Стандартната форма предвижда спецификациите да са на отделни формати от сборния чертеж, но е допустимо техните таблици да се разполагат и върху него. Някои фирми включват в спецификациите освен материалите за оригиналните детайли и допълнителни графи за вида и размерите на съответните заготовки. Това може да е полезно при организиране на процеса за изработка, защото не са необходими чертежи за осигуряване на доставките. Пример за спецификация за детайл INCISIVO е показан на - Фиг.5-31.
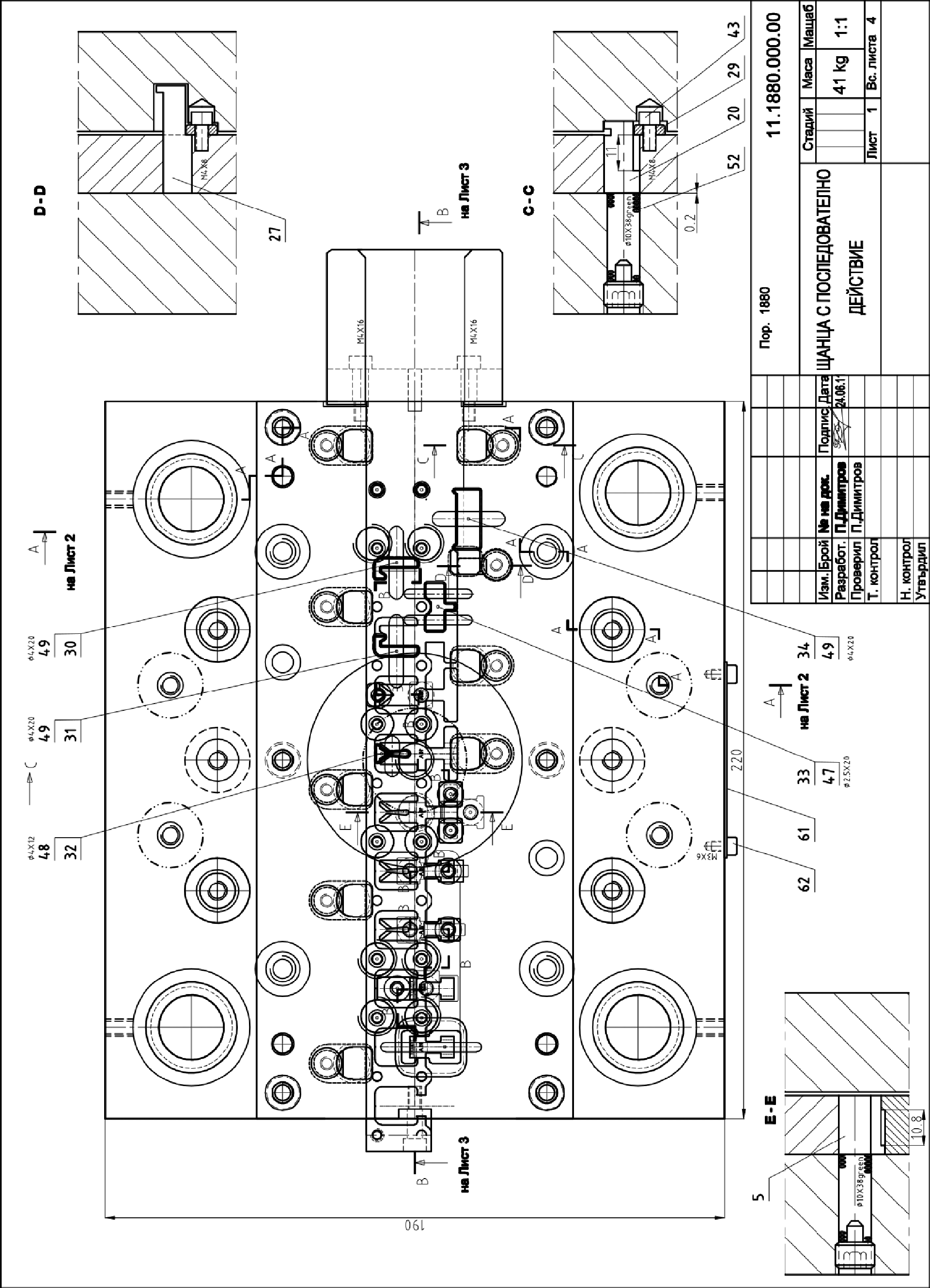
Фиг.5-28
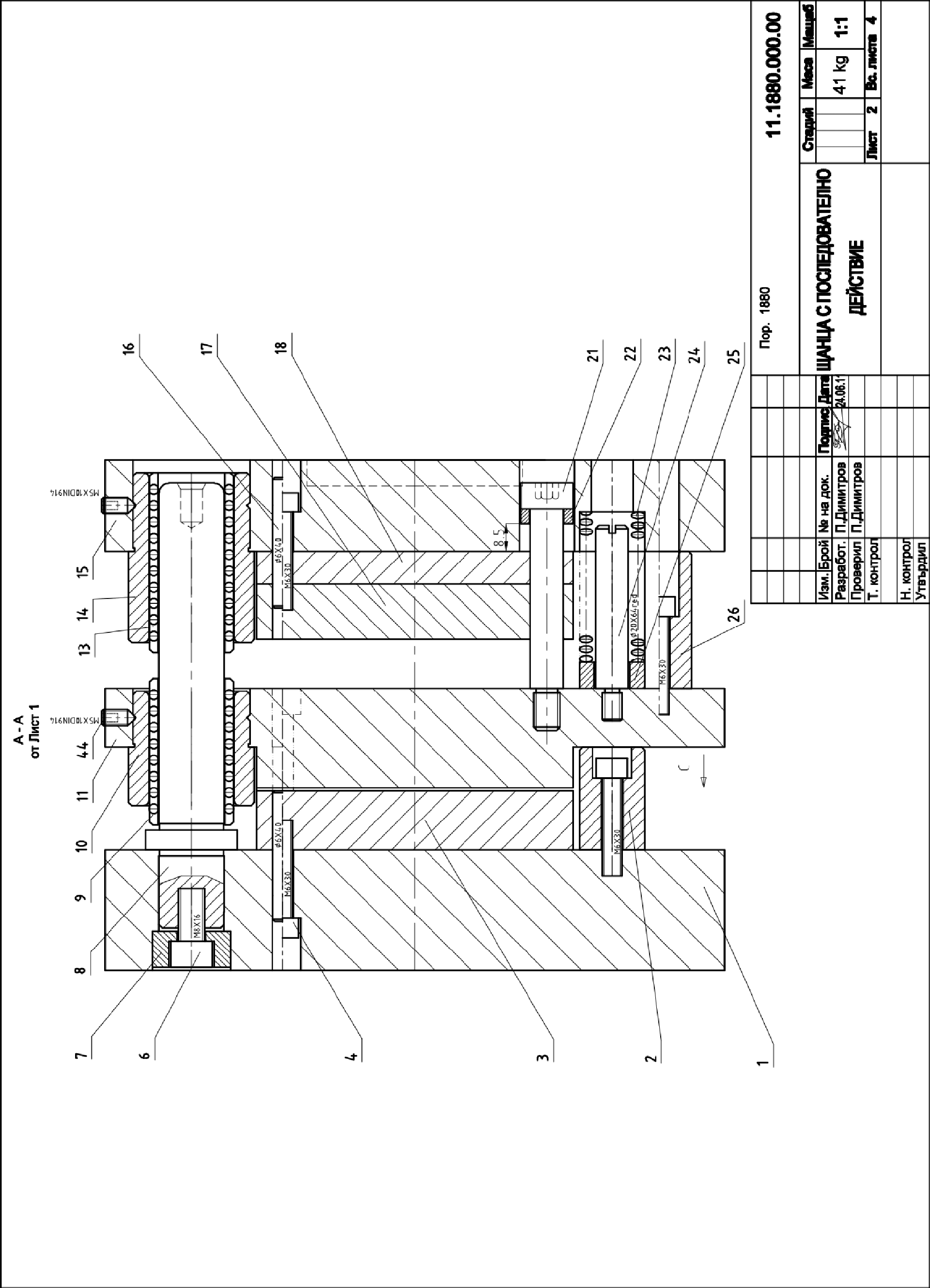
Фиг.5-29
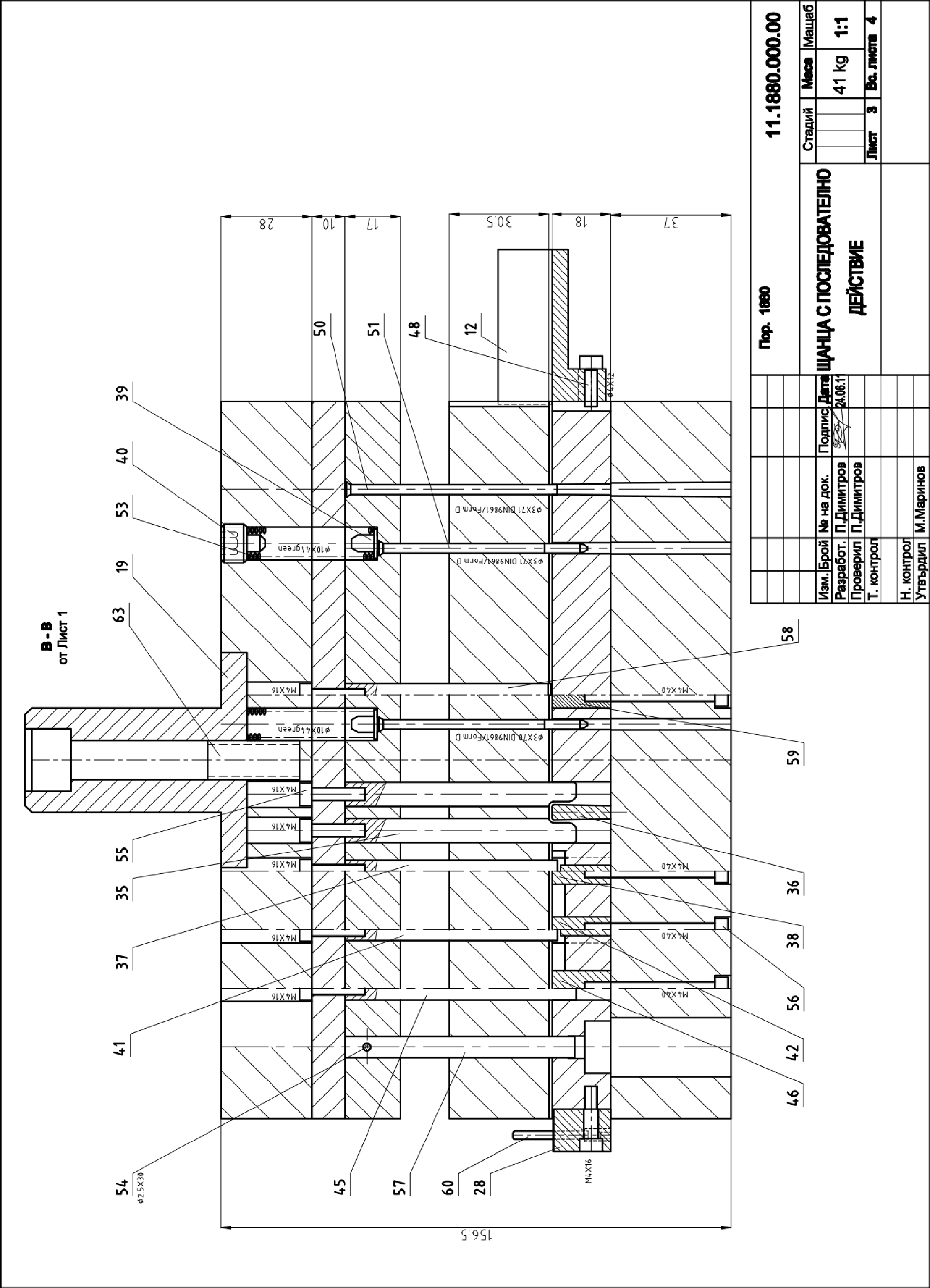
Фиг.5-30
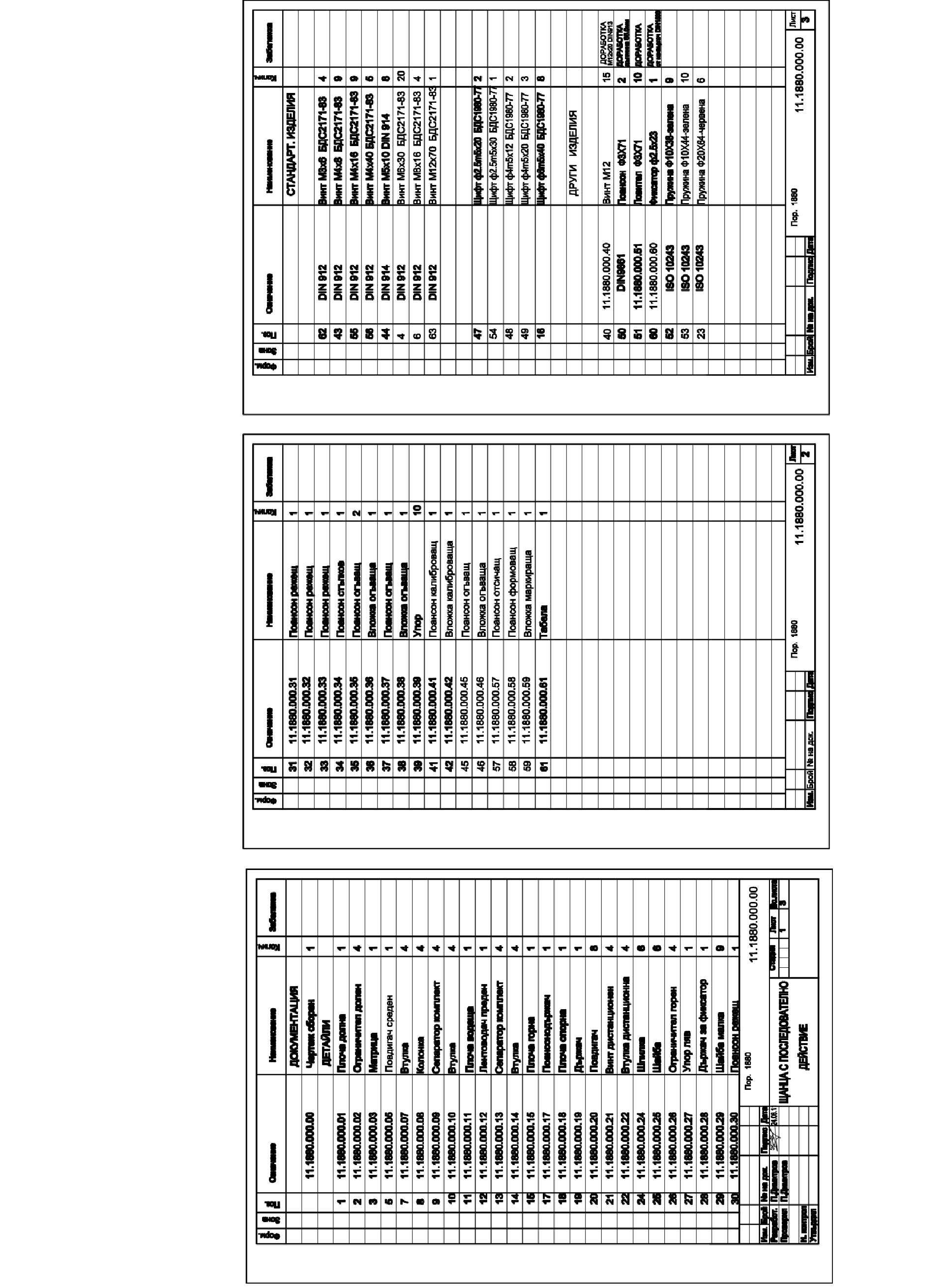
Фиг.5-31
3.5.3. Технологична схема на лентата или на заготовката, след извършената от инструмента операция – те показват всички технологични преходи на лентата или схемата на заготовката, повърхнините за базиране, получаваните размери и техните допуски. Важно е нанесените размери да могат да се контролират, като е посочен и метода, когато е необходимо (на пример съосни отвори на огънат детайл, контролирани чрез цилиндричен калибър с посочен размер (виж Фиг.4-6 – №02944-00). Полезна практика е схемите да съдържат технически данни за процесите на щанцоване, инструмента и пресата. Примерен чертеж на технологична схема за изработка на детайл INCISIVO е показан на Фиг.5-7.
3.5.4. Детайлни чертежи (работни чертежи) – те показват всички оригинални или допълнително обработени стандартни и покупни детайли с необходимите проекции, погледи, разрези, сечения, изнесени увеличени елементи, таблици с кординати и диаметри на отвори, размери с допуски за изработка, грапавост и отклонения от геомртричната форма, технически изисквания за материал, термообработка, маркиране, съвмесна обработка с друг детайл, указания за уточняване на определени размери след проба и други. Правилата за машиностроителните чертежи се прилагат и тук, но характера на единично производство и използваните технологии позволяват частично оразмеряване на някои части – само габаритни размери и големина на офсет спрямо друг, напълно оразмерен детайл, използван за база. Това е особено разпространен метод при щанците за изрязване и пробиване (особено за профилни отвори), където са оразмерени само поансоните - Фиг.5-32, а в останалите детайли, като матрица - Фиг.5-33, притискач, поансонодържач, долна плоча, водеща плоча са показани само контури с отбелязана стойност и посока на офсет. Това позволява да се икономисва време за изработка на управляващи програми за машини с ЦПУ и отстранява проблемите, породени от технически грешки при конструиране или програмиране. Много фирми оразмеряват само габаритните размери и кординатите на базови точки за отворите за този вид инструменти, за останалите, включително поансоните се използва компютърния 2D модел на самия детайл.
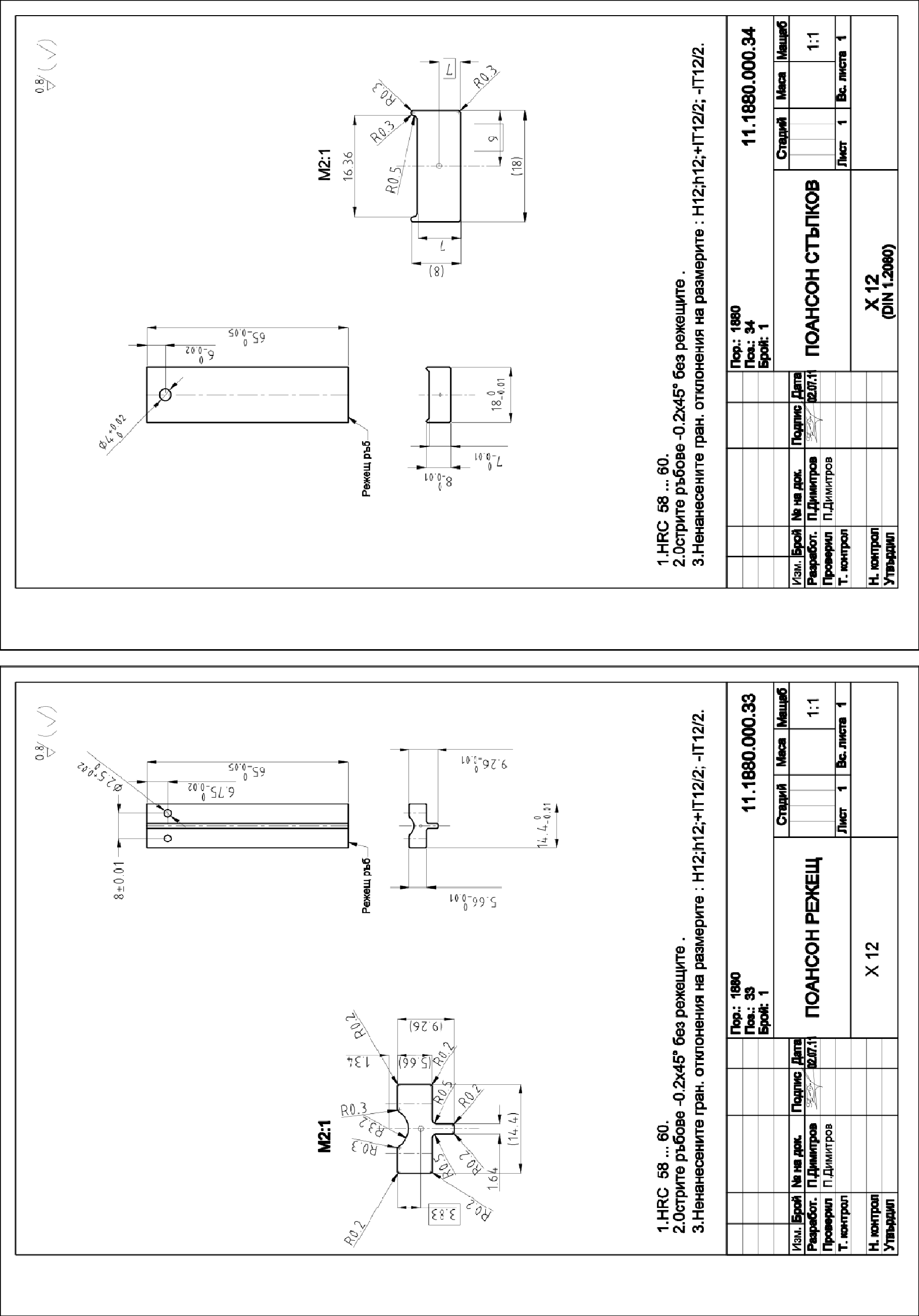
Фиг.5-32
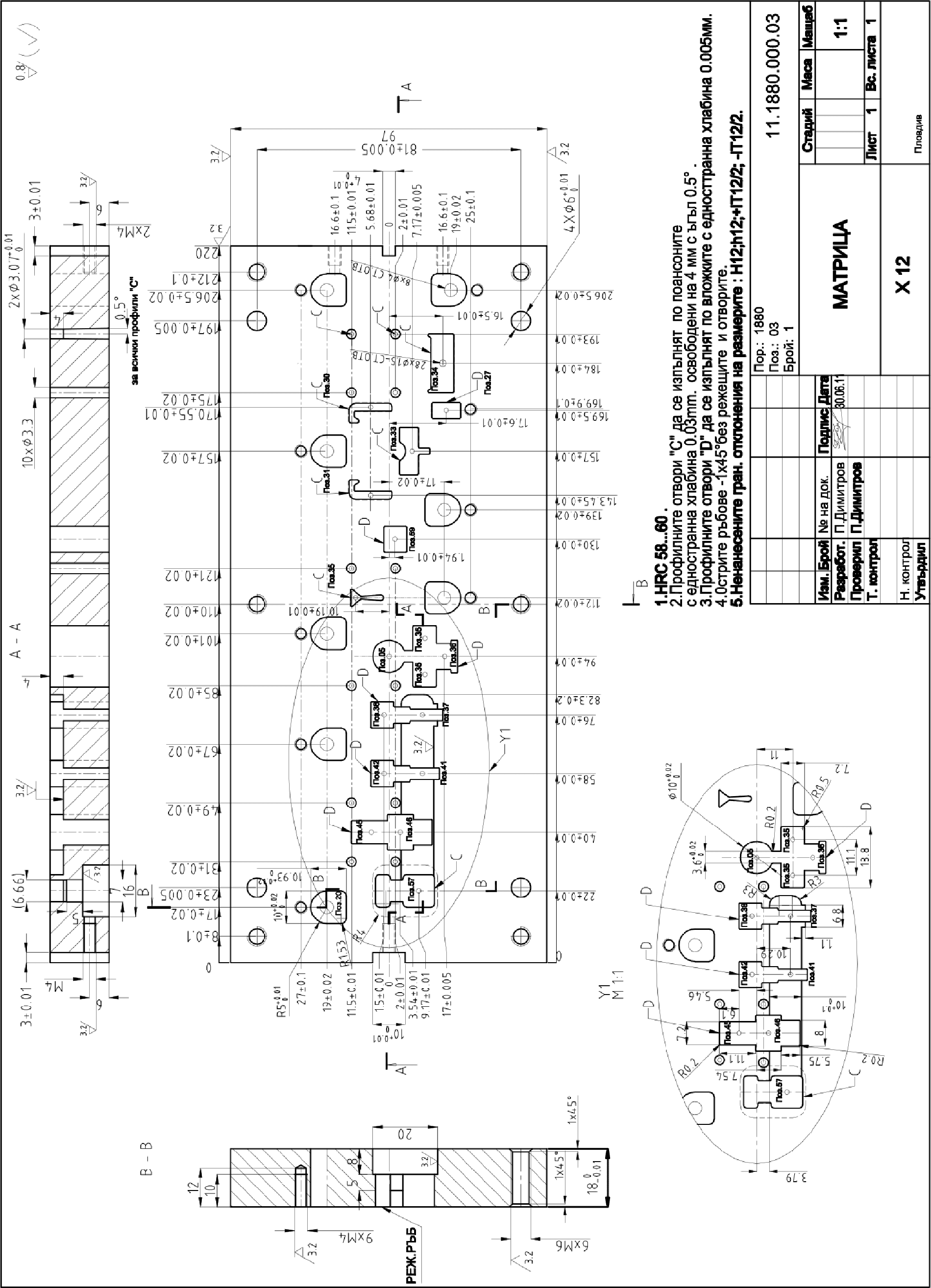
Фиг.5-33
3.6. Използване на CAD-CAM системи.
С развитието на комютърните технологии в инструменталното производсто масово се използват CAD системи (комютърни системи за проектиране) или CAD-CAМ системи (комютърни сисреми за проектиране и производство).Всички известни сиситеми oт среден клас притежават модул за създаване на листови детайли със съответни програми за определяне на плоска разгъвка (Solid Works, Solid Edge). Най-разпространените CAD-CAМ-SAE сиситеми oт висок клас, като NX, CREO (ProE), CATIA, VIZI CAD CAМ, дори имат модул за разработване на щанцови инструменти с последователно дейстие (Progressive die dissign). Тези модули представляват набор от диалогови прозорци с менюта, в които е събрана необходимата входна информация, след чието въвеждане се автоматизира решаването на определена задача, например частично или цялостно разгъване на участъци от модела на детайла, размножаване или преместване по стъпки, създаване на контури на поансони, изрязващи отпадъка около разгъвката, построяване на вложки и отвори за ловители, автоматично разпростаранение на необходимите отвори за поансоните със съответната хлабина във всички плочи и други. Те облекчават и автоматизират работата на конструктора при проектирането на технологичната схема и при конструиране на активните части, предлагайки избор от готови решения. Обикновено използват нормализирани блокове от каталозите на някои от изброените по-горе фирми за стандартизирани елементи за щанци, но могат да използват и създадени оригинални конструкции. Асоциативността между модела на обработвания детайл, 3D модела на технплогичната схема и конструкцията на инструмента с 2D чертежите, позволяват изключително бързо отразяване на извършваните промени. За съжеление, тези модули не могат да вземат решение вместо конструктора и успешното им приложение зависи от неговата компетентност в областта на пректирането на инструменти за щанцоване и неговите познания за съответната система. Основен недостатък при тях е, че високия клас системи, снабдени с тези модули, са много скъпи. Освен това, изключенията от правилата при разработка на щанцовите инструменти се налагат често, което значително намалява ефективността от високата степен на автоматизация при решаване на типични задачи и прилагане на готови решения.
4. Технолочична подготовка за изработка на щанците.
Изработката на инструментална екипировка е свързана с необходимост от планиране на доставка на материали, последователност при производство и графици за изпълнение. Добрата подготовка намалява рисковете и подобрява управляемостта на изработката.
4.1. Анализ на технологичността на конструкцията.
Инструменталното производство, по-специално изработката на щанци, е тясно специализиран процес, характеризиращ се с използването на универсално оборудване с висока точност, обслужвано от изключително квалифициран и опитен персонал. Независимо от това, не винаги наличното оборудване и квалификация на персонала могат да отговорят адекватно на огромното разнообразие от конструкции на инструменти за щанцоване и изисквания към тях. Това налага ясно да се разграничт възможностите за изработка при конкретните условия и необходимостта от използване на външен доставчик или под изпълнител за всеки инструмет.
Аналзът на технологичността на конструкцията дава отговор на въпросите – може ли да се изработи в конкретните условия и какво да се промени, за да е по-лесна изработката, без да се влошат бъдещите експлоатационни качества на инструмента. Накратко ще бъдат разгледани основните моменти, на които трябвада се бърне внимание при този анализ:
– Габаритните размери на инструмента и на най-големите му детали. За България размери над 1000х800х600 mm са проблемни за изработка. Най-разпростараненото оборудване е за габарит до 800х500х400 mm. Възможно решение е разделяне на инструмента на отделни под-инструменти (модулна конструкция). В тези конструкции обикновенно остават 1-2 голямо габаритни носещи детали, най-често плочи.
Пример за такава конструкция на щанца с последователно действие за детайл “CONTACT - заготовка 1” от Фиг.5-34
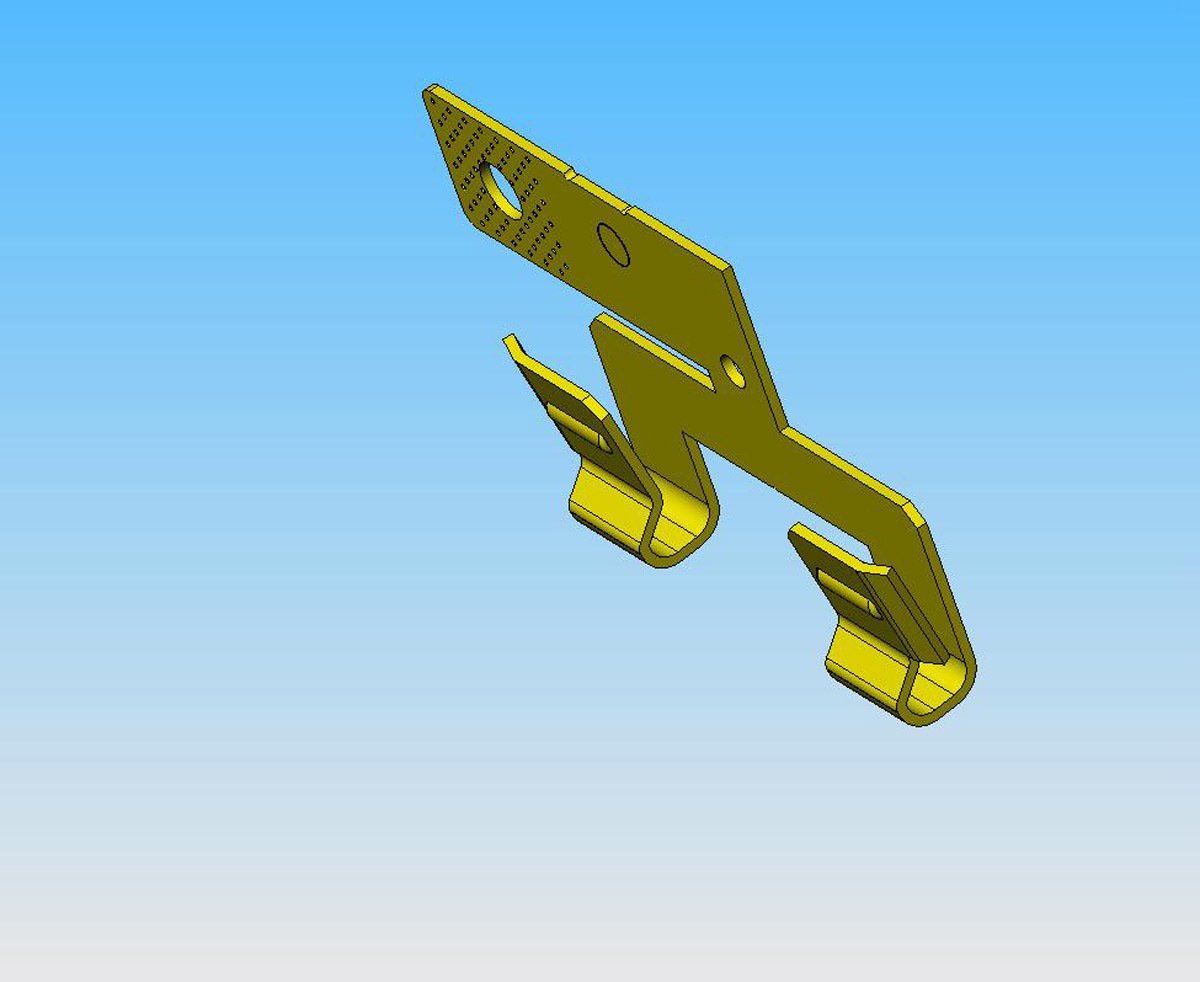
Фиг.5-34
и нейната лента от Фиг.5-35
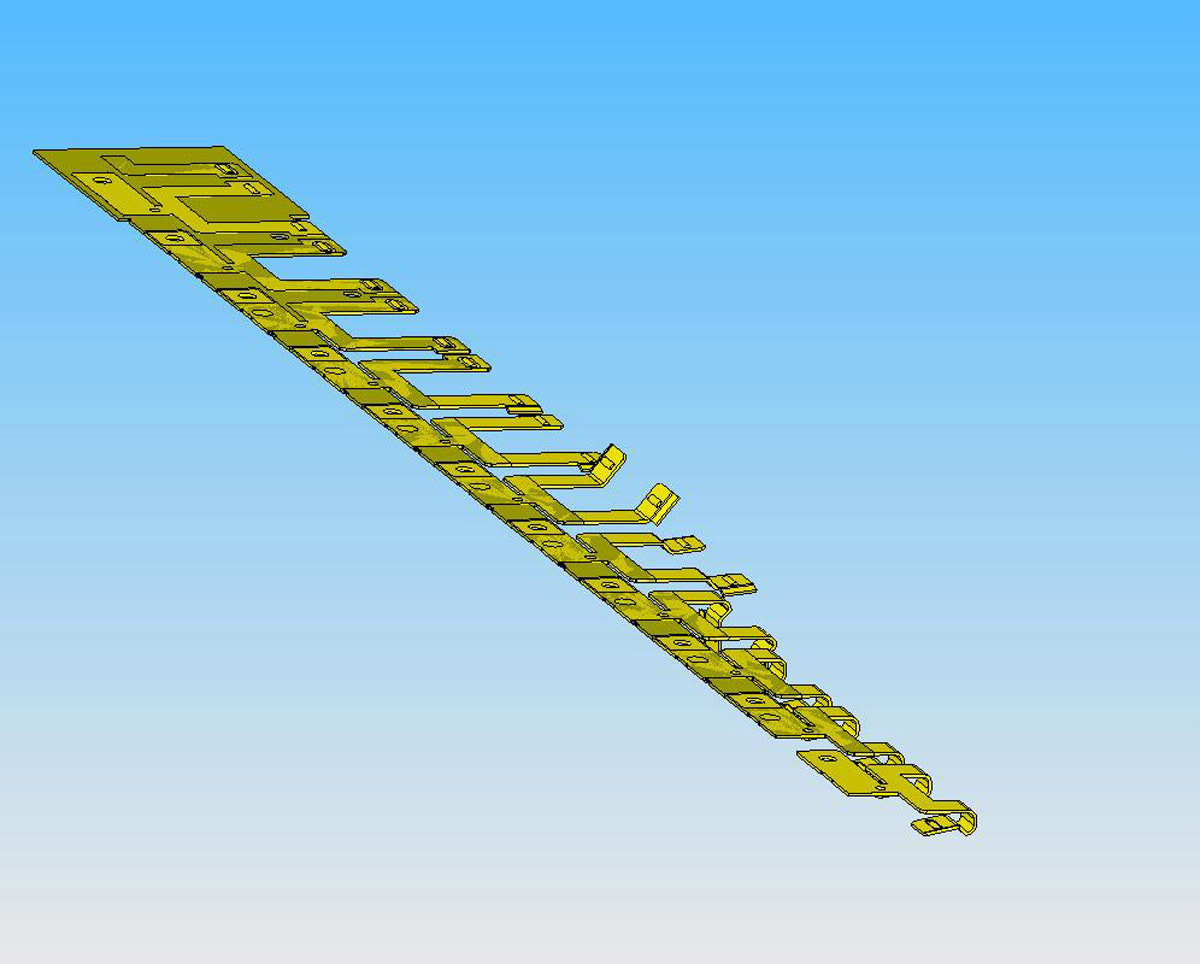
Фиг.5-35
е показан на Фиг.5-36.
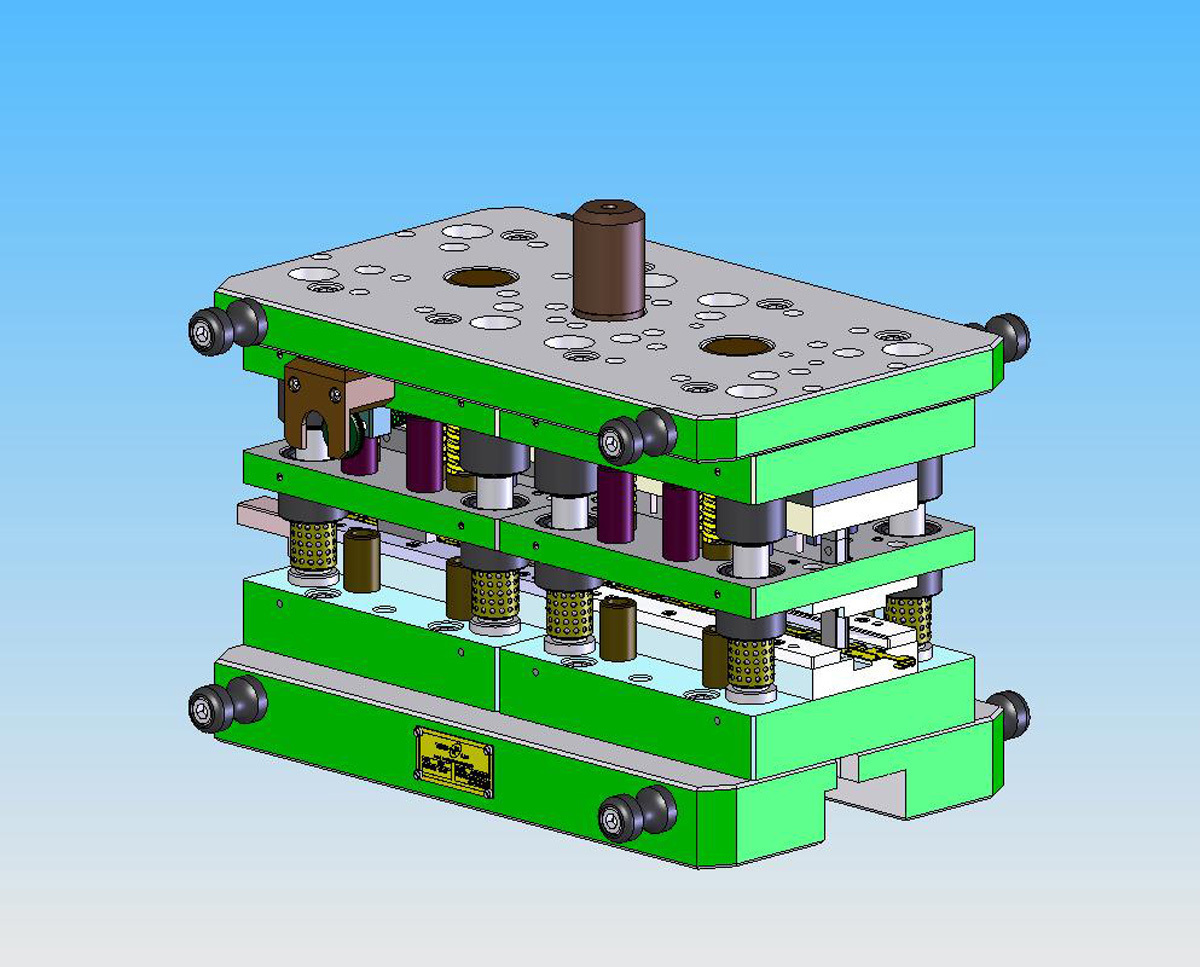
Фиг.5-36
Тя е съставена от два инструмента – преден блок - Фиг.5-37
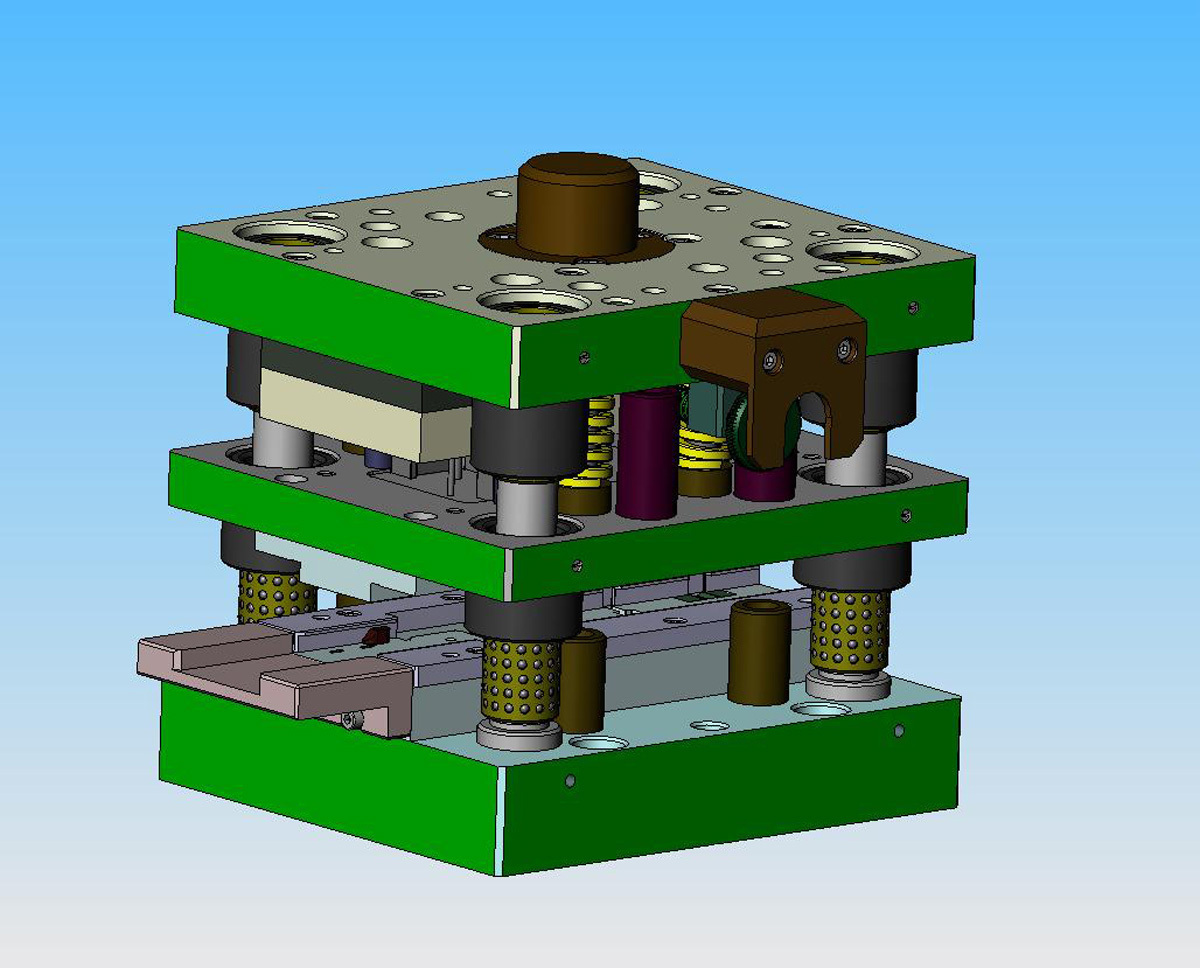
Фиг.5-37
и заден блок - Фиг.5-38,
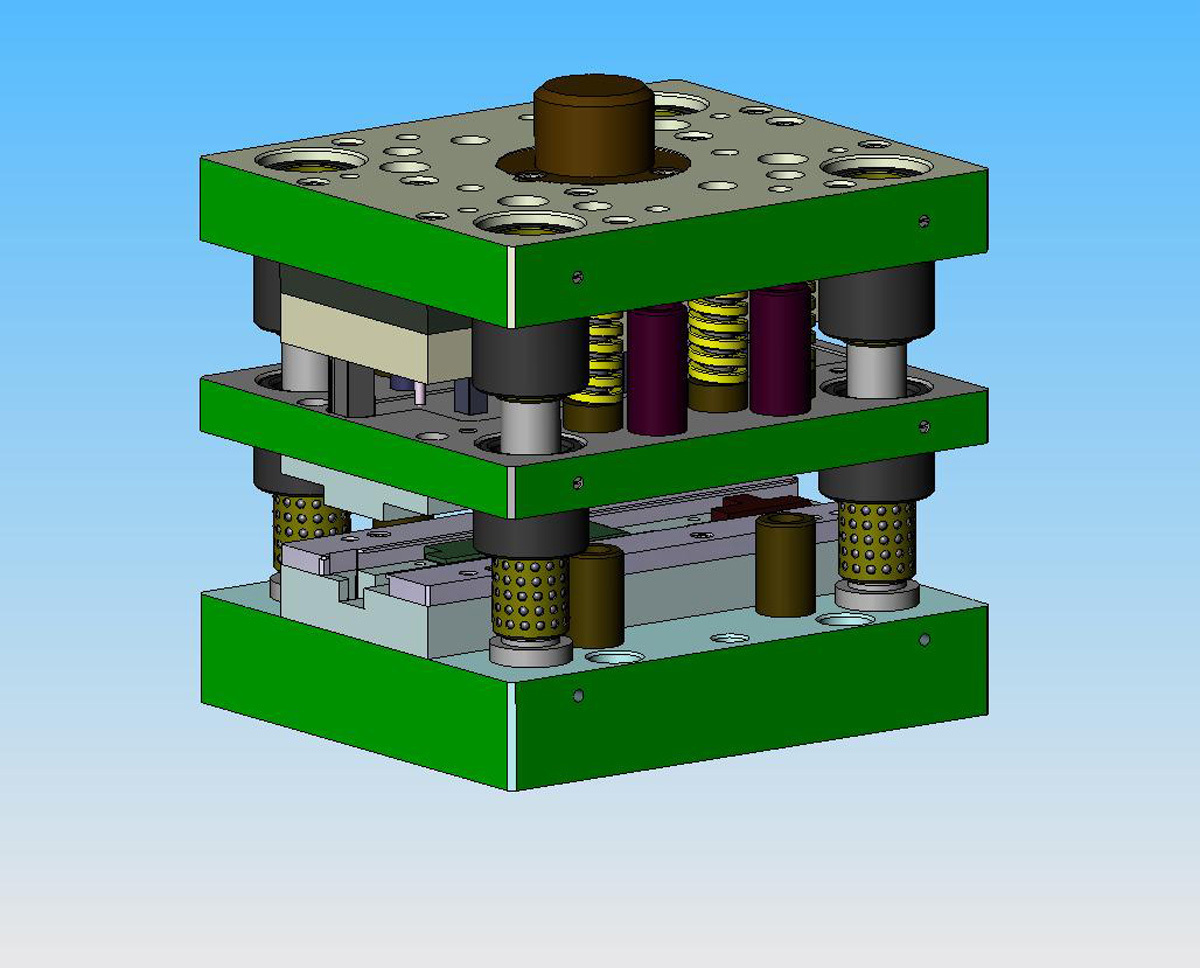
Фиг.5-38
обединени от общи долна и горна плочи. Удобството тук е лесното им обслужване и ремонт. Освен това, те са проектирани да могат да работят независимо един от друг като самостоятелни инструменти. Първо лентата се щанцова с преден блок, след което тя се обработа чрез заден блок до получаване на изхода на крайната заготовка - Фиг.5-39.
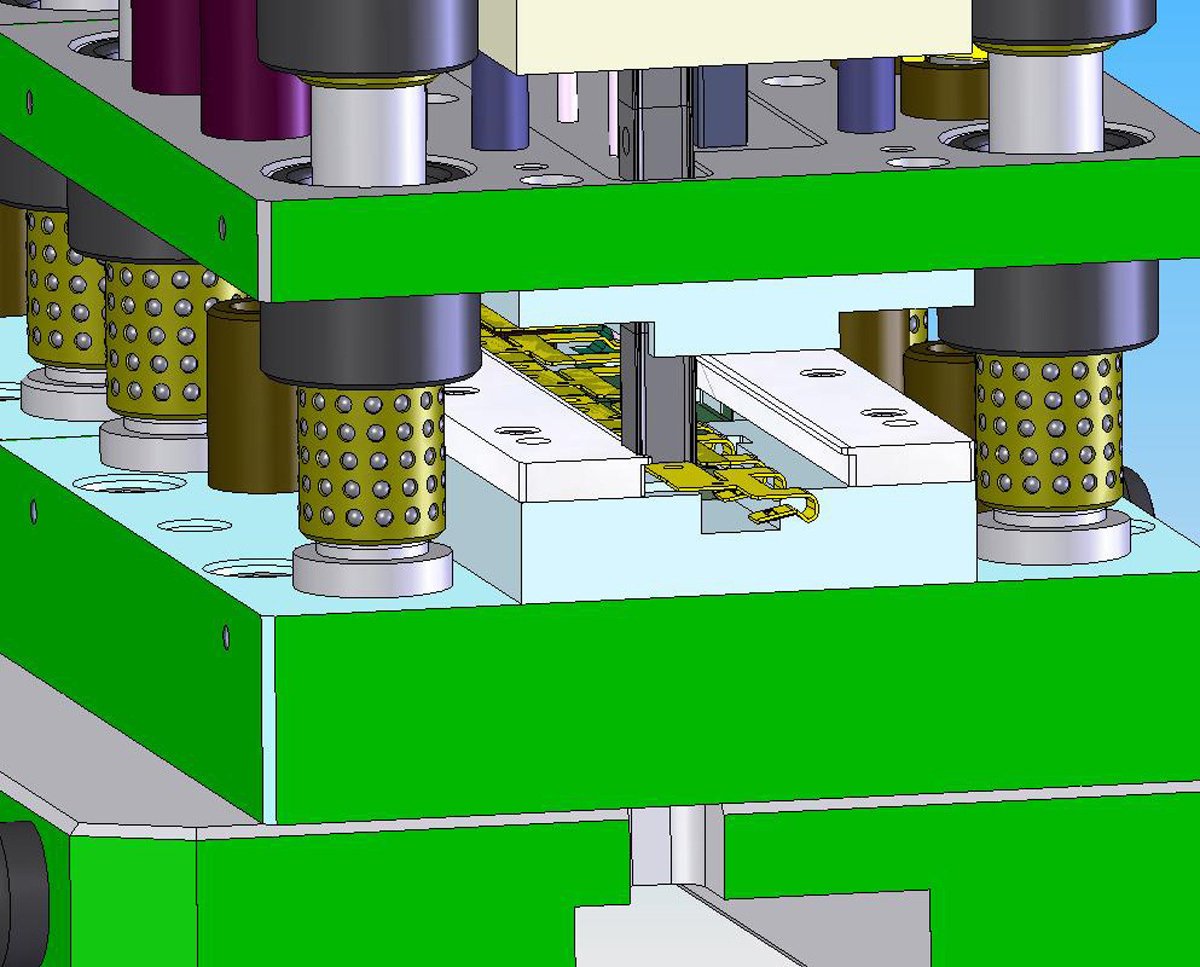
Фиг.5-39
Това е изключително удобно решение, когато производителя не разполага с нужната преса за проби на инструмента.
– Наличието в конструкцията на части, изискващи използване на заготовки, получени чрез леене или горещо щамповане. Единичното производство не може да си позволи тяхната упореба, поради изключително високата им цена при малки серии. Вместо това се препоръчва заварена или съставна конструкция.
– Използване на голямо габаритни монолитни активни части (матрици и поансони), за които е предвидена обемна закалка (над HRC 40). Обикновено, активните части за щанци са с твърдост над HRC 58. Прокаляемоста на инструменталните материали е под 80х80х80 mm (вътрешната част на заготовки с по-големи размери остава не закалена). Трябва да се отчете, че инструменталните материали с размери на сечението над 300х300 mm се намират трудно на пазара, освен това при тях деформацията след термообработка е много голяма. Резултатът при такива размери е необходимост от големи прибавки на точните размери преди закалка, чието отнемане след нея увеличава трудоемкостта на довършителните обработки няколко пъти. По тези причини е препоръчително такива матрици и поансони да се изпълняват съставни с отделни секции. Независимо от усложнението в конструкцията, те са оптималното решение за изработка и подръжка.
Пример за използване на съставни активни части при изтегляне и формоване на детайл „КАПАК“ (габаритни размери около 600х400х30 mm) от Фиг.5-40
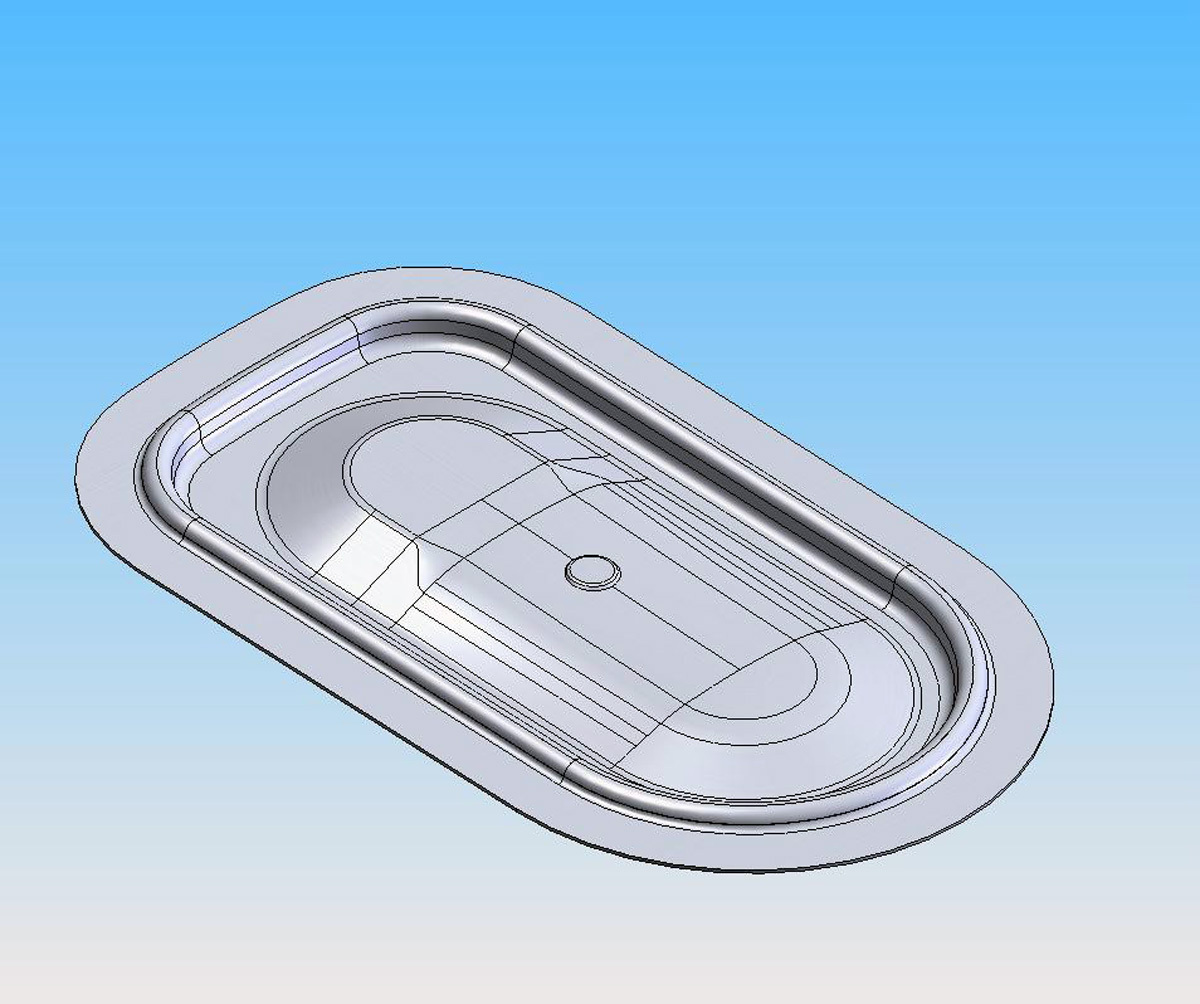
Фиг.5-40
са матрицата - Фиг.5-41,
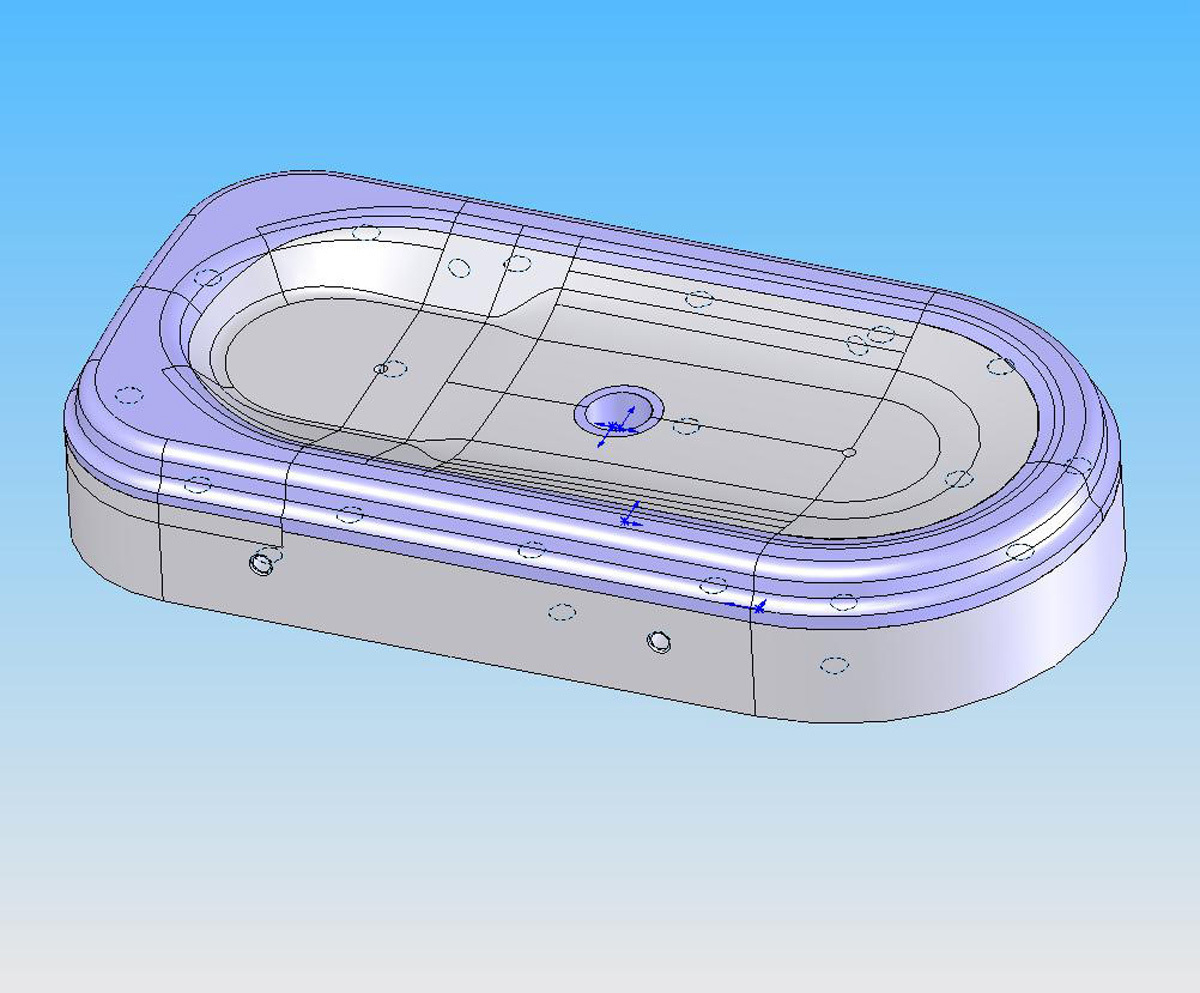
Фиг.5-41
представляваща стоманен матрицодържач с вградени 6 профилни закалени вложки (син цвят) и поансон - Фиг.5-42,
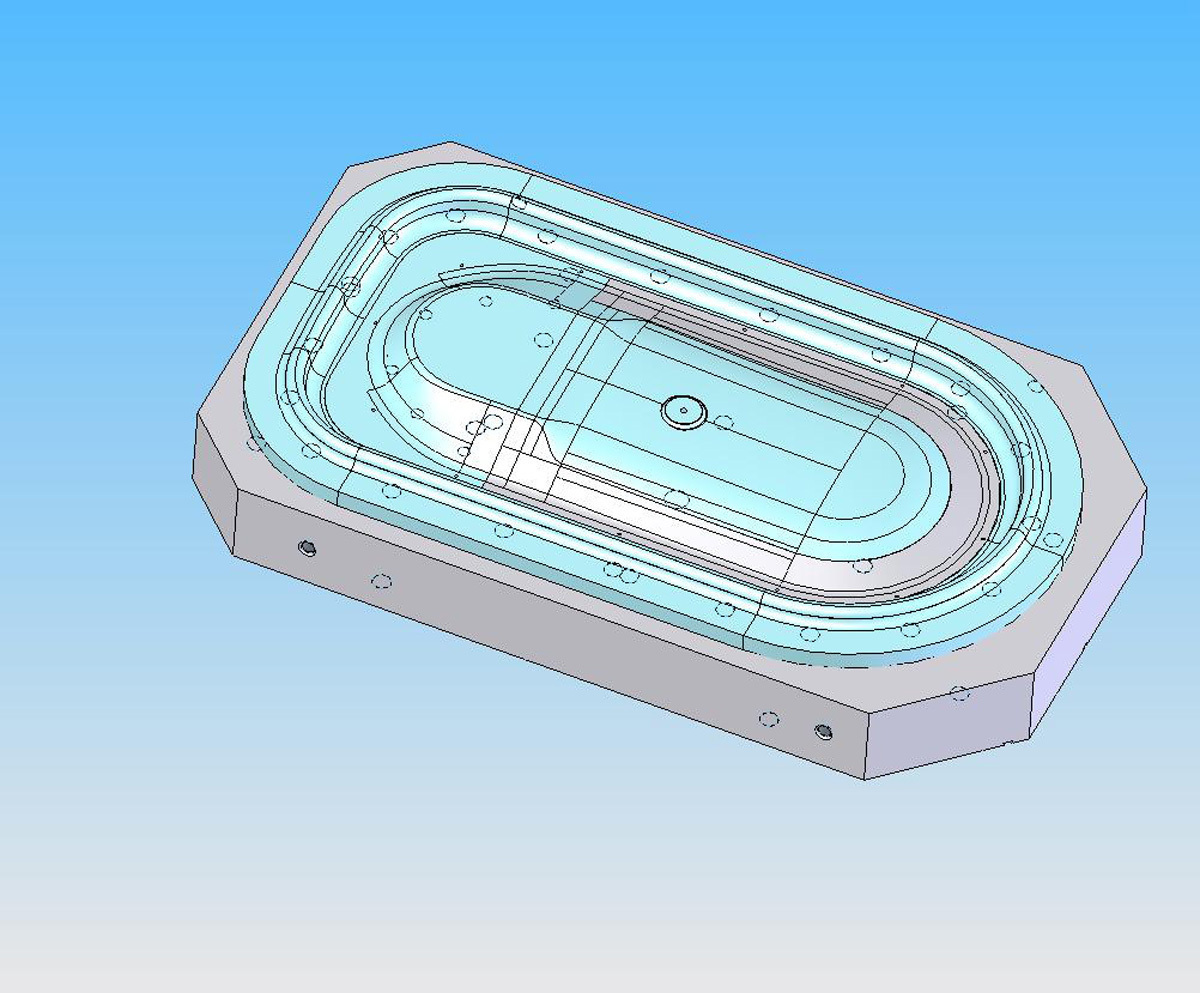
Фиг.5-42
представляващ стоманен поансонодържач с вградени 8 профилни закалени вложки (светлосин цвят).
– Проверка за теглото на заготвката на голямо габаритните детайли, която може да превишава допустимото за оборудването, независимо, че готовия детайл е по-лек. Обикновено това са детайли с дълбоки кухини и джобове, получени от плътна призматична или цилиндрична заготовка. В практиката се е стигало до повреда в подаващия механизъм на масата на обработращ център с ЦПУ, поради отсъствие на тази предварителна оценка.
– Проверка за завишени изисквания към точността на детайлите, оскъпяващи излично инструмента.
– Проверка за детайли с форми и конфигурации, които не могат да се изработят по изисквания от конструктора на инструмента начин.
4.2. Проектиране на технологични маршрути за активните и оригиналните части.
Създаването на технологичен маршрут за изработка на детайлите на щанците се извършва под различна форма в заисимост от опита, специализацията, срока за изработка и традициите на фирата - производител. Дори в малки специализирани фирми с квалифциран персонал от няколко човека, тези маршрути се създават мислено при запознаване с чертежите, но рядко се документират, защото всеки знае, кои детайли ще изработи, и на кои машини. При големите производители на инструментална екипировка обикновено, маршрута се описва на гърба на работния чертеж (отпечатване на таблица с операциите и машините) или се попълва отделна технологична маршрутна карта, която придружава чертежа. В тях има много работници и по няколко машини от вид, често едновременно се произвеждат няколко инструмента, което прави невъзможно всеки работник да познава маршрута и детайлите, които ще изработва.
В най-опростения вариант в маршрутната технология е описана само последователността на операциите – например за режеща матрица:
– ОПЕРАЦИЯ 1. Отрязване;
– ОПЕРАЦИЯ 2. Фрезоване;
– ОПЕРАЦИЯ 3. Плоско шлифоване;
– ОПЕРАЦИЯ 4. Координатно пробиване;
– ОПЕРАЦИЯ 5. Шлосерска;
– ОПЕРАЦИЯ 6. Термообработка;
– ОПЕРАЦИЯ 7. Плоско шлифоване;
– ОПЕРАЦИЯ 8. Координатно шлифоване;
– ОПЕРАЦИЯ 9. Нишкова електроерозия;
– ОПЕРАЦИЯ 10. Обемна електроерозия;
– ОПЕРАЦИЯ 11. Шлосерско-монтажна;
– ОПЕРАЦИЯ 12. Заточване.
Такъв вариант, обаче, е не приемлив за производители с повече от една машина за различните операции, защото създава неяснота, за коя точно машина е предвидена конкретната операция. По тази причина в маршрутните карти срещу всяка операция е предвидена графа за код на оборудването (машината). Операторите на една и съща машина често се различават по своята квалификация, което също трябва да се отрази в отделна графа, в зависимост от сложноста на предвидената работа. За да може производството да се планира и да се гарантира оптимлно натоварване на оборудването, за всяка операция се предвижда определно време за изпълнене. То се попълва в предвидена за това графа и може да е единичното време за изпълнение на конкретната операция върху един детайл в часове или времето за изпълнение на операцията върху цялата партида, за която е посочен общия брой заготоки. Това време понякога се използва и за заплащане, когато избраната форма на заплащане е на норма. Тук трябва да се отбележи, че тези времена за разлика от прилаганите при серийното производство, са само прогноза, която може да се различава от действителното време няколко пъти. Това е резултат от факта, че за определяне на необходимото време не се правят изчисления на технологични режими на работа, а също и на значителните отклонения на реалните от предвидените прибавки за обработка. В маршрутните карти има също графа за използваните приспособления или специални инструменти, която е много полезно да се попълва за случаите, когато разглежданата операция може да се изпълни с различни, но само едно ще гарантира очакваното качество (на пример да се стругова между центри точен детайл с голяма дължина с подвижен люнет, с което ще се постигне по-висока точност от обичайното струговане между центри). Препоръчително е, след името на операцията да се опише на кои повърхнини да се изпълни и каква прибавка за следваща обработка да се предвиди (особено за предварителните операции). В противен случай прибавката се оставя по усмотрение на работника, при това с оглед на неговото удобство, и в последствие може да се окаже недостатъчна или прекалено голяма. В картата има графа за размерите и теглото на изходната заготовка за детайла. Наличието на напълно попълнена маршрутна карта за всеки оригинален детайл е задължително условие за изпълнението на т. 4.8.
4.3. Подготовка на спецификация за доставка на материали.
Някои от производителите на инструменти използват специална графа в спецификацията на сборния чертеж за размери и материал на заготовката. Големите инструментални фирми обаче, най-често подготвят отделни спецификаци, в които обединяват по няколко детайла от различни щанцови инструменти, които са с еднакъв материал и напречно сечение на изходната заготовка. Така се намаляват номенклатурата и разходите за нейната доставка. В много случаи се налага (особено за плочи от листов прокат), дори да се правят специални скици с разположение на детайлите, подлежащи на газово, плазмено или водно нарязване. Удобството на отделните спецификации е в това, че те могат да се отделят и насочват към различни доставчици.
На пример:
– спецификации за доставка на инструментална стомана;
– спецификации за конструкционна стомана;
– спецификации за доставка на нормализирани части от определена фирма (поансони, водещи елементи, пружини);
– спецификации за стандартни скрепителни елементи; спецификации за други покупни възли).
Така лесно могат да се правят запитвания за оферти и на доставчиците не се предоставя информация от чертежи, която обикновенно е обект на фирмена тайна.
4.4. Разработка на целеви Блокове-заготовки.
Инструментите за щанцоване включват много режещи, водещи и огъващи вложки, често изработени от еднакъв материал с еднаква термообработка. Тези части обикновено са с еднакви или близки височини и се изработват с еднаква технология, най-често нишкова електро ерозийна обработка на контурите. Те могат да имат множество точни и стъпални отвори, резби, канали, освобождения. Всичко това позволява да се използват целеви Блокове-заготовки, които обединяват малките детайли и осигуряват необходимите стартови отвори за вдяване на нишката, базови отвори и повърхности за центроване, необходимите места за закрепване при ерозийната обработка. Главното предимство е, че се гарантира еднаква твърдоет на всички детайли, възможност за обработка на част от тях или на всичките с едно базиране и закрепване. Това спестява време за изработката и позволява постигане на по-висока точност при малки размери. Практически всички канали, профилни освобождения, резби, бази и други могат да се изпълнят с конвенционални металорежещи машини преди закалка, с което да се опрости тяхната изработка. Същевременно, изработката им на една установка с базите и базовите отвори, гарантира точно разположение спрямо ерозираните контури. За някои профилни детайли този подход е единствената възможност за изработка. Пример за такава Блок-заготовка за режещи матрични вложки от бързорезна стомана (за технолигична схема от Фиг.5-1) е показан на Фиг. 5-43, а на Блок-заготовка за водещи вложки на Фиг. 5-44.
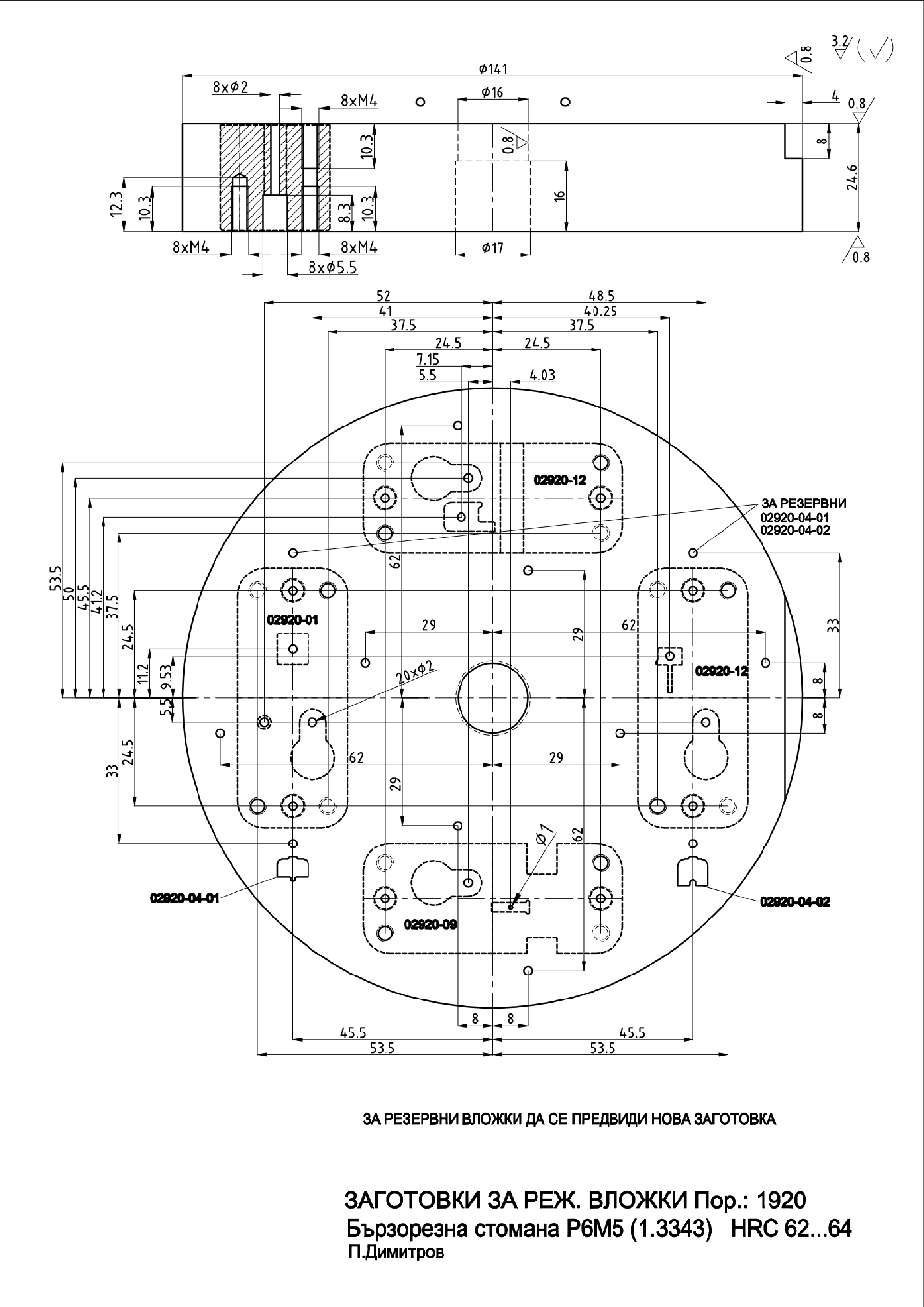
Фиг. 5-43
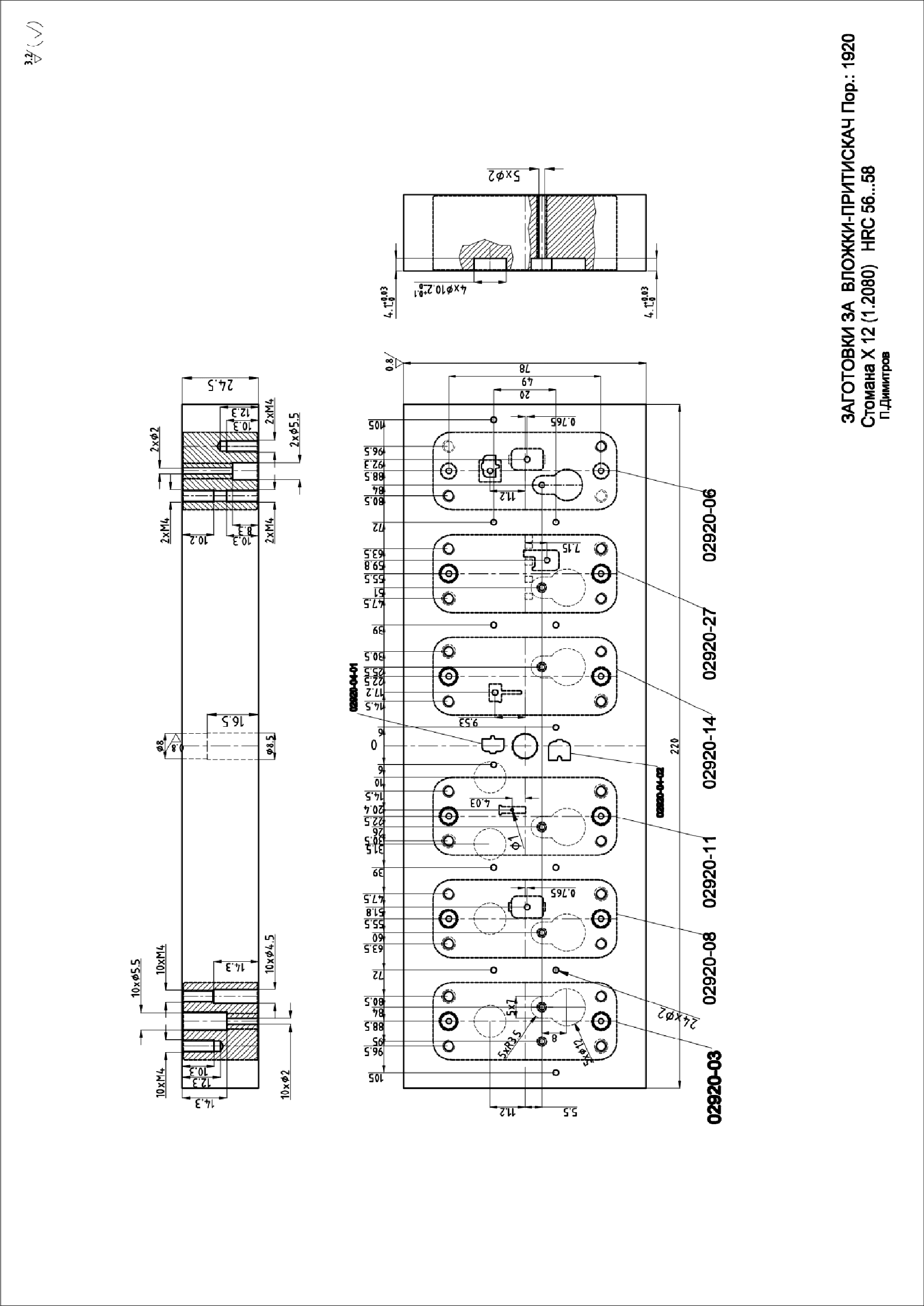
Фиг.5-44
Важно условие е да се остави не по-малко от 3 mm разстояние между ерозираните контури за гарантиране здравина на блока след изрязване на част от вложките. Особено внимание да се отдели на мястото на разположение на стартовите отвори, което е по-важно от тяхната точност. Отворите трябва да осигурят здрав мост между точката на врязване на нишката в контура и крайната точка за междините преходи. Необходимо е да се съобрази посоката на работа на ерозийната машина и да се отчита, че при падане на ерозираната заготовка след окончателна обработка, остават издатъци от скъсване на носещия мост. Те е най-удобно да са разположени на плоски повърхнини за следвашо зачистване чрез плоско шлифоване. Това условие се отнася за детайли с точни външни повърхнини, защото издатъците от скъсване на вътрешните повърхнини се отнемат при последния преход на нишката. Местата за закрепване на Блок-заготовката да осигуряват зона, не по-малка от 30 mm и да не пречат на преминаването на водачите на нишката. За целевия блок с много заготовки не е необходимо да се оставя специално такава зона – при правилно разположени базови повърхнини и стартови отвори, просто се използва площа на неизрязаните детайли или тази с вече изрязаните.
Прилагането на целеви Блокове-заготовки е много ефективно за режещите вложки и поансони от щанци с металокерамични твърдосплавни активни части. Изключително скъпия материал и ограничения набор от доставяни металокерамични твърдосплавни заготовки, изисква максимално използване на последните чрез оптимално разполагане на контурите на активните части. Пример за такова разполагане на режещи вложки за щанца с последователно действие за Лист роторен и Лист статорен (за технологична схема Фиг.5-10) е показан на Фиг.5-45.
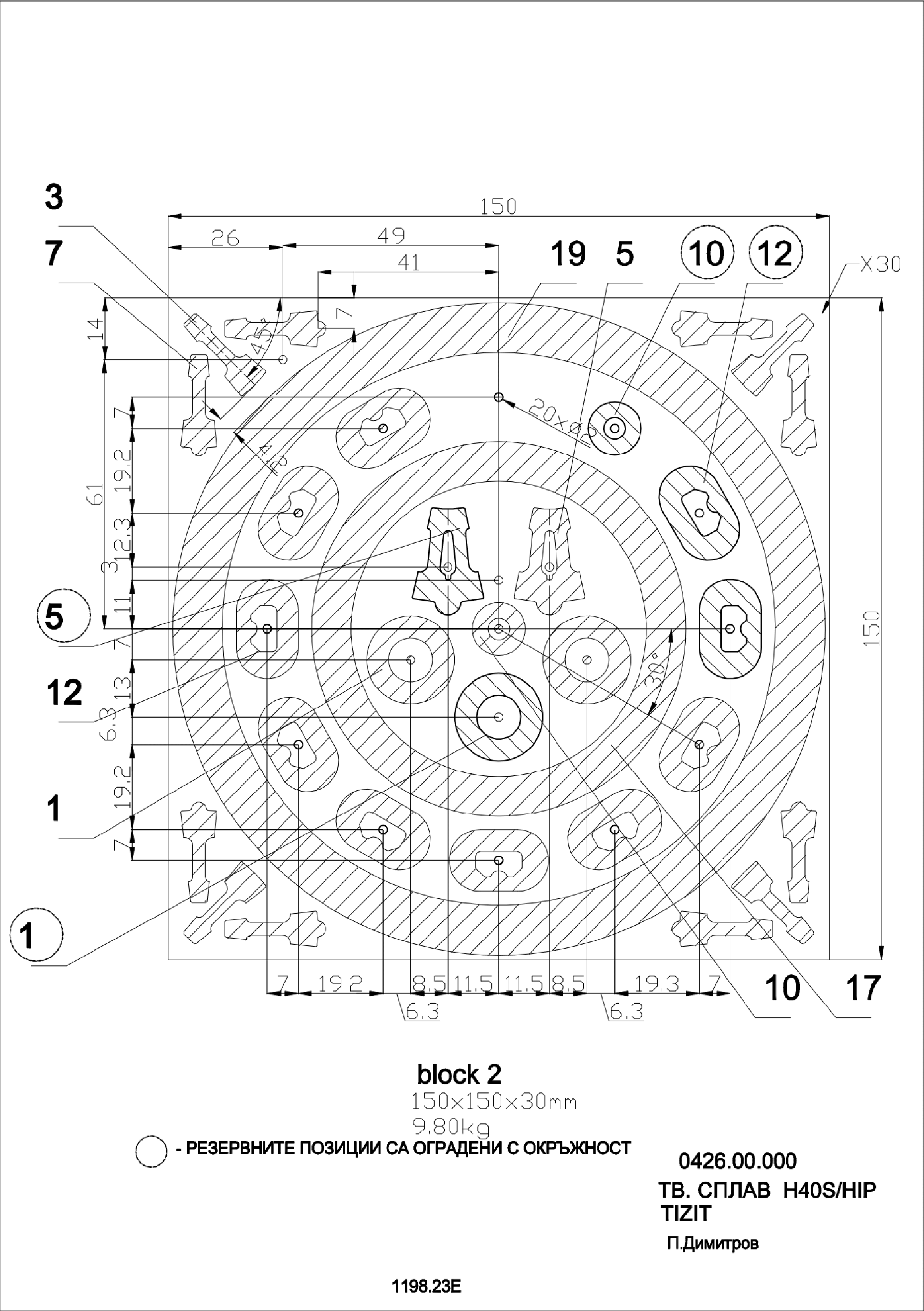
Фиг.5-45
4.5. Разработка на приспособления за изработка, монтаж и контрол.
Оптималният вариант при изработка на щанците е, техните активни и оригинални части да могат да се изработят само с универсални приспособления и инструменти, с които са комплектовани металообработващите машини. За съжеление, това не винаги е достатъчно и често се налага проектиране и изработка на специални инструменти и приспособления за решаване на конкретен проблем от производсво на даден инструмент. В литературата те са известни, като инструменти или приспособления от втори порядък (инструменти за производство на инструментите). Добре обмисленото изпълнение на такива приспособления улеснява изработката, контрола и монтажа на активните части на щанците.
Пример за приспособление за обработка на режещия профил на металокерамични твърдосплавни вложки (поз.03; поз.05; поз.07) чрез нишкова електро ерозия е показан на Фиг.5-46.
Това приспособление имитира разположението на вложките в инструмента, като са предвидени базови повърхнини за центроване и затягащи елементи. С него ерозирането и смяна на вложките могат да се извъшват без сваляне от машината, с което се печели време от отпадане необходимостта за центроване на всяка нова вложка и се повишва точността.
Металокерамичните твърдосплавни вложки (поз.03; поз.05; поз.07) се нареждат плътно една до друга и монтажа (демонтажа) на една от тях е невъзможен. Към това се добавя и изключителната крехкост на материала, поради което откъртване на вложките е често срещан проблем. За решаване на този проблем е разработено приспособление за избиване - Фиг.5-47.
То използва водеща плоча, която задържа вложките челно и направлява точно избиващия елемент.
Големият брой секторни металокерамични твърдосплавни вложки за роторните канали изисква, те да се измерят много точно, за да се напасват по диаметъра и страничните страни. Контролна призма и схемата на измерване на вложките с нея, чрез използване на магнитна стойка с индикаторен часовник с точнист 0.002 mm, е показана на Фиг.5-48.
Към специалните приспособления може да се прибави ексцентричния щифт за регулиране на хлабината между матрицата и поансоите - Фиг.5-49,
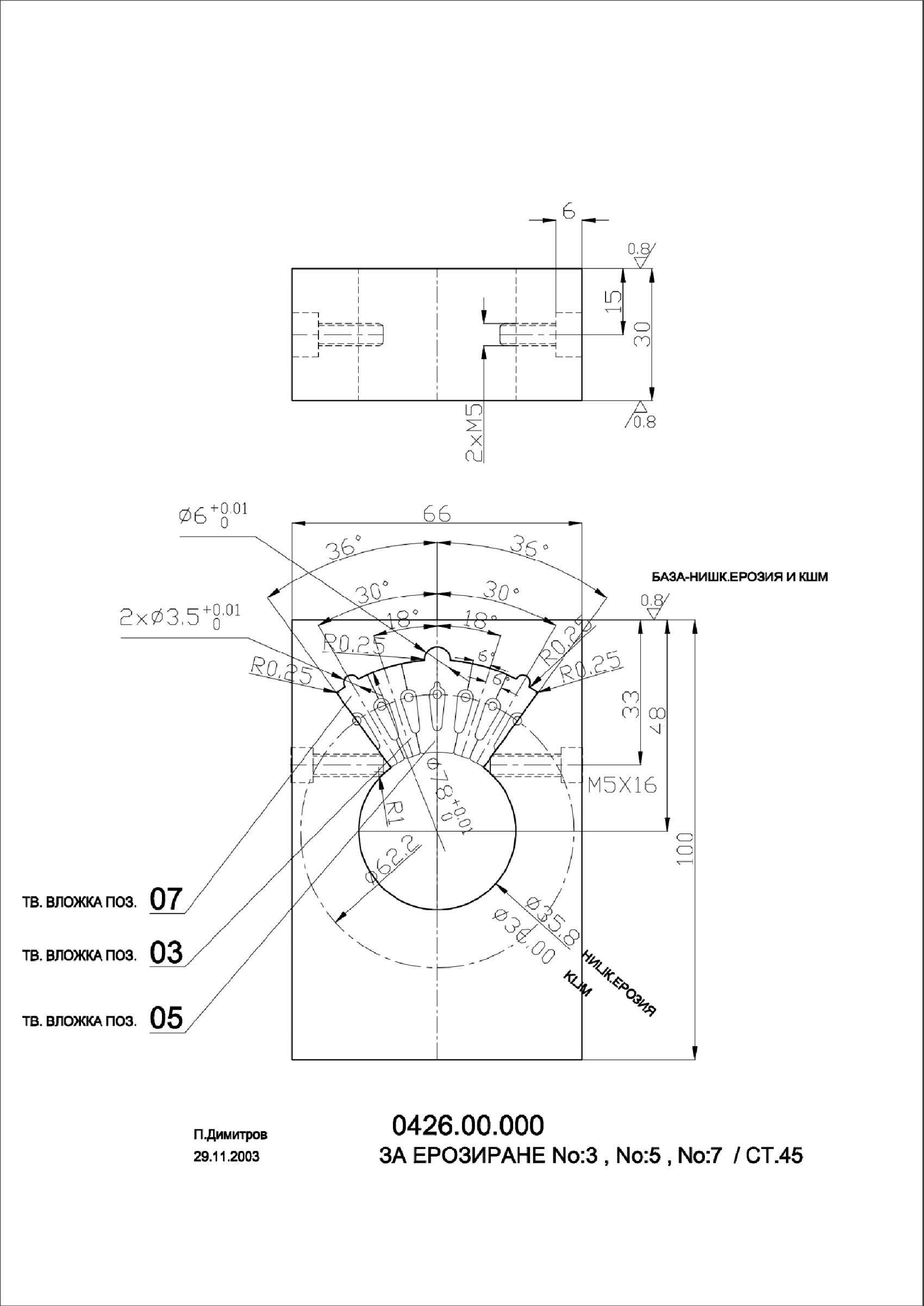
Фиг.5-46
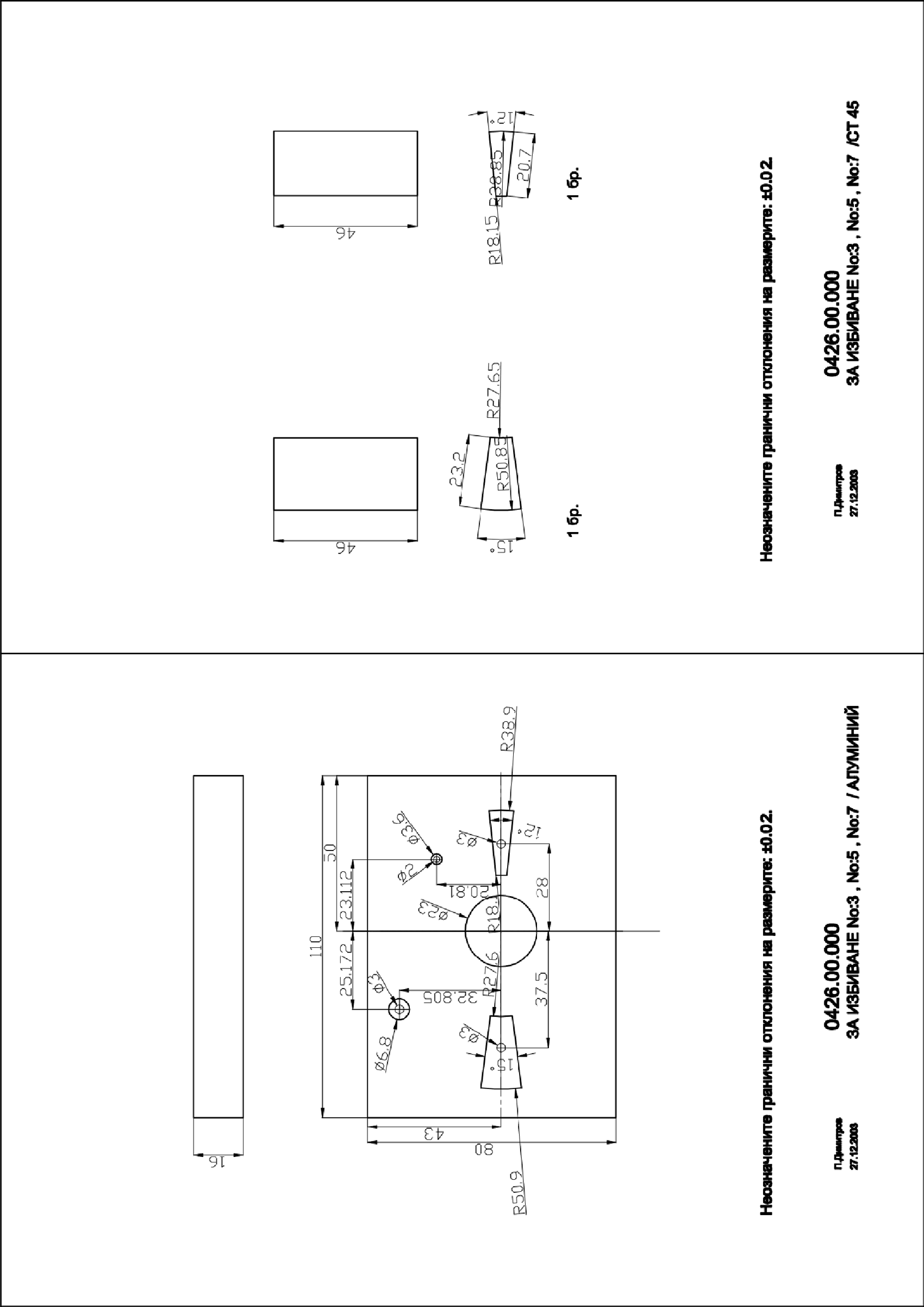
Фиг.5-47
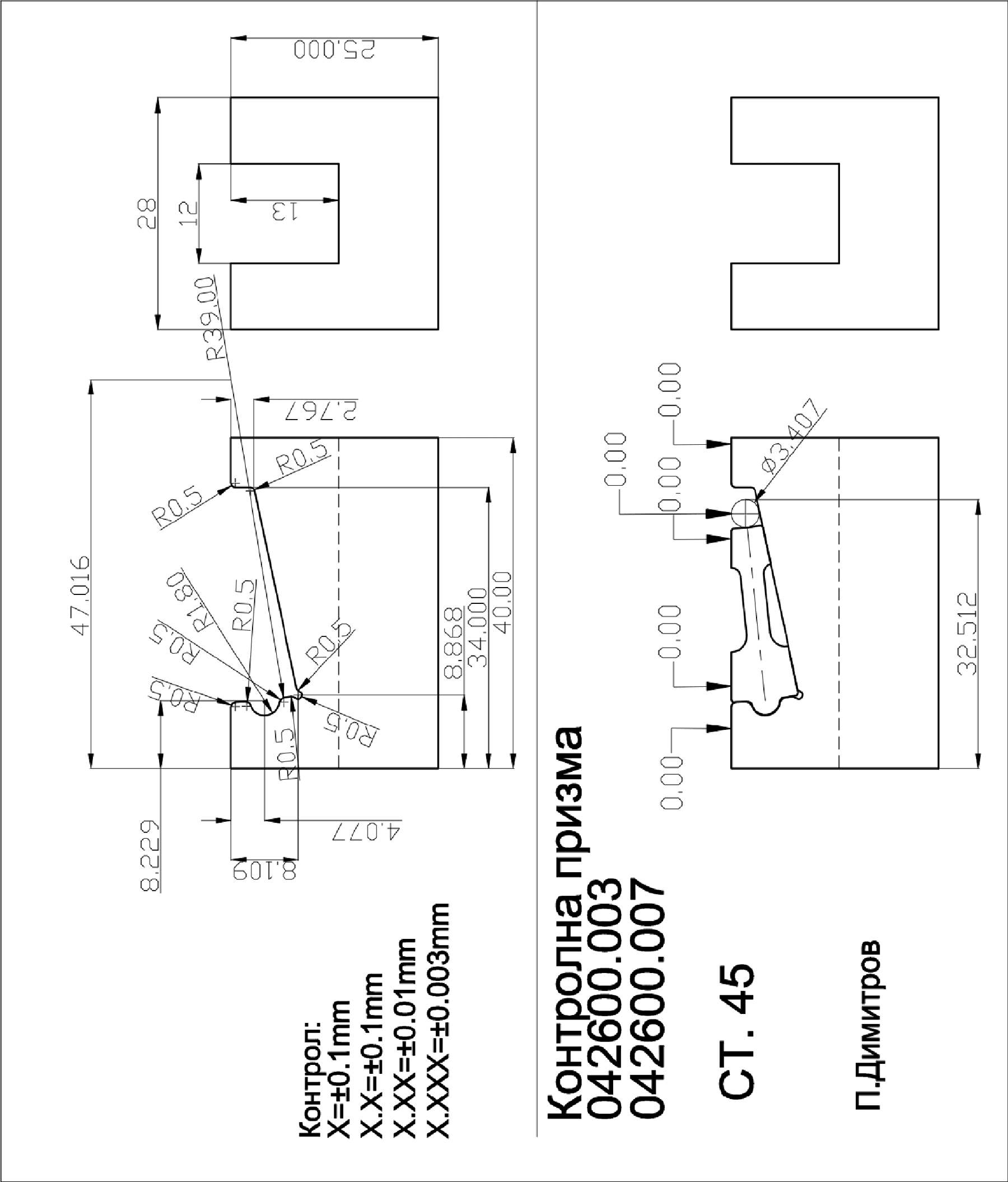
Фиг.5-48
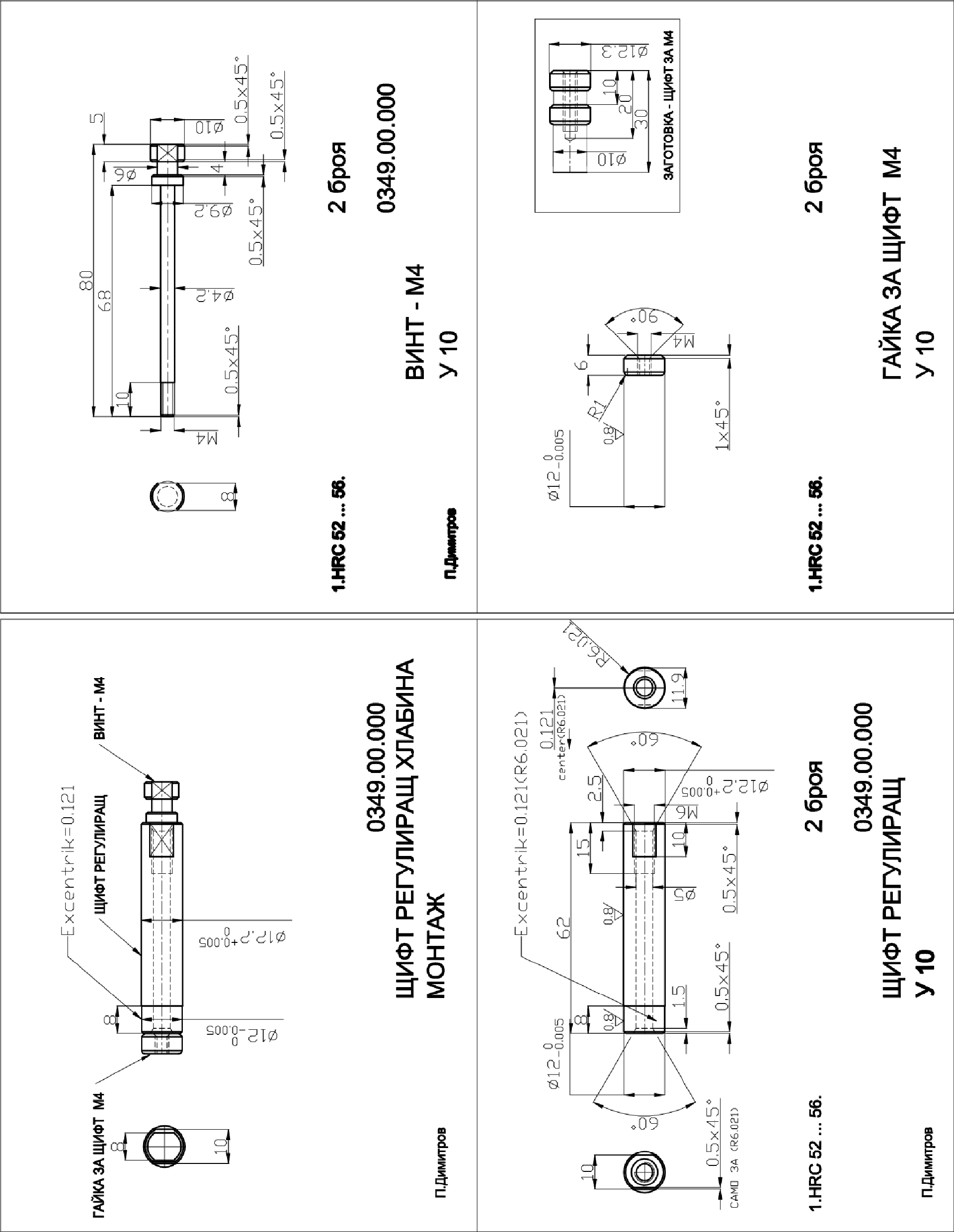
Фиг.5-49
който в комплект с втори такъв, позволява малки измествания на водача с поансоните в различни посоки и може да бъде фиксиран в най-доброто положение чрез затягане. Така се гарантира по-равномерно разпределена хлабина и точна обработка на водещите отвори на плочата за избраното положение. Методиката и схемата на настройка на ексцентричните регулиращи щифтове ще бъде разгледана в т.5.2.
4.6. Разработка на на модели за електроди.
Инструментите за формоизменящи операции (огъване, изтегляне, релефно формоване) често имат активни части (матрици и поансони) със сложни пространствени форми. Използването на закалени материали с твърдост над HRC58 и наличието на вътрешни радиуси под R2 mm, ограничава използването на металорежещи машини с ЦПУ. В някои матрици, поансони или притискачи, се налага изработване на освобождаващи легла под огънати или формовани участъци (особено при комбинирани щанци с последвателно действие), чиито размери и форма не позволяват получаване чрез конвенционални машини преди закалка. За решаване на тези проблеми се използват обемни електро ерозийни машини. Това е скъпа операция, изискваща инструменти от втори порядък – електроди, които са изработени от мед или графит. Електродите обикновено имат формата на повърхнината, която ще се ерозира. Понякога се прилагат електроди с различна от крайната форма, като резултата се получава след съчетание с траекторията на движение на електрода (например нарязване на резба). Огромното предимство на този метод е възможността за обработка на закалени материали и металокерамични твърди сплави. При изработката на модел за електрод със сложна форма е много важно е да има компютърен 3D модел на обработвания детайл, за да се създаде точната форма. Важна особеност е, че електрода никога не копира директно формата на обработваемата повърхност. Винаги се предвижда офсет за необходимта електродна хлабина, зависещ от режимите на електро ерозинната машина и материала на електрода. Понеже процеса елекро ерозия е свързан с износване на електрода, за изпълнение на операцията се предвиждат груб и чист електрод. Те се изработват с различен офсет (грубия е с по-голям) и работят при различни режими. Пример за меден електрод за обработка на матрицата за огънатия детайл от Фиг.5-2 е показан на Фиг.5-50.
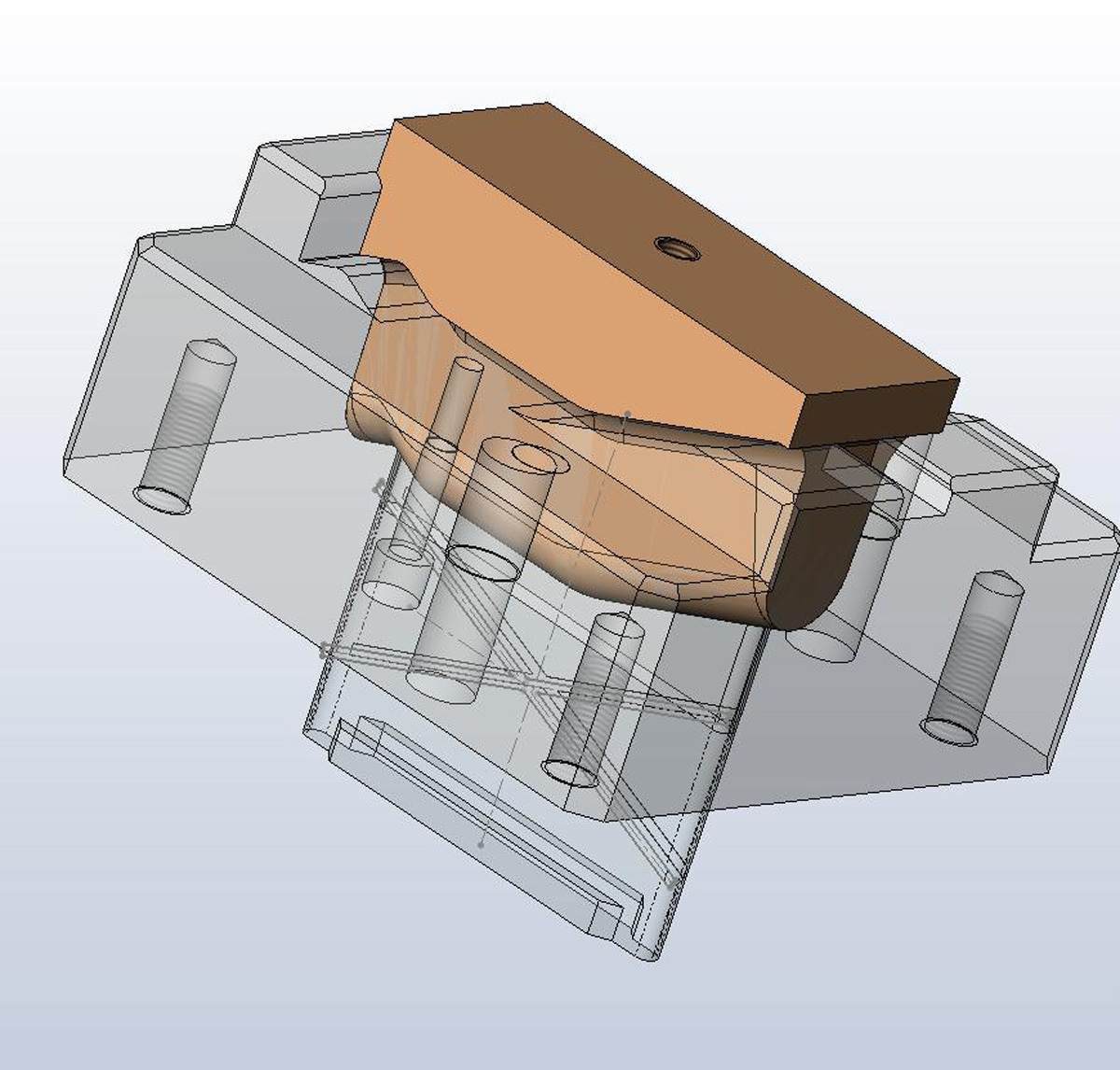
Фиг.5-50
С него едновременно се обработва заедно с огъващата матрица и профилния притискач. Електродът се закрепва към ерозийната машина с резба в горната си част и има 3 взаимно перпендикулярни базови равнини за центроване спрямо заготовката.
4.7. Подготовка на управляващи прогами за машини с ЦПУ.
Наличието на конструктивна документация (3D или 2D модели) и технологичен маршрут са изходните данни за създаване на управляващи прогами за машини с ЦПУ. Предварително подготвеният технологичен маршрут за всеки оригинален детайл дава отговор на въпроса, предвижда ли се такава обработка и на кои повърхнини. Наличието на маршрутна технологична карта ще даде информация и какви обработки са изпълнени до момента и какви прибавки за обработка са предвидени. От тук нататък задачата се поема от технолог - прграмист или самия оператор на машините с ЦПУ. Освен за оригиналните детайли, до него трябва да стигне информация и за всички допълнителни приспособления и електроди, за които са необходими програми. Препоъчва се да е известен реда за обработка на детайлите, защото в практиката програмите се правят малко преди детайла да се качи на машината и има случаи, когато е подготвена програма за не изработен детайл, а за този, който непосредствено се качва, няма програма.
4.8. Подготовка на график за изработка.
Всяко производство е свързано със срокове. Изработката на инструменти за щанцоване не прави изключение. Независимо дали инструмента е обект на договор с клиент или е необходим за усвояване на нов детайл, крайния срок се залага и се следи стриктно от съответното ръководство. Поради единичния характер на инструменталното производство, не винаги са налични достоверни данни за точно определяне на необходимото време за изработка и крайните срокове често се определят субективно. Задачата се усложнява от необходимостта да се съобрази и натоварването на всички машини за производство от други, паралено изработвани инструменти при определяне на този срок. Така от една страна няма достоверни времена за изработка на отделните детайли по операции (поради не извършване на технологични изчисления за режими на обработка), от друга точно засичане на времето ще е известо много след като срока е определен и дори за повторна обработка на същия детайл, то ще варира, защото не може да се гарантира постоянство на прибавките при единични заготовки.
За по-добра нагледност и възможност за отчитане на влиянието на различните фактори, се изготвя линеен план-график за производството на всеки инструмент. Пример на такъв график е показан на Фиг.5-51, а сборния чертеж на огъващата щанца (за детайл „Планка“ Фиг.3-5, първо огъване). на Фиг.5-52.
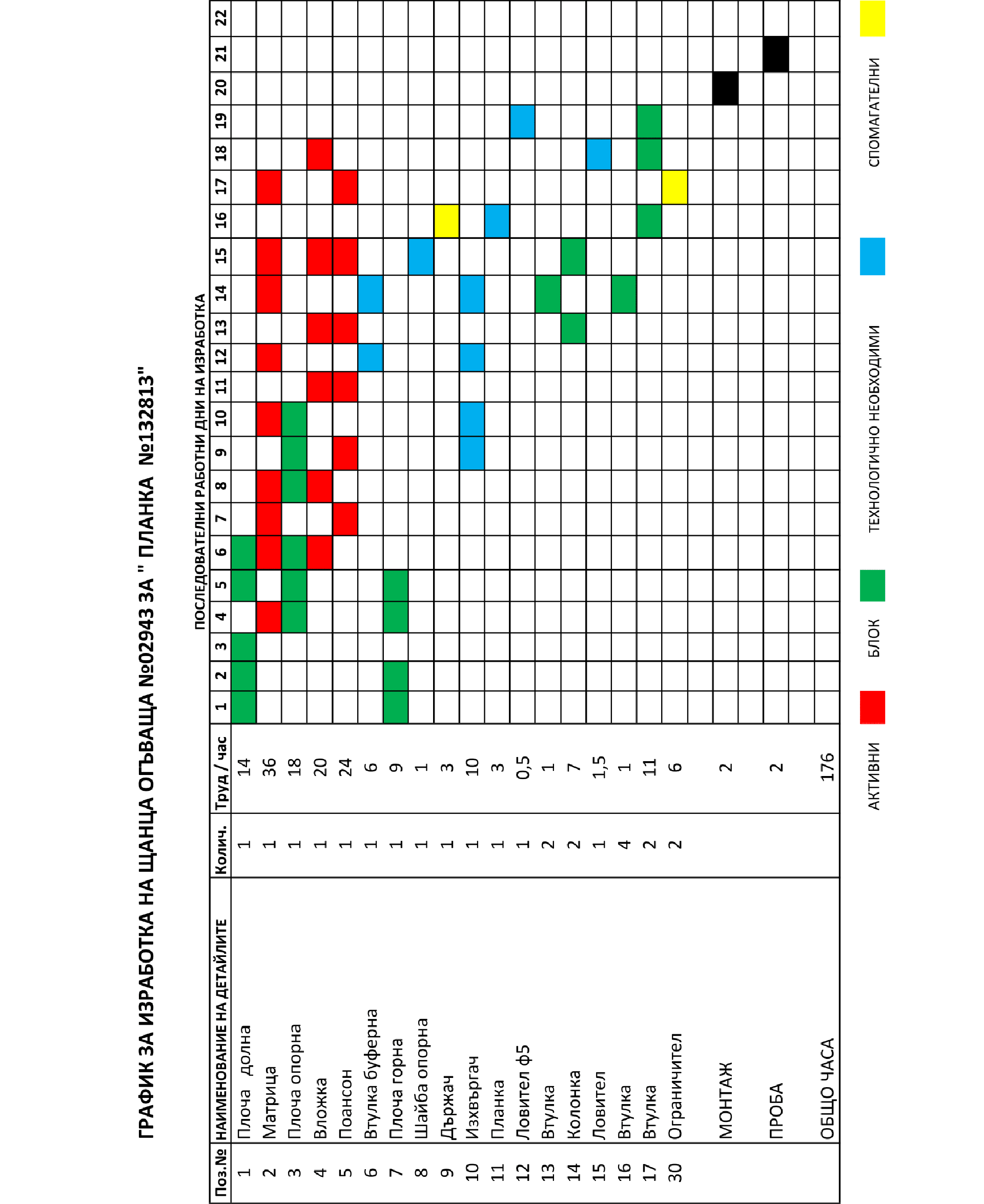
Фиг.5-51
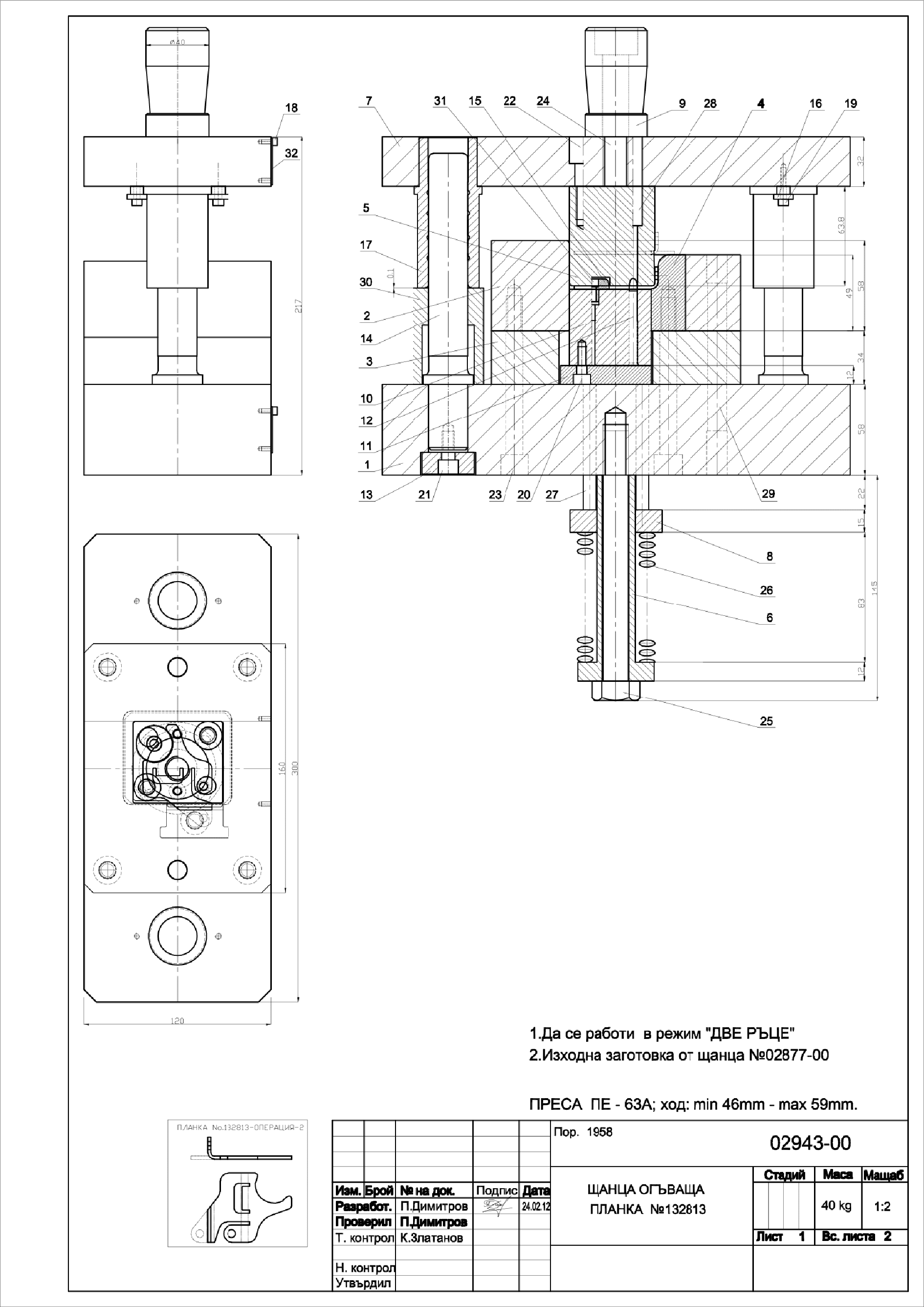
Фиг.5-52
Простият анализ на графика показва две неща:
– всички детайли имат различна продължителност на изработка, която не започва едновременно (не е необходимо);
– в периода на изработка на един детайл се забелязват прекъсвания, а самата продължителност като работно време (по 8 часа дневно) е по-голяма от общото време за изработка по технология.
Обяснението е просто – производството включва множество операции, извършвани последователно на различни машини, някои от които (например термообработка) технологично не могат да завършат и предадат заготовката в същия ден. Колкото по сложен е детайла (активни части), толкова повече операции и прекъсвания ще са необходими. Трябва да се отбележи, че дори конкретна операция по детайла да е завършена, той няма веднага да се предвижи до следващата, а дори и в този случай, едва ли тази машината ще е свободна и веднага ще започне неговата обработка. Разглеждайки няколко такива графика и операциите, които предстои да се изпълнят върху детайли от определен вид (активни, технологични, спомагателни), може по-точно да се предвиди необходимото прекъсване, вследствие натоварването по видове машини. Препоръчително е, частите с най-дълъг производствен цикъл (най-често активните, но понякога това са плочи от блока), да започнат изработката най-рано. Обратно – части с къс производствен цикъл, които не са необходими преди монтаж, да се започват по-късно. Така няма да е необходимо да се складират и полагат специални грижи за тях (например защита от корозия).
5. Разработка на инструкции за експлоатация.
5.1. Съставяне на инструкции за експлоатвция и техника на безопасност.
Всички щанцови инструменти трябва да се придружават от паспорт или инструкция за експлоатация. В нея трябва да са описани техническите характеристики на инструмента (габаритни размери, тегло, размери и материал на заготовката, вида на пресата, предвидената трайност), изискванията за техника на безопасност, които трябва да се спазват, условията за експлоатация, транспорт и съхранение, особеностите на поддръжка и настройка на инструмента. Примерно оформяне на такава инструкция за щанца с металокерамични твърдосплавни активни части за лента от Фиг.3-3 е показано на Фиг.5-53-A, Фиг.5-53-B, Фиг.5-53-C и Фиг.5-53-D.
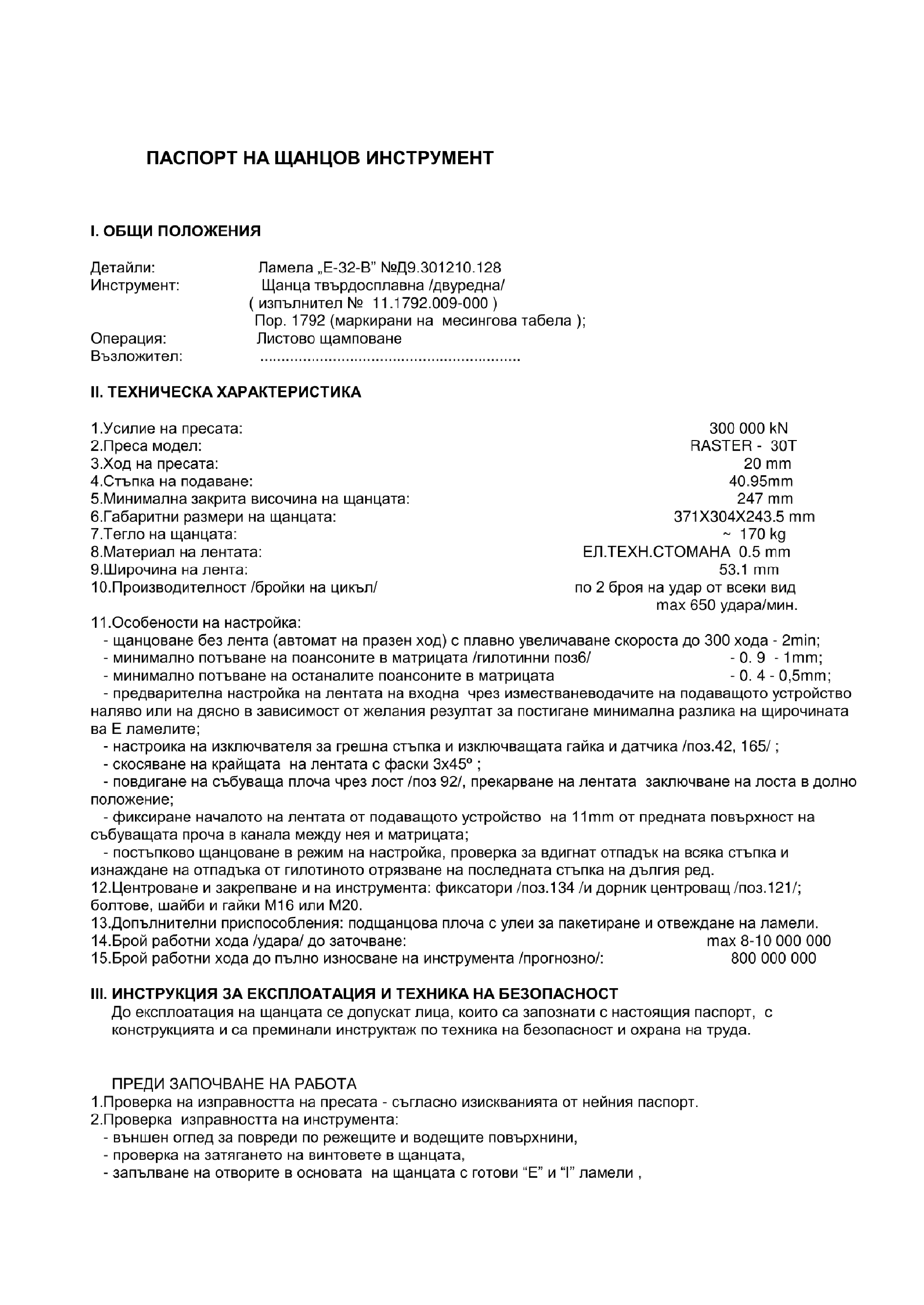
Фиг.5-53-A
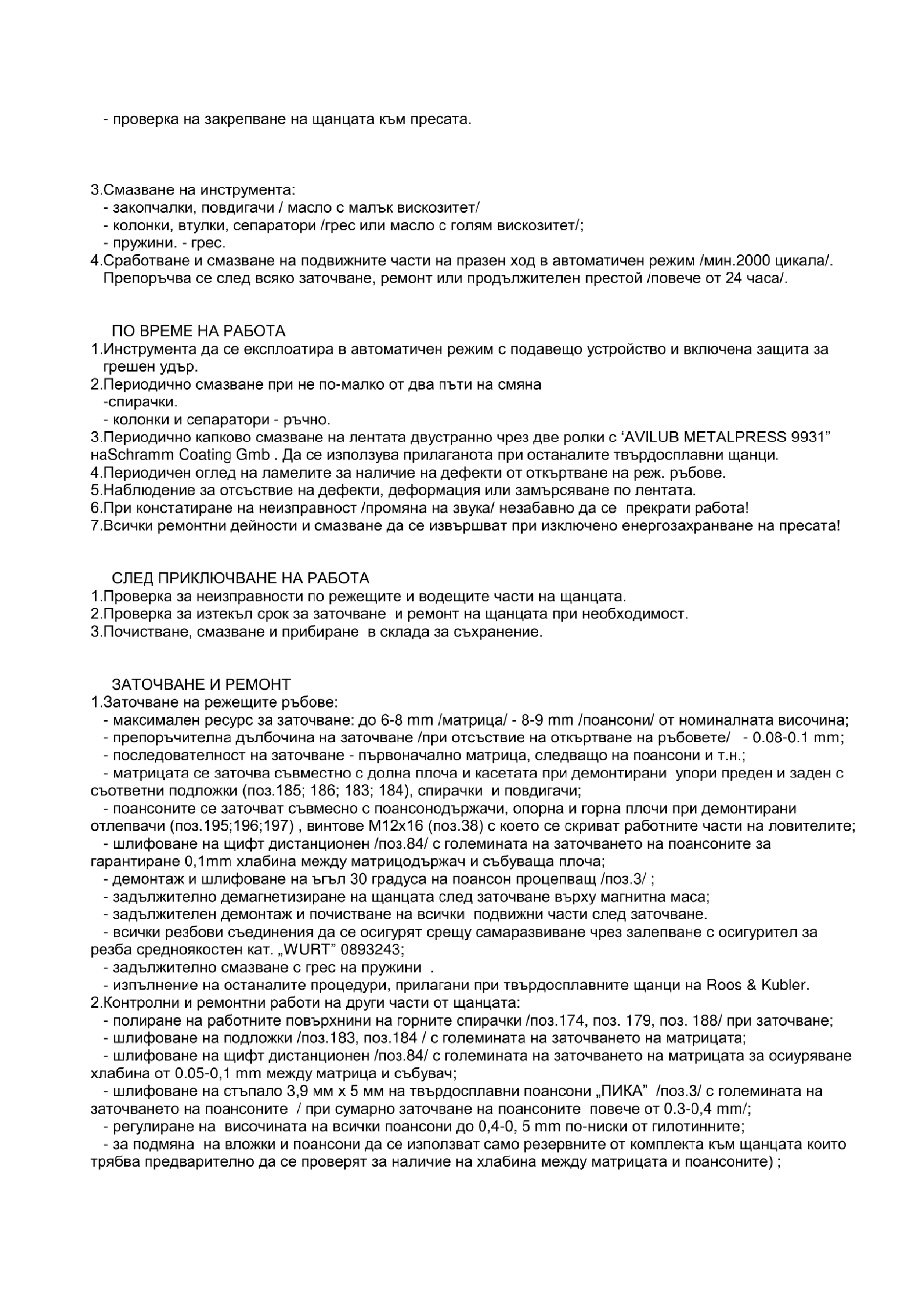
Фиг.5-53-B
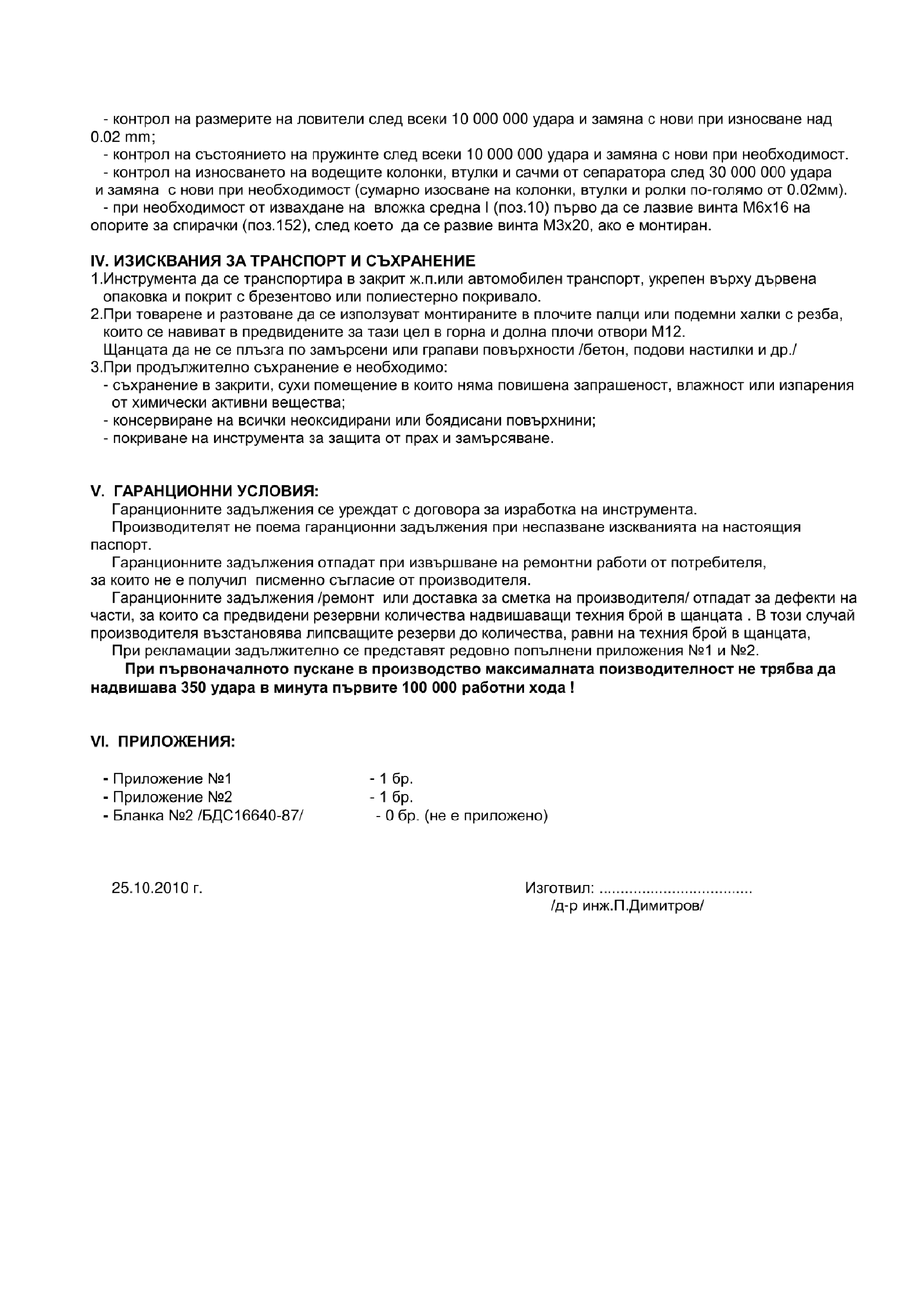
Фиг.5-53-C
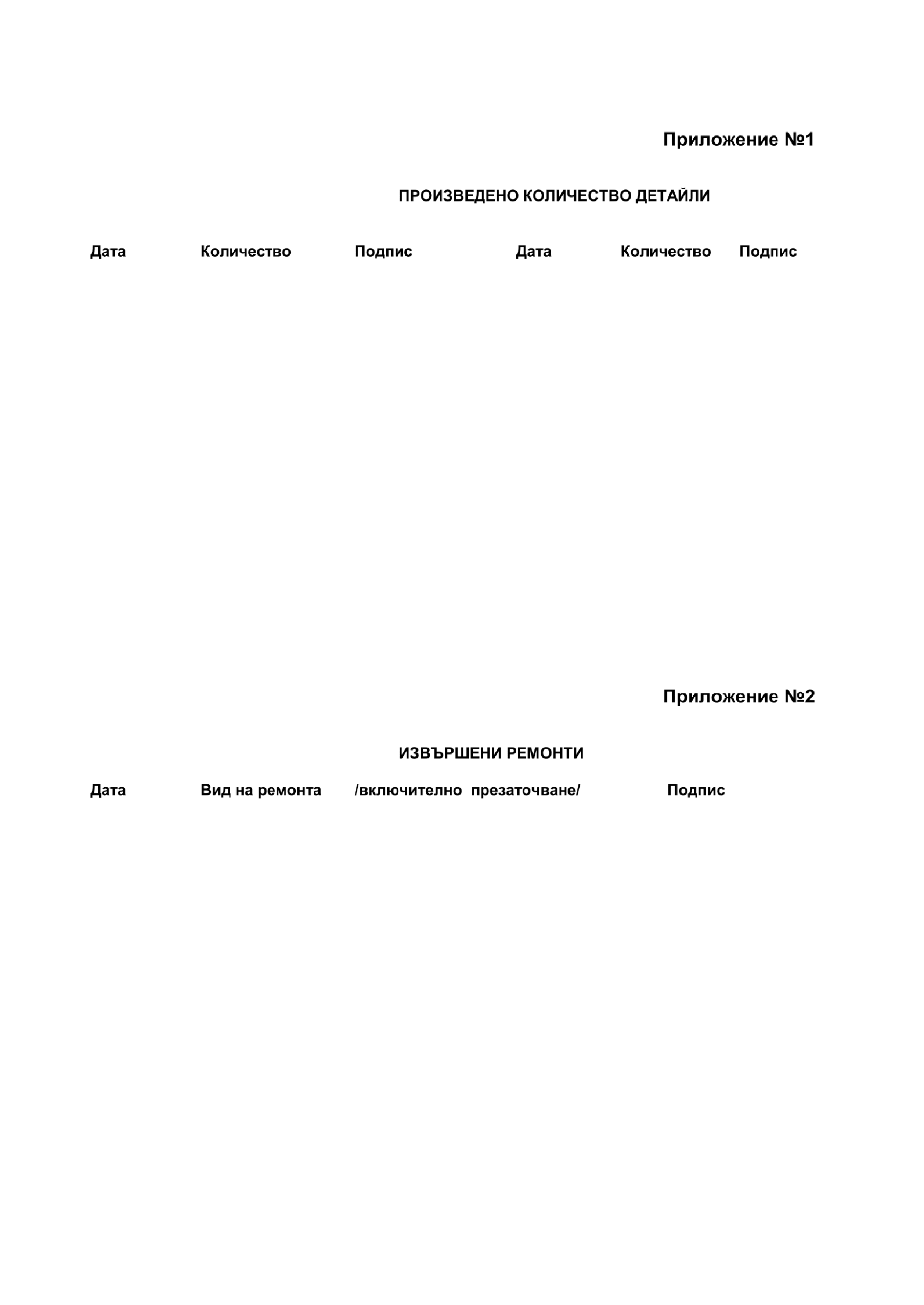
Фиг.5-53-D
5.2. Подготвянене на методика за настройка и проба.
Като пример на методика за настройка ще бъде разгледна схемата за прилагане на регулиращи ексцентрични щифтове за оптимално разпределение на хлабината между матрицата поансоните (виж Фиг.5-49). Обичайно явление е, при изработката на големи режещи щанци с много поансони (дължина над 500 mm), предназначени за тънък материал (до 0,50 mm), грешките на изработка и температурните деформации да водят до не равномерна хлабина за някои режещи контури. В критични ситуации някои поансони не влизат в матрицата. В такива случаи се използват технологични методи за корекция, като се изместват отворите за щифтове или за водещите колони съобразно най-доброто положение, за което поансоните влизат в матрицата. Схемата и възможните измествания са показани на Фиг.5-54.
Принципът на действие на регулиращите щифтове се състои в контролирано изместване и завъртане на водещата плоча с поансоните спрямо матрицата, затягане на подвижната част на щифта и фиксиране на водещата плоча в избраното положение за обработка на водещите отвори на колонките.
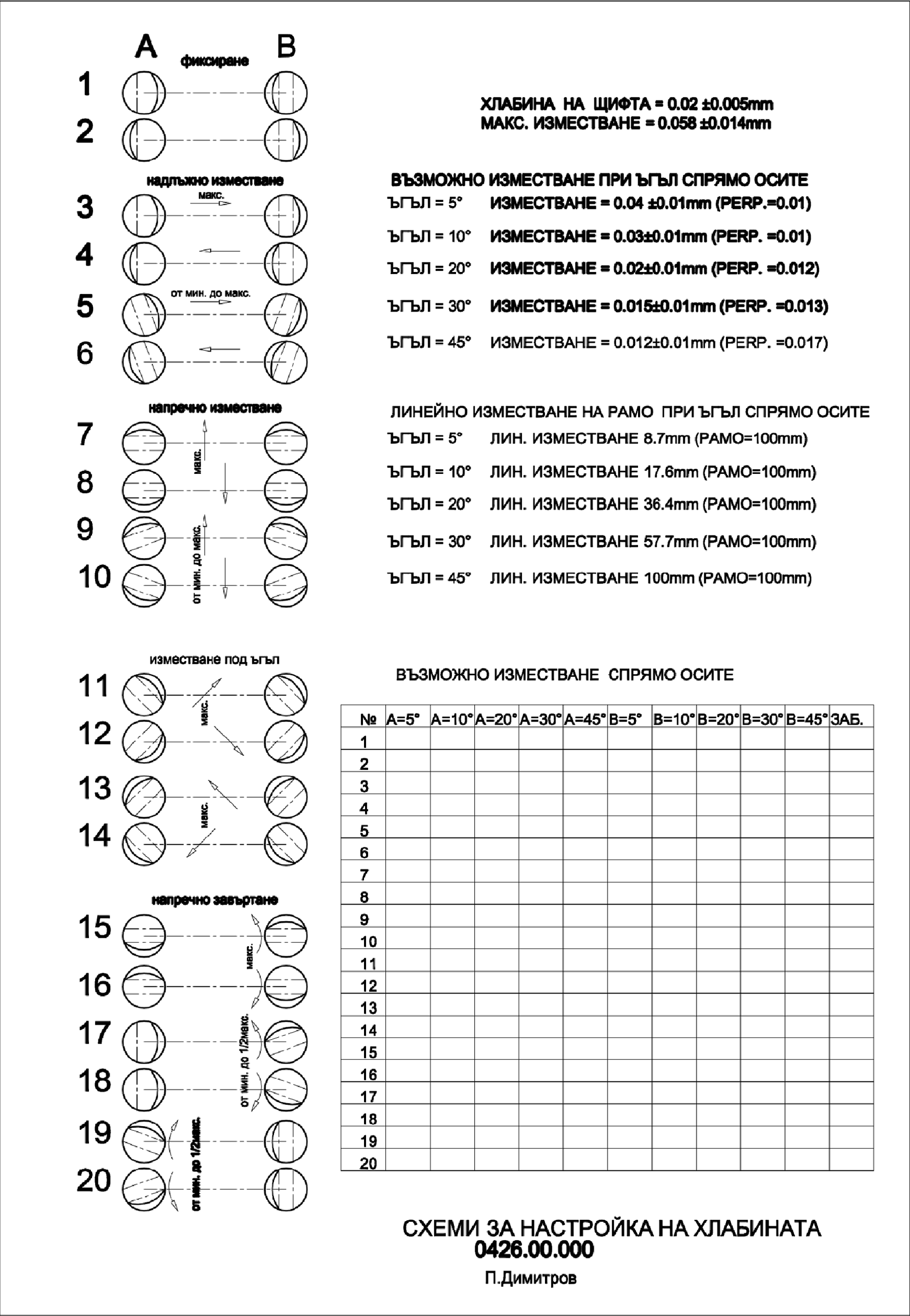
Фиг.5-54
ГЛАВА 6. КОНСТРУКЦИИ НА ИНСТРУМЕНТИТЕ ЗА ОБРАБОТКА НА ЛИСТОВ МАТЕРИАЛ (ЩАНЦИ, ЩАМПИ ЗА ЛИСТОВО ЩАМПОВАНЕ)
Съществуват много конструкции на инструменти за обработка на листов материал, различаващи се по вида на технологичните операции, по начина на тяхното изпълнение и съчетаване, по метода на транспортиране на заготовката между работните позиции, по вида на използваната изходна заготовка, по начина центроване и притискане на заготовката, по воденето на подвижните части на инструмента, по материала на матриците и поансоните и други признаци. Невъзможно е да се опишат всички конструкции и комбинации за щанците, защото в крайна сметка те зависят от конкретния детайл и въображението на конструктора. Разгледаните конструкции на основни типове щанци са практически изпробвани, като е наблегнато на ефективността и връзката на конструкцията с количеството произвеждани детайли, технолологичността на нейната изработка и лесна подръжка.
1. Едно операционни щанци - изрязващи, пробиващи, изтеглящи, огъващи, отбортоващи, формоващи.
Прилагат се при малък годишен обем от детайли – дребно серийно производство (примерно от 100 до 10000 за малки детайли, от 50 до 500 за голямогабаритни детайли). Може да се приеме, че детайли с размери под 100 мм са малки, а над 250 мм големи.
– Щанца за изрязване на изходна заготовка за изтегляне на неръждаем цилиндричен детайл с фланец е показана на Фиг.6-1 (сборен чертеж) и Фиг.6-2 (спецификация).
Щанцата е с вложки за матрица (поз.4) и поансон (поз.7), с притискач (поз.6) за събуване на лентата под въздействие на полеуретанова буферна втулка (поз.15). За позициониране на лентата се използват преден и страничен ограничители (поз.17 и поз.18). Това опростено решение е допустимо, защото не се търси точно разположение на изрязваните заготовки една спрямо друга – операцията се извършва изцяло за един ход. Ограничаването е с цел да осигури достатъчна големина (здравина) на свързващите отделните заготовки отпадъчни мостчета. Едностраното странично позициониране позволява да се работи дори с по-широка лента от необходимата. Подвижната и неподвижмата част на блока се направляват с колонка (поз.5) и втулка (поз.8) с триене при плъзгане, които са разположени в задната част за по-удобно ръчно подаване на лентата.
– Щанца за изтегляне на неръждаем цилиндричен детайл с фланец е показана на Фиг.6-3 (сборен чертеж) и Фиг.6-4 (спецификация).
Предназначена е за хидравлична преса с двойно действие на горния плъзгач и долен, механично задвижван повдигач, разполагаща с независими движения за притискане и изтегляне. Щанцата е с вложки за матрица (поз.2) и притискач (поз.5), с изтеглящ поансон (поз.6) и механичен избутвач на изтегления детайл (поз.8). За ръчно позициониране на изходната заготовка спрямо матрицата се използва ограничител (поз.4).Не е предвидено водене на подвижната и неподвижната част на блока, а се разчита на пресата.
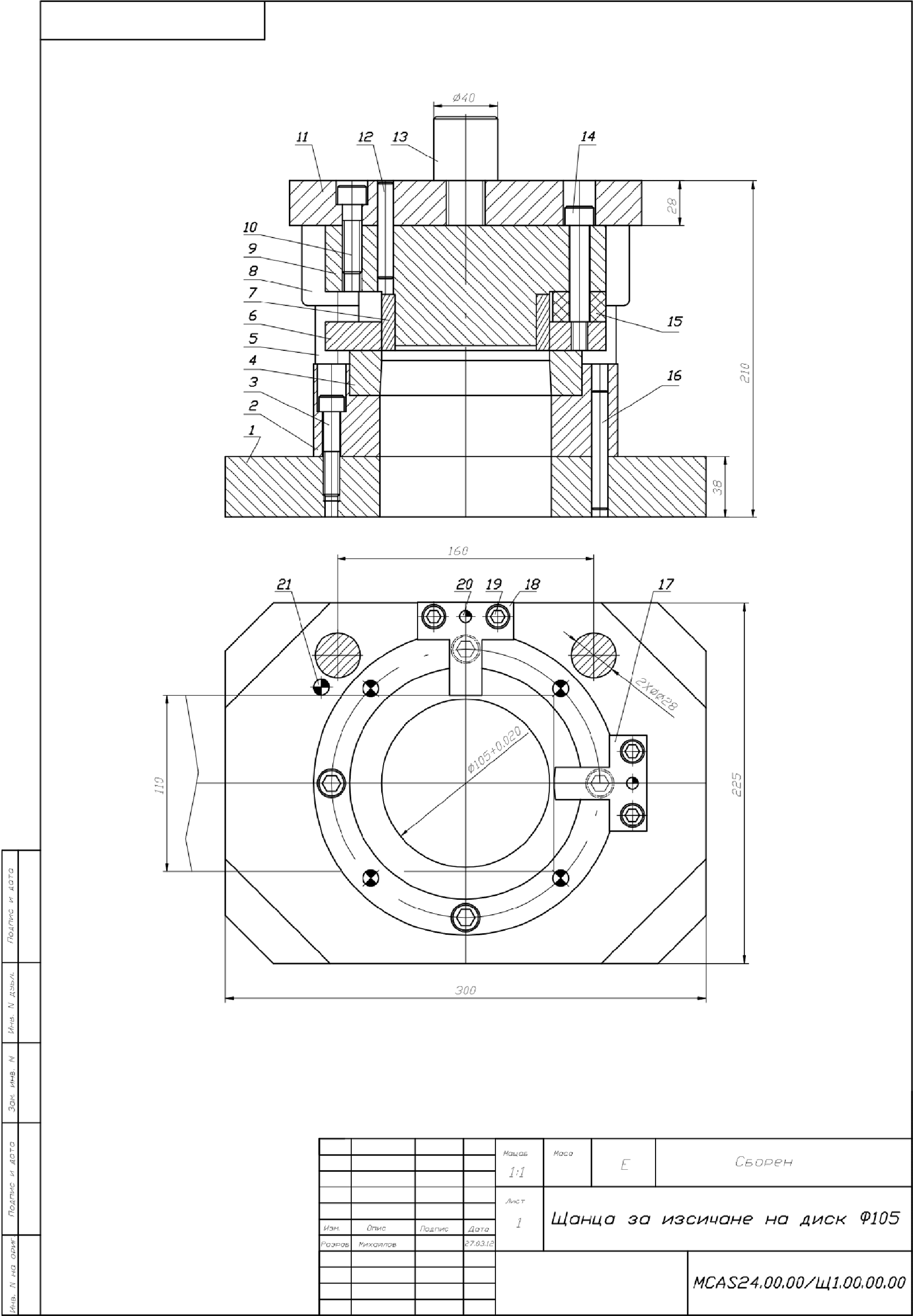
Фиг.6-1
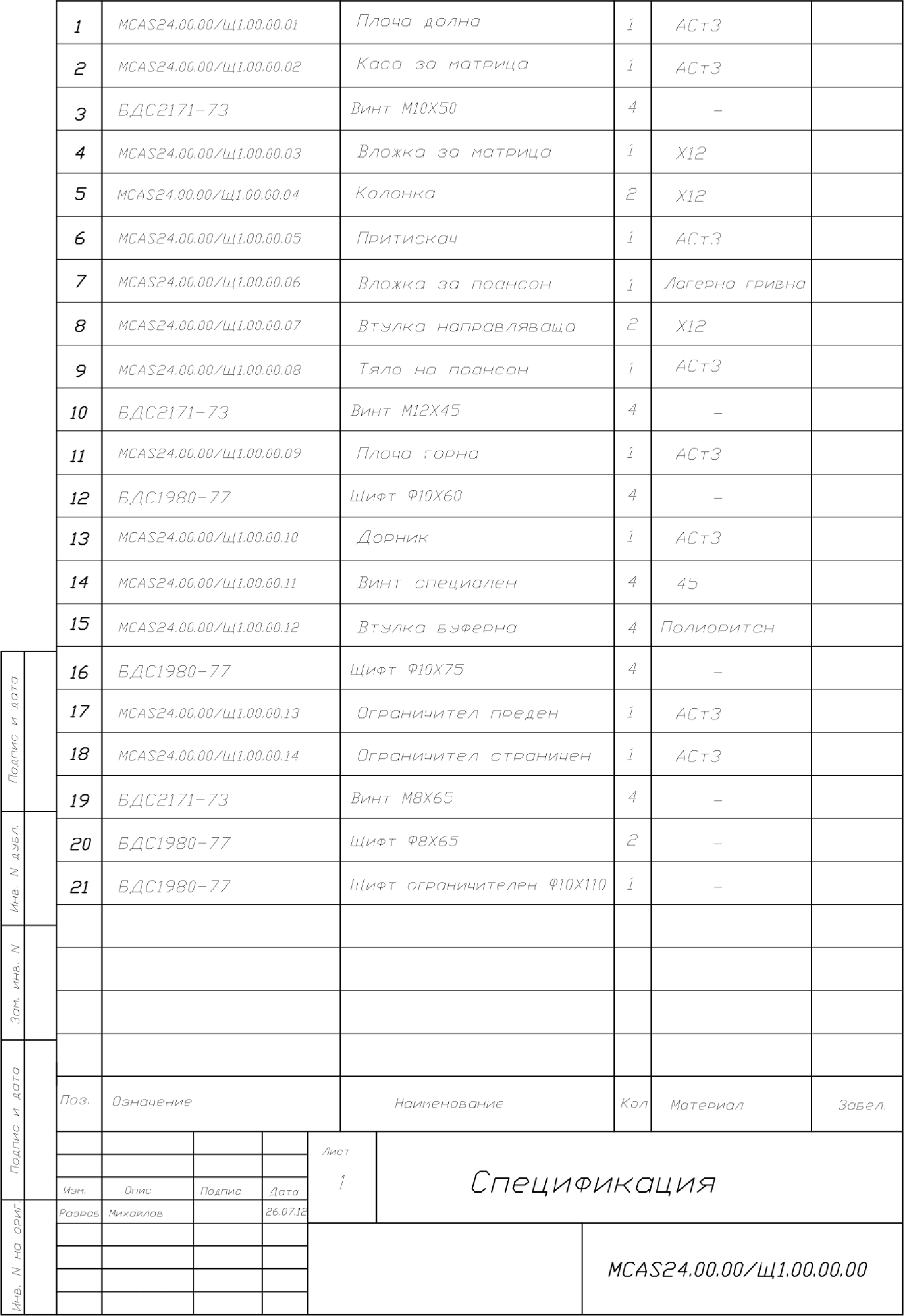
Фиг.6-2
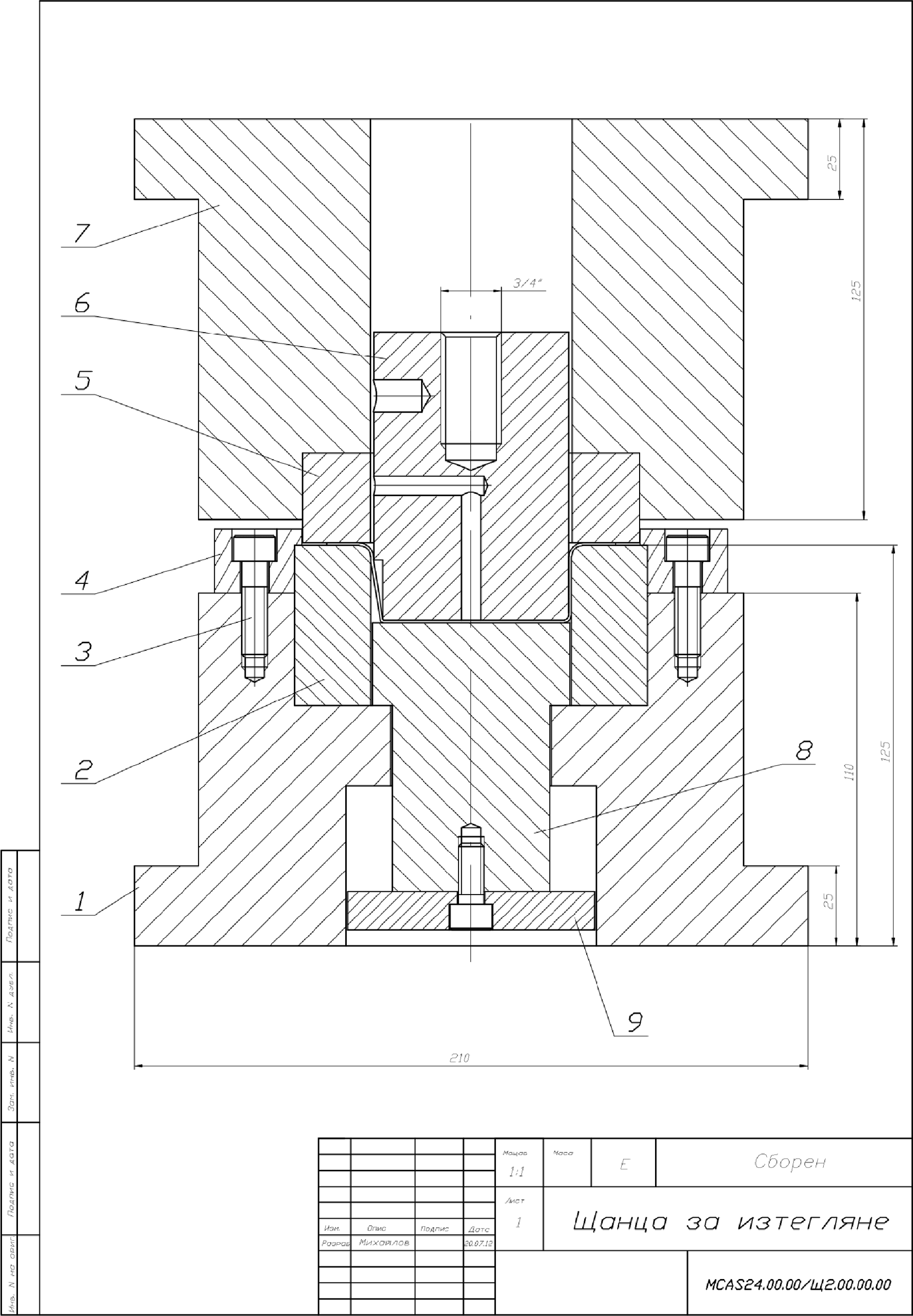
Фиг.6-3
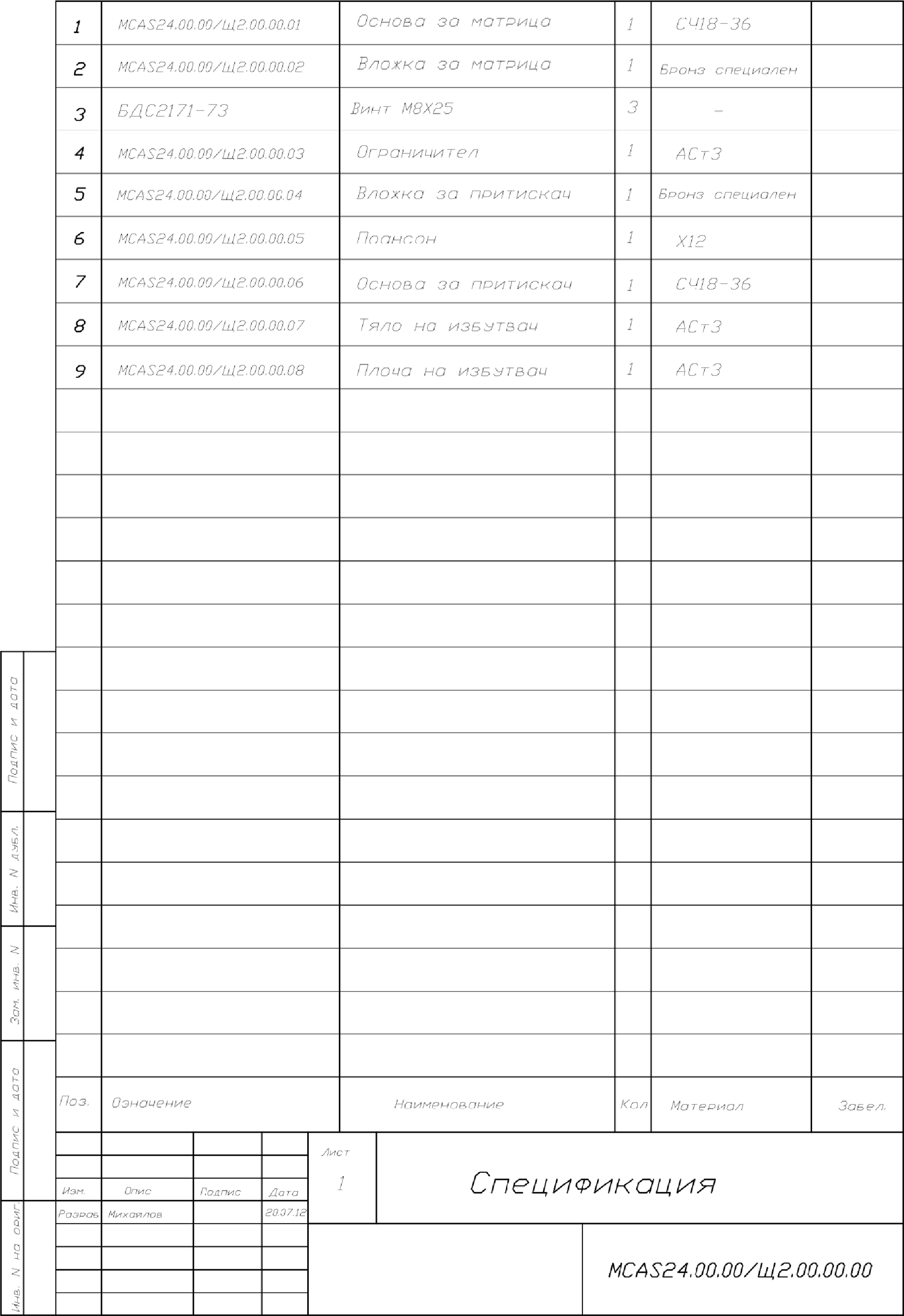
Фиг.6-4
– Щанца за второ огъване на детайл ПЛАНКА от Фиг.3-5 е показана на Фиг.6-5 (сборен чертеж) и Фиг.6-6 (спецификация).
Използваната заготовка е от щанца за огъване на Фиг.5-52. Щанцата е с огъваща вложка за матрица (поз.4) и огъващ поансон (поз.5), с долен изхвъргач (поз.10) за притискане и събуване на заготовката под въздействие на буферна пружина (поз.26) чрез щифтовете (поз.27). За позициониране на заготовката се използват ловителите-фиксатори(поз.12 и поз.15), базиращи по отвор ф5 mm и радиуса на изрязан външен профил. Подвижната и неподвижмата част на блока се направляват с колонка (поз.14) и втулка (поз.17) с триене при плъзгане.
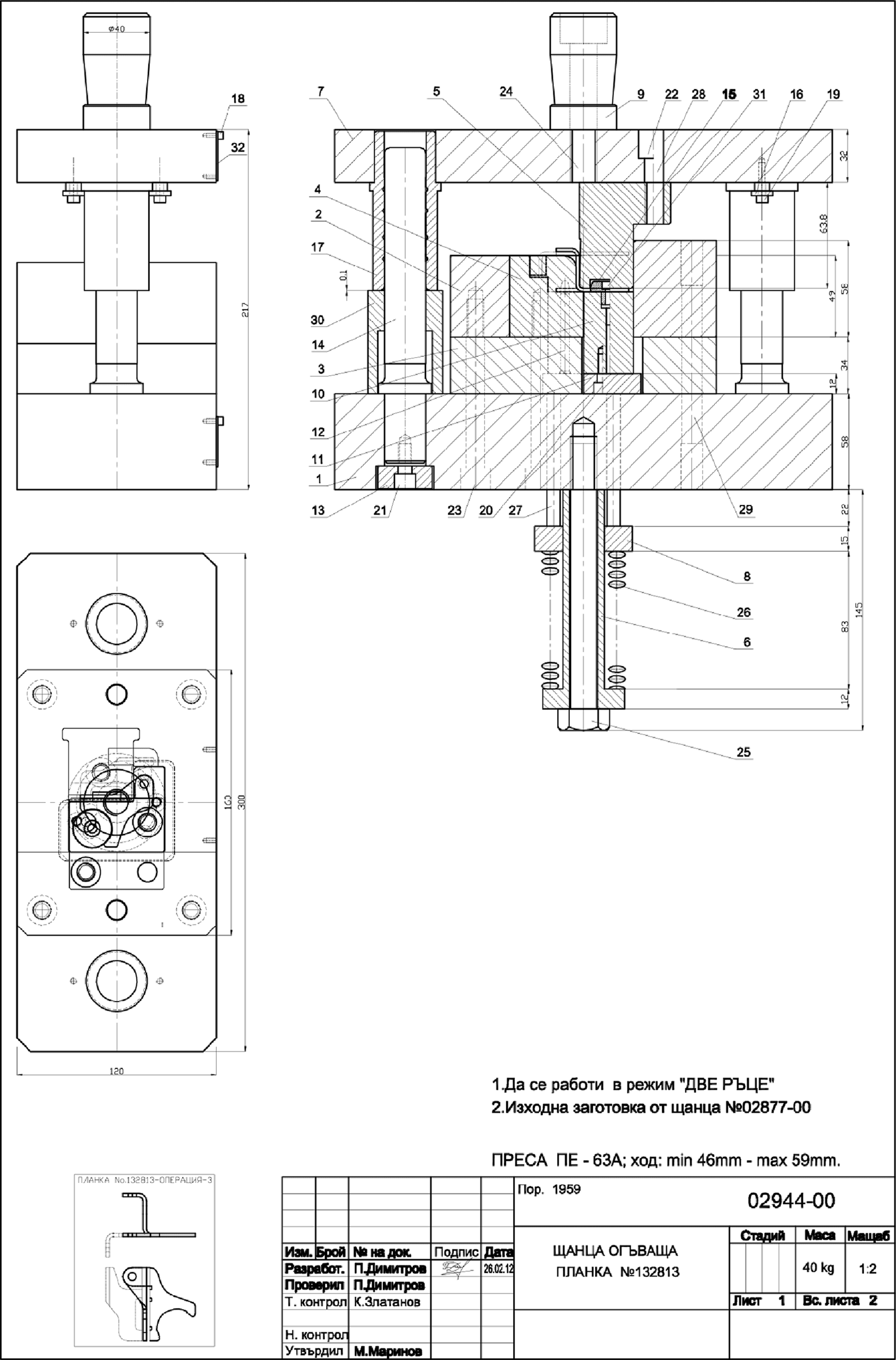
Фиг.6-5
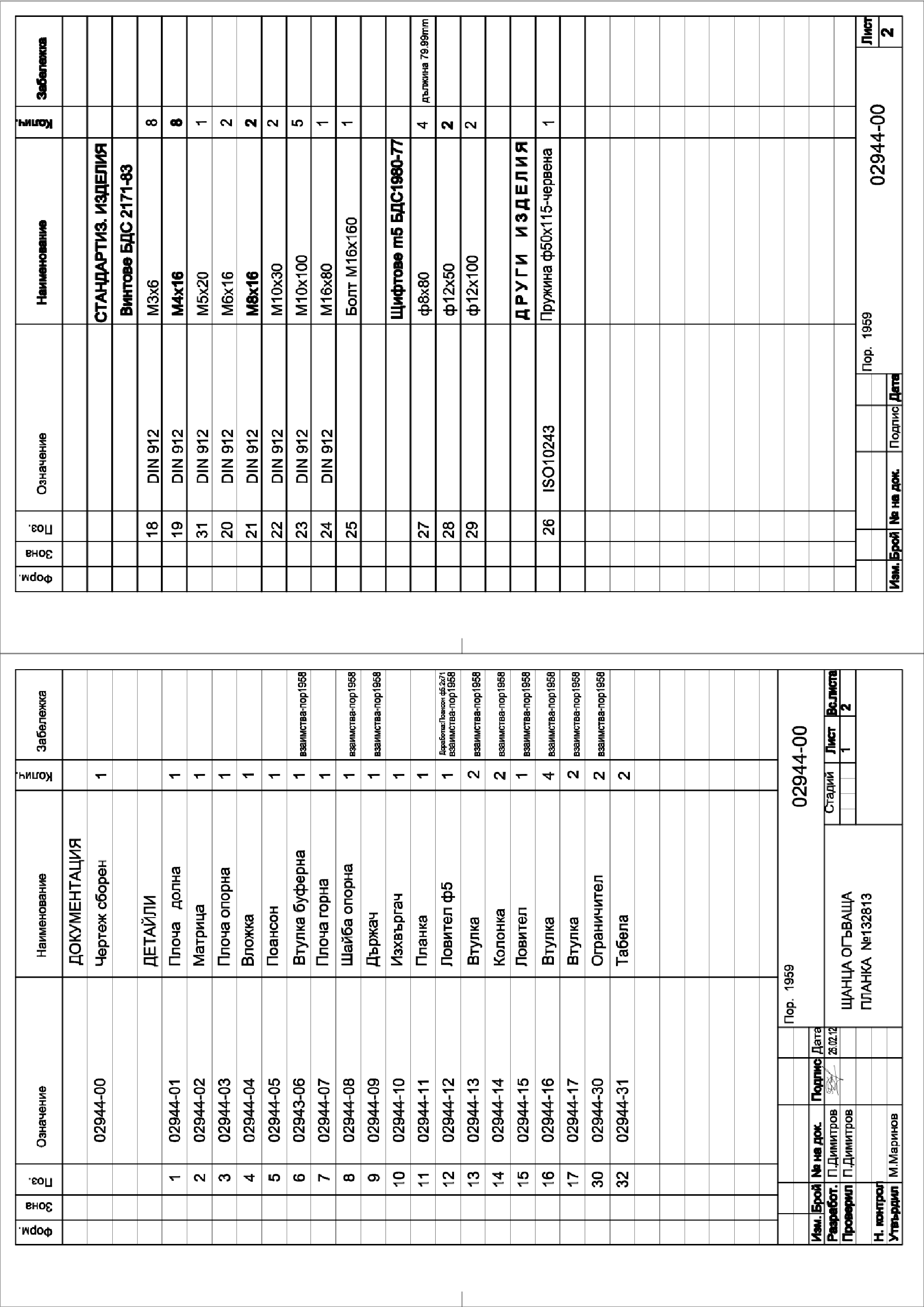
Фиг.6-6
– Щанца за външно отбортоване на детайл ПРЕДПАЗИТЕЛ ЗА ЪЛОШЛАФ - Фиг.6-7
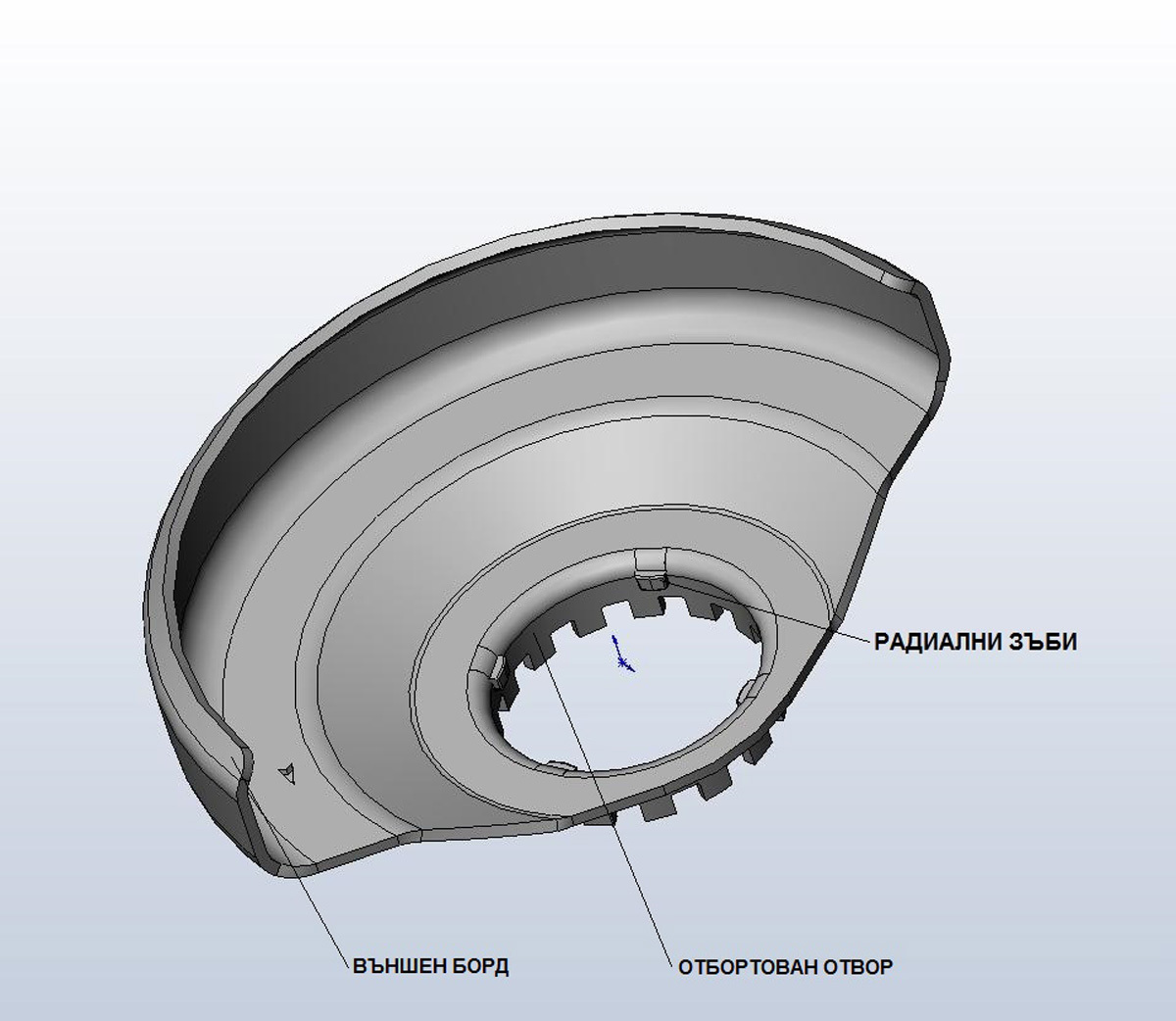
Фиг.6-7
е показана на Фиг.6-8 (общ вид) и Фиг.6-9 (надлъжен разрез).
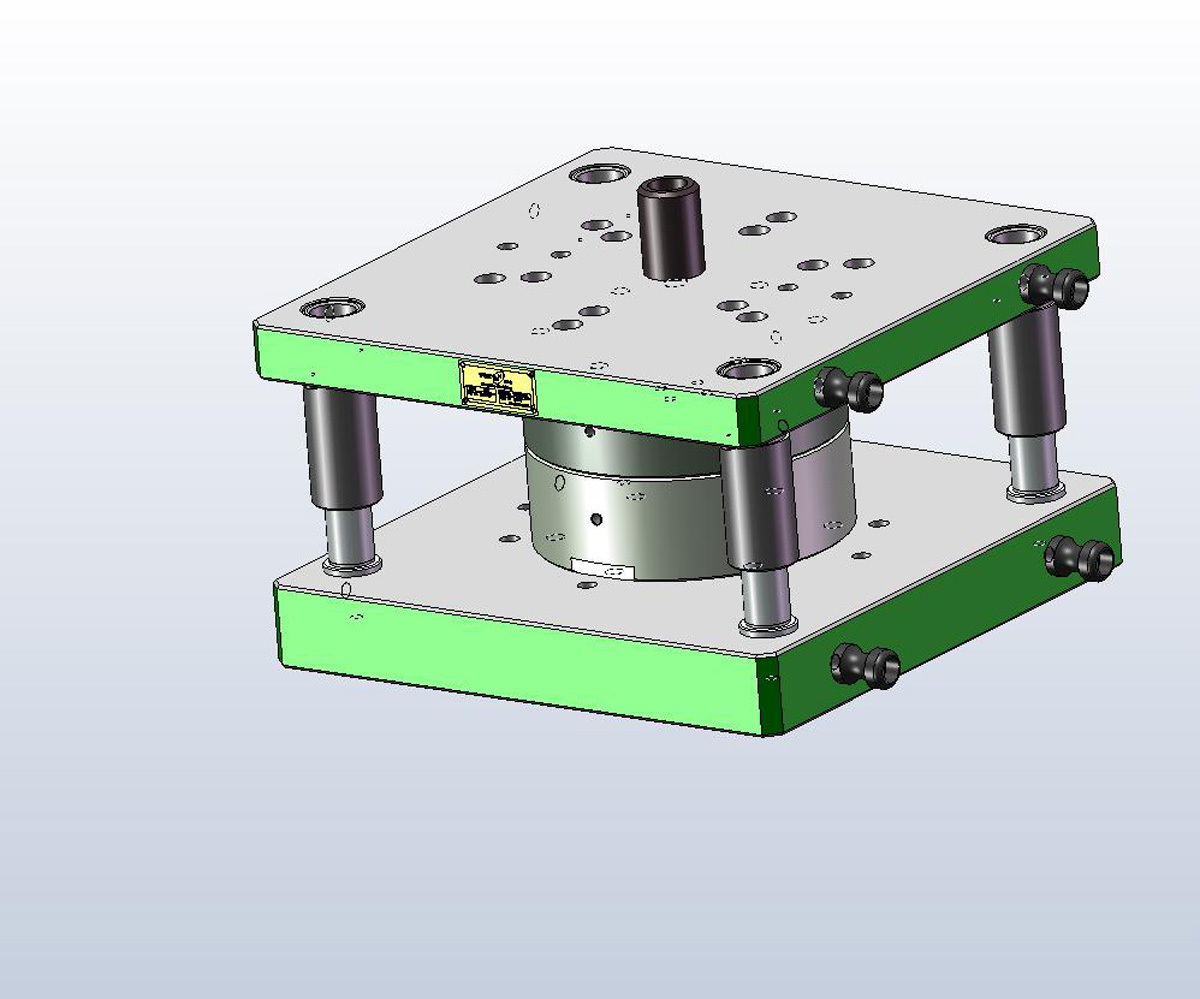
Фиг.6-8
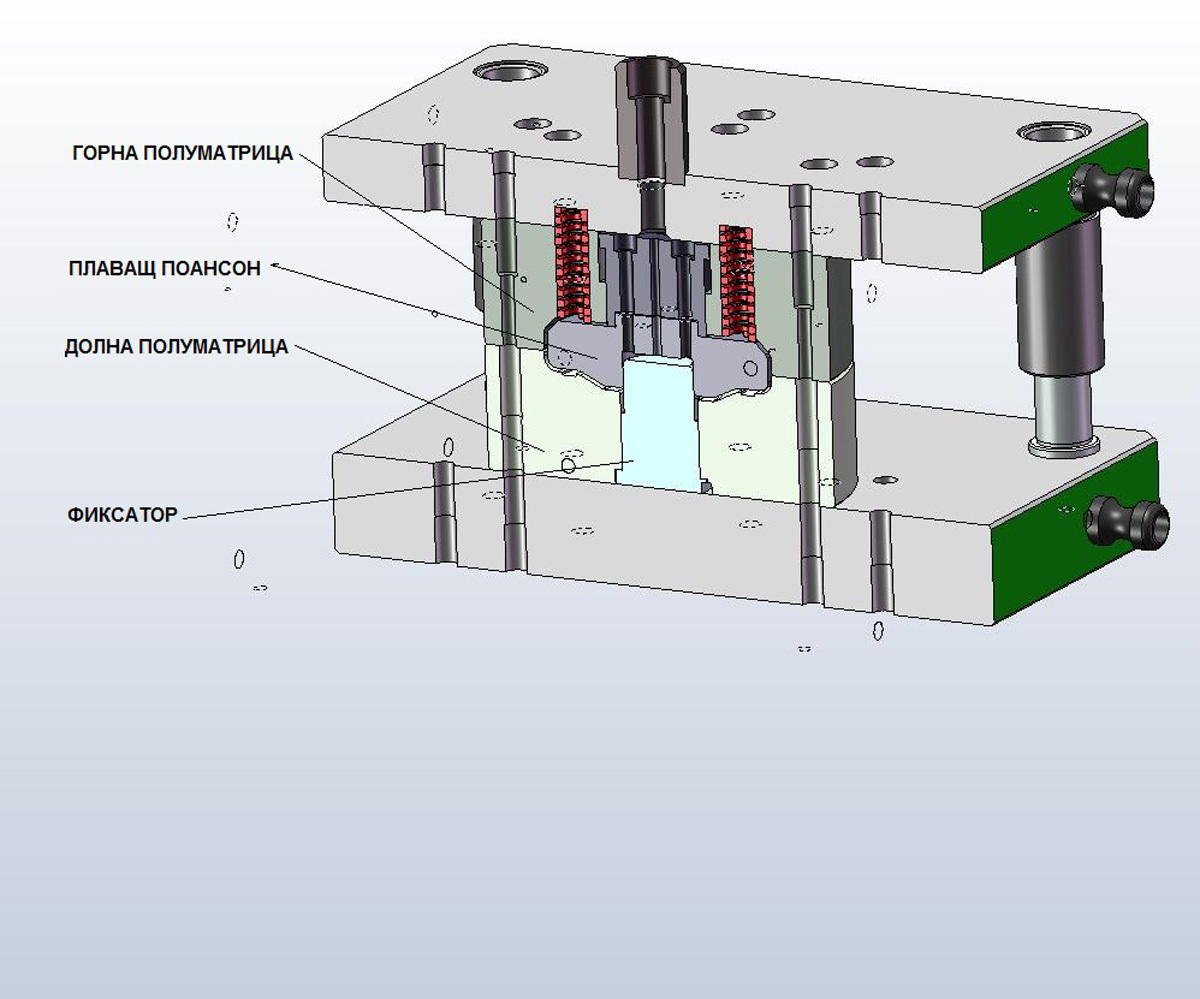
Фиг.6-9
Щанцата включва две полуматрици и плаващ поансон, позволяващ начално притискане на заготовката и изваждането на последната над долната полуматрица в края на хода, от където се сваля ръчно в радиална посока. За ръчно позициониране на изходната заготовка спрямо долната полуматрица се използва фиксатор. Подвижната и неподвижната част на блока се направляват с колонки и втулки с триене при плъзгане.
– Щанца за формоване на детайл КАПАК -Фиг.5-40 е показана на Фиг.6-10 и Фиг.6-11 (общ вид),
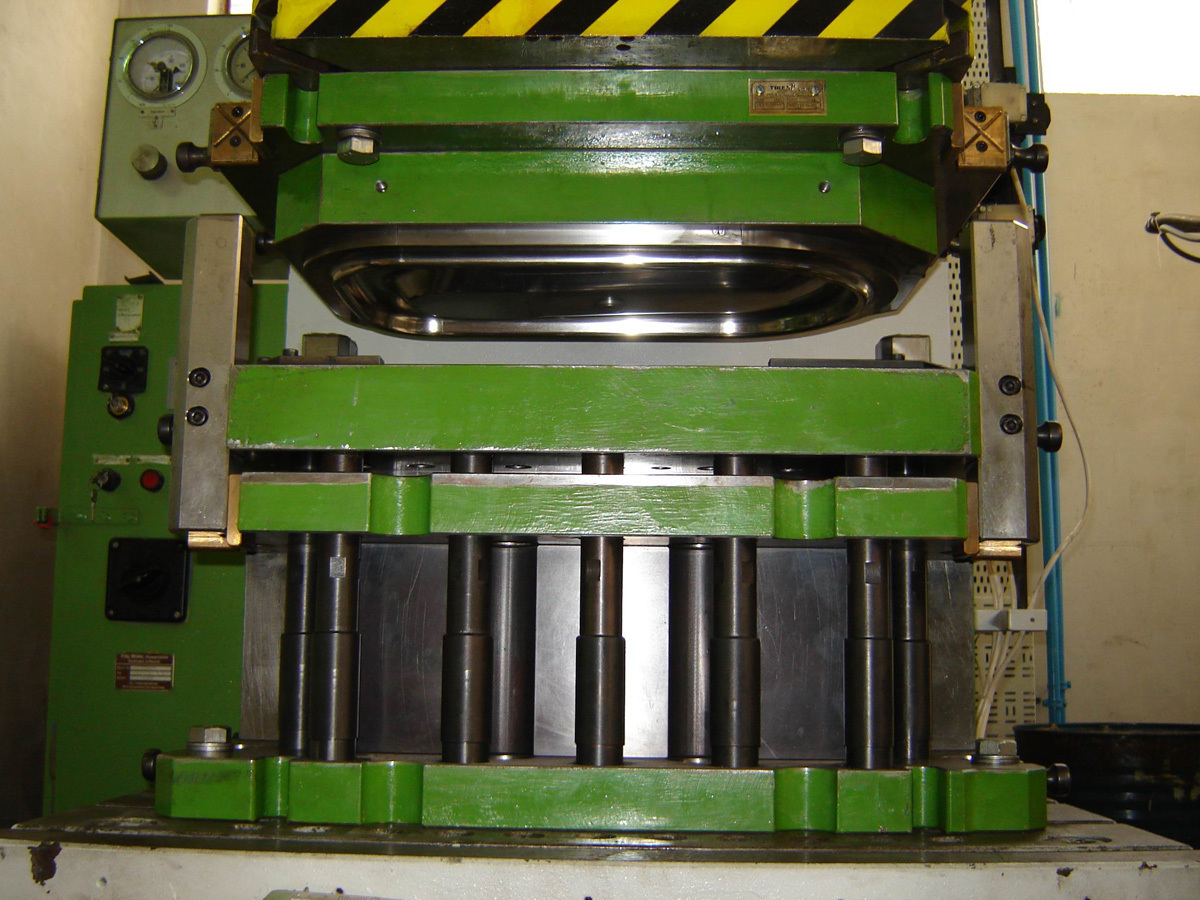
Фиг.6-10
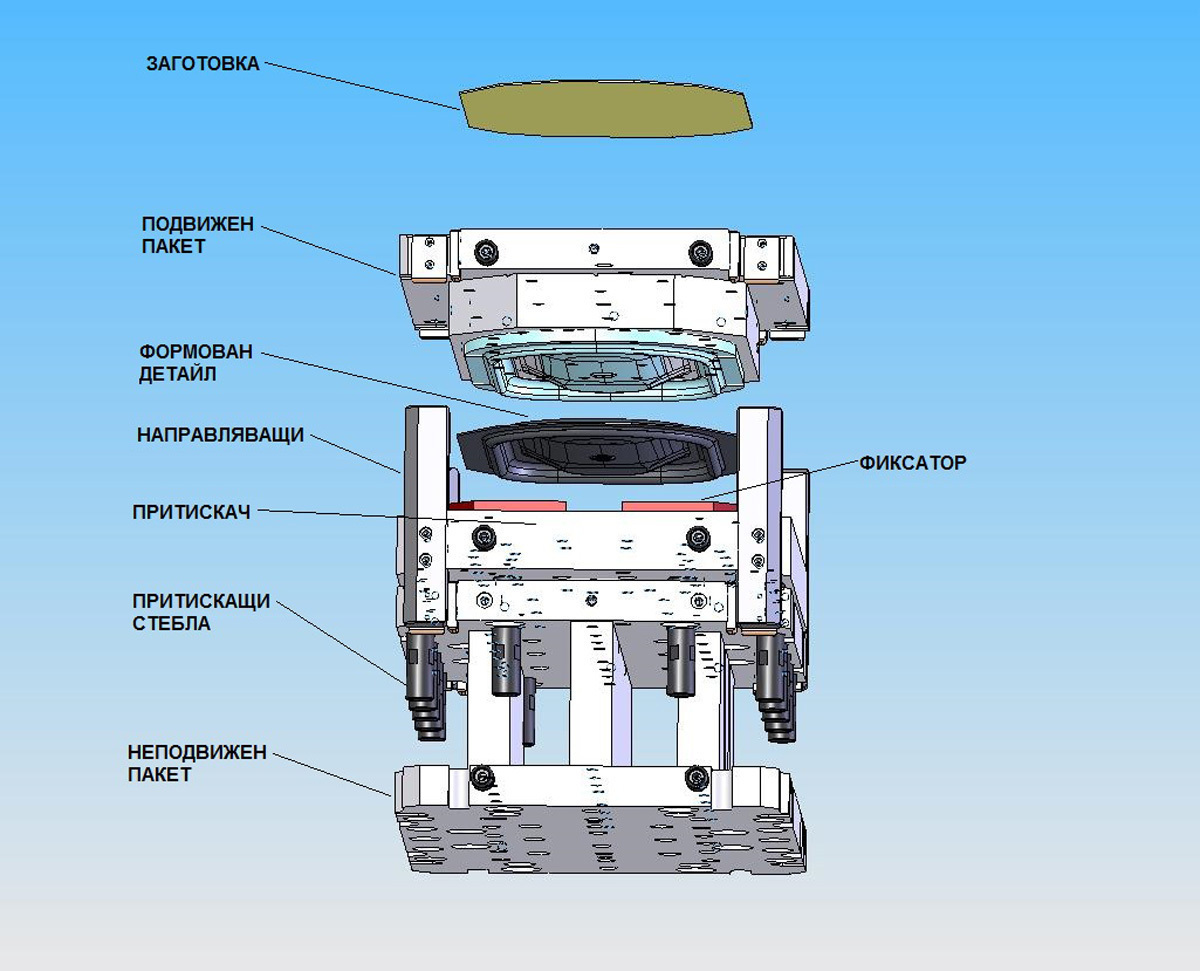
Фиг.6-11
и на Фиг.6-12 (неподвижен пакет с притискач).
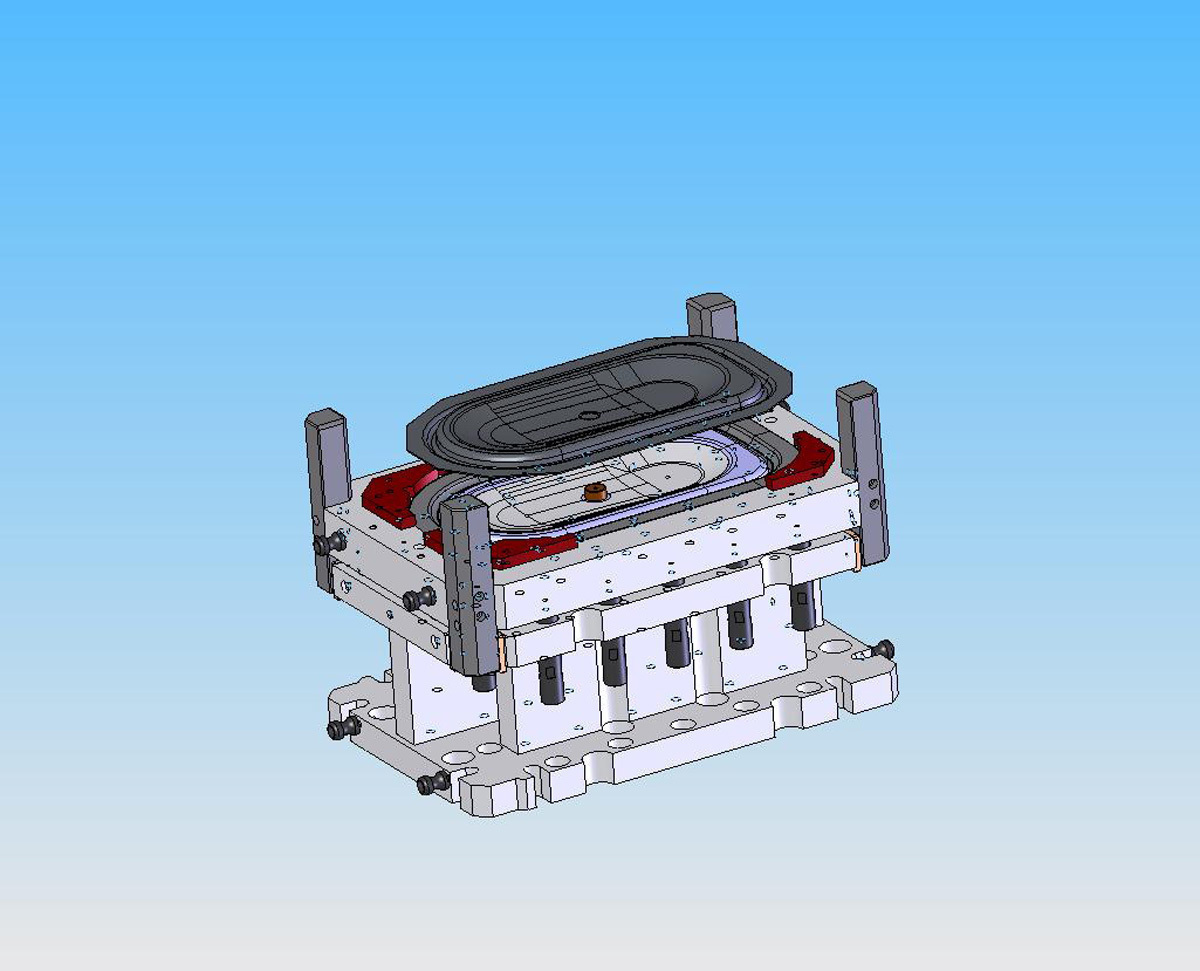
Фиг.6-12
Предназначена е за двойно действаща хидравлична преса с долен хидравличен буфер – за притискане, изтегляне и повдигане на готовия детайл. Активните части на щанцата включват формоваща матрица (виж Фиг.5-41), закрепена към неподвижния пакет, формоващ поансон (виж Фиг.5-42, закрепен към подвижния пакет и плаващ формоващ притискач - Фиг.6-13,
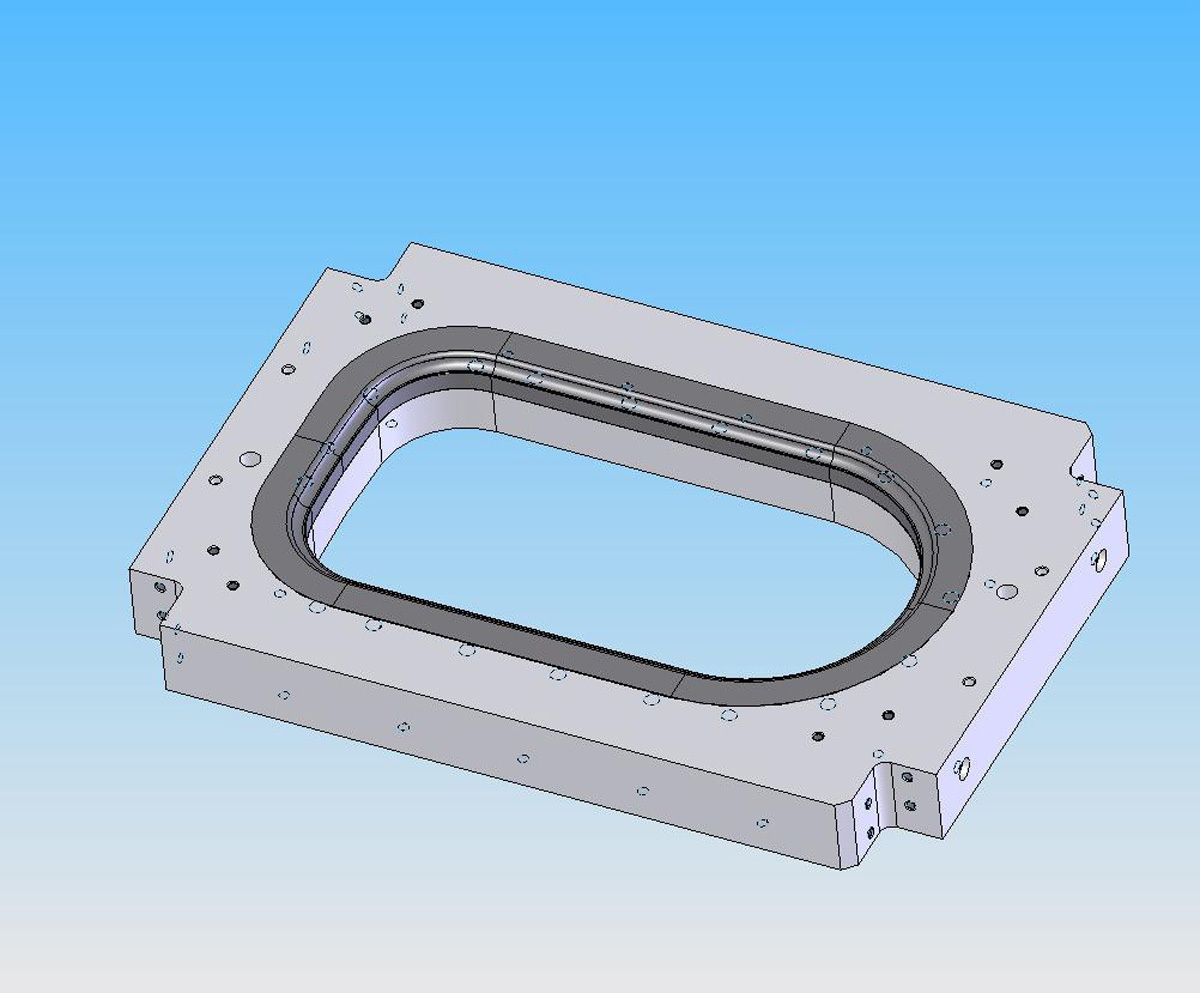
Фиг.6-13
който се води спрямо подвижния и неподвижния пакети. Поради големите размери на детайла, активните части са съставни – носеща стоманена плоча и вградени закалени секционни вложки. За ръчно позициониране на изходната заготовка спрямо матрицата и притискача се използват фиксатори, базиращи по външния контур. Притискачът предава технологичното натоварване на хидравличния буфер на пресата чрез набор от притискащи стебла. Воденето на притискача спрямо подвижния и неподвижния пакет е с призматични направляващи и бронзови пластини, разположени в ъглите. По този начин е възможно поемане на големи странични сили и е гарантирано повече място и удобство за поставяне и снемане на заготовката.
2. Много операционни щанци.
Прилагат се при голям годишен обем от детайли – едро серийно производство (примерно от 100000 до 1000000 за малки детайли, от 20000 до 200000 за голямогабаритни детайли). Важни за ефективното прилагане на този тип щанци са сложността и размерите на обработваемия детайл, влияещи на броя, вида и последователността на операциите. Колкото повече операции и по-големи размери има детайла, толкова по-малка е необходимата годишна серия за ефективно използване на много операционно щанцоване.
В зависимост от начина на изпълнение на операциите и (или) транспорта на заготовката до и от работна позиция са:
2.1.С последователно действие в лента (прогресивни) за пробиване и изрязване, за пробиване, изрязване, изтегляне, обрязване, за пробиване, формоване, огъване, изрязване.
– Щанца за пробиване и изрязване на изходна (плоска) заготовка за детайл ПЛАНКА от Фиг.3-5 е показана на Фиг.6-14 (сборен чертеж), на Фиг.4-5 (технологична схема на лентата) и на Фиг.6-15 (спецификация).
Конструкцията включва матрица (поз.2), режещи поансони (поз.8, поз.10, поз.20, поз.22, поз.23, поз.24, поз.25) и неподвижен водач (поз.3), който е предназначен да води поансоните спрямо матрицата и да гарантира тяхното събуване от лентата. Центроване и водене на лентата се извършва с ловители (поз.19) и лентоводачи (поз.4). Особеност на щанцата е използване на глави (поз.11, поз.12) и задържащи скоби (поз.21, поз.26, поз.27, поз.28) за събуване на поансоните, поради по-голямата дебелина на материала и свързаната с нея увеличена събуваща сила. Наред с това, такова решение позволява известна степен на свобода на поансоните в поансонодържача и тяхното самонагласяне спрямо водача (плаване). Подвижната и неподвижмата част на блока се направляват с колонка (поз.14) и втулка (поз.17) с триене при плъзгане, които не са задължителни, но намаляват натоварването и износването на поансоните и удължават живота на щанцата.
– Щанца за пробиване, изтегляне, калиброване, пробиване на дъното и обрязване на фланеца за детайл ВТУЛКА от Фиг.3-4 е показана на Фиг.6-16 (сборен чертеж - изглед от горе), на Фиг.6-17 (сборен чертеж – надлъжен разрез А-А), на Фиг.6-18 (сборен чертеж – напречен разрез В-В), на Фиг.5-9 (технологична схема на лентата) и на Фиг.6-19, Фиг.6-20 (спецификация).
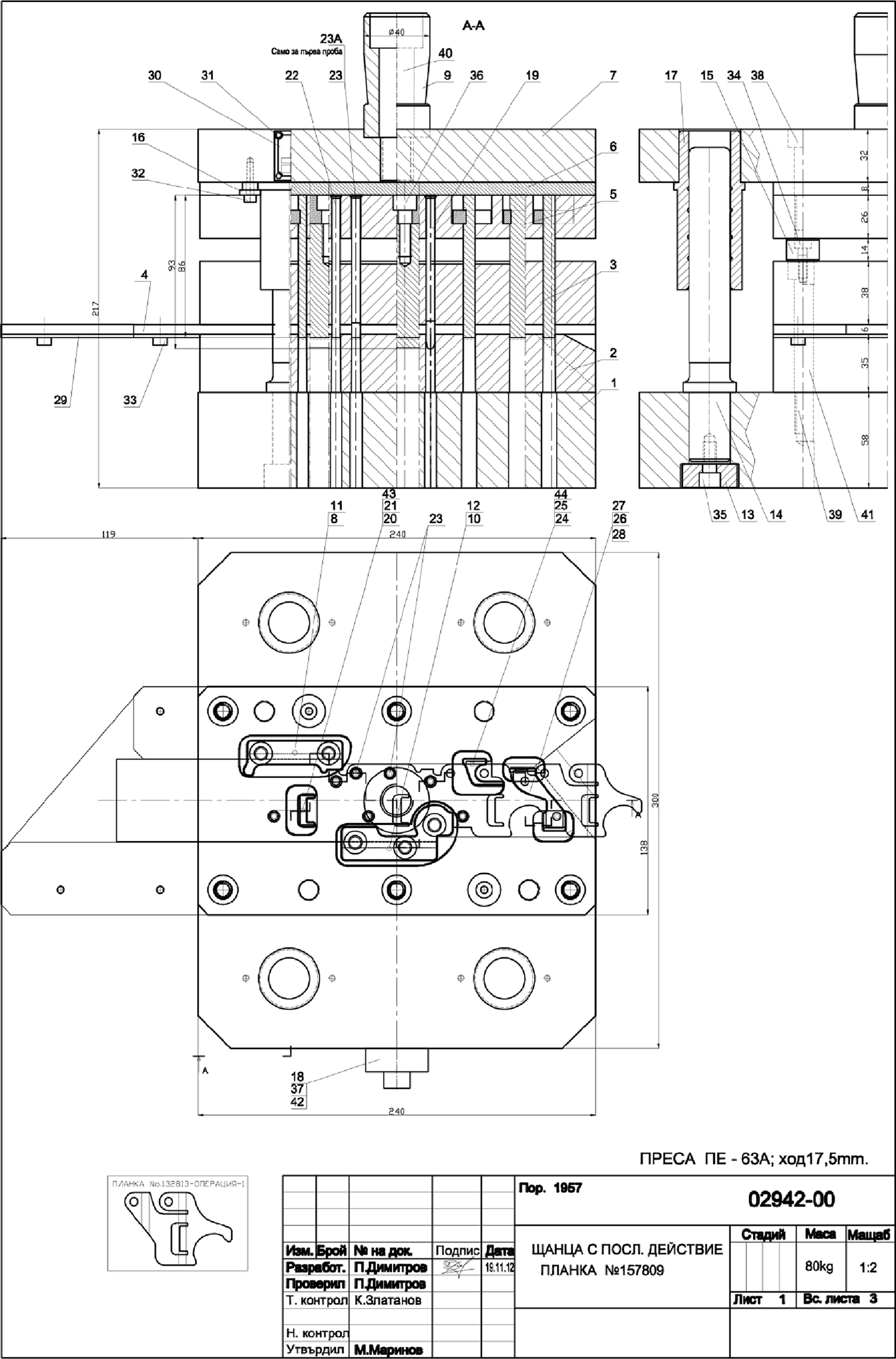
Фиг.6-14
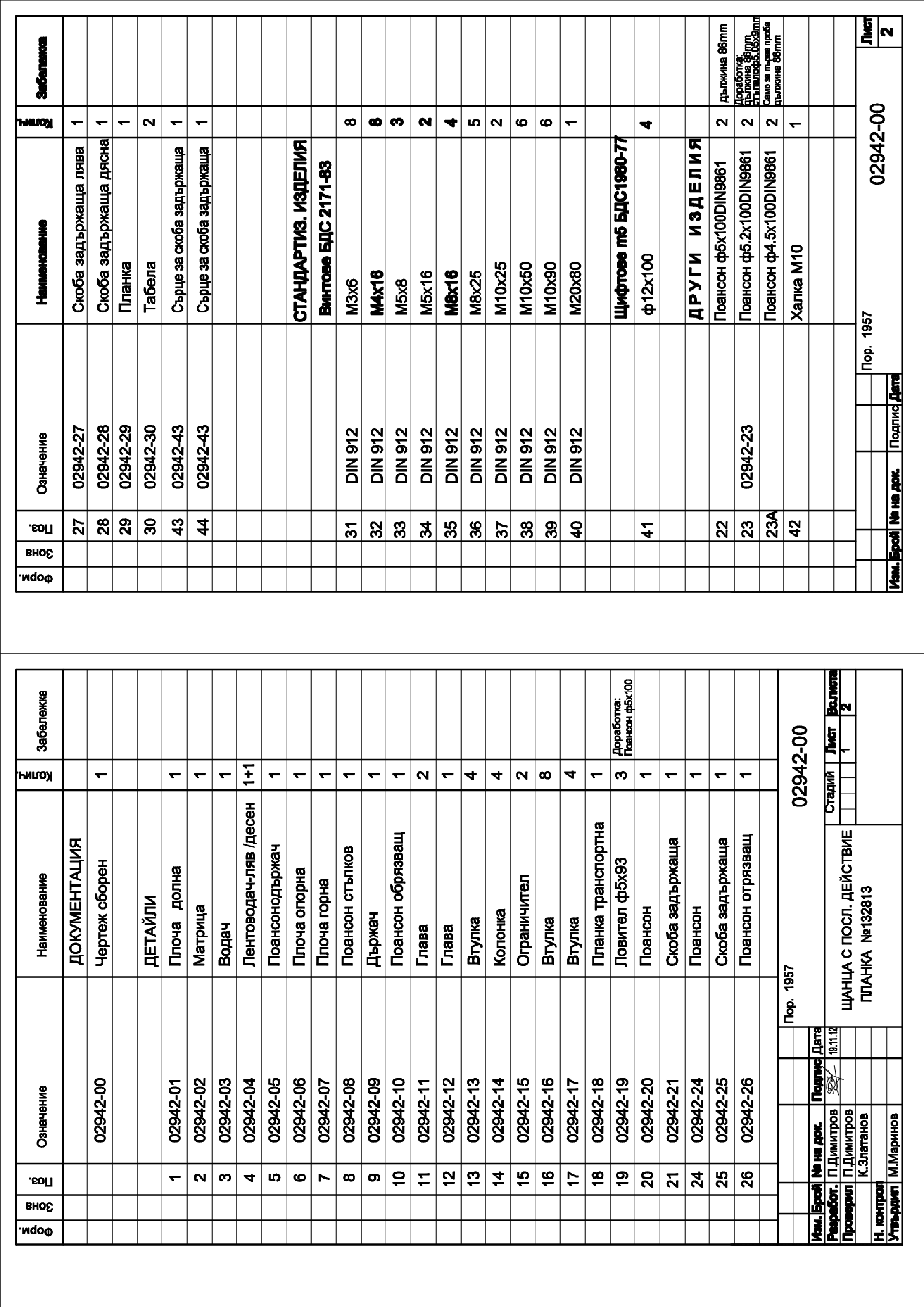
Фиг.6-15
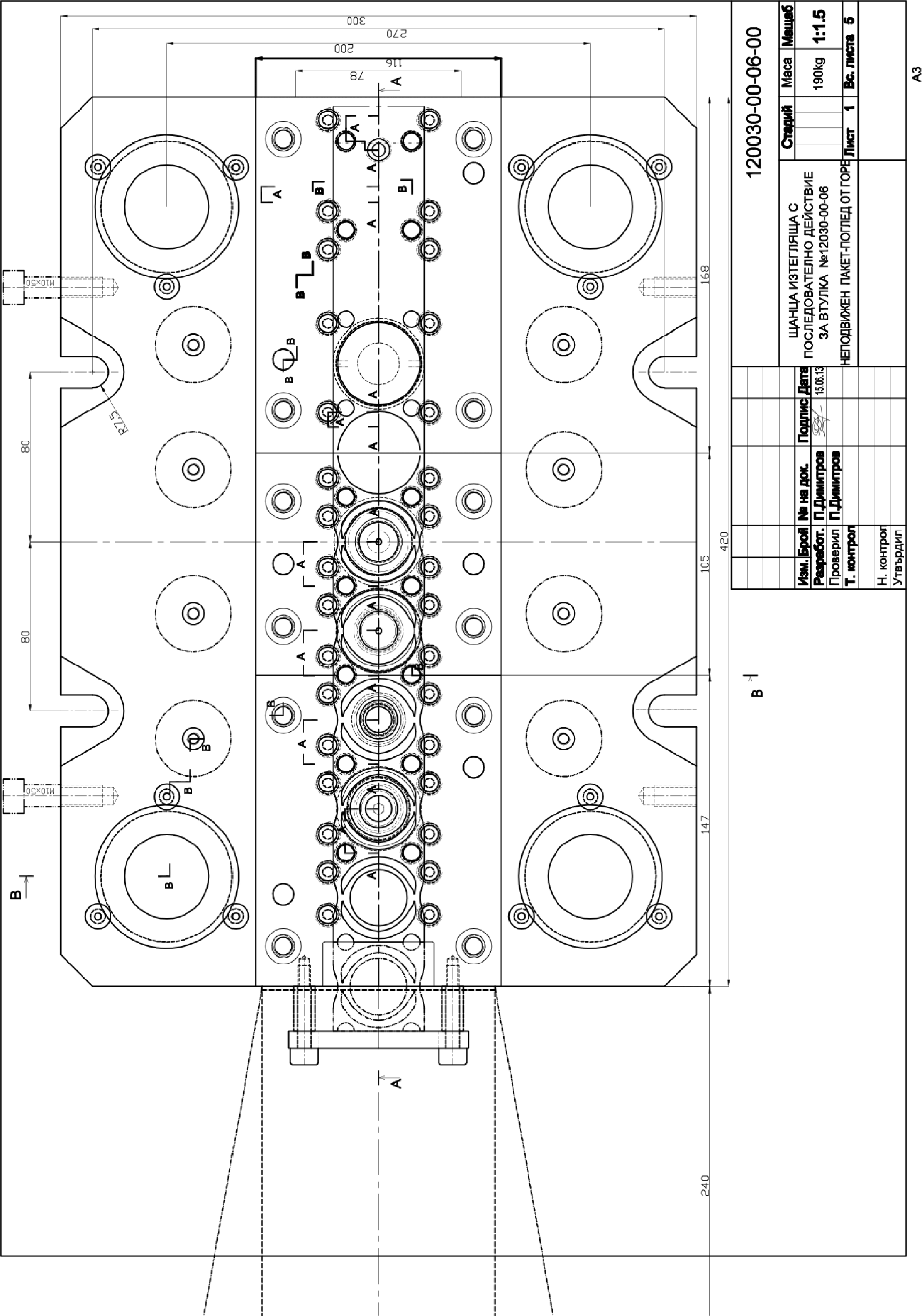
Фиг.6-16
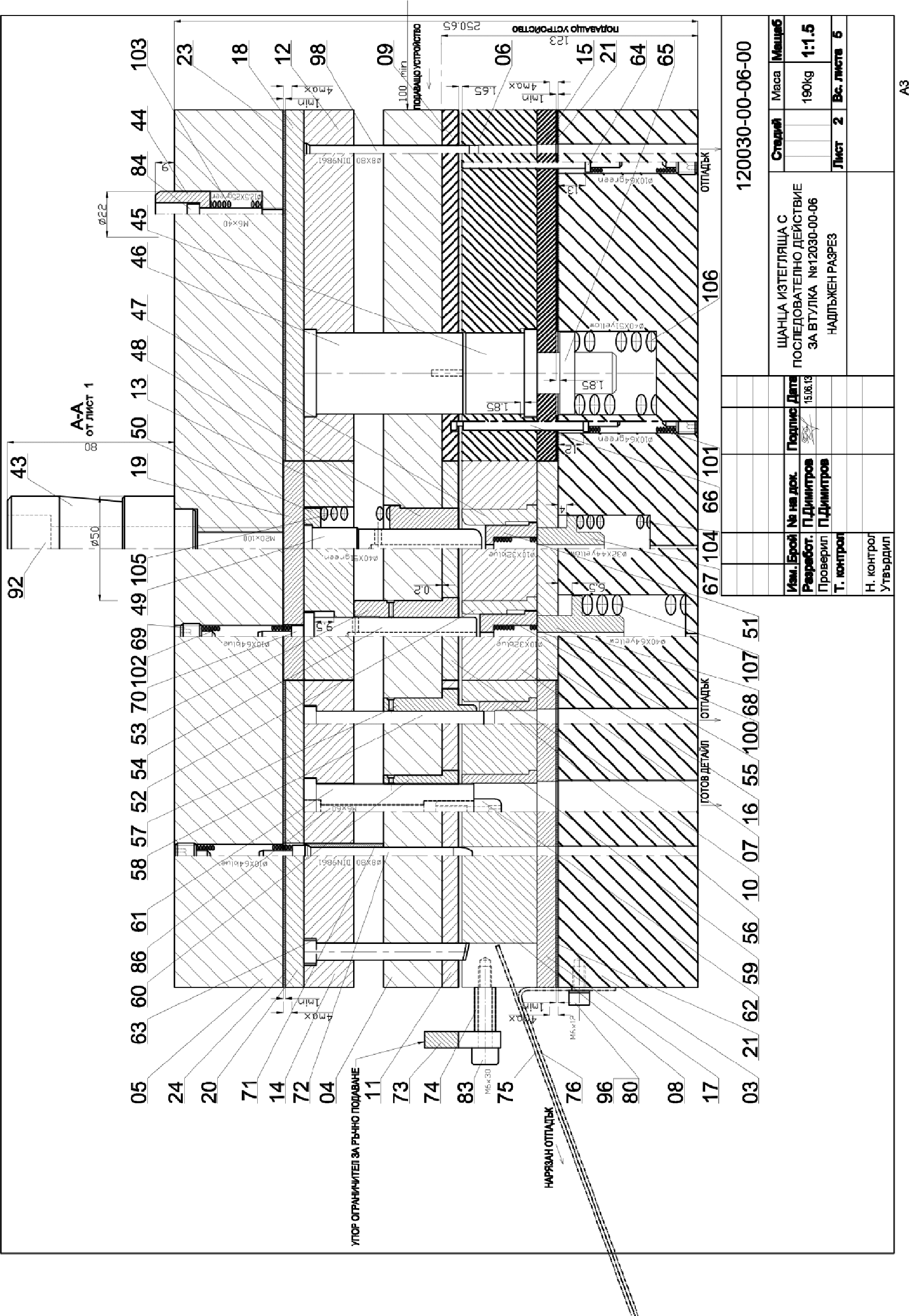
Фиг.6-17
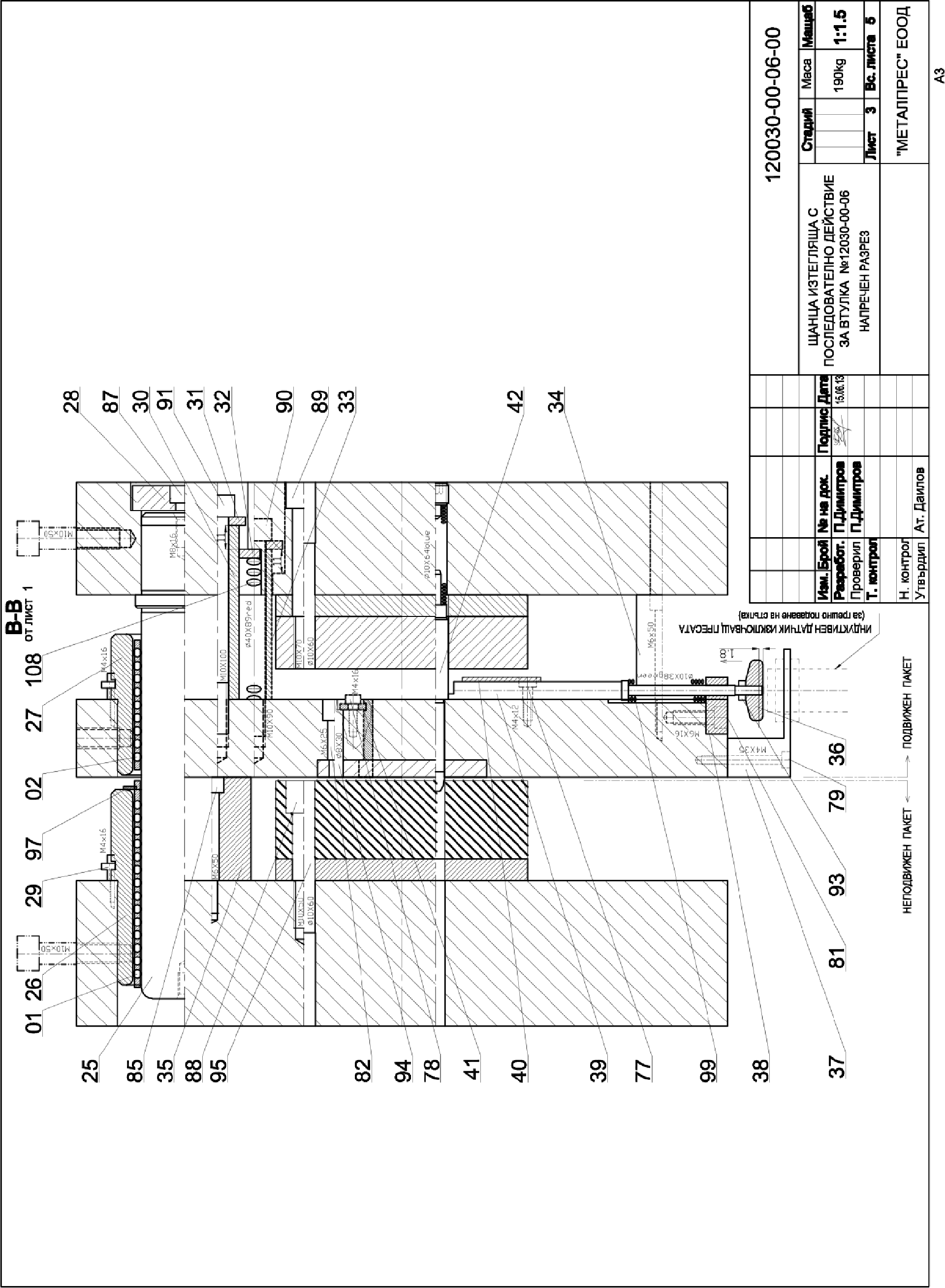
Фиг.6-18
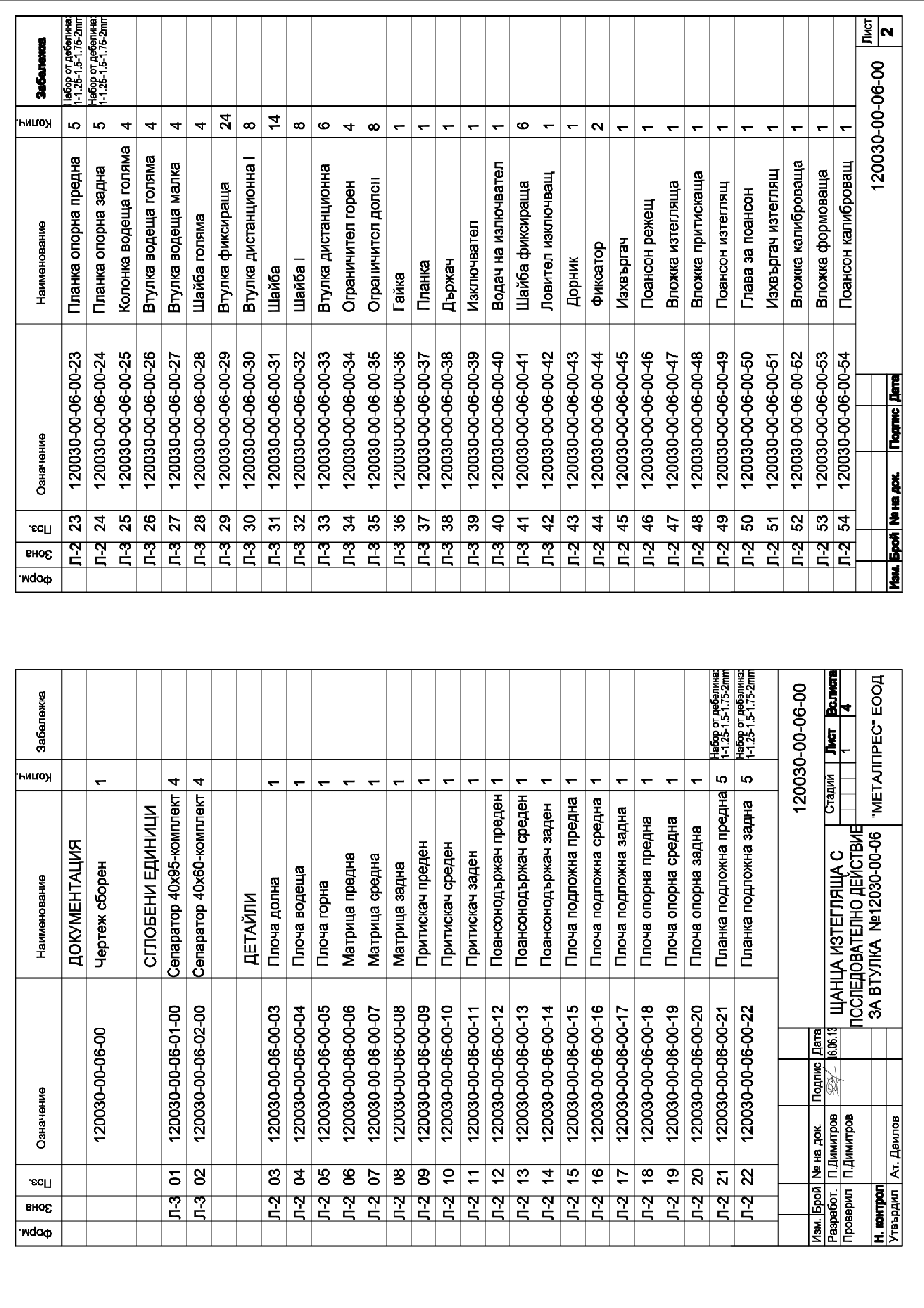
Фиг.6-19
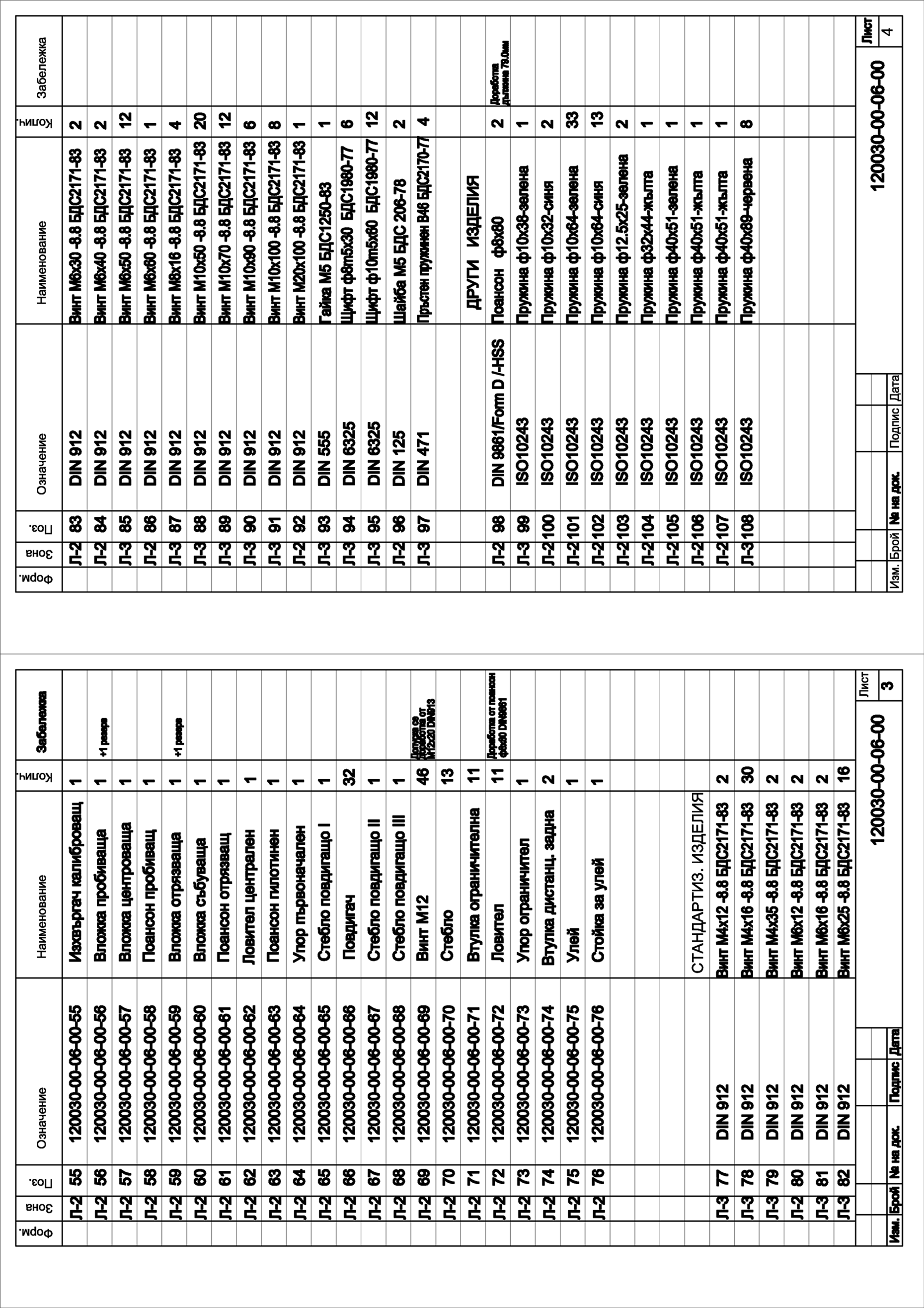
Фиг.6-20
Предназначена е за работа на преса с подаващо устройство за лентата. Конструкцията включва матрица от 3 части (поз.6, поз.7, поз.8), режещи поансони (поз.46, поз.58, поз.61, поз.63, поз.98) със съответните режещи вложки (поз.56, поз.59) и изтелящи поансони (поз.49, поз.54) със съответните изтеглящи вложки (поз.47, поз.52) .За притискане и събуване се използва подпружинена водеща плоча (поз.4), снабдена с 3 закалени притискача (поз.9, поз.10, поз.11) и вложки (поз.48, поз.53, поз.57, поз.60), както и самостоятелно притискане на първото изтегляне чрез пружина (поз.105). Разделението на части е с цел по-лесна подръжка, защото режещите матрици и поансони се затъпяват при работа и е необходимо периодично да се заточват. Под тях се монтират набор от сменни подложни планки (поз.21, поз.22, поз.23, поз.24), които компенсират намляването на височината след заточване. За водене и центроване на лентата са включени подпружинени повдигачи (поз.66), които водят и събуват лентата в специален канал и подпружинени ловители (поз.72), чиято конструкция позволява при грешно подаване да се вдигнат нагоре, вместо да деформират лентата и предизвикат счупване. За да се гарантира спиране на пресата при проблем с подаването на стъпка, в щанцата е предвиден изключващ ловител (поз.42), който чрез защитно устройство със сензор изключва електрическото захранване, когато не е попаднал в отвор на лентата. По този начин не се позволява старт до намесата на оператора и отстраняване на проблема. Щанцата е предвидена и за работа с ръчно подаване на лентата до упор-ограничител (поз.73). Точното водене (с нулева хлабина) на подвижния спрямо неподвижния пакет се извършва с триене при търкаляне посредством водещи колонки (поз.25), втулки (поз.26, поз.27) и сачмени сепаратори (поз.1, поз.2).
– Щанца за пробиване, маркиране, формоване на фаски, огъване и изрязване на детайл INCISIVO е показана на Фиг.5-28 (сборен чертеж - изглед от горе), на Фиг.5-30 (сборен чертеж – надлъжен разрез В-В), на Фиг.5-29 (сборен чертеж – напречен разрез А-А), на Фиг.5-7 (технологична схема на лентата) и на Фиг.5-31 (спецификация). Конструкцията включва матрица (поз.3), режещи поансони (поз.30, поз.31, поз.32, поз.33, поз.34, поз.50, поз.57) и огъващи поансони (поз.35, поз.37, поз.41, поз.45) с огъващи вложки (поз.36, поз.38, поз.42, поз.46). Маркиране на надпис “16А “ от долната страна на лентата става с маркиращи поансон и вложка (поз.58, поз.59). За притискане и събуване на лентата се използва подпружинена водеща плоча (поз.11). Водене и центроване на лентата се изпълнява от подпружинени призматични повдигачи (поз.20), които водят и събуват лентата в страничен канал, упор за ръчно подаване (поз.27) и подпружинени ловители (поз.51), чиято конструкция позволява при грешно подаване да се вдигнат нагоре, вместо да деформират лентата и предизвикат счупване. На входа на щанцата, лентата се подава през предварителен преден лентоводач (поз.12), а на изхода е предвиден фиксатор (поз.60), който влиза в пробитите за ловител отвори в отпадъка и позволява ръчно центроване в случаи, когато не може да се използва упора (поз.27) – края на лентата. Воденето с нулева хлабина или минимална стегнатост на подвижния спрямо неподвижния пакет се извършва с триене при търкаляне посредством водещи колонки (поз.8), втулки (поз.10, поз.14) и сачмени сепаратори (поз.9, поз.13).
2.2. С последователно действие (трансферни) зa многопозиционно изтегляне.
– Десет позиционна щанца за отрязване, изтегляне на седем прехода, калиброване на лагерно легло, обрязване и пробиване на детайл КРАК ЗА ЕЛЕКТРОМОТОР - Фиг.6-21
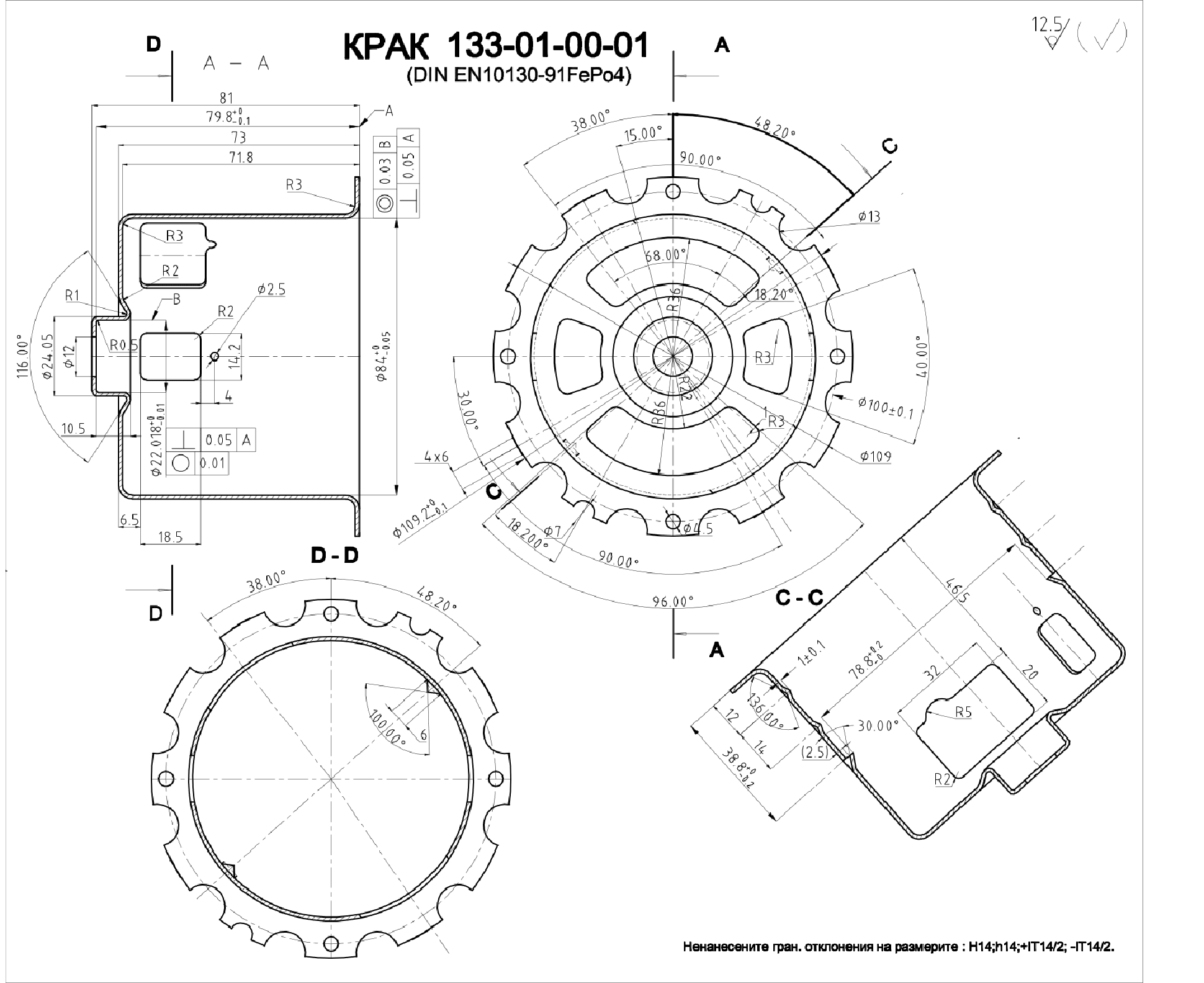
Фиг.6-21
е показана на Фиг.6-22 (сборен чертеж и спецификация) и Фиг.4-3 (технологична схема на процеса).
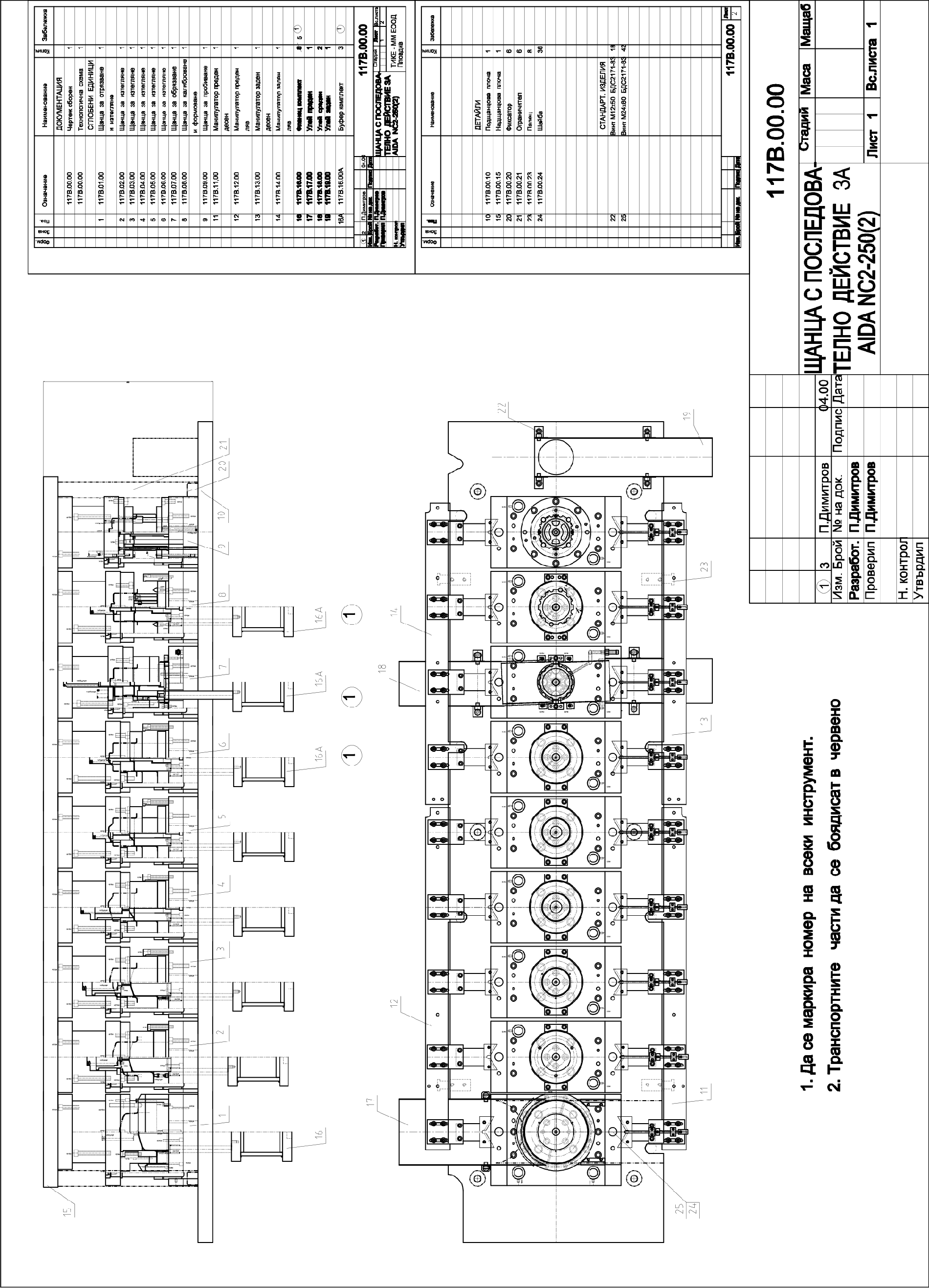
Фиг.6-22
Предназначена е за работа на 250 тонна многопозиционна преса AIDA-250 с подаващо устройство за лентата и три координатно подаващо устройство между позициите. Щанцата се състои от монтирани към подщанцова (поз.10) и надщанцова (поз.15) плочи отделни щанци – една щанца за отрязване заготовка и първо изтегляне (поз.1), пет щанци за следващо изтегляне (поз.2, поз.3, поз.4, поз.5, поз.6), една щанца за обрязване на фланеца (поз.7), една щанца за калиброване на лагерно гнездо и формоване на контролирана вдлъбнатина във фланеца (поз.8), една щанца за пробиване на профилни отвори в дъното и кръгли във фланеца (поз.9), с празна позиция в края. Останалите операции по пробиване на странични отвори в стените на детайла се изпълняват на отделни инструменти. Щанците са комплектовани с 5 пневматични буфера от пресата и 3 допълнително изработени пружинни буфера (поз.16А). Лентата се подава напречно на щанцата, а между отделните инструменти, заготовките се подават надлъжно със стъпка 230 mm чрез захващащи манипулатори (поз.11, поз.12, поз.13, поз.14), като те повдигат или спускат вертикално заготовката 40 mm. Това е допустимата височина за преодоляване на препятствия (фиксатори, упори, матрици повдигачи, вложки). Всеки инструмент е снабден с водещи колонки, закрепени в горната част, и втулки закрепени в долната част, за центроване на подвижните и неподвижни пакети. Дължината на колонките е по-малка и съобразена с хода на пресата (около 200 mm) така, че близо до горна мъртва точка на хода се гарантира безпроблемно преминаване на захващащи манипулатори със заготовките под тях. Отпадаците от изрязване на лентата, обрязване на фланец, пробиване на профилни отвори и готовия детайл (на 10 празна позиция) се отделят напречно на щанцата по улеи (поз.17, поз.18, поз.19). Дължината на щанцата е над 2500 mm с тегло около 4 тона. По тази причина, инструментите са проектирани да могат да се разглобяват на части, без да е необходимо снемане на цялата щанца от пресата. Работната производителност е между 15 и 22 детайла в минута.
2.3. Със съвместно действие (еднотипни операции) за пробиване и изрязване, за огъване в противоположни посоки; (разнородни операции) за изтегляне, отбортоване, формоване и разрязване.
– Щанца за изрязване и пробиване на плоска заготовка за детайл ПРЕДПАЗИТЕЛ ЗА ЪГЛОШЛАФ на Фиг.6-23
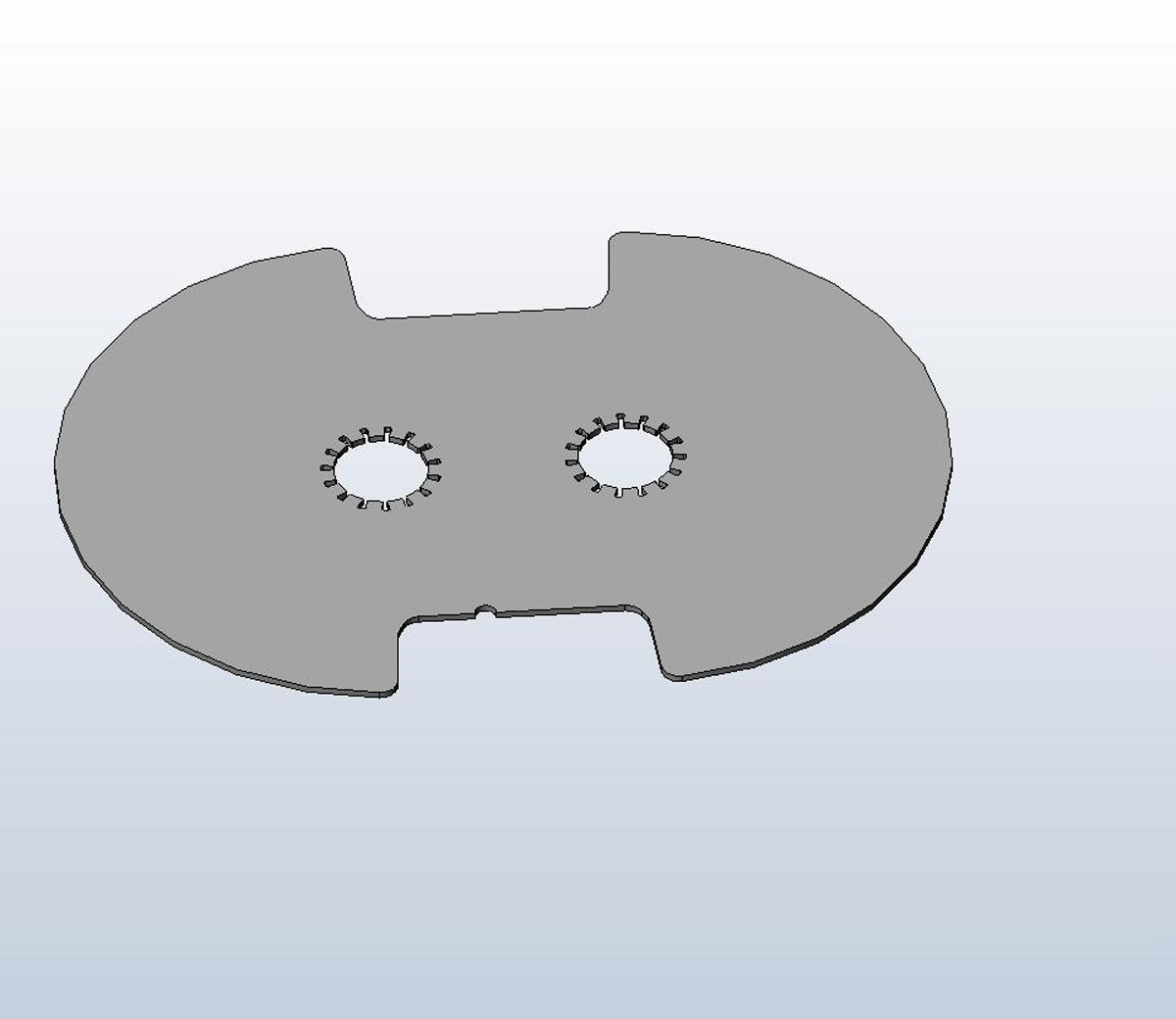
Фиг.6-23
е показана на Фиг.6-24 (общ вид),
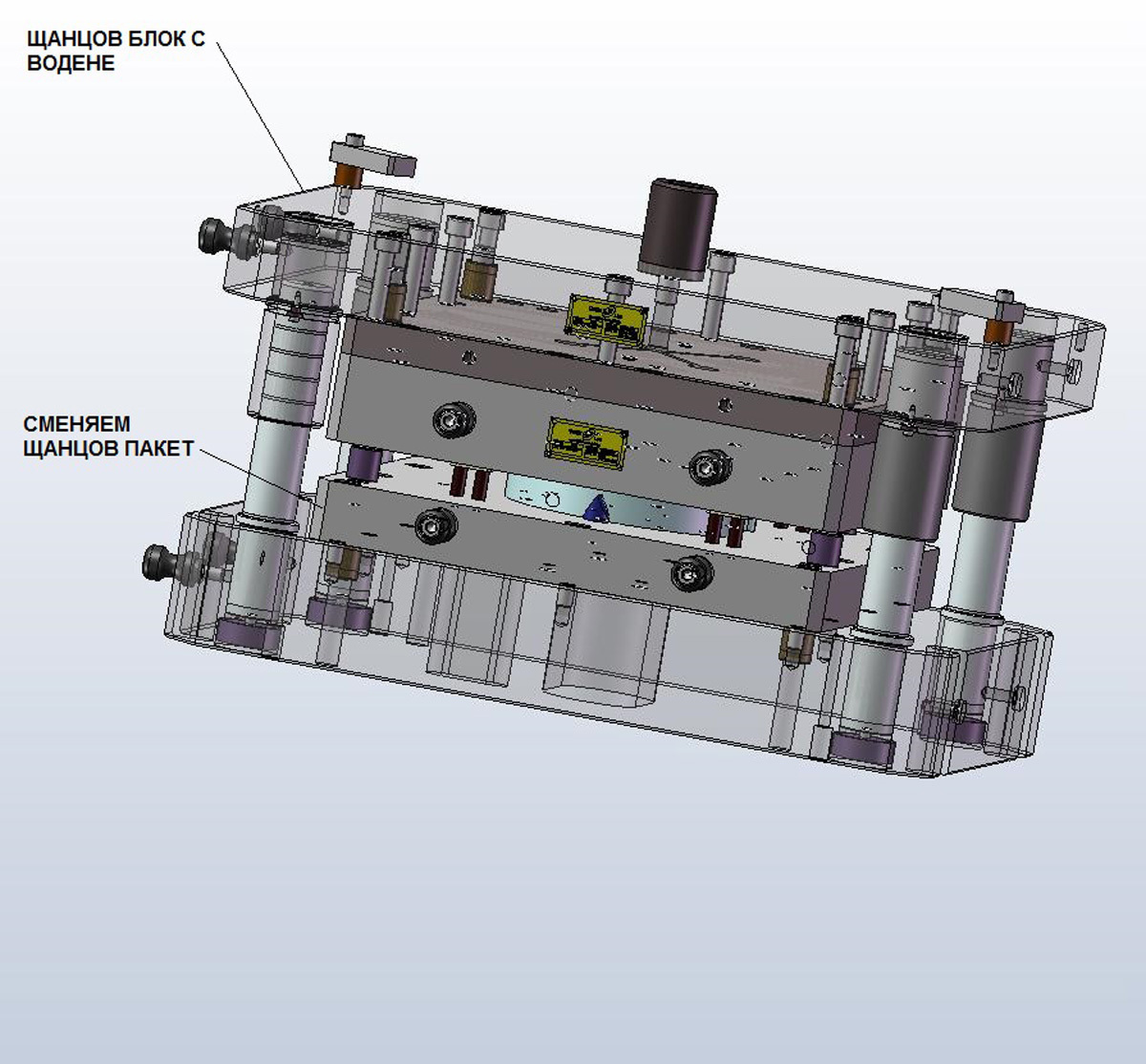
Фиг.6-24
на Фиг.6-25(сменяем пакет – общ вид)
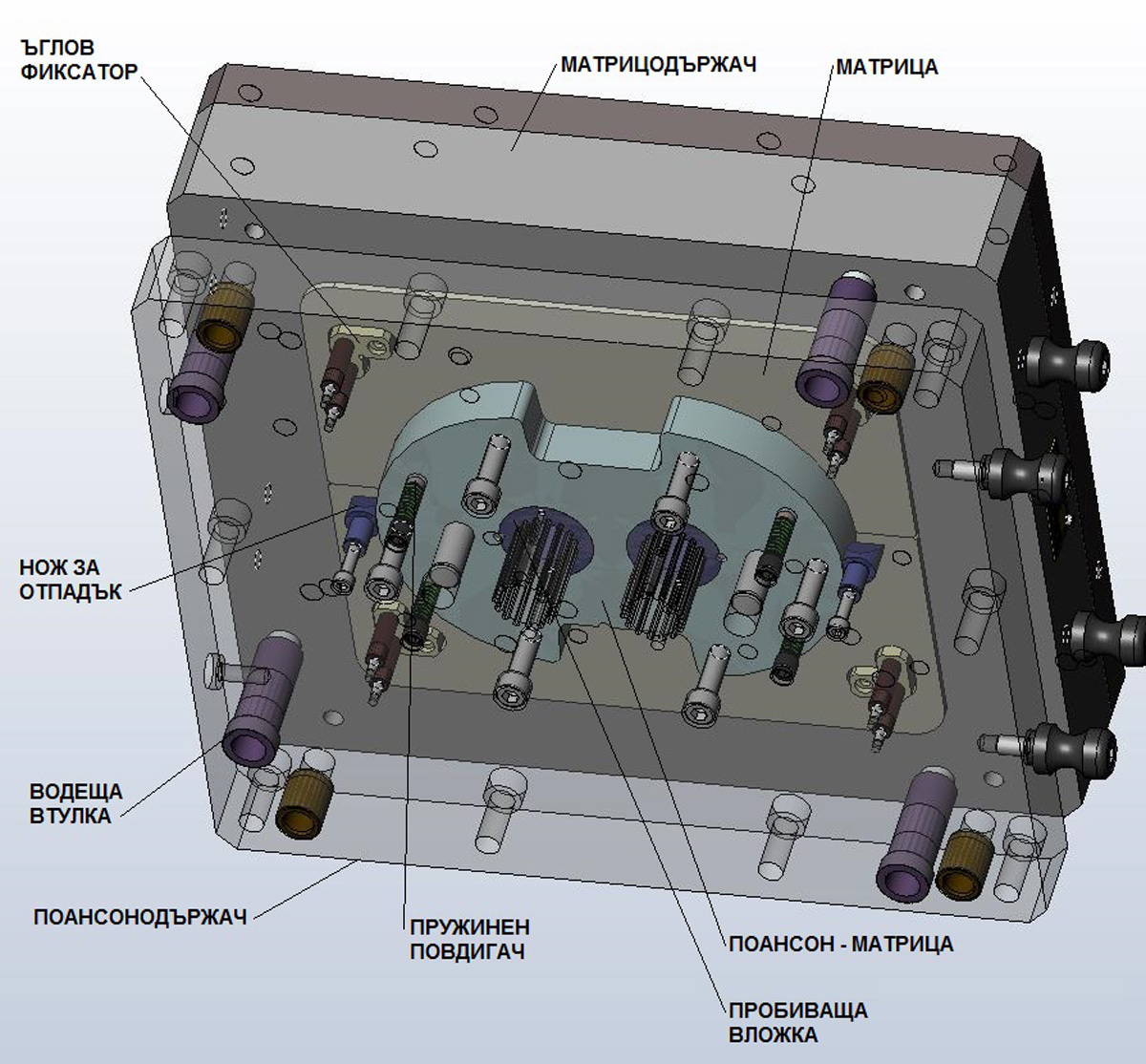
Фиг.6-25
и Фиг.6-26 (сменяем пакет-надлъжен разрез).
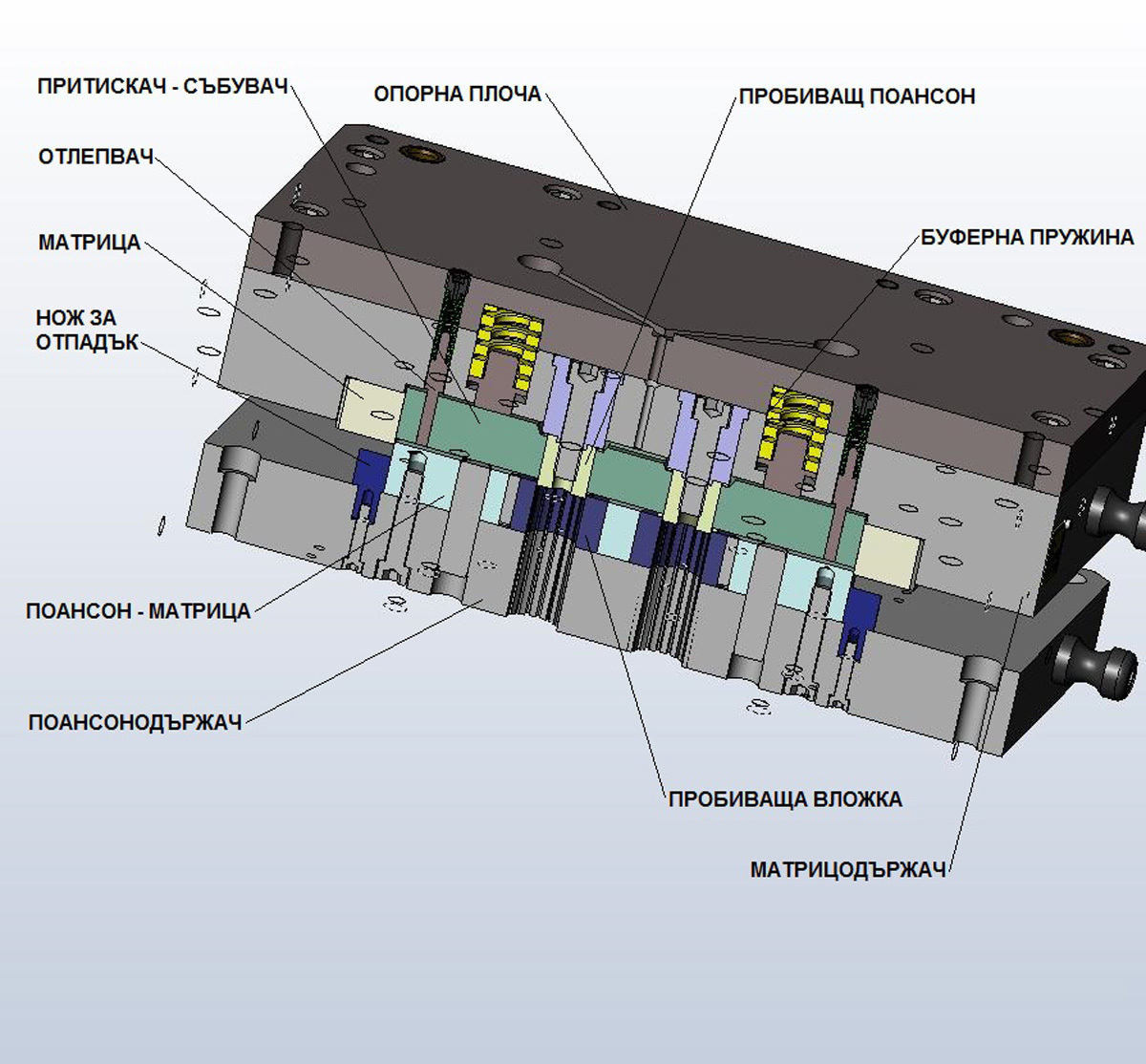
Фиг.6-26
Предназначена е за 100 тонна ексцентър преса. Конструкцията е съставена от щанцов блок с водене и сменяем пакет за производство на различни размери на детайл ПРЕДПАЗИТЕЛ ЗА ЪГЛОШЛАФ. Активните части от сменяемия пакет включват матрица и пробиващи поансони, закрепени в матрицодържач към подвижния пакет, поансон – матрица с пробиващи вложки, закрепена към поансонодържач на неподвижния пакет. Формата на профилните отвори и дебелината на материала са наложили съставно изпълнение на пробиващия поансон и вложка в поансон-матрицата. Това решение позволява, при откъртване на част от режещия ръб, да се смени само повредения поансон или вложка. Събуването на пробиващите поансони, избутването на заготовката от матрицата и нейното притискане при рязане се извършва от притискач под действието на буферни пружини. Центроването на правогълната изходна заготовка е по ъглови фиксатори. Повдигачите в поансон-матрицата и отлепвачите в притискача улесняват ръчното поставяне и изваждане на заготовката. За отделяне на отпадъците от изрязване на външния контур, се използват 2 ножа за отпадък, чиито остри ръбове разкъсват последователно слоевете отпадачен материал извън поансон-матрицата, след което те безпроблемно се изваждат настрани и изхвърлят. В сменяемия пакет са включени допълнително водещи втулки и колонки, които излизат от водене при отворена щанца за да гарантират поставянето и изваждането на заготовката, но в момента на рязане позволяват точно центроване на поансоните спрямо матрицата.
– Щанца за огъване на детайл ВИЛКА - Фиг.6-27
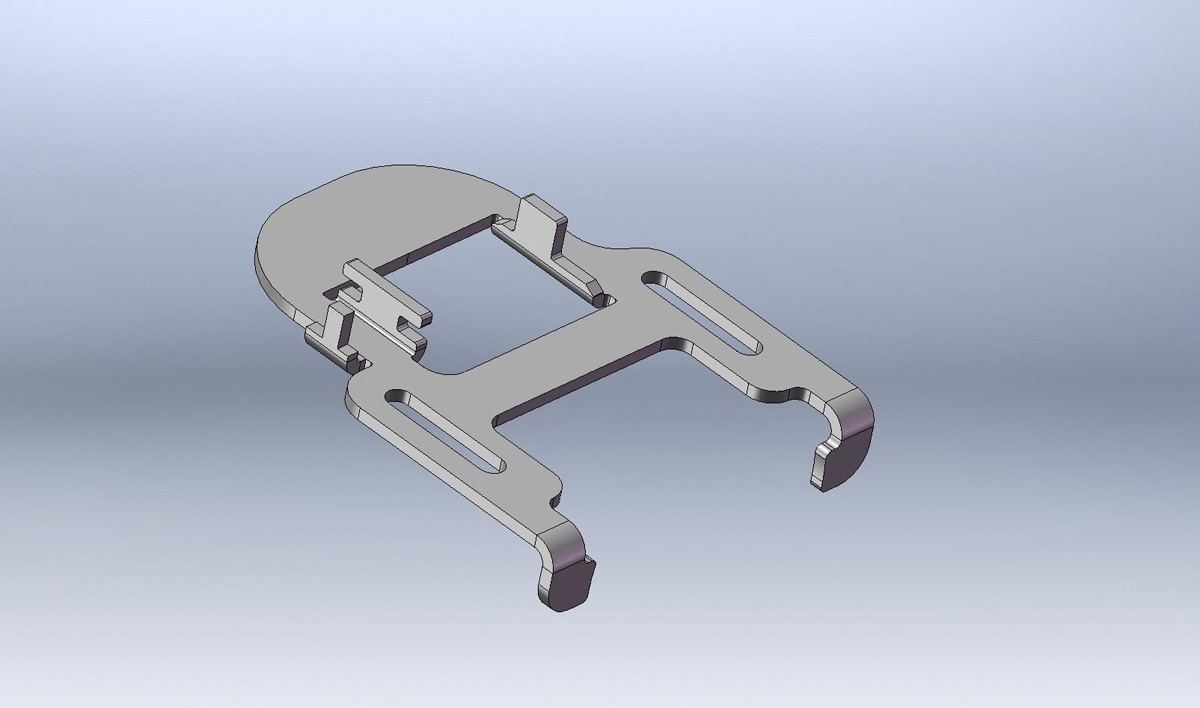
Фиг.6-27
е показана на Фиг.6-28 (сборен чертеж) и Фиг.6-29 (спецификация).
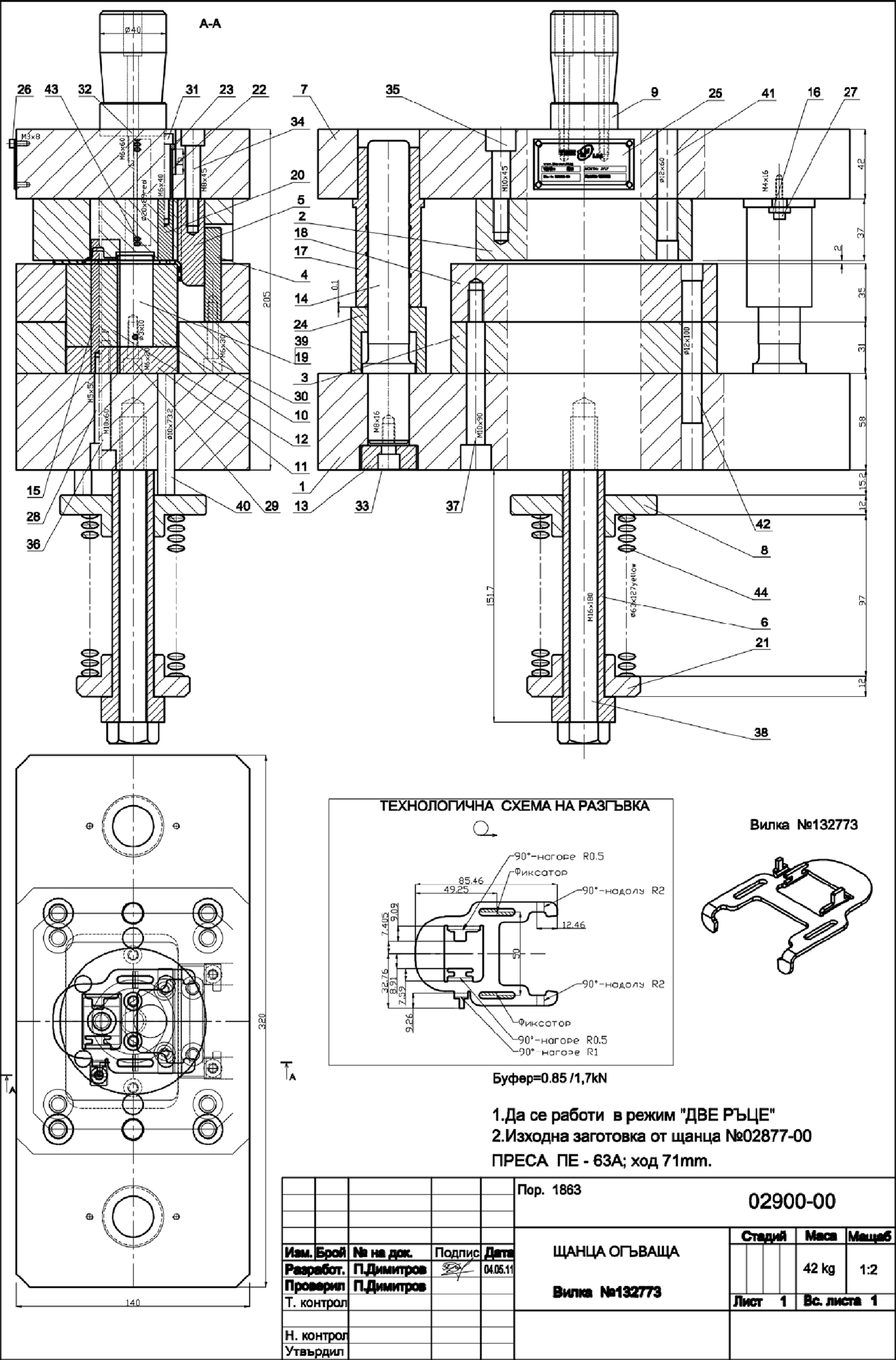
Фиг.6-28
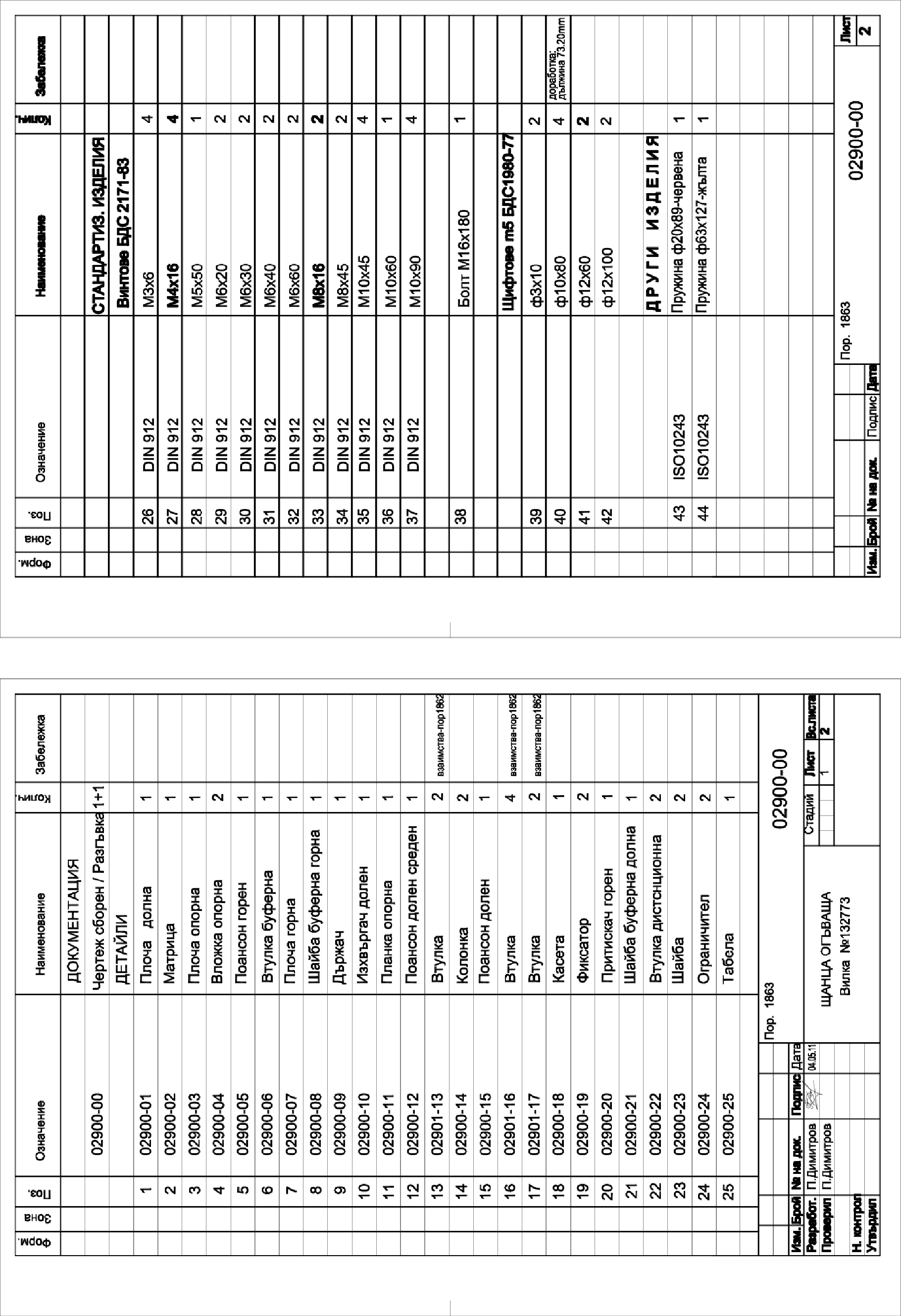
Фиг.6-29
Заготовка се огъва в две противоположни посоки за един работен ход – първоначално краищата на вилката на долу, след което езичетата в отвора и отстрани, на горе. Щанцата е с огъваща матрица (поз.2), горен и долни огъващи поансони (поз.5, поз.12, поз.15), с долен изхвъргач (поз.10) за притискане и събуване на заготовката под въздействие на буферна пружина (поз.44) чрез щифтовете (поз.40) и горен притискач (поз.20) с пружина (поз.43). Разликата в коравината на пружините (поз.43, поз.44) позволява притискане на заготовката и огъване на долу с поансона (поз.5) спрямо ръба на долния изхвъргач (поз.10) при незначително потъване на последния до момента на контакт на матрицата (поз.2) със заготовката, след което започва свиване на буферната пружина и огъването на горе с долните огъващи поансони (поз.12, поз.15). За центроване на заготовката се използват овални фиксатори (поз.19). Подвижната и неподвижмата част на блока се направляват с колонка (поз.14) и втулка (поз.17) с триене при плъзгане, като минималната височина на щанцата е зададена от ограничителна втулка (поз.24).
– Щанца за изтегляне, формоване, отбортоване и разрязване на детайл ПРЕДПАЗИТЕЛ ЗА ЪГЛОШЛАФ от Фиг.3-7 е показана на Фиг.6-30 (общ вид),
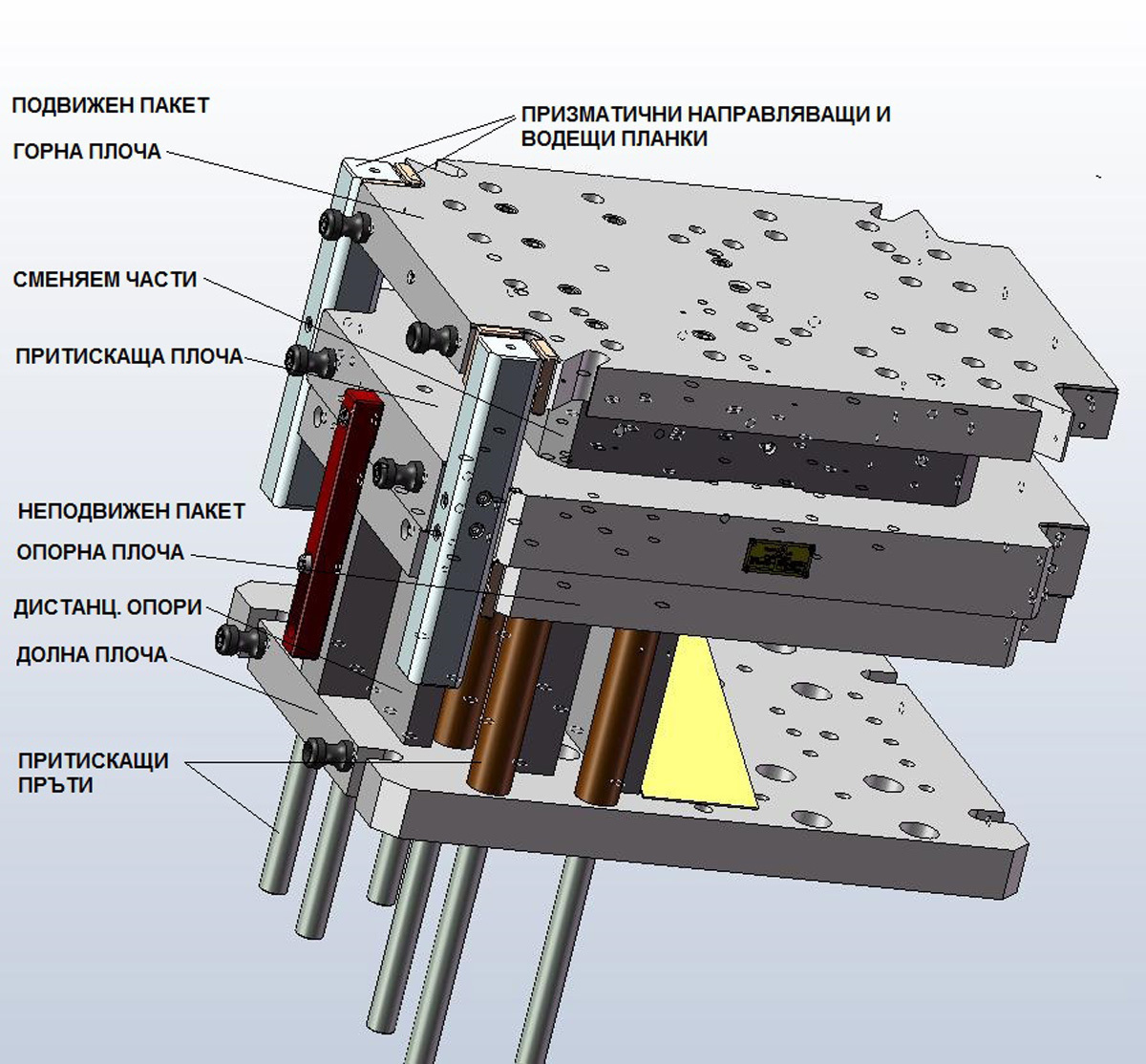
Фиг.6-30
на Фиг.6-31 (сменяеми части на подвижен пакет),
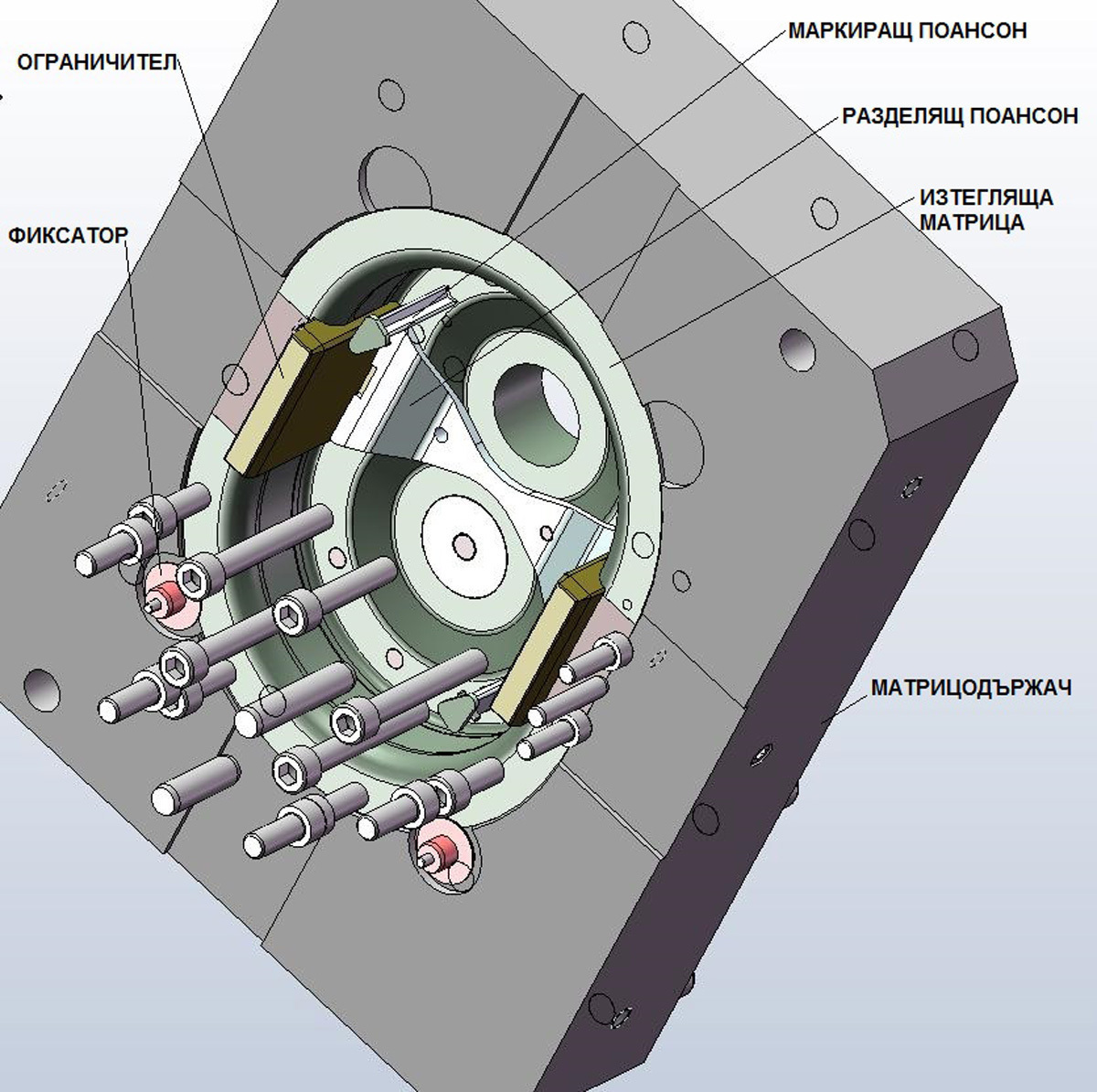
Фиг.6-31
на Фиг.6-32 (сменяеми части на неподвижен пакет с притискач),
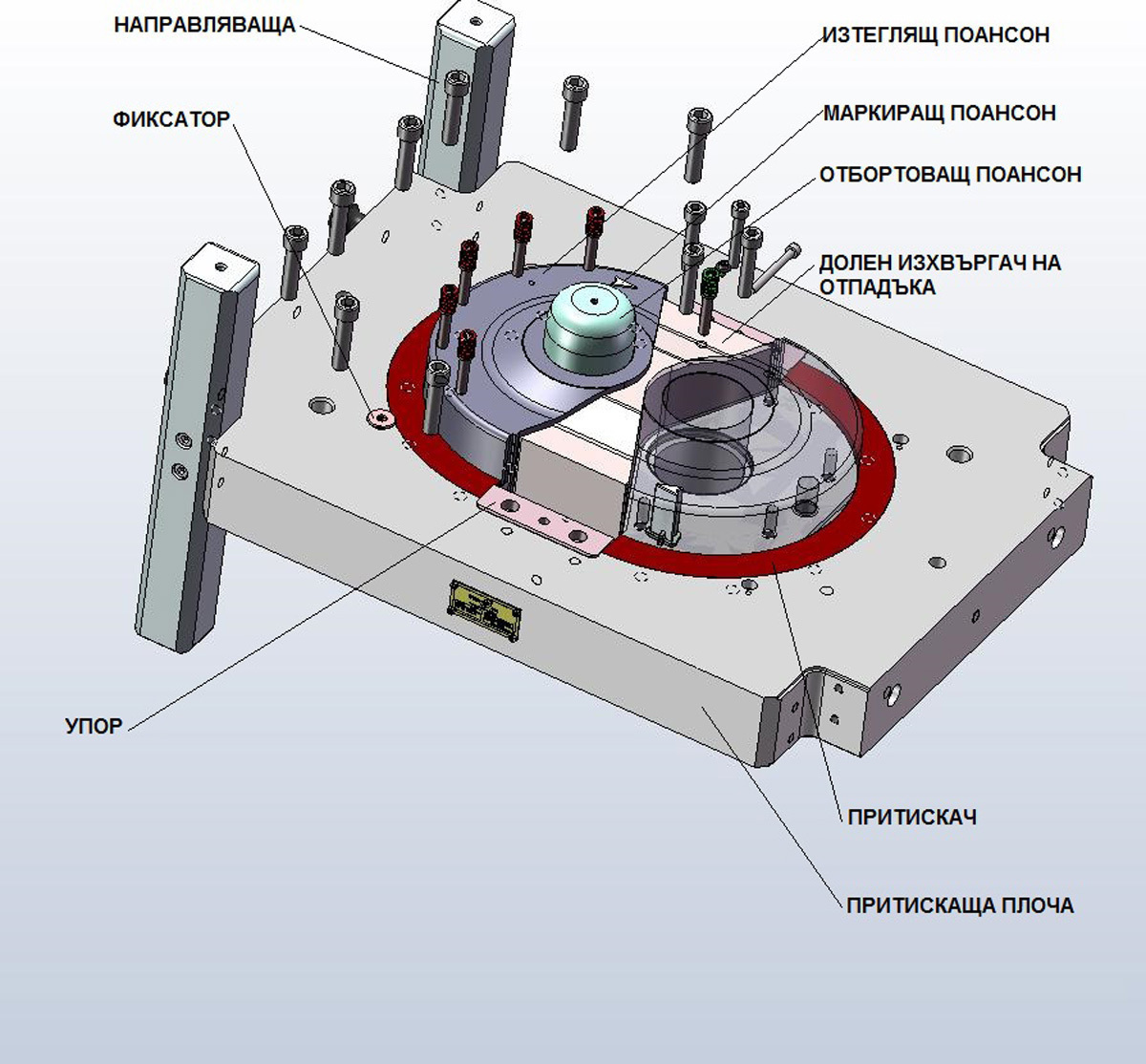
Фиг.6-32
и на Фиг.6-33 (надлъжен разрез на сменяеми части от подвижен и неподвижен пакет с притискач).
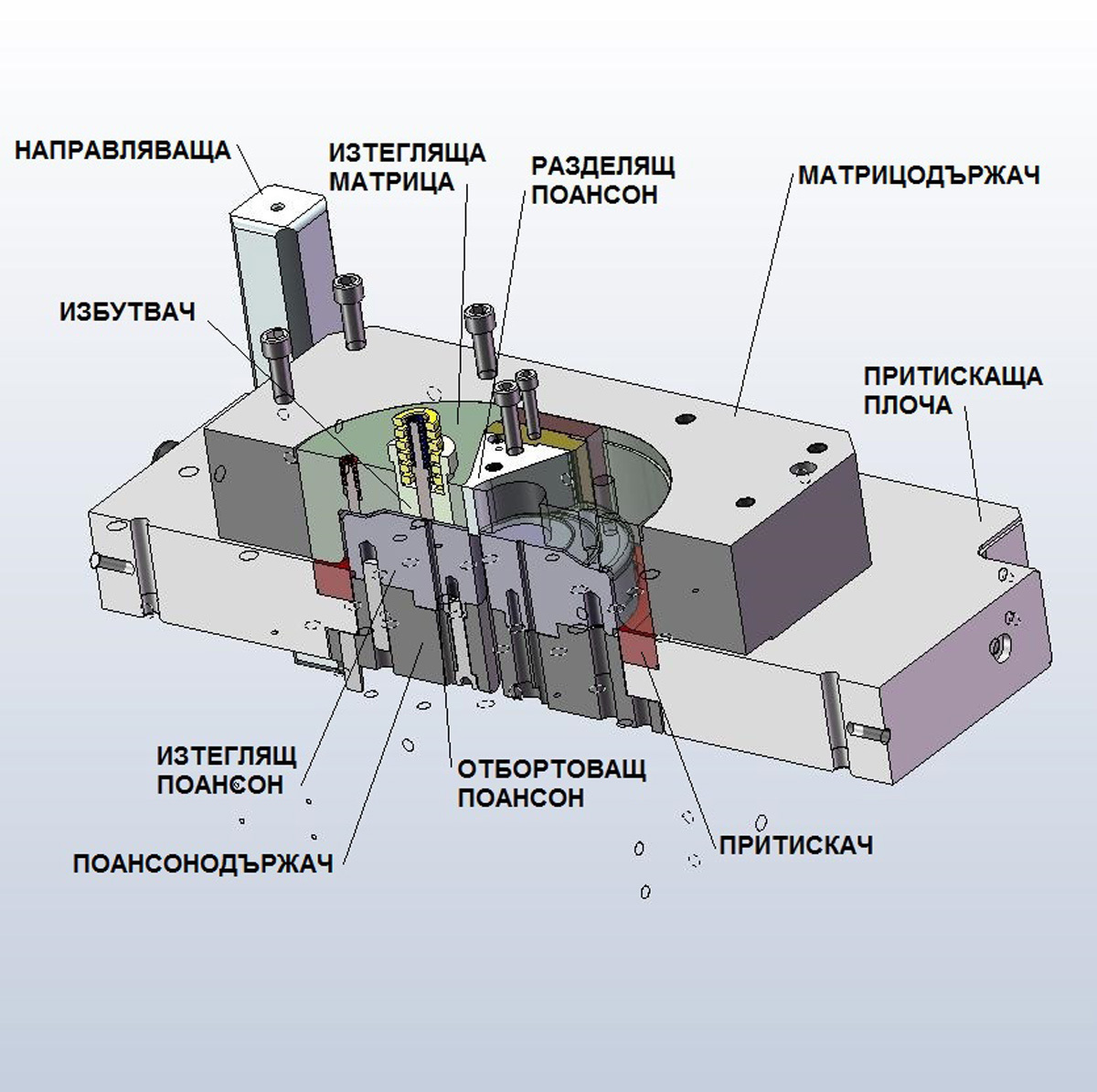
Фиг.6-33
Предназначена е за 250 тонна тройно действаща хидравлична преса с долен хидравличен буфер – за притискане и повдигане на готовия детайл и независимо долно хидрозадвижване на отбортоващи поансони. Щанцата се състои от постояни плочи – горна, притискаща, опорна с дистанционни опори между тях и сменяеми активни части за производство на различни размери на детайл ПРЕДПАЗИТЕЛ ЗА ЪГЛОШЛАФ. Активните части на щанцата включват 2 изтеглящи матрици и разделящ режещ поансон, закрепени в матрицодържач от подвижния пакет, 2 изтеглящи поансона, закрепени към поансонодържач от неподвижния пакет и 2 притискача в притискаща плоча, който се води спрямо подвижния и неподвижния пакети. В изтеглящите поансони са разположени 2 отбортоващи поансона, които са свързани с независим хидроцилиндър за движение нагоре и надолу. Там са разположени и маркиращите поансони. За ръчно позициониране на изходната заготовка от Фиг.6-23 спрямо матрицата и притискача се използват фиксатори, базиращи по външния контур. Притискащата плоча предава технологичното натоварване от притискачите на хидравличния буфер на пресата чрез набор от притискащи пръти. Технологичният процес започва с изтегляне на заготовката и нейното притискане при движението надолу на подвижния пакет, като малко преди долна мъртва точка се извършва разрязване на заготовката на два детайла и технологичен отпадък между тях. В края на хода се формова стрелка с маркиращите поансони. Притиснатата между изтеглящи матрица и поансон заготовка, се задържа в долно положение до изпълнението на работен ход нагоре и неговото връщане надолу от отбортоващите поансони, след което двата готови детайла се изхвърлят от матрицата и поансона, а средния отпадък се повдига от долен изхвъргач. Готовите детайли и отпадъка се отстраняват ръчно от работната зона преди поставяне на нова заготовка. Воденето на притискащата плоча с притискачите спрямо подвижния и неподвижния пакет е с призматични направляващи и бронзови пластини, разположени в ъглите. По този начин е възможно поемане на големи странични сили и е гарантирано повече място и удобство за поставяне и снемане на заготовката. Закрепените към притискащата плоча направляващи позволяват лесен монтаж и демонтаж при необходимост, без сваляне на щанцата от пресата.
3. Щанци с механизми за преобразуване на движението на пресата.
Щанците с вградени в тях допълнитени преобразуващи механизми се използват за детайли, чиято форма изисква движение на матрици или поансони в различна посока от тази на пресата. Типичен пример са изтеглени детайли с отвори, ребра, огънати участъци в страничните стени. Такива механизми понякога са необходими също за изваждане на детайли, които след края на операцията остават в поансона или матрицата. Прилагат се при голям годишен обем от детайли – едро серийно производство (примерно от 100000 до 1000000 за малки детайли, от 20000 до 200000 за голямогабаритни детайли). Възможно е ефективното им използване при сложни детайли и за по-малък годишен обем.
3.1. Едно операционни щанци с клинови преобразуващи механизми.
– Щанца за формоване на радиални зъби на детайл ПРЕДПАЗИТЕЛ ЗА ЪГЛОШЛАФ от Фиг.6-7 е показана на Фиг.6-34 (общ вид),
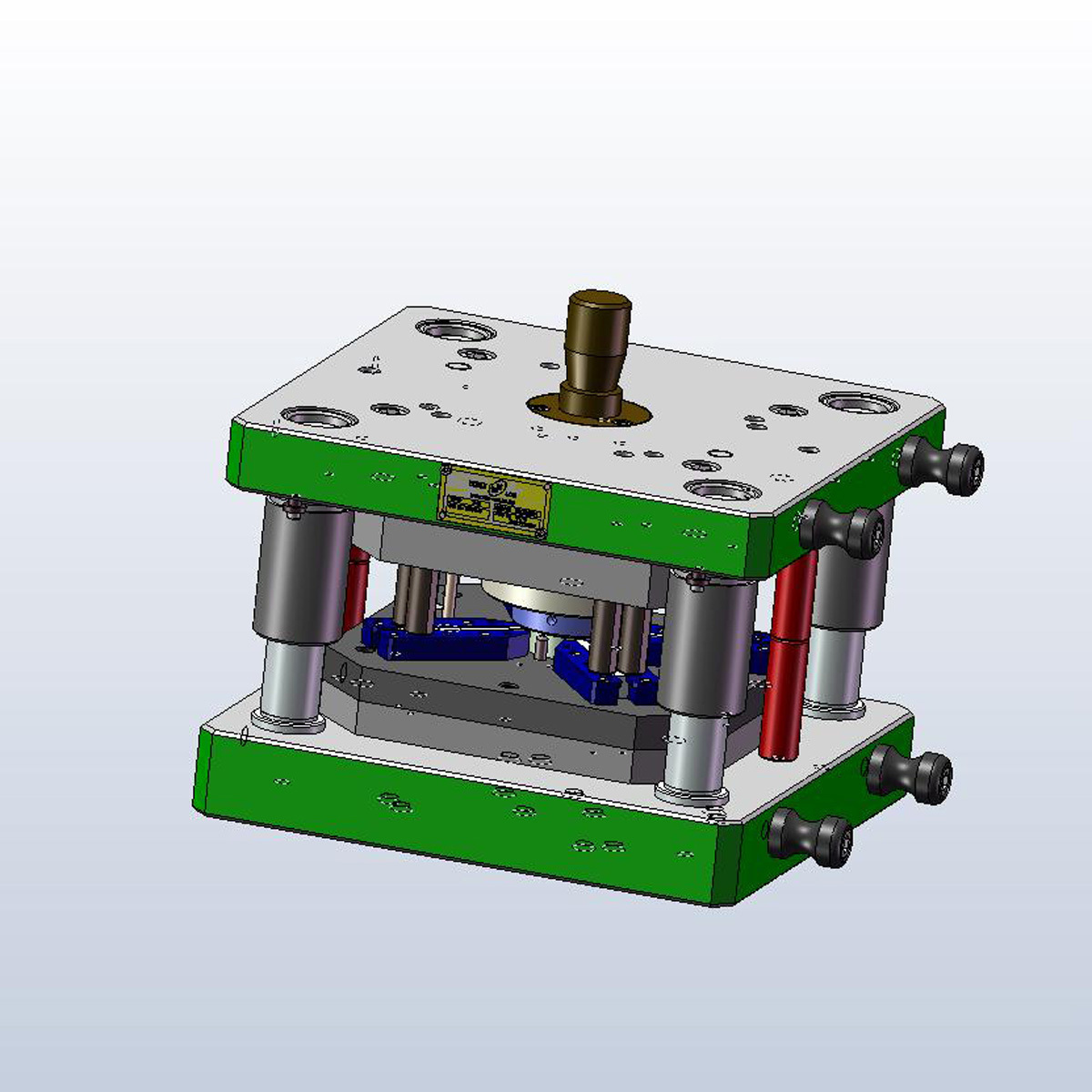
Фиг.6-34
на Фиг.6-35 и Фиг.6-36 (напречен и диагонален разрез)
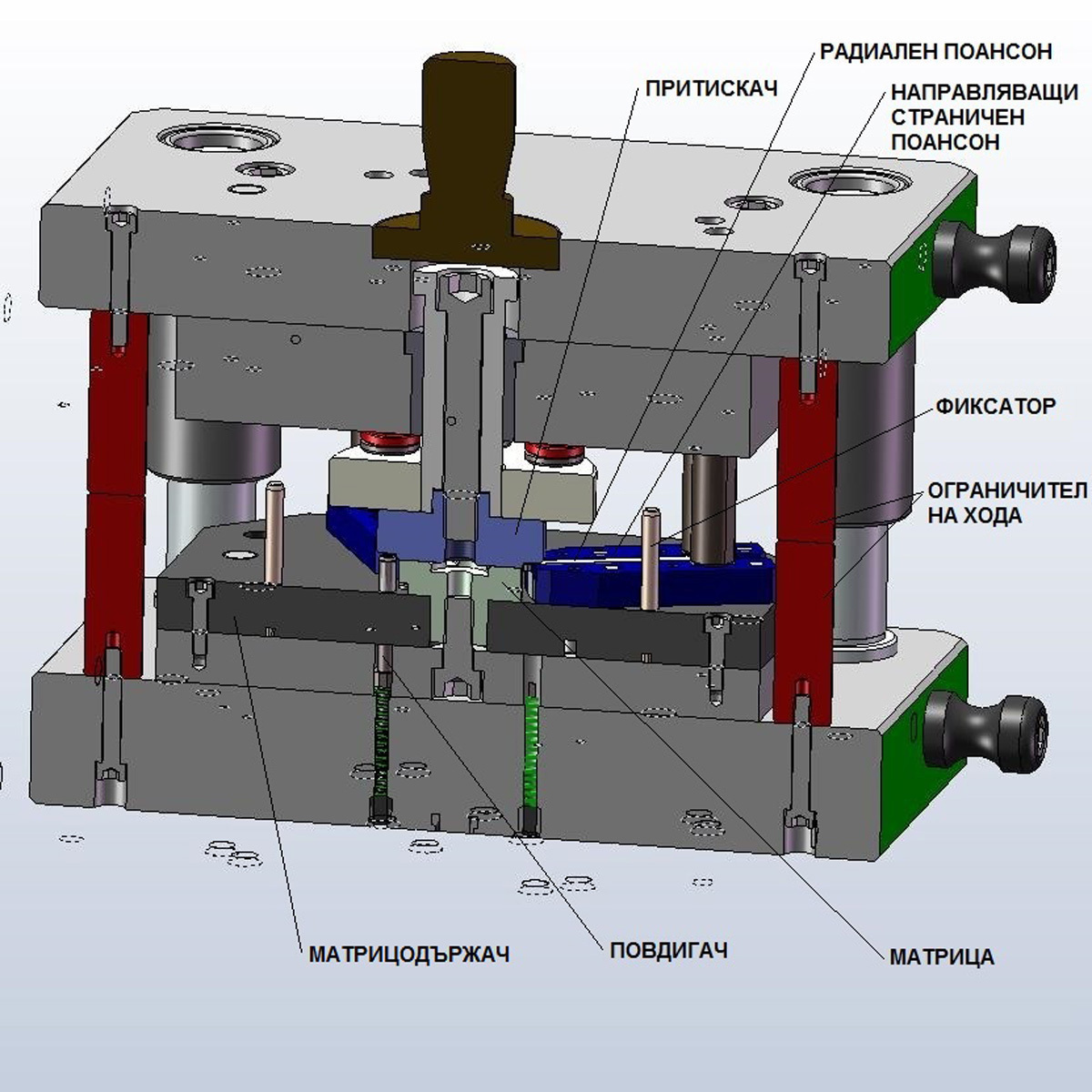
Фиг.6-35
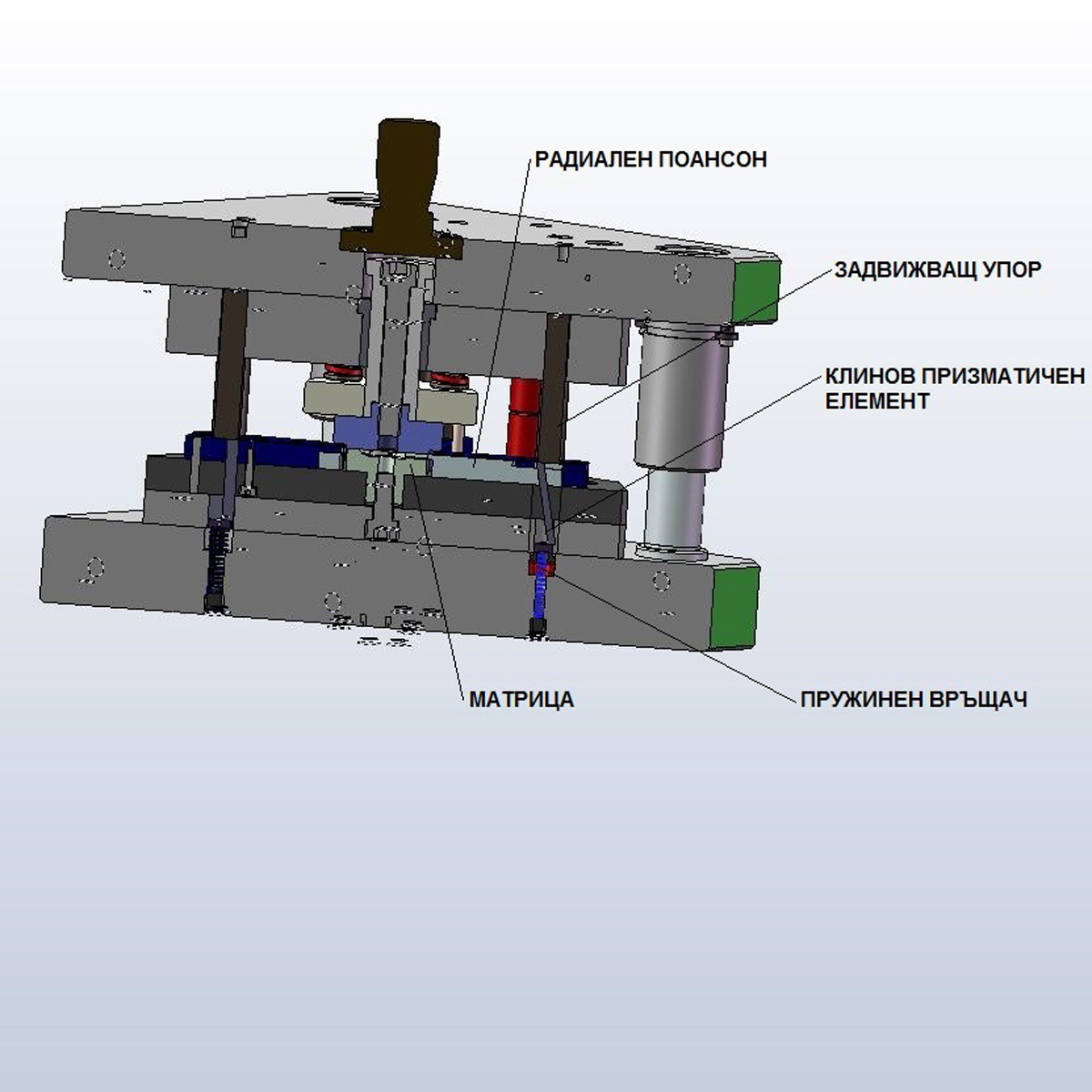
Фиг.6-36
и Фиг.6-37 (специален буфер с подщанцова плоча).
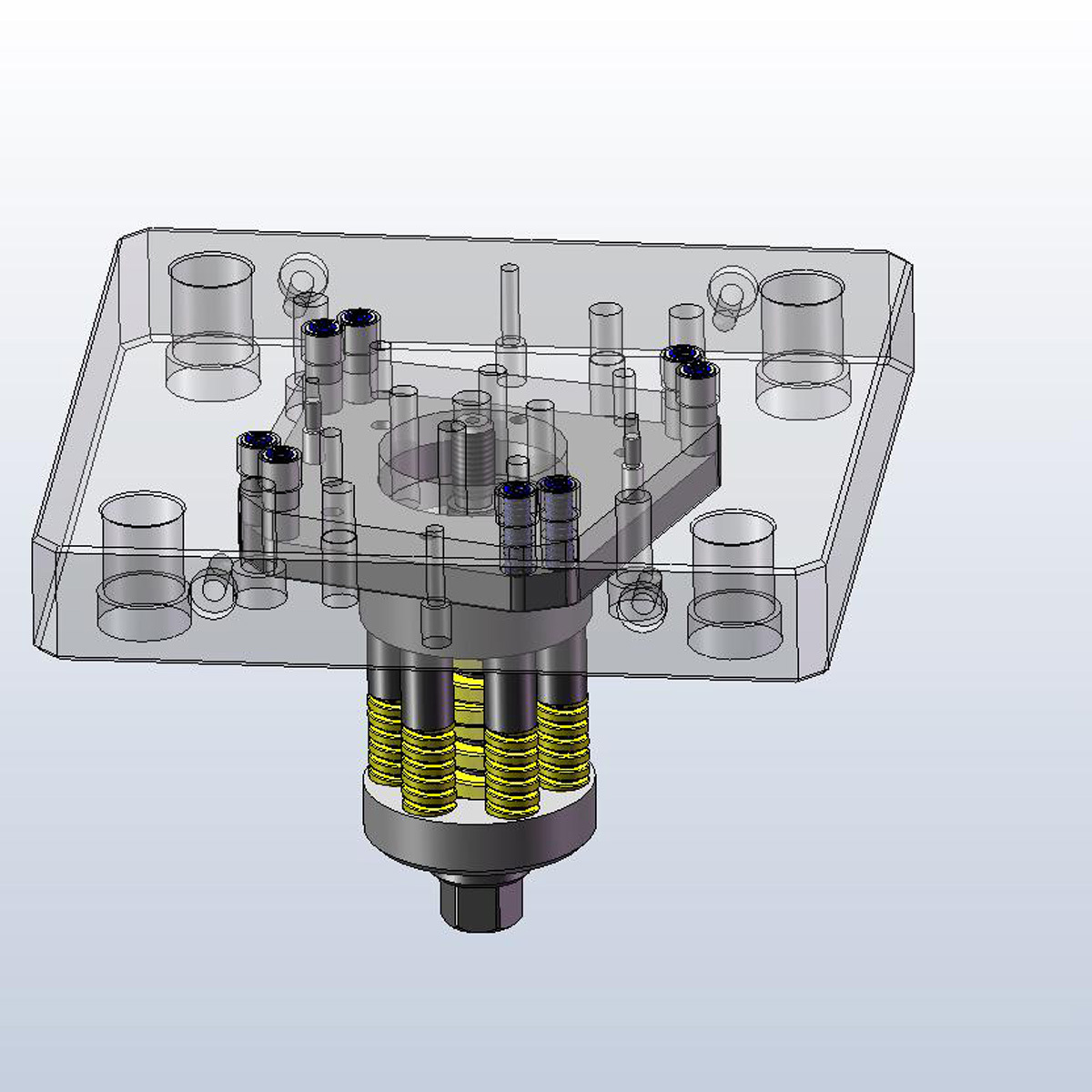
Фиг.6-37
Предназначена е за 25 тонна ексцентър преса. Щанцата се състои от матрица и радиални поансони с направляващи, закрепени на матрицодържач към неподвижния пакет. В задната част на всеки радиален поансон в правоъгълен отвор на матрицодържача са водят по 2 призматични клинови елемента, чиито изпъкнали наклонени профили са разположени в съответните наклонени канали на радиалния поансон. Така вертикалното движение на призматичните клинови елементи в матрицодържача, се преобразува в радиално (перпрендикулярно спрямо посоката на хода на пресата) за поансоните. Заготовката се притиска към матрицата от притискач, който изпълнява и ролята на горен затварящ ръб за матрицата. Задвижването на призматичните клинови елементи на долу и радиалните поансони навътре се извършва чрез задвижващи упори, закрепени към горната плоча на подвижния пакет, при хода на долу. Изваждането на радиалните поансони се осъществява чрез повдигане на призматичните клинови елементи от буфера, посредством пружинен повдигач при обратния ход на пресата. Заготовката се центрова по фиксатори и е изважда ръчно след края на работния ход. Подвижната и неподвижмата част на блока се направляват с колонки и втулки с триене при плъзгане.
– Щанца със съвместно действие за странично формоване, пробиване и огъване на вътрешен зъб от детайл КРАК ЗА ЕЛЕКТРОМОТОР (разрез С-С от схемата на сборния чертеж) е показана на Фиг.6-38 (сборен чертеж) и Фиг.6-39 (спецификация).
Предназначена е за работа на ексцентър преса с голям ход (150 mm) с ръчно залагане и изваждане на готовия детайл. Заготовка не само трябва да се пробие, формова и огъне странично в две противоположни радиални посоки за един работен ход, но трябва и да се извади от матрицата, на което пречи огънатия на вътре зъб. По тази причина са използвани два различни клинови механизми – първият преобразува движението на пресата в работен ход на поансоните, а втория позволява изваждане на готовия детайл от матрицата чрез повдигане и радиално преместване на съответните вложки. Щанцата включва двойка полуматрици (поз.22), центровани с шпонка (поз.31), режещ поансон (поз.40) и режеща вложка (поз.44), разположени в подпружинен плаващ водач (поз.3). В наклонен „Т“ образен канал на полуматриците (поз.22) се води подвижна вложка (поз.45), а в правоъглни отвори на водача (поз.3) се водят плъзгачите (поз.32, поз.39), чиито изпъкнали наклонени профили контактуват с наклонен канал на режещия поансон (поз.40). Горните части на плъзгачите (поз.32, поз.39) са закрепена към опорна плоча (поз.8), спрямо която посредством колонки (поз.28) се води водача. След контакта на водача (поз.3) с упори (поз.23) при хода на пресата на долу, плъзгачите се преместват спрямо водача и предизвикват радиално движение на режещите поансони (поз.40) към центъра. Прибирането на последните при обратния ход на пресата нагоре се извършва под действие на пружините (поз.12) посредством щифтове (поз.35) и траверса (поз.10). При обратния ход на пресата подпружинените повдигачи (поз.24) повдигат заготовката, която увлича подвижните вложки (поз.45), принуждавайки ги чрез наклонения „Т“ образен канал на полуматриците и щифтовете (поз.47), да се повдигнат вертикално и да се изместят радиално към центъра, с което се освобождава готовия детал от огънатия зъб и формованите зони. Подвижния и неподвижния пакет на щанцата се водят с колонки (поз.28) и втулки (поз.33) с триене при плъзгане.
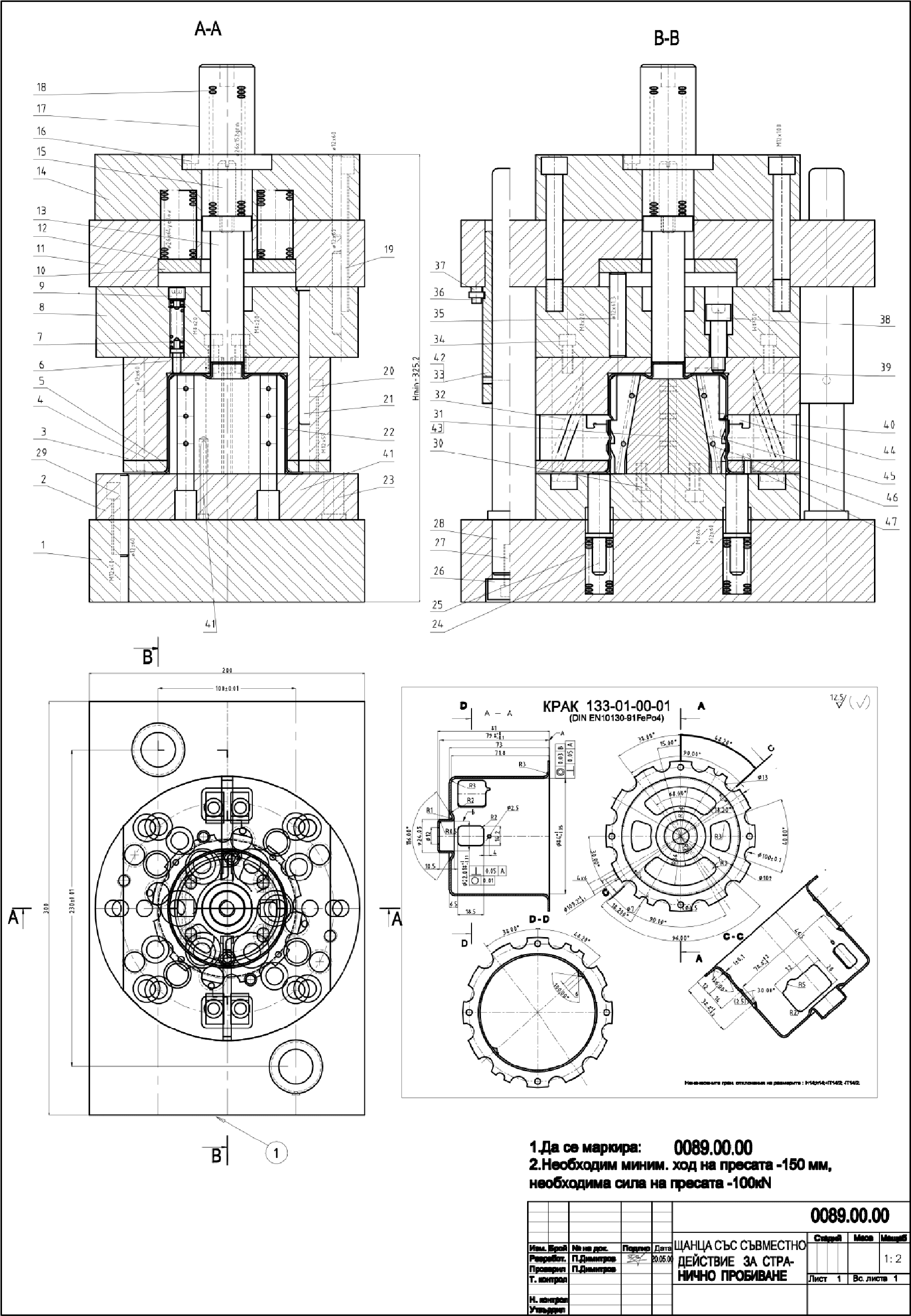
Фиг.6-38
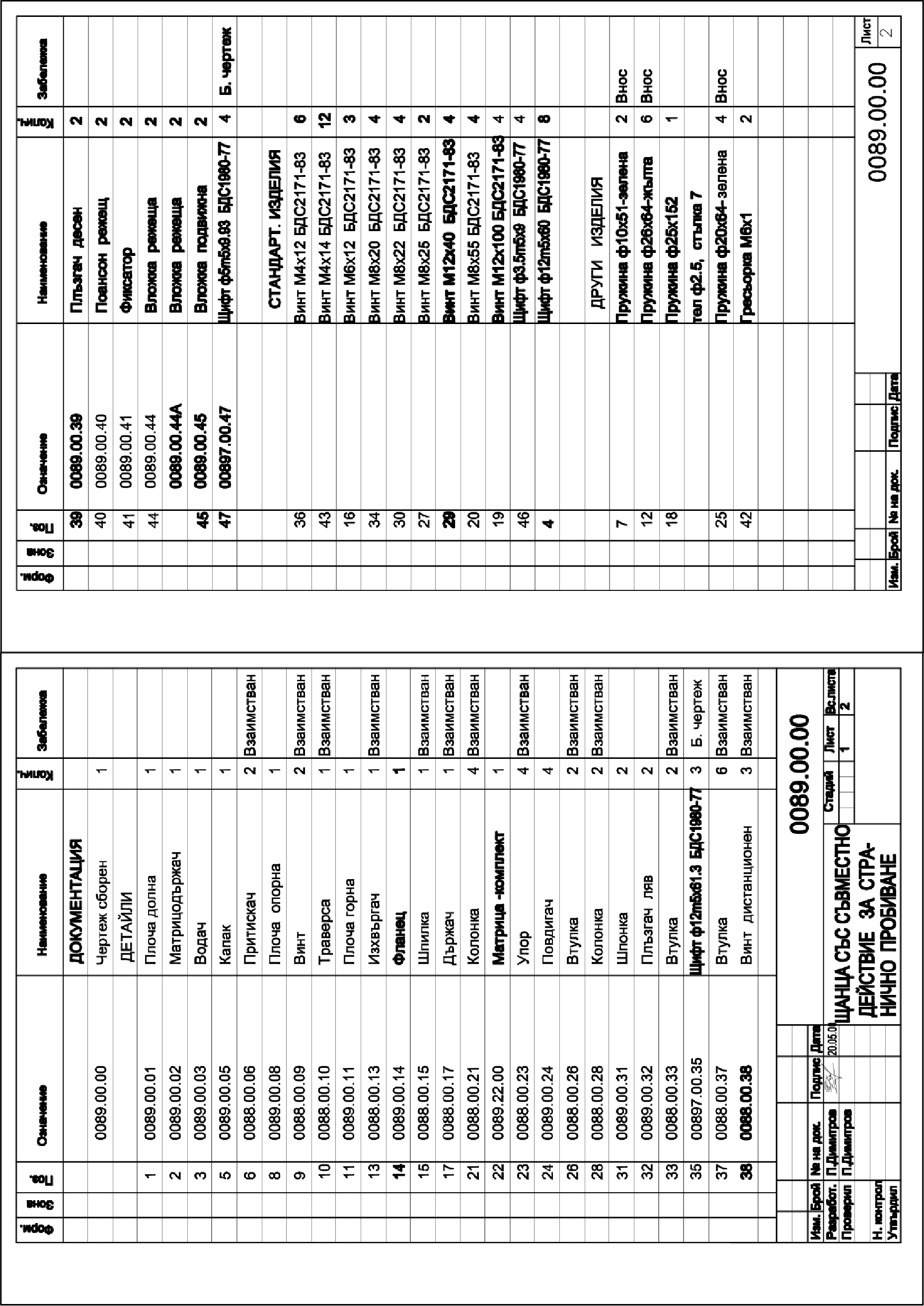
Фиг.6-39
3.2. Едно операционни щанци с гърбични преобразуващи механизми.
– Щанца за огъване на детайл “CONTACT“ - заготовка 2” от Фиг.6-40
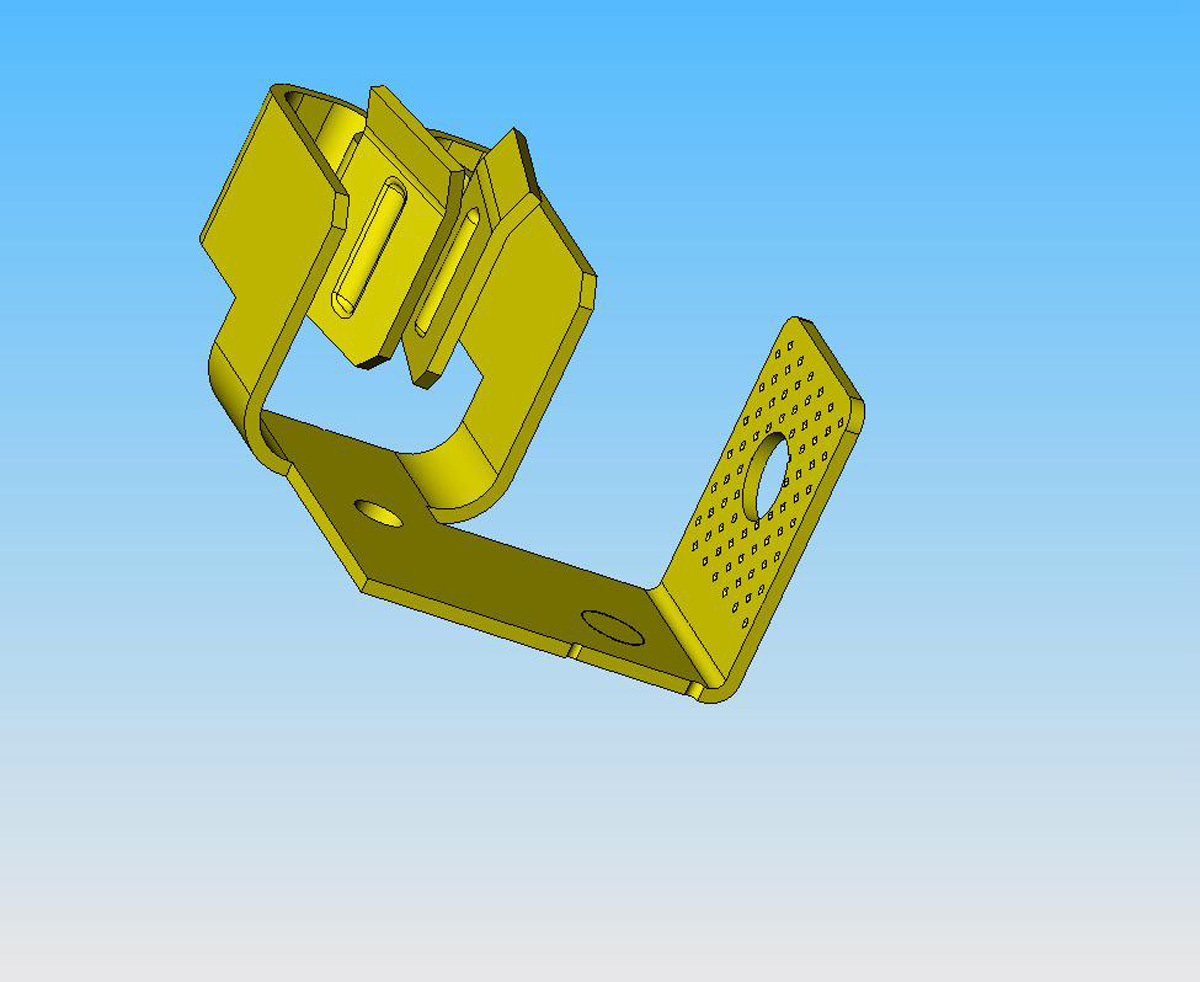
Фиг.6-40
е показана на Фиг.6-41 (общ вид)
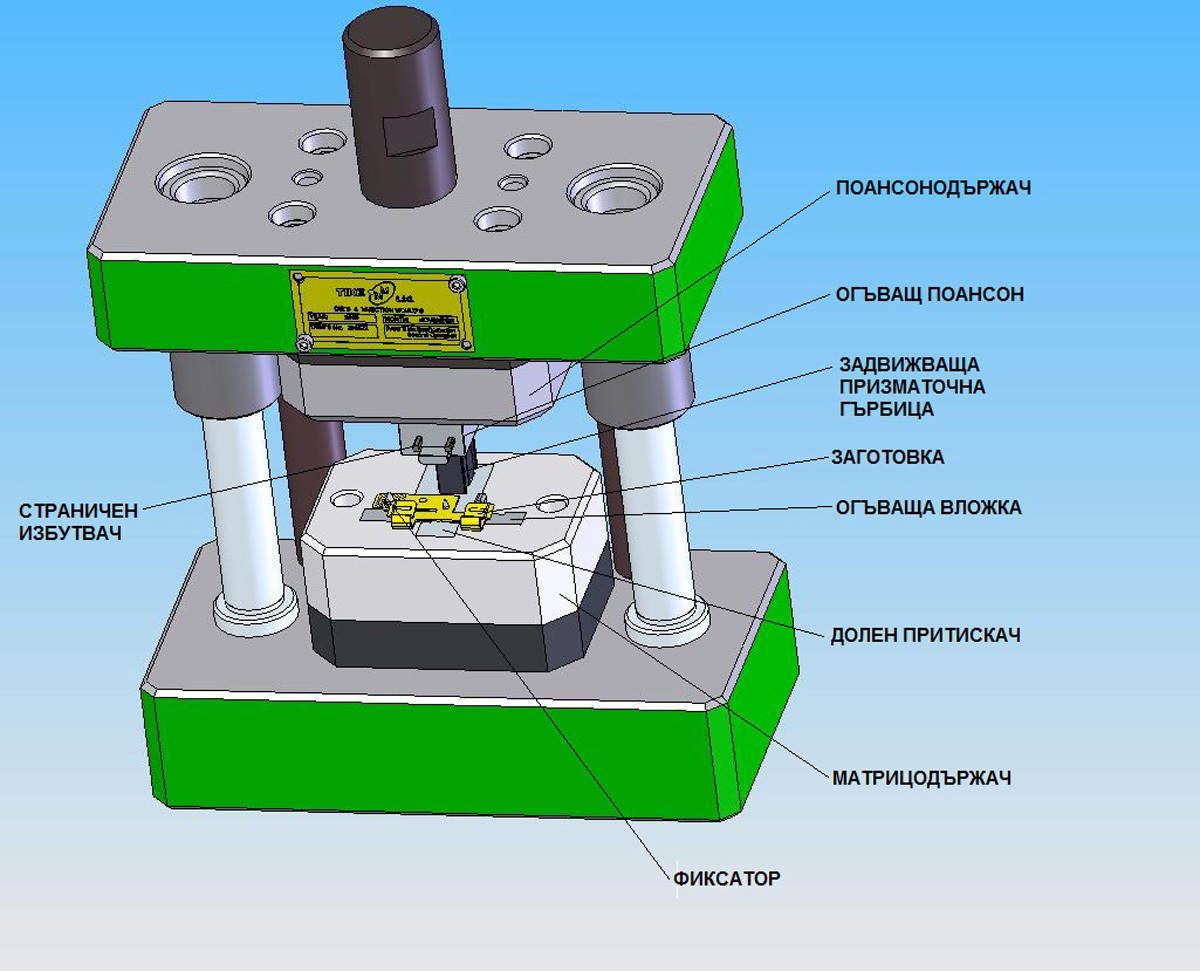
Фиг.6-41
и на Фиг.6-42 (гърбичен механизъм и странични избутвачи).
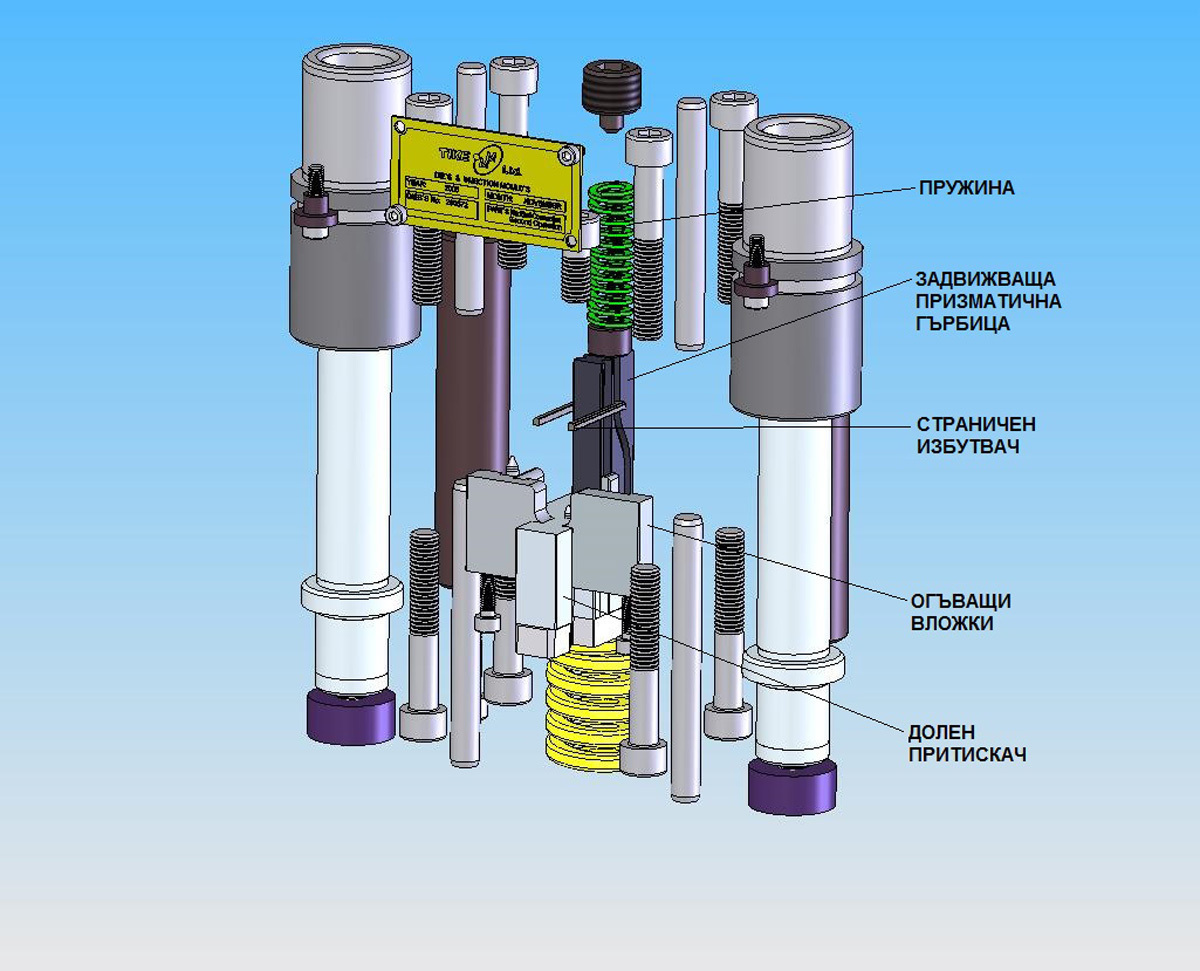
Фиг.6-42
Предназначена е за работа на 25 тонна ексцентър преса с ръчно поставяне на “CONTACT - заготовка 1” от Фиг.5-34. Малките размери и формата на заготовката след огъване, затрудняват изваждането от работната зона, защото детайла остава обхванал огъващия поансон - Фиг.6-43,
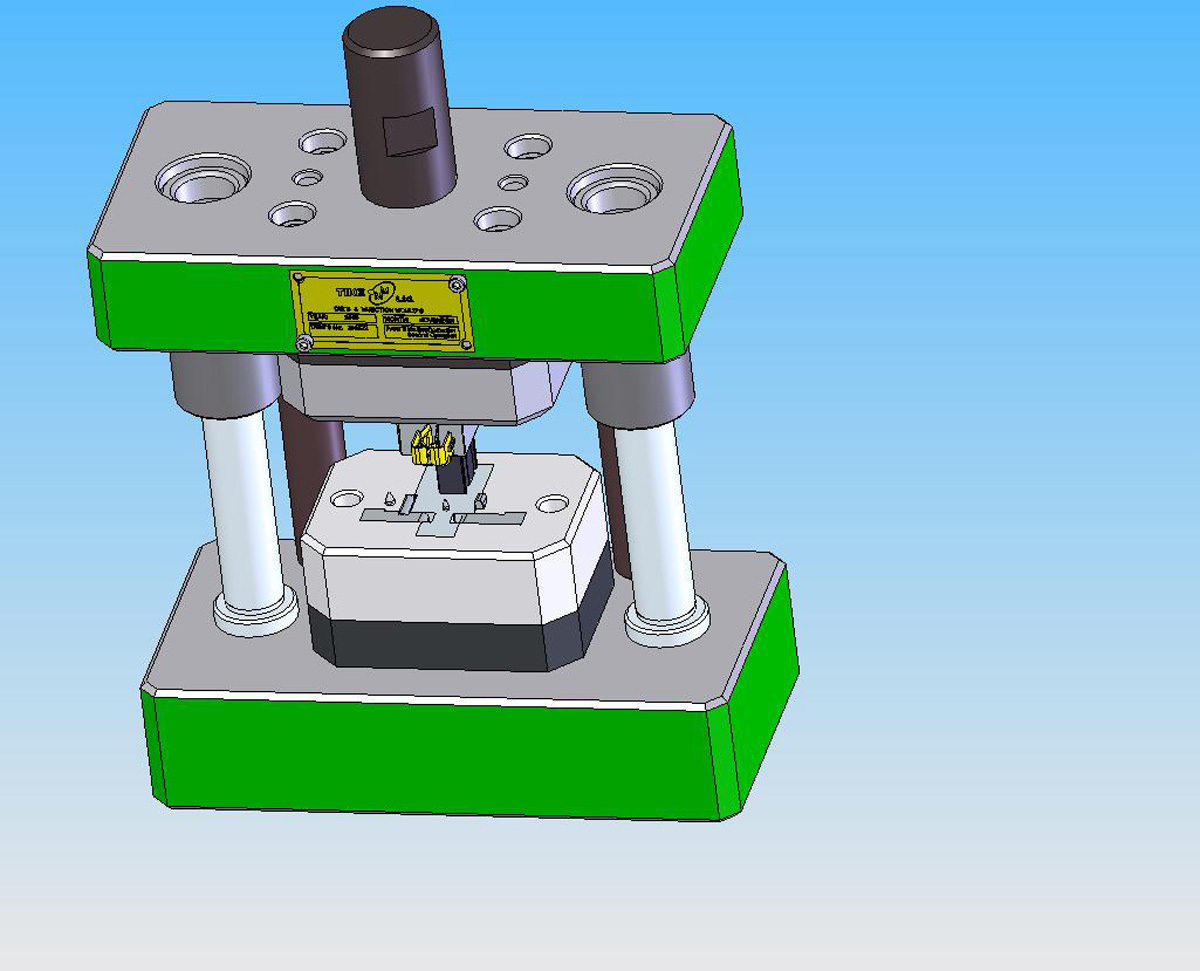
Фиг.6-43
от който трябва да се извади в посока перпендикулярна на хода на пресата. За решаване на проблема и от съображения за безопаност на работника, в поансона са поставени избутвачи, които чрез преобразуащ гърбичен механизъм изваждат огънатия детайл странично в посока към оператора. Щанцата включва матрицодържач с огъващи вложки, долен притискач и фиксатори. Към поансонодържач е закрепен огъващия поансон, по височината на който се води подпружинена задвижваща призматична гърбица със синусоидални канали, а напречно са разположени странични избутвачи. Задния край на последните контактува със синосуидалните канали, които ги принуждават да се прибират в огъващия поансон при хода на пресата надолу или да събуват огънатия детайл от поансона при обратния ход нагоре. Така, в момента на контакт на призматичната гърбица с матрицодържача, започва прибирането на странични избутвачи, което завършва преди началото на процеса огъване. Това гарантира безпрепятственото разполагане на огънатите рамена пред отворите за избутвачи в края на процеса. При хода нагоре, каналите на призматичната гърбица осигуряват необходимото за изваждане на огънатия детайл над матрицидържача закъснение на страничните избутвачи. Заготовката се центрова по два отвора чрез фиксатори. Подвижния и неподвижния пакет на щанцата се водят с колонки и втулки с триене при плъзгане.
3.3. Много операционни щанци с лостови преобразуващи механизми.
– Щанца с последователно действие за пробиване, отбортоване, формоване на фаски, огъване, закопчаване и изрязване на детайл ГАЙКА 63А от Фиг.3-1 е показана на Фиг.6-44 (сборен чертеж - изглед от горе), на Фиг.6-45 (напречен разрез А-А), на Фиг.6-46 (напречен разрез B-B), на Фиг.6-47 (напречен разрез C-C), на Фиг.6-48 (напречен разрез D-D), на Фиг.6-49 (напречен разрез E-E), на Фиг.6-50 (напречен разрез F-F), на Фиг.6-51 (напречен разрез G-G), на Фиг.6-52 (напречен разрез H-H), на Фиг.3-21 (технологична схема на лентата) и на Фиг.6-53 и Фиг.6-54 (спецификация).
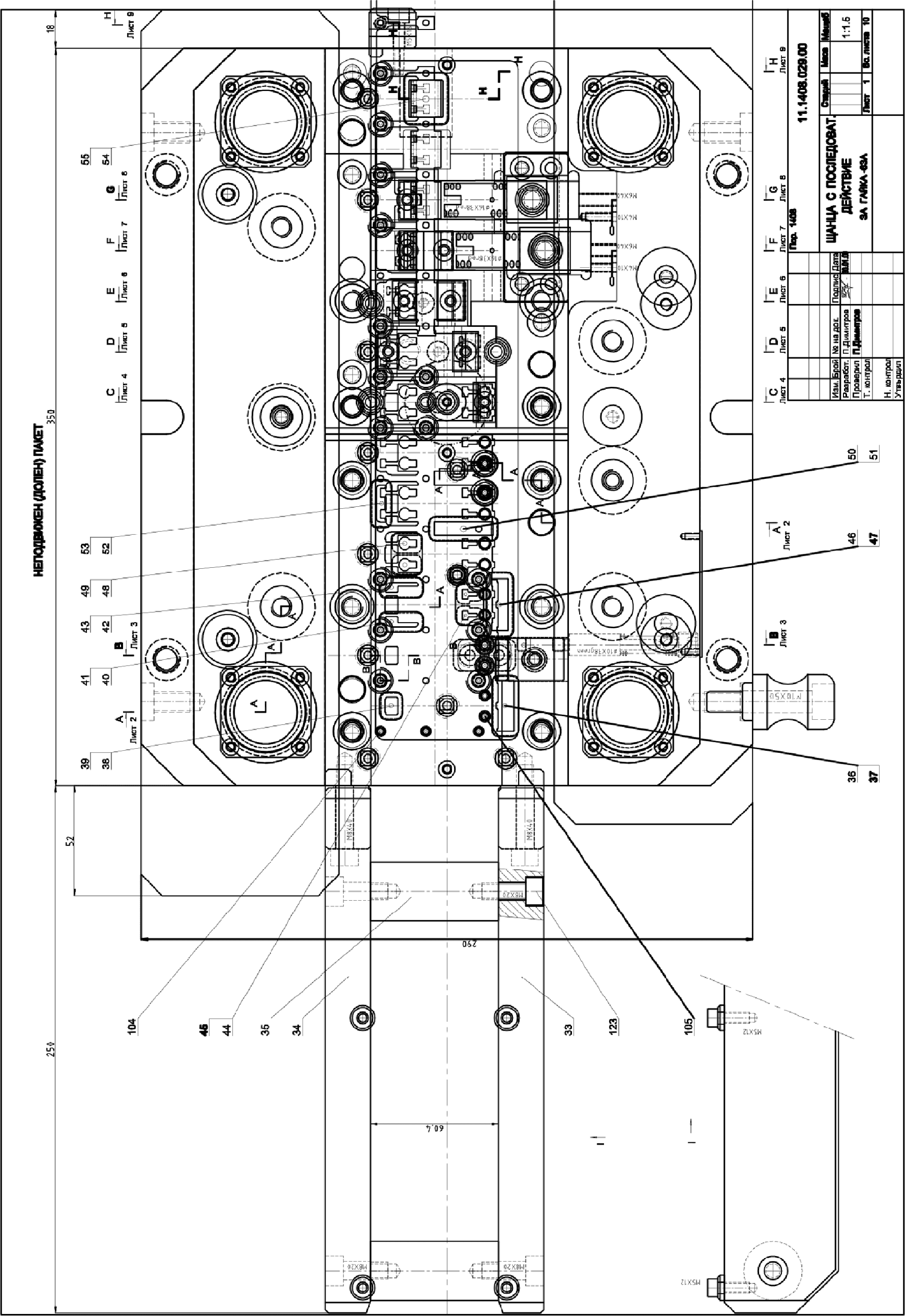
Фиг.6-44

Фиг.6-45
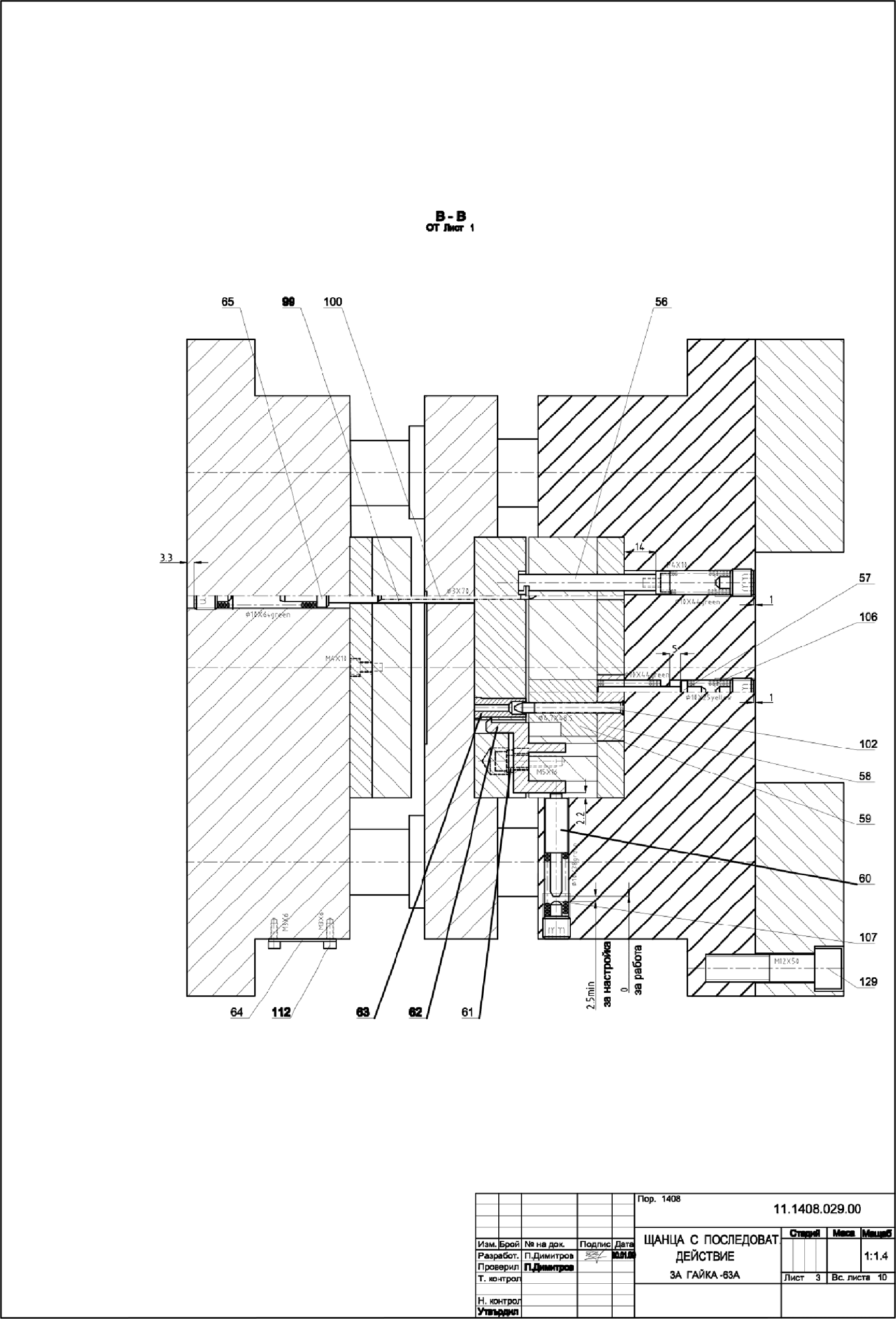
Фиг.6-46
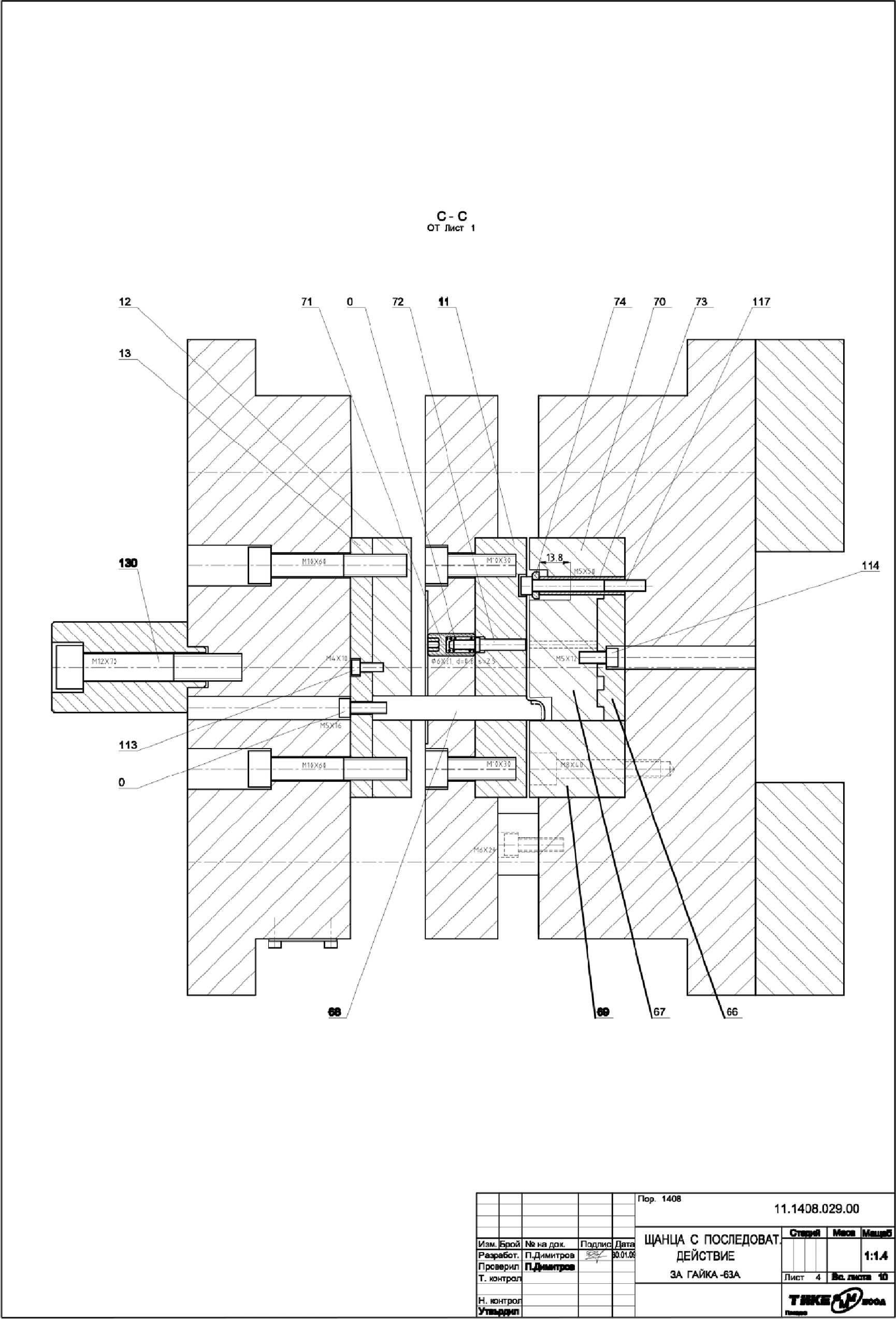
Фиг.6-47
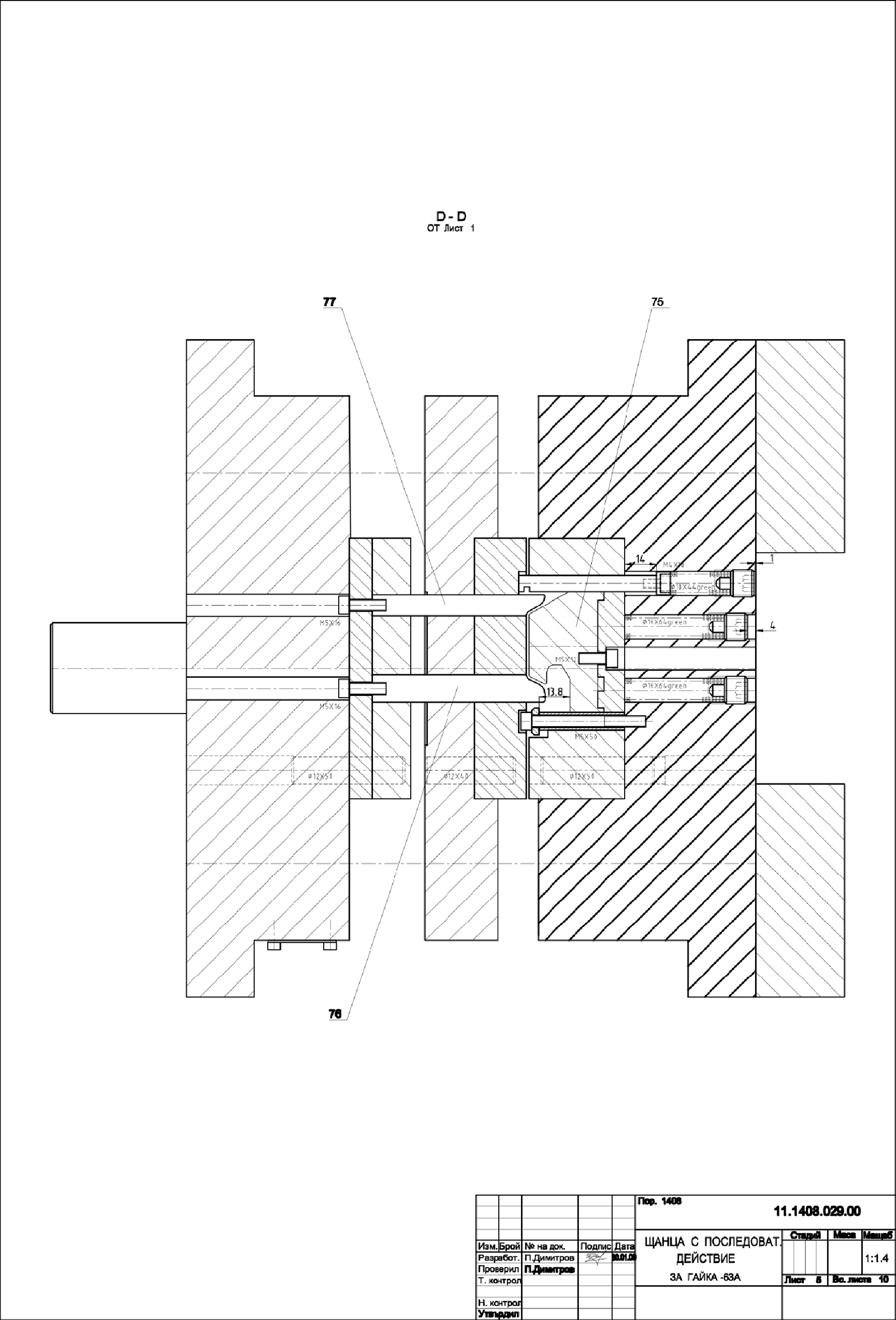
Фиг.6-48
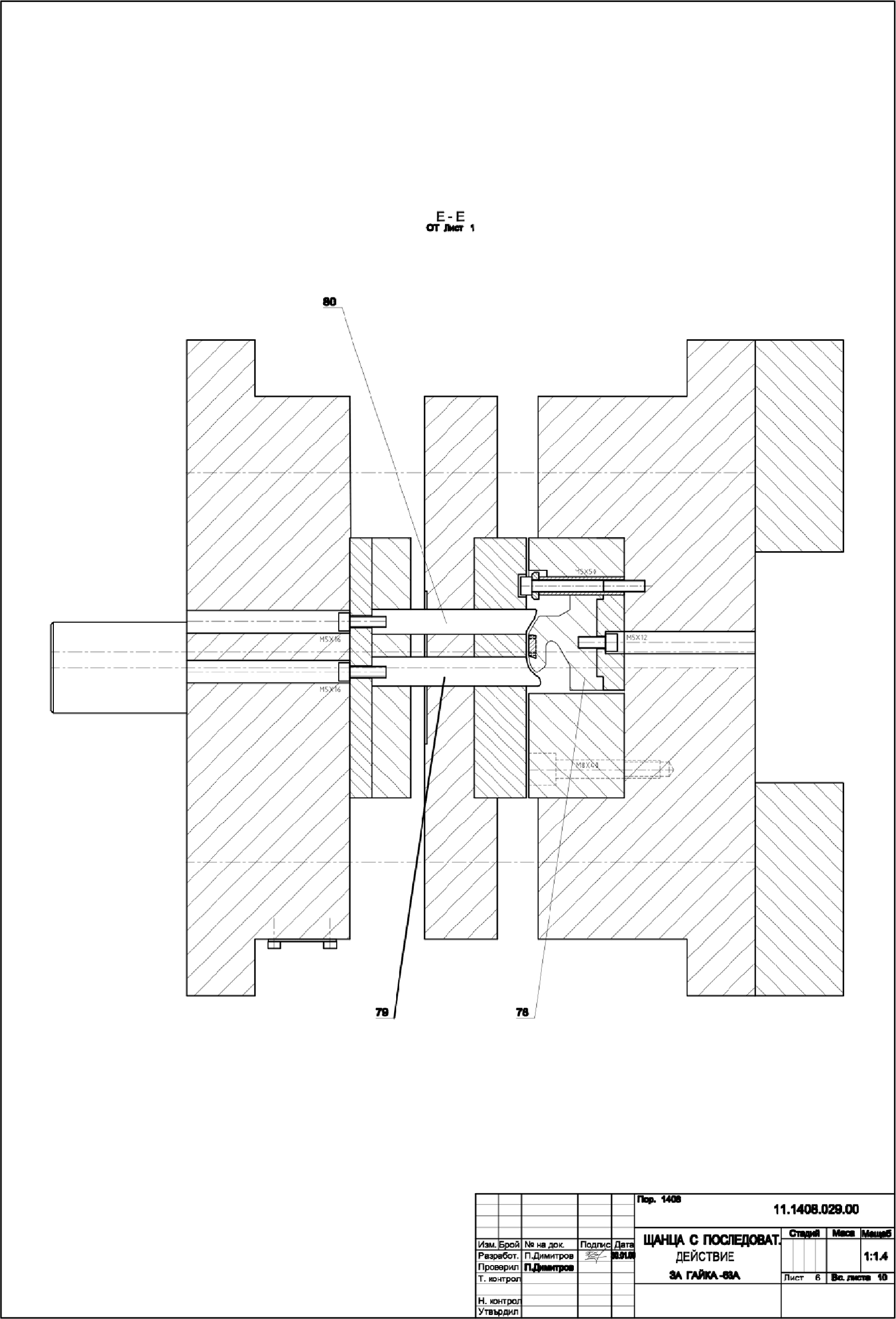
Фиг.6-49
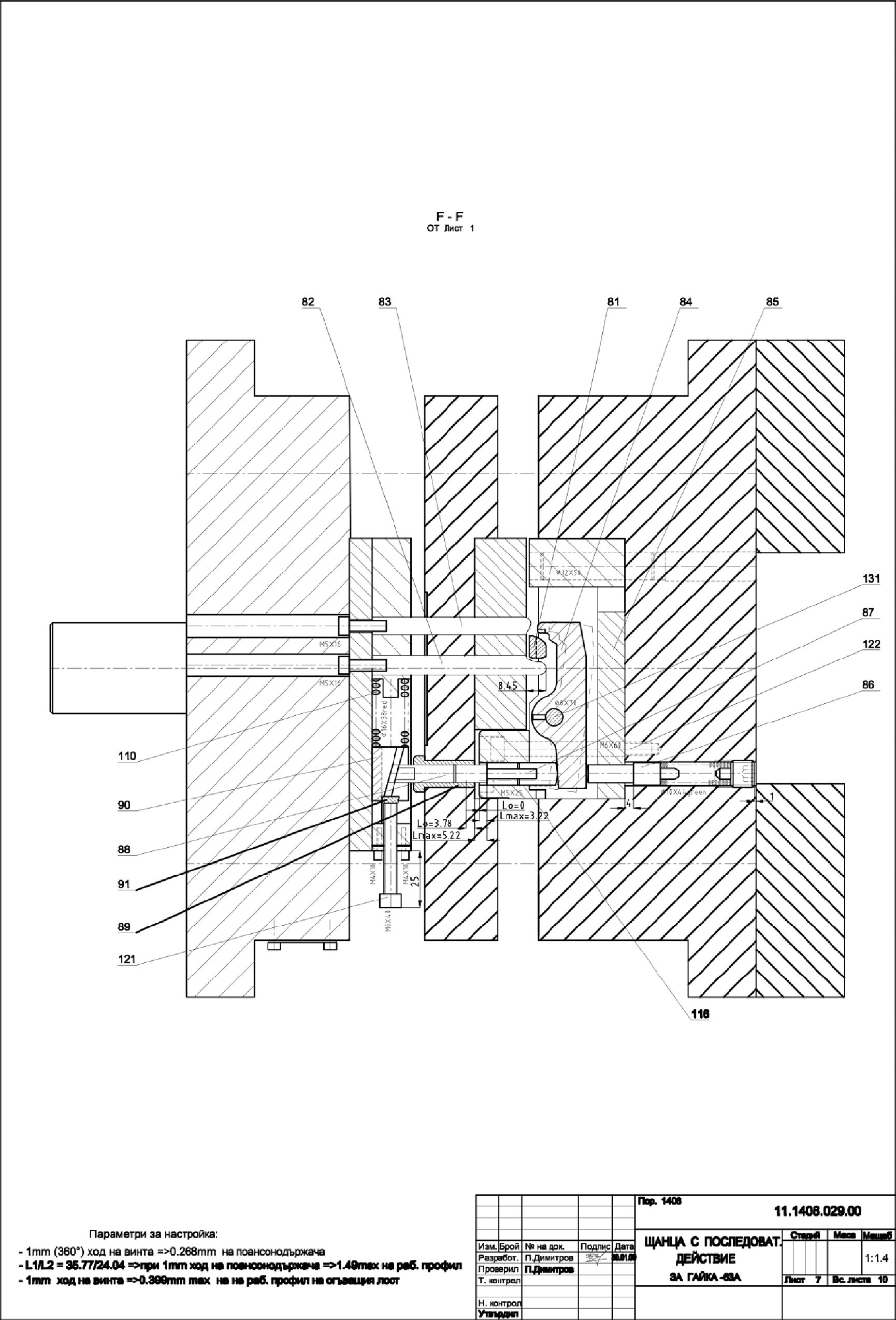
Фиг.6-50
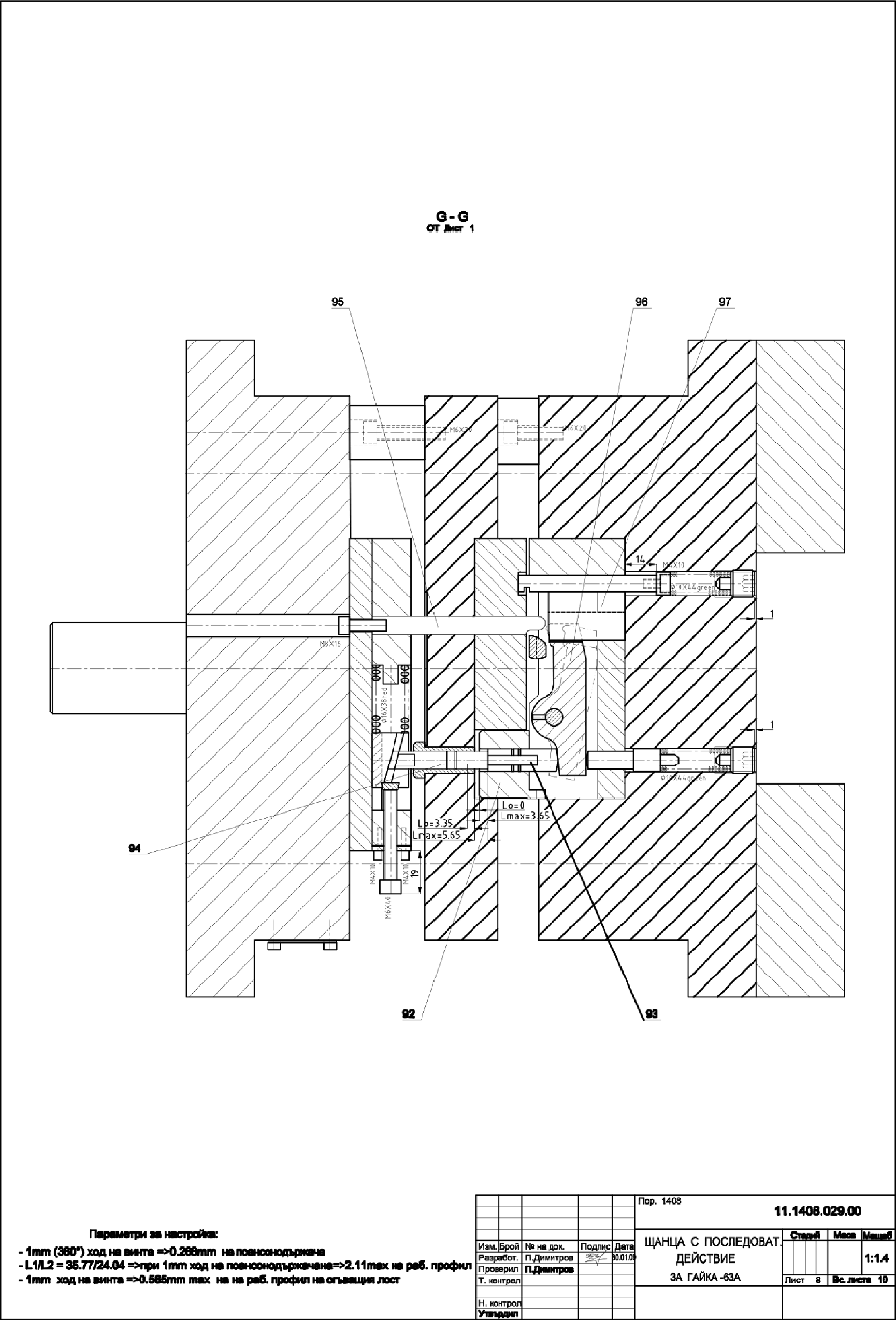
Фиг.6-51
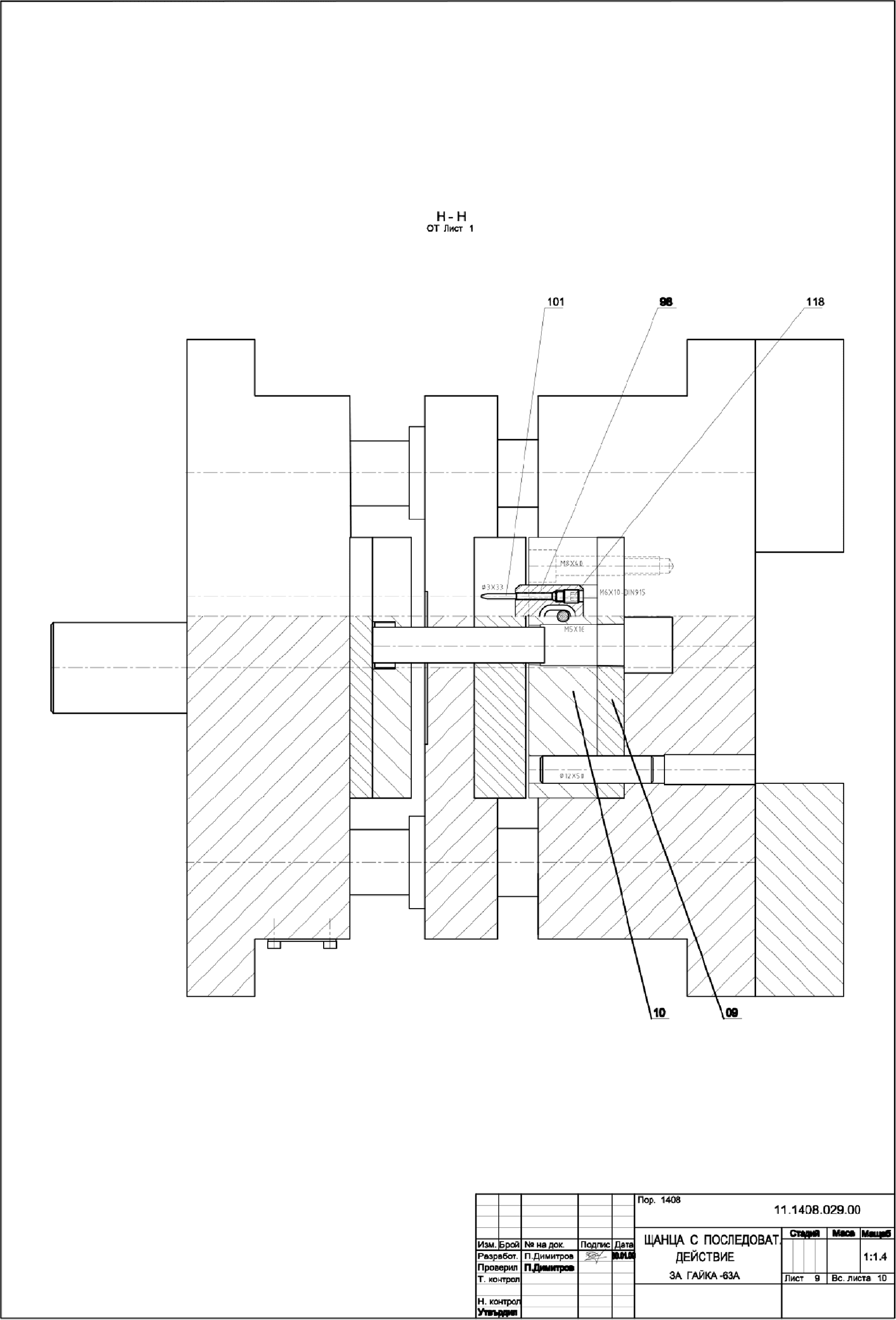
Фиг.6-52
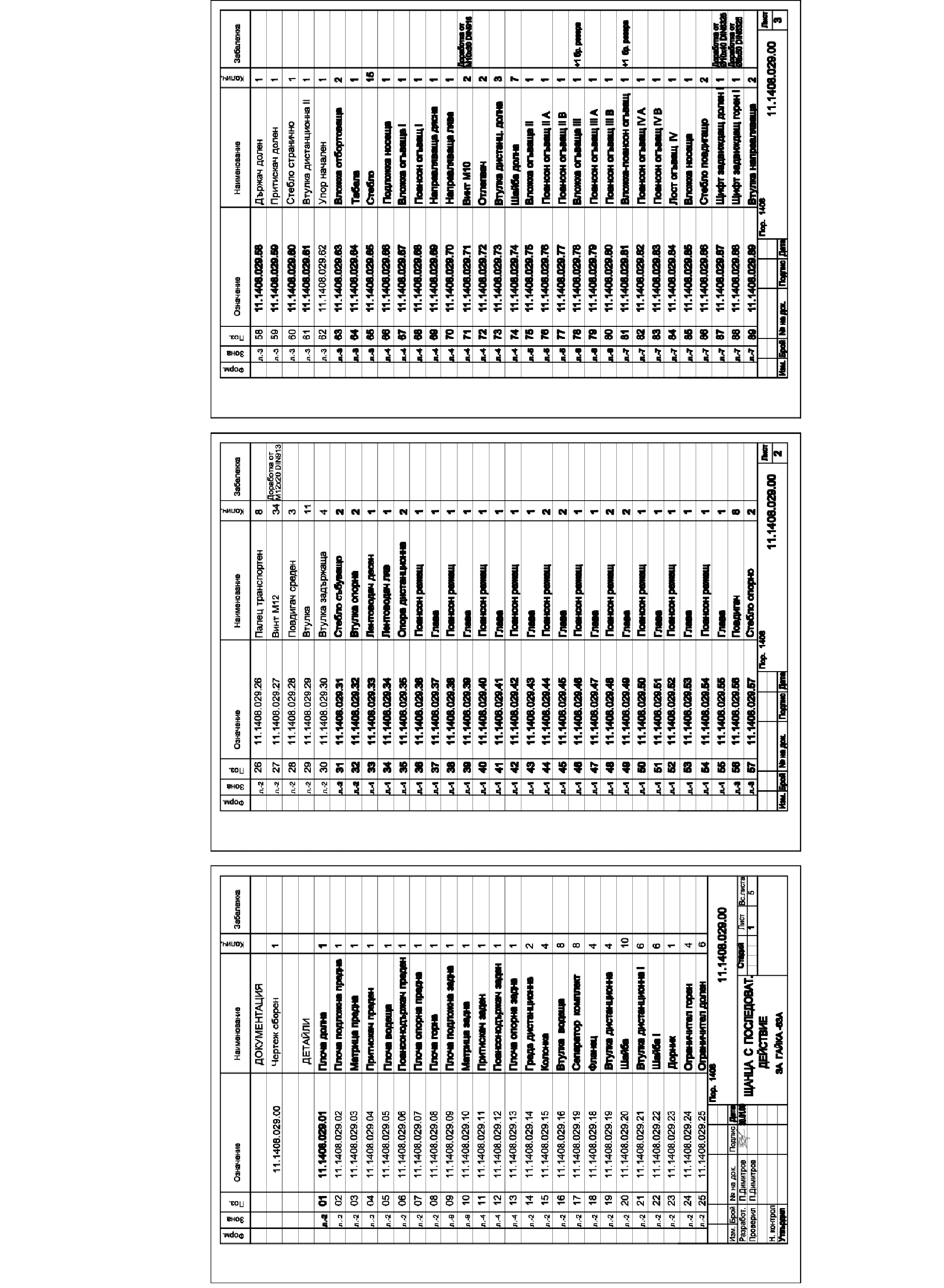
Фиг.6-53
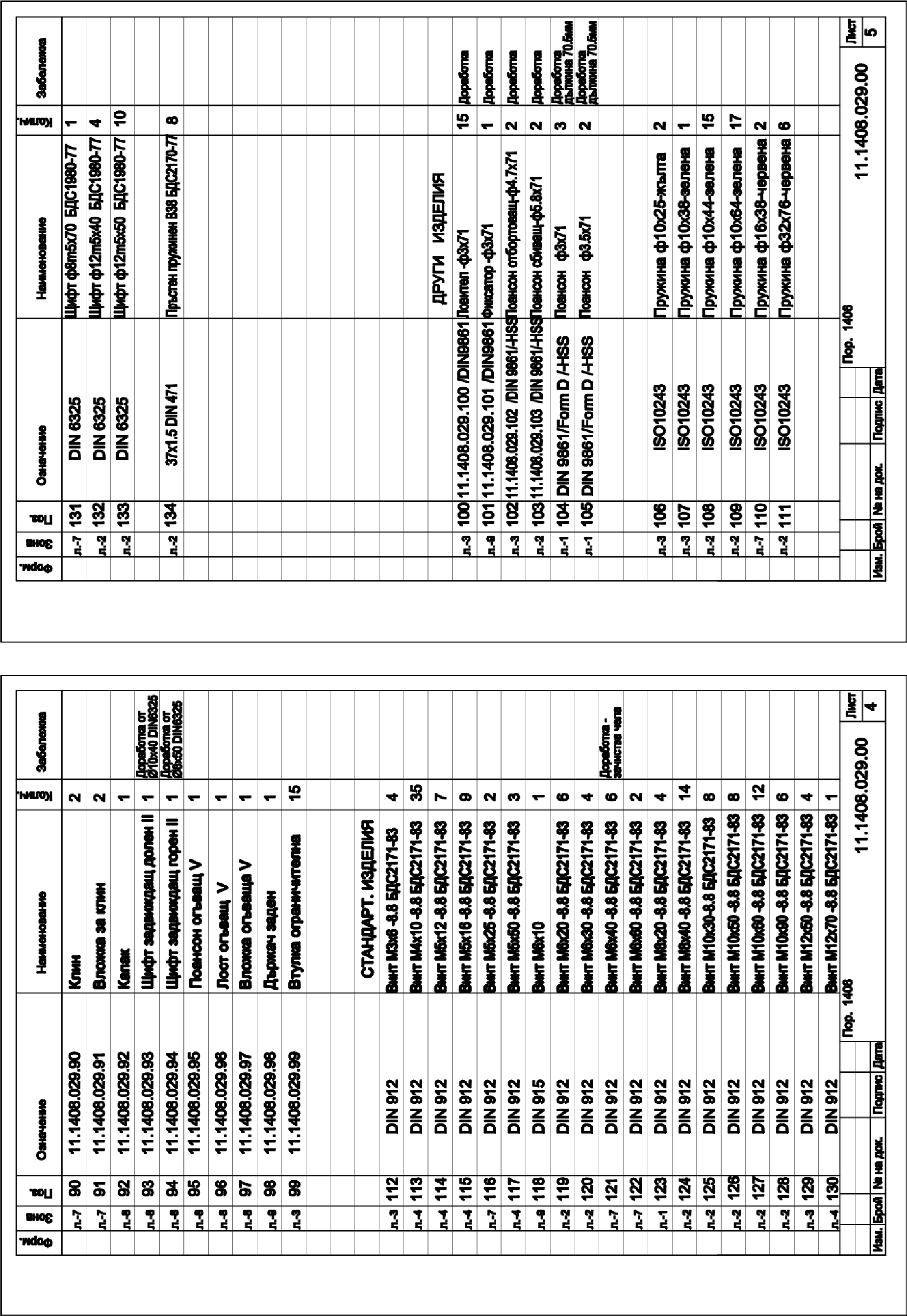
Фиг.6-54
Конструкцията включва предна и задна матрица (поз.3, поз.10), режещи поансони (поз.36, поз.38, поз.40, поз.42, поз.44, поз.46, поз.48, поз.50, поз.52, поз.54, поз.104, поз.105), огъващи поансони (поз.68, поз.76, поз.77. поз.79, поз.80, поз.81, поз.82. поз.83. поз.95), огъващи вложки (поз.67, поз.75, поз.78, поз.81, поз.85, поз.97), отбортоваща вложка с поансон (поз.63, поз.102) и формоващ фаска поансон (поз.103). Лентата се притиска и събува с преден и заден притискач (поз.4, поз.11), монтирани към подпружинената водеща плоча (поз.5), Водене и повдигане на лентата се извършва с повдигачи (поз.56), а точното центроване спрямо матрицата и поансоните от подпружинени ловители (поз.100), Режещите поансони са със запоени глави и са монтирани в преден и заден поансонодържач (поз.6, поз.12), а огъващите поансони и вложки са закрепени с винтове. Огъващите вложки в матрицата са плаващи и под действието на пружини се вдигат заедно с повдигачите, за да осигурят възможност на лентата с огънатите зони да се премества между отделните позиции. Лостовите преобразуващи механизми са показани на Фиг.6-50 и на Фиг.6-51. Огъващият лост IV (поз.84) повдига съгласувано с огъващия поансон (поз.82) долната част на огънатото рамо преди изпълнението на огъвка от поансон (поз.83), с което осигурява нейната опора и затваряне на 360º на детайла (разрез F-F от Фиг.3-2). Огъващият лост V (поз.96) на следващата работна позиция изпълнява роля на опорен заключващ поансон, като синхронизирано с огъващия поансон (поз.95) огъва езичетата нагоре до влизането им в изрязания заключващ профил на детайла (разрез G-G от Фиг.3-2). Огъващите лостове се задвижват чрез долни задвижващи щифтове (поз.87. поз.93), разположени в неподвижния пакет на щанцата. Тези щифтове се задействат от регулируемите посредством клин (поз.90) горни задвижващи щифтове (поз.88. поз.94), разположени в подвижния пакет на щанцата. Клина е разработен и като предпазен механизъм в случай, че огънатите езичета не могат да попаднат в изрязания заключващ профил. Тогава натоварването, предадено от горните задвижващи щифтове на клина, предизвиква неговото преместване и свиване на пружината (поз. 110), с което лостовете се предпазват от счупване. Настройката на горните задвижващи щифтове (поз.88. поз.94) се контролира чрез измерване на разстоянието между главата на регулиращия винт (поз.121) и плочата (размери 25 mm и 19 mm). На входа на щанцата лентата се подава през лентоводачи (поз.33, поз.34), а на изхода е предвиден регулируем по височина фиксатор (поз.101), който влиза в пробитите за ловител отвори в отпадъчната ивица от лентата и позволява ръчно центроване на последната и визуален контрол на стъпката на подаване. Воденето с минимална стегнатост на подвижния спрямо неподвижния пакет се извършва с триене при търкаляне посредством четири комплекта от водещи колонки (поз.15), втулки (поз.16) и сачмени сепаратори (поз.17). За по-голяма коравина и удобно обслужване, колонките (поз.15) са закрепени към водещата плоча (поз.5) неподвижно в средната си част – така свободната за огъване част е два пъти по-къса, а коравината е по-голяма.
4. Пренастроеваеми щанци за производство на набор от подобни детайли.
Често за детайлите от листов материал се разработват гама от различни типоразмери или набор от различни модификации на основната конструкция. Конкретната форма, размери и различните елементи, обект на модификация, определят технологията на щанцоване. В нея обикновено се залагат пренастроеваеми щанци за общи операции на основната конструкция и модификациите на детайла. Така се увеличава серията за пренастроевамия инструмент и се намалява общия брой необходими щанци. Пренастроеваемите щанци са ефективни при годишен обем от детайли за средно серийно производство (примерно от 10000 до 100000 за малки детайли, от 500 до 20000 за голямогабаритни детайли). Те могат да се окажат ефективни и за по-малки годишни количества при производство на много сложни голямо габаритни детайли.
4.1. Най-разпространениия вид пренастроеваеми щанци са със сменяеми активни части – матрици и поансони. Те изискват сваляне от пресата, разглобяване и замяна на активните части с други, сглобяване и нова настройка на пресата (например щанцата за външно отбортоване на детайл ПРЕДПАЗИТЕЛ ЗА ЪЛОШЛАФ от Фиг.6-8).
4.2. Друг вид пренастроеваеми щанци са с частично изключване или включване на активни части – поансони, вложки, упори. Тяхната настройка се извършва на пресата без сваляне на щанцата и са изключително подходящи при малки серии и различни модификации на основната конструкция на щанцования детайл.
4.3. Трети вид пренастроеваеми щанци са с преместване на едни и същи активни части, упори, фиксатори, лентоводачи на друго място. В повечето случаи, те също е необходимо да се свалят от пресата за пренастройка.
– Щанца с последователно действие за пробиване и изрязване на детайл “SHIELD BKP -4 -6 -8 -12” от Фиг.6-55, Фиг.6-56, Фиг.6-57, Фиг.6-58 (ленти за модификации -4, -6, -8, -12)
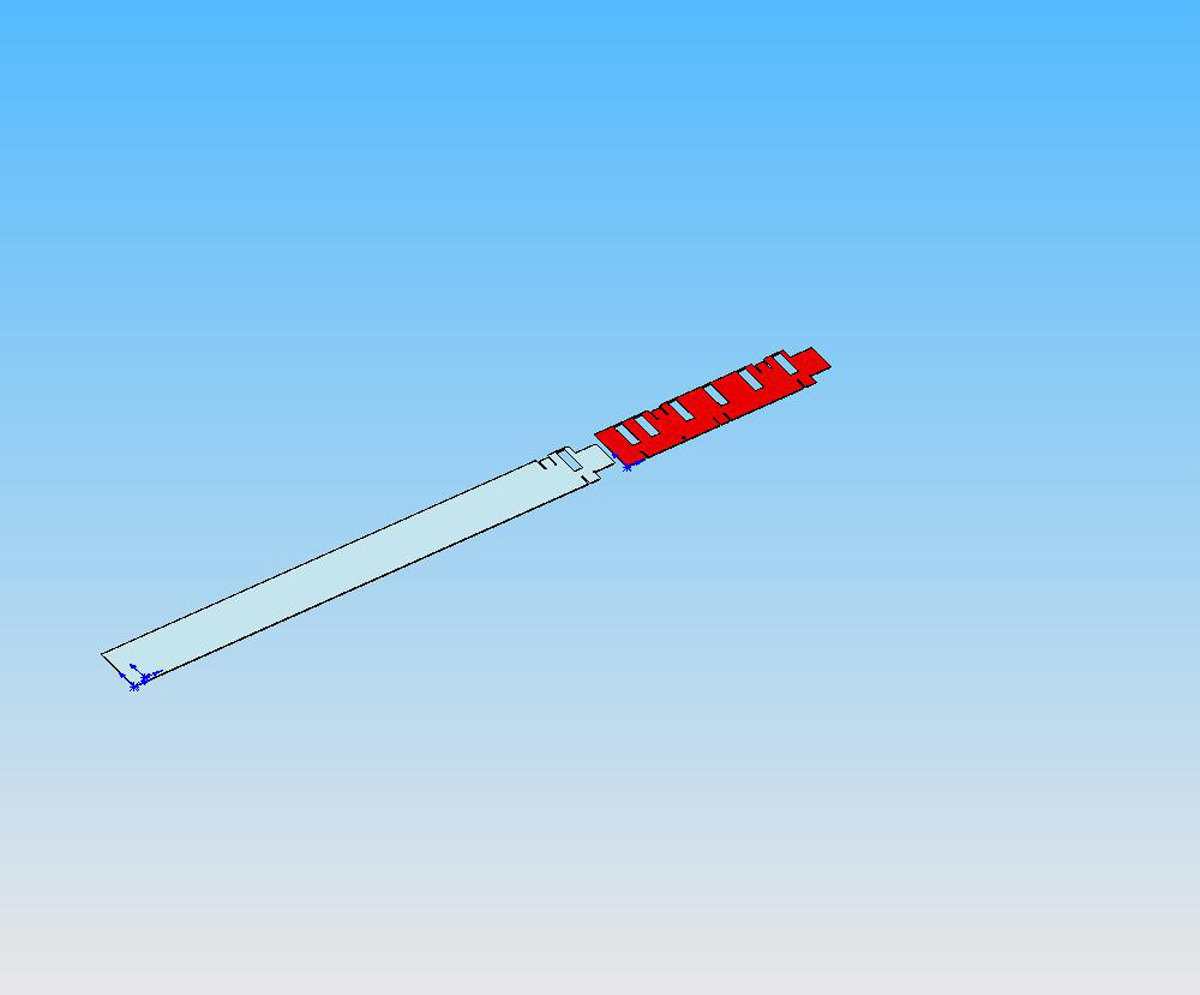
Фиг.6-55
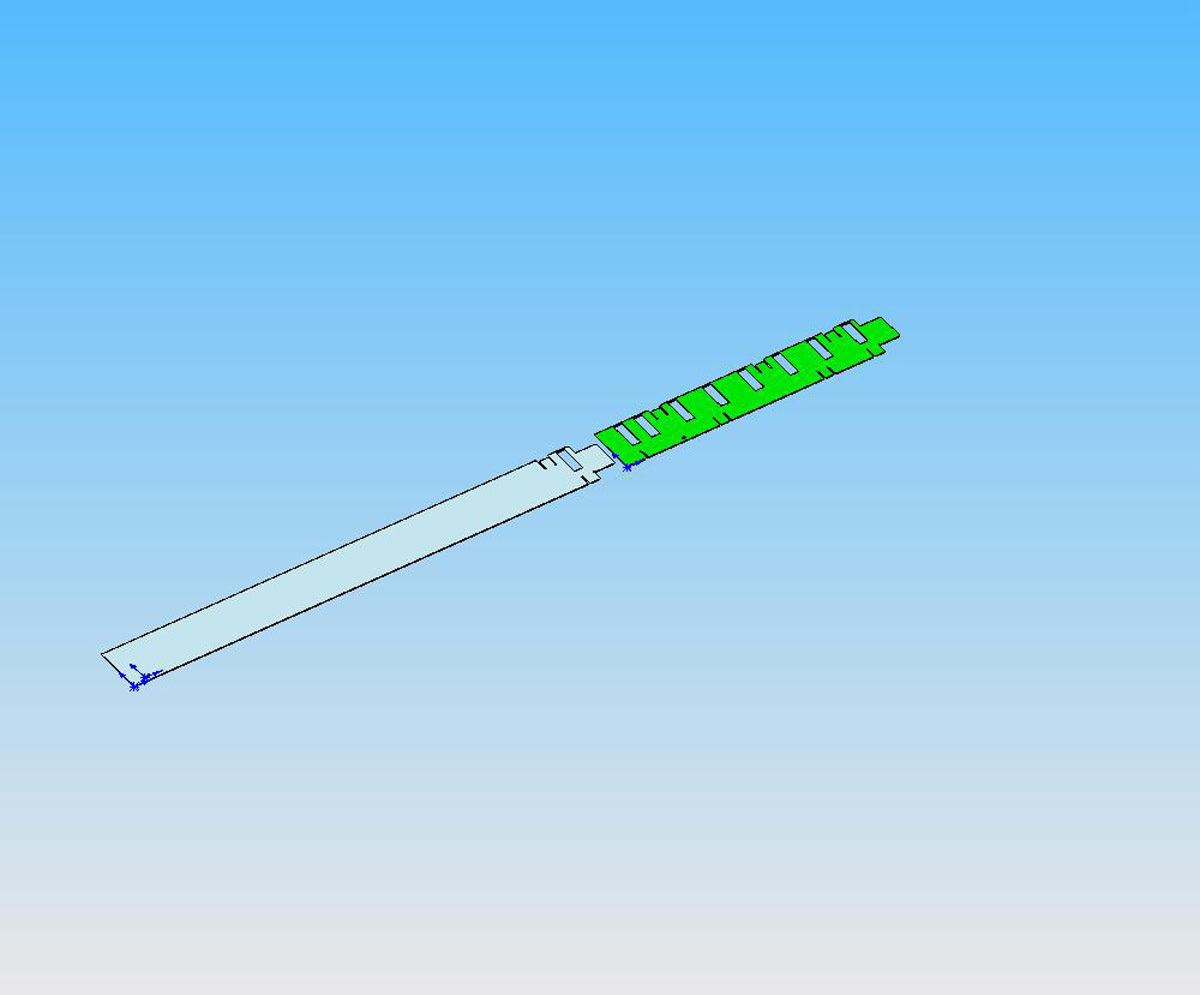
Фиг.6-56
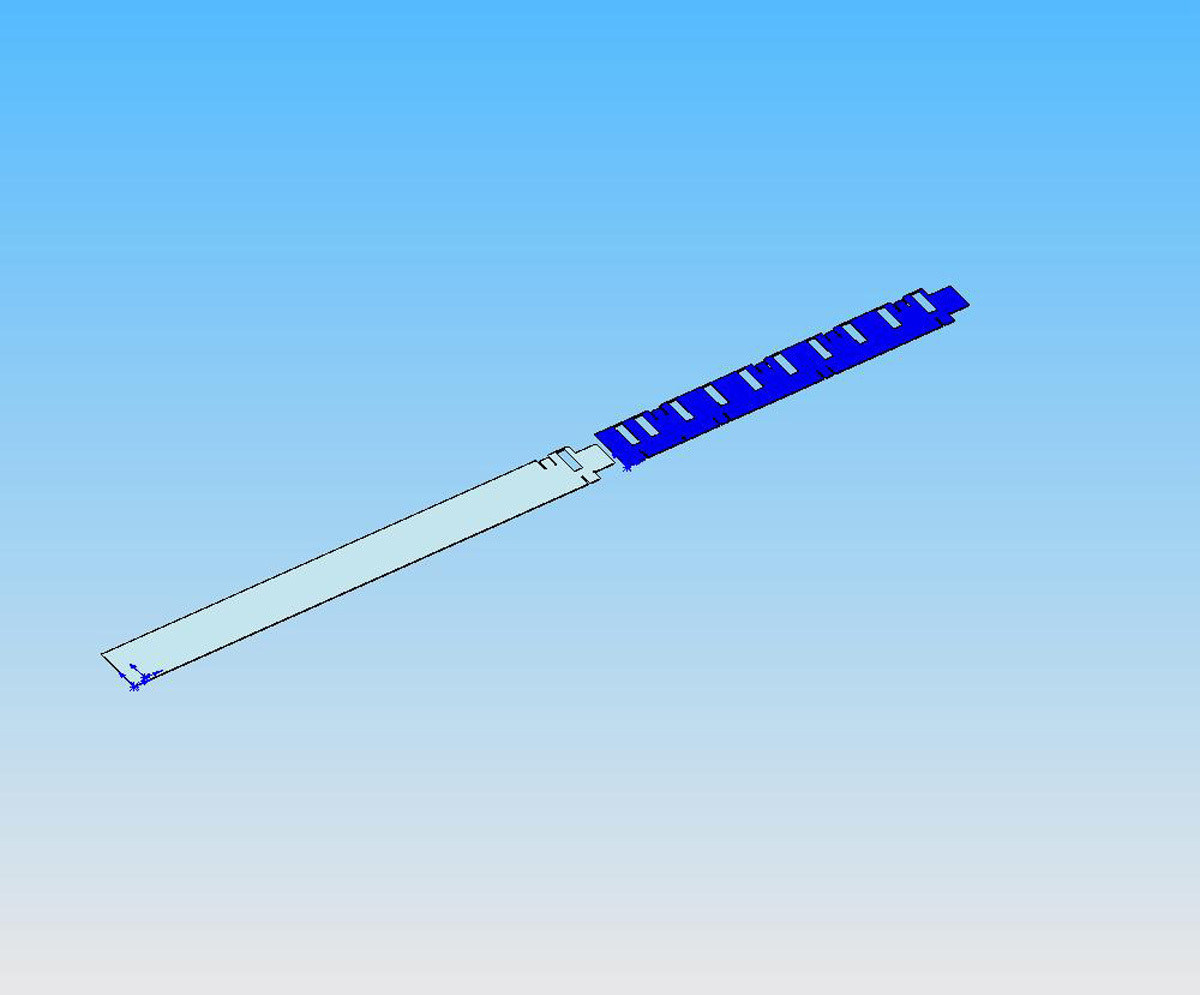
Фиг.6-57
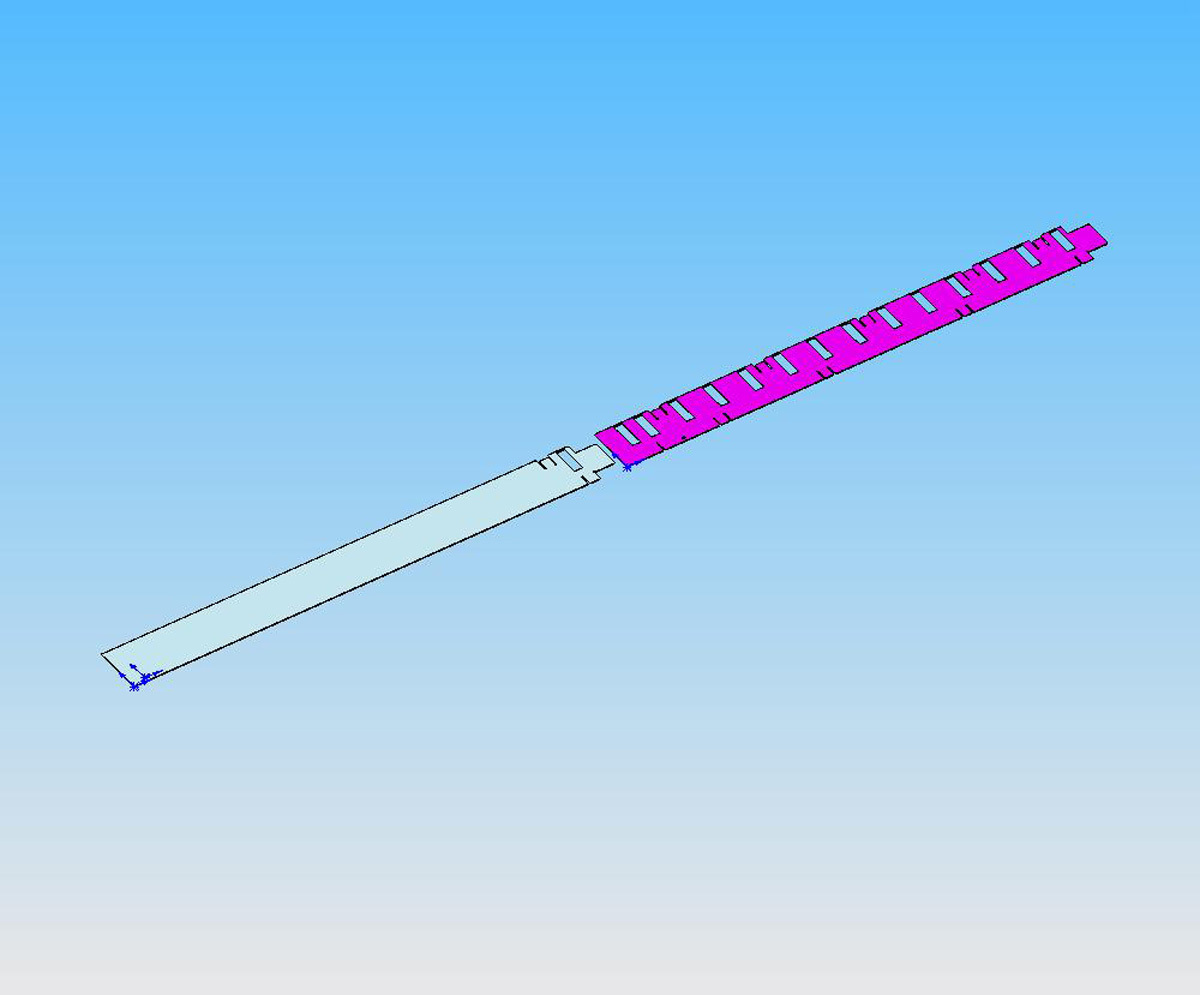
Фиг.6-58
е показана на Фиг.6-59 (общ вид)
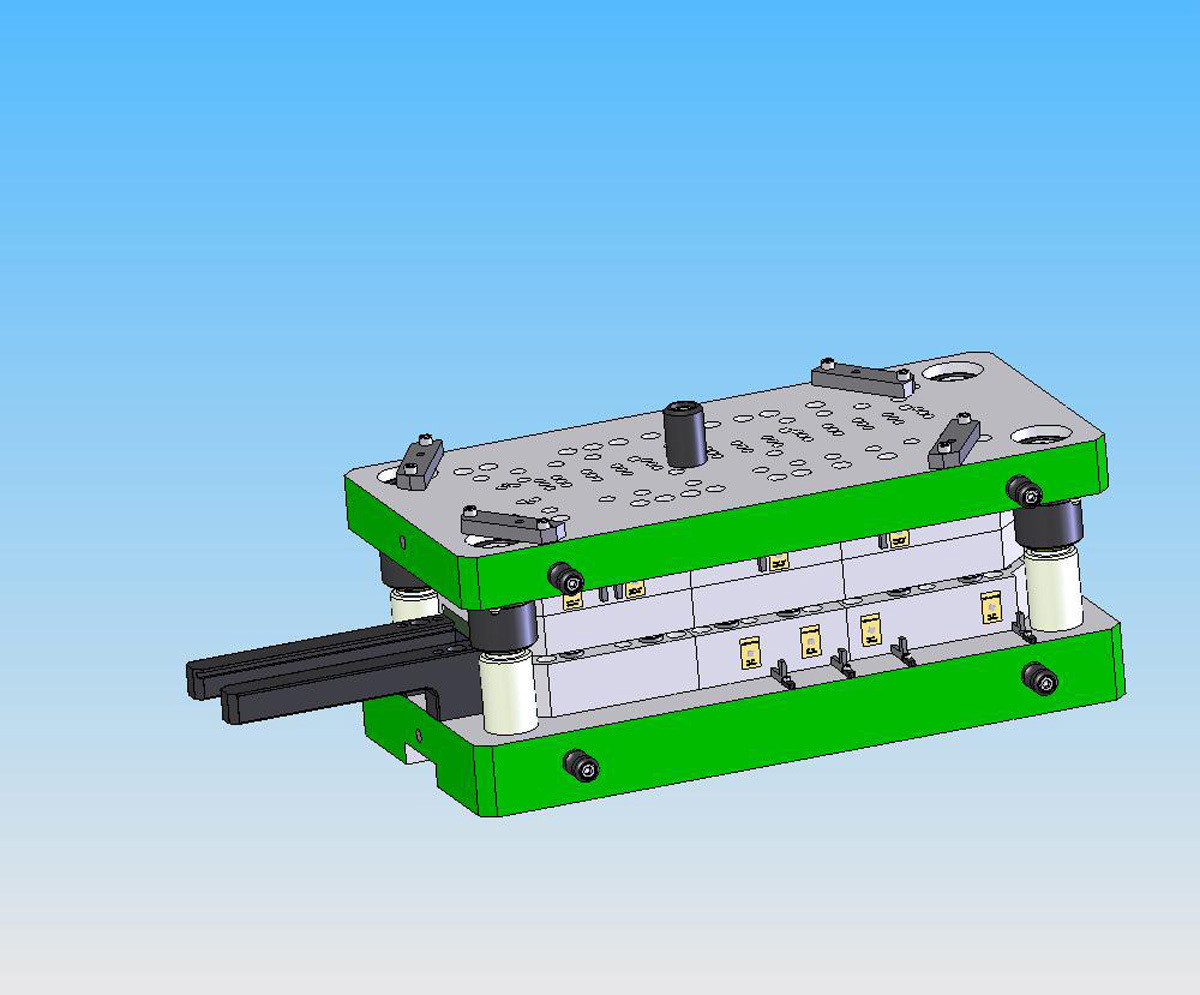
Фиг.6-59
и Фиг.6-60 (управляващи шибри).
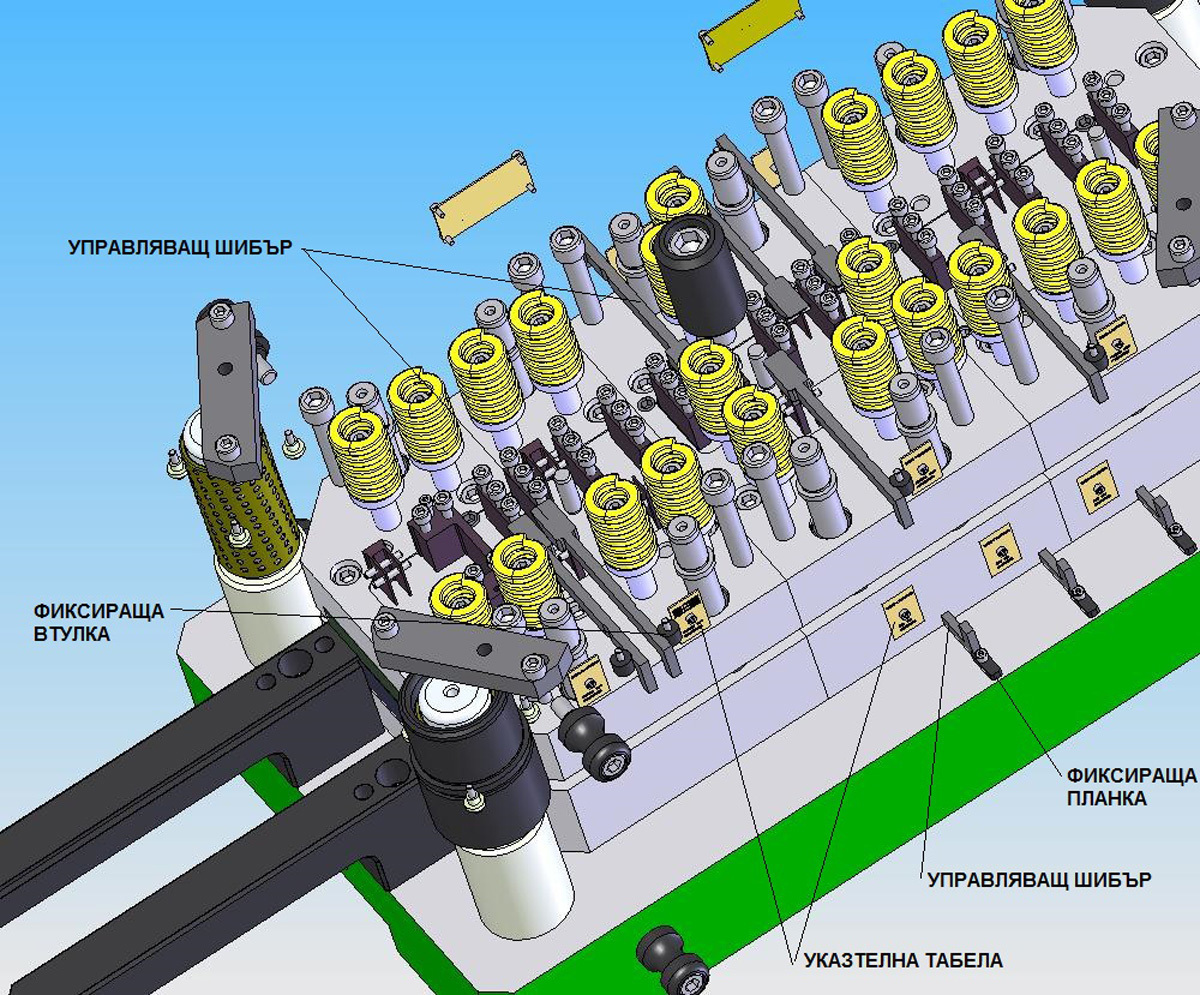
Фиг.6-60
Предназначена е за работа на 100 тонна ексцентър преса с ръчно подавяне на лента. Инструмента е секционен, съставен от 3 пакета, всеки от които включва матрица, режещи поансони, притискач и поансонодържач. Пренастройката за всеки вид се състои от включване (натискане към щанцата) или изключване (издърпване навън от щанцата) на всеки управляващ шибър, в зависимост от надписа на указателната табела и заключване в това положение чрез завъртане на фиксиращата втулка, до попадане в изпълнено за целта гнездо в шибъра (виж Фиг.6-60). Управляващите шибри са разположени над горната част на режещите поансони и работят на принципа – поансонът е включен, когато опира в шибъра, а изключен, когато шибъра е издърпан навън, с което поансона няма опора за да изпълни рязане и се повдига нагоре при работния ход. Лентата се води по преден лентоводач и се подава до упори, задействани от управляващи шибри в долната част на матриците. Подвижният и неподвижният пакети на щанцата се водят с колонки и втулки с триене при плъзгане.
– Щанца с последователно действие за пробиване, огъване, формоване, отрязване на детайл “ОСНОВА ЗА ДРОСЕЛ” от Фиг.6-61 (ленти за различните модификации)
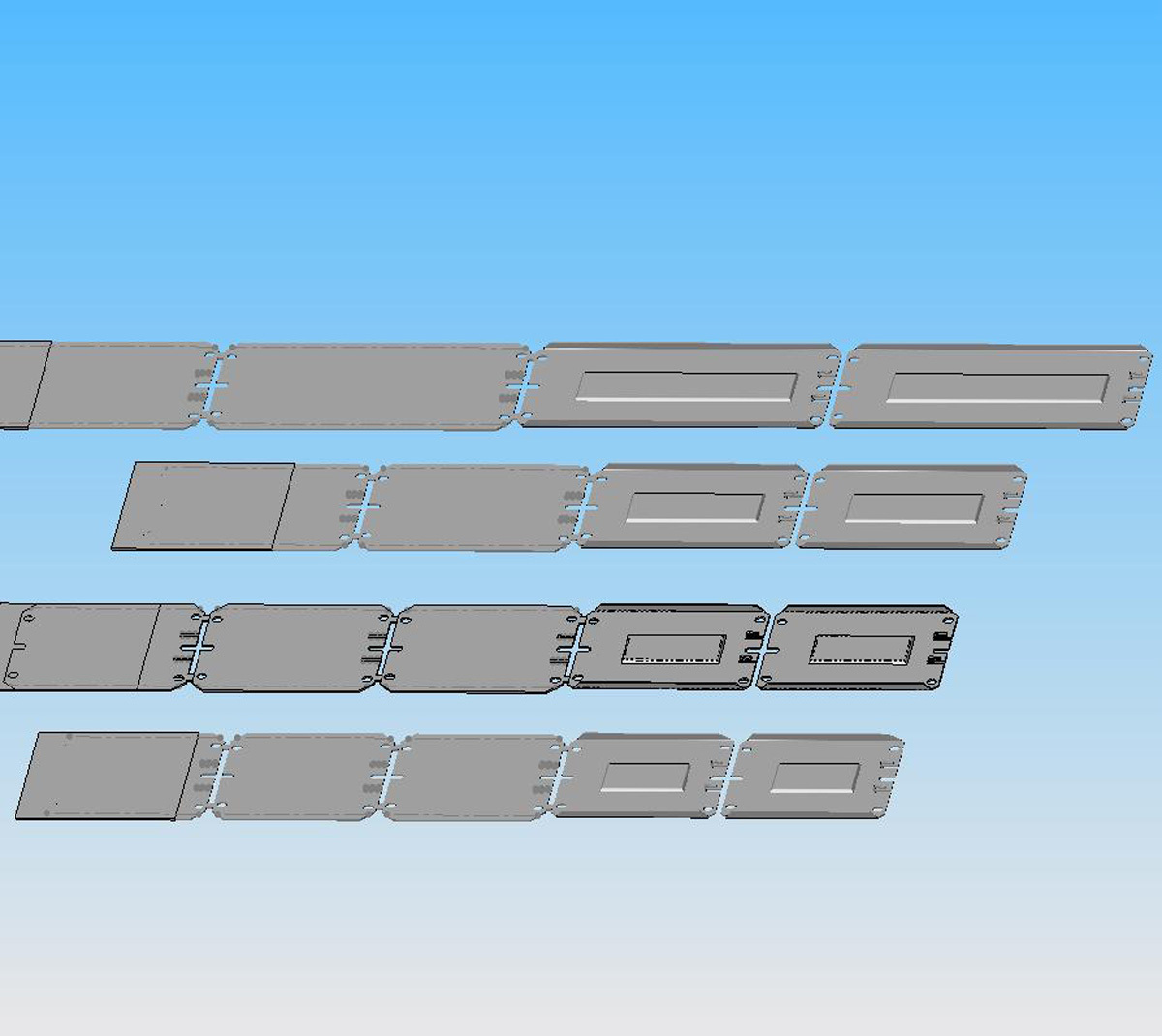
Фиг.6-61
е показана на Фиг.6-62 (общ вид),
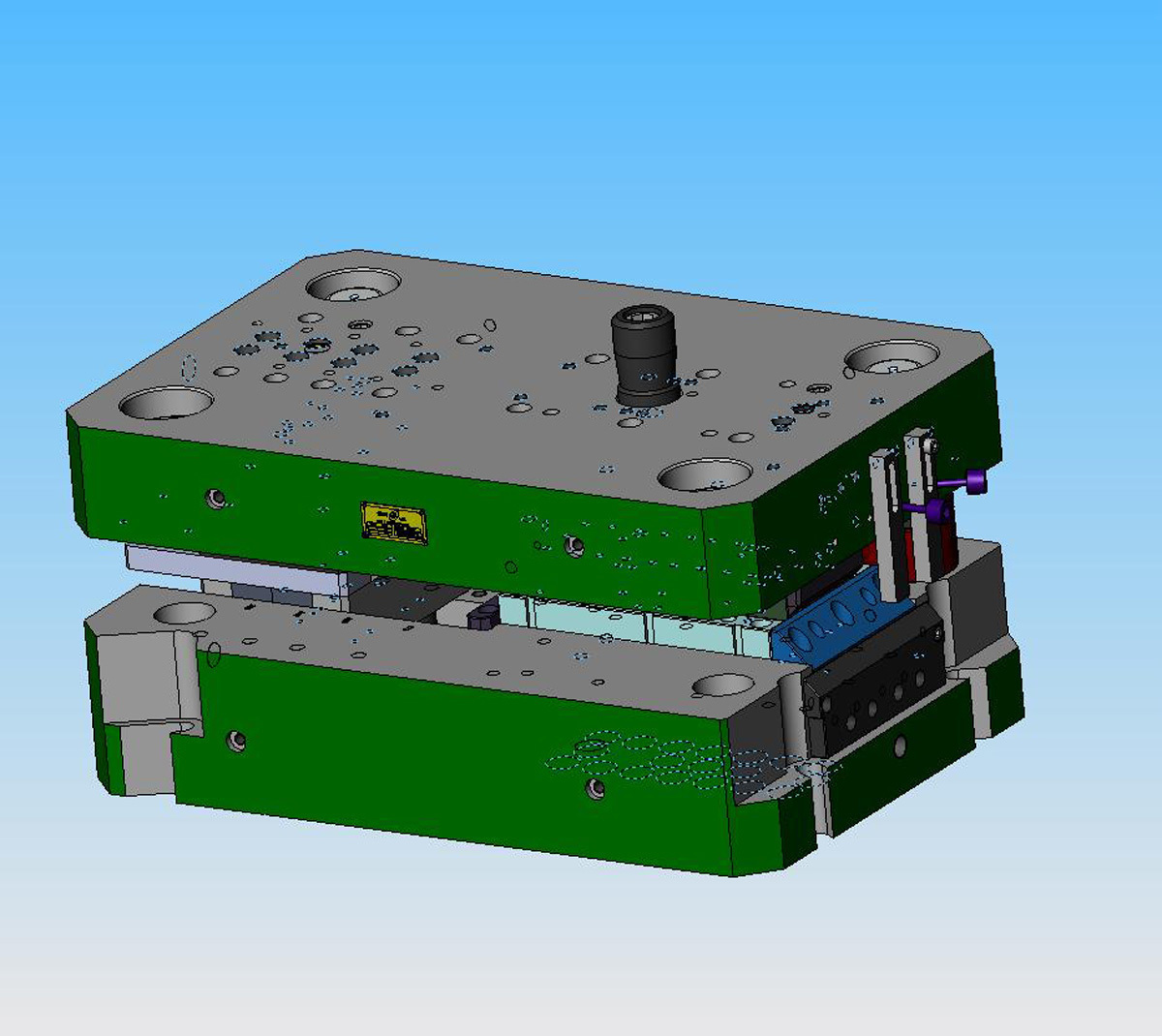
Фиг.6-62
на Фиг.6-63 (надлъжен разрез),
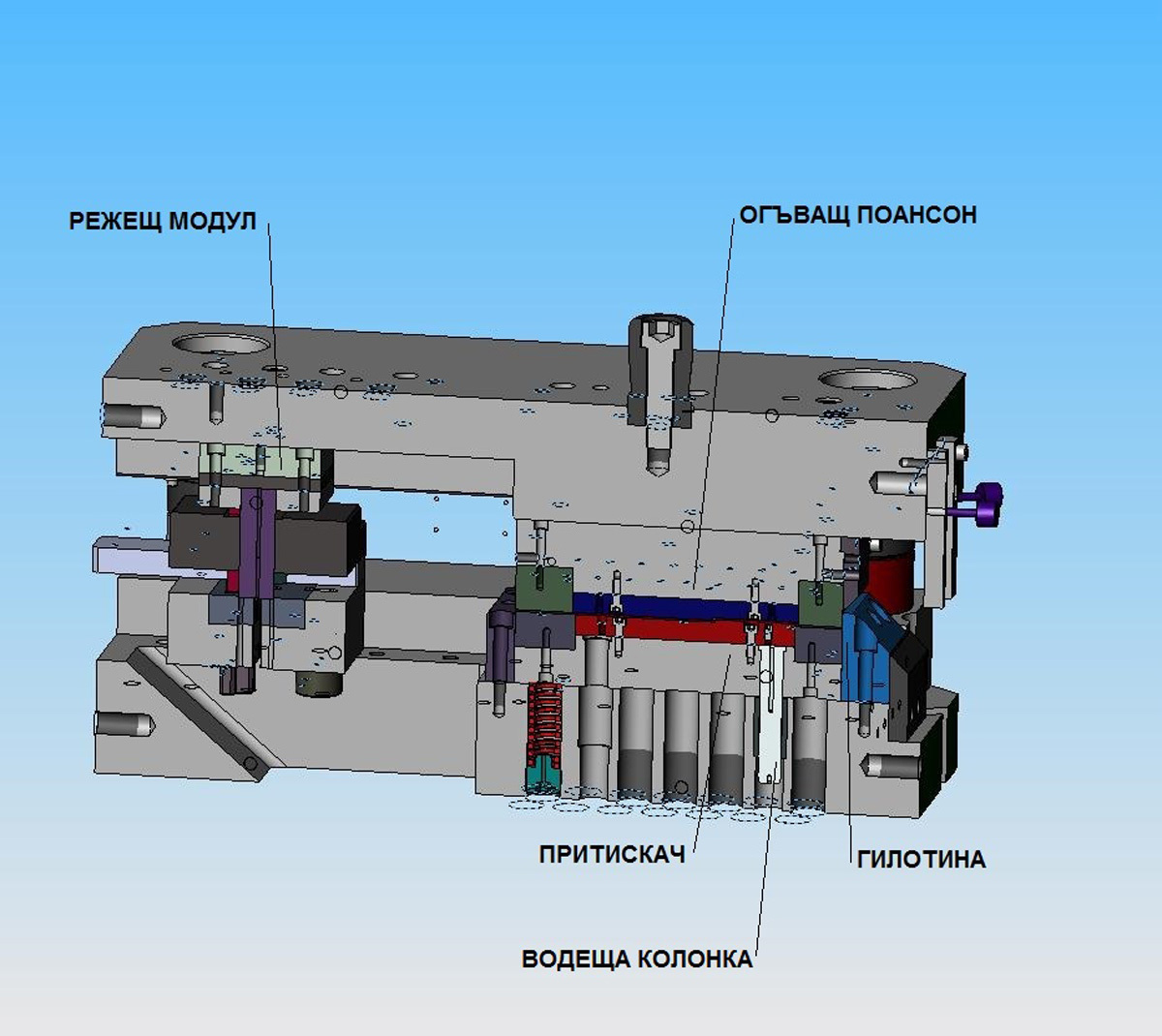
Фиг.6-63
на Фиг.6-64 (режещ модул),
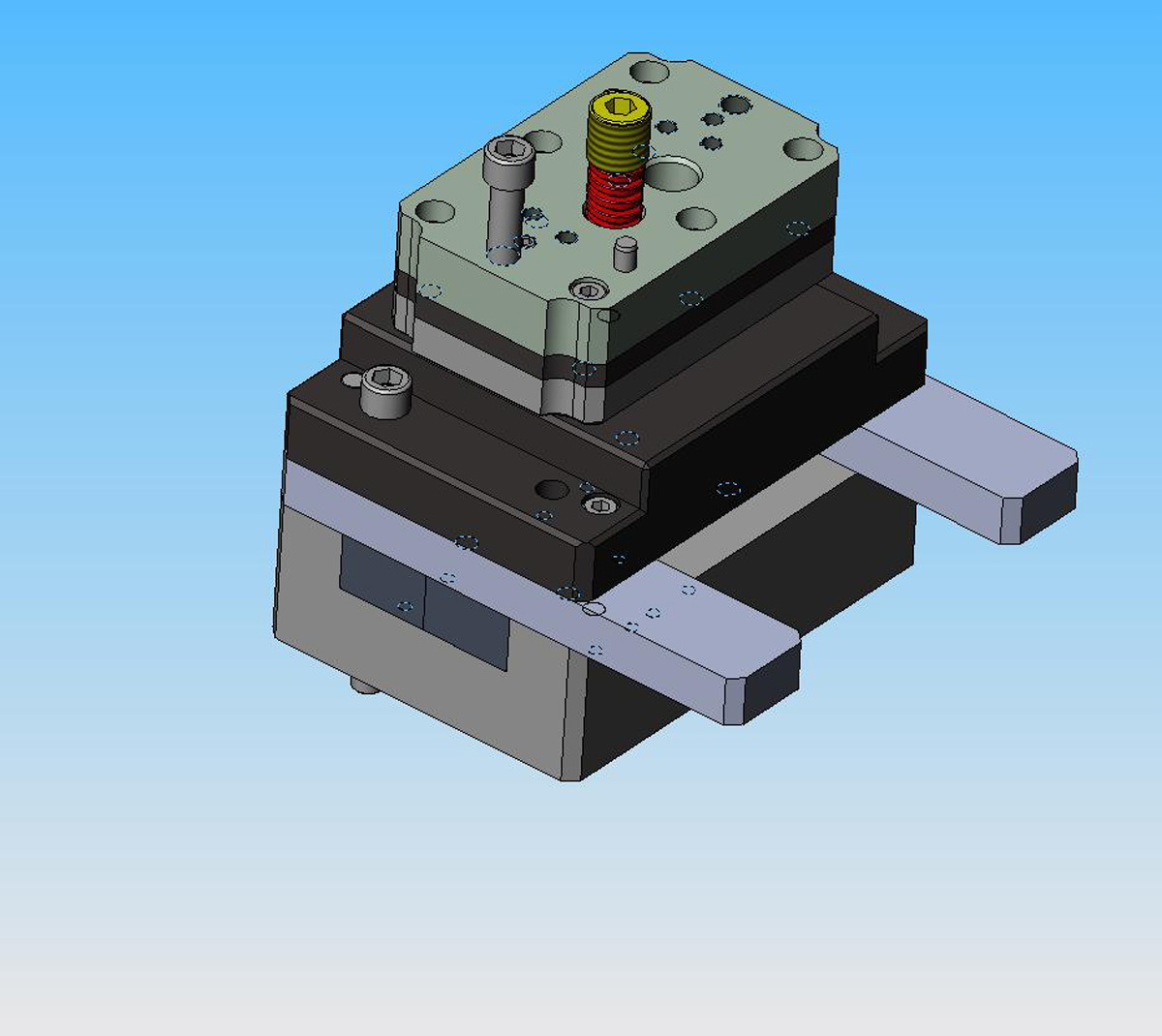
Фиг.6-64
на Фиг.6-65 (огъващ поансон),
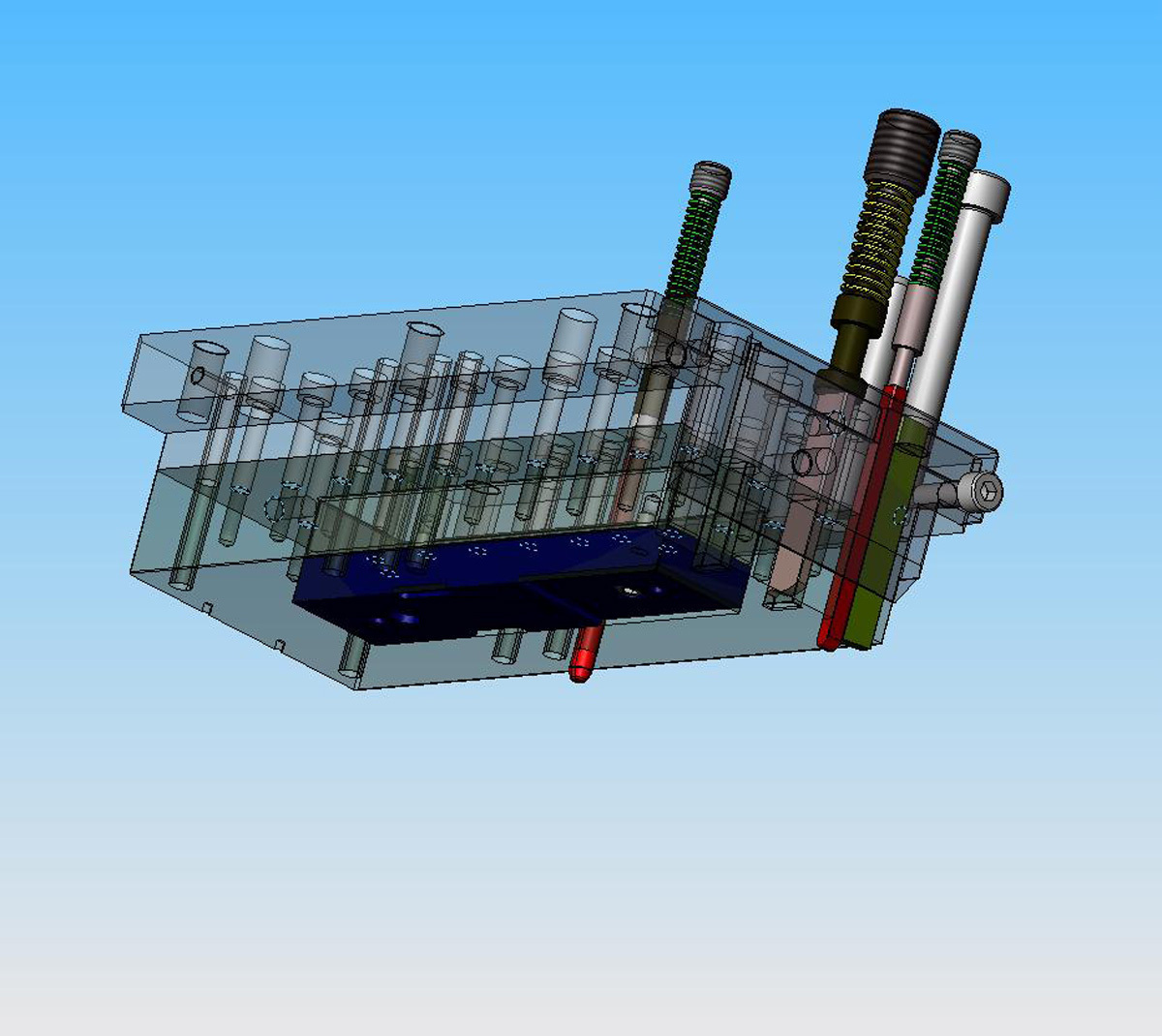
Фиг.6-65
на Фиг.6-66 (огъваща матрица),
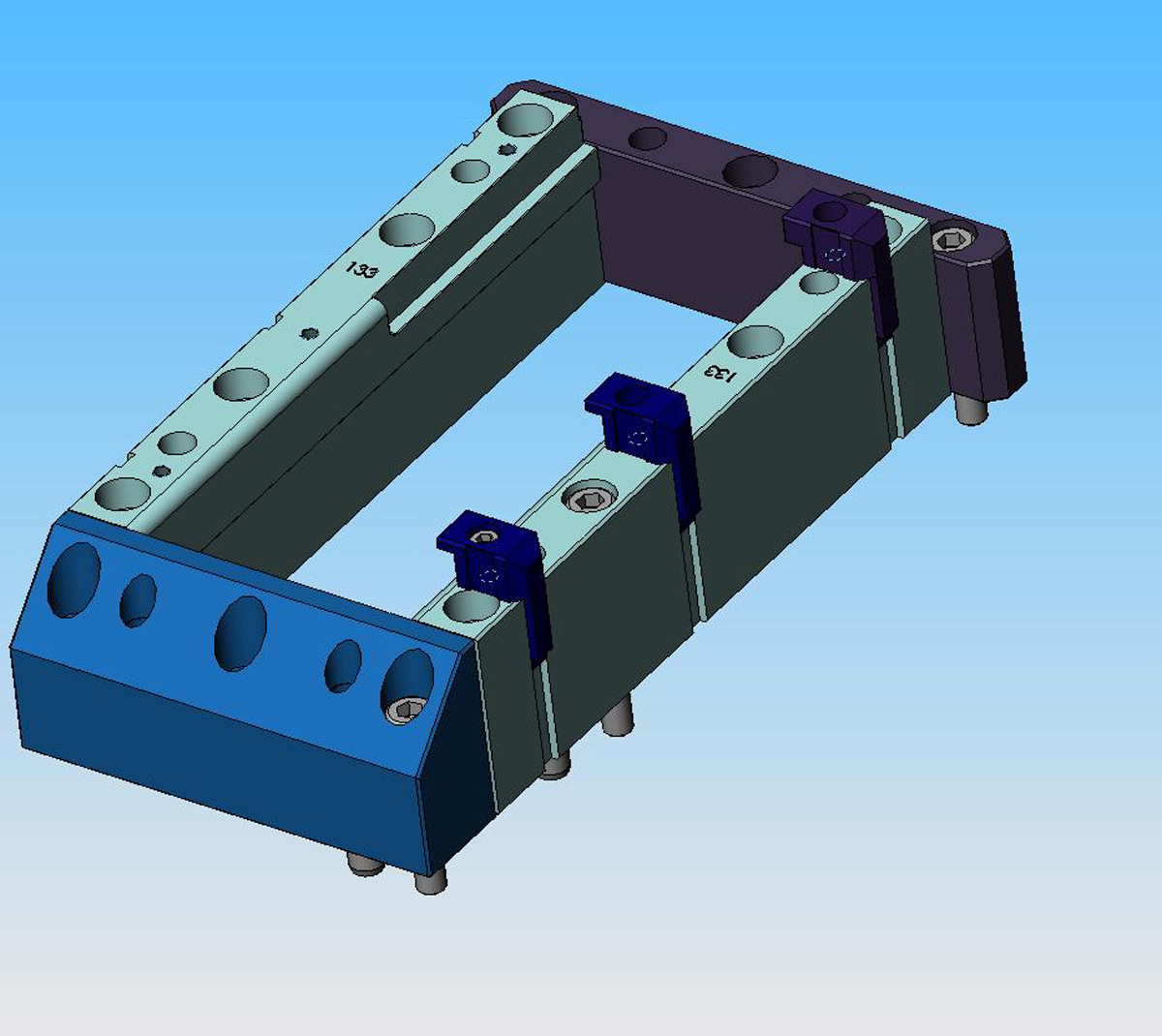
Фиг.6-66
на Фиг.6-67 (долен притискач).
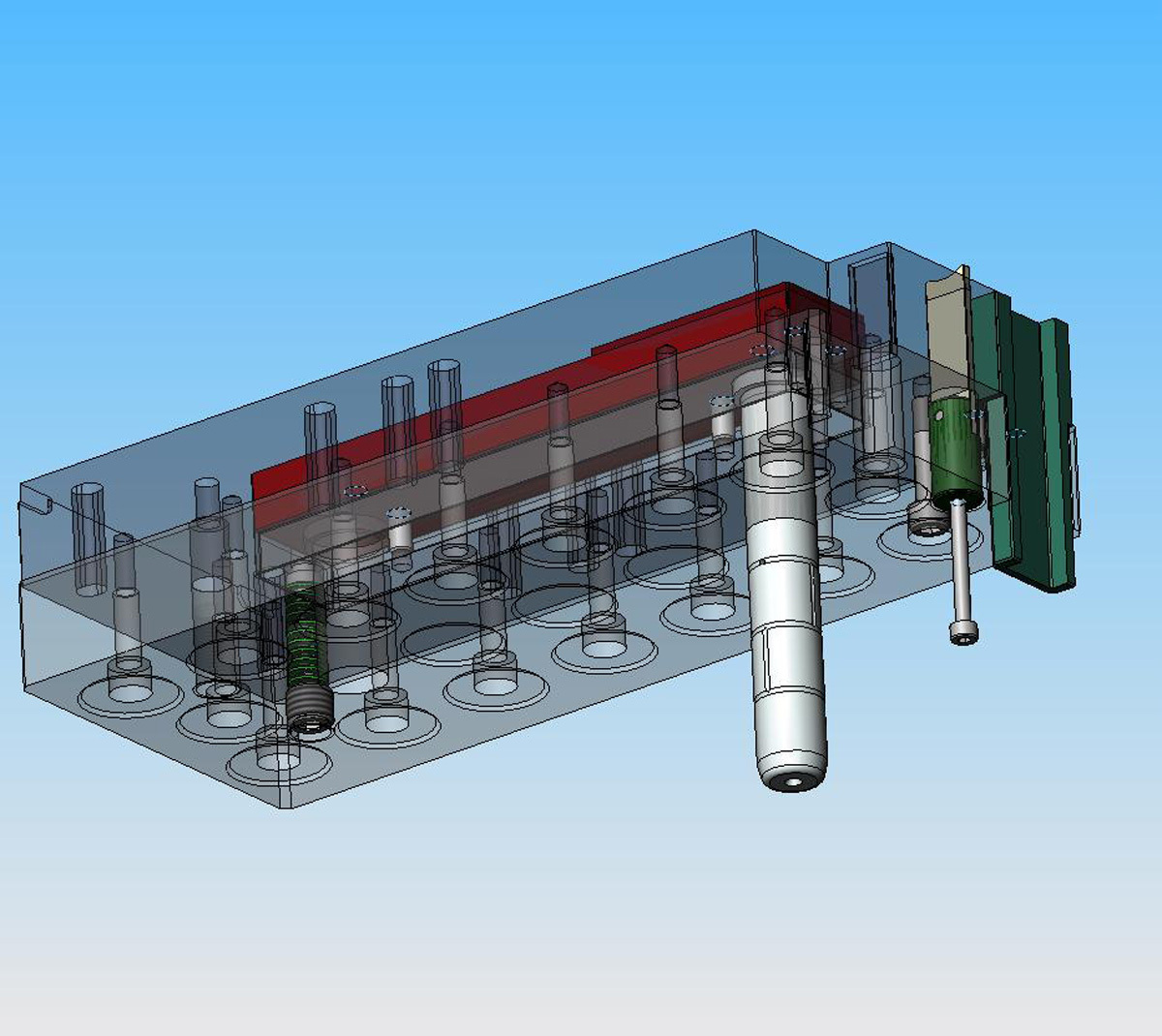
Фиг.6-67
Предназначена е за работа на 60 тонна ексцентър преса с автоматично подавяне на лента. Инструментът е съставен от огъващ пакет, включващ огъваща секционна матрица с гилотина, огъващ поансон с формоващи вложки, подпружинен долен притискач с формоващи вложки, и режещ модул, включващ основа с матрица, режещи поансони, неподвижен водач и поансонодържач. Лентата се центрова с подпружинени ловители, разположени в огъващия поансон. Пренастройката за всяка модификация на детайла се състои в преместване на режещия модул в необходимото положение спрямо гилотината в края на щанцата и подмяна на ловител и формоващи вложки в огъващия поансон и долния притискач. Подвижния и неподвижния пакет на щанцата се водят с колонки и втулки с триене при търкаляне чрез сачмени сепаратори.
5. Щанци с последователо действие с металокерамични твърдосплавни активни части.
Сериозен проблем при разделителните операции за някои метали е бързото износване на режещите матрици и поансони. Затъпяването на режещите ръбове предизвиква лощо качество на срязаните повърхнини и чепаци, което за някои изделия е недопустимо – на пример за роторни и статорни пластини на електромотори и ламели за дросели или трансформатори. Те се подреждат в пакети от десетки или стотици пластини и изискват успоредност между тях, която наличието на чепаци влошава. Възникналото противоречие между бързо износващите се режещи ръбове на матриците и поансоните при щанцоване на силициева ламарина и големия брой детайли в едно изделие, е решено чрез прилагане на нов вид материал за активните части – металокерамични твърди сплави на основа на волфрамов карбид с кобалтова свръзка. Посочените детайли (ротор-статорни и трансфотматорни пластини) са типичен пример за масово производство (годишно количество от 5 000 000 до 100 000 000 броя), където прилагането на металокерамичи твърдосплавни активни части е ефективно (една такава щанца замества до 10 обикновенни). Техните основни предимства са висока якост на натиск и изключителна износоустйчивост, надхвърляща 20-50 пъти тази на високо легираните инструментални стомани. Обаче, тези активни части имат сериозни недостатъци – крехкост и ниска якост на огъване, затруднена обработваемост и висока цена. Съчетаването на предимствата и недостатъците е намерило отражение в конструкциите на щанците – високата износоустойчивост е за сметка на усложнени, трудоемки и скъпи инструменти с повишена коравина на конструкцията и водещите елементи, със специални изисквания към пресите, на които ще се работят. Експлоатацията на такива инструменти, които за по-кратко ще бъдат наречени твърдосплавни щанци, е сериозно предизвикателство към квалификацията на поддържащия персонал и състоянието на инструменталното стопанство. Ленти от твърдосплавни щанци и самите трансформаторни и ротор-статорни пластини, са показани на Фиг.3-3 и Фиг.6-68.
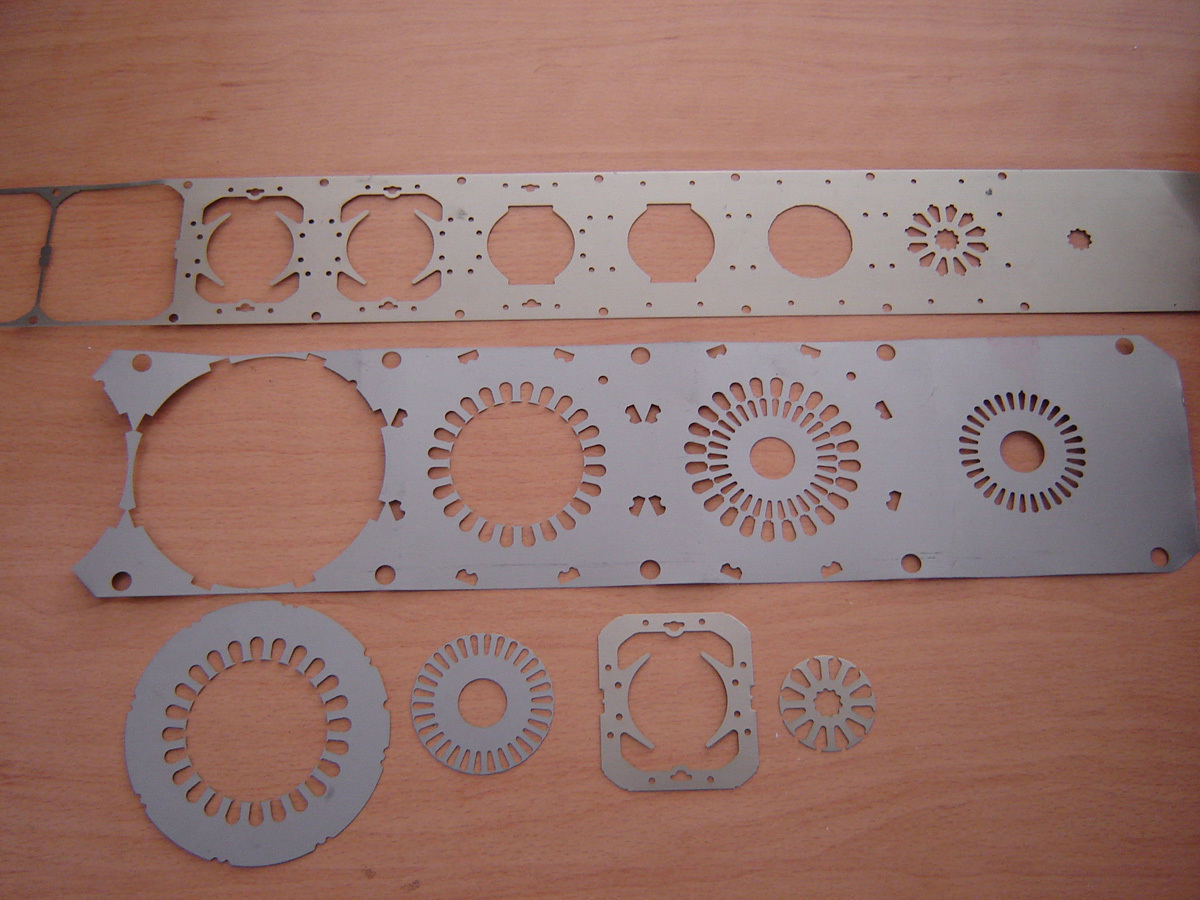
Фиг.6-68
– Твърдосплавна щанца с последователно действие за пробиване, изрязване и отрязване на детайли „Е“ и „I“ ПЛАСТИНИ ЗА ДРОСЕЛ е показана на Фиг.6-69 (общ вид),
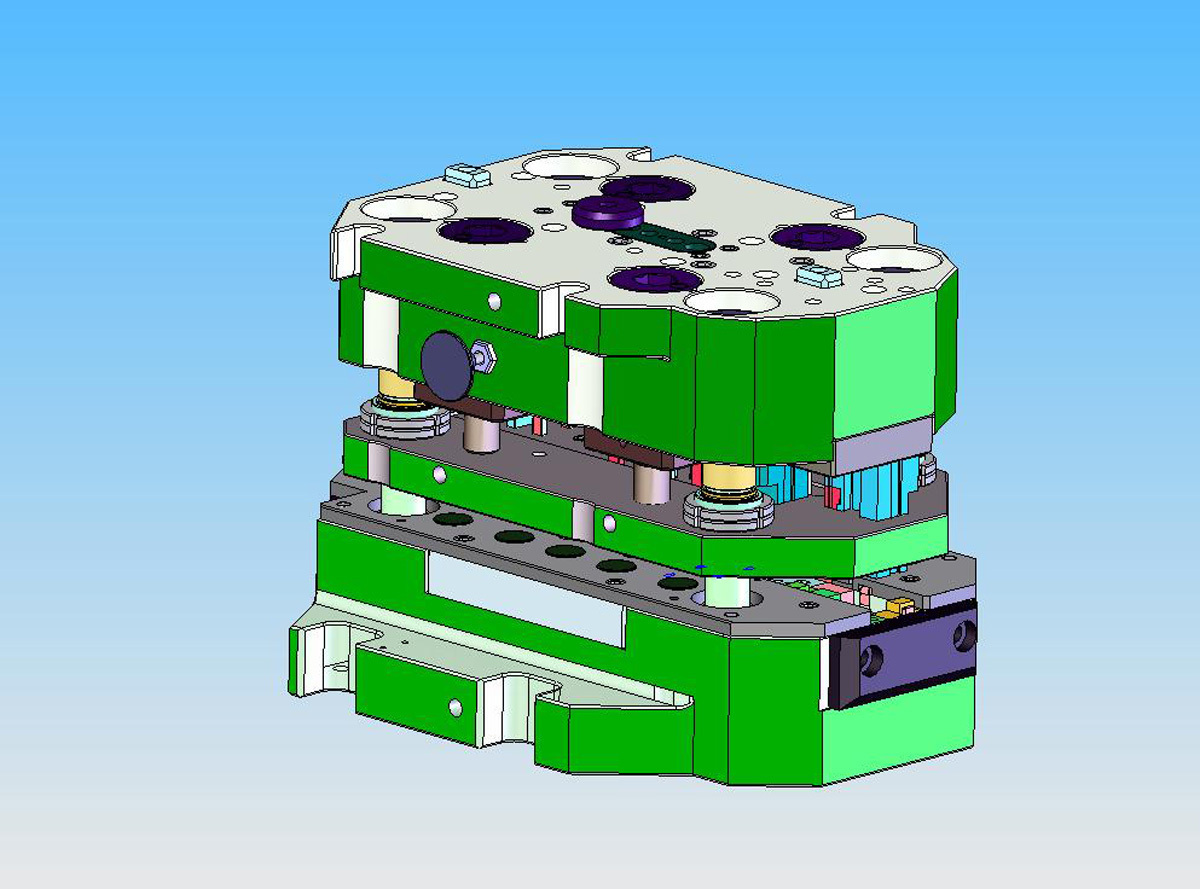
Фиг.6-69
на Фиг.6-70 (подвижен пакет),
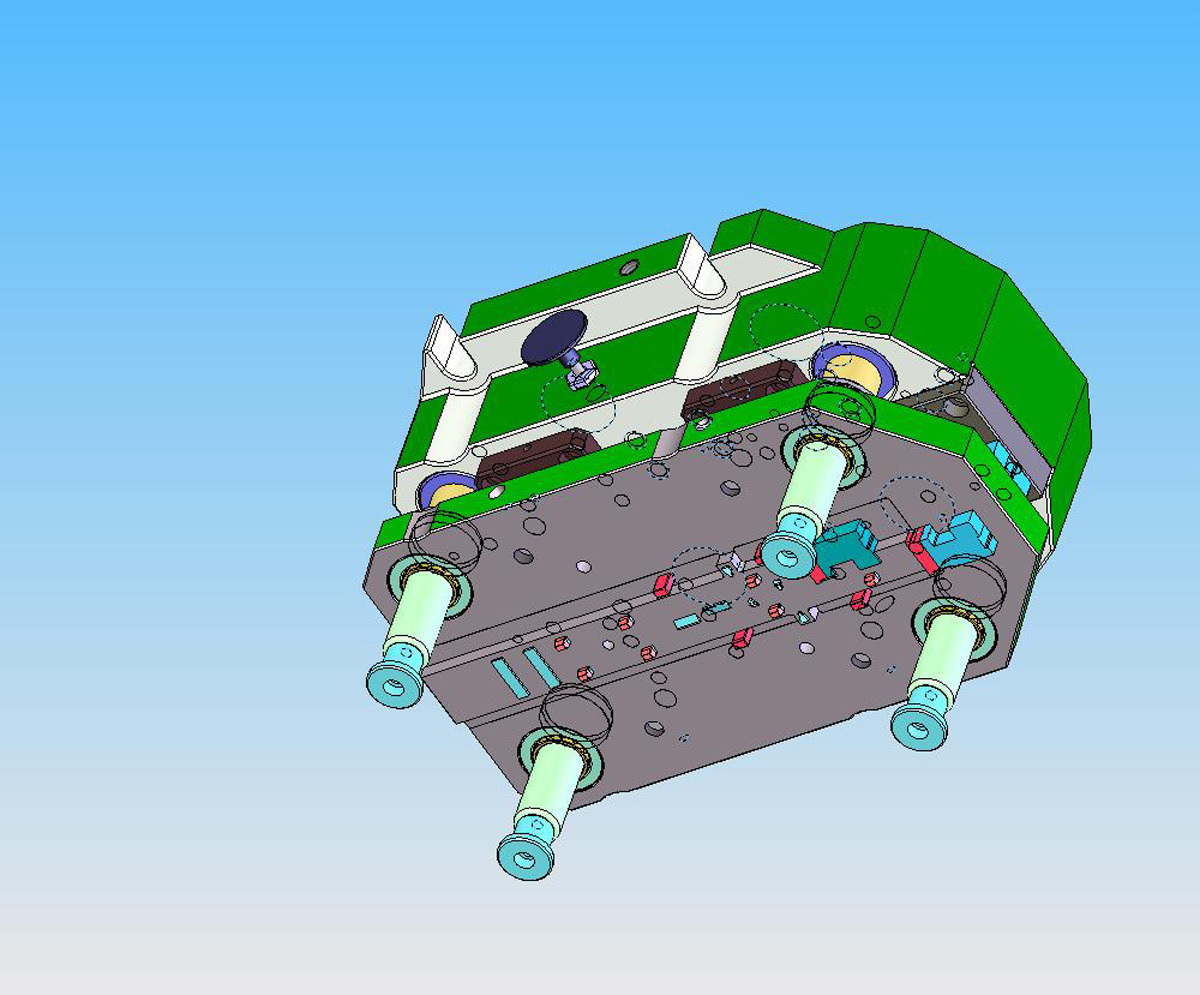
Фиг.6-70
на Фиг.6-71 (твърдосплавни режещи поансони в поансонодържача)
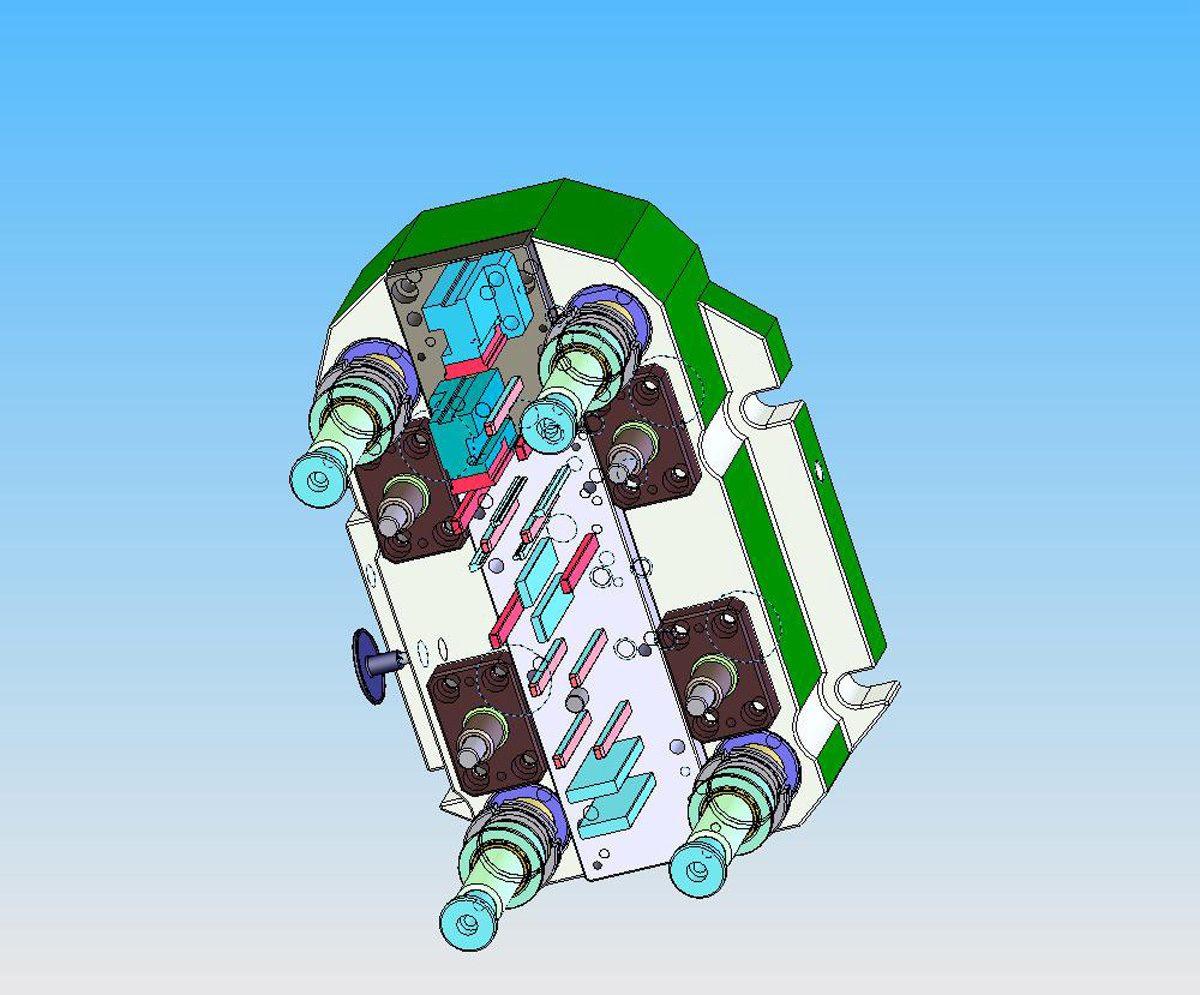
Фиг.6-71
и на Фиг.6-72 (схема на лента).
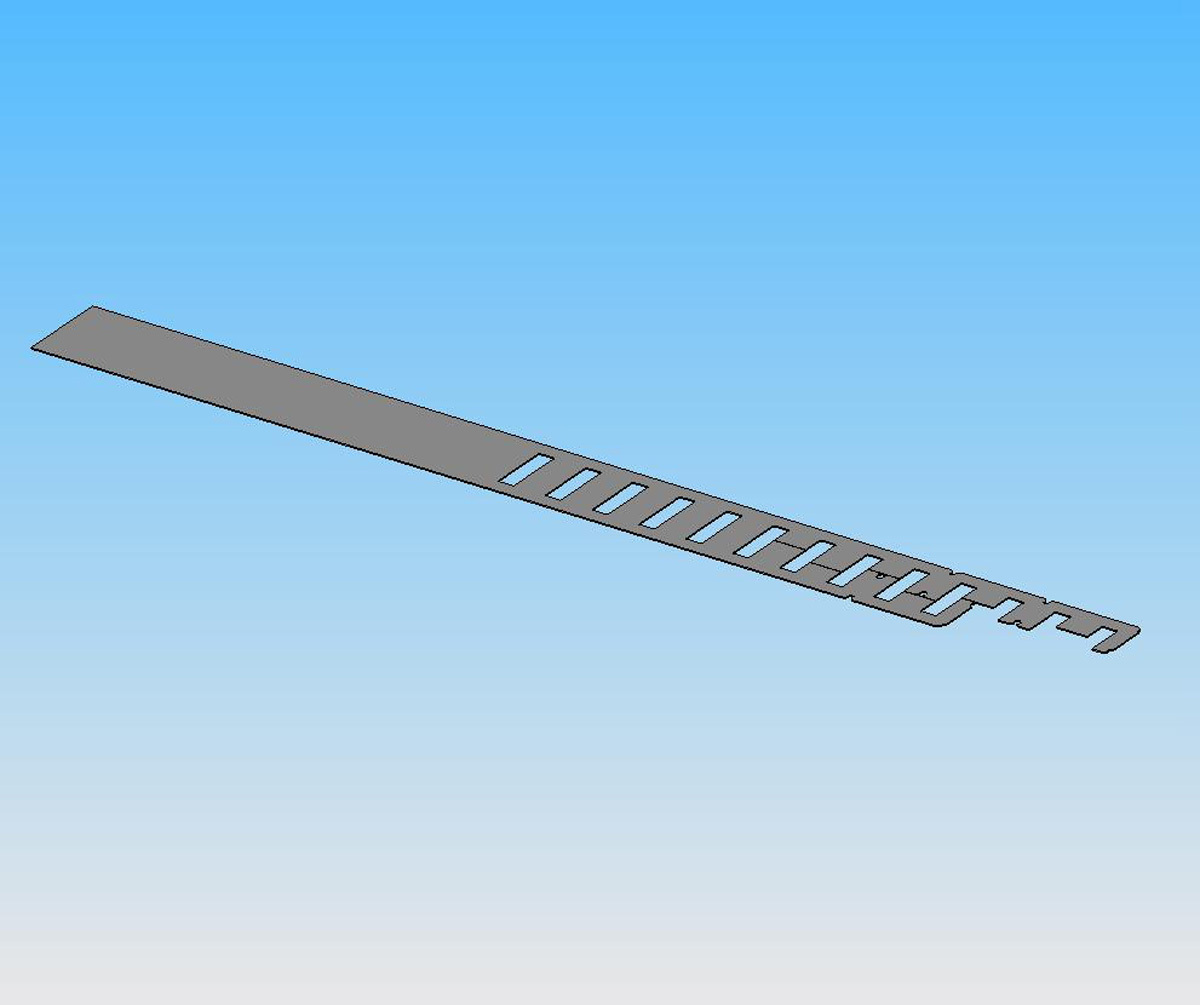
Фиг.6-72
Предназначена е за работа на бързоходна ексцентър преса RASTER-15 тонна с автоматично подаване на лентата. Твърдосплавната щанца се състои от стоманен матрицодържач с вградени твърдосплавни режещи вложки и твърдосплавни поансони със запоени глави, разположени в поансонодържач. Събуването на лентата и воденето на поансоните се извършва от притискач, вграден в подпружинена водеща плоча. За повишаване на коравината, матрицодържачът и поансонодържачът са монтирани в канали на долна и горна плочи. Лентата се води в армирани с твърдосплавни вложки лентоводачи и се центрова с твърдосплавни ловители. Има изключващ ловител за защита от грешка в стъпката на подаване. Изпълнената двуредна схема на щанцоване е с много висок коефициент на използване на материала – единствения отпадък са малките скосявания на „Е“ пластината. Воденето на подвижния спрямо неподвижния пакет се извършва с триене при търкаляне посредством четири комплекта от водещи колонки, втулки и сачмени сепаратори. За по-удобно обслужване, колонките са закрепени към горна плоча с конусна част – така бързо се снемат за съвместно заточване на поансоните, без друго разглобяване на подвижния пакет. Тази твърдосплавна щанца е с производителност над 500 удъра в минута (1000 пластини в минута). Щанцованите „I“ и „Е“ пластини се пакетират и отвеждат в специални ръкави (улеи), монирани под пресата. Щанцата е снабдена със специални спирачки, възпрепятстващи повдигането на отрязаните пластини в матрицата и гарантиращи плътното и паралелно подреждане в улеите.
По-нататъчното усъвършенстване от фирмата “Roos&Kübler” на подобен вид твърдосплавна щанца с последователно действие за пробиване, изрязване и отрязване на детайли „Е“ и „I“ ПЛАСТИНИ ЗА ДРОСЕЛ е показана на Фиг.6-73 (поглед от горе и надлъжен разрез).

Фиг.6-73
В тази конструкция подпружинената водеща плоча е заменена със събуваща плоча (поз.10), неподвижно закрепена при работа към матрицодържача (поз.11) с твърдосплавните режещи вложки. За лесно обслужване и почистване от отпадък при необходимост, събуващата плоча може да се повдига чрез лостово-гърбична система (поз.12) на 11-12 mm над матрицодържача. Твърдосплавните поансони (поз.1, поз.6, поз.7) се водят прецизно по отворите в поансонодържачите (поз.8, поз.9), като оставащата свободна работна дължина е много къса. Задържането на поансоните при събуване на лентата се извършва от сили на триене чрез свиване на еластични елементи (поз.3, поз,5) от винтове (поз.2, поз.4). Така, при откъртване на режещ ръб, бързо могат да се извадят и обърнат, без да е необходимо заточване. Воденето на подвижния спрямо неподвижния пакет се извършва с триене при търкаляне посредством четири комплекта от водещи колонки, втулки и ролкови сепаратори. За по-удобно обслужване, колонките са закрепени към долна плоча с конусна част – така бързо се снемат за съвместно заточване на вложките в матрицодържача след развиване на два винта за отделяне на събуващата плоча (поз.10). Поансоните с подвижния пакет се изваждат от колонките и са готови за съвместно заточване. Вследствие на описаните изменения, конструкцията е с по-висока коравина, по-лесна за обслужване и основното предимство – отсъствието на водене и триене на поансоните в подпружиненана водеща плоча, е позволило увеличаване на производителност над 700-800 удъра в минута (1600 пластини в минута).
– Едноредна твърдосплавна щанца с последователно действие за пробиване и изрязване детайли „ЛИСТ РОТОРЕН“ и „ЛИСТ СТАТОРЕН“ ЗА ЕЛЕКТРОДВИГАТЕЛ е показана на Фиг.6-74 (поглед отгоре), на Фиг.6-75 (надлъжен разрез А-А), на Фиг.6-76 (напречен разрез В-В), на Фиг.6-77 (напречен разрез С-С), на Фиг.5-10 (схема на лента) и на Фиг.6-78 (спецификация).
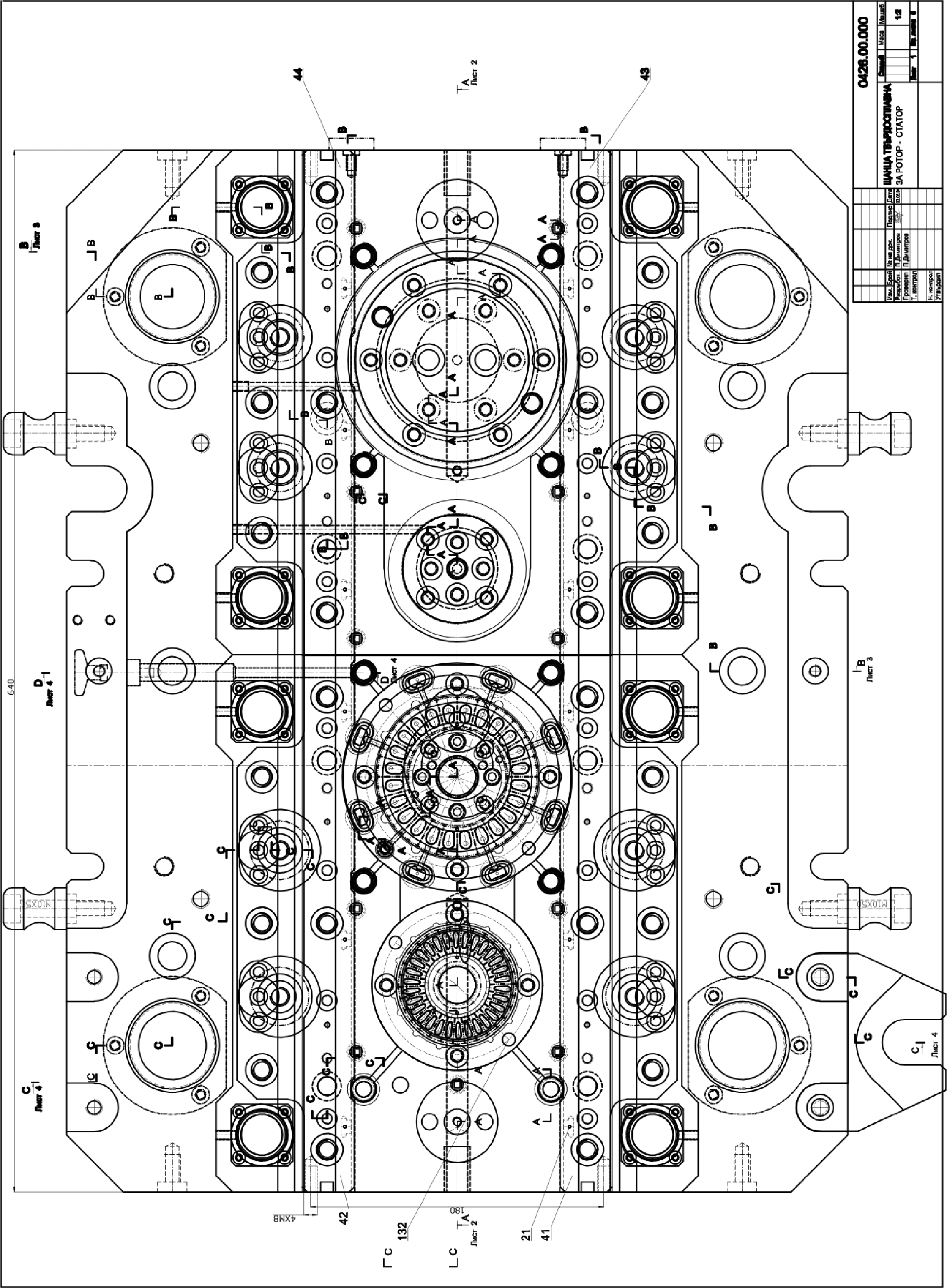
Фиг.6-74
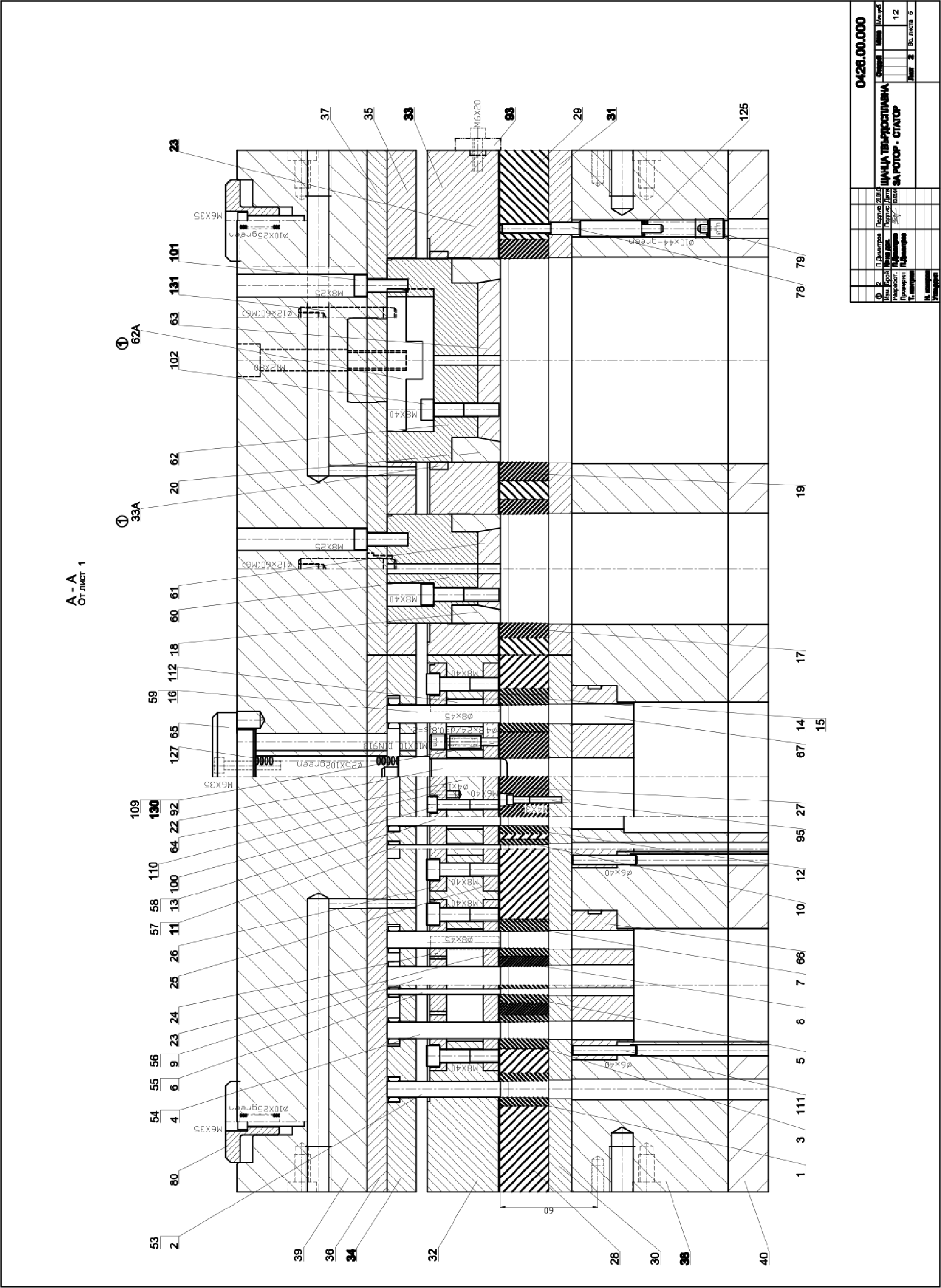
Фиг.6-75
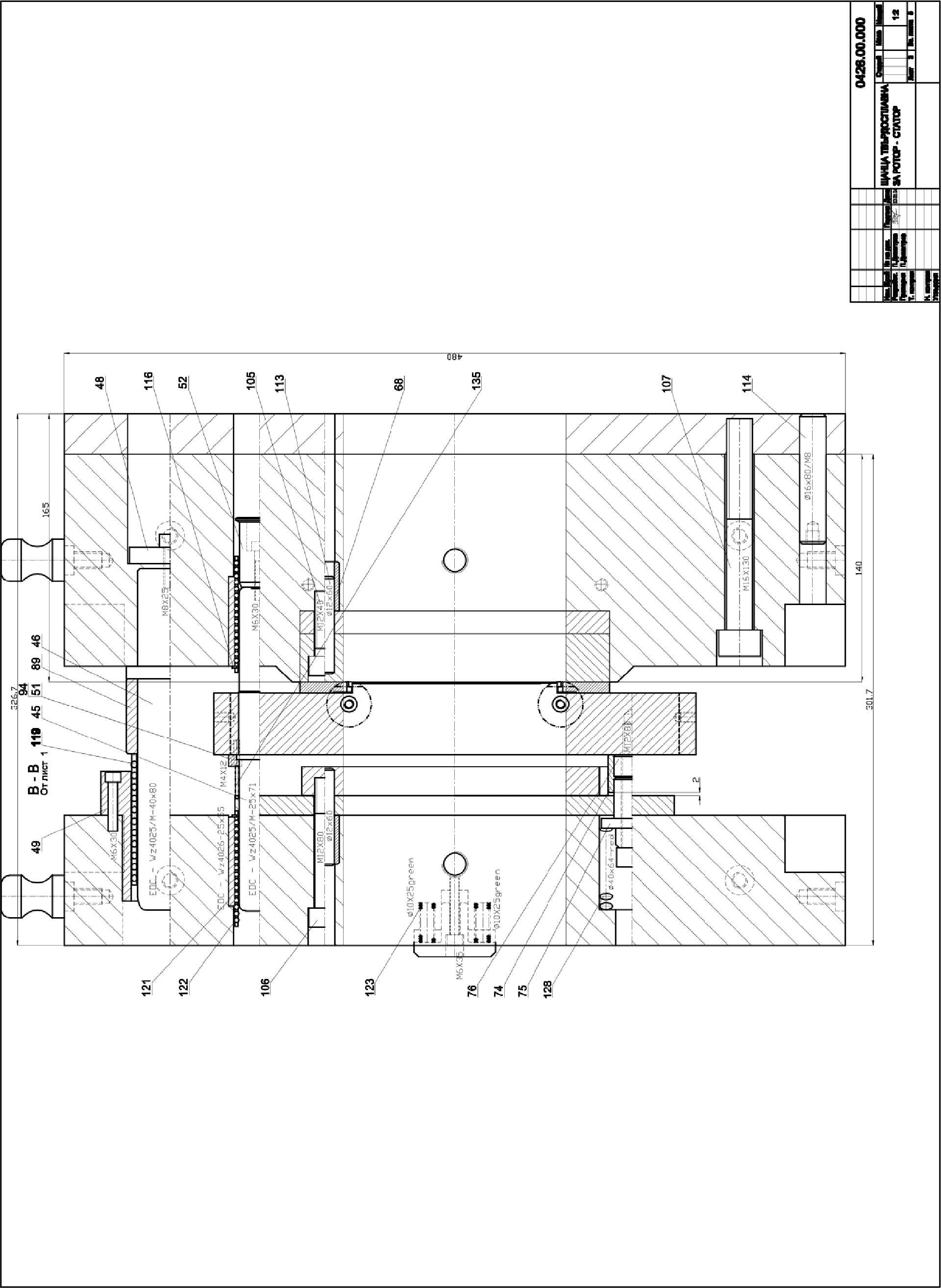
Фиг.6-76
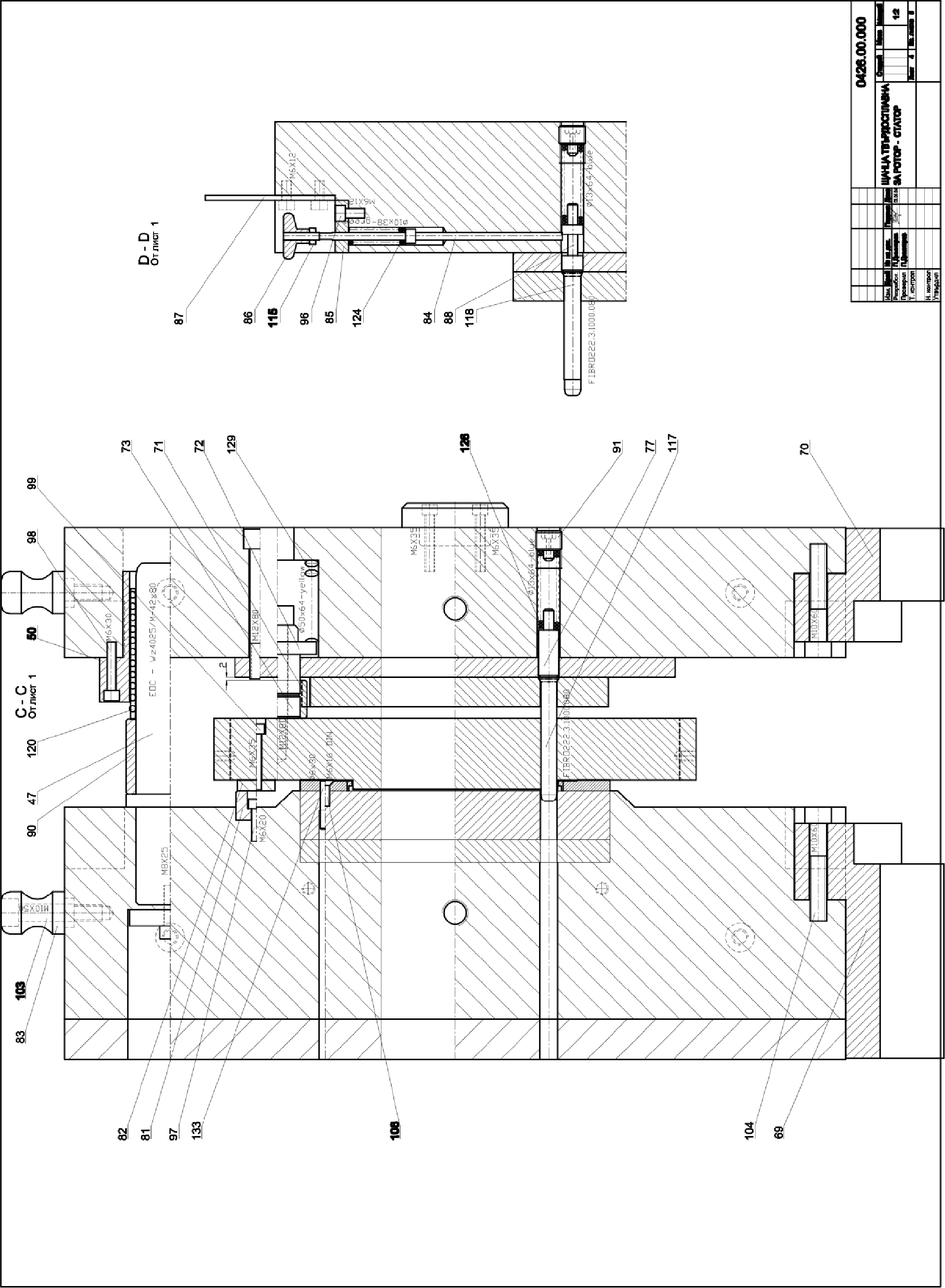
Фиг.6-77
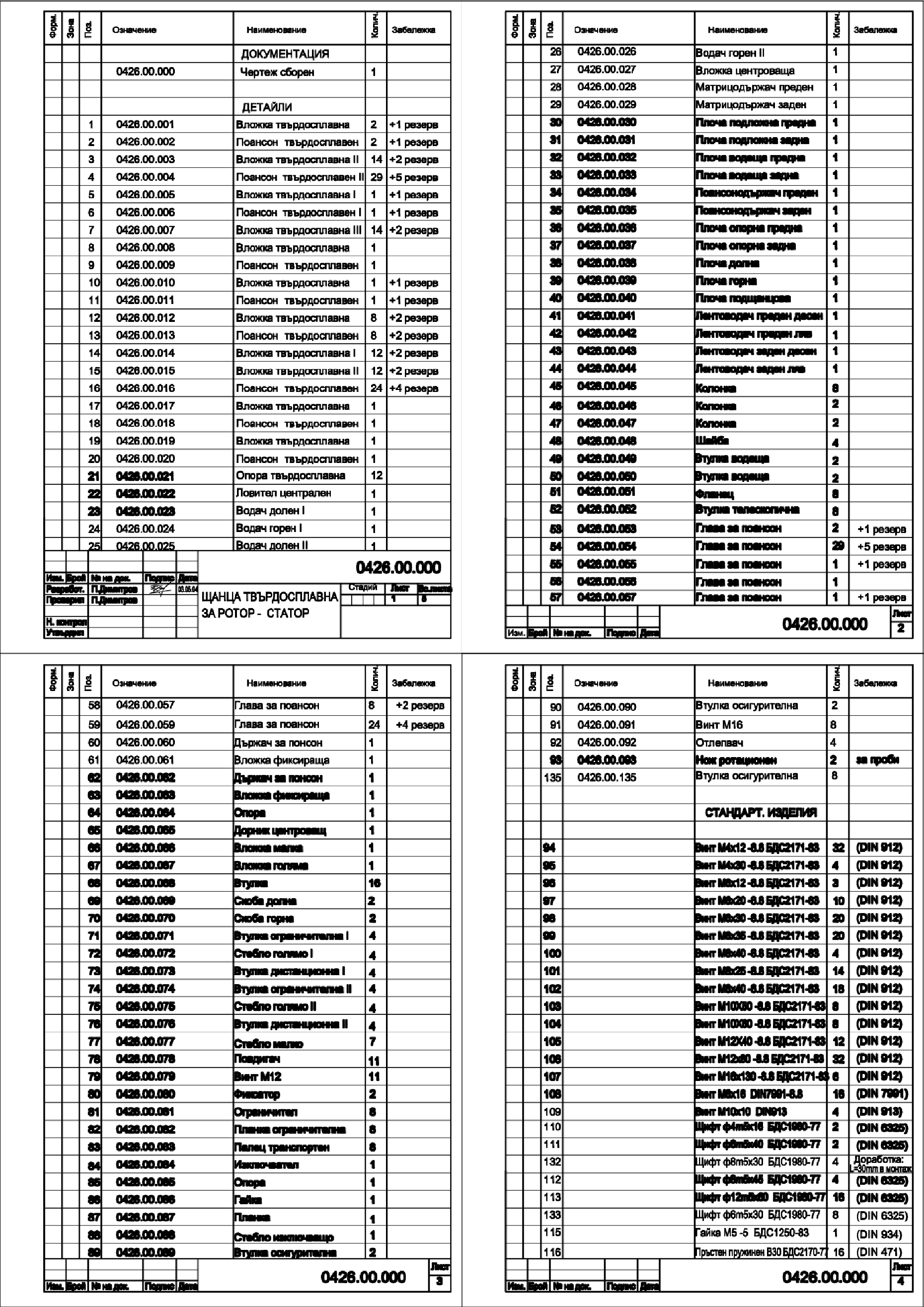
Фиг.6-78
Предназначена е за работа на ексцентър преса тип SCHULER-200 тонна с автоматично подаване на лентата и гилотина за нарязвяне на отпадъка. Щанцата се състои от преден и заден матрицодържачи (поз.28, поз.29) с вградени в тях твърдосплавни режещи вложки (поз.1, поз.3, поз.5, поз.7, поз.8, поз.10, поз.12, оз.14, поз.15, поз.17, поз.19), преден и заден комплект поансонодържачи (поз.34, поз.35) с твърдосплавни поансони (поз.2, поз.4, поз.6, поз.9, поз.11, поз.13, поз.16, поз.18, поз.20), предна и задна водещи плочи (поз.32, поз.33) с монтирани в тях две двойки водачи за пробиващите поансони за роторните и статорните канали (поз.23, поз.24, поз.25, поз.26). Твърдосплавните поансони се задържат в поансонодържачите със запоени стоманени глави, като за икономия на твърда металокерамична сплав по-големите (поз.18, поз.20) са изработени съставни и са механично закрепени към стоманени държачи (поз.60, поз.62). Така обособените предни и задни комплекти от части се водят в горна и долна плочи чрез допълнителни вътрешни колонки (поз.45), монтирани във водещите плочи, посредством втулки и сачмени сепаратори (поз.121, поз.122). Долната и горна плочи на блока (поз.38, поз.39) имат собствено водене – колонки (поз.46, поз.47), втулки (поз.49, поз.50) и сачмени сепаратори (поз.119, поз.120). Разделената конструкция и допълнителното водене е улеснило изработката, поддръжката при експлоатация и е увеличила коравината на щанцата. Лентата се води в лентоводачи (поз.41, поз.42), армирани с твърдосплавни вложки (поз.21) и се центрова с подпружиненени ловители (поз.117). Щанцата е защитена от грешно подаване на стъпка чрез изключващ ловител (поз.118). В горната плоча (поз.39) и предна водеща плоча (поз.32) има отвори и кухини за смазване на поансоните. Съставните твърдосплавни поансони се центроват към горната плоча на щанцата и имат хлабина във водещата плоча, за да се избегне възможността им за задиране. Роторните и статорните листове се пакетират и отделят в специални улеи под пресата. Производителността на щанцата е около 250 детайла от всеки вид за минута.
Известни са конструкции на твърдосплавни щанци, които извършват в процеса на изрязване на роторен и статорнен лист ъглово завъртане на всеки лист спрямо предходния и заключване с помоща на специални профили и канали. Чрез вграден брояч и изключващ механизъм, те позволяват производство направо на готовите роторни и статорни пакети. Естествено, цената на такива твърдосплавни щанци е много висока, а не винаги плътността на роторния пакет е такава, че да гарантира безпроблемното му динамично балансиране.
6. Едно операионни щанци за неметален листов материал.
Детайлите от неметален материал се изработват чрез различни от щанцоване процеси. Някои от тези детайли обаче, се получават от текстолитови, гетинаксови, полистиролни, стъклопластови, картонени и други материали, под форма на лист. За тяхната изработка се използват щанци за пробиване и отсичане. Основна особеност при тези видове инструменти е необходимост от притискане, съчетано с почти нулева хлабина между матрица и поансон. По долу ще бъдат разгледани
различни от показаните в [1], [2] и [3] инструменти, които са много близки по конструкция до обработващите метални листи (при спазване на посочените по-горе особености). Щанците за пробиване и отсичане са част от технологична линия за вакумно формоване и са разположени след пресформа, вакумно формоваща листа. Задвижват се от специални вертикална (за пробиване) и хоризонтална (за отсичане) преси в линията.
– Щанца за пробиване на радиални отвори в детайл ‘САКСИЯ ЗА РАЗСАД” е показана на Фиг.6-79 (общ вид)
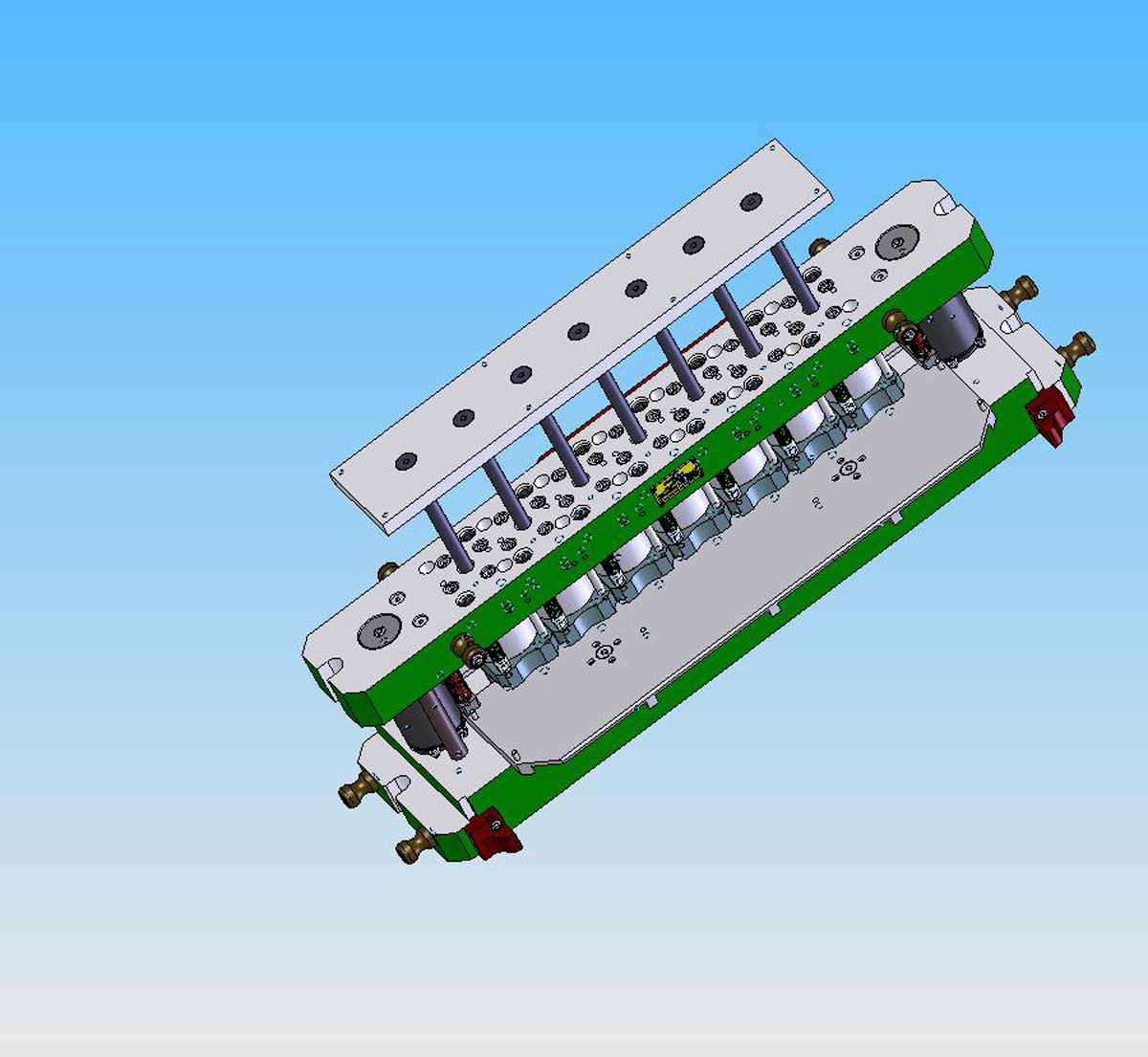
Фиг.6-79
и на Фиг.6-80 (схема на лента с пробивани саксии).
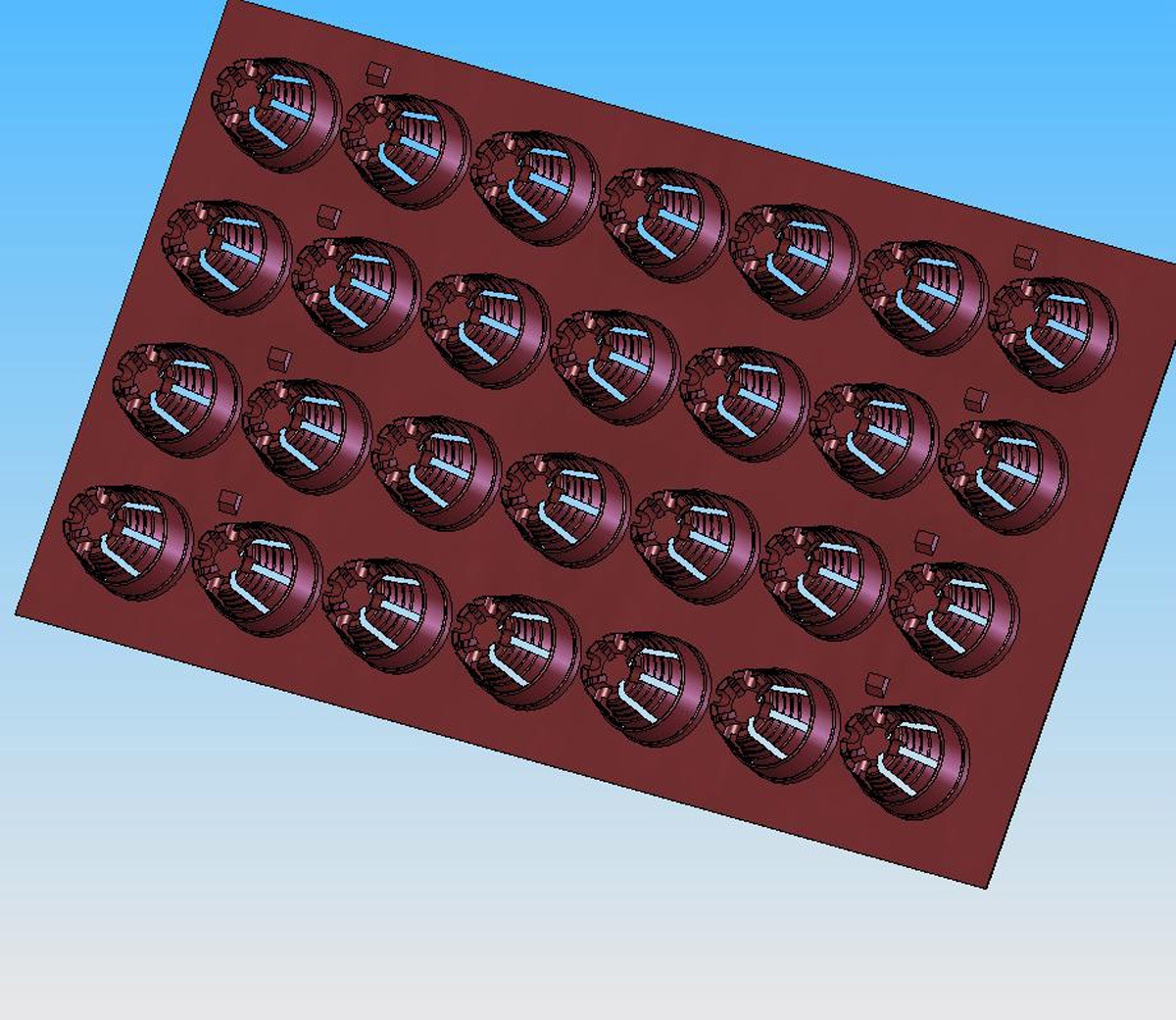
Фиг.6-80
Тя се състои от блок и седем пробиващи модула - Фиг.6-81 (общ вид).
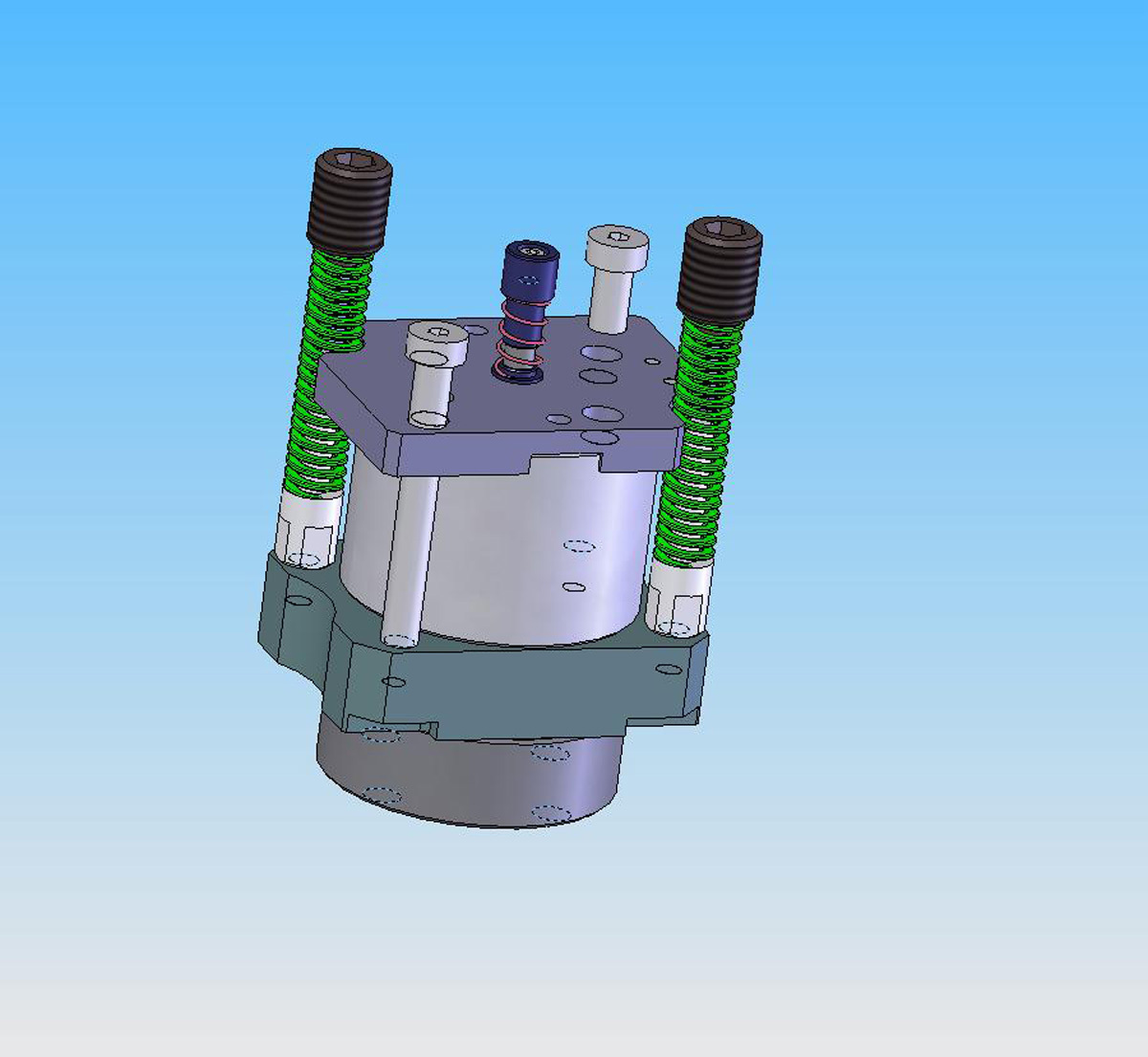
Фиг.6-81
Всеки модул е съставен от профилна матрица, специално заточени поансони, раположени в профилен поансонодържач и подпружинен притискач - Фиг.6-82.
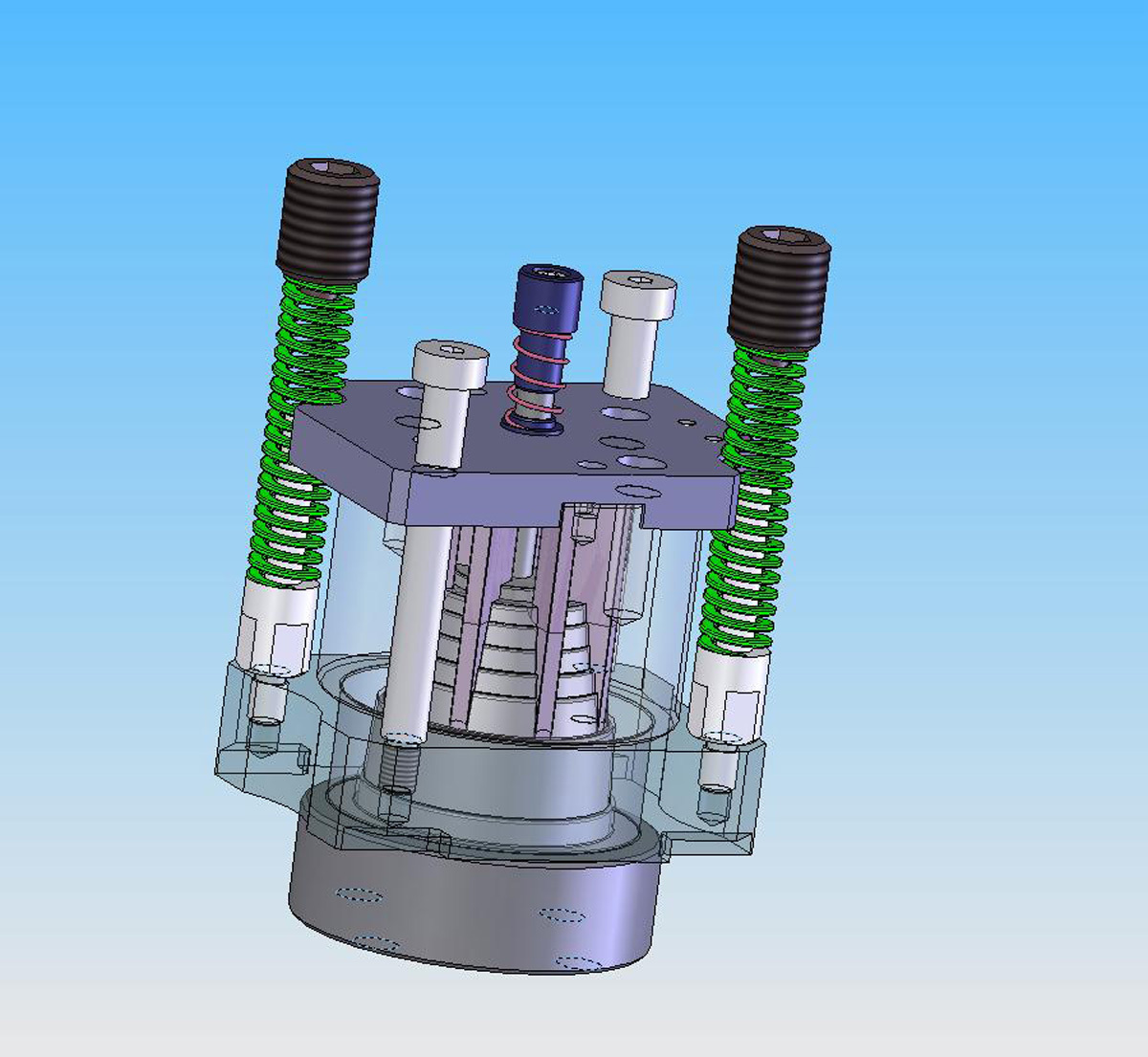
Фиг.6-82
Профилната матрица на всеки модул се фиксира към неподвижния пакет на щанцата, а поансоните в поансонодържача с подпружинен притискач се настройват спрямо нея и затягат към подвижния пакет. Лентата със саксиите се центрова чрез конусните профили на матрицата и поансонодържача и се пробива по редове с по 7 броя за ход. Воденето на подвижния спрямо неподвижния пакет се извършва с триене при търкаляне посредством водещи колонки, втулки и сачмени сепаратори.
– Щанца за отсичане на детайл ‘САКСИЯ ЗА РАЗСАД” е показана на Фиг.6-83 (общ вид)
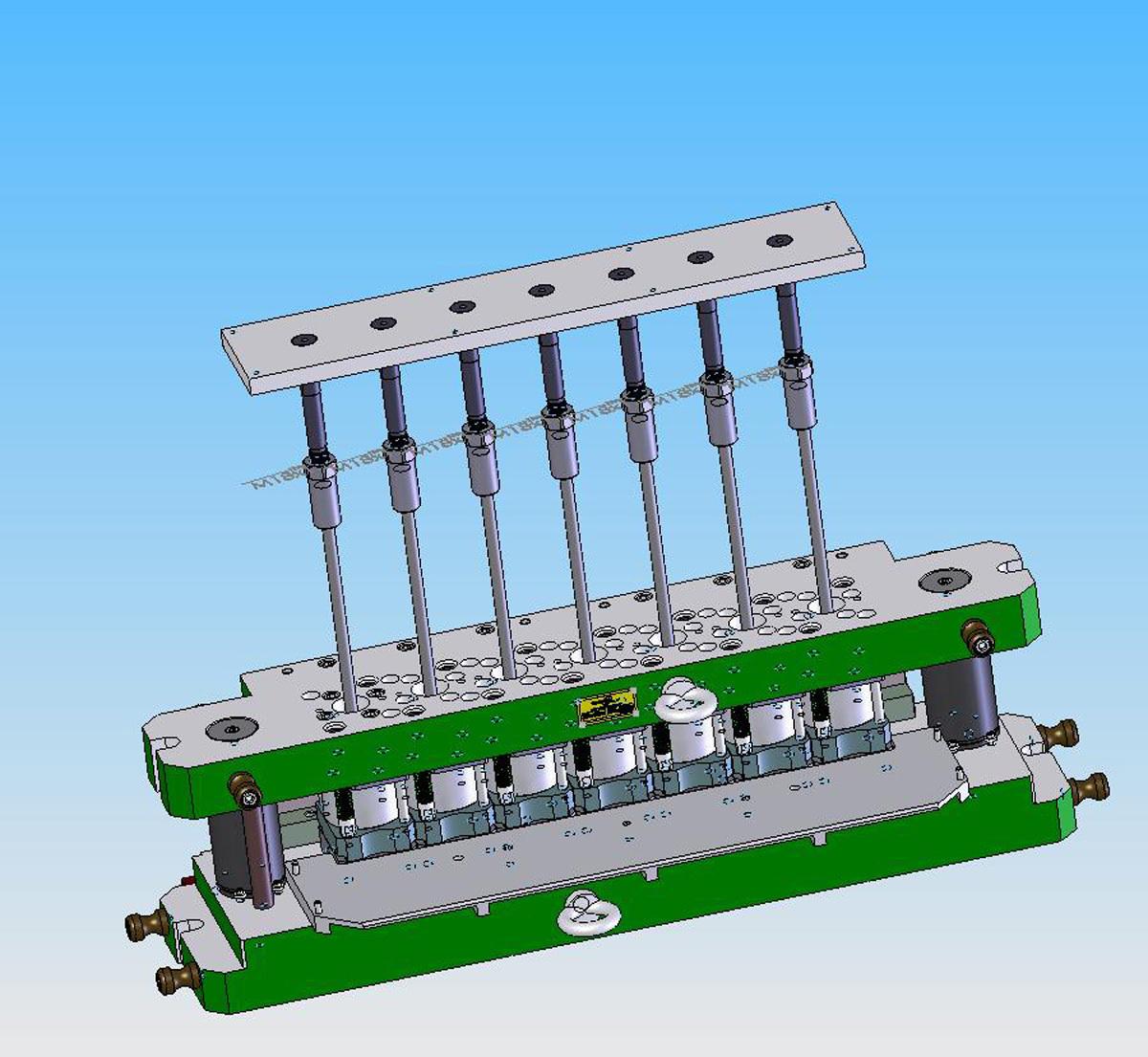
Фиг.6-83
и на Фиг.6-84 (отсечена саксия).
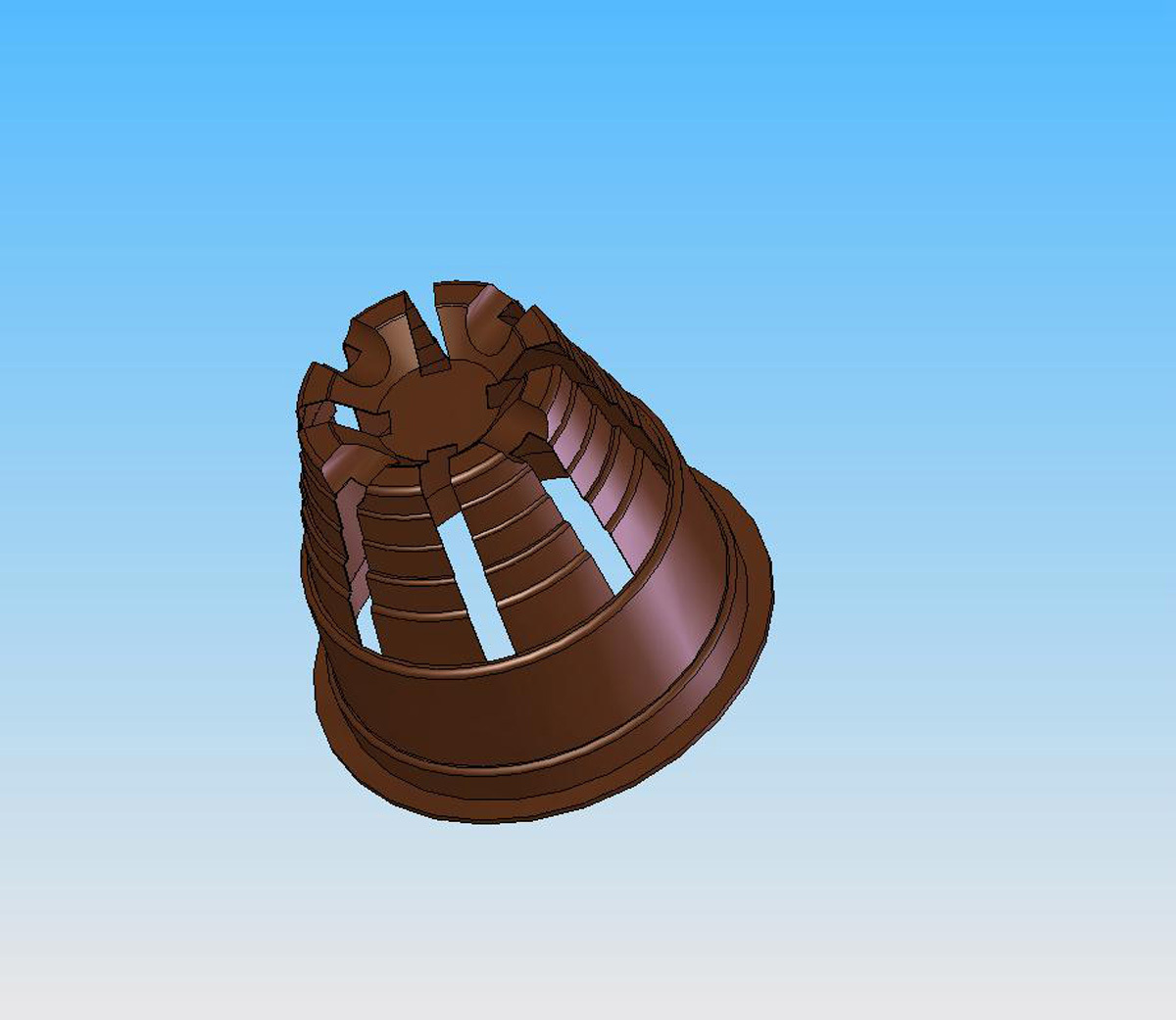
Фиг.6-84
Тя се състои от блок, седем отсичащи модула Фиг.6-86 (общ вид),
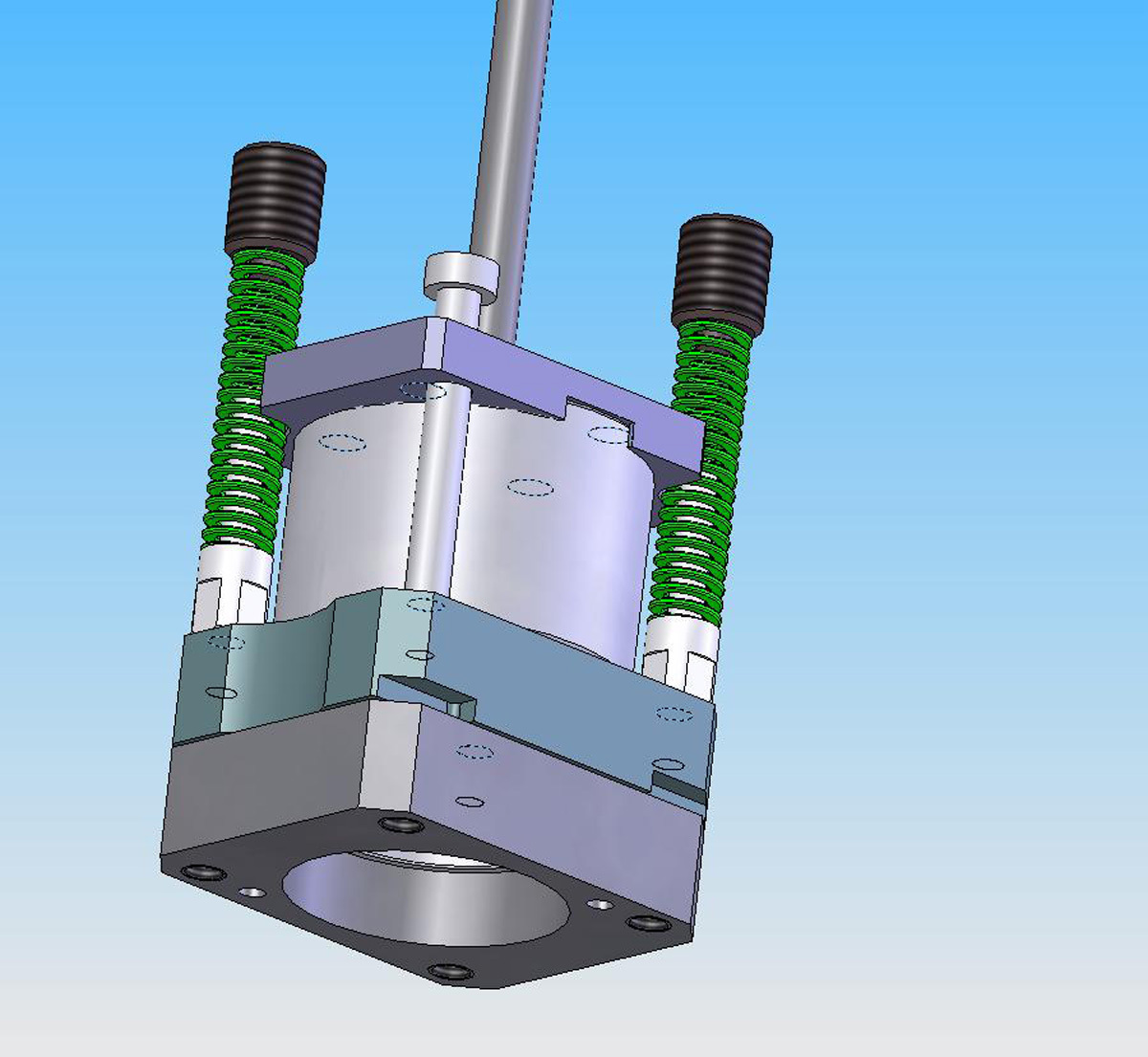
Фиг.6-86
гилотинни поансони и вложки Фиг.6-85
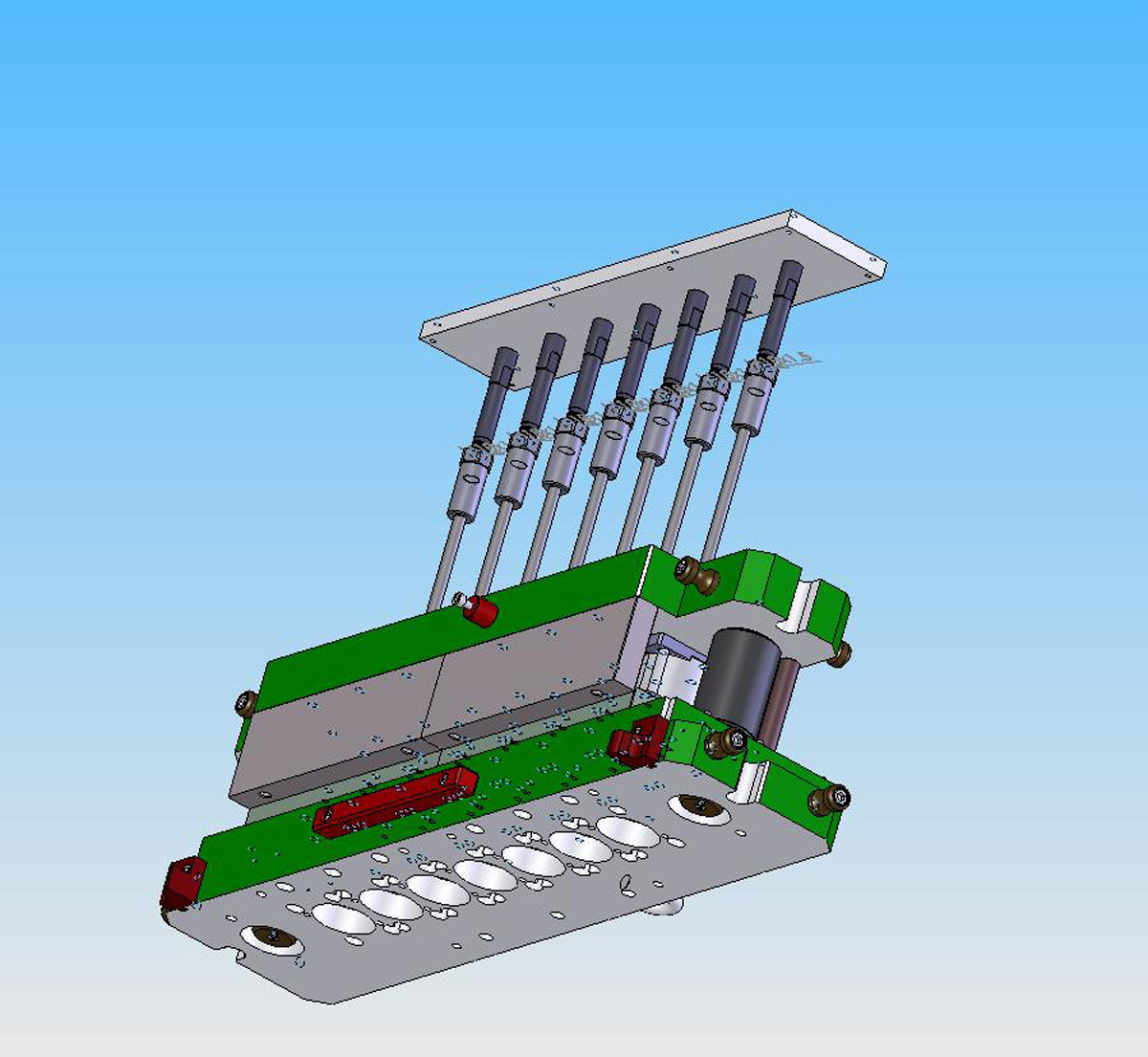
Фиг.6-85
и избутваща система, задвижвана пневматично от хоризонтална преса. Всеки отсичащ модул е съставен от отсичаща матрица, отсичащ поансон и подпружинен притискач - Фиг.6-86.
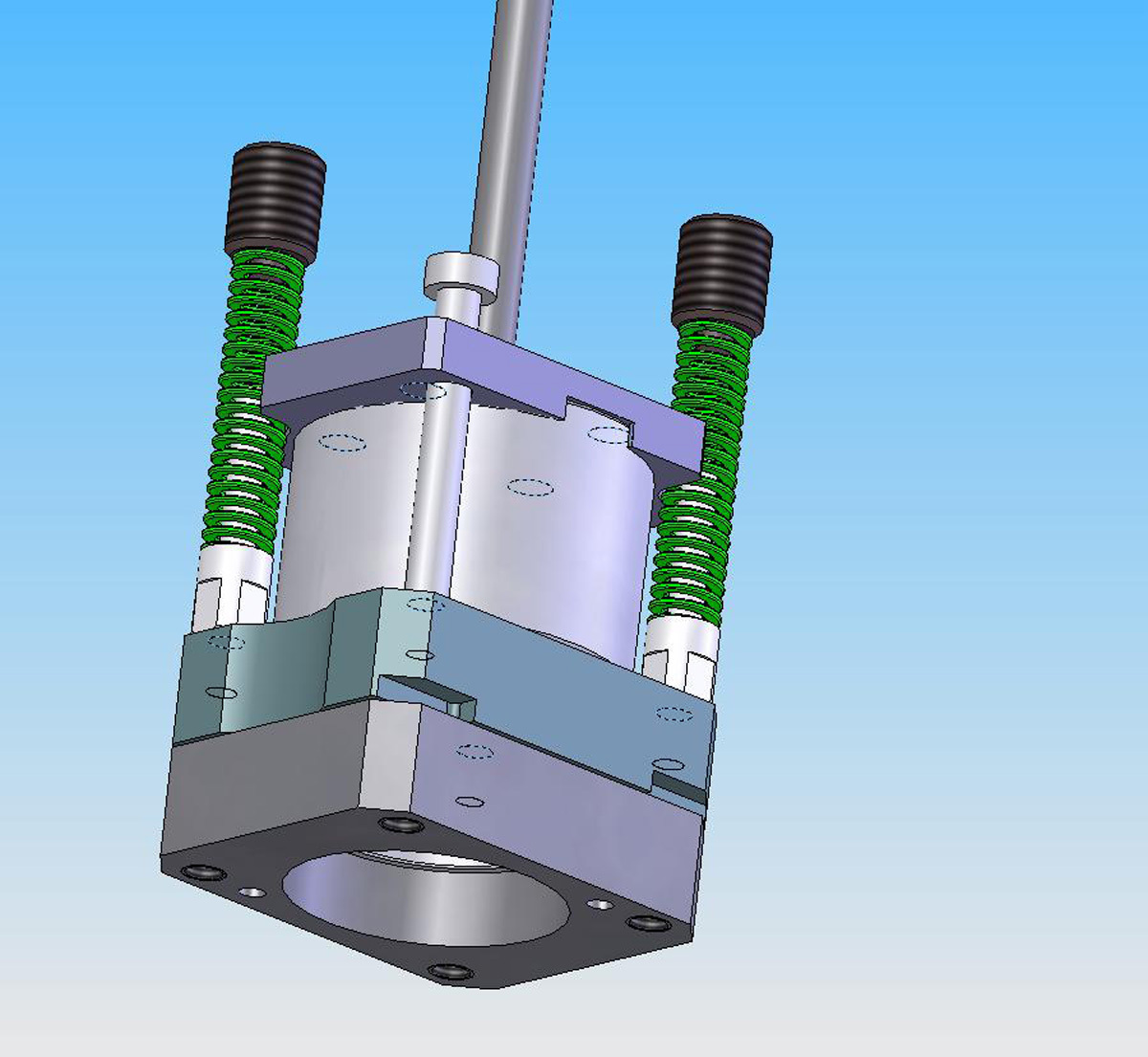
Фиг.6-86
Отсичащата матрица на модулите се фиксира към неподвижния пакет на щанцата, а поансона с подпружинен притискач се настройва спрямо нея и затяга към подвижния пакет. Лентата със саксиите се центрова чрез конусните профили на отсичащите поансони и от всеки ред се отсичат по седем броя за ход, а отпадъка се нарязва с гилотините поансони. Отрязаните саксии се отделят през отвора на матрицата чрез избутващата система и се стифират в снопове с определена височина. Воденето на подвижния спрямо неподвижния пакет се извършва с триене при търкаляне посредством водещи колонки, втулки и сачмени сепаратори.
7. Щанци и приспособления за изработка на прототипни детайли и малки еднократни серии.
За много детайли от листов матал е необходимо изработка на прототипи, за да се провери тяхната работоспособност. За разлика от пластмасовите детайли, при тях не можа да се използва 3D принтер. Съществуват технологии (лазерно рязане, водно рязане, нишково електроерозийно рязане, рязане с ножици) за получаване на плоски разгънати заготовки от ламарина, без необходимост от изработка на специални инструменти. Получаването обаче, на 3D прототипи с формоизменени зони (огънати, изтеглени, отбортовани, формовани ребра и други части), без специално изработени приспособления, е невъзможно. В отделни случаи, годишните количества за някои детайли са толкова малки (не повече от няколко десетки), че е не изгодно да се проектират и изработват щанци. Разбира се, това се отнася за режещите инструменти, които могат да се заменят с други, макар и не толкова производителни технологии. За огънати, изтеглени, отбортовани или формовани зони са необходими упростени приспособления или щанци. Основния принцип тук е максимално опростяване и намаляване броя на необходимите активни части, за да се сведат до минимум разходите за инструменти. В идеалния случай те са поансон и матрица, по-рядко се добавя притискач или някаква вложка. Процесът се разбива на единични операции. Когато е възможно, формата на поансоните и матриците се изпълняват за две операции – от едната страна за първата, след обръщането им на 180º за втората. В много случаи, за сметка на известно усложнение на матриците и поанцоните, е възможно те да центроват заготовката или по между си без други части. От гледна точка на конструиране, прототипните инструменти са по-сложни от останалите, защото няма правила и изискват голямо въображение.
– За пример е показано прототипно приспособление за щанцоване на детайл ЩИПКА от неръждаема стомана на три операции - Фиг.6-87 (сборни чертежи, технологични схеми и спецификация).
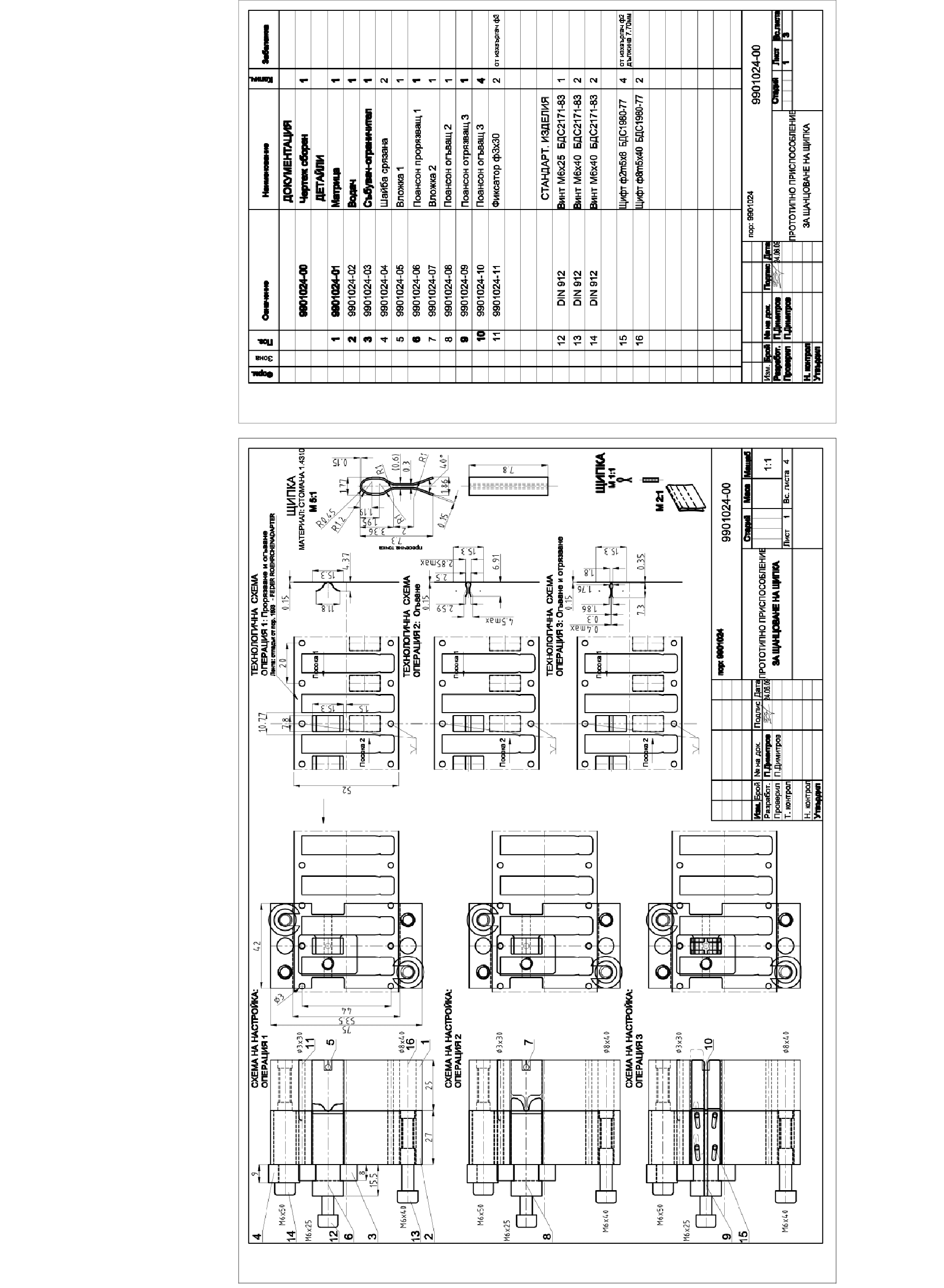
Фиг.6-87
В разглеждания случай, поради малките дебелина и размери, заедно със специфичната форма на детайла, са не приложими посочените по-горе технологии за получаване на плоска заготовка. Предварителната заготовка е просто лента с пробити на стъпка отвори за фиксиране. Останалите три операции – прорязване с огъване, второ огъване и окончателно огъване с отрязване, се изпълняват с едни и същи матрица, водач, срязана шайба и фиксатор (поз.1, поз.2, поз.3, поз.4, поз.11). Сменят се само поансони и вложки (поз.5, поз.6, поз.7, поз.8, поз.9, поз.10). Лентата се центрова с фиксатори (поз.11) по отворите и се затяга чрез срязани шайби и винтове (поз.4, поз.14). Последователно се обраборва с вложките и поансоните - първо поз.5, поз.6, после поз.7, поз.8, накрая поз.9, поз.10, след което винтовете се разхлабват, срязаните шайби и водача се издърпват и лентата се премества на следващата стъпка. По този метод безпроблемно се произвеждат ръчно 30-40 детайла за по-малко от два часа, с което се изпълнява цялото годишно количество.
В заключение, към описаните конструкции на инструментална екипировка за щанцоване остава да се спомене за още един тип конструкция, която няма да бъде разгледана. Това е екипировката за много супортни пренастроеваеми щанцо-огъващи автомати. Самата концепция на специализирания автомат позволява огромни възможности, включително изработка с монтаж на два или повече щанцовани детайла, завяряване и резбонарязване чрез специално разработени за тези операци модули. Екипировката обикновено се състои от огъващ център и режещ инструмет. Преди време към тези възли се добавяха и специално проектирани и изработени за конкретния процес гърбици, но последните разработки на BIHLER показват, че те успешно могат да се заменят с виско моментни електрозадвижвания, управляване с ЦПУ.
ГЛАВА 7. АКТИВНИ (РАБОТНИ) ЧАСТИ НА ЩАНЦИТЕ
Активни части на инструменти за обработка на листов материал се наричат поансоните, матриците, поансон-матриците и всички вложки, които при работа контактуват с щанцования материал и променят формата му в готов детайл. Те са от първостепенна важност, защото определят работоспособността и възможностите на щанците. Съществува огромно разнообразие от матрици, поансони и вложки, които могат да бъдат класифицирани и отделени в групи, според вида на изпълняваната от тях операция, конструктивните им особености (вид, работна част, закрепване) и използвания инструментален материал. При проектирането и изработката на активни части не бива да се проуска тяхната технологичност, удобство при експлоатация и хармоничното им вписване в конструкцията на щанцата.
1. Видове инструментални материали за изработка на активните части на щанците.
1.1. Високо въглеродни инструментални стомани.
Тези стомани съдържат въглерод над 0.7% и позволяват закаляване с твърдост до HRC 61. Имат сравнително ниска прокаляемост и склоност към образуване на пукнатини, поради което се използват за поансони и матрици с малки размери и проста форма. Типични представители на тази група са У8А и У10А. По износоустойчивост заемат най-ниската степен от всички инструментални материали.
1.2. Високо легирани инструментални стомани.
Високо легираните стомани съдържат въглерод над 1.5% и лигиращи метали – основно хром, никел, молибден, волфрам, ванадий. Те позволяват закаляване с твърдост до HRC 61 и се характеризират с по-висока жилавост и якост от високо въглеродните стомани. Имат сравнително добра прокаляемост и устйчивост към образуване на пукнатини, поради което се използват за поансони и матрици с по-големи размери и сложна форма. Типични представители на тази група са Х12 (1.2080), Х12МФ (1.2379) и 1.2436. Имат по-висока износоустойчивост от от високо въглеродните стомани. Стомана 1.2379 се отличава с вторичен пик на твърдостта при високо температурно отвръщане, което я прави подходяща за нанасяне на покрития oт TiN, TiC или карбонитриране, чрез които се увеличава повърхностната твърдост и износоустойчивостта.
1.3. Бързорезни инструментални стомани.
Тези стомани по своята същност са високо легирани сплави, получени по прахово металургичен път и съдържат волфрам и други легиращи елементи над 9%. Позволяват закаляване с твърдост до HRC 64 при специален режим на тройно охлаждане. Отличават се с висока якост, жилавост и топлоустойчивост, поради което се използват за високо натоварени поансони и матрици с малки размери и проста форма. Представители на тази група са Р9, Р6М5 (1.3343), VANADIS-4. Имат по-висока износоустойчивост и топлоустойчивост от високо легираните инструментални стомани. Подходящи са за нанасяне на повърхностни покрития oт TiN, TiC, TiСN, чрез които допълнително се увеличава износоустойчивостта.
1.4. Металокерамични волфрамово-карбидни твърди сплави.
Тези сплави съдържат волфрамов карбид от 8% до 15% и останалата част кобалт, осигуряващ свръзката между изключително твърдите кристали на волфрамовия карбид. Понякока съдържат малък процент карбиди на титан или тантал, но най- широко приложение в щанците за разделителни операции намират едно компонентните сплави на основа на волфрам. Достигат твърдост до HRА 91. Произвеждат се с различна зърненост по прахово металургичен път и се подлагат на горещо изостатично пресоване на заготовките. Имат изключителна якост на натиск, износоустойчивост и топлоустойчивост, но ниска жилавост и якост на огъване. Те са скъпи и се обработват трудно, основно чрез диамантно шлифоване и електофизични методи (електроерозия). Типичен представител е сплавта H40S/HIP. Използват се главно за силно износващи се високо натоварени режещи поансони и матрици в масовото производство. Те имат най-висока износоустойчивост от всички извесни инструментални стомани, използвани за пресова обработка.
1.5. Износоустойчиви покрития и обработки на инструменталните материали.
Повърхностните покрития TiN, TiC, TiСN (титанов нитрид, титанов карбид, титанов карбо-нитрид) представляват твърди износоустойчиви повърхностни слоеве, съдържаши нитриди и карбиди на титана. Достигат микротвърдост над HV 2400 по скала 0.05N. Характеризират се с гладкост, нисък коефициент на триене и добра адхезия. Обичайните процеси за тяхното изпълнение се извършват във вакумна среда при температура 450°С - 550°С. Поради тази причина не са подходещи за всички инструментални материали, защото нагряването за повечето високо въглеродни и легирани стомани води до високо температурен отпуск и рязко падане на твърдостта.Това е съпроводено също с деформации и изменение в размерите. Независимо от високата твърдост на повърхността, не подходящите материали остават меки във вътрешността си и не могат да изпълнят основните си функции. Този вид покрития са ефективни за бързорезни и за някои високо легирани инструментални стомани, като 1.2379.
Друга обработка за повишаване износоустойчивостта на повърхностния слой е карбонитрирането. При нея повърхностите са обогатяват с въглерод и азот на дълбочина около 0.2 - 0,3 mm при температура около 550°С. Достига се твърдост над HRC 64 и се повишават износоустойчивоста и корозионната устойчивост, но нагряването има неблагоприятни последици за твърдостта на повечето високо въглеродни и легирани стомани. Подхоящ инструментален материал за този процес е стомана 1.2379.
1.6. Препоръки за избор на инструментален материал.
Правилния избор на инструментален материал е в основата на ефективното използване на щанците. Прилагането на широко разпространен инструментален материал с недостатъчни якост и износоустойчивост в активните части на щанците за серийно и масово производсво, ще доведе до преждевременно износване и големи разходи за ремонти и поддръжка. В обратния случай, използането на износоустойчив материал за активни части при малки серии или единично производство, няма да позволи ефективно използване на неговия ресурс и неоправдано ще оскъпи щанците. Разбира се, принципа има изключения, при които определени технологични операции за конкретен детайл са възможни само при използване на износоустойчиви инструментални материали с висока якост. Пример за такава операция е пробиване на отвори с диаметър, по-малък от дебелината на материала. Критерий за избора на материал е вида на операцията, определяща характера на износване и натоварването.
Разделителните операции изискват сили, превишаващи якостта на щанцования материал, които се разпределят в тесни зони около режещите ръбове. По тази причина, натоварванията на матриците и поансоните са значително по-високи, от тези при формоизменящите операции. При това те се прилагат ударно. Резултатът е по-голямо износване и необходимост от използване на материали с по-висока якост и износоустойчувост. Максималното налягане на режещите ръбове за еднакъв материал, в зависимост от относителната дебелина на детайла S/d при оптимална хлабина от 5% [1] достига до:
– S / d = 1.0 - около 13,5 пъти якоста на обработваемия материал;
– S / d = 0.5 - около 8.3 пъти якоста на обработваемия материал;
– S / d = 0.1 - около 4.2 пъти якоста на обработваемия материал;
– S / d = 0.05 - около 3.6 пъти якоста на обработваемия материал.
Максималните стойности на налягането на режещите ръбове при безхлабинно рязане (0.005 mm на страна) може да са до 1,4 пъти по-високи, от от посочените по-горе за оптимална хлабина при S / d = 1.0 (дебелина разделена на диаметър или минимален размер). Като основа за обоснован избор на подходящ материал за режещи части, може да се използва графиката от Фиг.7-1,
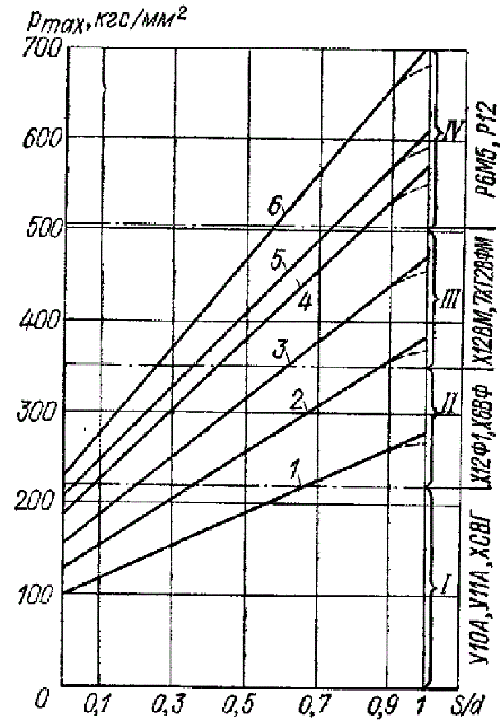
Фиг.7-1
където за различни марки въглеродна и легирана стомана (1 - 08кп; 2 - 20; 3 - 30; 4 - 4; 5 - Х18Н10Т; 6 - 65Г) са построени кривите на максималното налягане, а по вертикалата от дясно са отбелязани границите на приложение на различните инструментални материали (без металокерамични твърди сплави). Вижда се, че в един инструмент може да е необходимо използване на различен инструментален материал. В това е едно от предимствата на съставните вложкови матрици и поансони. При пробиване на малки отвори в твърди (предварително уякчени) материали с висока якост, дори бързорезните стомани или маталокерамичните сплави може да нямат достатъчен запас от якост. В тези случаи се препоръчва да се оптимизира формата на заточване на режешите ръбове, като се създадат по-големи контактни площи, за намаляне на максималното налягане. В литературата се описани различни форми на заточване на поансона, но те са само насока за търсене на решение. Всеки конкретен случай се нуждае от експериментална проверка и оптимизация. Следователно, при разделителните операции е ефективно да се използват от високо въглеродни стомани до твърди сплави, според натоварването и размерите на активните части. Тези инструменти се заточват периодично, затова е важна обемната якост, а не само твърдостта на повърхностния слой.
Формоизменящите операции изискват сили, не превишаващи якостта на щанцования материал, които се разпределят в сравнително широки зони, дължащи се на ограничения за минимално допустими радиуси на огъване, изтегляне, формоване. По тази причина, натоварванията на матриците и поансоните са по-ниски от тези при разделителните операции. При това, те се прилагат плавно поради наличието на радиуси. Резултатът е по-малко износване и възможност за използване на материали с по-ниска якост, без чувствително намаляване на износоустойчивостта. При формоизменящите операции (огъване, изтегляне, отбортоване, оформяне на ребра) е ефективно да се използват от високовъглеродни стомани до бързорезни стомани (за малки маркиращи поансони). Твърди сплави се използват по изключение (изтегляне или калиброване). При тези инструменти не се прилага заточване, затова е важна твърдостта на повърхностния слой. Прилагането на повърхностни покрития е основен начин за повишаване износоустойчивостта.
2. Активни части за разделителни операции на листов материал.
Поансоните, матриците, поансон-матриците и всички режещи вложки за пробиване, изрязване, прорязване, отрязване, разделяне, обрязване, отсичане, са включени в тази група и част от тях са разгледани в конструкциите на щанци.
2.1. Монолитни и съставни активни части за разделителни операции.
В щанцовите инструменти за разделителни операции се използват монолитни матрици (виж Фиг.5-33) и поансони (виж Фиг.5-32), когато размерите и натоварването на режещите ръбове позволяват. При детайли с големи размери, поансоните и матриците се изпълняват съставни на отделни секции, които се центроват и закрепват към плочите с цилиндрични щифтове и винтове. Стиковането по между им е по малки участъци, които лесно се напасват. За противодействие на компонентите от силите на рязане, които се опитват да раздалечат секциите една от друга, се използват допълнителни клинове, опорни стъпала или цели държачи. Друг вариант на съставни матрици и поансони са вложковите конструкции, които позволяват използване на различни материали за вложките.
Типичен пример за съставни вложкови активни части са твърдосплавната матрица от Фиг.7-2 (секторна вложкова матрица за пробиване на роторни канали), която е изградена от монтирани твърдосплавни вложки (поз.3, поз.5, поз7, поз.8) в стоманен матрицодържач и твърдосплавен поансон от Фиг.7-3,
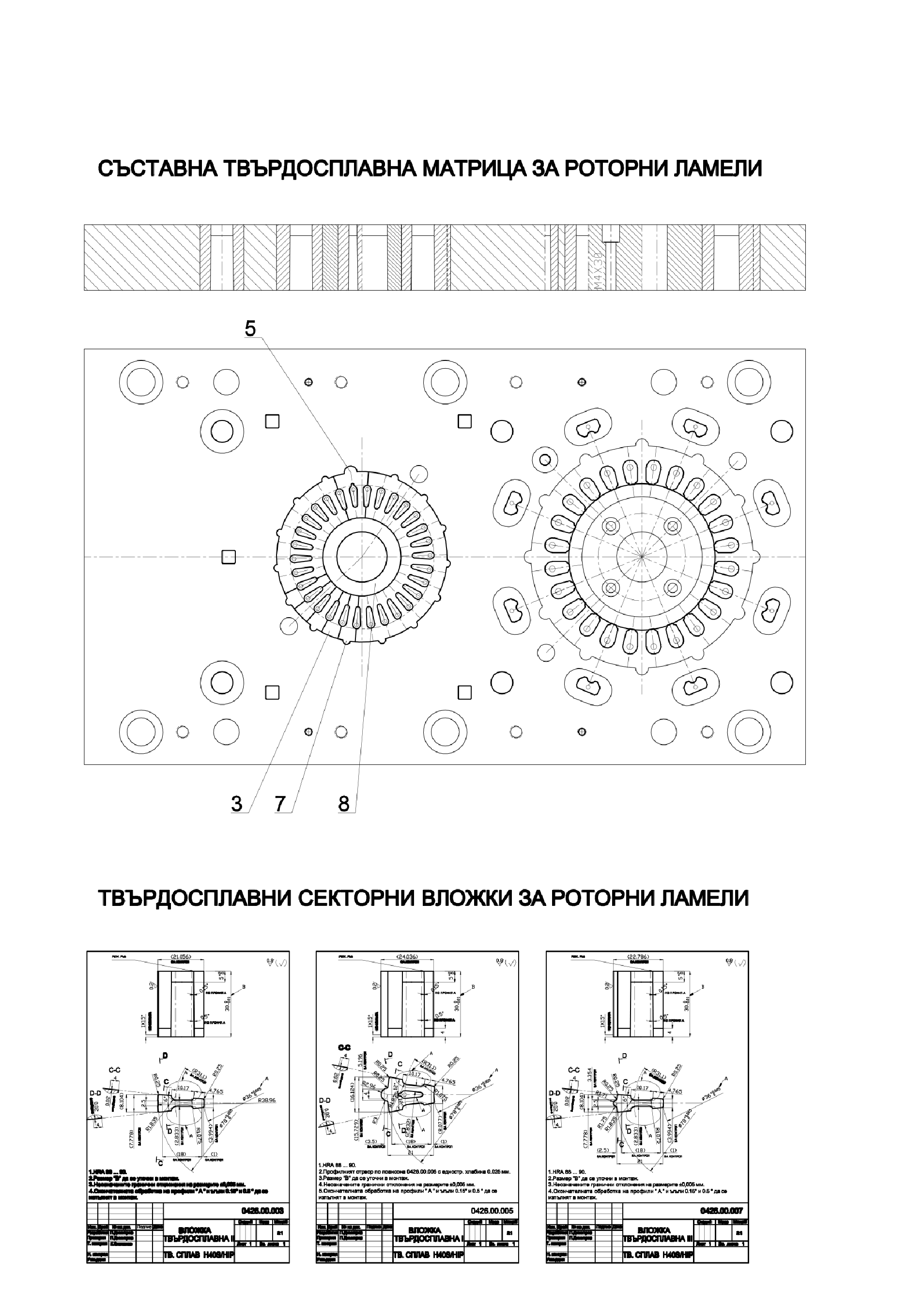
Фиг.7-2
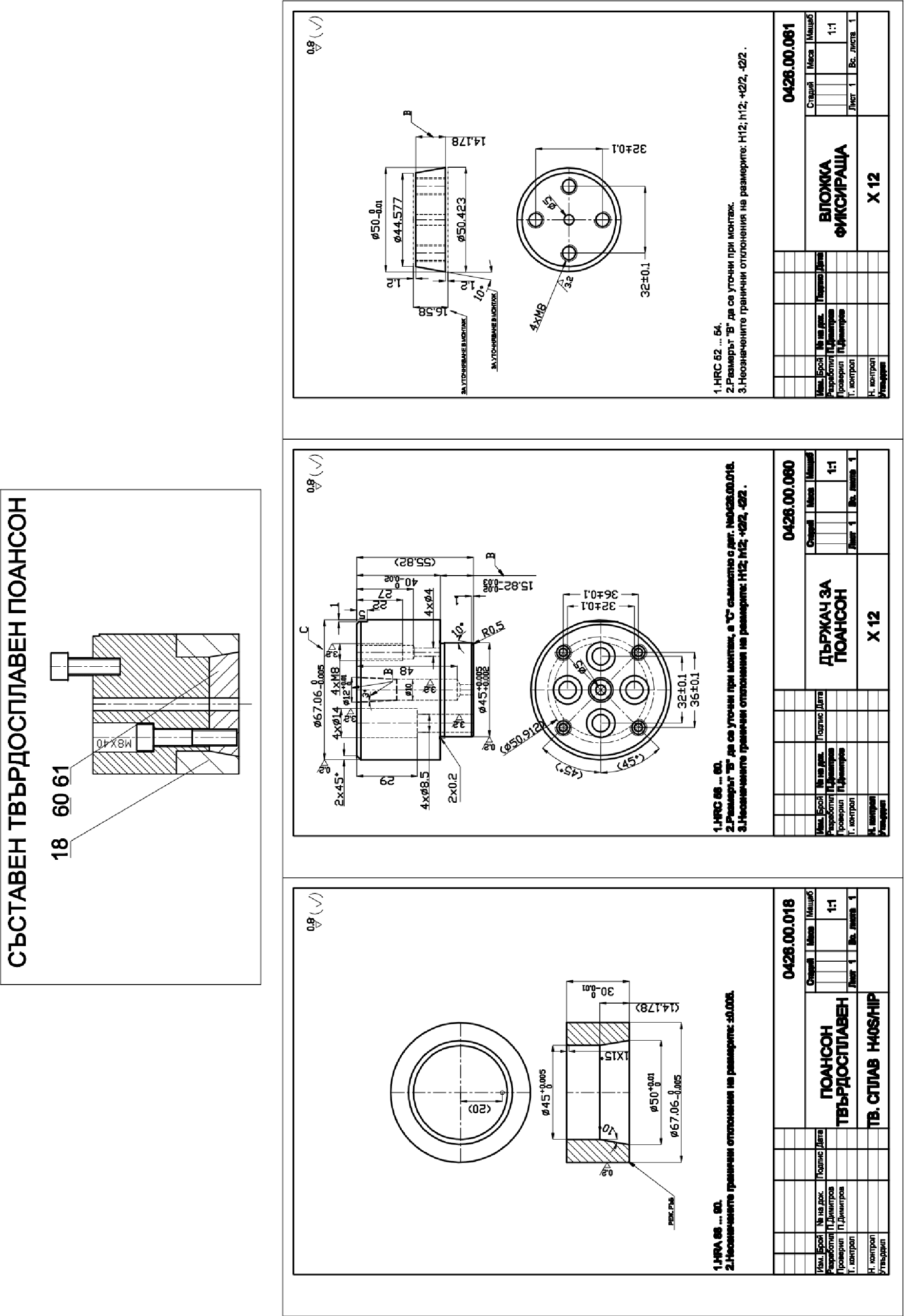
Фиг.7-3
включващ твърдосплавна вложка (поз.18), стоманен държач за поансон (поз.60), стоманена фиксираща вложка (поз.61). Закрепването между частите и съставния поансон към горната плоча на щанцата е с винтове, а за твърдосплавната част със задържащ конус, което позволява изработка и на профилни поансони чрез нишкова електро ерозия. Центроването и закрепването на съставната матрица към долната плоча на щанцата е с щифтове и винтове. Вложковите съставни твърдосплавни матрици трябва да се проектират с достатично разстояние между отворите в матрицодържача за да се намали вероятност за поява на пукнатини (препоръчително около 30% от дебелината на матрицодържача, но не по-малко от 4 mm). Матрицодържачите се изработват от инструментална легирана стомана и се закаляват и отвръшат до HRC 52. Точноста на изработка при тях е много висока (допуски до 0.005 mm). Стремежът е, да се изпълнят сглобки с нулева или минимална хлабина (до 0.003 mm), за гарантиране взаимнозаменяемост при откъртване. Дори такава точност не е достатъчна при показаните секторни вложки за роторни канали на електродвигател – там се извършва допълнително измерване, групиране, напасване. Важна особеност е, предвиждане на освобождаващи зони по вложките, чрез които се извършва начално центроване и подвеждане спрямо отворите и следващо фиксиране с няколко капки секундно лепило LOCTIDE.
Твърдосплавните поансони с малки размери се изработват монолитни - Фиг.7-4, а задържането в поансонодържача при събуване на лентата, се осъществява чрез запоени със сребърен припой стоманени глави. Това решение е подходящо заради не големите сили на събуване (при дебелина на материала 0.5mm). По-големи дебелини от 1,2 mm изискват друг метод на задържане в поансондържача или специален тест на здравината на спойката и допълнително осигуряване на главата (на пример щифт с малък диаметър).
Стоманените матрици с големи размери или от технологични и експлоатационни съображения, също се изпълняват секциони - Фиг.7-5. Тук предна и задна матрици са режещи и се заточват, средната носи изтеглящи вложки и остава с началната височина. Това решение, позволява лесно възстановяване на еднаквата дебелина на трите след заточване, чрез подлагане на набор от пластини под предна и задна матрици, които са предвидени в конструкцията.
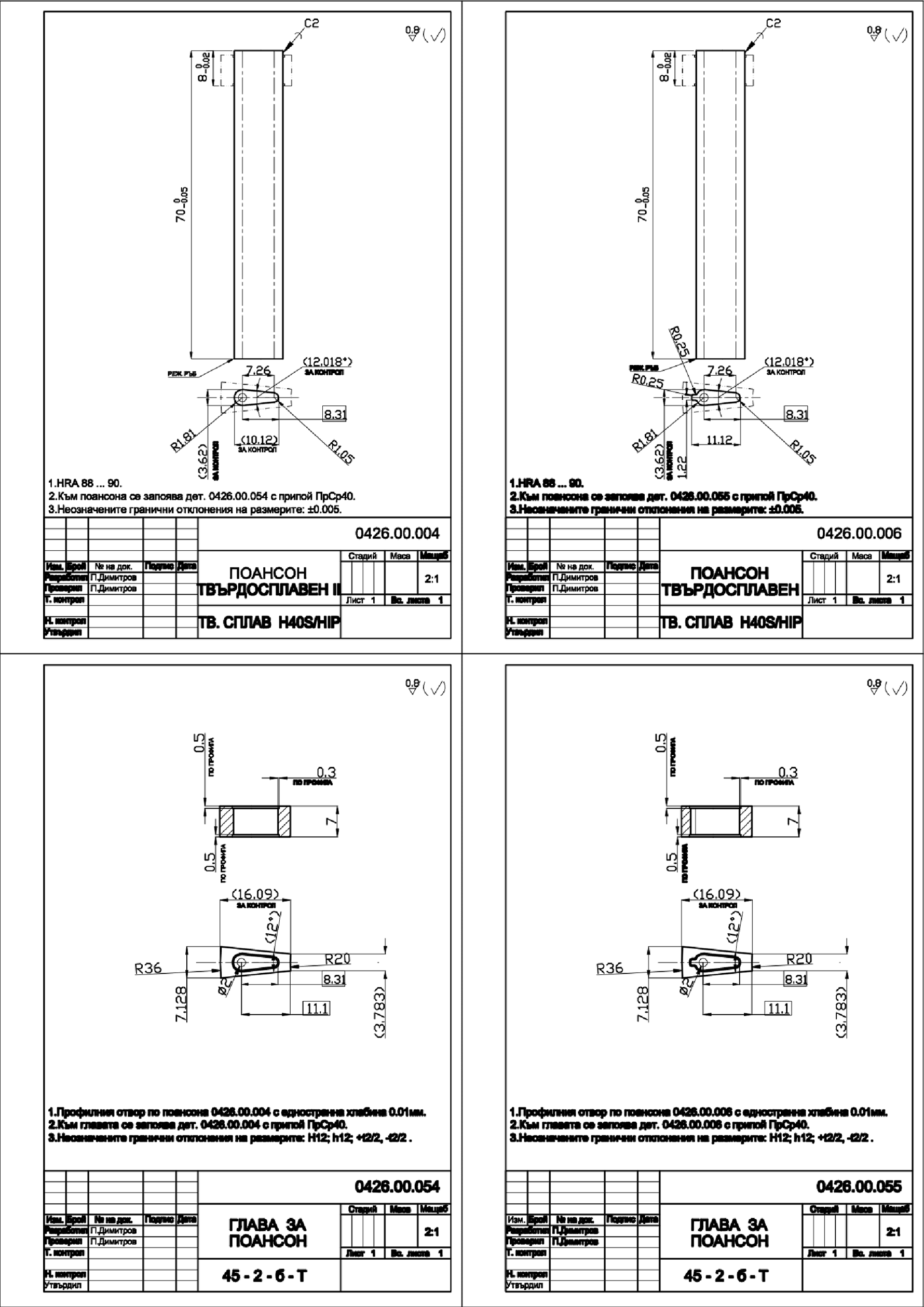
Фиг.7-4
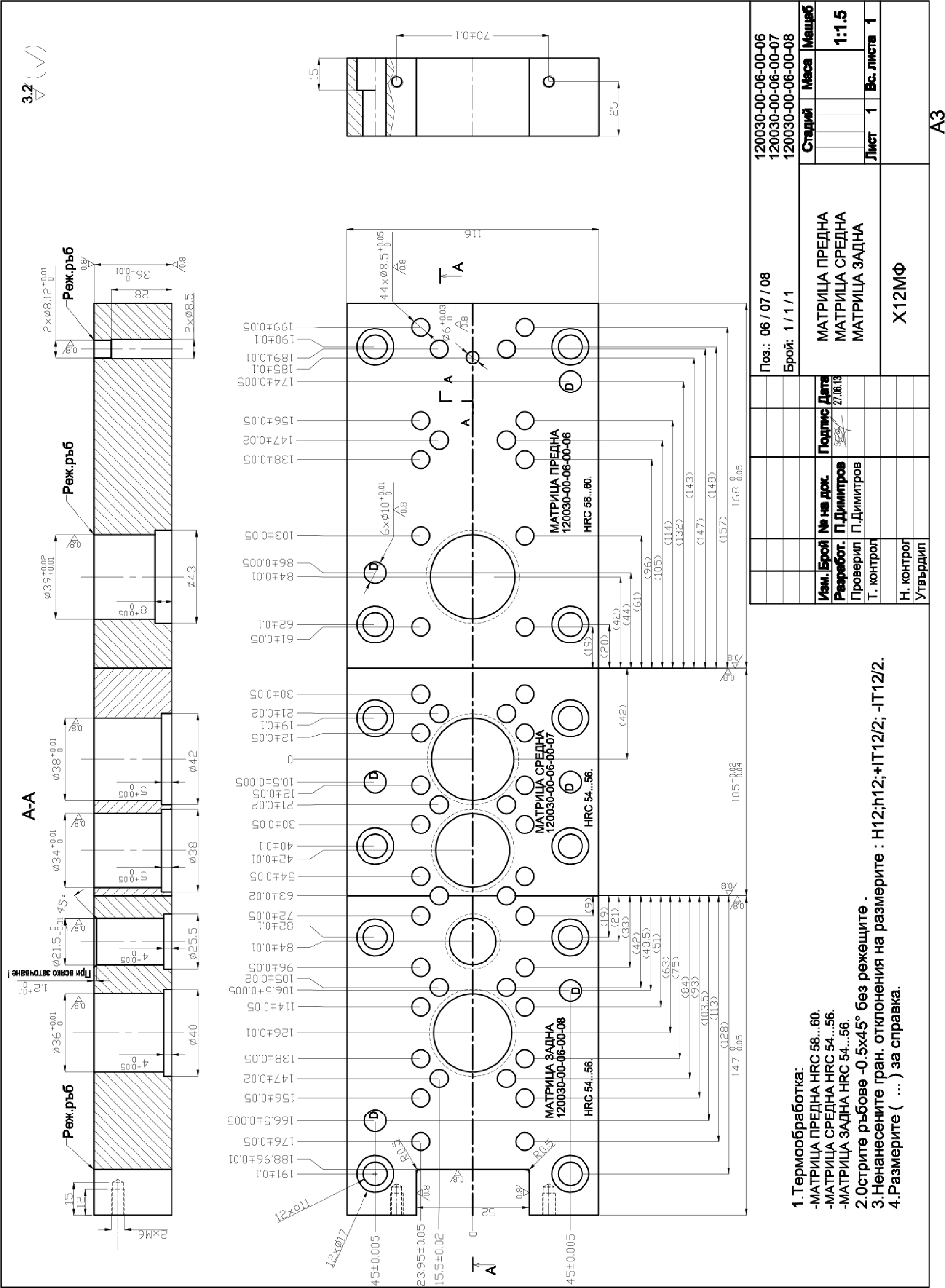
Фиг.7-5
2.2. Конструктивни особености на активни части за разделителни операции.
Според оформянето на работния профил на режещите матрици и вложки, се различават следните видове:
– С прави режещи стени, перпендикулярни на работната плоскост на матрицата от Фиг.7-5 (матрица предна, отвор ф39). Прилага се в случаите, когато пробития или изрязан детайл се връща обратно в лентата или изважда над матрицата от повдигачи (последователни и съвместно действащи щанци).
– С прави режещи стени на височина за заточване, перпендикулярни на работната плоскост на матрицата и освобождаване под тях - Фиг.7-6.
Прилага се в случаите, когато отпадъка от пробиване или изрязания детайл се избутват надолу през матрицата. Много е удобен за кръгли отвори, но е неподходящ за малки размери, поради опасност от заклинване.
– С прави режещи стени на височина за заточване, перпендикулярни на работната плоскост на матрицата и с конусно освобождаване под тях - Фиг.7-7.
Прилага се в случаите, когато отпадъка от пробиване или изрязания детайл се избутват надолу през матрицата. Удобен е за изработени чрез нишкова електро ерозия отвори, когато не съществува опасност от заклинване на детайла или отпадъка. Препоръчва се използването му за тънки материали, в случаи на едновременно изработване на профилите от матрица и притискач, за гарантиране на точност на разположението, когато хлабината на рязане и на водене е до 0,01 mm.
– С конусни режещи стени на височина за заточване, наклонени под малък ъгъл спрямо перпендикуляра на работната плоскост на матрицата и конусно освобождаване под тях с по-голям ъгъл - Фиг.7-8.
Прилага се в случаите на малки размери на отпадъка от пробиване или изрязания детайл, когато съществува опасност от заклинване при избутването им надолу през матрицата. Удобен е за изработени чрез нишкова електро ерозия отвори.
Режещите матрични вложки се различават и по начина на задържане в матрицодържача. Конструкцията с нулева хлабина или стегнатост бе разгледана по-горе. Допълнителна възможност е прилагане на опорно стъпало от Фиг.7-6, което е удобно за кръгли отвори, но е по-неудобно за правоъгълни или с друга форма. Макар и рядко, режещите матрични вложки могат да се задържат и чрез резбови отвори, подобно на матриците.
Режещите поансони се различават конструктивно, според начина на задържане на поансоните в поансонодържача:
– Чрез резбови отвори - Фиг.7-9
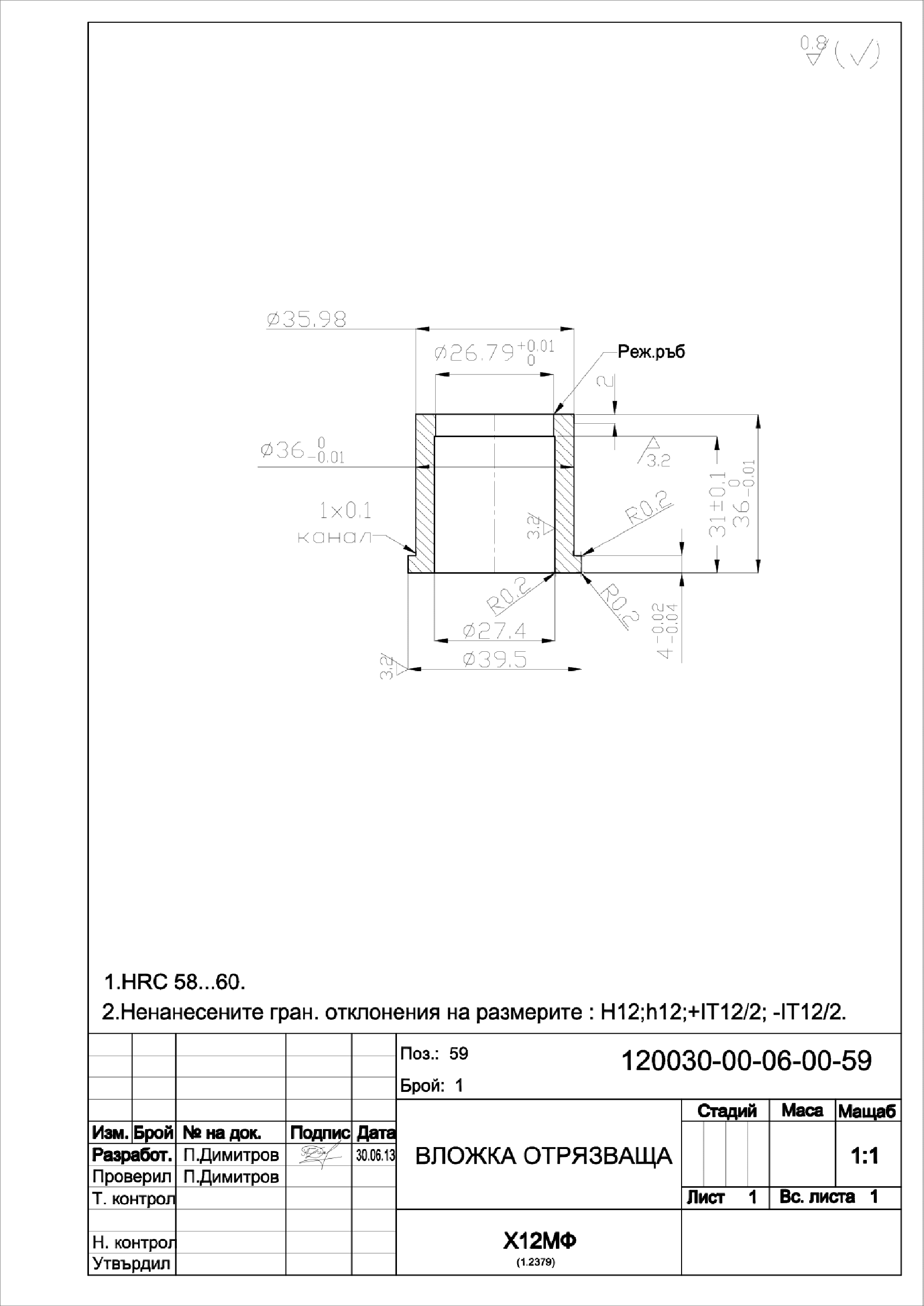
Фиг.7-6
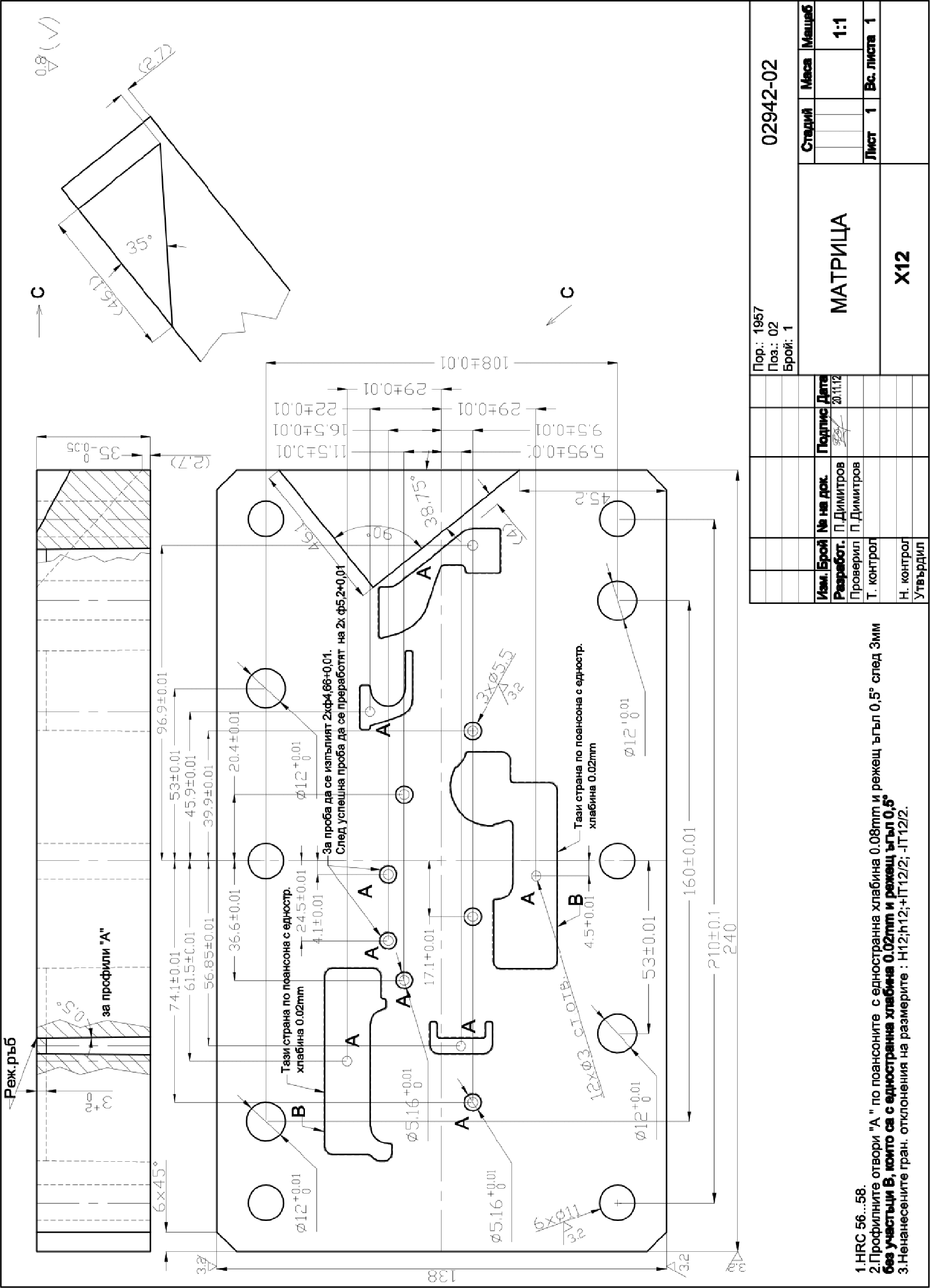
Фиг.7-7
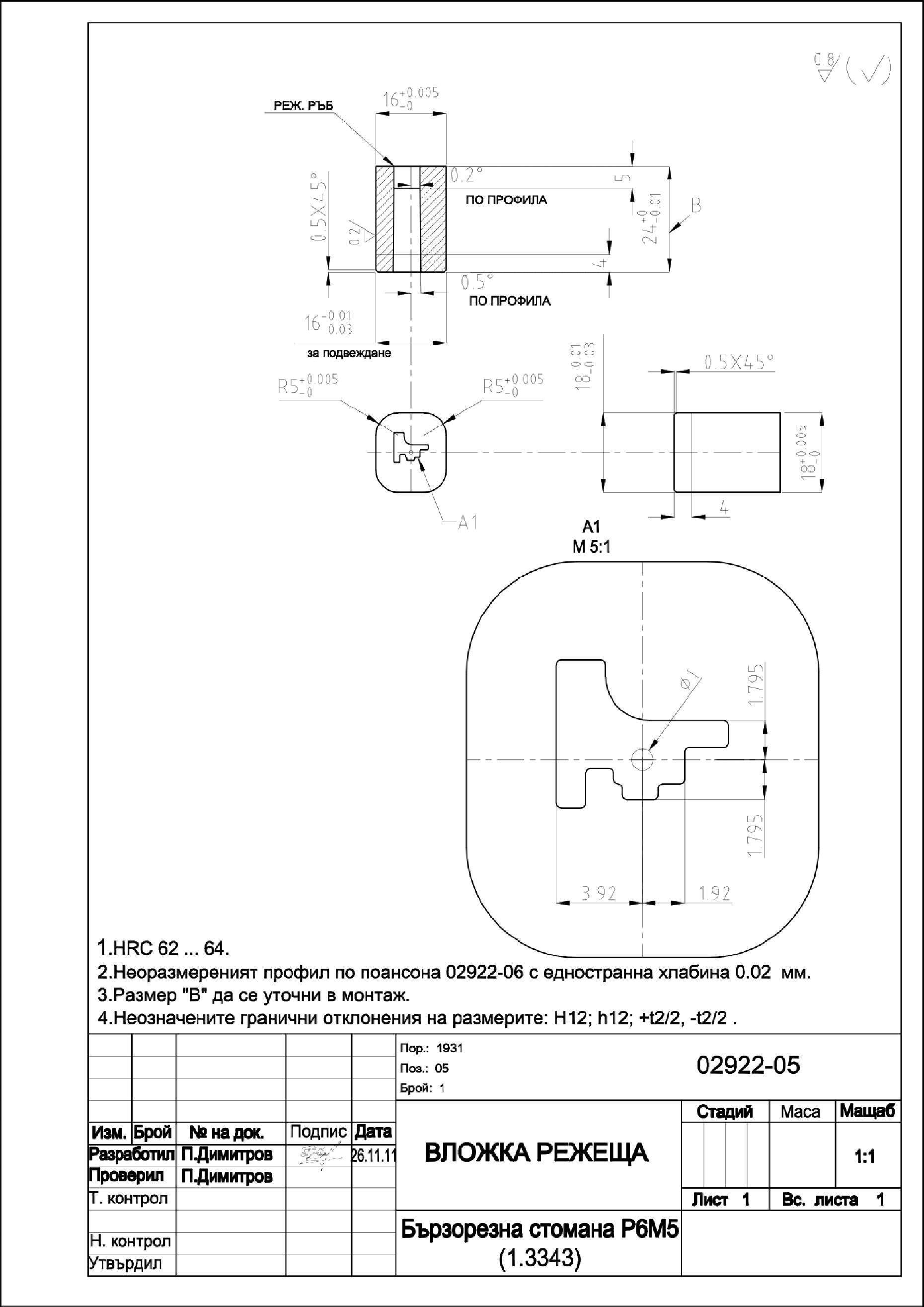
Фиг.7-8
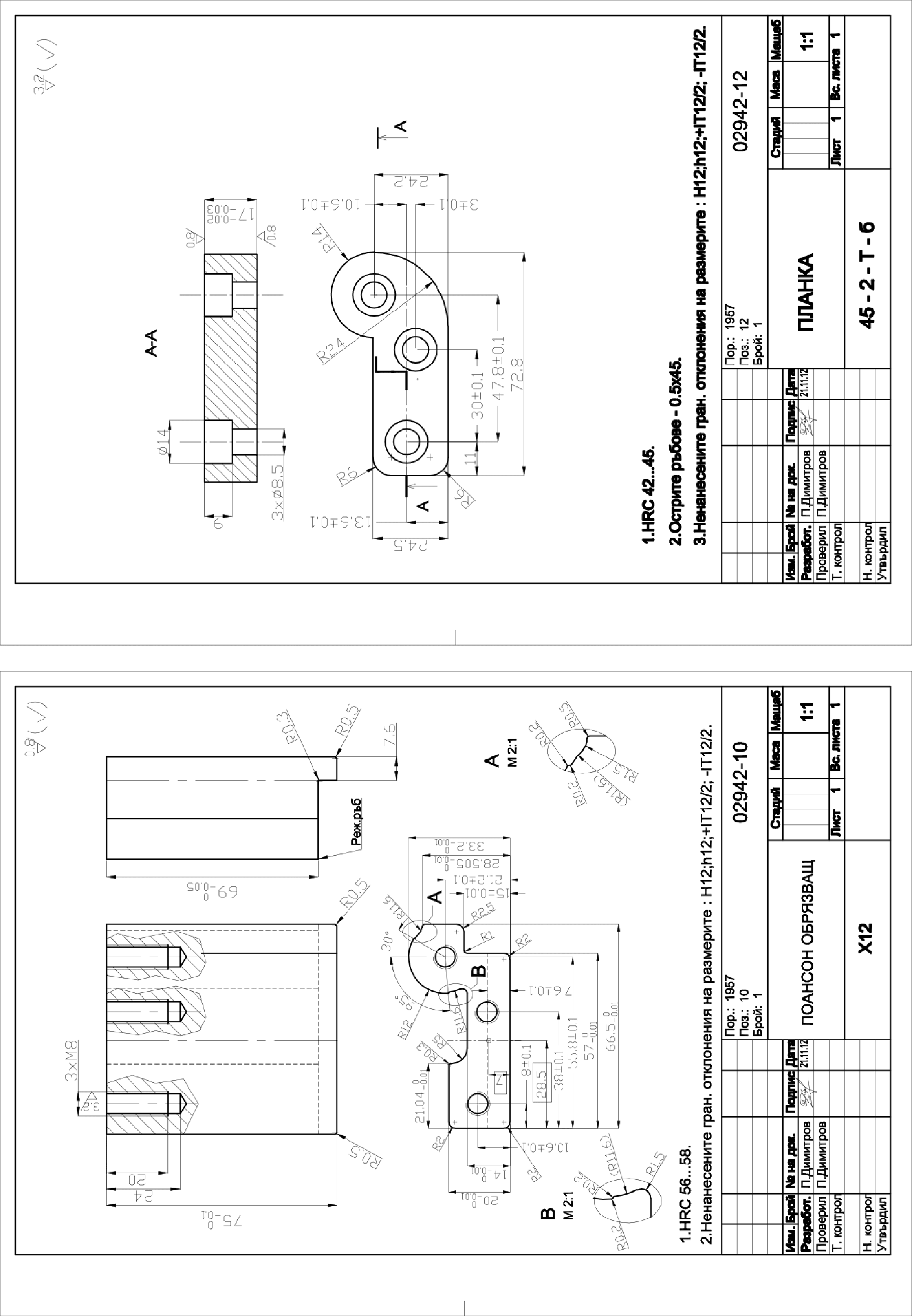
Фиг.7-9
за съставни поансони, за поансони с голяма сила на събуване на лентата (при дебелина над 2 mm), когато има достатъчно място за отворите. Това конструктивно решение е подходящо при произволна форма на поансона, получавана чрез нишкова електро ерозия. Най-ефективен метод за тяхното получаване е предварително подготвяне на закалени Целеви Блок - заготвки за ерозиране с изработени резби (виж Фиг.5-43).
– Чрез запоени стоманени глави в горната част на поансона - Фиг.7-10.
Това конструктивно решение е подходящо при произволна форма на поансона, получавана чрез нишкова електро ерозия и средна сила на събуване (дебелина под 1,5 mm). Прилага се както за стоманени, така и за твърдосплавни поансони. Наличието на нагрявана част за разтопяване на припоя, прави метода не подходящ за къси поансони или вложки (с дължина под 30-40 mm) от инструментална легирана стомана, защото се намаля твърдостта на нагрятата зона.
– Чрез задържащо стъпало в горната част на поансона - Фиг.7-11.
Това конструктивно решение е подходящо при кръгла или правоъгълна форма на поансона, получавана чрез шлифоване. Не е подходящо за изработени чрез нишкова електро ерозия поансони с произволна форма. То обаче, позволява прилагане при големи сили на събуване.
– Чрез чеканка (конусно раздуване) в горната част на поансона - Фиг.7-12.
Това конструктивно решение е подходящо при произволна форма на поансона, получавана чрез шлифоване или чрез нишкова електро ерозия. Прилага се само за стоманени поансони за средна сила на събуване от лентата (дебелина под 1,5 mm). Понеже процеса на чеканка е свързан с нагряване, зоната на нагряване (минимум 20mm) e с по-ниска твърдост. Не се препоръчва за много тънки поансони и при дължина на поансона под 50 mm. Режещи цилиндрични поансони с конусна глава са стандартното изпълнение по DIN 9861. Могат да се използват и за изработка на ловители, показани на Фиг.7-13.
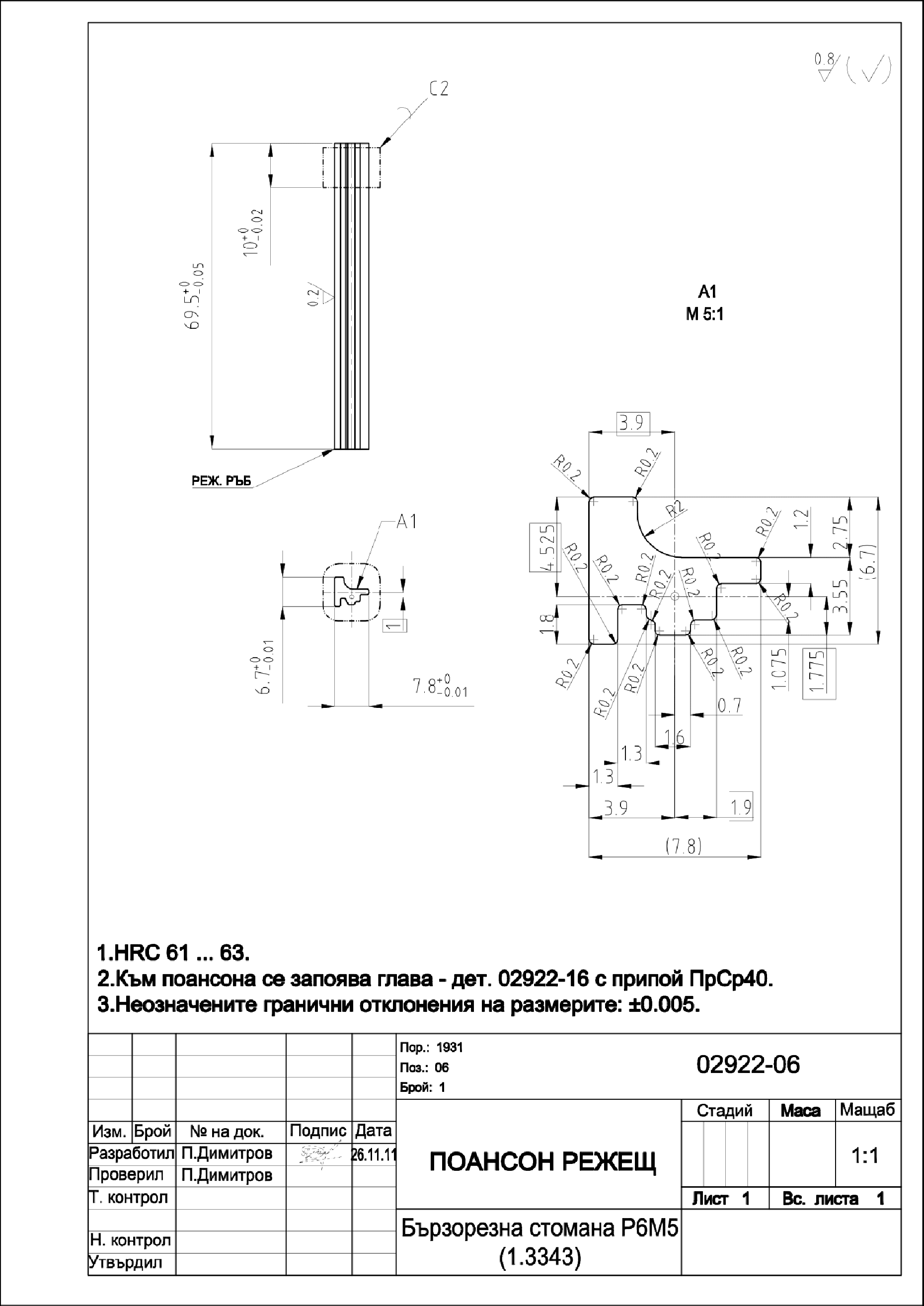
Фиг.7-10
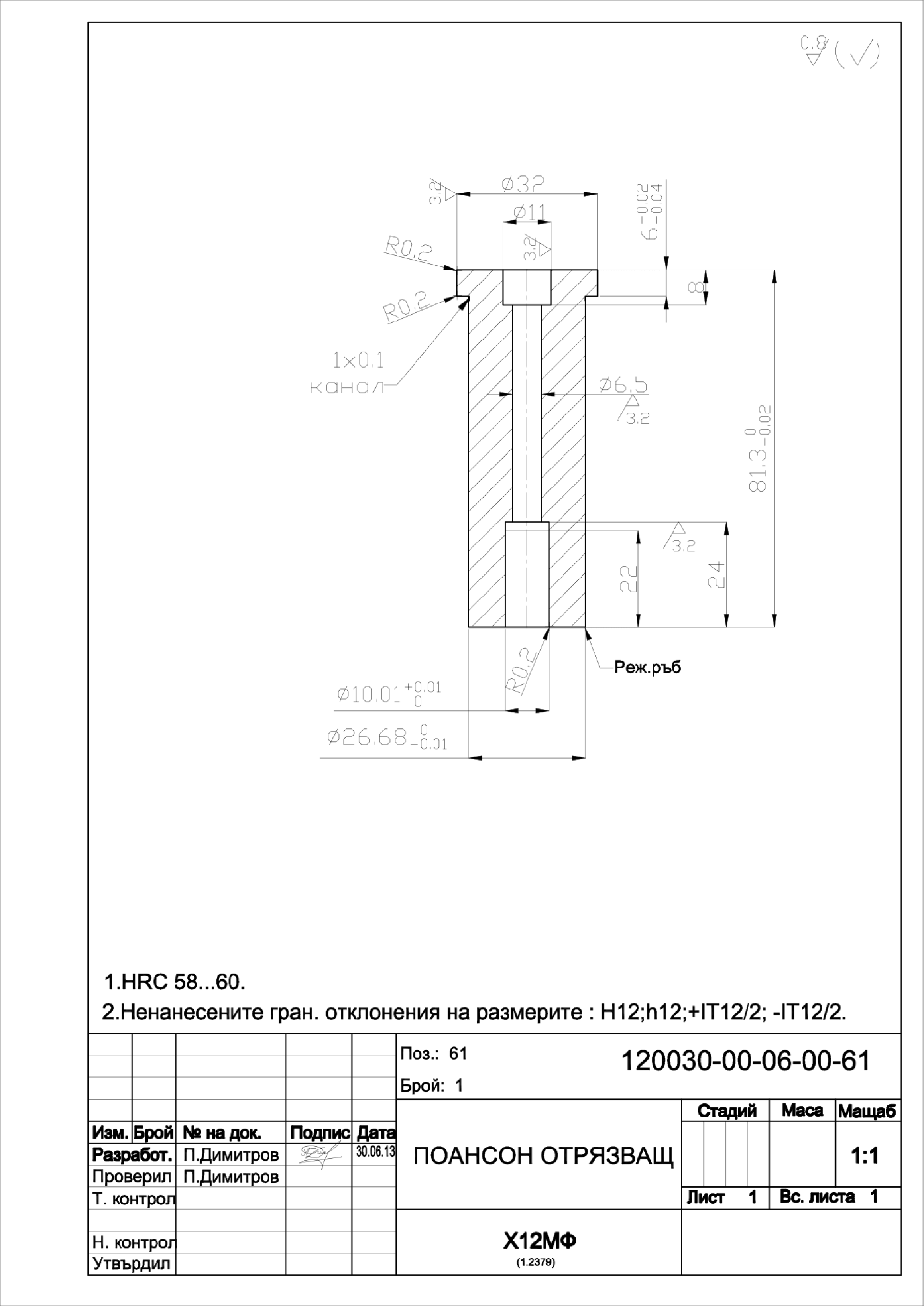
Фиг.7-11
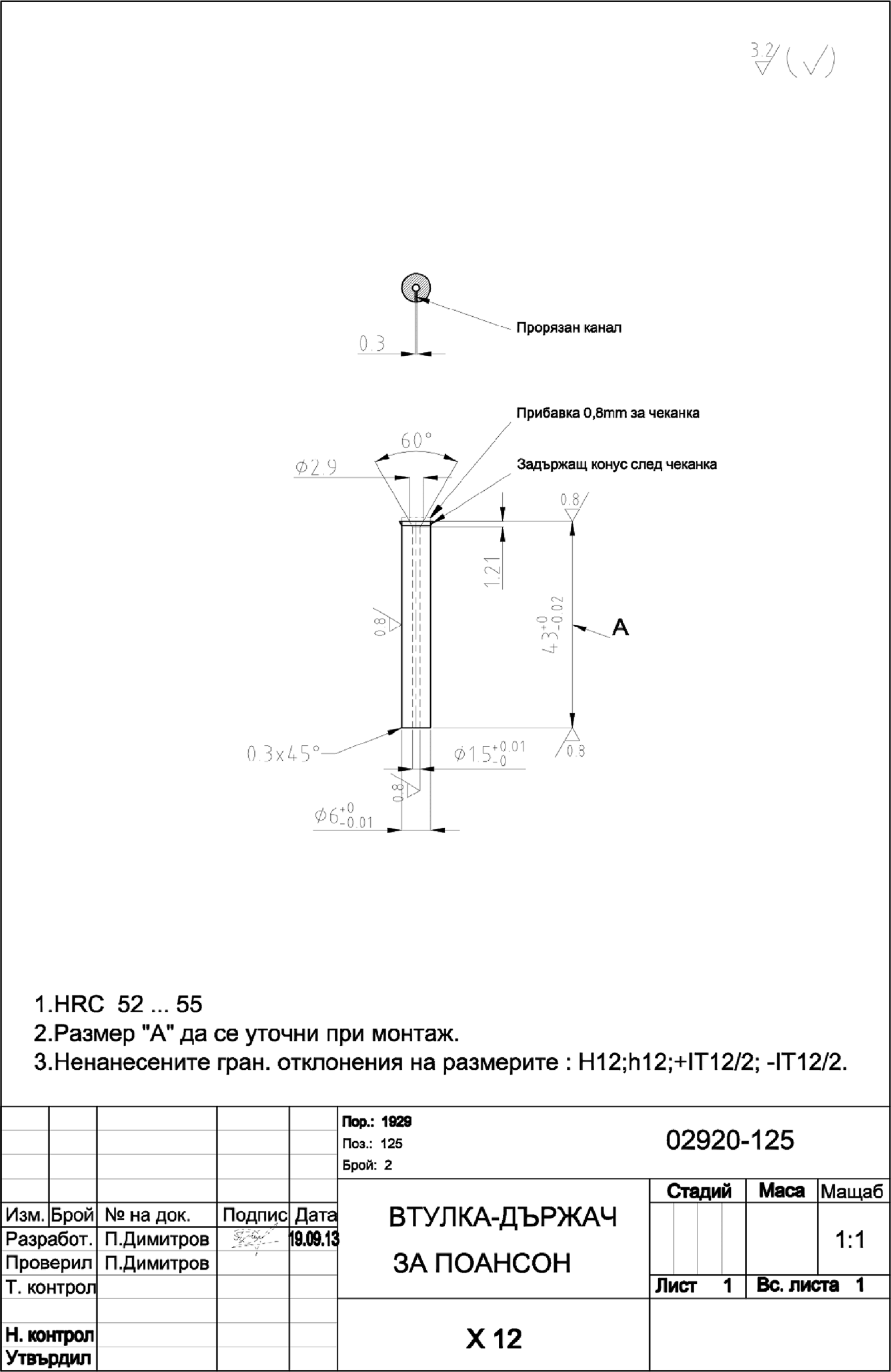
Фиг.7-12
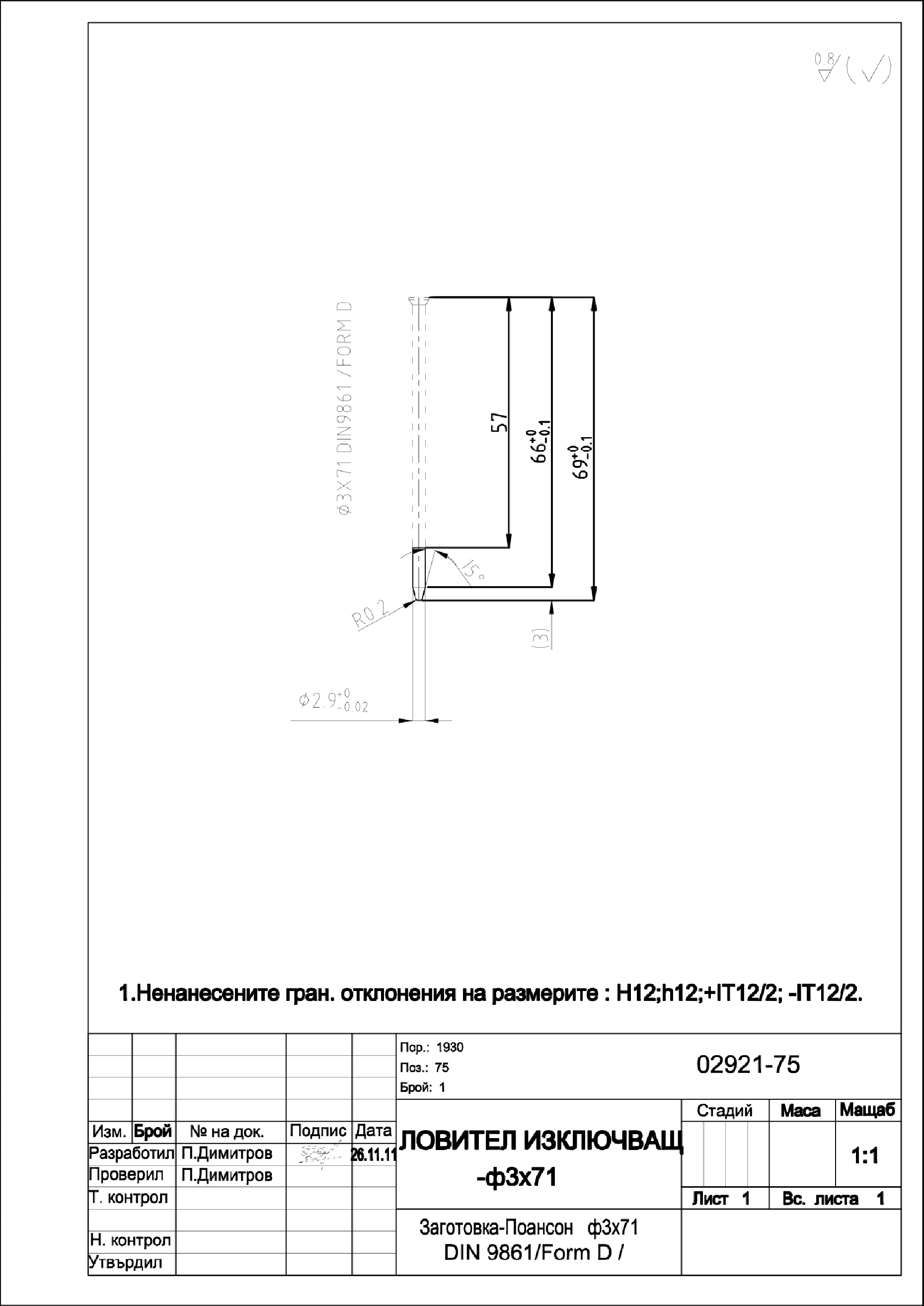
Фиг.7-13
– Чрез задържащи канали в горната част на поансона Фиг.7-14, в които се монтира задържаща скоба, планка или щифт, предаващи натованрването от събуване на лентата от поансона на поансонодържача. Това конструктивно решение е подходящо при произволна форма на поансона, получавана чрез шлифоване или нишкова електро ерозия. В някои случаи се използва и за задържане на твърдосплавни поансони. Препоръчва се при големи сили на събуване (при дебелина над 2 mm). Важно е, да се осигури достатъчно напречно сечение на поансона и да се гарантира равномерно предаване на силата от каналите.
– Чрез напречни отвори в горната част на поансона (виж Фиг.5-32), в които се монтират задържащи цилиндрични щифтове, предаващи натоварването от събуване на поансона на поансонодържача. Това конструктивно решение е подходящо при произволна форма и сравнително тънки поансони, когато е осигурено достатъчно място за отворите. Щифтовете се монтират странично преди поставяне на поансоните в поансонодържача така, че да стърчат равномерно от двете страни. За тях в поансонодържача са изработени канали с дълбочина, позволяваща скриване на горната част на поансона.
– Чрез сили на триене (виж Фиг.6-73) посредством еластични елементи (поз.3, поз.5). Подходящ метод за малки поансони и сили на събуване. Това решение е много близко до бързо смените поансони, описани в [1].
Друга разновидност на метода чрез сили на триене, е използване на заклинване с клин - Фиг.7-16 за „П“ образен поансон с изключитено малки размери от Фиг.7-15 (1.52х1.62х0,36 mm).
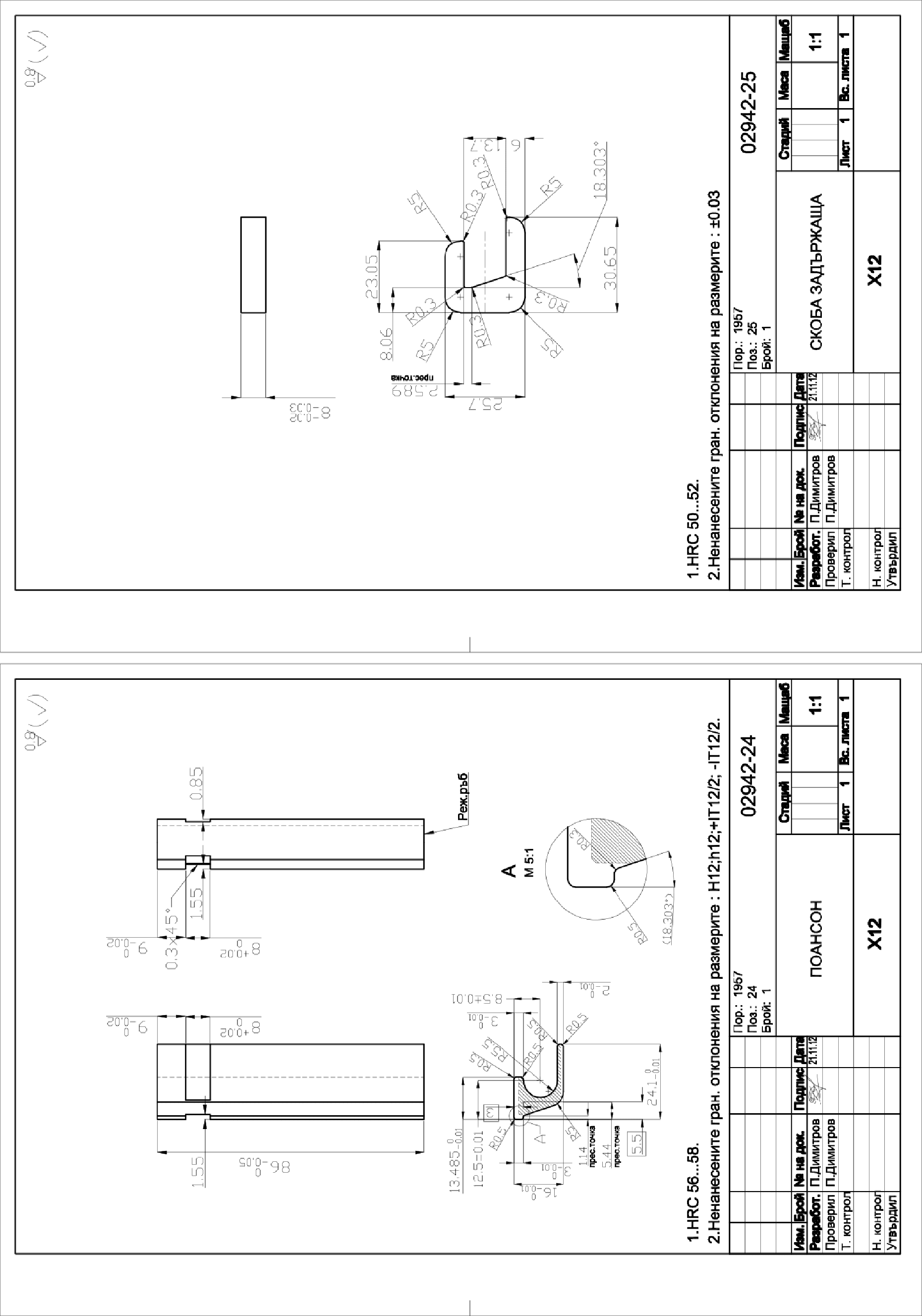
Фиг.7-14
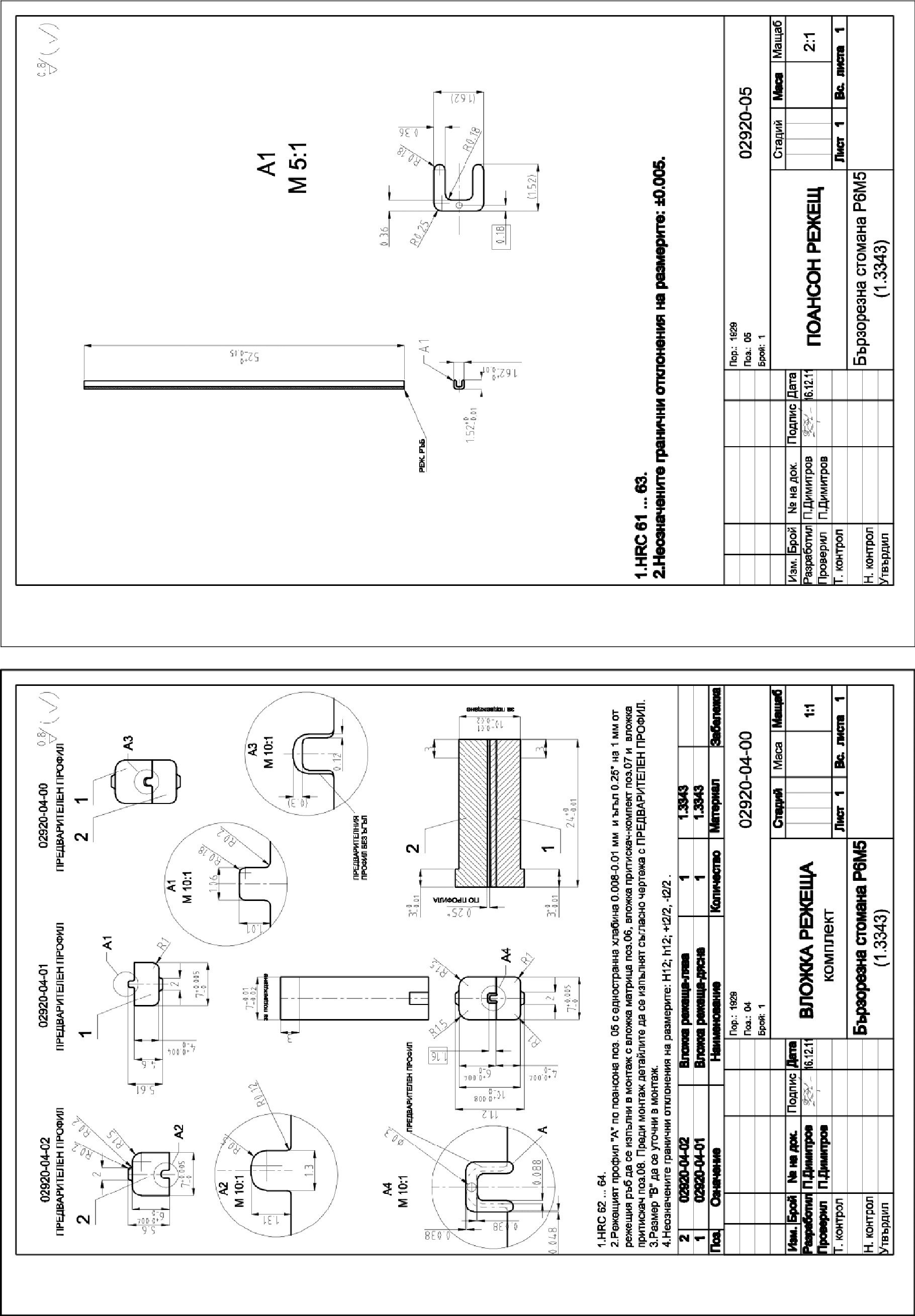
Фиг.7-15
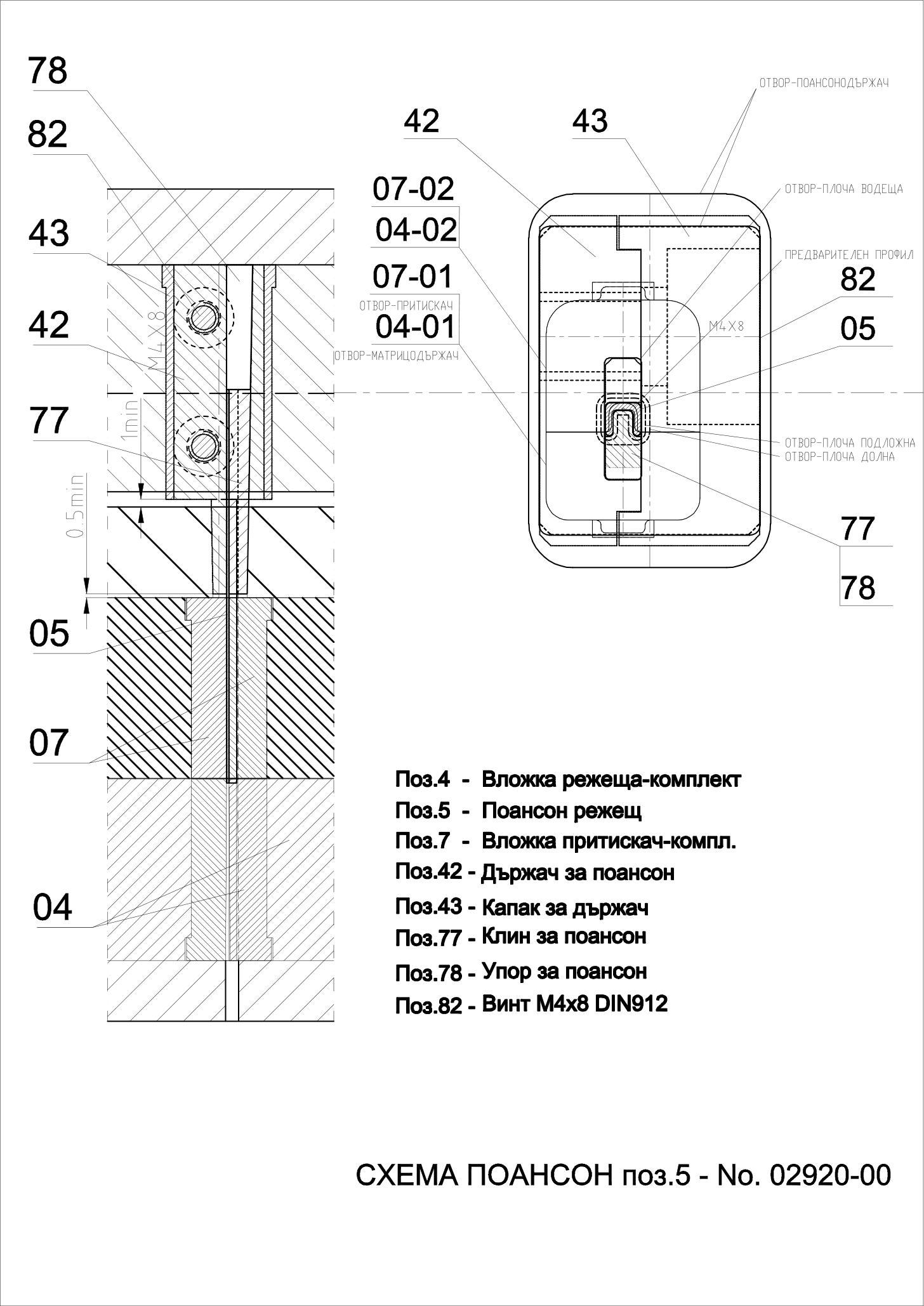
Фиг.7-16
Вижда се, че не само задържането на поансона (поз.05), но и изработката на режещата вложка (поз.04-01) е критично и изисква съствана конструкция. Задържането от силите на събуване на режещия поансон (поз.05) се осъществява със специален държач (поз.42) с капак (поз.43) посредством заклинващ клин (поз.77) и упор (поз.78). Държача на поансона е осигурен в поансонодържача със стъпало. Конструкцията е оразмерена за минимална свободна дължина на режещия поансон извън водене от 1 mm за да не се допусне загуба на устойчивост.
Воденето и задържането на поансони с малко напречно сечение е сериозен проблем, влияещ отрицателно върху надеждната експлоатация на щанцата. Има решения с телескопични водещи вложки със специална форма, монтирани в притискача и поансонодържача, не позволяващи свободната дължина, без водене на поансона [1]. Те обаче, са много сложни за изработка. Препоръчително е, стандартни цилиндрични поансони с диаметър до 1.5 mm да се водят и задържат в поансонодържача с прорязана втулка-държач от Фиг.7-12, като се оставя свободна от водене част до два пъти диаметъра на поансона. Това решение е много просто и лесно изпълнимо за съвременните нишкови електро ерозийни машини. При скъсяване на поансона след заточване, лесно може да се отнеме материал от долната страна на втулката-държач.
3. Активни части за формоизменящи операции на листов материал.
Поансоните, матриците, всички вложки за огъване, изтегляне, формоване, отбортоване, оребряване, релефно формоване и маркиране, калиброване, планиране и други, са включени в тази група и част от тях са разгледани в конструкциите на щанци.
3.1. Монолитни и съставни активни части за формоизменящи операции.
В зависимост от размерите, поансоните и матриците на щанцови инструменти за формоизменящи операции могат да бъдат монолитни, изработени от една заготовка и не съдържащи други части, и съставни, представляващи сглобен възел. Обикновено поансони и матрици с малки размери, за които закаляването не проблем, се изработват монолити - Фиг.7-17.
При големи размери се използват съставни матрици (виж Фиг.5-41) и поансони (виж Фиг.5-42), изработени от вградени в стоманени матрицодържачи или поансонодържачи, закалени вложки (с лилав или син цвят). Тези вложки се задържат в държачите чрез резбови отвори с винтове, а за центроване се използват цилиндрични или конусни щифтове и шпонки. При матрици и поансони с цилиндрична форма (изтеглящи) се използва запресоване към съответния държач.
В зависимост от операцията за която са предназначени се разделят на:
– матрици, вложки и поансони за огъване от Фиг.7-17, от Фиг.7-18 и Фиг.7-19;
– матрици, вложки и поансони за изтегляне от Фиг.7-20;
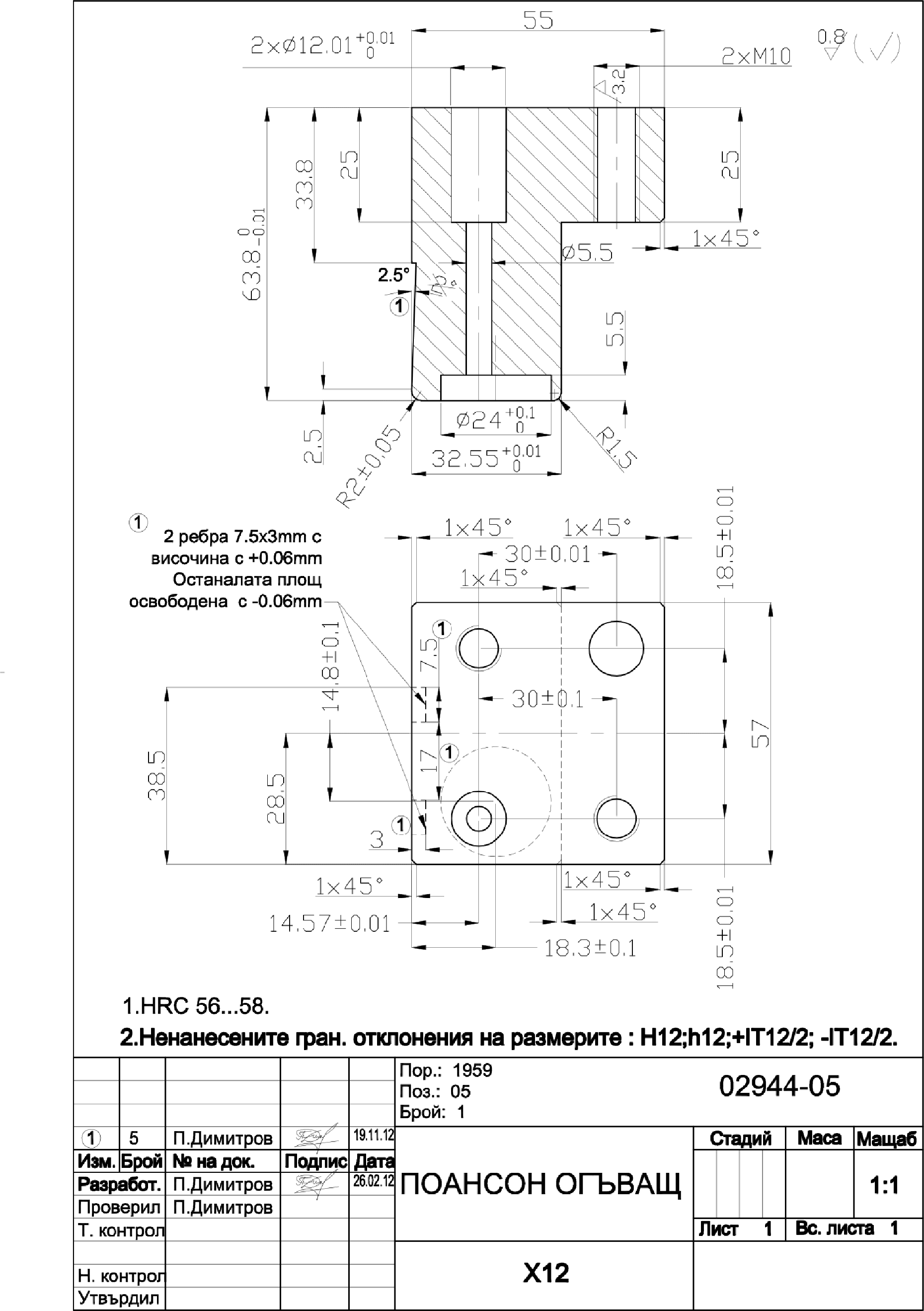
Фиг.7-17
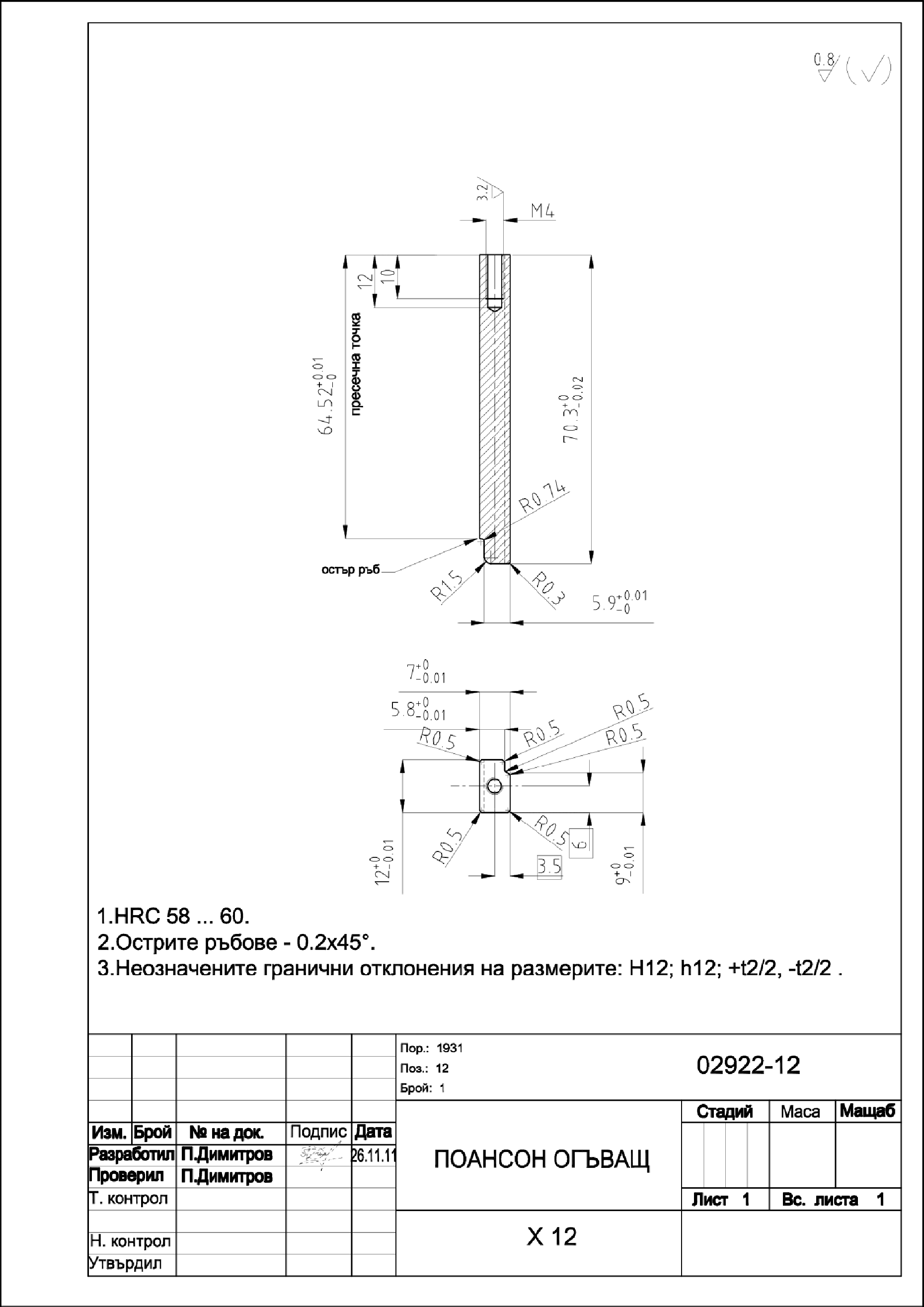
Фиг.7-18

Фиг.7-19
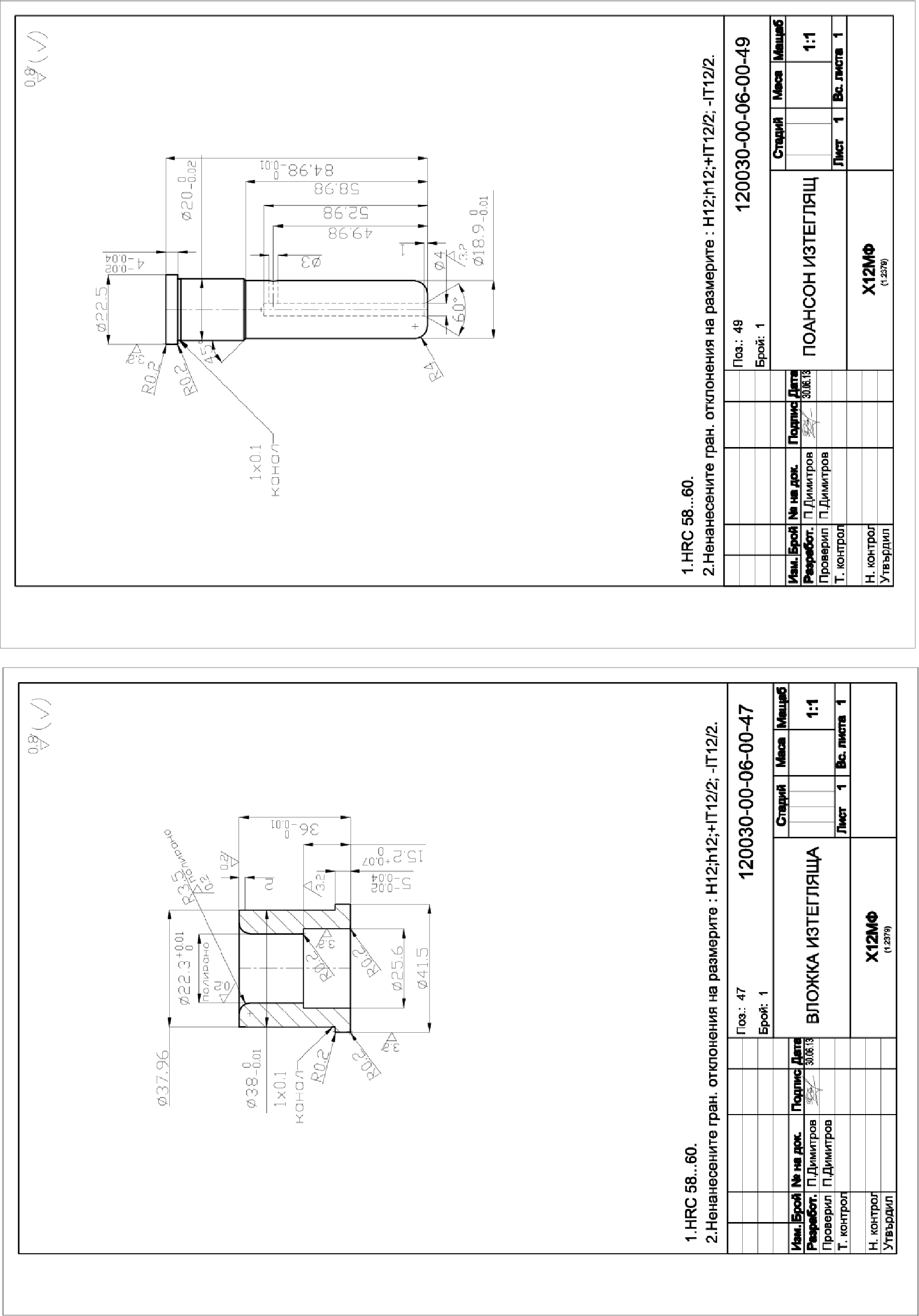
Фиг.7-20
– матрици, вложки и поансони за формоване от Фиг.5-41 и Фиг.5-42;
– матрици, вложки и поансони за отбортоване, маркиране, планиране.
3.2. Конструктивни особености на активни части за формоизменящи операции.
Всички изброени по-горе видове матрици и поансони се различават по начина на задържане:
– Със стъпало от Фиг.7-20 – подходящ за изтеглящи щанци или прости еднооперационни огъващи щанци. Лесен за изпълнение при цилиндрична или призматична форма.
– С резбови отвори и винтове – подходящ за щанци с последоватено действие, при които заточването на режещите части изисква отнемане от огъващите (изтеглящите или формоващите) поансони от Фиг.7-18 и вложки от Фиг.7-19 (или поставяне на компенсираща подложка, която да определя височината).
Конструктивното изпълнение на някои огъващи вложки в щанци с последоватено действие налага, те да изпълняват допълнителна функция на повдигач. Такова решение се налага за огъвки с ъгъл по-голям от 90°. Вложката - повдигач не само трябва да извади огънатата зона над нивото на матрицата, но и да позволи безпрепятственото преместване на огъвката успоредно на лицето на матрицата до следващата работна позиция. Разрез на такава конструкция с плаваща огъваща вложка (поз.21) е показана на Fig.7-21.
В долната и част са монтирани долна подложка (поз.38) и втулка повдигаща (поз.29) посредством винт. Под действието на пужината (поз.102), огъващата вложка се показва над нивото на матрицата при отворена щанца, позволявайки свободно изваждане на огънатата част и позициониране на следващата стъпка. При работния ход на пресата, притискача натиска лентата и вложката с долната подложка до упор и ги заключва в това положение до завършване на процеса на огъване от поансона (поз.22), след което с прибирането на поансона и вдигането на притискача при обратния ход, вложката отново се повдига и освобождава лентата.
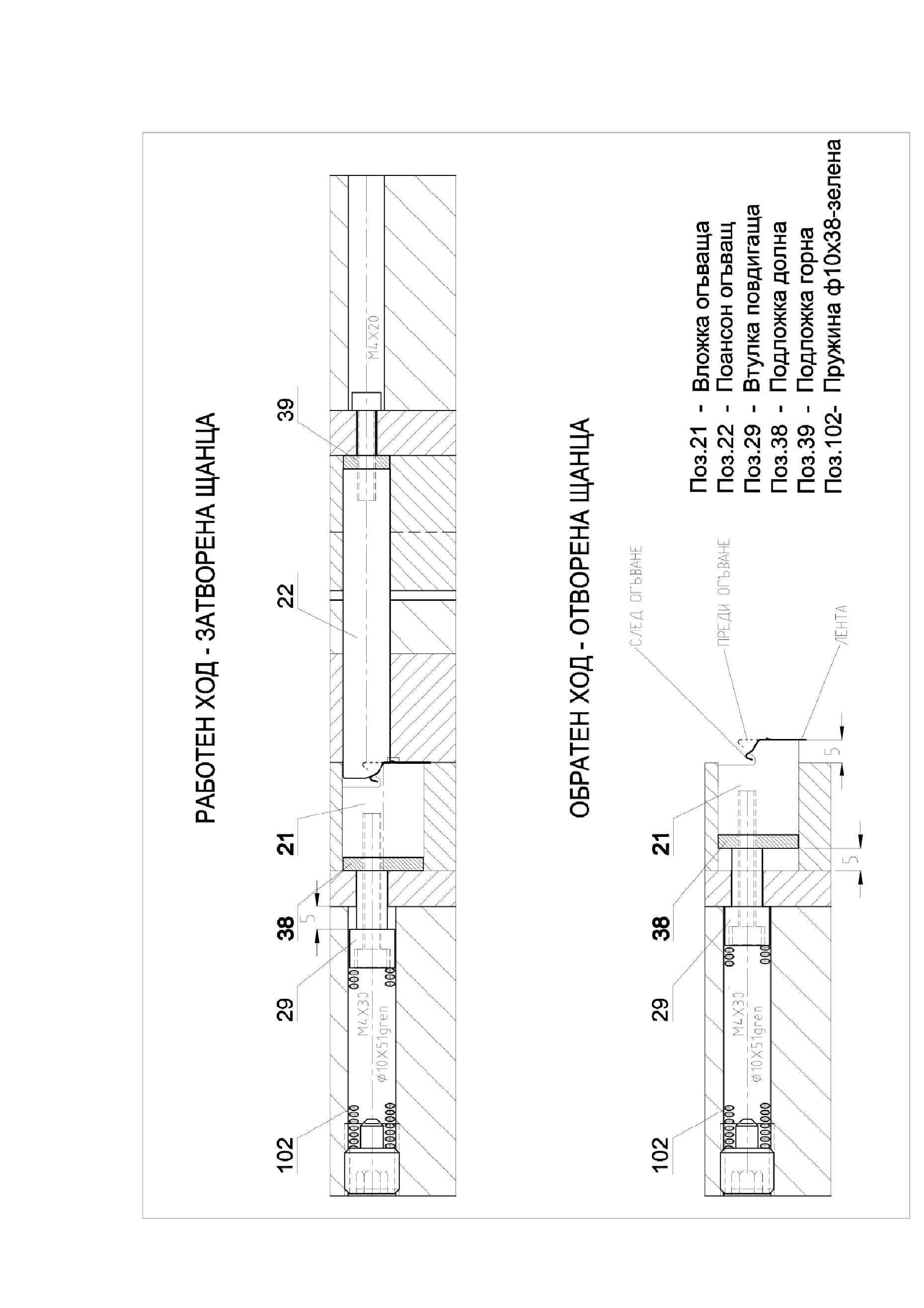
Fig.7-21
Описаните групи от активни части не обхващат всички съществуващи видове. Акцентът е върху разгледаните основни операции и видове щанци, като технологичната операция е определяща за изискванията и натоварването, а конструкцията и инструменталния материал са следствие.
ГЛАВА 8. ТЕХНОЛОГИЧНО НЕОБХОДИМИ (НОСЕЩИ, ВОДЕЩИ, ПОЗИЦИОНИРАЩИ) И СПОМАГАТЕЛНИ ЧАСТИ НА ЩАНЦИТЕ
Щанците включват в своята конструкция два вида технологично необходими части.
Първият вид нямат пряко взаимодействие със заготвката, но осигуряват правилното разположение на поансоните спрямо матриците при тяхното движение (направляващи части), необходимата здравина на конструкцията (носещи части) и противодействие на събуващите сили при обработка на листов материал (задържащи части). Тези части изграждат блока на щанците. Изработват се главно от конструкционна стомана (45, 40Х), но по някога се използват сив чугун или алуминиеви сплави (без направляващите).
Вторият вид контактуват със заготовката или лентата, като центроват (позициониращи части), подвеждат или изваждат заготовката (отделящи части) спрямо матриците и поансоните. Те се изработват от инструментални легирани стомани (Х12, Х12МФ), в отделни случаи, според предназначението си, от високо въглеродни инструментални (У8А, У10А, А12А) или конструкциони (40Х) стомани и се закаляват. При масово производство в щанците с твърдосплавни режещи части за позициониращите елементи се използват и металокерамични твърди сплави.
Спомагателните части позволяват закрепване на елементите от конструцията (скрепителни части) и на самата щанца към пресата (закрепващи части), противодействат на технологичните сили (буферни пружини), предпазват оператора или облекчават настройката (предпазни части, улеи, защитни ограждения, информационни табели), транспорта, монтажа и демонтажа (транспортни части).
1. Технологично необходими части на щанците.
1.1. Носещи части на щанцата.
Това са плочите на блока, най-често горна, долна и водеща плочи. При необходимост (големи натоварвания на малка площ) между тях и активните части се поставят заклени подложни или опорни плочи, които разпределят равномерно натоварването от вложките и поансоните. На тях се закрепват всички елементи от конструкцията. Долната плоча - Фиг.8-1
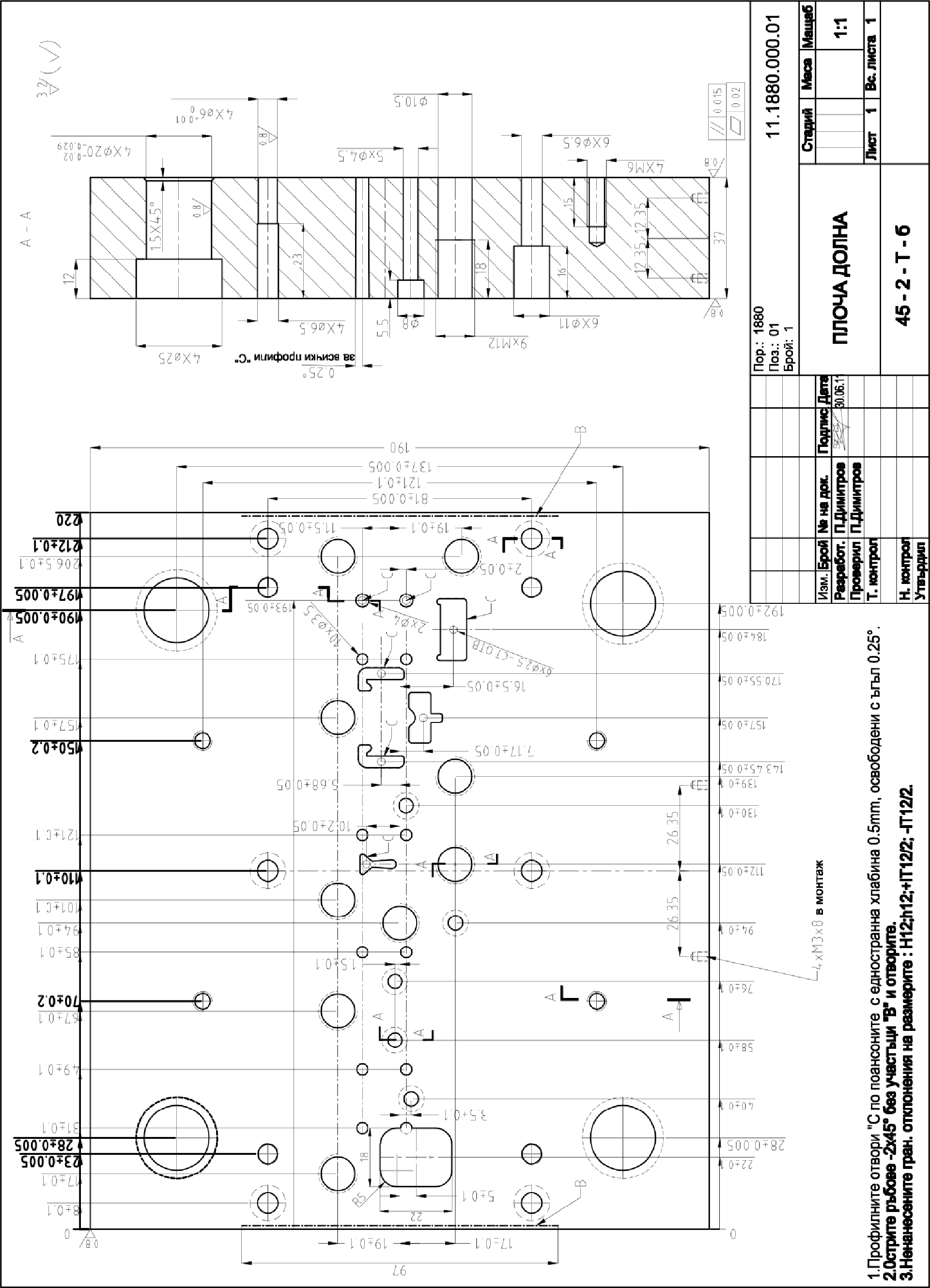
Фиг.8-1
обикновено е неподвижна и към нея се закрепват чрез винтове и щифтове матрици, матрицодържачи или поансонодържачи. В нея има точни отвори за центроващите щифтове и направляващите части – колонки или втулки. Когато към плочата се закрепва режеща матрица, се изработват и освободени отвори за отпадъка от рязане или готовия детайл. Препоръчтелно е отворите за малки отпадъци да имат малък наклон (разширение в долната част). Често се предвиждат канали за закрепване към масата на пресата (виж Фиг.6-74) и странични отвори за транспортни части, облекчаващи работата при голямо тегло. В някои случаи, в горната част на плочата се изработва точен надлъжен канал за вграждане на матрицодържачи или поансонодържачи. Така се постига по-голяма коравина на цялата щанца. Отворите под главите на винтове се изработват в долна плоча за леки щанци, където не проблем да се обръщат при разглобяване. При големи и тежки щанци в долната плоча се изработвата резби, а отворите за главите на винтове се изработват в матрицата. Обикновено долните плочи не се закаляват. Изключение се допуска само при малки плочи за твърдосплавни щанци.
Горната плоча - Фиг.8-2 в щанците най-често е част от подвижния пакет и към нея се закрепват опорна плоча, поансонодържач или матрицодържач. В нея има точни отвори за центроващите щифтове и за направляващите части – колонки или втулки, в зависимост от конструкцията, както и всички крепежни и резбови отвори. В горната част има отвор за центроване и монтиране на държач за пресата (дорник). По някога, в плочата се предвиждат канали или отвори за закрепване към плъзгача на пресата (при големи събуващи сили) и странични отвори за транспортни части, облекчаващи работата при голямо тегло. Рядко в долната част на плочата (при голяма дебелина) се изработва надлъжен канал за вграждане на матрицодържачи или поансонодържачи. Това може да се налага за съгласуване височината на щанцата със закритата височина на пресата. Тези плочи обикновено не се закаляват.
Водещата плоча - Фиг.8-3 в щанците е част от подвижния пакет. Към нея се закрепва притискач, ако не е закалена или има вложки, за които е необходима опора. В плочата има точни отвори за направляващите части – колонки или втулки, в зависимост от конструкцията. Всички поансони, преминаващи през нея се водят директно (при закалена плоча) или в залети със специални антифрикционни епоксидни материали отвори. По някога, за плочи с притискач, отворите за поансоните се изработват с малка хлабина за улесване на изработката. За притискача в долната част на плочата (при достатъчна дебелина) се изработва точен надлъжен канал за вграждане. При голямо тегло в нея се предвиждат странични отвори за транспортни части, облекчаващи монтажа. Често, по технологични и експлоатационни съображения, се използват няколко закалени къси водещи плочи с отделни колонки и втулки, вместо една дълга (виж Фиг.6-74). В щанците с последователно действие, обикновено водещата плоча е плаваща под действие на буферни пружини, но са възможни и конструкции с неподвижна водеща плоча, която изпълнява функцията и на събувач за лентата - Фиг.6-14 (поз.3). Твърдостта на закалените водещи плочи се избира в зависимост от използвания материал (HRC45 – HRC56).
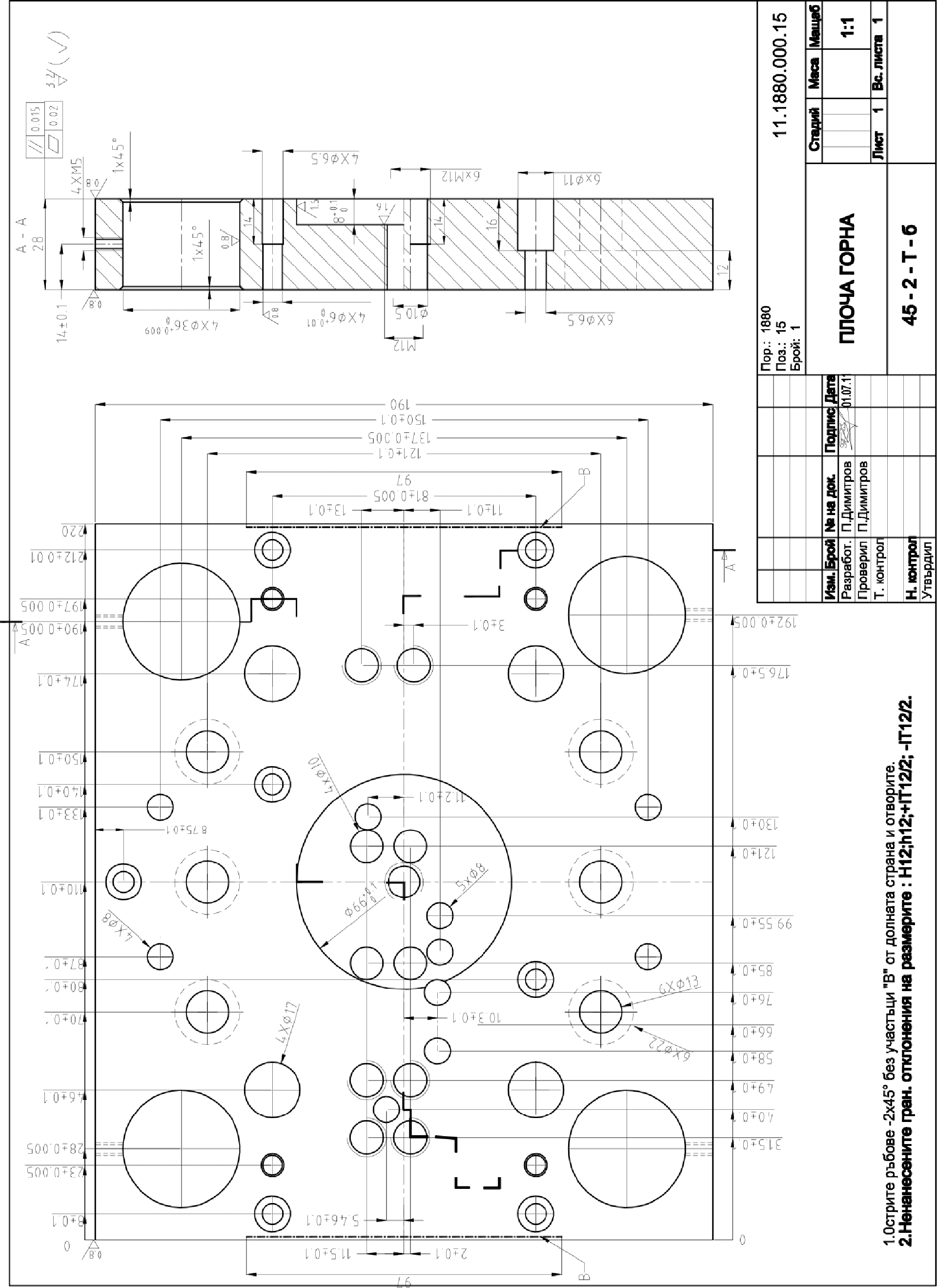
Фиг.8-2

Фиг.8-3
1.2. Задържащи части на щанцата.
Задържащите части на щанцата са матрицодържачи (при съставни матрици) и поансонодържачи. В зависимост от конструкцията на щанцата, поансонодържачите - Фиг.8-4
могат осигуряват задържането на поансоните срещу събуващи сили, или освен това да центроват поансоните спрямо матрицата - Фиг.6-73 (поз.8, поз.9), изпълнявайки функцията на водач.
В първия случай отворите за поансоните и задържащите повърхнини се изработват с малка хлабина (0.05-0.1 mm на страна) за самонагласяне при щанцоване и облекчаване изработката и монтажа.
Във втория случай отворите за поансоните са с нулева или минимална хлабина (0-0.003 mm на страна), а за цилиндрична форма се изполва дори стегнатост.
Центроването на поансонодържачите за втория случай се изпълнява от точно изработени отвори за щифтове. Тези отвори за първия случай обикновено се освобождават с 0.05-0.1 mm за да се гарантира лесен монтаж. При малки размери на поансонодържача, в щанците за малки производствени серии, отвори за щифтове могат да не се изработват – разчита се на поансоните и хлабината между скрепителните отвори и винтовете, да го центроват спрямо водещата плоча. Закрепването на поансонодържача е с резбови отвори. Поансонодържачите обикновено не се закаляват – изключенията са за специални изпълнения на конструкцията (на пример от Фиг.6-73).
1.3. Направляващи части на щанцата.
Тези части осигуряват необходимото разположение на подвижния спрямо неподвижния пакет и монтираните в тях матрици и поансони във всеки един момент от работния ход. От друга страна, те трябва да гарантират необходимата коравина на конструкцията, която да не позволи преждевременно износване на на поансоните. В зависимост от конструкцията и необходимата точност на разположение между матрицата и поансоните, определена главно от технологична хлабина на рязане, се прилагат два принципно различни метода за направляване – с триене при плъзгане и с триене при търкаляне.

Фиг.8-4
– Конструкцията на направляващи части с триене при плъзгане се състои от двa детайла – колонка и водеща втулка от Фиг.6-14 (поз.14, поз.17). Връзката е възможна само при наличие на хлабина между тях (сглобка за движение), която да позволи навлизане на смазващо вещество. Точно минимално необходимата хлабина затруднява прилагането на такова конструктивно решение при щанци за пробиване и изрязване на тънки листове. На пример за дебелина под 0,5 mm, едностранната хлабина е 0.015 mm и е по-малка от препоръчваната между колоната и втулката. За изработката на колонки и втулки се използват легирана лагерна стомана (ШХ16), циментуема стомана и като изключение високовъглеродна инструментална стомана (У12А), които се закаляват до HRC60-62. Във втулките се изработват канали за смазване. Тези части могат да се доставят като нормализирани елементи, произведени от фирмите „FIBRO Normalien“, „DME“, „RABORDIN INDUSTRE“, „AGATHON“, „STRACK Normalien“, „MEUSBURGER“, „DANLY“, „DEYTON LAMINA“, „SUPERIOR“, „PEDROTTI”. Предлагат се водещи втулки със специални бронзови антифрикционни покрития на отвора, за намаляне коефициента на триене и износването, а също и самосмазващи се втулки. Конструктивна разновидност на направляващи чрез триене при плъзгане е призматичната стоманена направляваща колона, водеща по бронзови пластини, монтирани в ъглите на горна и долна плочи от Фиг.6-32.
– Конструкцията на направляващи части с триене при търкаляне се състои от три основни детайла – колонка, водеща втулка и сепаратор с търкалящи тела - Фиг.8-5 (сачмен сепаратор).
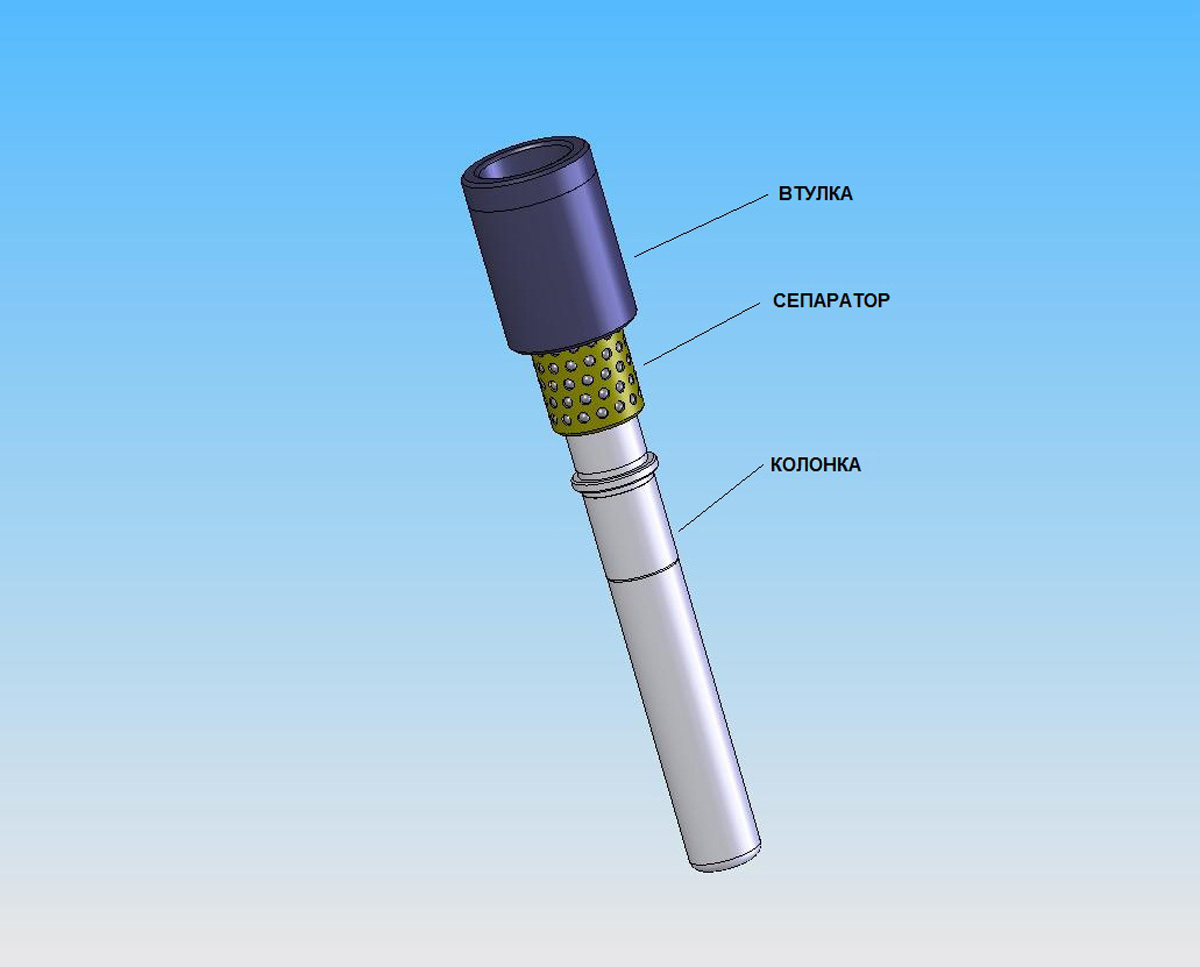
Фиг.8-5
При този вид се препоръчва нулева хлабина или предварителна стегнатост (0.002-0.01mm според диаметъра) между колонката, втулката и търкалящите тела. Смазването на възела удължава живота, но не е определящо за работоспособността на щанцата. Отсъствието на хлабина позволява прилагането на това конструктивно решение при щанци за пробиване и изрязване на тънки листове. В зависимост от търкалящите тела в сепаратора са възможни сачмено водене - Фиг.8-5 и ролково водене (пример от каталога на фирма AGATHON AG) - Фиг.8-6.
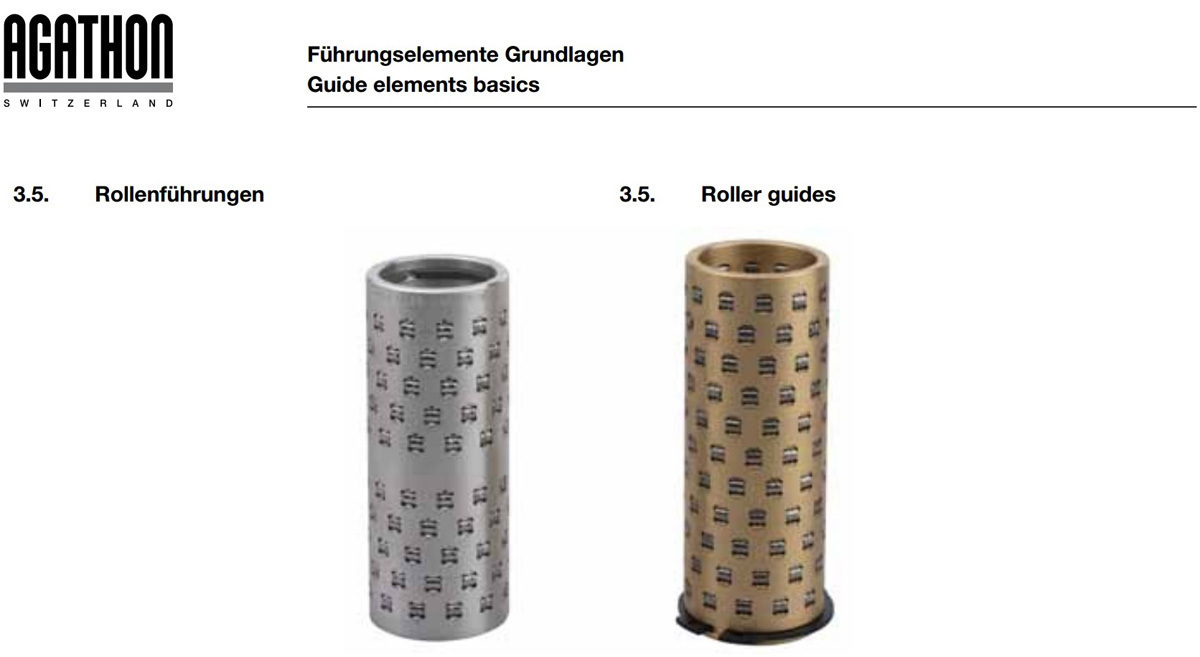
Фиг.8-6
Ролковите сепаратори имат по-висока коравина и износоустойчивост, но са значително по-скъпи от тези със сачми. Те се изработват в комплект с колонките и втулките и не могат да се използват отделно, защото ролката е изпълнена с профил, чиято средна част отговаря точно на диаметъра на колонката, а външната част на диаметъра на отвора на втулката. При ролковото водене е допустима значително по-малка предварителна стегнатост, от посочената по-горе. Основното изискване към възли със сачмено или ролково сепараторно водене, е висока повърхностна твърдост и изключителна гладкост и точност на формата – всяко отклонение увеличава стегнатостта и рязко намалява техния живот. По тези причини се препоръчва в щанците за едро серийно и масово производство да е използват нормализирани водещи комплекти, доставени от известни фирми.
Конструкцията на направляващ възел със сачмено сепараторно водене за щанца с плаваща водеща плоча е показана на Фиг.8-7.
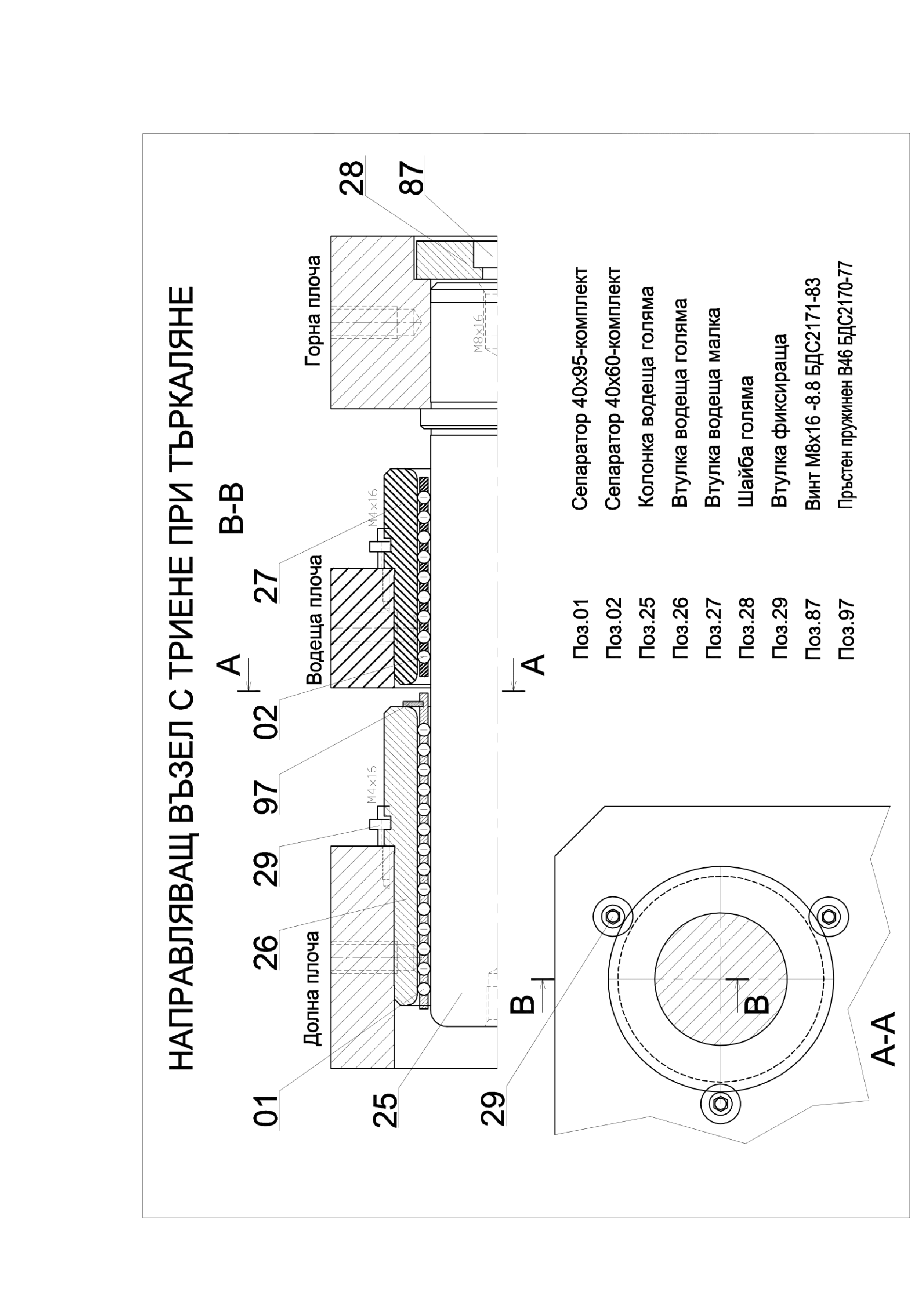
Фиг.8-7
В него колонката (поз.25) е закрепена в горна плоча чрез шайба (поз. 28) с винт (поз.87) и може да се разглобява при необходимост. Сглобката е с минимална хлабина (до 0.007 mm). Прилагането на стегнатост води до задиране при демонтаж и не е подходящо решение за инструменти, при които се предвижда общо заточване на матрици или поансони и свързаното с него разглобяване на колони. Колонката се води по втулките (поз.25, поз.27) чрез сачмените сепаратори (поз.01, поз.02). Втулките се задържат срещу изваждане от отворите в плочите посредством винтове и фиксиращи втулки (поз.29), чийто борд влиза в съответни канали. Тази концепция поволява лесно изваждане на подвижния от неподвижния пакет, като сепаратора се задържа от пропадане в отвора на втулката от пружинен пръстен (поз.97). Извадените частите от подвижния пакет (плочи и поансони) остават центровани. Чертежи на колонка, водеща втулка и сачмен сепаратор са показани на Фиг.8-8, Фиг.8-9 и Фиг.8-10.
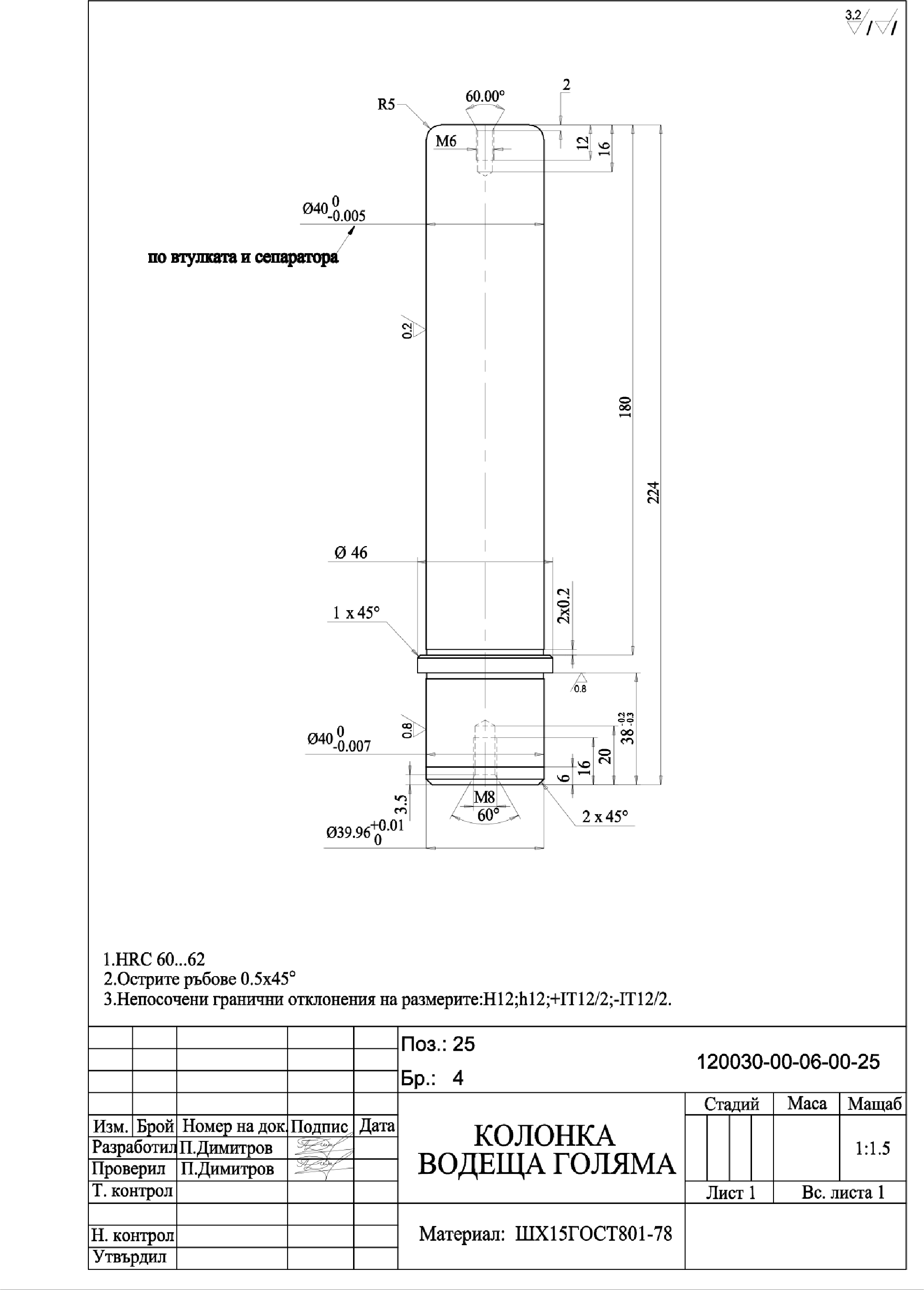
Фиг.8-8
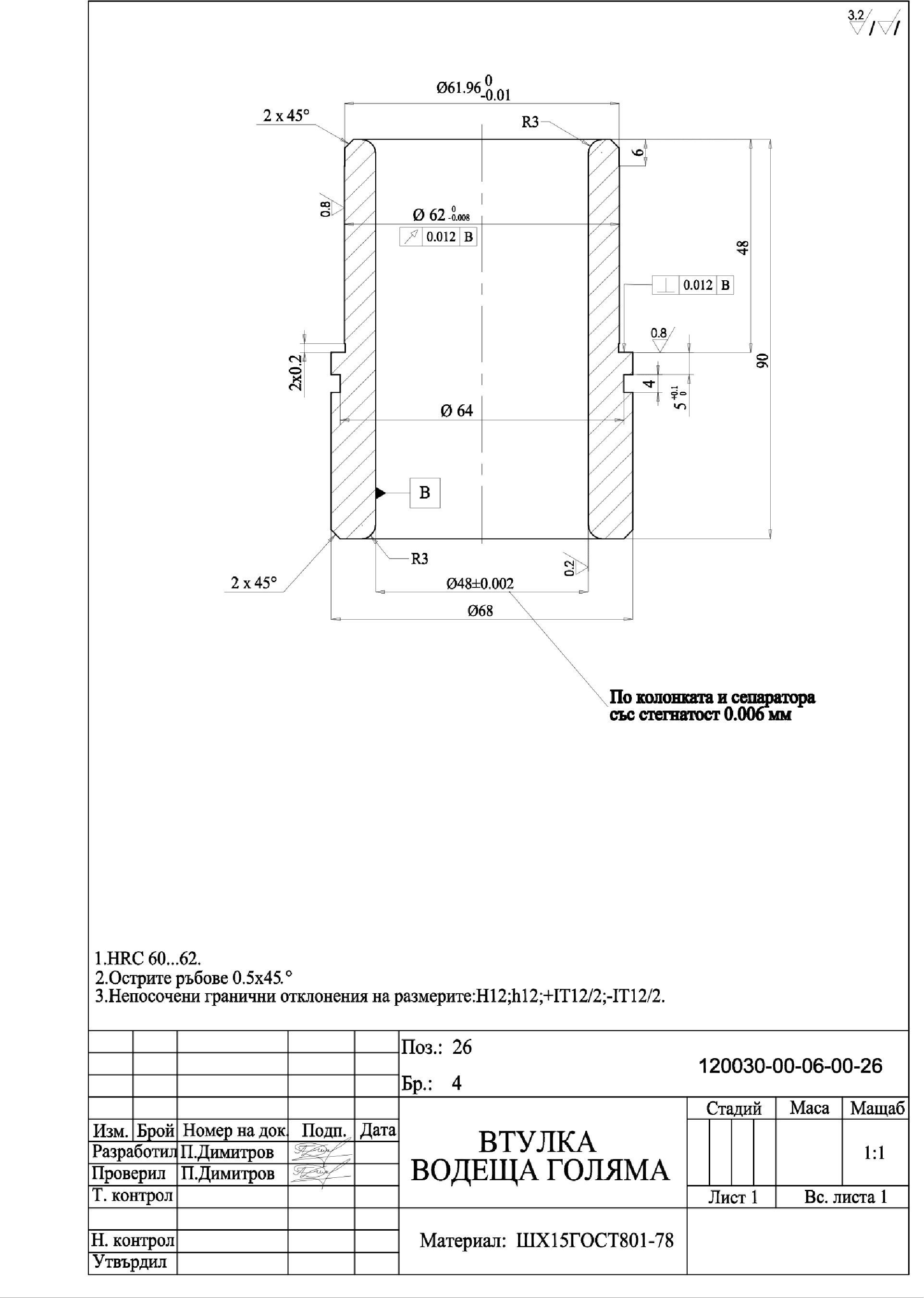
Фиг.8-9
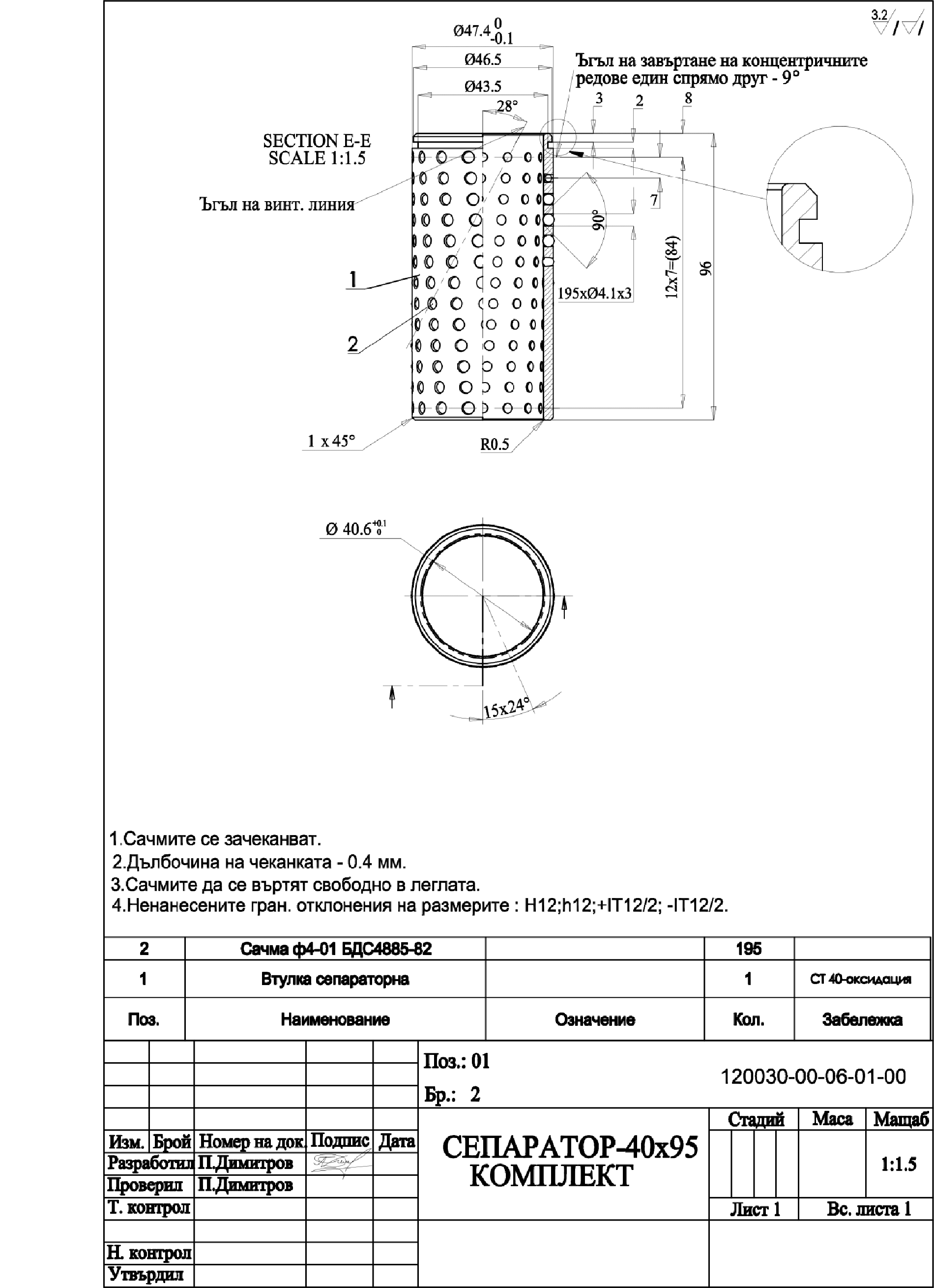
Фиг.8-10
Сепараторната втулка се изработва основно от месинг или алуминий, но за малки размери се използва пластмаса. Последните два материала са подходящи за инструменти, предназначени за експлоатация на високо скоростни автоматични преси (честота над 500 хода в минута) заради по-малката маса и инерционни сили. При работа на обикновени ексцентър преси в ръчен режим или на хидравлични преси, е допустимо използване на конструкционна стомана с оксидация за сепараторната втулка (виж Фиг.8-10). Описаната конструкция на направляващ възел със сачмено сепараторно водене за щанца с плаваща водеща плоча може да се изпълни и с фиксирана колонка (поз.8) в долна плоча (поз.1) от Фиг.5-29, което е допустимо при малки щанци, защото при демонтаж на подвижния пакет извадените частите – плочи и поансони е възможно да се разместят (вече не се центроват с колонки). По-добър конструктивен вариант е при фиксирана колонка (поз.15) във водеща плоча (поз.05) с фланец (поз.18) от Фиг.6-45, където вследствие на намалението на работната дължина на колоната наполовина спрямо зоната на закрепване, възможната деформация (провисване) се намалява 8 пъти (увеличена коравина на конструкцията). Извадените части от подвижния пакет (плочи и поансони) остават центровани с горната част от колонката. В тази конструкция е предвидена задържаща втулка (поз.30), чрез която се изважда заедно с подвижния пакет и долния сепаратор, като по този начин той остава центрован и при хода надолу безпроблемно заема необходимото положение за монтаж. Така щанцата може да работи с по-голям ход, при който колонката излиза извън водещата втулка.
– Конструкции без направляващи части.
В някои щанци при малки серии за производство е възможно да не се използват направляващи части - например Фиг.6-3 (щанца за изтегляне). В този случай се разчита на направляващите на пресата, които обикновено са с по-голяма от необходимата за щанците хлабина, което предизвиква преждевремено износване на матрицата и поансона. Когато трайността на активните части не е от значение, отсъствието на втулки и колони води до значително опростяване и поевтиняване на щанцата, поради което е напълно оправдано. Центроването за щанцата от посочения пример се извършва с поставена изтеглена заготовка между матрицата и поансона, след което те се затягат леко към пресата, плъзгача се вдига в горно положение, изважда се заготовката и се извършва окончателното стягане на инструмента. Разбира се, този метод изисква голям опит от настройчика и не е подходящ за всички операции (наример пробиване или изрязване на тънък материал). За режещи щанци може да се използва неподвижна водеща плоча, която изпълнява функциите и на водач за поансоните и подвижния пакет и събувач на лентата, подобно на Фиг.6-14 (без поз.14, поз.17). Друго масово срещано решение за инструмент без направляващи части се използва при огване на метални листове с абкант.
Конструрането и изработката на направляващи части с триене при плъзгане – колонка и водеща втулка, се препоръчва само за специални случаи, когато не може да се осигури използване на нормализирани водещи елементи, поради недостатъчно място като случая от Фиг.6-63 (на пример за водене на долния притискач). Качеството на продаваните нормализирани направляващи елементи е много високо и трудно може да се постигне от всяка инструментална.
1.4. Позициониращи заготовката или лентата части на щанцата.
Позициониращите части центроват заготовката или лентата спрямо матрицата и поансона на всяка работна позиция и са определящи за точността на щанцования детайл. Изключение от това правило се среща само за щанци със съвместно действие, които едновременно пробиват отвори и изрязват външен контур и при най-простите едно операциони щанци за изрязване на контур без отвори (виж Фиг.6-1 ). При тези видове точността на центроване на заготовката или лентата не влияе на точността на щанцования детайл, която зависи от точността на изработка на активните части.
В зависимост от предназначението им, позициониращите части могат да са подвижни или не подвижни спрямо заготовката и лентата.
– Подвижни части – ловители.
Те се монтират в подвижния пакет и при неговото движение към заготовката влизат в контакт с нея и я центроват преди контакта и с поансоните. Конструктивно те са изградени от преходна зона, която има задача плавно да измести заготовката, фиксираща част, която трябва да задържи заготовката в необходимото положение и глава или стъпало, които трябва да противодействат на силите от триене да отскубнат ловителя от неговото легло. Формата на напречното сечение (фиксиращата част на ловителя) зависи от конкретния детайл и контактната зона. Когато е възможно, за центроване на лентата или заготовката се използват цилиндрични ловители - Фиг.8-11, които лесно се изработват от стандартни поансони по DIN 9861 с доработка на преходната част с конус или радиус. За правилна работа, между отвора в заготовката и диаметъра на ловителя, е необходима хлабина (минимум 0,02 mm). В обосновани случаи (например центроване на заготовка с дебелина 0,1 mm), е възможно да се използва конусна повърхнина, която да се наглася осово спрямо отвора и да гарантира нулева хлабина. Доколкото такъв ловител трябва да е подвижен осово за нагласяне на конусната повърхнина, реалната грешка ще зависи от неговата хлабина спрямо водещия отвор.
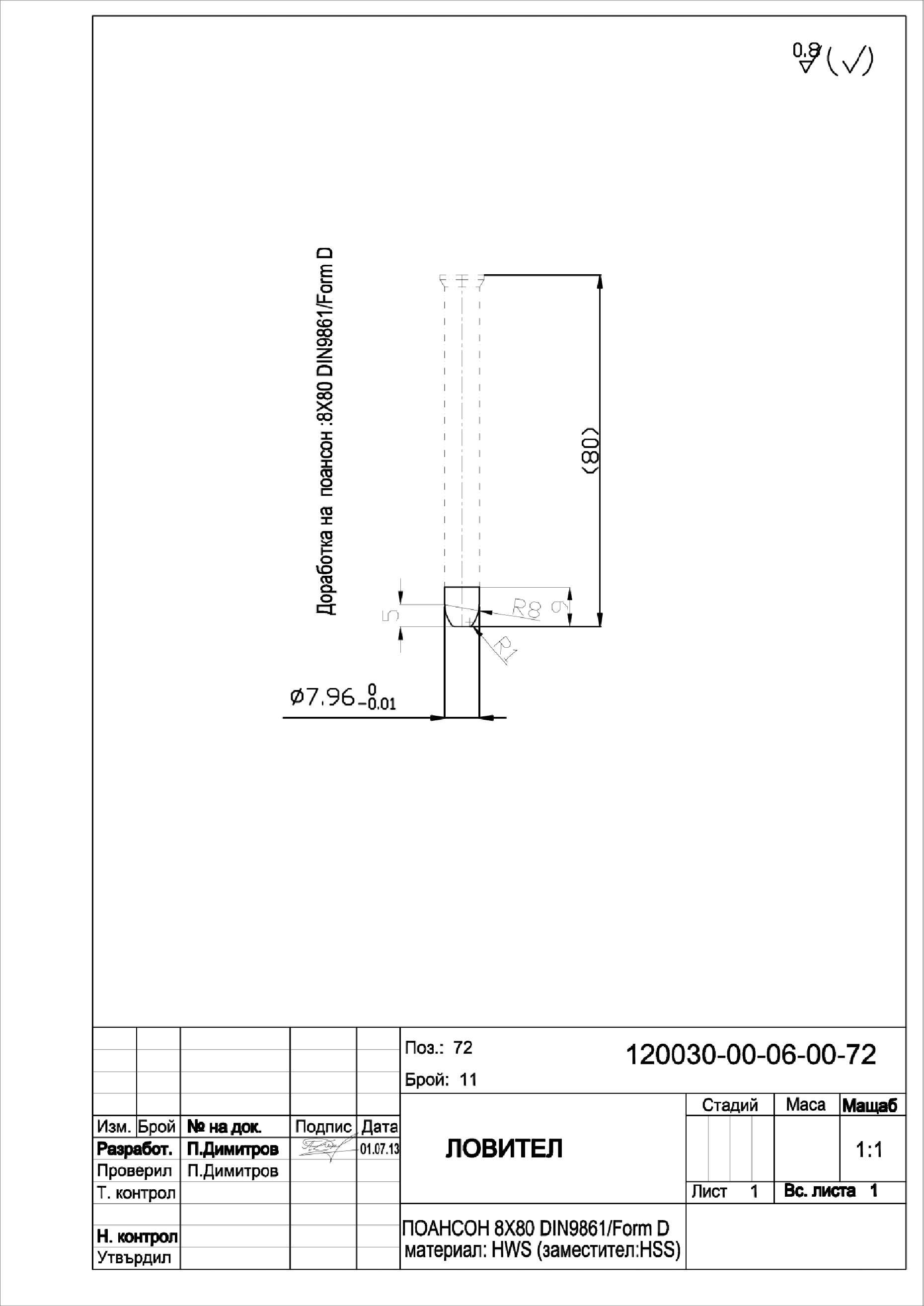
Фиг.8-11
При щанците, предназначени за работа на автоматична преса, се предвижда изключващ ловител от Фиг.7-13, който задейства прекъсвач или датчик, изключващ пресата при грешно подаване на стъпка. Когато е възможно (в щанцата има достатъчно ловители), той се изработва с по-голяма хлабина (минимум 0,08 mm) за да се избегне безпричиното спиране на пресата от триенето му с отвора. Конструкцията на ловителите може да е твърда - Фиг.6-14 (поз.19) или плаваща под пружини - Фиг.6-46 (поз.100). Първия вид кострукция е проста за изработка, но има огромен недостатък. При грешно подаване на стъпка, той попада над плътен материал и се превръща в поансон, който изтегля или скъсва материала. Освен якостни проблеми, при това явление е затруднено изваждането на лентата и понякога изисква сваляне от пресата и разглобяване на щанцата. Поради тази причина, обикновено се използва при щанци за ръчна работа.
Второто конструктивно решение на ловител, няма този недостатък. При грешно подаване на стъпка, той попада над плътен материал и възникващата осева сила свива пружината, което позволява скриване на ловителя в притискача. Това решение се препоръчва за тънки ловители и при работа на автоматична преса. Пружината над ловителя трябва да се избере по коравина така, че нейната сила да е достатъчна за преодоляване силите на триене при нормална работа, но да е значително по-малка от необходимата за пробиване или изтегляне на материала. Максимална деформация на пружината трябва да позволи свиване до стойност, представляваща сума от първоначалното свиване, височината на стърчащата част на ловителя извън притискача и целия работен ход на поансоните. Конструкциите с плаващ подпружинен ловител имат две разновидности. В разгледана на Фиг.6-46 конструкция, ловителят (поз.100) е поставен в ограничителна втулка (поз.99), която ограничава височината на ловителя под притискача. Така ловителя е неподвижен спрямо притискача при нормални условия и не се движи при работния ход на поансоните надолу, което увеличава неговия живот.
Втората разновидност на плаващ подпружинен ловител е показана на Фиг.5-30, където главата на ловителя (поз.51) се ограничава от поансонодържача. Това води до движение на ловителя спрямо притискача и лентата заедно с поансоните при работния им ход, което предизвикава по-голямо износване и намалява неговия живот. Тази конструкция се препоръчва само при малък работен ход на поансоните (до 4 mm).
– Неподвижни части – фиксатори и упори.
Фиксаторите - Фиг.8-12 се монтират в неподвижния пакет и заготовката влиза в контакт с тях, когато я центроват преди контакта на поансоните с нея.
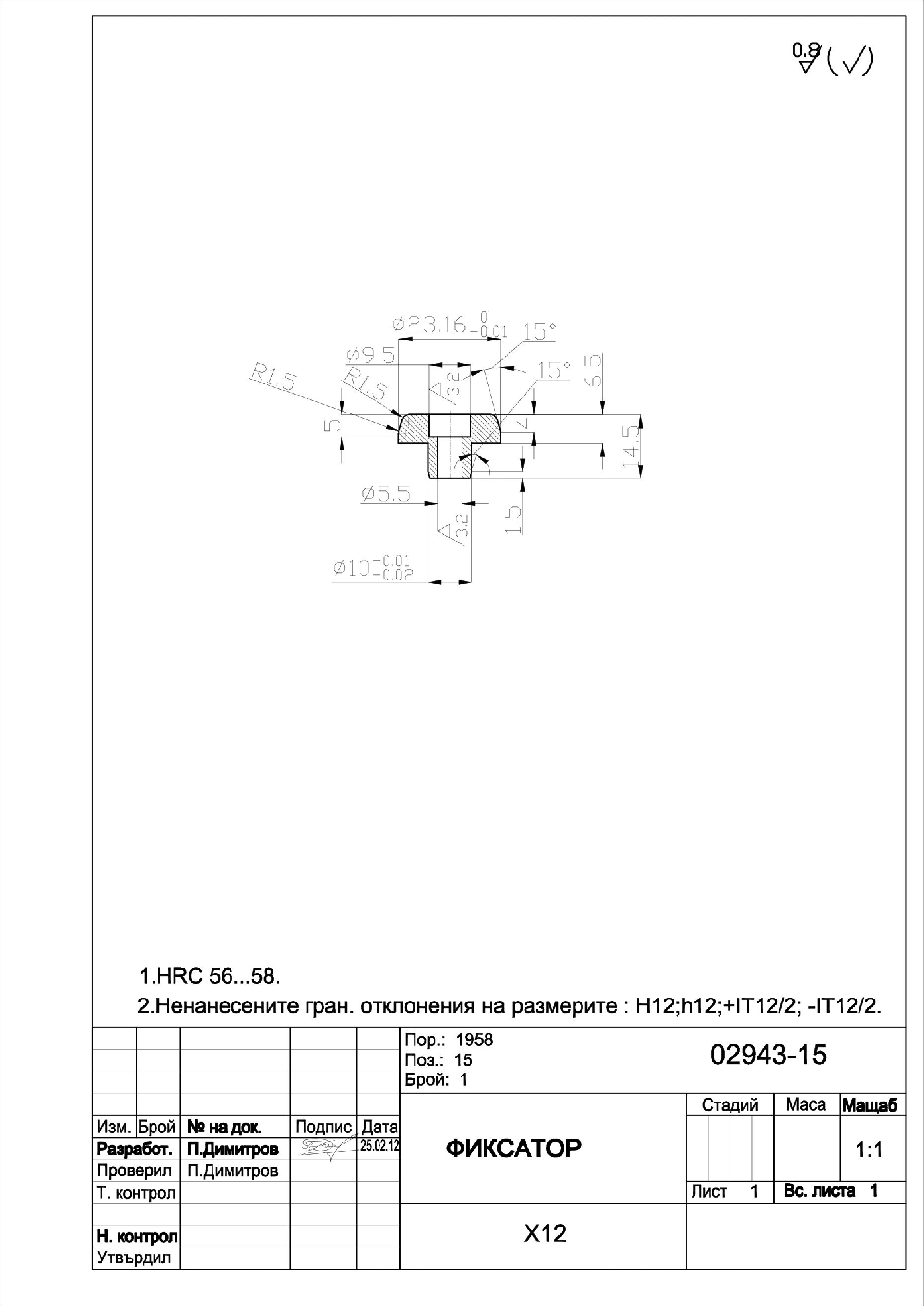
Фиг.8-12
Конструктивно, те също са изградени от преходна зона, която има задача плавно да насочи заготовката и фиксираща част, която трябва да задържи заготовката в необходимото положение. Формата на фиксаторите зависи от повърхнините, по които ще центроват заготовката. Тяхното задържане на място срещу силите на триене може да се извърши по различни начини – с винт (виж Фиг.8-12), с глава или стъпало, дори чрез запресоване в отвор. В някои случаи за фиксатор се използват плочки с малка дебелина, в които е изпълнен профилен отвор за центроване на заготовката по външния контур.
Упорите се монтират в различни зони на неподвижния пакет и най-често ограничават преместването на лентата или заготовката в някъква посока. В зависимост от тяхното предназначение може да са:
– основни за ограничаване стъпката на подаване на лентата след стъпков поансон от Фиг.5-28 (поз.27 от разрез D-D) и от Фиг.8-13;
– крайни за ограничаване стъпката на подаване на лентата след нарязването и от Фиг.6-17 (поз.73);
– предварителни (временни) за определяне началното разположение на лентата от Фиг.6-17 (поз.64).
Конструктивно се изпълняват като неподижни упори от Фиг.5-28 (поз.27) и подпружинени потъващи упори от Фиг.6-17 (поз.64). Последния вид се използва, когато трябва да позволяват свободно премонаване на лентата. При възможност, упорите се проектират да съвместяват повече от една функция – например предварителен упор с повдигач, лентоводач с упор и събувач на лентата, предварителен упор със страничен притискач и събувач на лентата от Фиг.6-46 (поз.62).
Позициониращите части се изработват от легирана инструментална стомана и се закаляват до HRC 58.
1.5. Отделящи заготовката или лентата части на щанцата.
Тези части осигуряват подвеждането на заготовката или лентата към работната позиция и нейното отвеждането (изваждането) след края на работния ход. За подвеждането се използват различни видове лентоводачи, а за изваждането повдигачи, избутвачи, изхвъргачи и отлепватели. Често те съвместяват по няколко функции – на пример изхвъргач с притискач.
Лентоводачите конструктивно могат да са изпълнени цели - Фиг.8-14 или съставни, армирани с твърдосплавни вложки в изработени канали - Фиг.8-15.
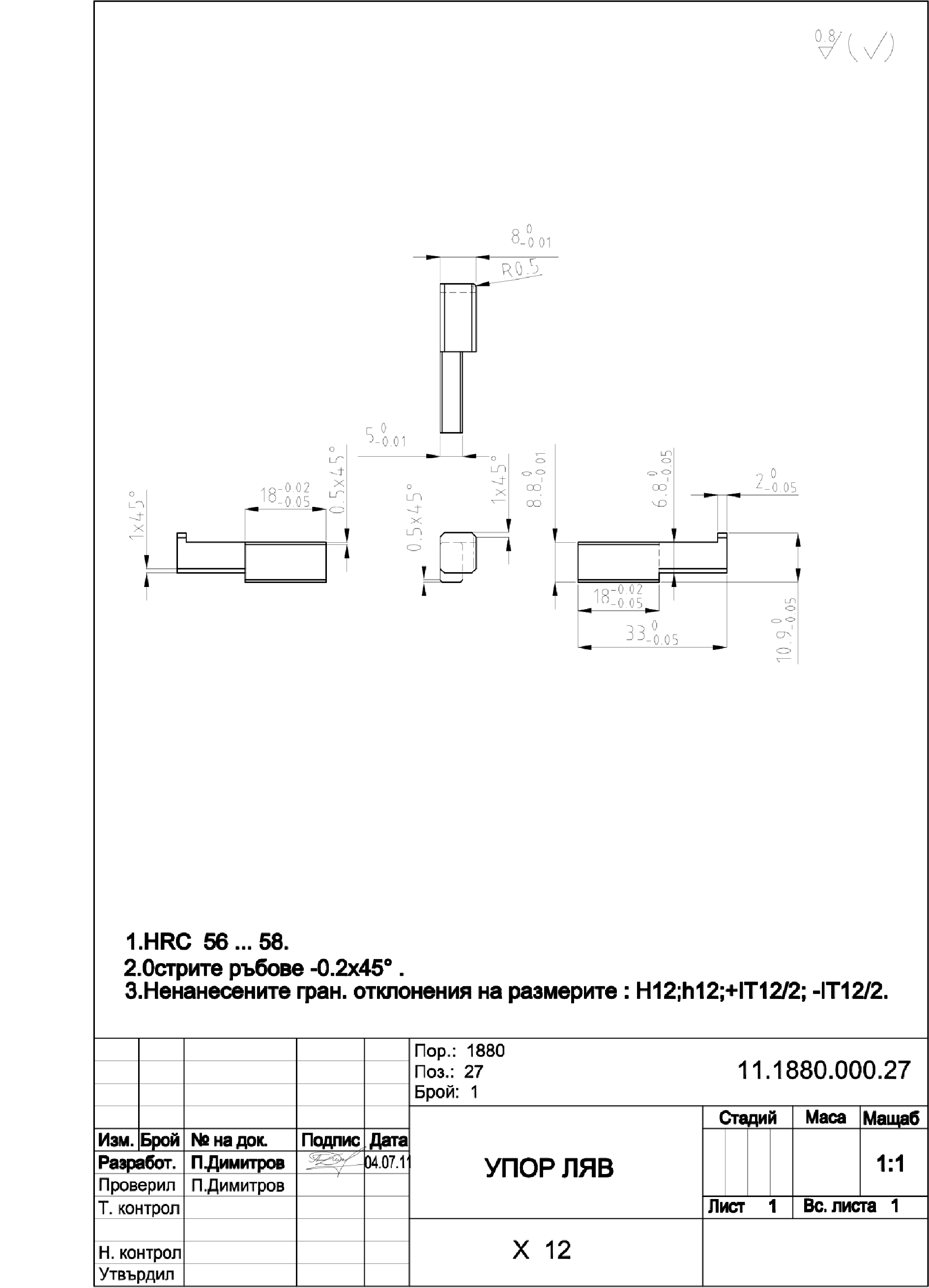
Фиг.8-13

Фиг.8-14

Фиг.8-15
Разгледаните лентоводачи са непрекъснати и гарантират водене на заготовката по цялата им дължина. Както беше споменато, те изпълняват и други функции – събуване на лентата от ловителите при отваряне на инструмента, а в някои случаи и упор за ограничаване на стъпката на подаване на лентата. Обикновено, те се центроват към матрицата с щифтове и се задържат с винтове. По някога се налага да се използват местни лентоводачи, които практически са прекъснати и имат много малка дължина, не позволяваща надежно водене на заготовката или лентата. Затова се използват групи от такива лентоводачи с подходящо разположение, осигуряващо контакт на лентата с нова група, преди излизането и от старата. Те могат да са оформени като неподвижни лагерни ролки и като плаващи подпружинени повдигачи с цилиндрична форма - Фиг.8-16 или призматична форма - Фиг.8-17 (чертеж 11.1880.000.20).
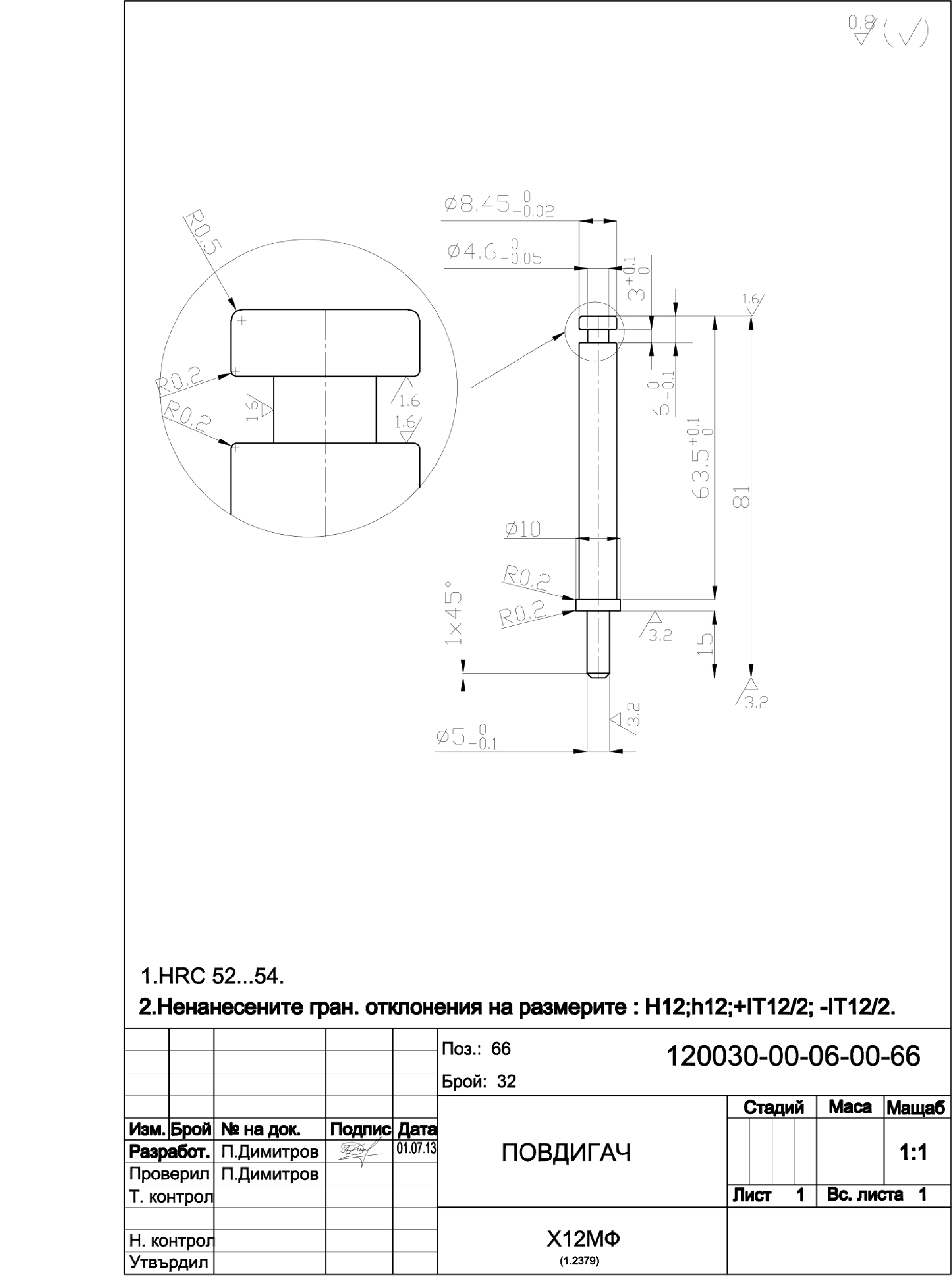
Фиг.8-16
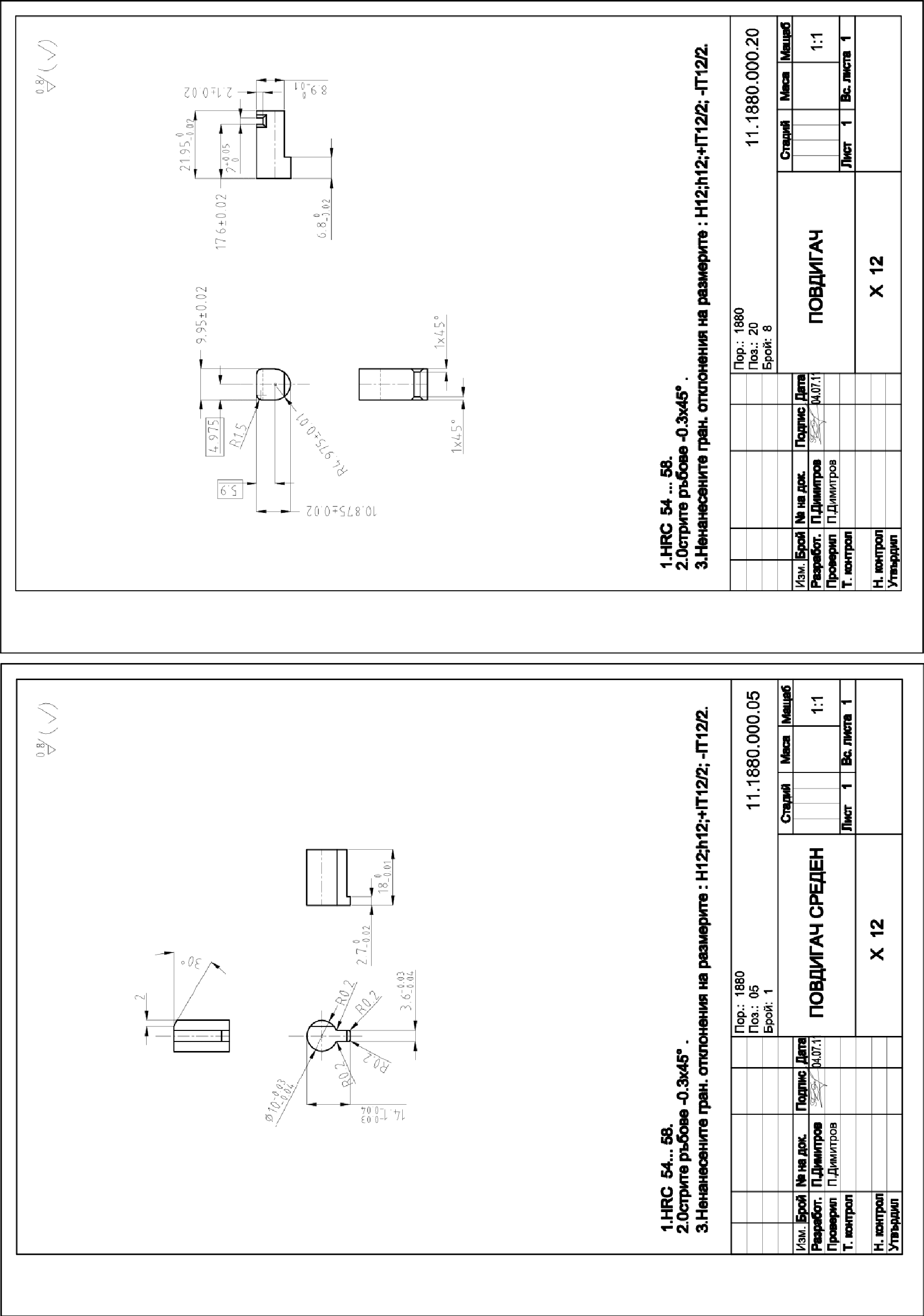
Фиг.8-17
В горната част на плаващите повдигачи са изработени канали, в които лентата се движи с достатъчна хлабина. Всяка страна на каналите има своя функция – долната повдига лентата, страничната я ограничава и насочва по дължина на щанцата, горната събува лентата от ловителите. Този тип лентоводачи-повдигачи имат предимството, че независимо от големината на пружинната сила, чрез принудително натискане върху повърхнината над канала от притискача, те се потапят в матрицата без да предизвикат деформации върху лентата, колкото и податлива да е тя. Дългогодишният опит от използването на плаващите лентоводачи-повдигачи показва, че по-надежни са призматичните от Фиг.8-17 (чертеж 11.1880.000.20). Макар и по-сложни, те водят много по-сигурно лентата и при тях не се наблюдава деформация и изскубване на лентата над канала при събуване. Употребата им в щанците с последователно действие налага, те да повдигат лентата на еднаква височина, която в разгледаната конструкция се задава от ограничаващо стъпало или борд. Заточването на режещите матрици обаче, след време ще доведе до прекалено високо повдигане на лентата, което в много случай нарушава правилната работа на щанците. В тези случаи се препоръчва конструкцията на повдигача (поз.56) от Фиг.6-46, който в долната си част има резбови отвор, свързващ с винт и ограничителната шайба. Така, при необходимост повдигача се шлифова от долната страна, с което може да се гарантира необходимия ход на повдигане.
Повдигачите могат да се изпълнят с различна форма и конструкция, в зависимост от място на повдигане. Най-прости за изработка са цилиндричните, но те рядко са надеждни и при сложни детайли се препоръчват профилните от Фиг.8-17 (11.1880.000.05). Повдигaчите са задължителен елемент от конструкцията за всички щанци с формоизменящи операции и само за тези щанци за разделителни операции, където отрязаната заготовка се връща в лента или изважда обратно над матрицата. Препроръчително е да се използват и при щанците за разделителни операции, работещи на автоматични преси с подаващо устройсто, за да се елиминира влиянието на чепаците от рязане. В този случай те изпълняват по-скоро функцията на отлепвачи на лентата, които облекчават подаването.
Отлепвачи на заготовката или лентата задължително се използват за много тънки детайли или ленти, които имат склонност да залепват към матрицата или поансона и могат да останат върху тях, с което да нарушат нормалното рязане. В някой случаи (силно изрязани и тънки ленти), такива подпружинини отлепвачи се поставят в притискача за да помогнат за събуване на лентата от ловителите - Фиг.6-47 (поз.72). Такива отлепвачи имат ход до 1mm. Отлепвачи са необходими и при ръчно залагане на заготовки за огъващи, изтеглящи, обрязващи операции, когато заготовката е с фланец или плоска част, която остава залепена за матрицата и детайла трудно може да се извади ръчно.
Отделящите части се изработват от инструментална стомана и се закаляват в зависимост от материала, предназначението и конструкцията им в интервала HRC45 - 56.
2. Спомагателни части на щанците.
2.1. Скрепителни части на щанцата.
Всички плочи, матрици, а понякога и поансони, в щанците се свързват чрез резби посредством винтове. Най-използваня вид на винтове е с цилиндрична глава и вътрешен шестостен по ISO 4762 (DIN 912). Те задължително са с повишена якост – клас 8.8 до12.9. Понякога се употребяват и винтове със скрита конусна глава и вътрешен шестостен по ISO 10642 (DIN 7991) или стопорни винтове с вътрешен шестостен с плосък (DIN 913) или конусен край (DIN 914).
Центроването на плочите, матриците, а понякога и на поансоните се извършва чрез закалени цилинични щифтове по ISO 8734 (DIN 6325) . За глухи отвори се прилагат закалени цилинични щифтове с вътрешна резба в единия край (DIN 7974), които при необходимост могат да бъдат извадени от глухия отвор чрез винт или специално приспособление. Други видове винтове, гайки, шайби, щифтове се използват по изключение.
Изборът на скрепителни винтове и центроващи щифтове се извършва на база натоварването им по общите правила, разледани в курсовете по машинни елементи и съпротивление на материалите.
2.2. Буферни пружини.
Повечето щанци изискват притискане, събуване или друго действие, за което са нужни еластични елементи, наречени общо буферни пружини. В някои случаи те могат да са част от конструкцията на пресата, да са оформени като самостоятелни буферни възли за масата на пресата от Фиг.5-11 или вградени в конструкцията на щанцата от Фиг.5-23.
Винтовите пружини за натиск са най-разпространените. Те са лесни са изчисление и на пазара се предлагат пружини с различно сечение и форма на тела, от който са изработени. Препоръчват се винтовите пружини с правоъгълно сечение по ISO 10243, предназначени за различен вид натоварване: леко, с максимална деформация до 40% от дължината на пружината (зелен цвят) - Фиг.8-18;
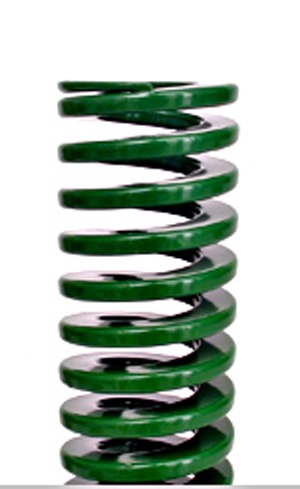
Фиг.8-18
средно, с максимална деформация до 37,5% от дължината на пружината (син цвят) - Фиг.8-19;
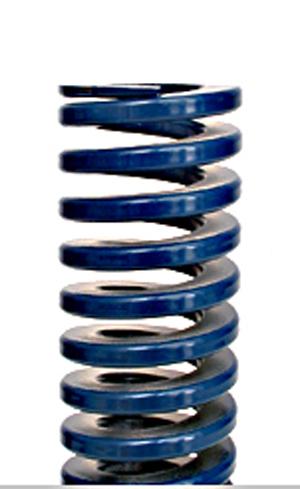
Фиг.8-19
тежко, с максимална деформация до 30% от дължината на пружината (червен цвят) - Фиг.8-20;
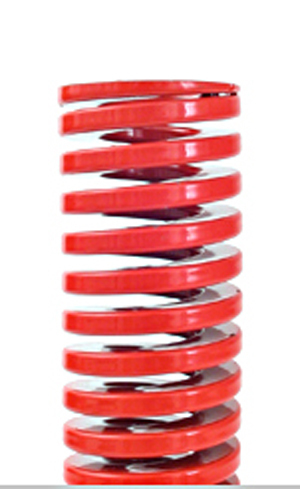
Фиг.8-20
и свръх тежко, с максимална деформация до 25% от дължината на пружината (жълт цвят) - Фиг.8-21.
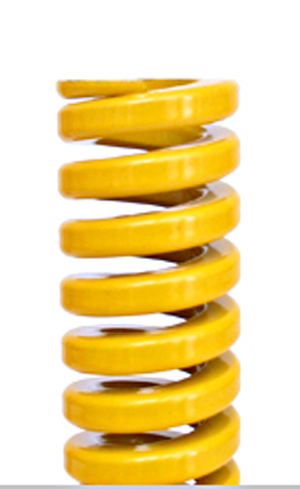
Фиг.8-21
Външните, вътрешните диаметри и техните дължини са стандартизирани, което позволява лесно преминаване от една група към друга. Тези деформации, обаче, не трябва да се залагат като работни в конструкцията на щанците – производителят е посочил в своите каталози за всеки вид до каква деформация може да се очаква живот на пружината над 1 500 000 цикъла. Наличието в каталозите на коравина на пружината в N/mm и максимално допустима деформация в mm, ги прави лесни за избор. На пружините се задава предварително свиване (над 5% от дължината), покриващо минимално необходимата сила на притискане. Основният им недостатък е, че при голям работен ход на пружината, наред с нарастване на нейната дължина, се увеличава и крайната сила, което в много случаи не е необходимо, а по някога може да е недопустимо (например при тънки детайли, които биха загубили устойчивост). Използват се и пружини с кръгло или овално сечение на тела, с различни дължини и диаметри. Основното правило при комбинацията на винтови пружини е, че последователно свързаните еднакви пружини имат максимална сила на единичната пружина и деформация, представяваща сума на максималните деформации на всичките, а паралелно свързаните еднакви пружини имат максимална сила, представяваща сума на максималните сили на всичките пружини и деформация, на равна на максималната за единична пружината.
Тарелчатите пружини представляват конусни шайби, изработени от закалена пружинна стомана - Фиг.8-22.
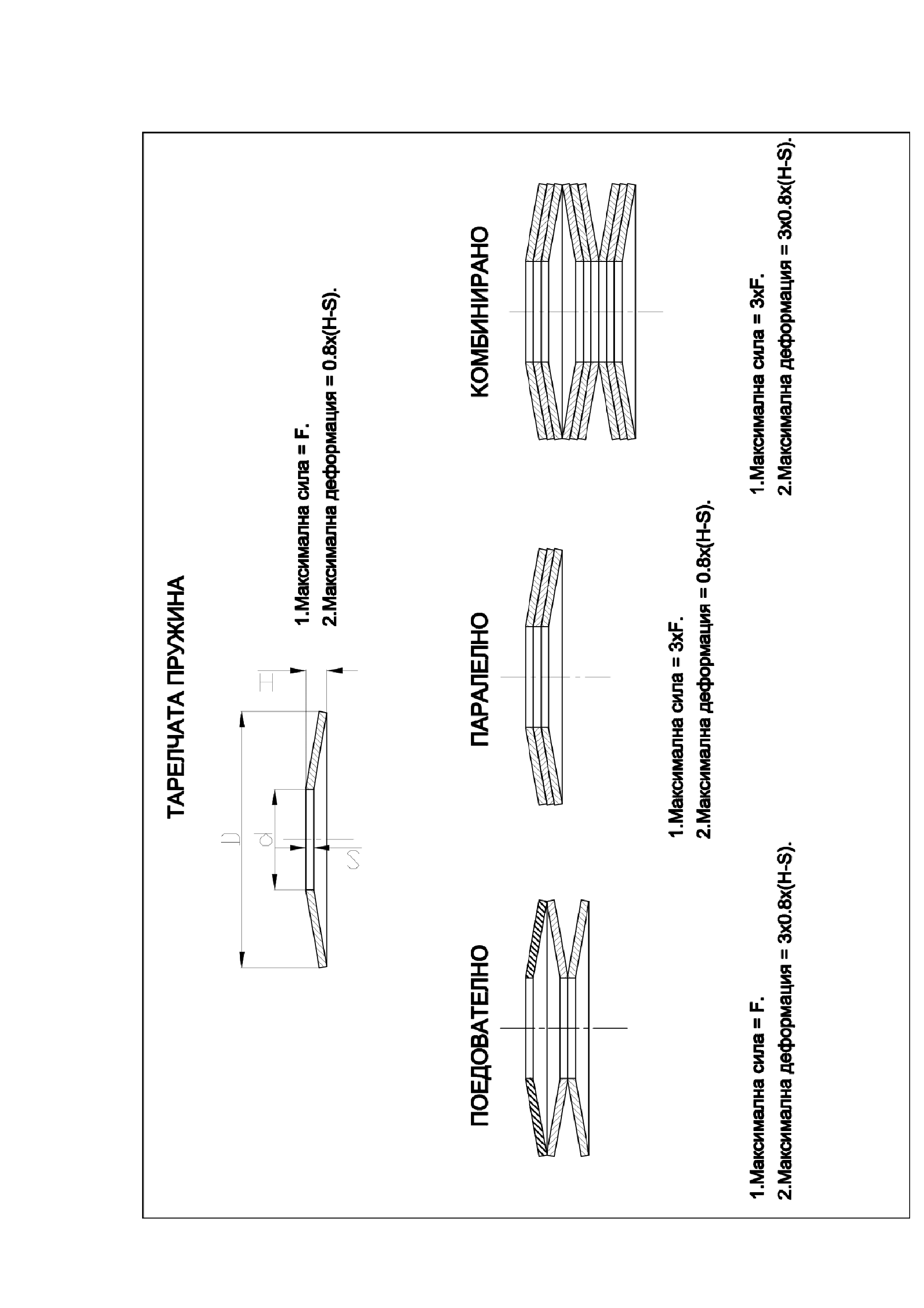
Фиг.8-22
Техните размери са по DIN 2093, но лесно могат да бъдат изработени с шанца, при необходимост от настандартни размери. Те се използват при големи сили и малки премествания. В зависимост от начина на подреждане, с едни и същи пружини се постигат различни варианти за максималната сила и допустима деформация на буферния възел (виж Фиг.8-22). За надеждната работа на такъв буфер е задължително, тарелчатите пружини да се центроват и водят с малка хлабина по закален шлифован дорник, а над и под крайните пружини да се монтират закалени и шлифовани шайби. Това изискване е свързано с деформацията им при работа, която е съпроводена от сили на триене. При необходимост от няколко еднакви буфера с тарелчати пружини, се извършва групов подбор на всеки набор от пружини така, че всеки от тях да има най-близка височна до останалите.
Полиуретанови втулки или плочки също се използват като буфери пружини. Те могат да са с различна твърдост по Шор (от 80 до 95), поради което имат различна допустима максимална деформация (от 25% до 15% от дължината). Правилото за силата и деформацията при комбиниране на полиуретанови елементи е същото, както при винтовите пружини – при последователно свързване силата остава същата, но деформацията е сума от тази за всеки елемент, при праралелното свързване силата е сума от съответната за всеки елемент, а деформацията остава същата. Полиуретанорите елестични елементи се достават на отделни втулки, на пръти с или без отвор, от които се нарязват детайли с нужната дължина. Свиването при полиуретановите буфери (над 15%) е не линейно, което трябва да се вземе впредвид при проектирането. Те имат голям хистирезис, поради което е препоръчително предварително свиване не по-малко от 6-7%, за да не се окаже след няколко стотици натоварващи цикъла, че предварителната сила е намаляла или изчезнала.
Газовите цилиндри от Фиг.8-23
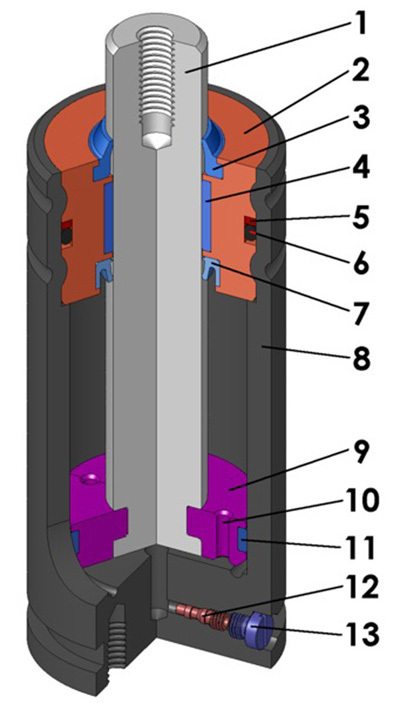
Фиг.8-23
са друг вариант на буферни пружини. Те работят на принципа на свиване на работен газообразен флуид под налягане в затворен цилиндър (поз.8) чрез прът с бутало (поз.1, поз.9). Чрез промяна на налягането в цилиндъра се променя и пружината сила. Най-разпространени са използващите азот под налягане до 200 bаr цилиндри, но се срещат специални конструкции на пневматични буфери със стандартно налягане от 6 bаr. Основното предимство на газовите цилиндри пред останалите видове пружини, е възможността за постигане на големи сили и ходове при малки размери, без увеличаване на силата с повече от 10% за целия ход. Пример за приложението на буфер от азотни цилиндри в щанца със съвместно действие за отрязване на заготовка и изтегляне е показан на - Фиг.8-24.
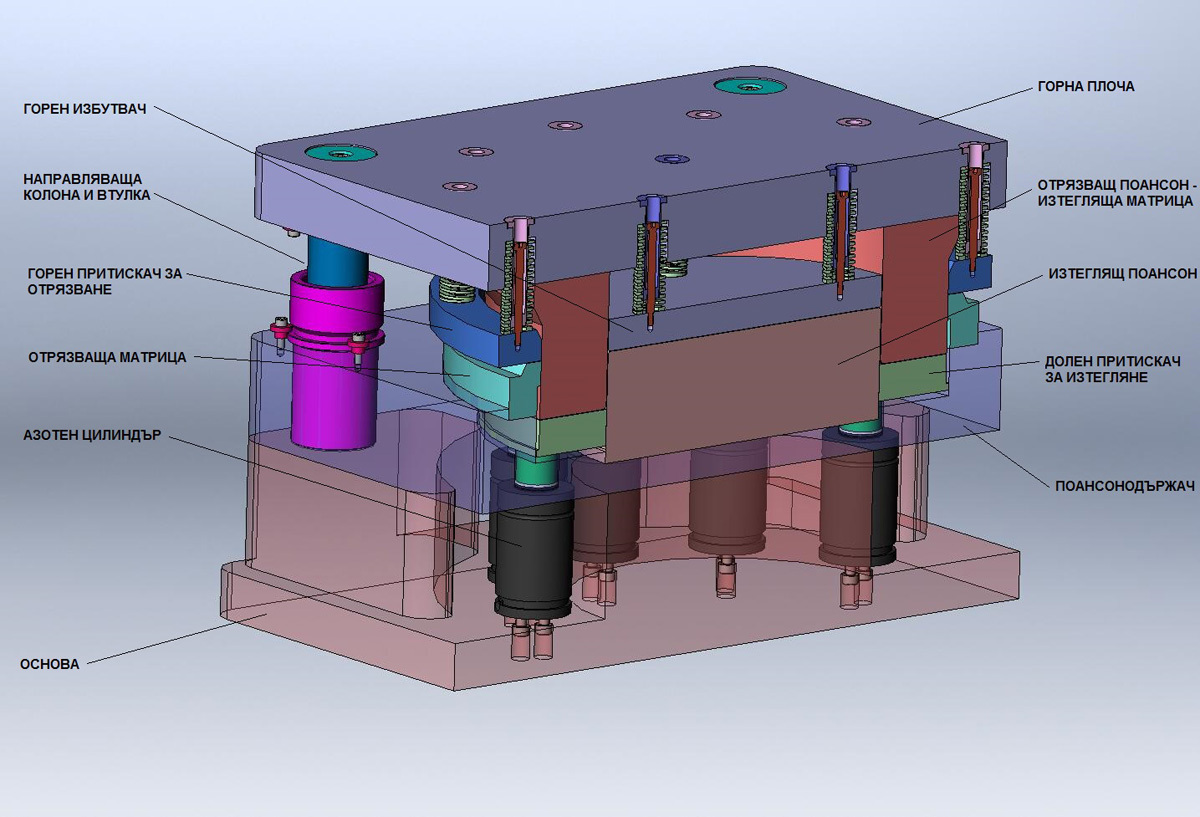
Фиг.8-24
Газовите пружини намират широко разпространение във формоизменящите инструменти за автомобилната промишленост.
Всички фирми, изработващи нормализирани части за щанците, предлагат и повечето от разгледаните видове пружини.
2.3. Предпазни части на щанцата.
Това са механични ограничители на хода. Те служат за ограничаване възможния ход на поансоните (виж Фиг.5-25) и на подвижната плоча с притискача (виж Фиг.5-20) надолу, за да се избегнат повреди по активните части. Задължителни са за работещите на хидравлични преси инструменти, където изпълняват ролята на възспиращ упор в края на работния ход, поемащ натоварването на пресата. При ексцентър пресите се използват и за настройка на долната точка на работния ход – обичайният метод е проверка за контакт, чрез отпечатък върху поставена тънка хартия. Главните изисквания към тях са, да могат да поемат силата на пресата при необходимост, да са на удобно място за визуален контрол и настройка, да могат лесно да се разглобяват при необходимост от уточняване на тяхната дължина (при режещи щанци).
Важен защитен механизъм при щанците за автоматична преса е системата за изключване на пресата при грешно подавне. Тя се състои от подпружинен изключвател (поз.84) от Фиг.6-77, получаващ сигнал при повдигане на изключващия ловител (поз.118) от изключващо стебло (поз.88), което освобождава предния му край и след преместването на изключвателя навътре, издърпва гайката (поз.86), с което се задейства индуктивен датчик или краен изключвател, прекъсващ захранването на преса. Системата реагира на повдигане на изключващия ловител, не по-голямо от 1.5 mm, което се осигурява от зоната на застъпване на изключвателя с фланеца на изключващото стебло (поз.88). Стойности под 1 mm са несигурни при работа – възможно е от триенето с лентата при началния контакт, изключващият ловител да трепне, с което да предизвиква неоправдано спиране на пресата. Системата е конструирана така, че до намеса на оператора, изключващият ловител остава блокиран в горно положение и пресата е изключена.
Добра практика е, предпазните части да се боядисват с червен цвят, за да изострят вниманието на обслужващия персонал.
2.4. Закрепващи части на щанцата към пресата.
В повечето случаи щанците се закрепват неподвижно към пресата. Изключения се срещат за някои видове преси (например винтова преса) в единичното производство, когато се изпълняват едва няколко удъра. Вида на закрепването зависи от особеностите на щанцата и самата преса – чрез винтове, планки, центроващи дорници, държачи. Най-често при малки щанци се използва задържане чрез силите на триене на цилиндричен държач - Фиг.8-25
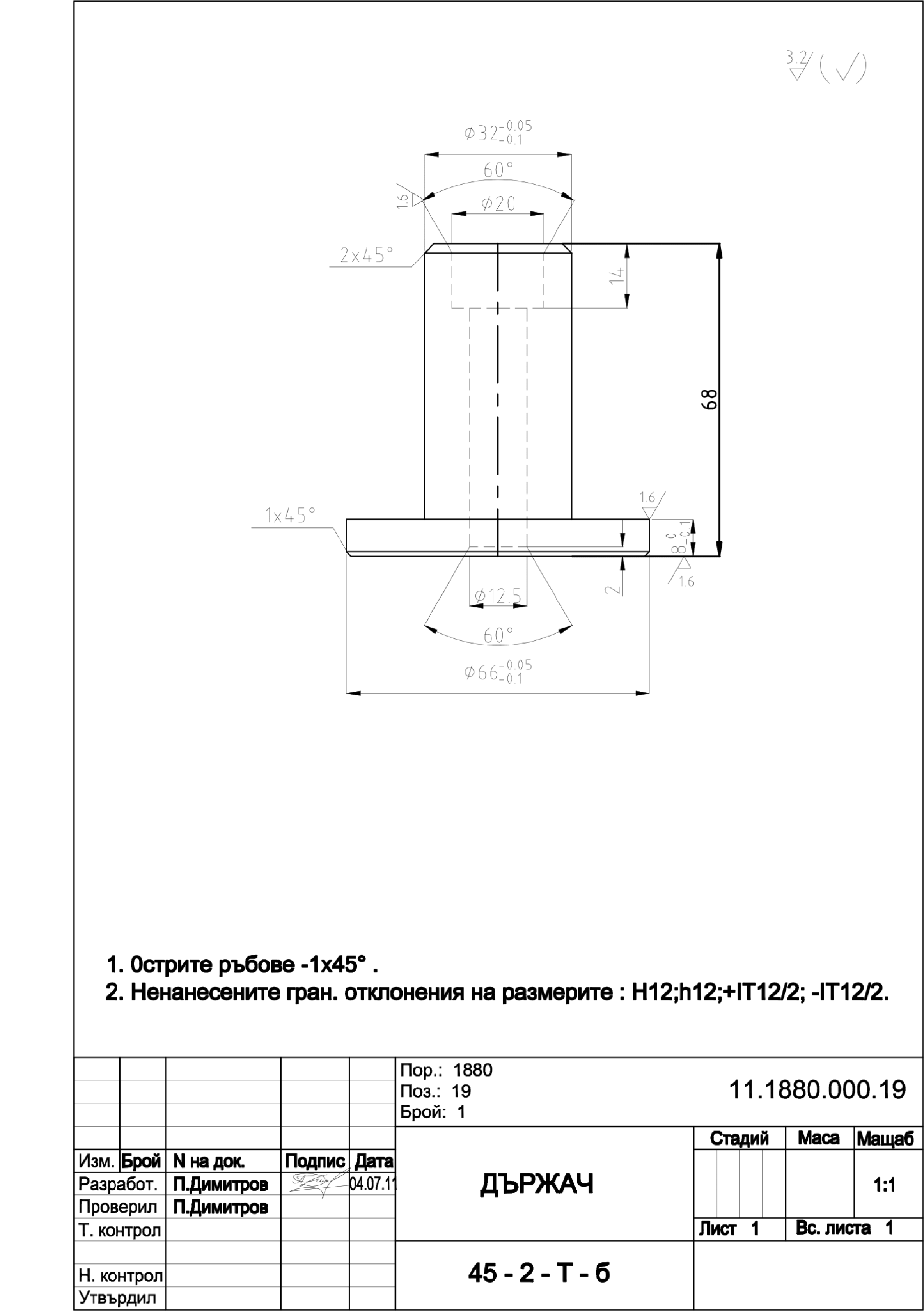
Фиг.8-25
към плъзгача на пресата. Формата и размерите на последния позволяват успоредно със задържането да се извърши и центроване на щанцата спрямо пресата. Държачът е свързан с горната плоча чрез винт. Неподвижният пакет на щанцата обикновено се закрепва към масата директно с винтове или посредством скоби и планки. В случаи на работа с прецизни щанци, на преси с недостатъчна точност на водене на плъзгача, посочения неподвижно свързан с горна плоча държач, е неприложим, защото всички грешки на пресата ще се предават на инструмента и ще предизвикат бързото му износване. Тук е целесъобразно да се използва по-сложна конструкция на плаващи шарнирни дъжачи, които притежават известна ъглова и линейна степен на свобода. Така, отклоненията при движение на плъзгача на пресата, няма да се предават изцяло на воденето и активните части на щанцата и нейната трайност до заточване или ремонт ще се повиши.
При щанците, работещи върху автоматична преса с устройство за подаване на лентата, освен центроване и закрепване спрямо центъра на масата, е необходма точна ъглова ориентация спрямо подаващото устройство и масата. При тях заедно с държача - центроващ дорник (поз.65) от Фиг.6-75 се използват допълнителни фиксатори (поз.80) или шпонки, които влизат в надлъжен канал, изработен в долната страна на плъзгача на пресата. По този начин щанцата ще е ориентирана по един и същ начин след всяко сваляне и качване.
Доставчиците на нормализирани части за щанците предлагат различни видове нормализирани държачи за тях.
2.5. Транспортни части на щанцата.
Габаритните размери на нструментите за щанцоване и тяхното тегло може да варира в изключитено широки граници – от няколко килограма до 10 тона. Затова, трябва да се обърне принципно внимание на осигурените условия за монтаж, демонтаж, транспорт и съхранение. Ако, за щанца с тегло от няколко килограма (дори няколко десетки килограма), това условие се нарежда на едно от последните места по важност, защото нейните части и самата щанца се вдигат, транспортират, качват и свалят от пресата на ръка, то при тегло от няколко стотин килограма или повече, условието заема едно от челните места по важност. В отделни случаи, когато качването и свалянето е затруднено, се търси решение, чрез разделяне на големите части на по-малки, незвисимо от конструктивното усложнение и оскъпяване на целия инструмент (например отделните щанци, техните матрици и поансони от Фиг.6-22). Като стандартно правило, в части за щанци с тегло над 20 килограма, трябва да се предприети мерки за тяхното лесно вдигане, сваляне, транспортиране с механизирани средства, например електротелфери. Обикновено за целта е достатъчно да се изработят резбови отвори на подходящи места (най-вече от страни на плочите). В тях, при необходимост от манипулация, се поставят специални транспортни халки, палци или други нормализирани части за повдигане. Чертеж на транспортен палец с висока товароносимост е показан на Фиг.8-26.
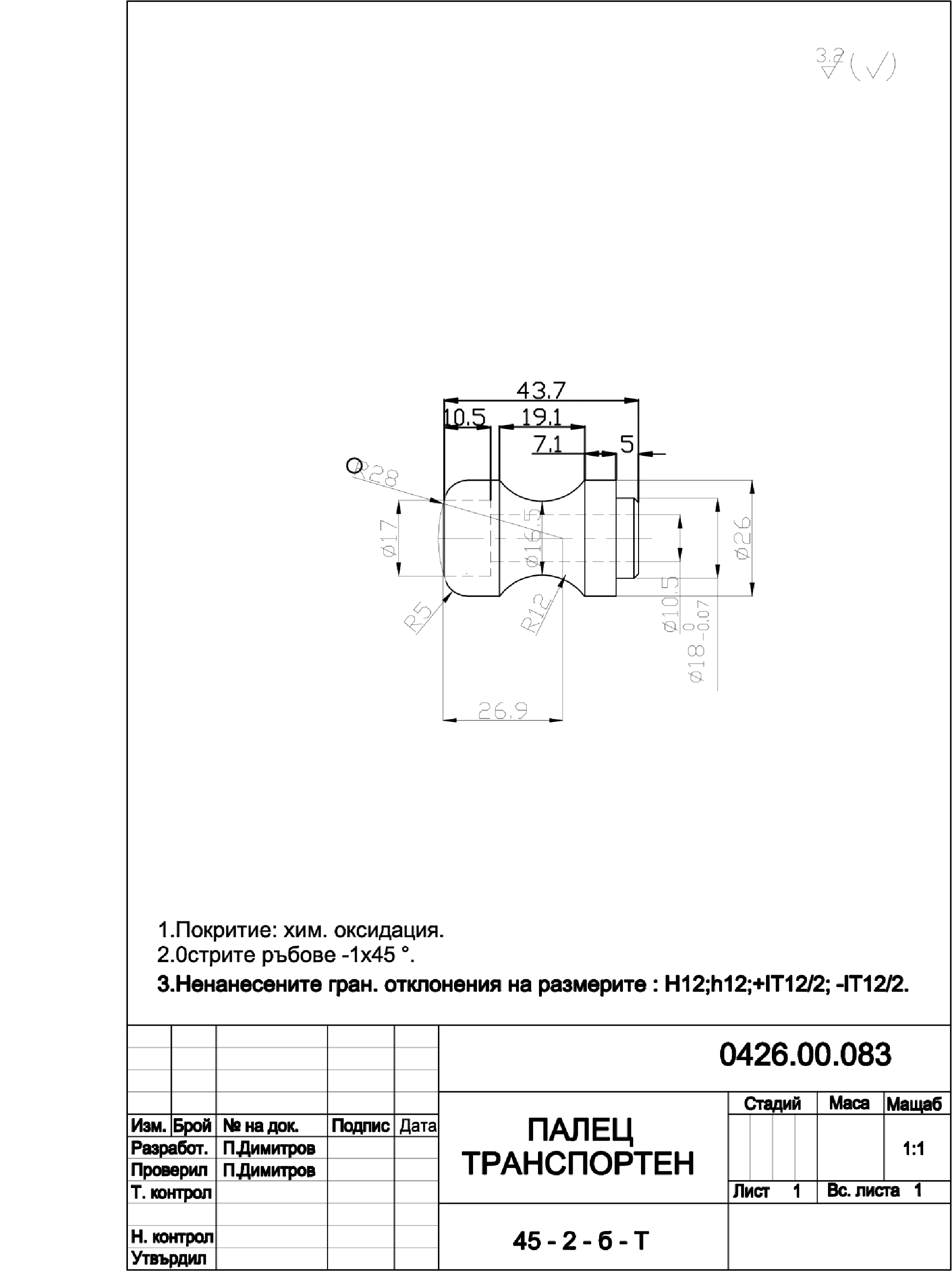
Фиг.8-26
Главната особеност е в това, че благодарение на цилиндричната повърхност, той се напасва към отвора на плочите и дори при разхлабен винт не се намалява носещата му способност. При него резбовия отвор и винта не са носещи, както при голяма част от нормализираните транспортни части и това разширява неговото поле на приложение от 50 kg до 1500 kg.
2.6. Улеи и защитни ограждения.
Улеите се използват за извеждане извън работната зона на щанците на готовиите детайли или отпадъка от лентата (поз.75) отФиг.6-17 и не допускане на смесване между двете. В повечето случаи, детайлите или отпадъците се извеждат под действието на гравитационите сили от тяхното тегло. За да се реши успешно тази задача, те се проектират под най-големия възможен ъгъл, който трябва да е по-голям от ъгъла на триене (около 6°). Оформят се така, че с отдалечаването от инструмента да се разширяват. В редица случаи, на пример при малка височина, или при отпадъци с малко тегло, тези мерки не са достатъчни. Тогава на подходящо място в или около инструмента се поставя издухваща дюза за сгъстен въздух, която да извежда отпадъка или детайла по улея и да възпрепятства неговото задръстване. Например в притискача от Фиг.5-18 е изпълнен отвор за издухване на отрязания детайл по наклона на матрицата.
В щанците с ръчно подаване на материала или заготовките, в някои случаи се предвиждат защитни прозрачни или ламаринени ограждения, които да ограничат достъпа на оператора до подвижните части, с цел предотвратяване възможностите за травми и наранявания. Техния вид изцяло зависи конструкцията и предназначението на инструмента. Те трябва да отделят всички подвижни части, където работника по невнимание може да постави пръстите си и да оставят свободни само зоните за подаване и извеждане на материала.
2.7. Други спомагателни части за щанците.
В зависимост от конструкциите на щанците, съществуват и други спомагателни части, като специални винтове, дистанционни втулки, дистанционни шайби, компенсиращи заточването подложки, закалени втулки за щифтове и други. На пример, регулиращия винт за пружина - Фиг.8-27,
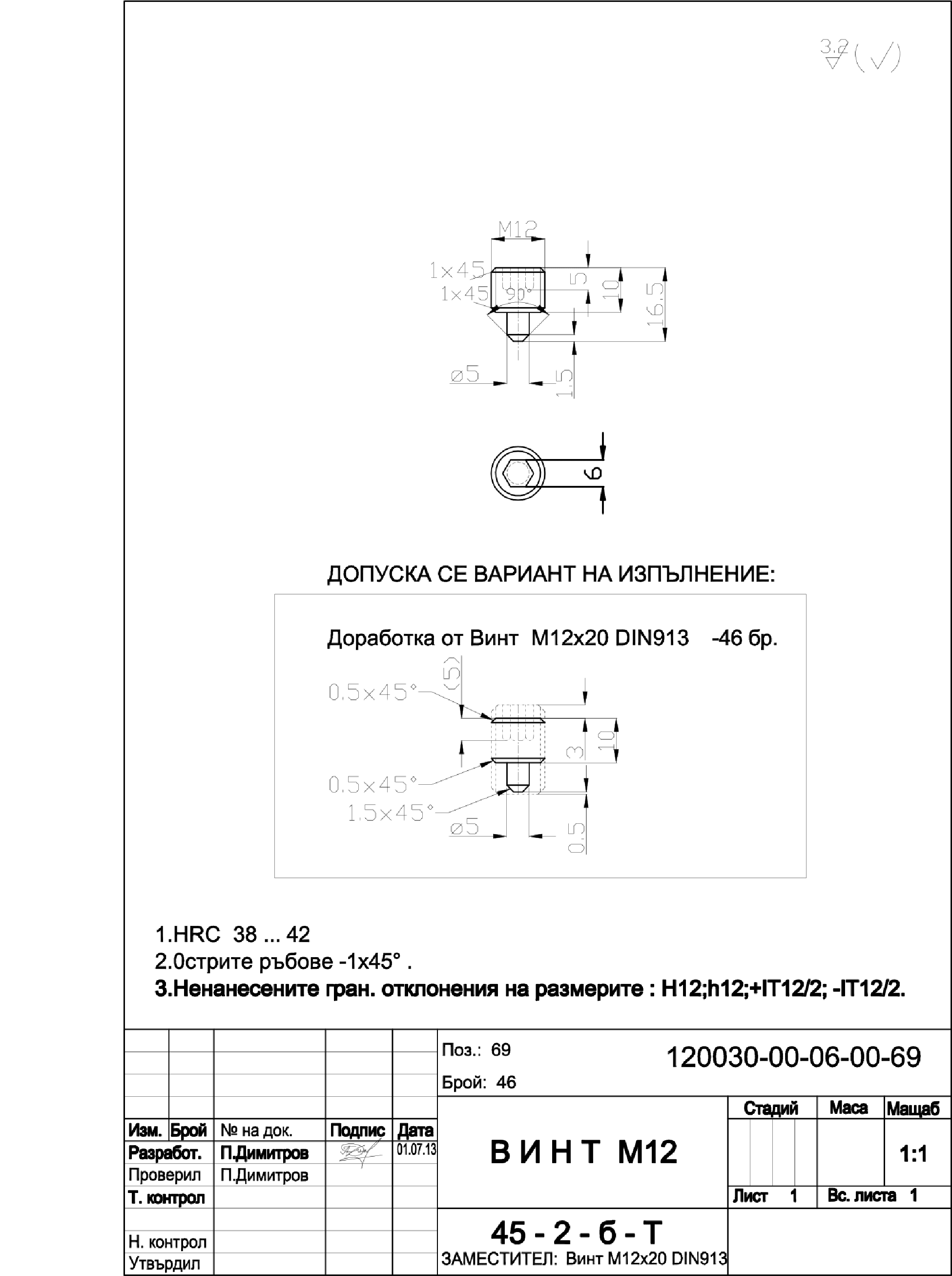
Фиг.8-27
чийто преден цилиндричен край води точно вътрешния диаметър на пружината и не позволява разместване и зацепване на нейните навивки с профила на резбата. Такова зацепване би довело до ограничаване на възможността на част от пружината за деформация, би претоварило друга част от нея, и би ускорило нейното излизане от строя. Освен това, зацепването на навивки от пружината с профила на резбата, не би позволило регулиране на нейната сила.
2.8. Информационни табели на щанцата.
Такива табели не са задължителни, но много облекчават идентификацията на щанците в големите пресови цехови. В много случаи клиентът изисква задължително поставяне на такива табели, като уточнява тяхното съдържание. Табелата трябва да дава информация за производителя на щанцата, годината на производство, идентификационен номер, детайла и операцията за която е предназначена, максимано необходимата сила и ход на пресата, марката на материала, дебелината и широчината на лентата (за режещи щанци). На пренастройващи се щанци, допълнително трябва да се поставят табели, или маркират съответните части, да се посочи включено или изключено е работното положение на управляваната част за конкретната конфигурация на детайла.
ГЛАВА 9. ИЗБОР НА ПРЕСОВО ОБОРУДВАНЕ
При разработката на идеен проект бе показано, че инструменталната екипировка за щанцоване на конкретен детайл винаги се проектира за експлоатация на определен вид преса. Не може и да бъде по друг начин, защото конструкцията на щанците освен с щанцования детайл, трябва да се съгласува с принципа на работа, размерите и конструктивните особености на пресовото оборудване. Разбира се, в началния етап е невъзможно да се определят всички изисквания на конкретния детайл за щанцоване към пресовото оборудване. Най-често в идейния проект се поставят приблизителни условия за вида на оборудването с неговата производителност, номиналната технологична сила и максимален ход, което то може да осигури. Обикновено, избора на пресово оборудване допълнително се ограничава до наличното при производителя. Основните параметри, които е трябва да се съобразят при избора на пресово оборудване, са вид, ход, номинална сила, мощност, закрита височина, размери на работното пространство, производителност и наличност на допълнителни устройства.
1.Вид на пресата.
За пресовите операции върху листов материал се използва различни по вид пресово оборудване. По долу ще бъдат разгледани само особеностите на избора за три вида от най-използваните преси, препоръчвани за различни серии и технологични операции.
1.1. Ексцентър преса с отворена „С“ – образна конструкция на тялото.
Общия вид на 25 тонна универсална ексцентър преса модел ПЕ-25А е показан на Фиг.9-1.
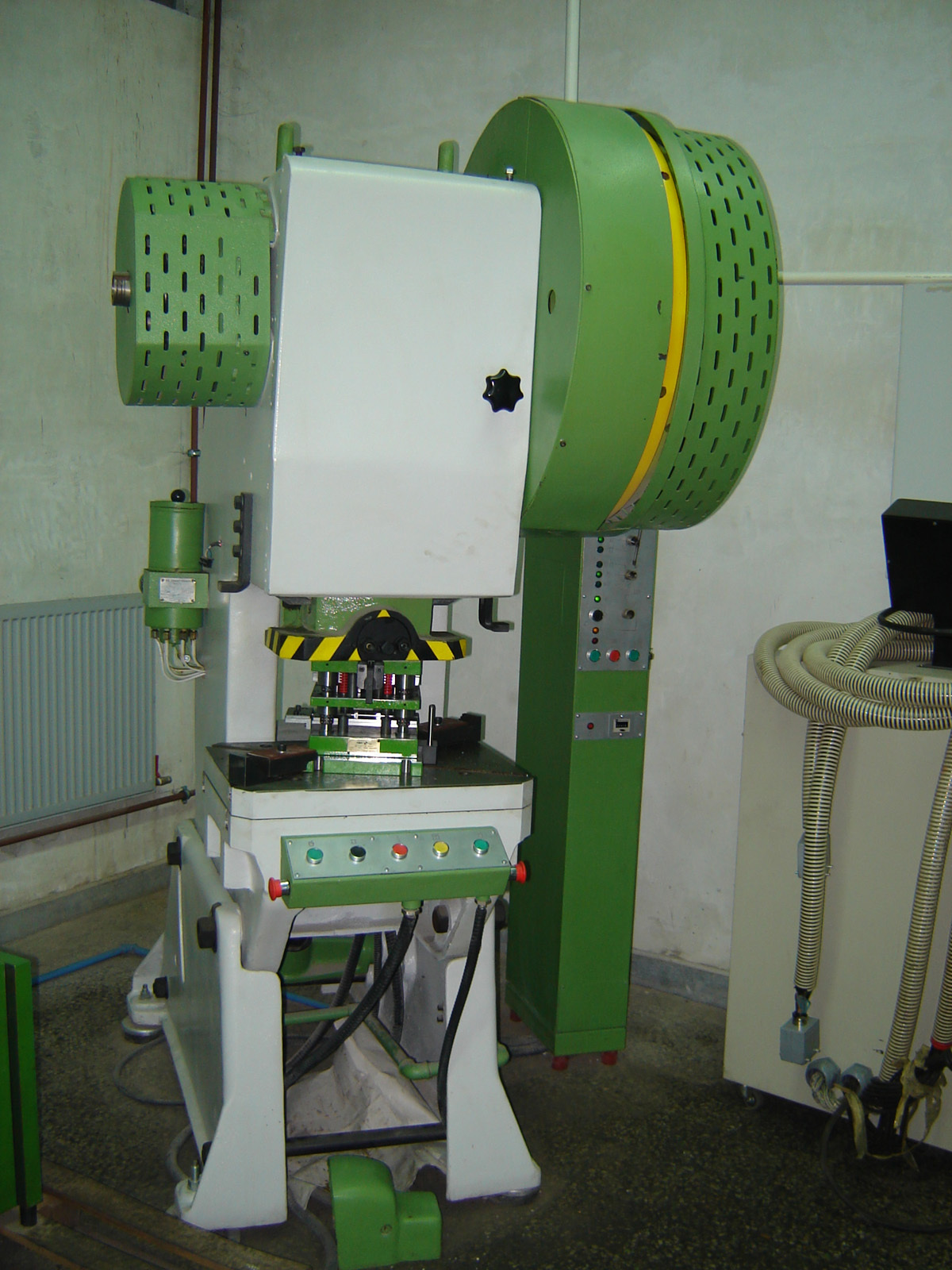
Фиг.9-1
В България са произведени серия преси от този тип с номинална сила 25 тона, 40 тона, 63 тона и 100 тона. Тези преси са с постояна скорост на главния електродвигател, но дължината на хода може да се променя от минимална, до максимална през определени дискретни стойности, различни за всеки модел. Имат вграден регулировъчен винт за настройка на височина на инструмента. Моделите за 25 тона и 40 тона позволяват накланяне на стойката с масата спрямо хоризонта, за облекчаване извеждането на щанцованите детайли или отпадък. Пресите са предназначени за работа в режим на единичен удар или на непрекъснат цикъл, като задействането може да се управлява по различен начин (с педал, с бутон, с два бутона едновременно). Защитата от претоварване е механична (разрушаваща се бленда с определена дебелина).
Разгледаните особености ги правят удобни както за ръчна работа с единични заготовки или ленти от лист, така и за серийна работа. Променливата дължина на хода позволява да се прилагат за разделителни и формоизменящи операции на щанцоване.
Главният недостатък на този вид преси (изобщо на ексцентър преси), използващи коляно мотовилков механизъм за преобразуването на въртеливото движение във възвратно постъпателно, е променливата допустима сила по протежение на хода - Фиг.9-2.
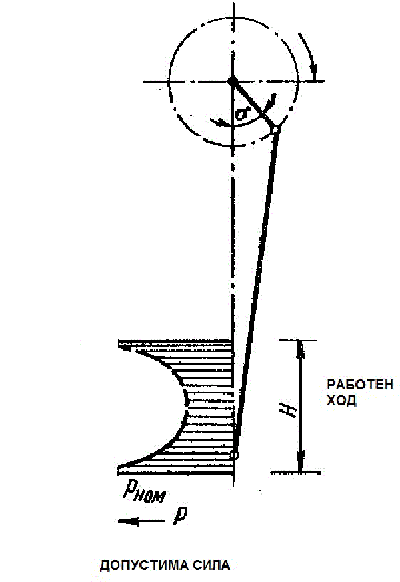
Фиг.9-2
Това е удобно за разделителните операции (малък ход), но изисква много внимателна проверка за формоизменящите (голям ход) или при съвместно изпълняваните операции (виж Фиг.5.13). Най-простото решение [1] е избора на преса с 1,5-2 пъти по-голяма номинална сила (преоразмеряване). Такъв подход до известна степен решава проблема и с втория важен недостатък на универсалните ексцентър преси, произтичащ от отворена „С“ – образна конструкция. Той е свързан с големите деформации на стойката, които имат вертикална и хоризонтална съставна на изместването на оста на плъзгача, и могат да доведат до удар на между ръбовете на поансоните и матрицата при пробиване или изрязване с малка хлабина. По тази причина се препоръчват използването на достатъчно стабилно водене в щанците, предназначени за работа на такива преси, а за прецизни режещи матрици и поансони с малка хлабина, да се използват плаващи шарнирни държачи за закрепване.
1.2.Автоматична преса със затворена конструкция на тялото.
Такъв модел на конструкция за SCHULER 80 тонна е показана на - Фиг.9-3,
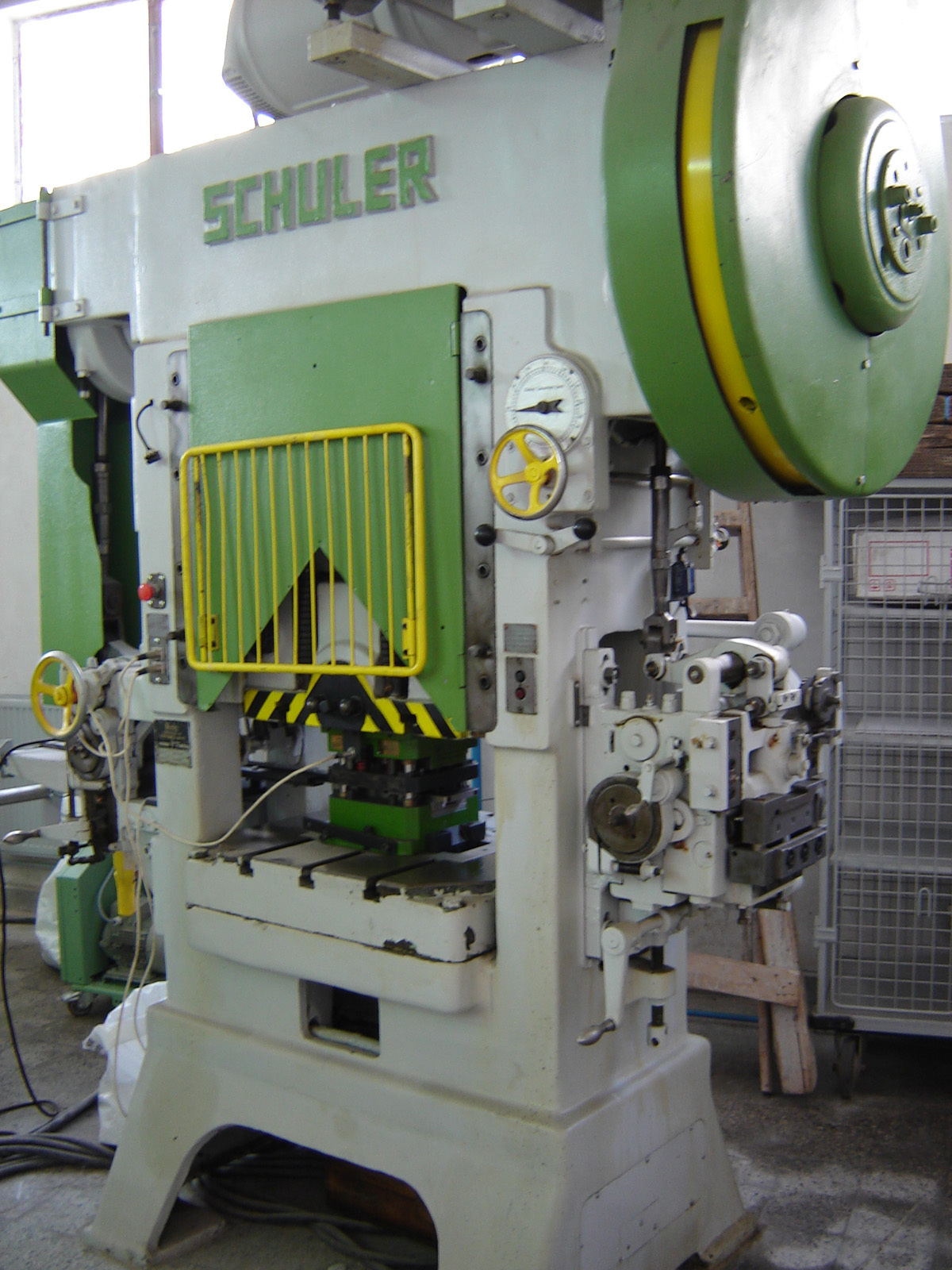
Фиг.9-3
а размотаващо-изправящото устройтво за лентата, е на показано на - Фиг.9-4.
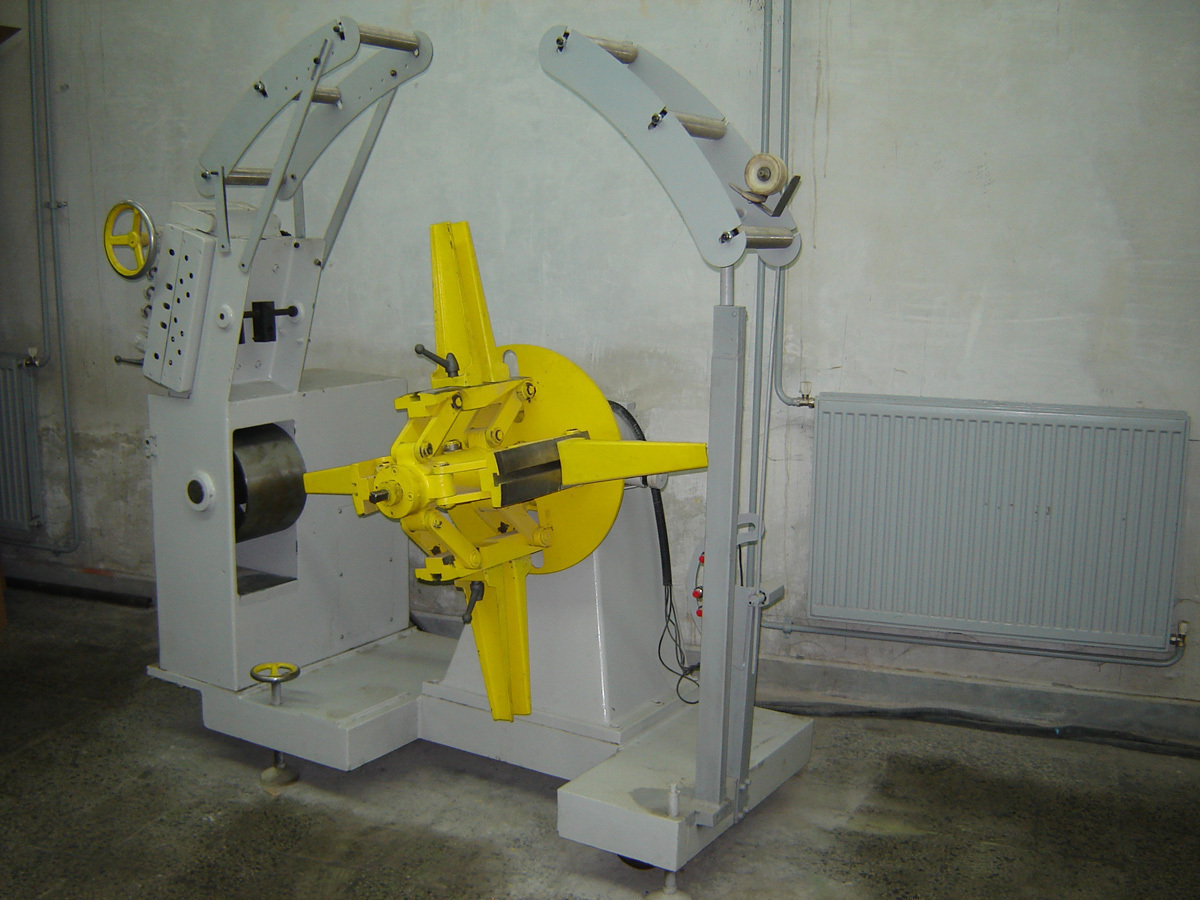
Фиг.9-4
Заедно те образуват производствена линия за щанцоване на лентов материал, обезпечаваща всички действия от развиване и изправяне на лентата, нейното подаване на необходимата стъпка в щанцата, работен ход, отделяне на отпадъка и готовия детайл, до нарязване на остатъка от лентата с гилотина. Конкретният модел е с постоянна дължина на работния ход, но честотата на ходовете (производителността) може да се променя. Има модели като BRUDERER BSTA и RASTER с дължината на хода, която може да се променя от минимална до максимална през определени дискретни стойности. Тези преси също имат вграден регулировъчен винт за настройка на височината на инструмента, задвижван ръчно или механично и снабден с брояч - Фиг.9-5.
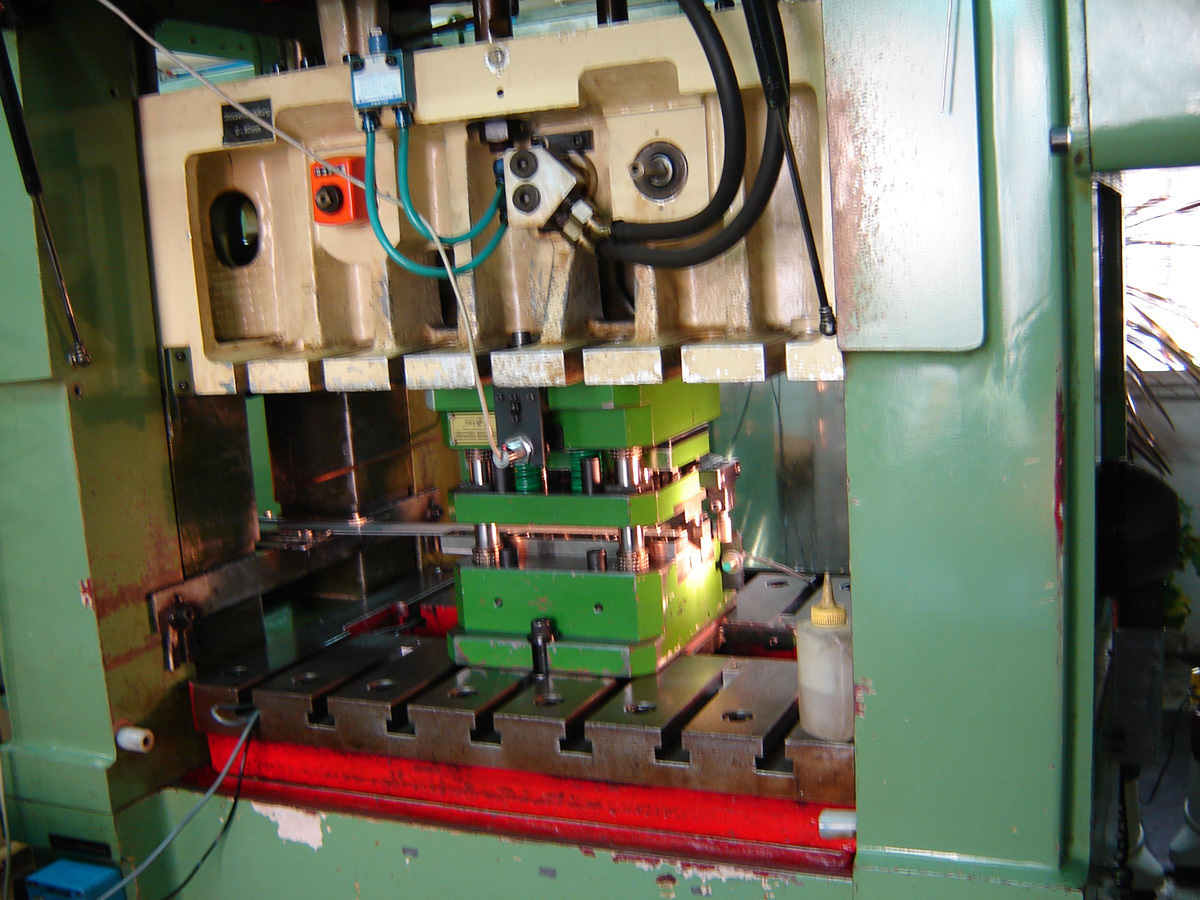
Фиг.9-5
Съвременните автоматични преси са с 8 точково ролково водене на тяло на плъзгача, двуточково предаване на силата (двоен коляно мотовилков механизъм), динамично балансиране на инерционните сили, система за предпазване и защита от няколко кръга чрез безконтактни (индуктивни или лазерни) датчици Фиг.9-5 (RASTER 60 тона). Те могат да контролират точното подаване на стъпка, падането на готовия детайл (задръстване на улей), падането или вдигането на определен отпадък (навдигане на притискач), край на лентата и необходимост от смяна, използването за защитни ограждения. Както беше посочено по-горе, силата при този вид преси, също е променлива по дължина на хода, но конструкцията им допуска много по-малки деформации, като хоризонтална съставна на изместването на остта на плъзгача е премахната. Препоръчват се при големи производствени серии от щанцовани детайли, както за разделителни, така и за формоизменящи операции, произвеждани от лента, навита на руло.
1.3.Хидравлична преса c двойнодействие с отворена конструкция на тялото.
Моделът на преса МULER 250 тона е показана на Фиг.9-6.
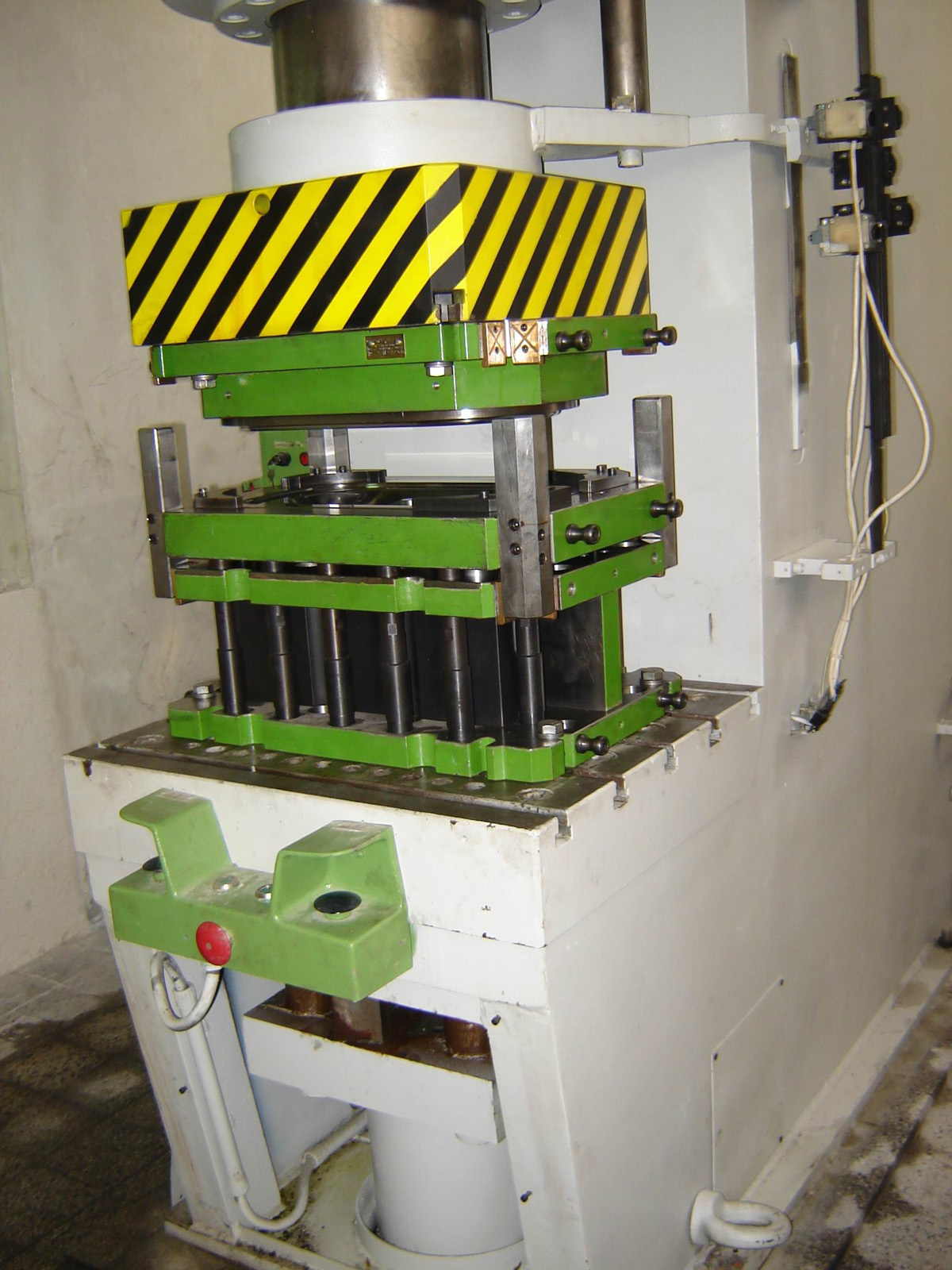
Фиг.9-6
Пресата има главен хидро цилиндър за работния ход и допълнителен хидро цилиндър под масата за създаване сила на притискане и изваждане на детайла. В някои варианти, в главния цилиндър или в масата, има допълнителен цилиндър и тогава пресата е тройно действаща. Важна особеност на хидравличните преси е големия работен ход, който те могат да осъществят. При тях номиналната сила не се променя по дължината на хода, а остава постоянна, но може да се настройва по големина. По този начин се осигурява и самата защита на пресата, защото надхвърляне на силата отваря предпазни клапани и на практика пресата спира (не въможно заклинване, както при ексцентър пресите). Този вид преса се препоръчва за формоизменящи операции (осбено при дълбоко изтегляне), най-често с единични заготовки. Те са бавни и не са походящи за големи серии от щанцовани детайли. За разгледаната отворена конструкция на тялото, не се препоръчва изпълнение на пробиване или изрязване с малка хлабина, без осигуряване на стабилна система на водене на инструмента. Съществуват и затворени конструкции, частично решаващи проблема с деформациите. Хидравличните преси се изработват за номинални сили от няколко десетки до няколко хиляди тона.
2.Ход и номинална сила на пресата.
2.1. Ексцентър пресите и автоматичните преси с регулируем ход позволяват избор на неговата дължина между минималния и максималния възможни. Конструкцията на използваните механизми за регулиране е изцяло механична, изпълнена под форма регулируема ексцентрикова втулка, с чието завъртане спрямо рамото на коляновия вал се променя хода. Тъй като фиксирането на втулката е чрез отвори или зъби, регулирането на хода е възможно само за определните дискретни стойности. Това условие трябва да се взема в предвид винаги, когато се конструира инструмент, изискващ определен ход.
Както бе посочено, ексцентър пресите имат променлива допустима сила по протежение на работния ход, която е най-малка по средата (виж Фиг.9-2). Обаче, промяната на хода оказва допълнителен ефект върху допустимата сила при ексцентър пресите, показан на диаграмата на Фиг.9-7.
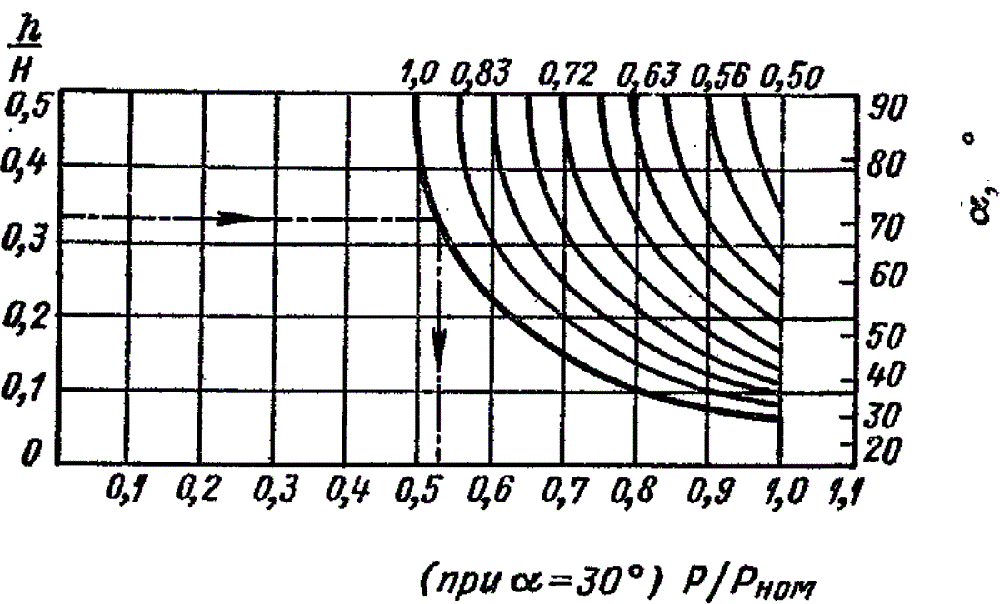
Фиг.9-7
От диаграмата се вижда, че вида на кривата се запазва, като минималната сила е в средата на хода при h/H = 0,5, където h е текущата стойност от големината на хода H, но за всеки ход има различна крива за силата. Всяка крива е означена в горната си част с число от 1 до 0,50, показващо отношението между регулирания ход и максималния ход на пресата. Обикновено, номиналната сила се задава при ъгъл на завъртане на коляното около 30º преди долна мъртва точка на хода. При максимален ход (крива 1), минималната сила е около 50% от номиналната (отношение на текущата сила към номиналната Р/Р ном). При намаляне на хода около два пъти (крива 0,50), минималната сила е около 95% от номиналната. При това номиналната сила се гарантира вече и за ъгъл на завъртане на коляното около 70º преди долна мъртва точка на хода (виж дясната вертикална скала).
Разгледаните разсъждения позволяват да се направи много важна препоръка за избора на ход при конструиране на щанци за ексцентър преса – да се избира най-малкия възможен ход. Това ще доведе не само до по-голяма допустима сила, но ще повиши и производителноста.
2.2. Хидравличните преси позволяват лесен избор на регулируем ход. Разгледаните ограничения не важат за тях. Понеже максималния ход зависи от хода на буталото на хидравличния цилиндър, те могат да осигурят произволна дължина в интервала от нула до този ход. Тук точната стойност на хода зависи от момента на спиране на буталото. Вече беше споменато, че номиналната сила при хидравличните преси е постоянна и зависи главно от диаметъра на буталото и налягането в хидавличния цилиндър. Чрез промяна на налягането в системата може да се променя максималната сила на пресата, което е важно предимство при формовъчни операции, за да не се допуснве повреждане на инструмента.
При преси с двойно действие трябва да се вземат в предвид максималния ход и максималната сила на притискащия хидравличния цилиндър, разположен под масата на пресата. Тук е задължително лесното регулиране на налягането, за да може да да се постигне необходимата притискаща сила, която се отчита с контролен манометър.
3.Мощност и производителност на пресата.
Въпросът за проверка на пресата по мощност е от значение само за ексцентър пресите при работа в автоматичен режим с многопозициони комбинирани инструменти. В някои частни случаи може да са необходими подобни проверки при изтеглящи операции. Необходмия запас от енергия при ексцентър пресите се покрива от инерцията на маховик, който се завърта от електродвигател. Когато необходимата работа за извършване на технологичните операции в даден момент, превиши кинетичната енергия, която може да отдаде маховика, последния забавя движението си, с което принуждава електродвигателя да се претовари и повиши температурата си, в резултат на което може да се стигне до изгаряне на намотките му и необходимост от смяна на електродвигателя. Това налага, когато възможностите за избор на преса са ограничени до наличните, да се направят всички възможни проверки, и ако е необходимо да се промени конструкцията на инструмента в етапа на проектиране.
Основния въпрос е, как да се направи тази проверка. Най-простият вариант, да се види мощността на елктродвигателя, и да се сравни с необходимата технологична работа е неприложим. Той изразява средната мощност във времето и не може да определи, дали ще възникне претоварване в някъкъв момент. Затова е необходимо да се сравни полезната работата на пресата с необходимата технологична работа за един и същ интервал от време. Това може да стане чрез сравнение на площите от диаграмите “сила – ход на пресата” и “необходима сила – ход” за конкретен технологичен процес за единица време, което е графична интерпретация на мощността. Понеже рядко са налични необходимите номограми на Фиг.9-8
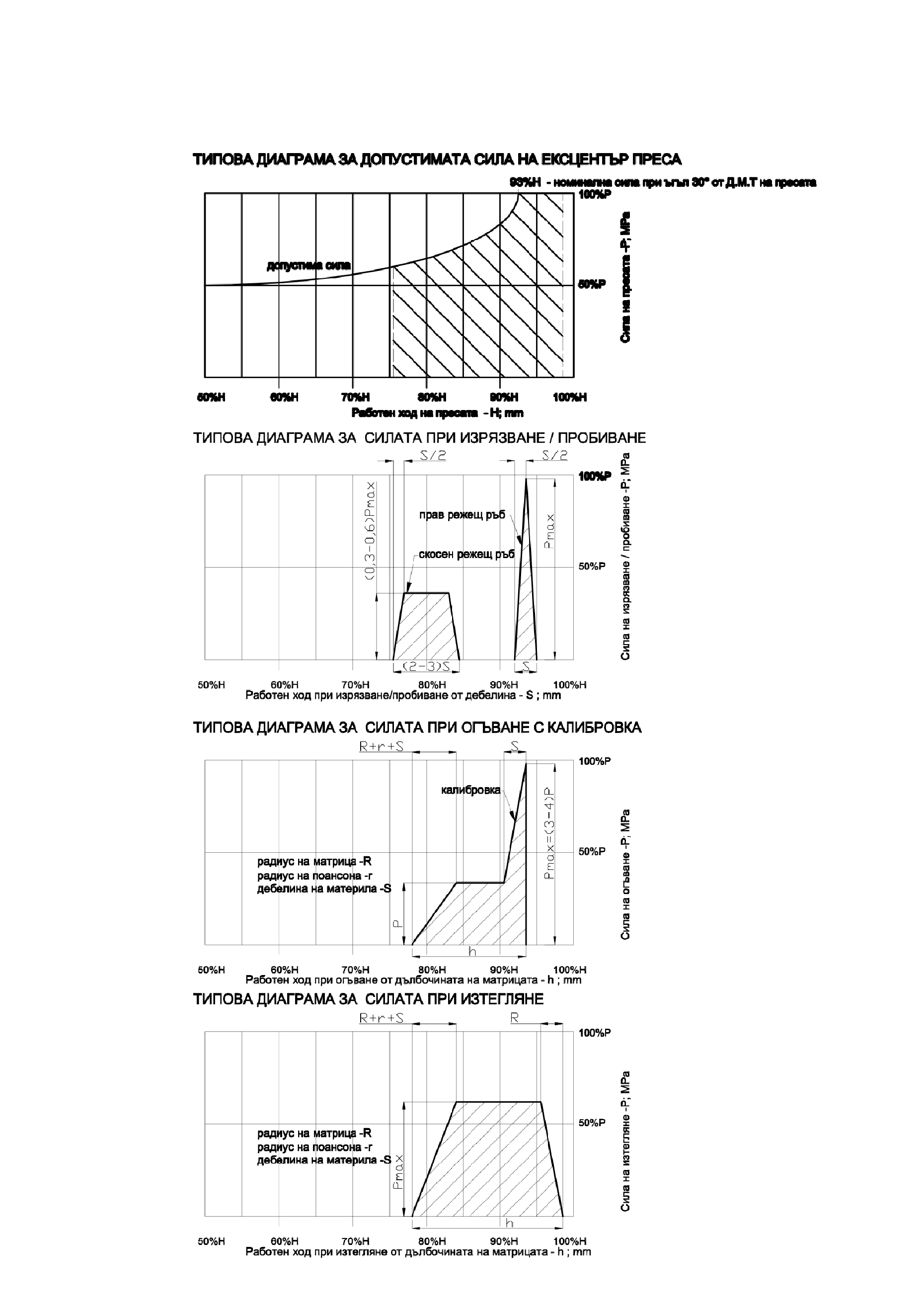
Фиг.9-8
са показани типови диаграми с възлови точки за построяване на кривата на промяна на допустимата сила за пресата и типови опостени диаграми за изменение на силите при операции пробиване – изрязване с прави и скосени режещи ръбове, при огъване с калибровка в края и при изтегляне. Те могат да бъдат построени в подходящ мащаб по изчислените технологични сили и ходове. Условието е, диаграмите да се построят в еднакъв мащаб (препоръчително е използване скалата на пресата). Началото за всяка крива трябва да отговаря точно на реалния момент спрамо края на работния ход на пресата (100%Н). Защрихованите площи отговарят на необходимата работа за всяка операция и тяхната сума трябва да е по-малка от защрихованата площ на пресата за интрвала от началото на първата до края на последната операции. Така построените диаграми позволяват лесно определяне на площите от всяка CAD система. Разбира се, метода е приблизителен, прекалено опростен и не отразява точно реалните процеси, но е първа стъпка към намиране на решение – нагледно показва кой процес е критичен и трябва да се промени в инструмента. Добра идея е, да се предвиди коефициент на сигурност (1.1-1,2), който да отразява с колко защрихованата площ на пресата трябва да е по-голяма от сумарната площ на останалите, за да се приеме, че пресата няма да е претоварена по мощност.
Мощността и производителността са свързани – по-високата производителност изисква по-висока скорост на работа, което означава по-голяма необходима мощност. По-висока производителност може да се постигне и при съшата скорост, но при едновременна обработка на два детайла. Тук отново се стига до проверка на необходимата мощност на пресата по разгледания метод, но диаграмите на силите ще се удвоят.
4. Размери на работното пространство и закрита височина на пресата.
При конструиране на щанците е много важно те да са съобразени с пресите, на които ще работят. Затова са необходими паспортни данни за пресата, които най-често са текстов вид - Фиг.9-9. По-удобен вариант е, когато по таблични дани се построи чертеж на работното пространство, както е показано за автоматична преса BRUDERE BSTA 25 на Фиг.9-10.
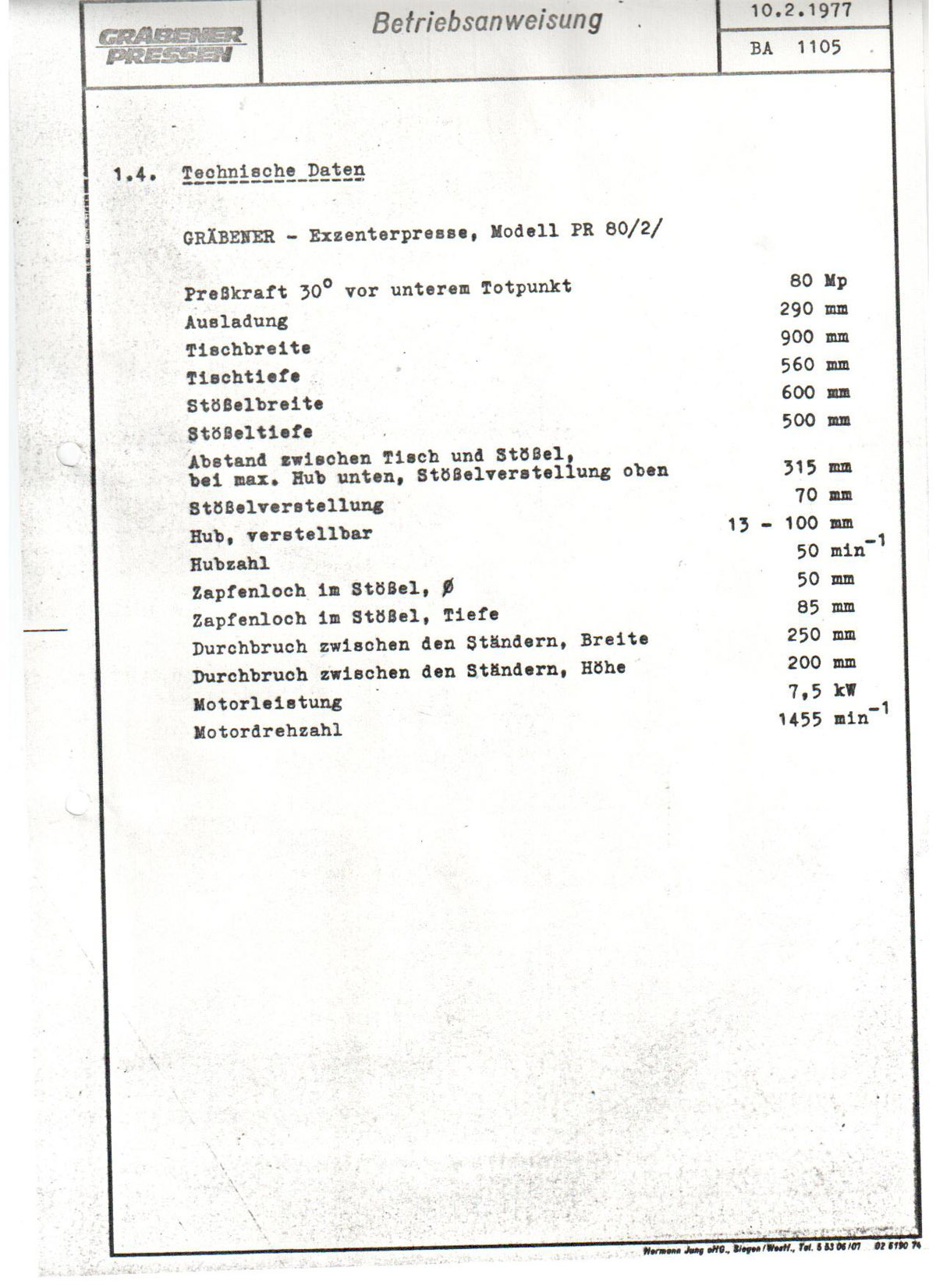
Фиг.9-9
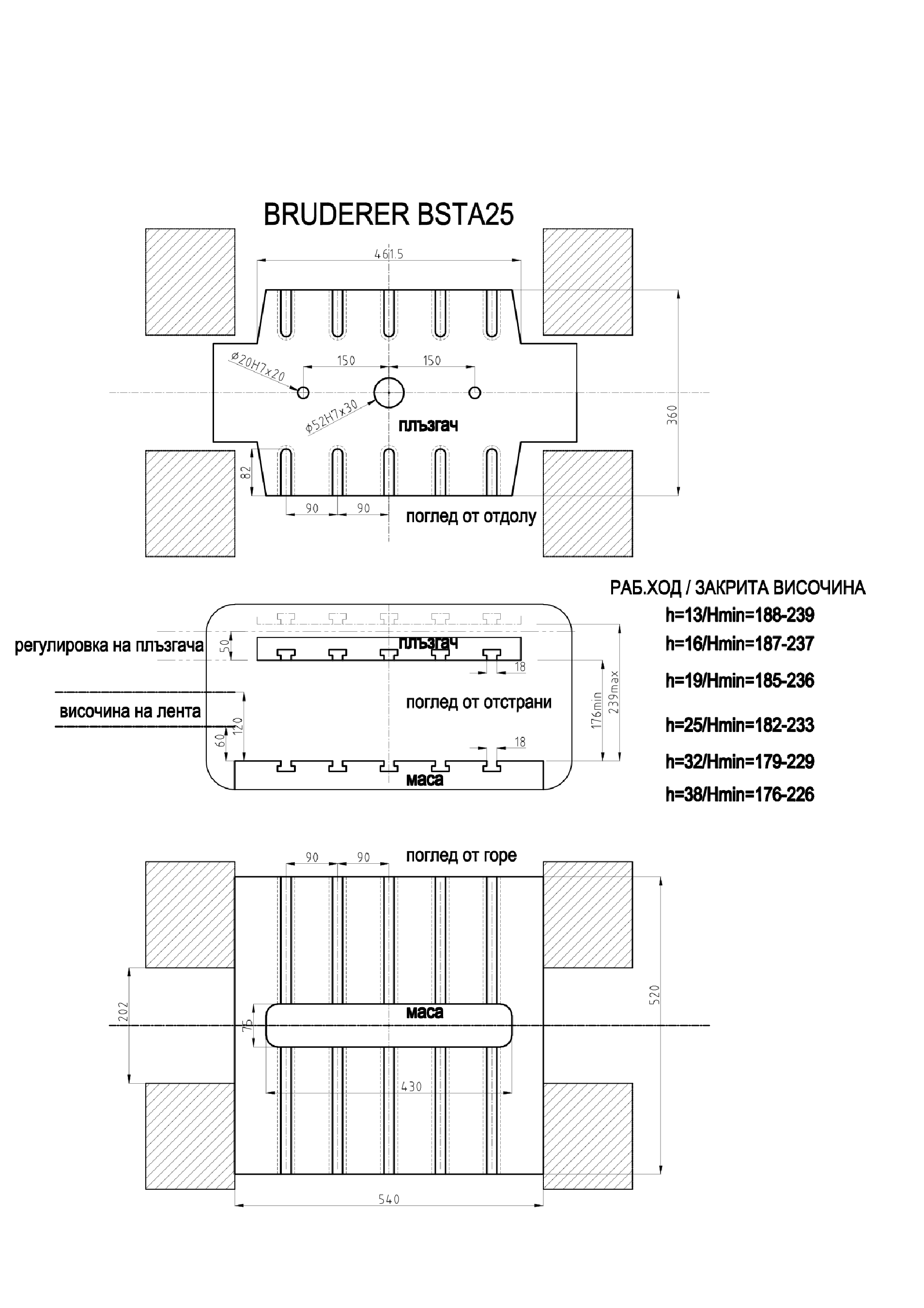
Фиг.9-10
По този чертеж лесно могат да се проверят размерите на масата и плъзгача, към които ще се закрепва щанцата, разположението и вида на присъединителните повърхнини в плъзгача, освободения канал за падане на отпадък или готов детайл в масата на пресата, височината на подаване на лентата и допустимия диапазон на височината на щанцата. Вижда се, че в зависимост от хода, този диапазон е различен. Трябва да се държи сметка и за вида на щанцата, когато се избира височиата – за разделителните операци е желателно новия инструмент да има височина близка, но по-малка от горната граница на регулиране. Така след заточване размерът ще намалява и по-пълно ще се използват възможностите на пресата за регулиране.
Закрита височина на пресата е разстоянието между плъзгача и масата на пресата в долна мъртва точка (д.м.т.) при най-малка дължина на мотовилката (навит до край регулировъчен винт на плъзгача) и максимален ход. Тя определя максималната височина на затворения инструмент, който може да се използва от пресата. По-висок инструмент може да се постави при горно положение на плъзгача, но при работния ход надолу ще се стигне до заклинване и повреда на пресата и инструмента. При по-нисък инструмент, разликата се компенсира чрез регулировъчния винт.
При хидравличните преси терминът закрита височина на пресата губи своя смисъл, защото при нея няма опасност от заклинване, Когато щанцата е с по-малка височина от необходимата, под нея се поставят шлифовани подложки или траверси. Казаното за работното пространство е в сила и при хидрвличните преси. Тук трябва да се построят и разположените под масата плочи и хидро цилиндри. Общия вид и размерите на работното пространство на 250 тонна двойно действаща хидрвлична преса с притискащи плоча и хидроцилиндър под масата на пресата е показан на Фиг.9-11.
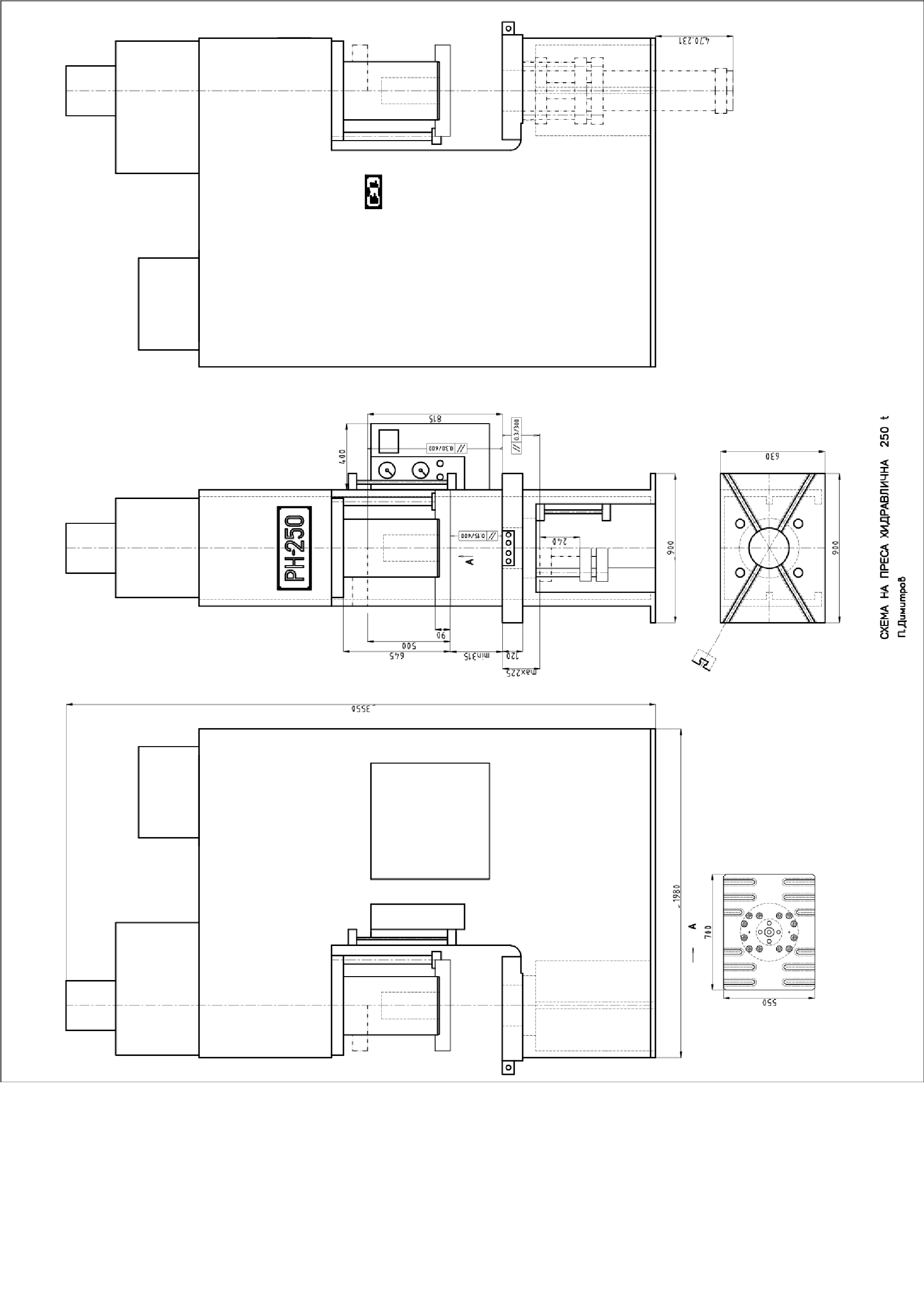
Фиг.9-11
В заключение за избора на преса трябва да се подчертае, че обикновено щанците се съобразяват и променят според пресата, доколкото това е възможно. Обратния случай е рядко изключене, когато се проектира нова производствена мощност, за която cе подготвят инструменти и се избират и доставят нови преси. И в двата случая, по-скоро се проверява съответствието на преса с иструмент.
ГЛАВА 10. МЕТОДИ И ТЕХНОЛОГИЧНИ ПРОЦЕСИ, ИЗПОЛЗВАНИ ПРИ ИЗРАБОТКАТА НА ИНСТРУМЕНТИ ЗА ЛИСТОВ МАТЕРИАЛ (ЩАНЦИ)
Производството на инструменти за обработка на листов материал (щанци) е специфична част (нестандартна инструментална екипировка) от машиностроителната индустрия, осигуряващо изработка на средства за производство на серийни изделия в различни индустрии. Поради специфичите му особености (единично, уникално производство), не всички технологични процеси, използвани в машиностроенето са подходящи – на пример леене, коване, горещо щамповане, заваряване, обработка на зъбни колела. Тук на кратко ще бъдат разледани и сравнени по производителност, точност и възможност за обработка на твърди материали, най-разпространените методи за механична и електрофизична обработка на нестандартна инструментална екипировка.
1.Механична обработка чрез стружко отделяне (рязане на металите).
1.1. Струговане
– Принцип и описание: Заготовката извършва въртеливо движение, инструмента постъпателно.
– Видове операции: Външно, вътрешно, челно, профилно, резбонарязване.
– Технологични възможности: Груба, получиста, чиста обработка на различни материали. Ограничена употреба при закалена стомана над HRC50. Не приложим за обработка на твърди инструментални материали.
– Производителност: Висока – до 10000 кубични милиметра за минута.
– Практическа точност и грапавост: Допуск – над 0,025 mm, грапавост – над Ra 1,6.
– Машини: Универсални стругове. Стругове с ЦПУ.
1.2. Фрезоване
– Принцип и описание: Инструментът извършва въртеливо движение, заготовката постъпателно.
– Видове операции: Насрещно или еднопосочно, плоско, профилно, канали, зъбофрезоване, резбофрезоване.
– Технологични възможности: Груба, получиста, чиста обработка на различни материали. Ограничена употреба при закалена стомана над HRC40. Не приложим за обработка на твърди инструментални материали.
– Производителност: Висока – до 10000 кубични милиметра за минута.
– Практическа точност и грапавост: Допуск – над 0,04 mm, грапавост – над Ra 3,2.
– Машини: Универсални фрезови машини. Инструментални фрезови машини. Машинни центри с ЦПУ.
1.3. Пробиване
– Принцип и описание: Инструментът извършва въртеливо и постъпателно движение.
– Видове операции: Пробиване, зенкероване, райбероване, разстъргване, резбонарязване с метчик.
– Технологични възможности: Груба и чиста обработка на различни материали. Ограничена употреба при закалена стомана над HRC40. Не приложим за обработка на твърди инструментални материали.
– Производителност: Средна – до 2000 кубични милиметра за минута.
– Практическа точност и грапавост: Допуск – над 0,025 mm, грапавост – над Ra 1,6. Посочените стойности с отнасят за разстъргване, при райбероване те са по-високи, а при пробиване са по-ниски.
– Машини: Настолни пробивни машини. Колонни пробивни машини. Кординатно разстъргващи машини. Машинни центри с ЦПУ.
1.4. Стъргане
– Принцип и описание: Инструментът извършва възвратно-постъпателно движение, заготовката установъчно на всеки двоен ход.
– Видове операции: Надлъжно, напречно, дълбане на шпонкови и шлицеви канали в главина.
– Технологични възможности: Груба и получистачиста обработка. Не приложим за обработка на твърди инструментални материали и закалена стомана. Ефективен при обработка на тесните страни на плочи от прокат. Намира ограничено приложение.
– Производителност: Средна – до 1000 кубични милиметра за минута.
– Практическа точност и грапавост: Допуск – над 0,05 mm, грапавост – над Ra 6,3.
– Машини: Хобел машини. Шепинг машини. Щос машини.
1.5. Отрязане
– Принцип и описание: Инструментът извършва възвратно-постъпателно (механична ножовка), постъпателно (лентоотрезна машина) или въртеливо движение (циркуляр) и напречно подавателно движение.
– Видове операции: Отрязване с ножовка, с лентотрезна машина, с циркуляр.
– Технологични възможности: Груба обработка (раздеяне на заготовка). Не приложим за обработка на твърди инструментални материали и закалена стомана.
– Производителност: Ниска – до 600 кубични милиметра за минута.
– Практическа точност и грапавост: Допуск – над 1mm, грапавост – над Ra 12,5.
– Машини: Механична ножовка. Лентоотрезна машина. Циркуляр.
1.6. Шлифоване
– Принцип и описание: Инструментът извършва въртеливо движение, заготовката възвратно-постъпателно (плоско шлифоване) или въртеливо движение (цилиндрично шлифоване); инструмента извършва въртеливо движение и възвратно-постъпателно движение (профилно шлифоване); инструмента извършва въртеливо движение, възвратно-постъпателно и планетарно движение (координатно шлифоване).
– Видове операции: Плоско; външно, вътрешно и челно цилиндрично; профилно, координатно; резбошлифоване; зъбошлифоване.
– Технологични възможности: Чиста обработка (окончателна). Приложим за обработка на твърди инструментални материали и закалена стомана.
– Производителност: Ниска – до 20 кубични милиметра за минута.
– Практическа точност и грапавост: Допуск – над 0,005 mm, грапавост – над Ra 0,32.
– Машини: Плоско шлифовъчни машини. Универсални кръгло шлифовъчни машини. Вътрешно шлифовъчни машини. Безцентрови кръгло шлифовъчни машини. Профилно шлифовъчни (оптични) машини. Универсални заточващи машини. Координатно шлифовъчни машини.
1.7. Притриване и полиране
– Принцип и описание: Инструментът (притир) извършва възвратно-постъпателно или въртеливо движение спрямо заготовката в специална притриваща среда (диамантена паста).
– Видове операции: Външно, вътрешно, челно, профилно.
– Технологични възможности: Довършителна обработка (окончателна). Приложим за обработка на твърди инструментални материали и закалена стомана.
– Производителност: Много ниска – до 0,1 кубични милиметра за минута.
– Практическа точност и грапавост: Допуск – над 0,002 mm, грапавост – над Ra 0,05. Полирането се използва главно за намаляване на грапавостта, притриването – за повишаване точността на формата, размерите и контактната площ.
– Машини: Най-често се изпълнява ръчно. За полиране се използват универсални машини (например струг, бормашина) или специални високообортни електрически или пневматични инструменти.
1.8. Шлосерски операции
– Принцип и описание: Предимно ръчни операции свързани с монтаж, демонтаж, напасване на отделни елементи и някои машинни операции (полиране, притриване, резбонарязване).
– Видове операции: монтажни операции, нарязване на резба с метчик и плашка, пробиване, райбероване, ръчно изпиляване, полиране, притриване.
– Технологични възможности: Предварителна или довършваща обработка. Зависи от квалификацията и е много важна за качеството на инструментите.
– Производителност: Ниска.
– Практическа точност и грапавост: Зависи от квалификацията.
– Машини: Най-често се изпълнява ръчно. Рядко се използват универсални машини (например бормашина) или специални високобортни електрически или пневматични инструменти.
2.Електрофизична обработка.
2.1. Обемна електро ерозия
– Принцип и описание: Заготовката и инструмента-електрод са свързани с електрически източник и са разположени в резервоар с диелектричен флуид - Фиг.10-1.
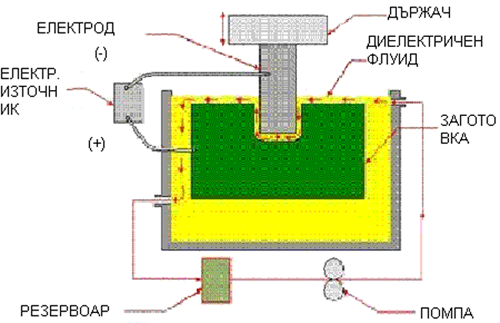
Фиг.10-1
Електрода извършва възвратно-постъпателно движение спрямо заготовката, при което интезивността на електрическото напрежение при сближаване нараства, до настъване на пробив в диелектрика и поява на електрически разряд (волтова дъга). При него повърхността на заготовката и електрода в зоната на дъгата се разрушават и отделените микро частици се отнасят от диелектричен флуид. Малко след възникване на дъгата, електродът се отдръпва и процеса на разрушаване се прекраява за определен интервал от време. Обикновенно, формата на електрода се копира върху заготовката, но е възможно използването на програмирано съчетание на формата на електрода с движение по зададена траектория.
– Видове операции: Обемно – 3D, повърхностно – 2D/3D, профилно – 3D/4D, резбонарязване, пробиване на стартови отвори, разпробиване на счупени в отвори инструменти.
– Технологични възможности: Груба, получиста, чиста обработка на различни метали. Приложим за обработка на закалена стомана и твърди инструментални материали. Не приложим за материали, не проводими електрически. Възможност за получаване на различен релеф на обработваните повърхности.
– Производителност: Ниска – до 80 кубични милиметра за минута. Зависи от материала на електрода, машината и избраните режими.
– Практическа точност и грапавост: Допуск – над 0,03 mm, грапавост – над Ra 2,5. Зависи от материала и износването на електрода, машината и избраните технологични режими .
– Машини: Обемни електро ерозийни машини с ЦПУ.
2.2. Нишкова електро ерозия
– Принцип и описание: Заготовката и инструмента-електрод (тънка тел) са свързани с електрически източник и между тях се подава диелектричен флуид (дейонизирана вода) - Фиг.10-2.
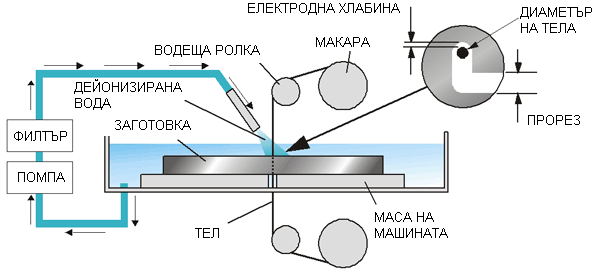
Фиг.10-2
Електрода (тънка тел) извършва постъпателно движение спрямо заготовката, като се развива от една макара и навива на друга. При това интезивността на електрическото напрежение, поради сближаване на телта със стената на прореза нараства, до настъване на пробив в диелектрика и поява на електрически разряд (волтова дъга). При него повърхността на заготовката и електрода в зоната на дъгата се разрушават и отделените микро частици се отнасят от подаваната под налягане дейонизирана вода. Подаването на нови, не износени участъци, които влизат в зоната на заготовката, осигурява непрекъстатост и точност на процеса. Получената форма на заготовката зависи от траекторията на движение на електрода-тънка тел.
– Видове операции: повърхностно – 2D, профилно – 4D.
– Технологични възможности: Получиста, чиста обработка на различни метали. Приложим за обработка на закалена стомана и твърди инструментални материали. Не приложим за материали, не проводими електрически. Възможност за получаване на два различни профила на долната и горна обработвани повърхности (например окръжност от горна страна, плавно преливаща в квадрат от долната).
– Производителност: Ниска – до 20 кубични милиметра за минута. Зависи от материала, дебелината на заготовката и избраните режими. При работа с тел ф0,25 mm, производителността най-удобно се изразява в квадратни милиметра за час или минута.
– Практическа точност и грапавост: Допуск – над 0,01 mm, грапавост – над Ra 1,6. Зависи от материала и избраните технологични режими. Да се има впредвид наличието на прегорял слой и налеп (около 0,003 mm) по ерозираните страните, който трябва да се изчисти!
– Машини: Нишкови електро ерозийни машини с ЦПУ.
2.3. Термообработка
– Принцип и описание: Промяна на свойствата на заготовката (твърдост, якост, износоустчивост) чрез процес на фиксиране на подходяща структура или насищане на повърхноста с твърди химически елементи и техни съединения.
– Видове операции: Обемно или повърхностно закаляване; закаляване с токове с висока честота; ниско, средно и високотемпературно отвръщане; отгряване; циментация; азотиране; вакумно насищане на повърхността с волфрамови карбиди и нитриди.
– Технологични възможности: Получаване твърди инструментални материали – HRC 62 (при покрития над HRC 65).
– Производителност: Ниска – процесите продължават от няколко часа до повече от денонощие.
– Практическа точност и грапавост: Всички процеси са свързани с деформаци и е необходима прибавка за последваща обработка! Деформациите са от 0.03 mm до 0.5 mm в зависимост от вида на процеса за термобработка, формата, материала на заготовката, размерите и нейната предварителната подготовка.
– Машини: Пещи и вани за термообработка.
3. Контролни процеси.
3.1. Универсални измервателни инструменти
– Принцип и описание: механични, електромеханични и еталонни уреди за измерване или сравнение на контролирания параметър (дължина, ъгъл, форма, твърдост, грапавост).
– Видове операции: измерване на линейни размери и ъгли с универсални инструменти, измерване на линейни размери чрез сравнение с гранични пластини или гранични щифтове.
– Технологични възможности: 0т 0,02 до 500 mm.
– Производителност: Ниска – ръчно изпълними операции. Повтаряне на измерванията за предотвратяване на грешки.
– Практическа точност: над 0,002 – 0.01 mm.
– Инструменти: Шублери и микрометри с нониус. Шублери и микрометри с циферблат или електронен дисплей. Ъгломери. Вътромери и дълбокомери. Индикаторни часовници с магнитна стойка. Плоско паралелни гранични пластини. Гранични цилиндрични щифтове. Луфтомерни пластини. Твърдомери. Еталонни пластини за грапавост.
3.2. Оптични измервателни инструменти
– Принцип и описание: Многократно оптическо увеличение на измервания обект.
– Технологични възможности: 0т 0,01 до 50 (100) mm.
– Производителност: Ниска – ръчно центроване на обекта. Повтаряне на измерванията за предотвратяване на грешки.
– Практическа точност: над 0,005 mm.
– Инструменти: Оптически проектор. Измервателен микроскоп.
3.3. Три координатна измервателна машина
– Принцип и описание: Програмно задаване набор от контролни точки за измервания обект и автоматично изпълнение и обработка на резултатите.
– Технологични възможности: Според обхвата на машината.
– Производителност: Висока. Възможност за многократно повторение.
– Практическа точност: над 0,003 mm.
– Машини: Три координатна измервателна машина.
В производството на нестандартна инструментална екипировка се прилагат голяма част от машиностроителните процеси и технологии, реализирани чрез използване на универсално оборудване и инструменти. Характера на производство не позволява експериментиране или пускане на нулева серия за тестване и настройка на технологичния процес. Поради тази причина, усъвършенстването на методите е насочено към подобрение на качеството (сигурността и точността на процесите), а не към повишение на производителността. Важно място трява да се отдели на CAD-CAМ процесите и компютърното моделиране и симулация преди самото производство, за да се намали опасността от възникване на скъпо струващи грешки (например сложни и скъпи детайли да се изработват по няколко пъти).
ГЛАВА 11. ТИПОВИ ТЕХНОЛОГИЧНИ МАРШРУТИ ЗА ИЗРАБОТКА НА АКТИВНИТЕ, НА ТЕХНОЛОГИЧНО НЕОБХОДИМИТЕ И СПОМАГАТЕЛНИ ЧАСТИ НА ИНСТРУМЕНТИ ЗА ПРЕСОВАНЕ НА ЛИСТОВ МАТЕРИАЛ (ЩАНЦИ)
Типовите технологични процеси и технологични маршрути за свързаните операции се базират на разработване на технология за производство само за един детайл, който е характерен – „типичен” за дадена група подобни детайли, определана след класификация на детайлите по конструктивно - технологични признаци. Детайлът от групата се избира така, че да съдържа всички характерни конструктивни елементи, изискващи определена технология за изработка, и се нарича „Комплексен детайл”. В някои случаи може изкуствено да се създаде такъв детайл. Целта е, да се създаде технологичен процес за най-сложния вариант, включващ всички важни операции, който да позволи чрез изключване на операции, бързо и лесно да се състави технологичен маршрут за по-простите детайли.
При инструментите за листово щамповане (щанци) класифицирането на детайлите е обособило три групи, две от които са определящи за качеството и работоспособността на щанците – активни части, като матрици, поансони, поансон-матрици и вложки (могат да са и матрични и поансонни) и технологично необходими части, като носещите плочи (горни, долни, водещи), водещите втулки и колонки, лентоводачи, ловители, фиксатори, упори, ограничители, притискачи, събувачи, повдигачи, отлепвачи. Спомагателните части са с проста конструкция и технология за изработване, поради което за тях не е необходим типов технологичен маршрут.
1. Типови технологични маршрути за активни части.
Основните детайли в тази група са класифицирани като матрици и като поансони, които значително се различават по технология на изработка. Поради тази причина са избрани „Комплексен детайл – матрица” и „Комплексен детайл – поансон”. Отчитайки производствения опит и особеностите при изработката на поансони и вложки, е добавен „Комплексен детайл – Целева Блок-Заготовка”.
– Критерият за избор на „Комплексен детайл – матрица” е наличие на центроващи и закрепващи отвори, режещи матрични профили с освобождаване, профилни отвори за вложки, различни канали и освобождение за огъвки, закалка и шлифоване на повърхнините. Най-пълно отговаря на тези изисквания матрица за щанца с последователно действие за пробиване, огъване и изрязване от Фиг.5-33.
– Критерият за избор на „Комплексен детайл – поансон” е наличие на профилни центроващи повърхнини и закрепващи отвори, профилирана работна част (в друга равнина), закалка и шлифоване или полиране на повърхнините. Най-пълно отговаря на тези изисквания огъващ поансон за щанца с последователно действие за пробиване, огъване и изрязване отФиг.7-18.
– Критерият за избор на „Комплексен детайл – Целева Блок-Заготовка” е наличие на центроващи и закрепващи резбови отвори, режещи матрични профили с освобождаване, различни канали и освобождение за огъвки, закалка и шлифоване на повърхнините. Най-пълно отговаря на тези изисквания Блок-Заготовка за матрични или притискачни вложки за щанца с последователно действие за пробиване, огъване и изрязване от Фиг.5-44 (избрана е за заготовка за вложки в притискач).
1.1. Типов технологичен маршрут за „Матрица”.
Разработен е маршрут за „Матрица” с чертеж No.11.1880.000.03 от Фиг.5-33. Типовата технологична маршрутна карта - Фиг.11-1
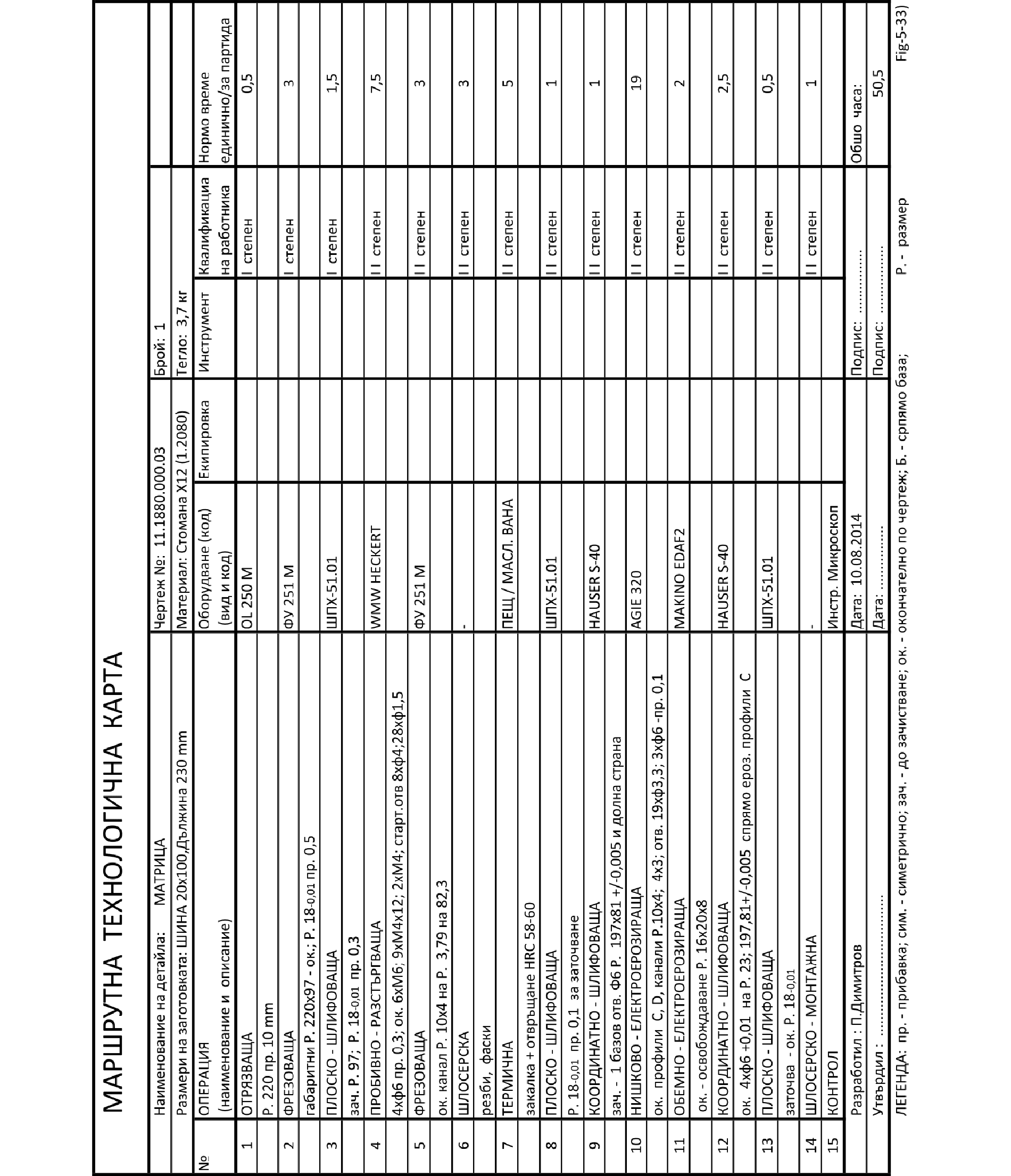
Фиг.11-1
включва всички характерни операции с тяхната обичайна последователност. Изходната заготовка е най-често е горещо валцована шина. Същeствуват и заготовки с допълнителна обработка и точни размери (с прибавка 0,3 – 0,4 mm), но са по-скъпи. Само при големи заготовки (над 300х300 mm) се използва изкован прокат. В картата освен размери се посочва материала и теглото на заготовката. Начина на означаване, описване на съдържанието на операциите и тяхната последователност е показан в попълнената карта. Задължително условие е кратко позоваване на повърхнините за обработка на съответната операция, използваните базите и прибавката, която трябва да се остави или размерът, който да се получи. Прибавката за следваща обработка при подлежащи на закалка детайли е решаващ фактор за качеството и производителността на процесите. След закалка (изобщо след термообработка) стоманата променя своя обем и настъпват неизбежни деформации. Малката прибавка води до висока производителност, но може да не е достатъчна за цялостно зачистване на обработваните повърхнини, поради неравномерното разпределение след нагряване и охлаждане. Голямата прибавка увеличава пропорцианлно времето за окончателните обработки. Изобщо, прибавката зависи от размерите и формата и е въпрос на компромис за избор на по-малката злина. За практиката може да се приеме, че на заготовки от легирана инструментална стомана с размери под 50 mm е достатъчна прибавка 0,2 mm, от 100 до 200 mm е достатъчна прибавка 0,3 mm. Над 200 mm може да се пресметне, като максималния размер се умножи с 1.0015. След всяка операция, в съответната графа се попълва машината (оборудването), на която ще се изпълни. Препоръчва се да се означи и неговия код, за да не се допуска неопределеност при наличие на повече от една машина. В края на всеки ред за дадена операция се попълва квалификацията на работника и времето предвидено за нея (или за партидата). Важно изисквание е, при съставяне на маршрутна карта да се обмисли въпроса за използваните бази и при липса на подходящи да се вмъкне операция за тяхното създаване, като се спазва принципа за тяхното единство (да се използват едни и същи бази). В долния десен край на картата трябва да се попълни общото време в часове, предвидено за всички операции. То ще е необходимо на следващ етап при планиране на изработката на детайла.
1.2. Типов технологичен маршрут за „Поансон”.
Разработен е маршрут за „Поансон огъващ” с чертеж No.02922-12 от Фиг.7-18. Типовата технологична маршрутна карта - Фиг.11-2
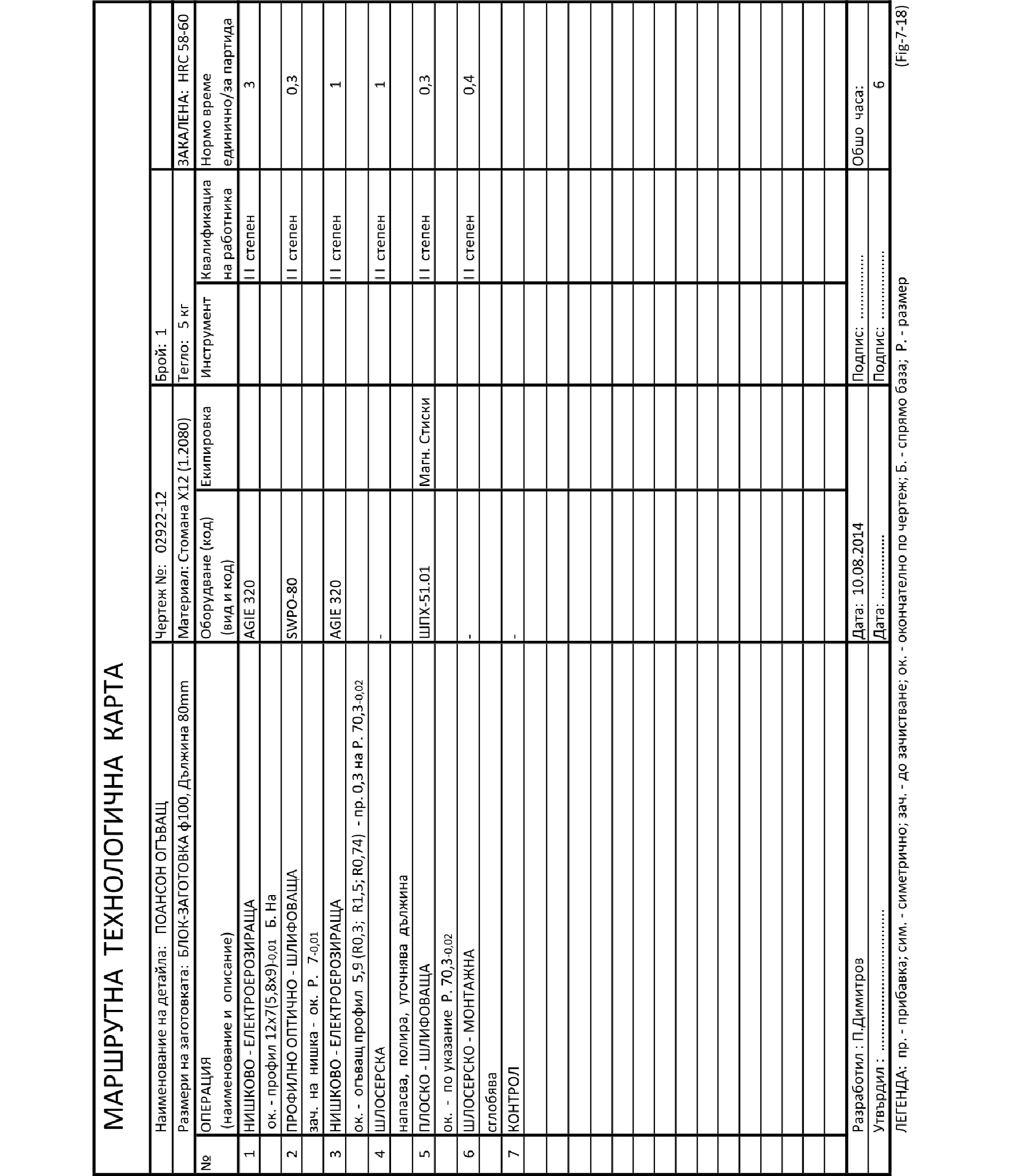
Фиг.11-2
включва всички характерни операции с тяхната обичайна последователност. Изходната заготовка е най-често Блок-Заготовка, изработена от горещо валцована шина и закалена до предписаната твърдост. В картата се посочват размерите, материала, теглото на Блок-Заготовката и означение, ако има такова. Начина на означаване, описване на съдържанието на операциите и тяхната последователност е показан в примерната карта. Задължително условие е позоваване на повърхнините за обработка на съответната операция, използваните базите и прибавката (ако е необходима), която трябва да се остави или размерът, който да се получи. Ако не се предвижда прибавка, най-често се записва „окончателно по чертеж“. След всяка операция в съответната графа се попълва машината (оборудването), на която ще се изпълни и нейния код. В края на всеки ред за дадена операция се попълва квалификацията на работника и времето предвидено за нея (или за партидата). В долния десен край на картата трябва да се попълни общото време в часове, предвидено за всички операции. Практиката е, първо да се изработват поансоните и след това матрици, притискачи, поасонодържачи и водещи плочи. По този начин се цели първо, да се подготвят и тестват техните програми, които в последствие да се приложат и корегират за съответните отвори и второ, поансоните да се използват като „профилен калибър пробка”. Винаги е по-евтино да се бракува и изработи отноново един поансон, отколкото една матрица с много профили.
1.3. Типов технологичен маршрут за „Целева Блок-Заготовка”.
Разработен е маршрут за „Блок-Заготовка вложки-притискач” с чертеж Пор. 1920 от Фиг.5-44. Типовата технологична маршрутна карта - Фиг.11-3
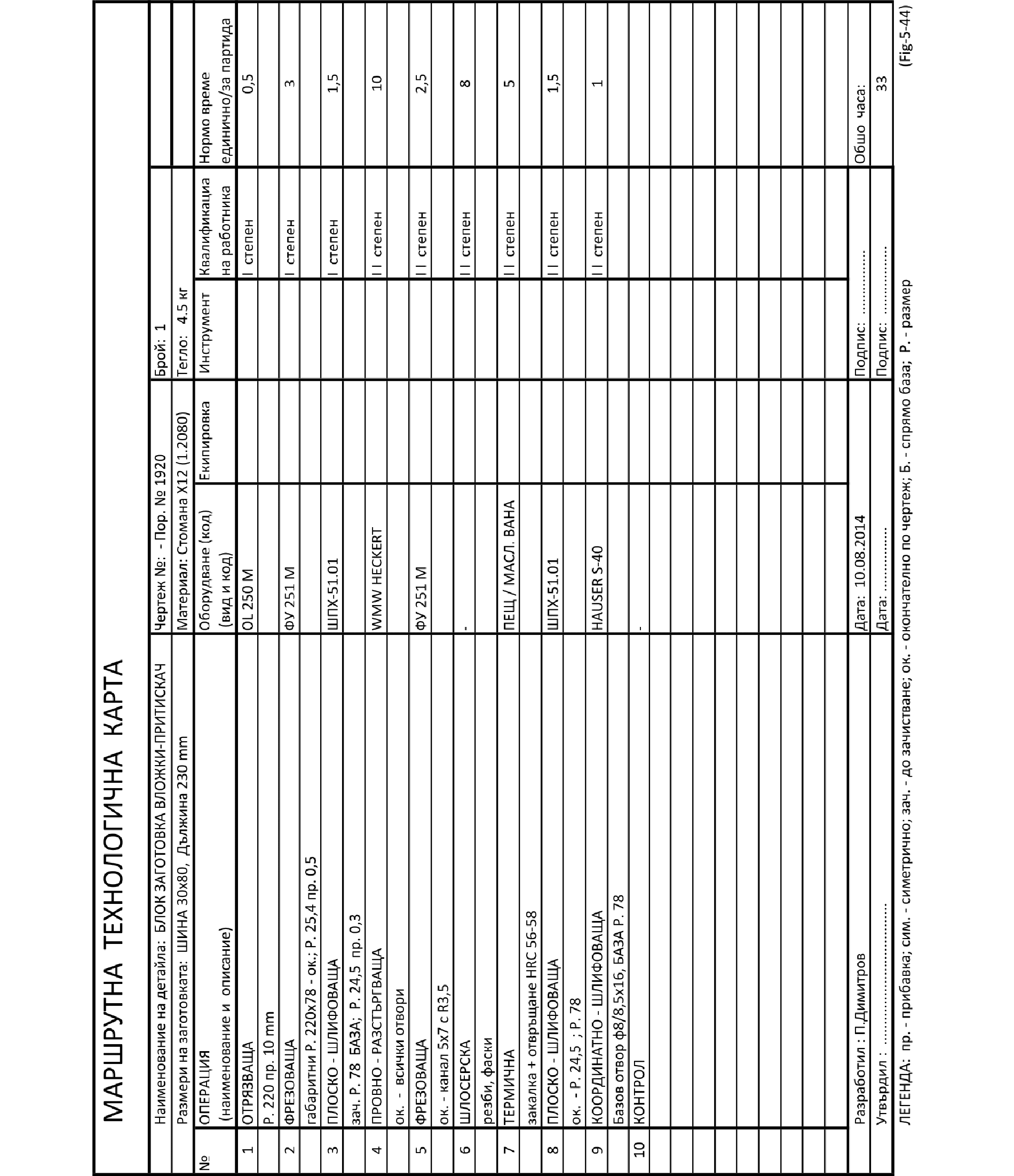
Фиг.11-3
включва всички характерни операции с тяхната обичайна последователност. Изходната заготовка е най-често е шина, изработена от горещо валцован стоманен профил. В картата се посочват размерите, материала, теглото на заготовката. Начина на означаване, описване на съдържанието на операциите и тяхната последователност е показан в картата. Задължително условие е позоваване на повърхнините за обработка на съответната операция, използваните базите и прибавката (ако е необходима), която трябва да се остави или размерът, който да се получи. Специално внимание се отделя на изработка на бази – те трябва да са обработени в началото, за да се използват нататък. След всяка операция в съответната графа се попълва оборудването, на която ще се изпълни и неговия код. В края на всеки ред за дадена операция се попълва квалификацията на работника и времето предвидено за нея. В долния десен край на картата трябва да се попълни общото време в часове, предвидено за всички операции.
Практиката да се изработват чертежи на Блок-Заготовки е различна. В някои фирми се подготвят от конструктора, който е „достатъчно навътре в нещата”. Принципно, това е чисто технологична задача, защото трябва да се съобрази наличност на подходяща заготовка, особености на машините за нейната обработка, условията за минимални разстояния и начин на разположение на вложките или поансоните, разположението на базите за центроване. В други фирми се прави само скица на ръка или изобщо не се прави скица, а се разчита на устни указания на място.
2. Типови технологични маршрути за технологично необходими части.
Основните детайли в тази група са носещите плочи (горни, долни, водещи), водещите втулки и колонки, лентоводачи, ловители, фиксатори, упори, ограничители, притискачи, събувачи, повдигачи, отлепвачи. Голямото разнообразие на включените детайли налага допълнителна класификация, като тип „Плочи”, „Ротационни” и „Други”. Най-важна е първата подгрупа, която обхваща горни, долни, подложни, опорни, водещи плочи, притискачи, поансонодържачи. Във втората подгрупа се включват водещи втулки, колонки, ловители, фиксатори отлепвачи, които много често са покупни, доставят се в завършен вид и за тях маршрутна технология може да не се разработва. Поради тази причина е избран „Комплексен детайл – плоча”.
– Критерия за избор на „Комплексен детайл – плоча” е наличие на центроващи и закрепващи отвори, отвори за водещите втулки и колонки, освобождаващи профили под отпадък или профилни отвори за вложки и поансони, различни канали и освобождения, шлифоване на повърхнините, наличие на термообработка. Никой от реалните детайли не отговаря изцяло на тези изисквания, затова е избран най-близкия до тях – плоча долна за щанца с последователно действие за пробиване, огъване и изрязване от Фиг.8-1. В детайла не е предвидена термообработка, но данните за нея могат да се вземат от маршрута за „Матрица” и ще са необходими само за притискач или опорна плоча.
2.1. Типов технологичен маршрут за „Плоча”.
Разработен е маршрут за „Плоча долна” с чертеж No.11.1880.000.01 от Фиг.8-1. Типовата технологична маршрутна карта - Фиг.11-4
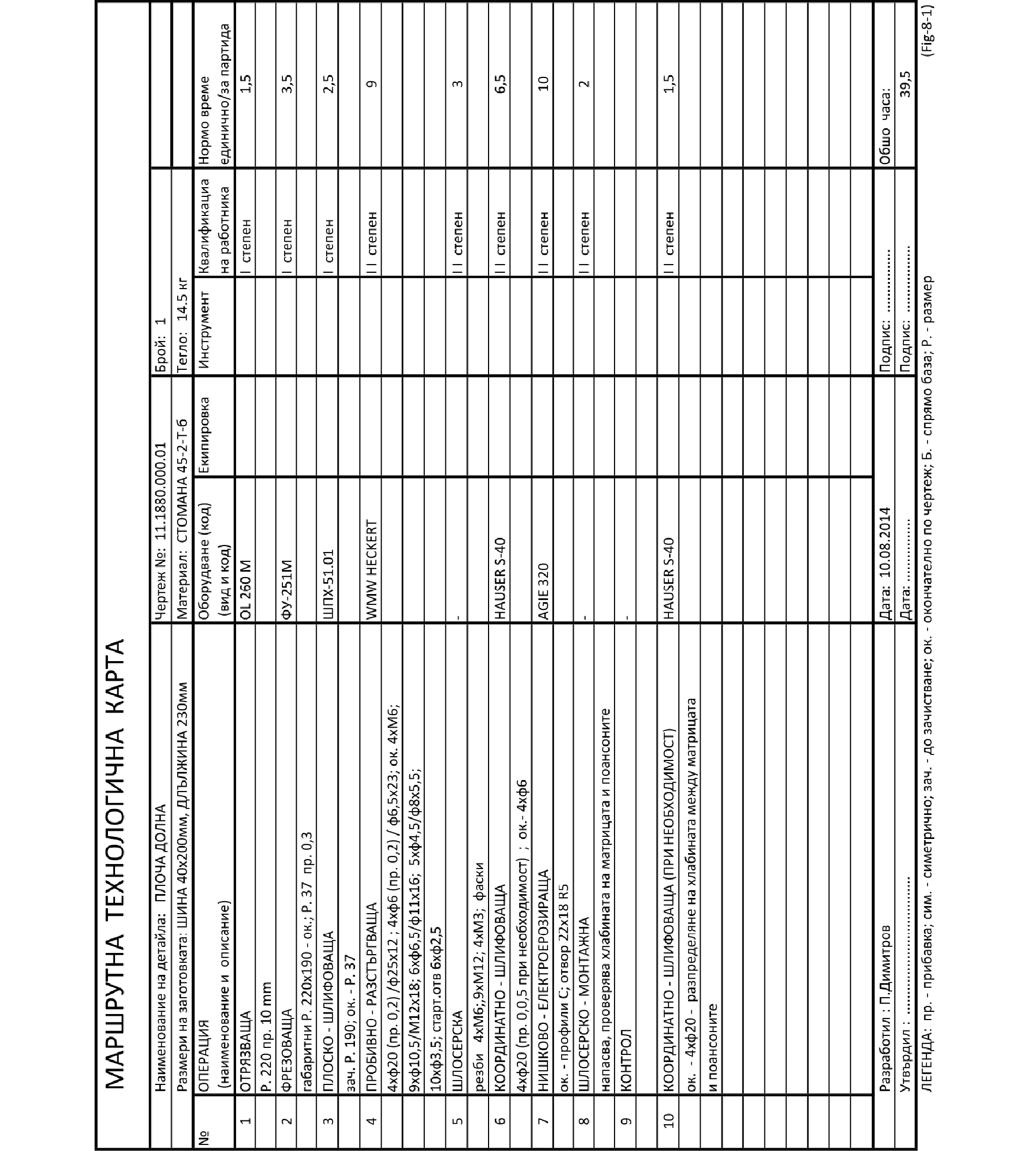
Фиг.11-4
включва всички характерни операции с тяхната обичайна последователност. Изходната заготовка при малки размери е най-често е горещо валцована шина. За големи размери същаствува вариант за заготовки с допълнително обработени страни чрез газово-плазмено рязане (с прибавка над 8 – 10 mm). В картата освен размери се посочва материала и теглото на заготовката. Начинът на означаване, описване на съдържанието на операциите и тяхната последователност е показан в картата с попълнен пример. Задължително условие е позоваване на повърхнините за обработка на съответната операция стехните размери, използваните бази с буквени означения и прибавката, която трябва да се остави или размерът, който да се получи. Прибавката за следваща обработка при подлежащи на закалка детайли е решаващ фактор за качеството и производителността на процесите. Вниманието да се концентрира върху големината на прибавката не само от гледна точка на размерите, но и от наличие или отсъствие на термообработка и нейния вид. Прибавката за детайли без термообработка е много по-малка от подлежащи на закалка. Тя цели да компенсира само грешките при изработка и трябва да е минимум два пъти по-малка от назначаваната за същите размери при закалка (особено при шлифоване на малки отвори). Важно е да се прецени, дали след термообработка (според предписаната твърдост) заготовката може да се обработва на конвенционални машини (фрезови, пробивно-разстъргващи и други). В някои случаи твърдостта е под HRC 40-45, което позволява да се оставя дори по-голяма прибавка от тази за шлифоване и операцията да се раздели на чиста обработка и окончателна. При определяне на базите, трябва да се спазва описаното по-горе правило за тяхното единство и колкото може по-ранната им обработка. Ако е необходимо, да се вмъкне допълнителна операция, специално предвидена за изработка на бази. За този вид детайли те най-често са шлифована хоризонтална плоскост (равнинна), шлифована тясна странична зона (линейна) и шлифован отвор (цилиндрична – начало). След всяка операция в съответната графа се попълва оборудването и неговия код. В края на всеки ред за дадена операция се попълва квалификацията на работника и времето предвидено за нея. В долния десен край на картата трябва да се попълни общото време в часове, предвидено за всички операции.
3. Особености и изключения в типовите технологични маршрути.
Матриците с по-големи размери или големи, близко разположени отвори и профили, могат да се изработват по типовия технологичен маршрут за „Матрица” от Фиг.11-1, но трябва да се добави допълнителна отгряваща (термична) операция преди първата плоско-шлифоваща. Фрезоващата операция за габаритни размери трябва да се разшири, като се опише в кои отвори и профили, какви освобождаващи отвори да се изпълнят. Първа термична операция става отгряването, за което трябва да се предвиди достатъчно време, защото изстиването на заготовката трябва да се изпълни бавно заедно с пещта (може да са необходими повече от 6-10 часа).
Режещите поансони също се изработват от Блок-Заготовката, но може да имат не включени операции спрямо типовия технологичен маршрут „Поансон” от Фиг.11-2, свързани с конструкцията за тяхното задържане в поансонодържача – например пробиване на отвор за щифт чрез обемна ерозия (Обемно-електроерозираща); профилно шлифоване на канал за задържащ елемент (Профилно-шлифоваща); запояване (Шлосерска) и профилно шлифоване на глава (Профилно-шлифоваща). Характерна особеност след нишково-електро ерозираща операция е необходимост от допълнителна профилно, плоско или кръгло-шлифоваща операция за отнемане на остатъчната част на свързващия мост в зоната на „старт – край” от траекторията на нишката. Тази част винаги остава при обработка на външни повърхнини, докато при вътрешните, с повторно преминаване на нишката тя се премахва.
Притискачи и опорни плочи могат да се изработват по типовия технологичен маршрут за „Плоча” от Фиг.11-4, но те имат не включени операции преди координатно-шлифоваща, като Термична и Плоско-шлифоваща. Тяхното попълване може да се взаимства от маршрутна технологична карта за „Матрица” от Фиг.11-1.
От изключително значение е при разработка на технологията за щанците с режещи части, да се проучат заложените допуски и необходимата хлабина между матрицата и поансоните. Обикновено, много конструктори смятат, че точността на изработка е въпрос на технология и не е техен проблем. Това е вярно само за един частен случай – режещи щанци за материал с дебелина над 1,2 – 1.5 mm, където едностранната хлабина е над 0.05 mm. Практическите наблюдения при изработката на режещи щанци за дебелина на листа 0.3 - 0.5 mm са установили сериозни проблеми, известни като „стържещи в матрицата поансони” или „чукащи в матрицата поансони”. И в двата случая изработката не е осигурила равномерна хлабина – в първия, поансонът все пак влиза в матрицата с почти „нулева хлабина”, а във втория изобщо не навлиза в отвора на матрицата. Проба на пресата за такива щанци води до излизане от строя още с първите удъри.
За решаващото значение на равномерно разпределената хлабина между матрица и поансон говори факта, че едва 25% неравномерност (еднострано намаляване с 25%, съпроводено с 25% увеличение в противоположната страна) води до намаляване на трайността на щанцата повече от 2 пъти.
По долу този проблем ще бъде изследван подробно за установяване на причините и предлагане на препоръки за решение.
Модел на проста щанца за изрязване или пробиване с всички функционални части е показан на Фиг.11-5.
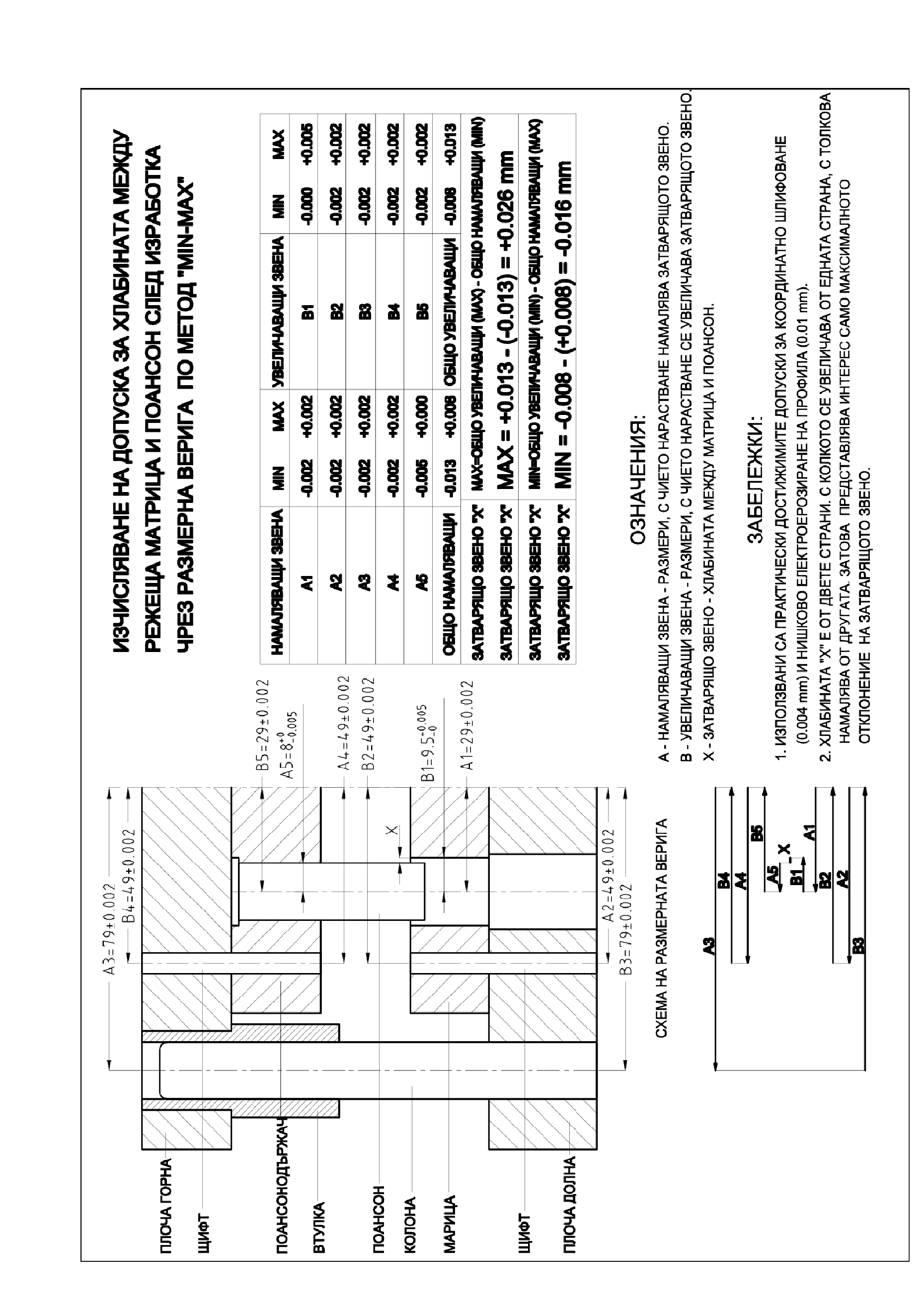
Фиг.11-5
На него са означени определящите разположението на матрицата спрямо поансона размери, с максимално достижимите практически допуски за окончателните операции – нишкова-електроерозираща на активните части и координатно-шлифоваща за всички отвори. Размерите са разположени по начина на тяхното практическо изпълнение – спрямо ос (обикновено се работи със среда на размера, за да се изключат грешки от неправилно измерване). За функционалните размери е създадена размерна верига, чието затварящо звено е хлабината между матрицата и поансона. Решението е търсено по метода „мимимум – максимум”, известен като метод на пълна взаимозаменяемост. Това означава, че се търсят максималното и минимално отклонение на затварящото звено „Х” (в случая хлабината) при изработени размери с предписаните гранични отклонения. Aбсолютната стойност на максималното отклонение на хлабинта достига до стойност от 0.026 mm. Практически това означава, че при хлабина под тази стойност (за дебелини под 0.6 mm) е възможен удар на режещия ръб на поансона по ръба или челната повърхност на матрицата. В действителност, това е само вероятност, но предвид характера на единично производство, рискът да се случи удар поради натрупване на грешки е по-висок от 50 %. Следователно, тук производството и технологията нямат вина и това е обективен процес.
На основа на доказаното по-горе, могат да се направят следните препоръки за проектиране на технологичния процес:
– да се предвидят други технологични методи за постигане на необходимата точност при малка хлабина – метод на напасването или метод на компенсиращо звено;
– да се предвидят методи за съвместно едновременно обработване (матрица-притискач-водеща плоча);
– да се съгласува с конструктора промяна в конструкцията.
За практически цели ще е полезно следното правило:
– при хлабина равна или по-голяма от 0,04 mm (дебелина на материала около 1mm), не се вземат специални технологични мерки;
– при хлабина равна или по-голяма от 0.01 mm, но по-малка от 0,04 mm (дебелина на материала около 0,3-0,8 mm), се вземат специални технологични мерки, прилагащи метода на напасване или компенсиращото звено;
– при хлабина равна или по-малка от 0.01 mm (дебелина на материала до 0,25 mm), се вземат специални технологични мерки, прилагащи метода на съвмесно едновременно обработване и на компенсиращото звено.
Разгледаният случай за типовия технологичен маршрут за „Плоча” от Фиг.11-4 е за хлабина от 0,03 mm и специалните технологични мерки (метод на напасването) се състоят в добавяне на допълнителна операция за разпределяне на хлабината чрез координатно-шлифоване на отворите за колонките при монтирани към плочата матрица, притискач, водеща плоча и поансони. Шлифоването се извършва спрямо центровете на отворите за втулките на водещата плоча. Може да се изпълни и обратно – запаса да е на отворите във водещата плоча. Важно е, да се предвиди в маршрута и да се остави запас на съответните отвори. За координатното шлифоване могат да помогнат регулиращи ексцентрични щифтове за оптимално разпределение на хлабината между матрицата и поансоните от Фиг.5-49 и схемата на възможните измествания с тях от Фиг.5-54.
Случай за специални технологични мерки, прилагащи метода на съвместно едновременно обработване и на компенсиращото звено за хлабина от 0,008 mm (дебелина 0,1 mm), е приложен за инструмента за детайл „Пластина контактна No. 107349”. Щанцата с последователно действие е показана на Фиг.11-6 (неподвижен пакет), на Фиг.11-7 (напречен разрез А-А), на Фиг.11-8 (напречен разрез В-В), на Фиг.11-9 (подвижен пакет), на Фиг.11-10 (технологична схема), на Фиг.11-11 и Фиг.11-12 (спецификации).
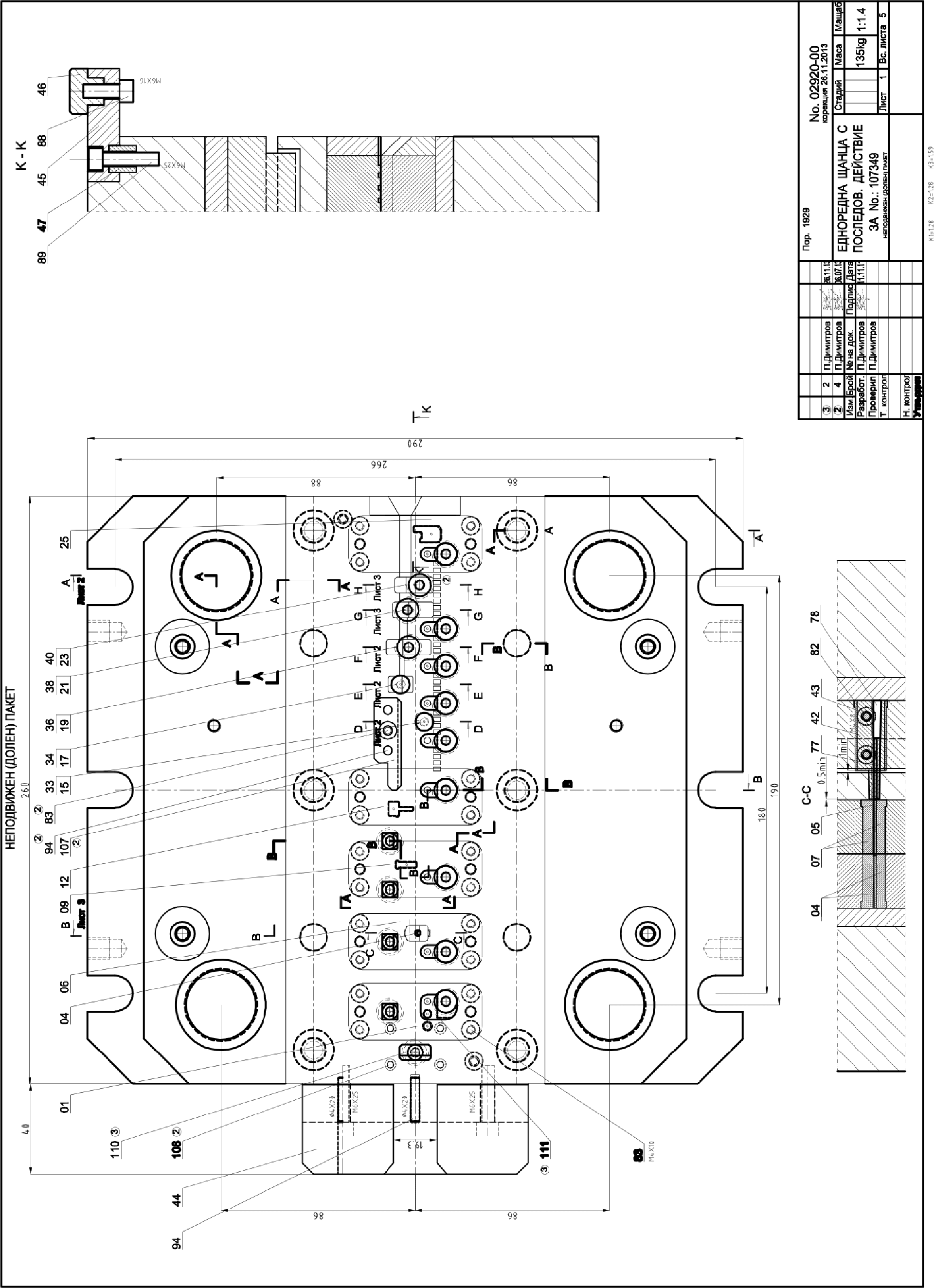
Фиг.11-6
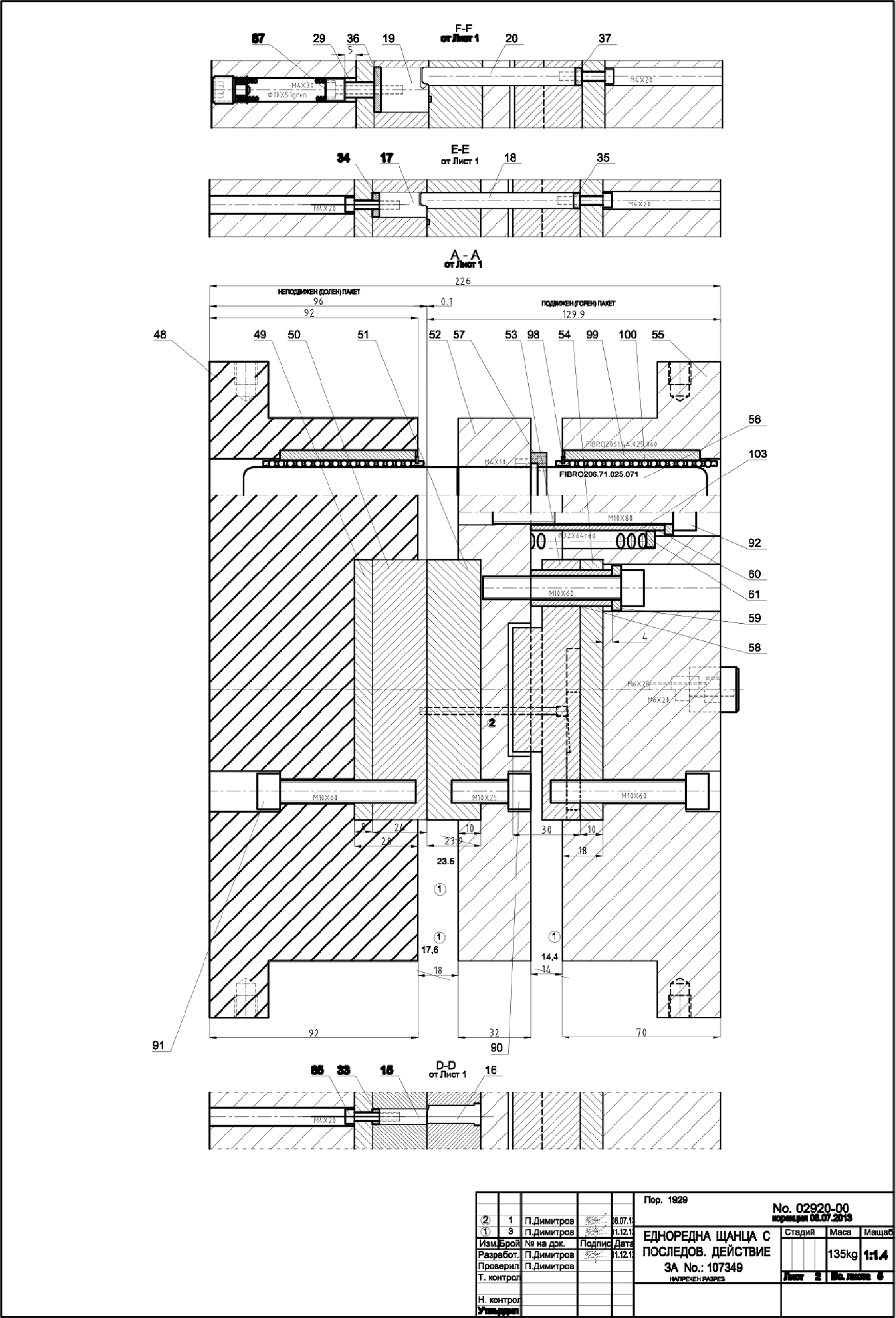
Фиг.11-7
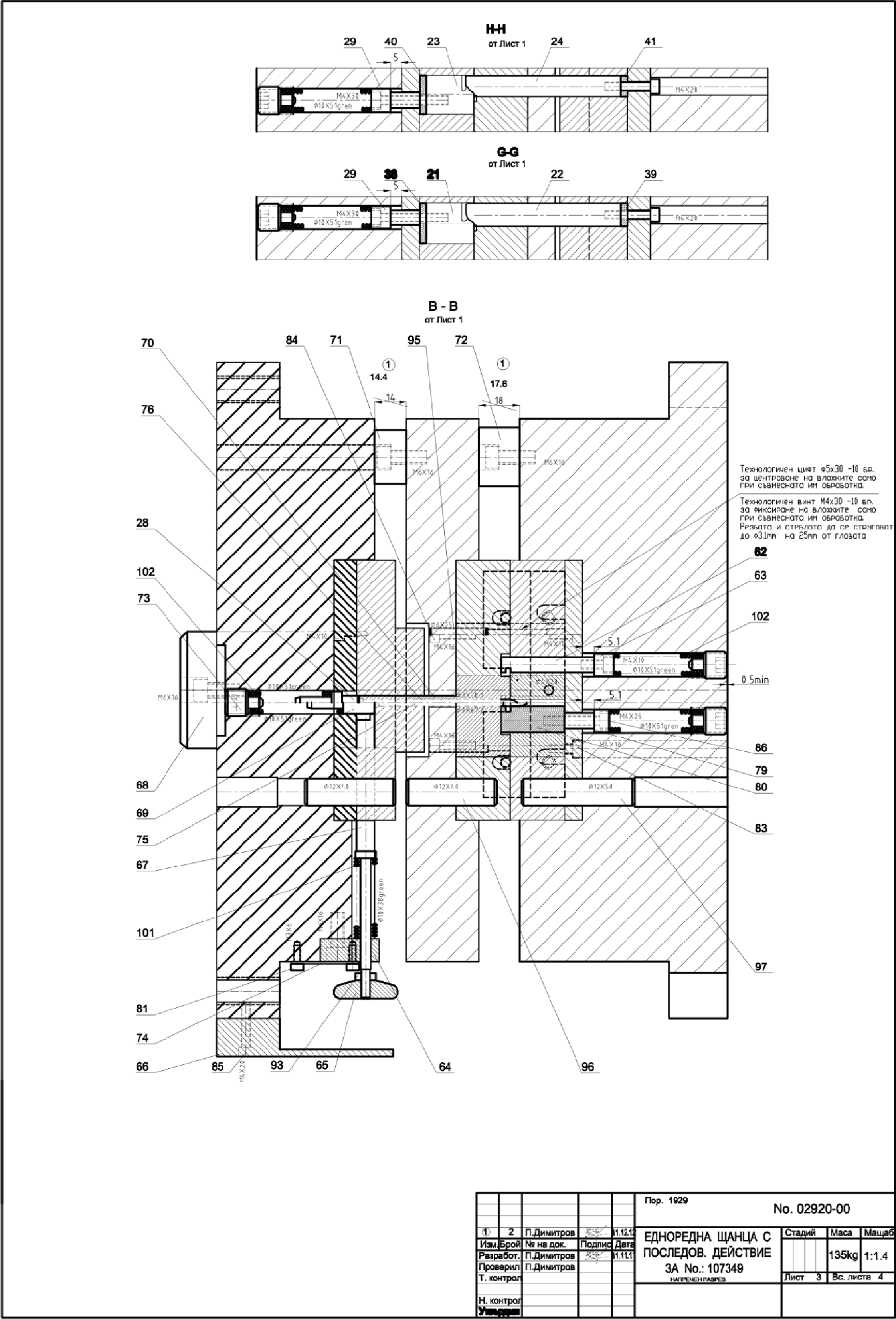
Фиг.11-8
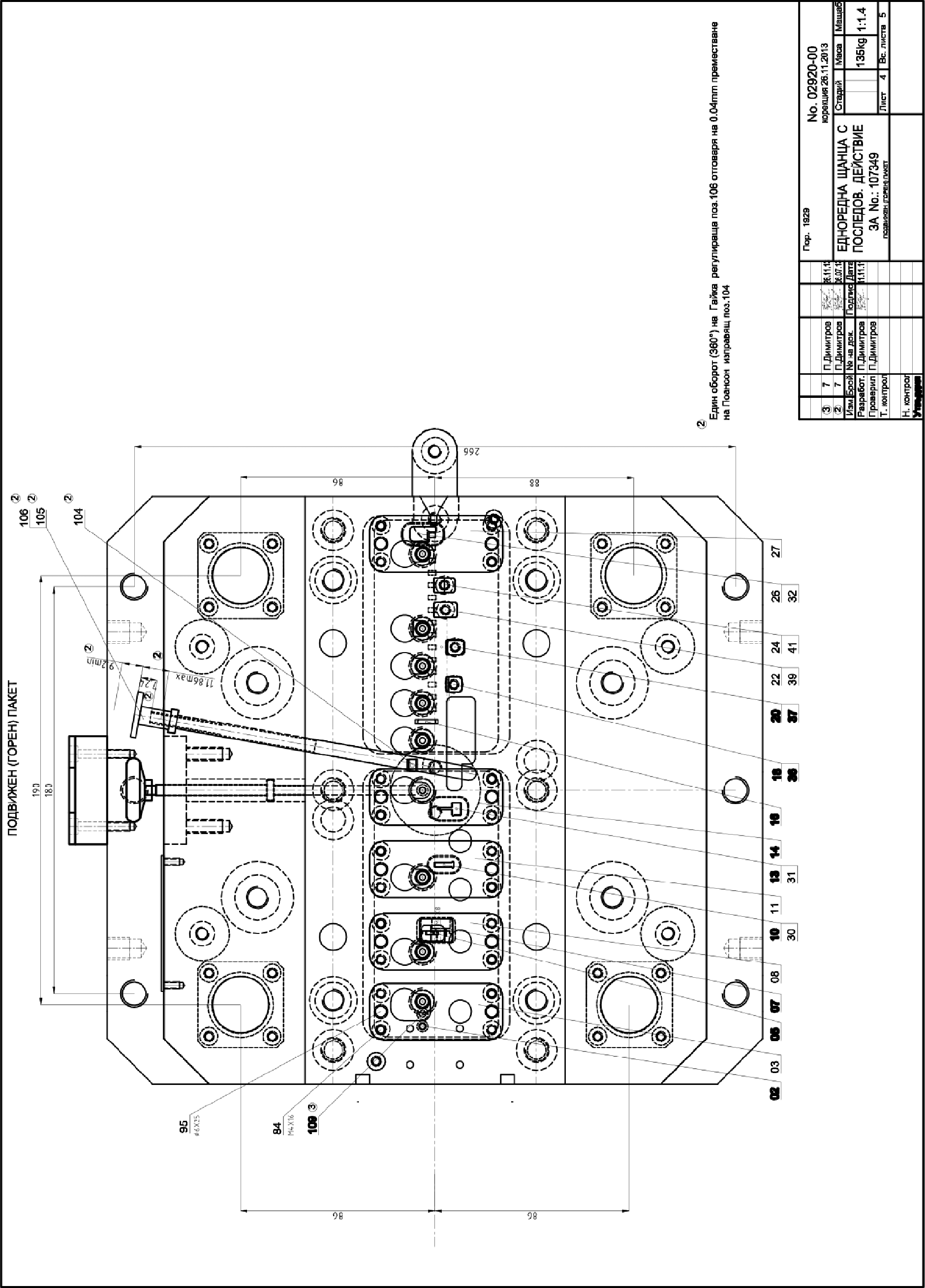
Фиг.11-9
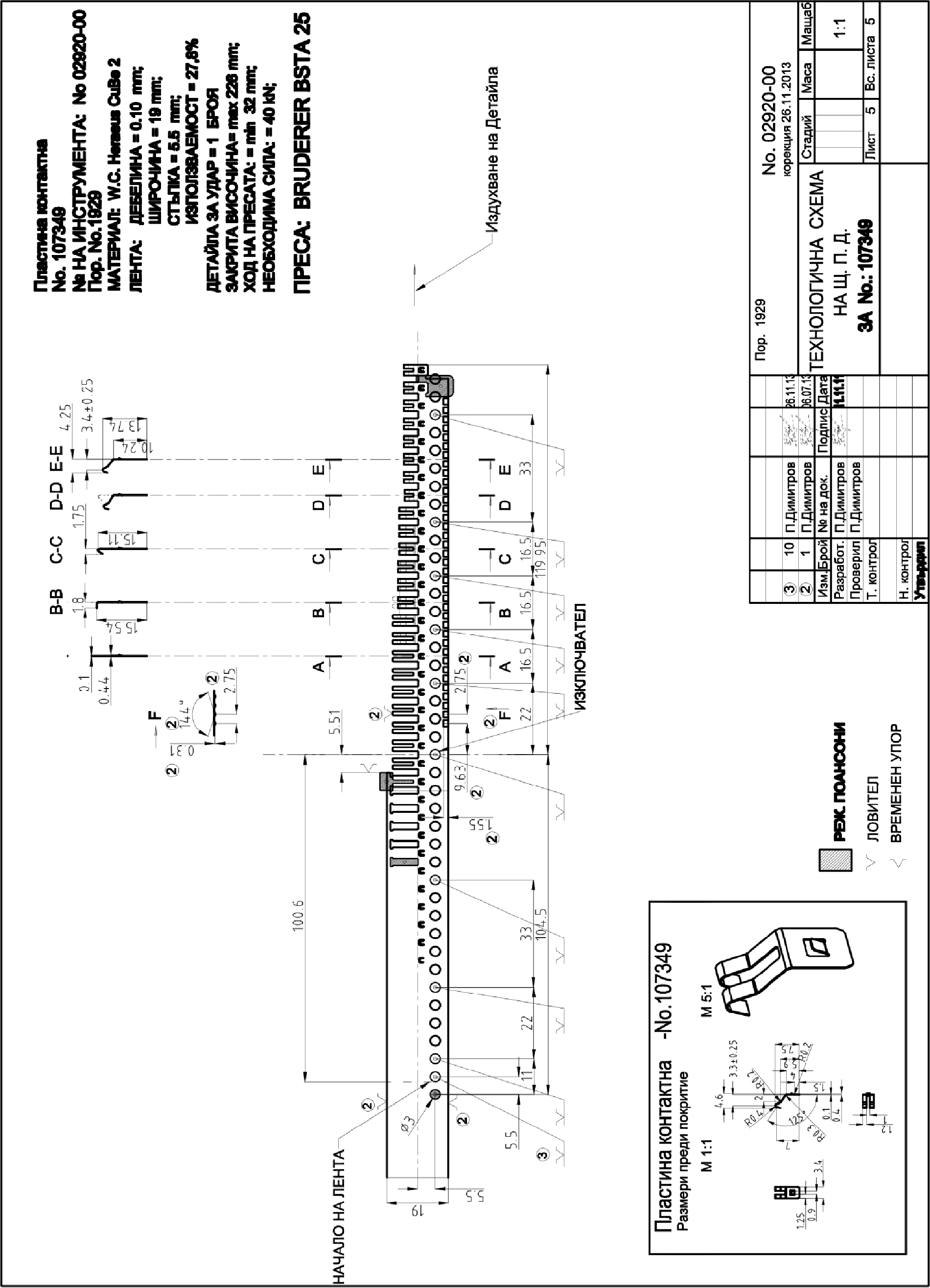
Фиг.11-10
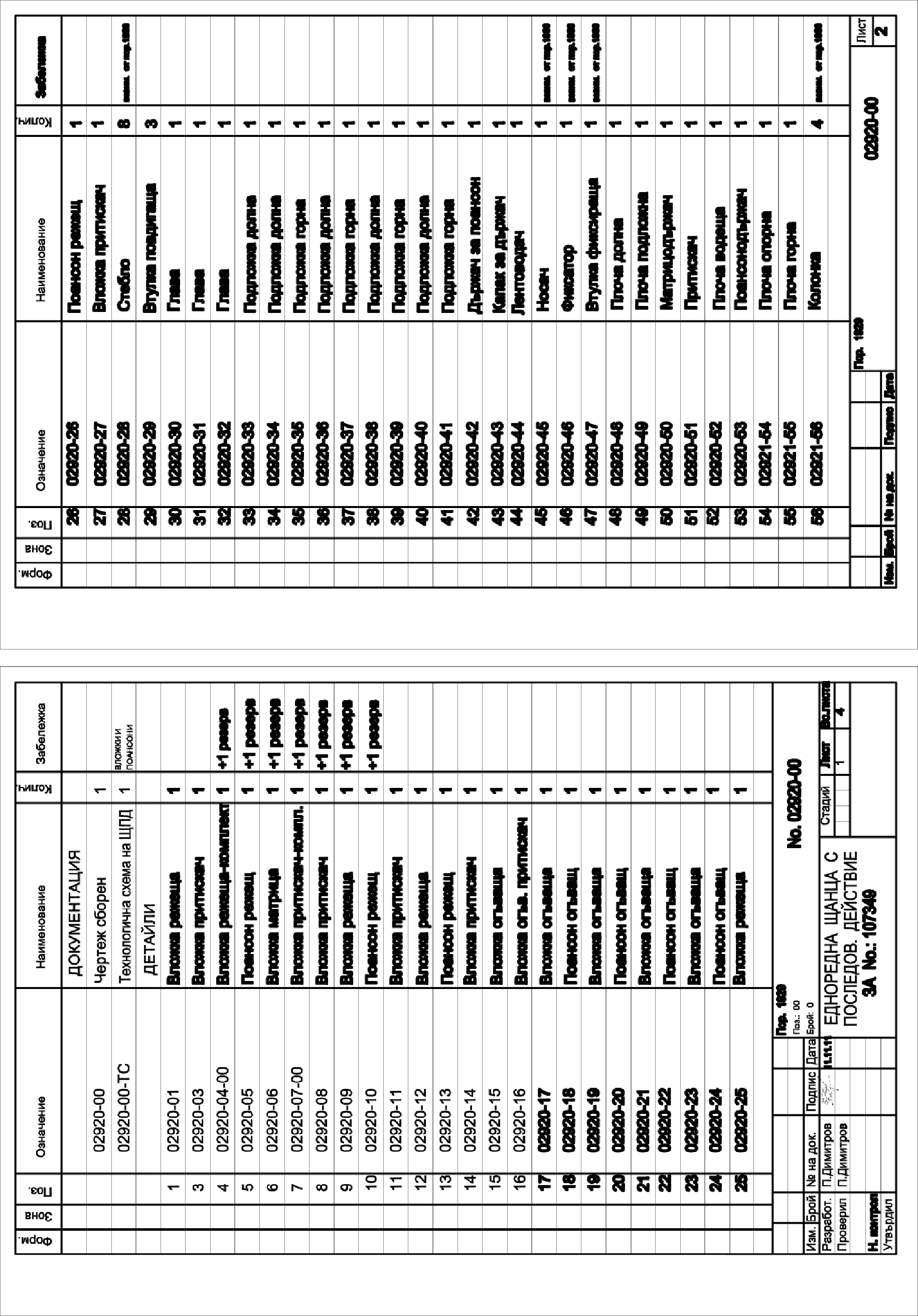
Фиг.11-11
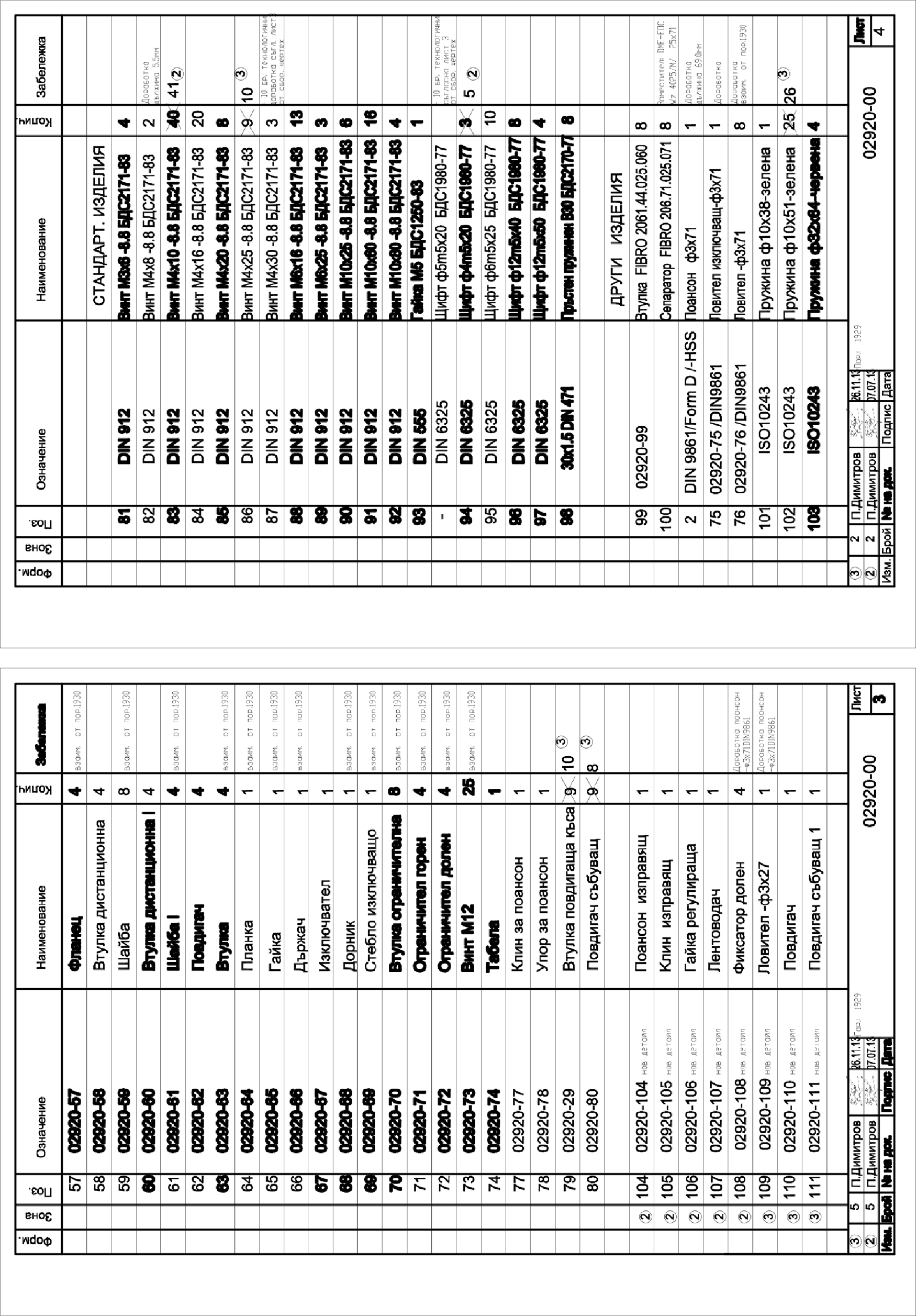
Фиг.11-12
Режещите вложки и поансоните са от материал HSS (1.3343). Трудната изработка при тази хлабина е наложила конструктивно усложняване на инструмента, за да се предвиди прилагане на едновременна обработка на режещите отвори и компенсиране на грешката на тяхното разположение, чрез въвеждане на допълнителни вложки в притискача. Комплект от матрична вложка и вложка за притискача са показани на Фиг.11-13.
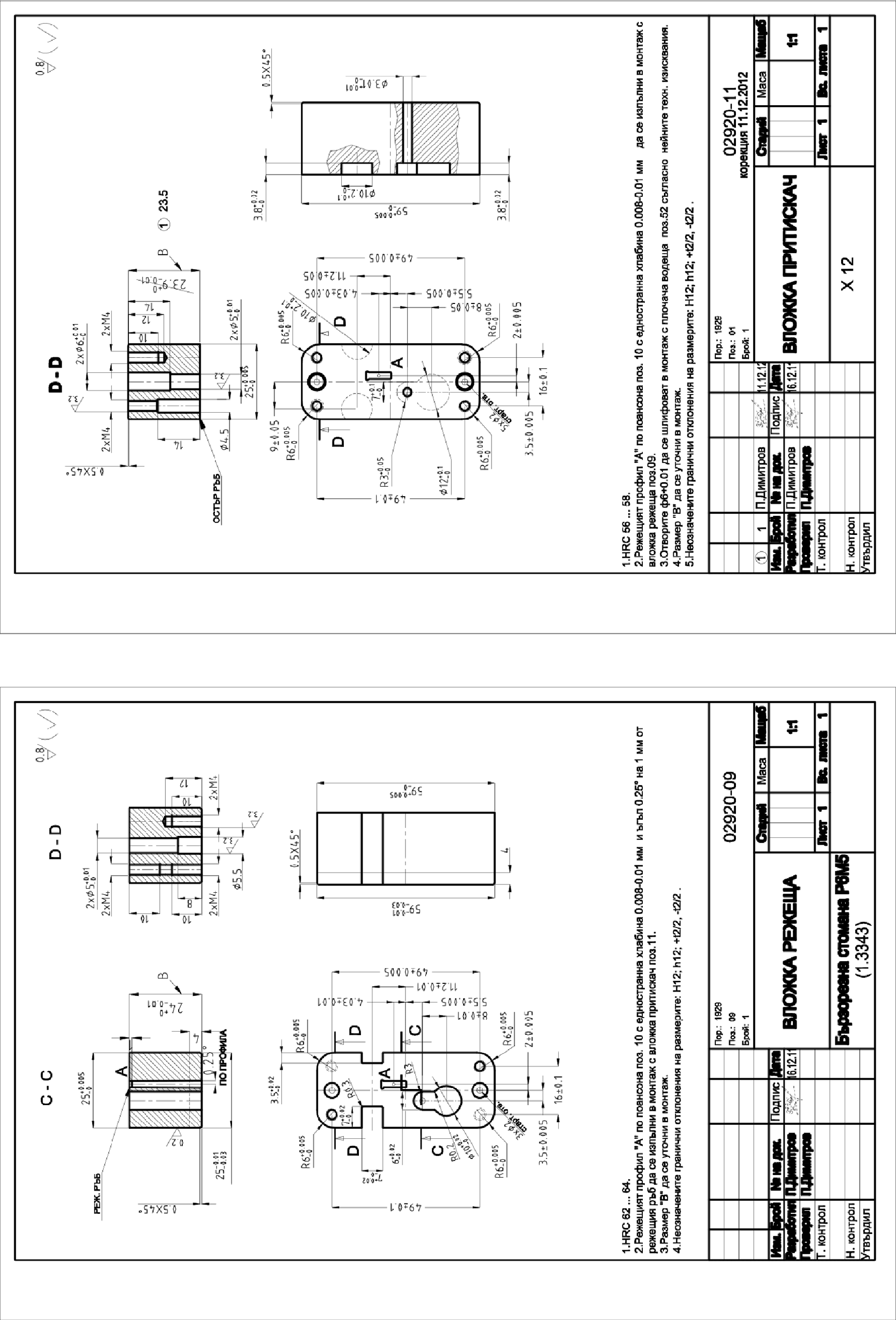
Фиг.11-13
Вложките са с еднакви размери и имат центроващи технологични отвори за щифтове и резбови отвори за взаимно закрепване една към друга. Първоначалната изработка се състои в нишково електро ерозийно изрязване на външните контури на режещите вложки с прибавка (виж Фиг.5-43). Следва нишково електро ерозийно изрязване на външните и вътрешни контури на вложки – притискач съвместно с режещи вложки, закрепени към Целеви Блок-Заготовки (виж Фиг.5-44). Получените след ерозия вложки, остават закрепени една към друга. Габаритните им размери и външни радиуси се шлифоват едновременно на координано-шлифоваща машина. След напасване на поансоните, сглобените комплекти от вложки (режещите) се монтират към матрица, долна плоча, притискач и водеща плоча. В монтирано положение се шлифоват отворите ф6 на вложките за притискача едновременно със съответните отвори във водешата плоча. След поставяне на предвидените щифтове ф6 за връзка с водеща плоча и проверка на движението на поансоните, технологичните щифтове ф5 и винтове М4, свързващи вложките, се изваждат. По този начин конструктивно е заложена технологията за производство (допълнителни технологични щифтови отвори ф5, гарантиращи центроването на частите при съвместното шлифоване на отворите ф6 в монтаж и резби за свързване на вложките при съвместа обработка).
4. Обобщаване на технологичния процес.
Получените маршрутни технологични карти за всички детайли на инструмента позволяват да се сглоби и оцени целия технологичен процес. Те отговарят на изискването да се опише пътя за всеки детайл, времето за неговата изработка и разпределението му по различните операции, размерите и теглата на материала на заготовките. Едновременото разглеждане на заложените времена в технологичните карти позволява формиране на общото натоварване по видове машини и операции, определяне на срок за изработка и оценка на необходимите парични (заплати) и времеви ресурси, както и цената на целия инструмент. Използването на данните за материал и размери на заготовката от машрутните карти, позволява да се създадат обобщени списъци с необходимите по вид и количество материали за доставка. Изчисленото общото време, неговото разпределение по операции, паричните разходи за всяка операция и цената за щанца с последователно действие за пробиване, огъване, изрязване за „Контакт двоен“ поръчка 1242В (виж общия вид на Фиг.11-16,
лентата на Фиг.11-17, матрица на Фиг.11-18 и притискач на Фиг.11-19) са показани в таблица на Фиг.11-14, а за твърдосплавна двуредна щанца с последователно действие за пробиване и изрязване на „Ламела EI-26“ поръчка ТЩ0597 (виж общия вид Фиг.6-69 и лентата Фиг.6-72) са показани в таблица на Фиг.11-15.
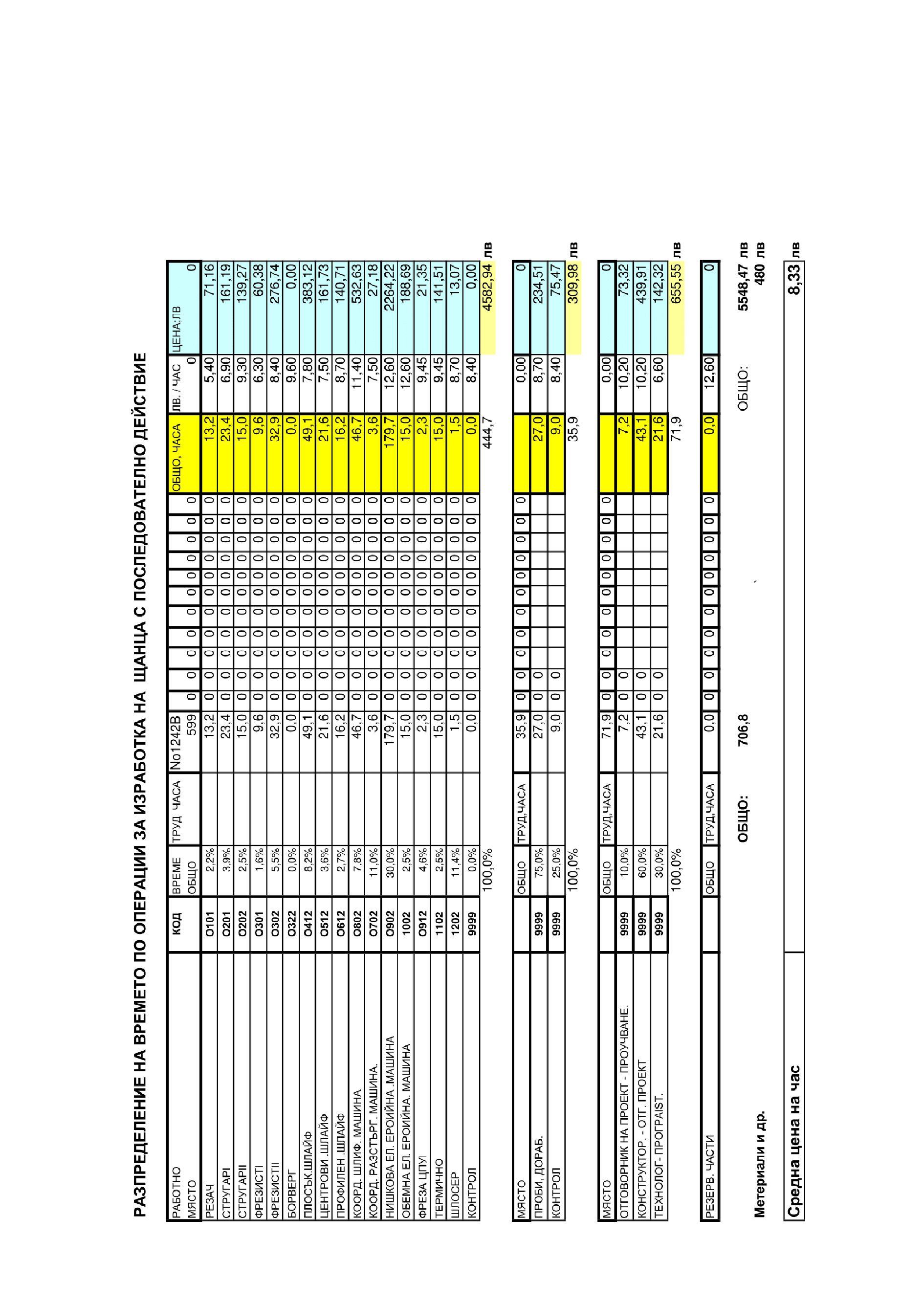
Фиг.11-14
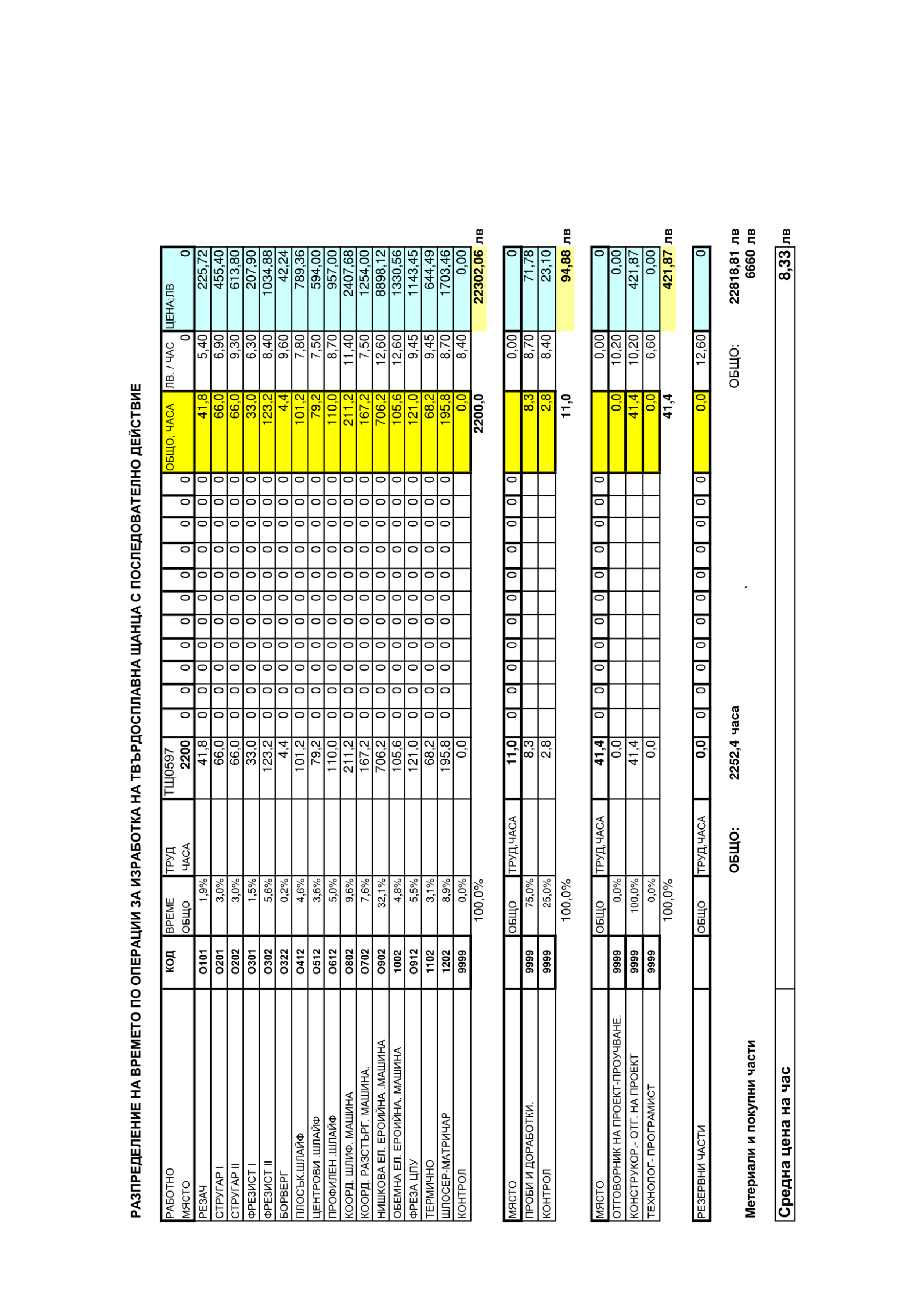
Фиг.11-15
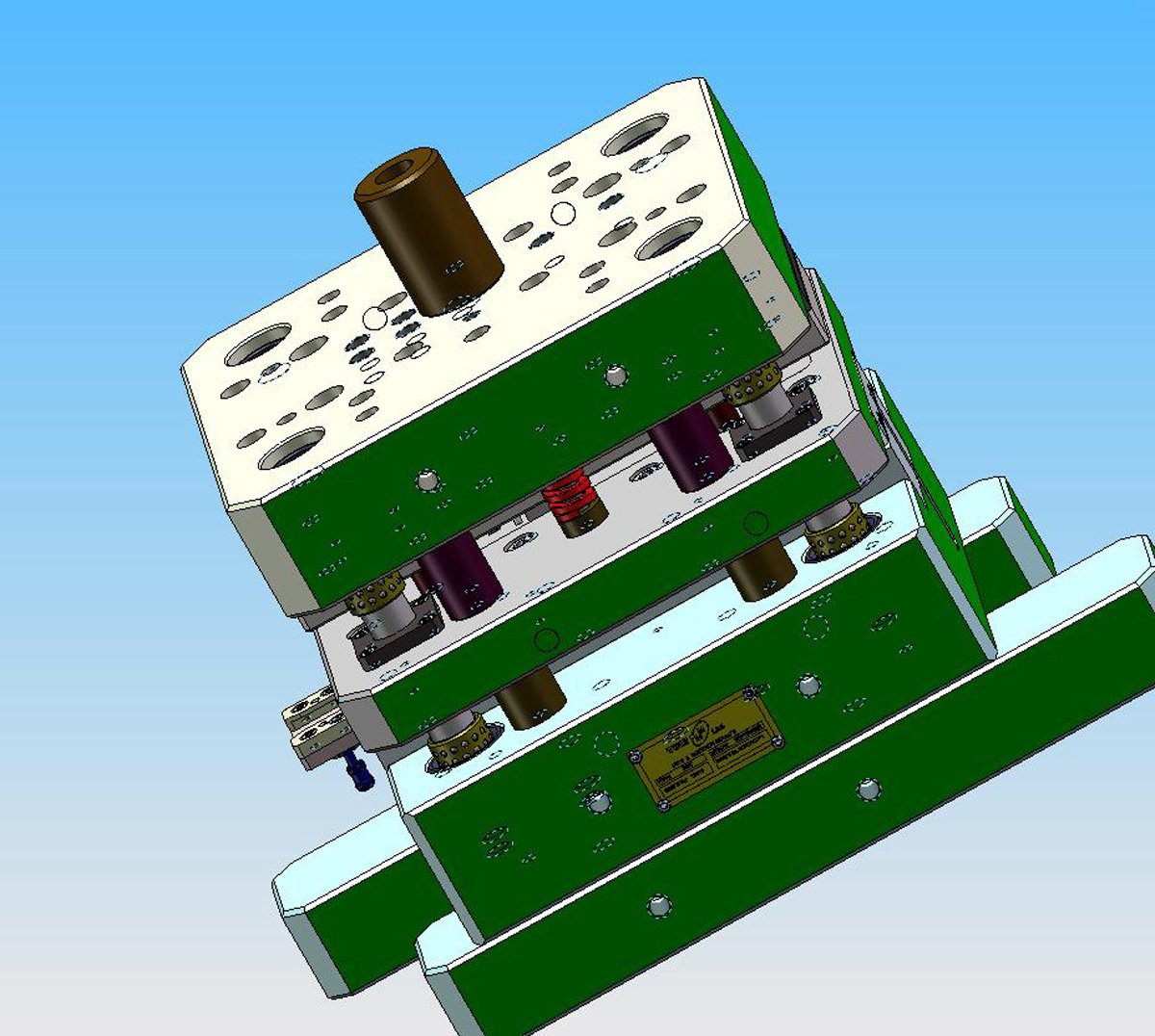
Фиг.11-16
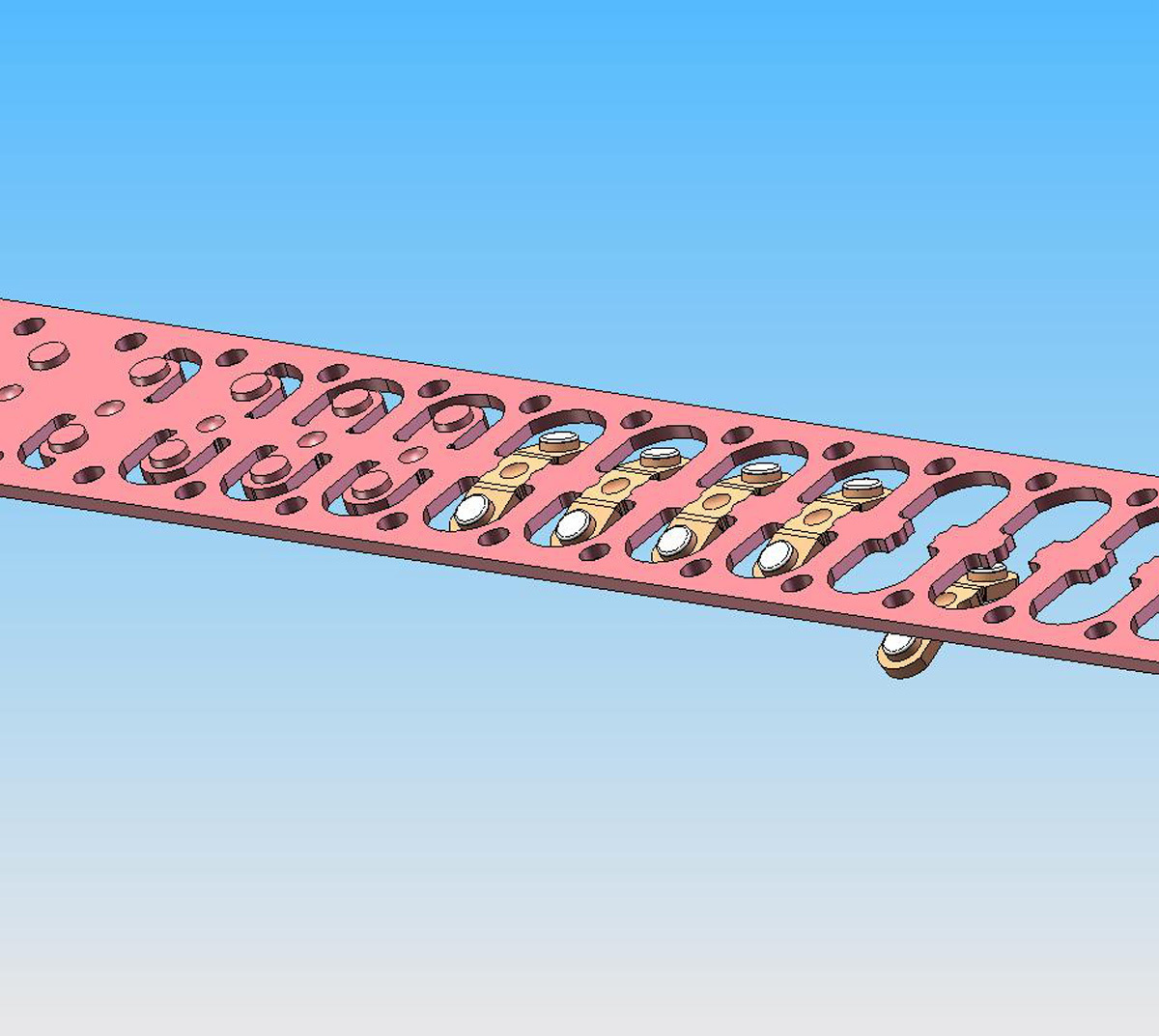
Фиг.11-17
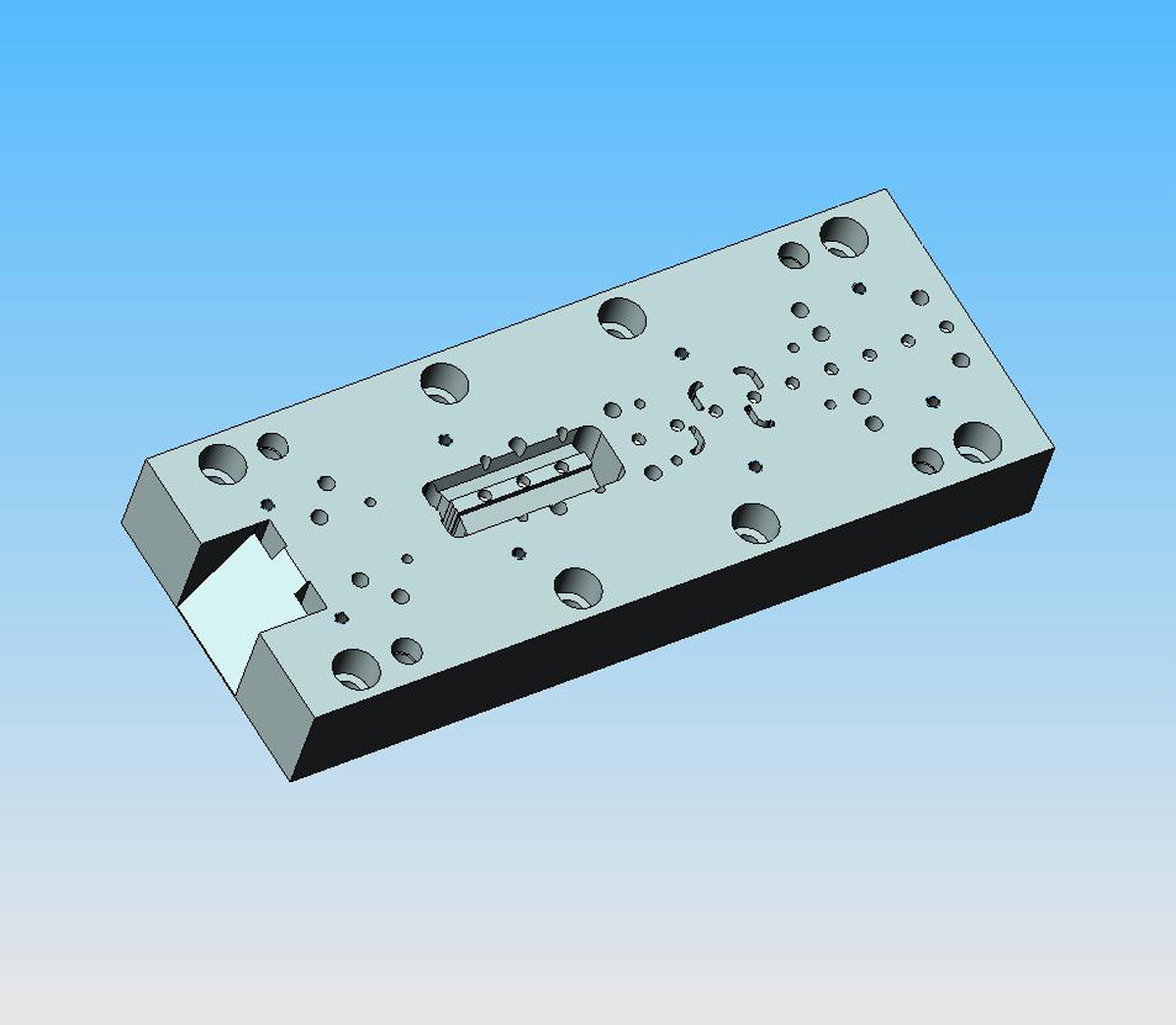
Фиг.11-18
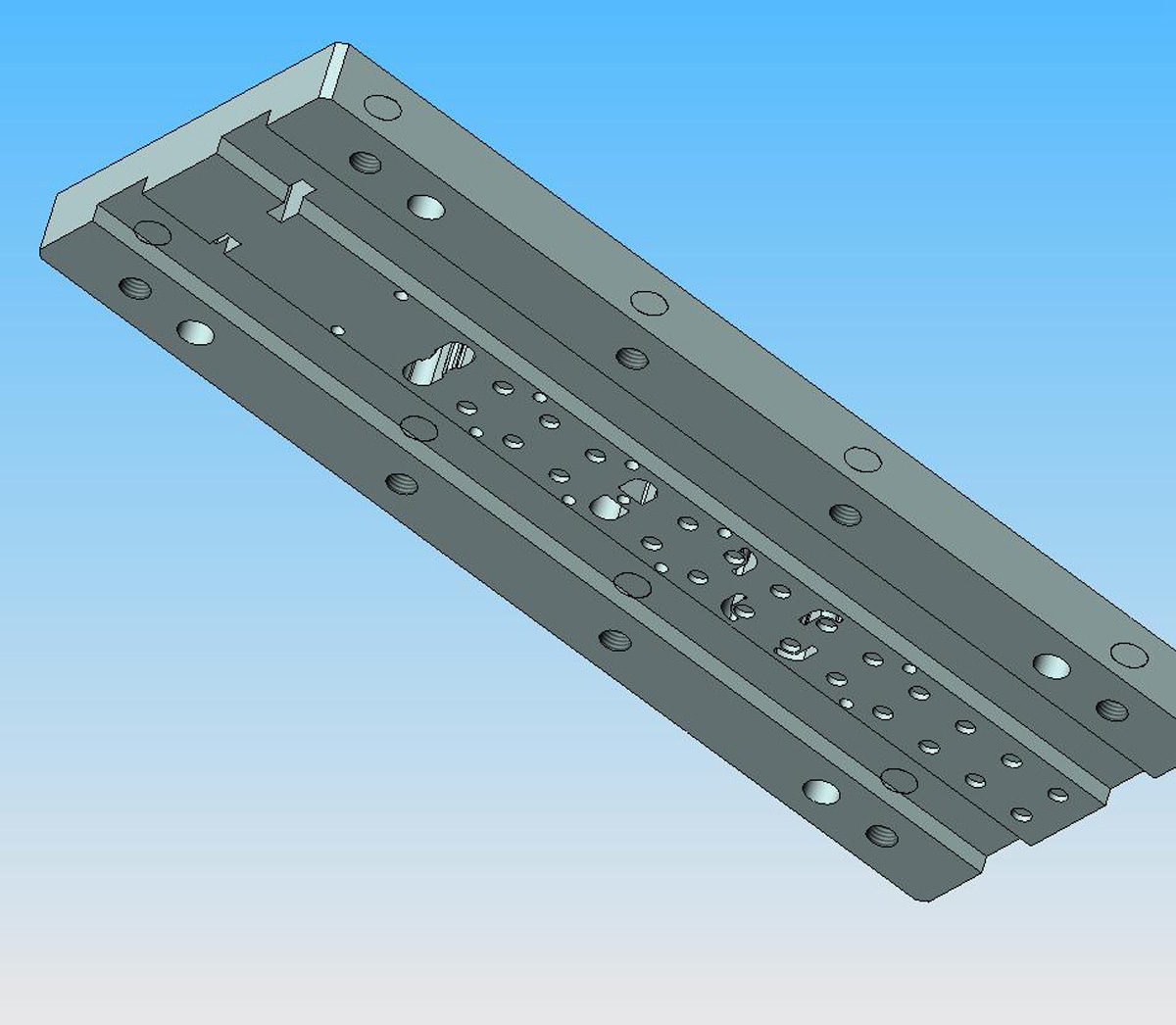
Фиг.11-19
От таблиците се вижда, че познавайки общото време и приблизителното разпределение по операции, разходите за изработка и необходимия ресурс от време могат се планират още в етапа на разработка на идеен проект на инструмента.
ГЛАВА 12. ОРГАНИЗАЦИЯ НА ИНСТРУМЕНТАЛНОТО ПРОИЗВОДСТВО, ИЗРАБОТКАТА, МОНТАЖА И КОНТРОЛА НА ИНСТРУМЕНТАЛНАТА ЕКИПИРОВКА ЗА ПРЕСОВА ОБРАБОТКА НА ЛИСТОВ МАТЕРИАЛ
Производственият процес на специални нестандартни инструменти, включително щанци, изработва единични уникални изделия, чиито съставни части рядко са повече от един брой от вид. Партида от еднакви части тук е изключение, ако все пак се срешат такива, техния брой рядко надхвърля 4 детайла. Обикновено се изработват по няколко различни щанци в един и същ период от време, всяка от които е съставена от десетки оригинални части, изискващи над 10 технологични операции. Погледнато от страни, движението на това огромно количество детайли изглежда хаотично, често пътищата на детайлите се присичат, получава се натрупване на детайли и задръстване при някои машини (тесни места), отделни детайли се загубват сред общия поток и трудно могат да бъдат открити. Аналогията за единично производство на инструменти е „Брауново движение на молекулите” – подобно на тях, с увеличението на температурата (в случая броя на изработваните щанци), нараства интензивноста и броя на ударите между молекулите (в случая натрупване на детайли, тяхното изчезване или препокриване с други), до достигане на пълна неуправляемост. Такъв производствен процес не може да е ефективен, без да се вземат мерки за създаване на някъкъв ред. За това е нужно организиране, планиране и управление на инструменталното производство.
1. Организиране на инструменталното производство.
Нестандартното инструментално производство може да бъде организирано по различни начини в зависимост от големината, разбирането на ръководството (собствениците) и традициите на различните фирми. При всички форми, то трябва да притежава технологичен (обработващи машини), работен (квалифицирани работници) и управленски (ръководство) ресурс, който ще определи неговия производствен капацитет и възможности. Необходимите дейности и ресурси се намират в непрекъснати функционални връзки по между си. Организационно функционалната схема на инструменталното производство е показана на Фиг.12-1.
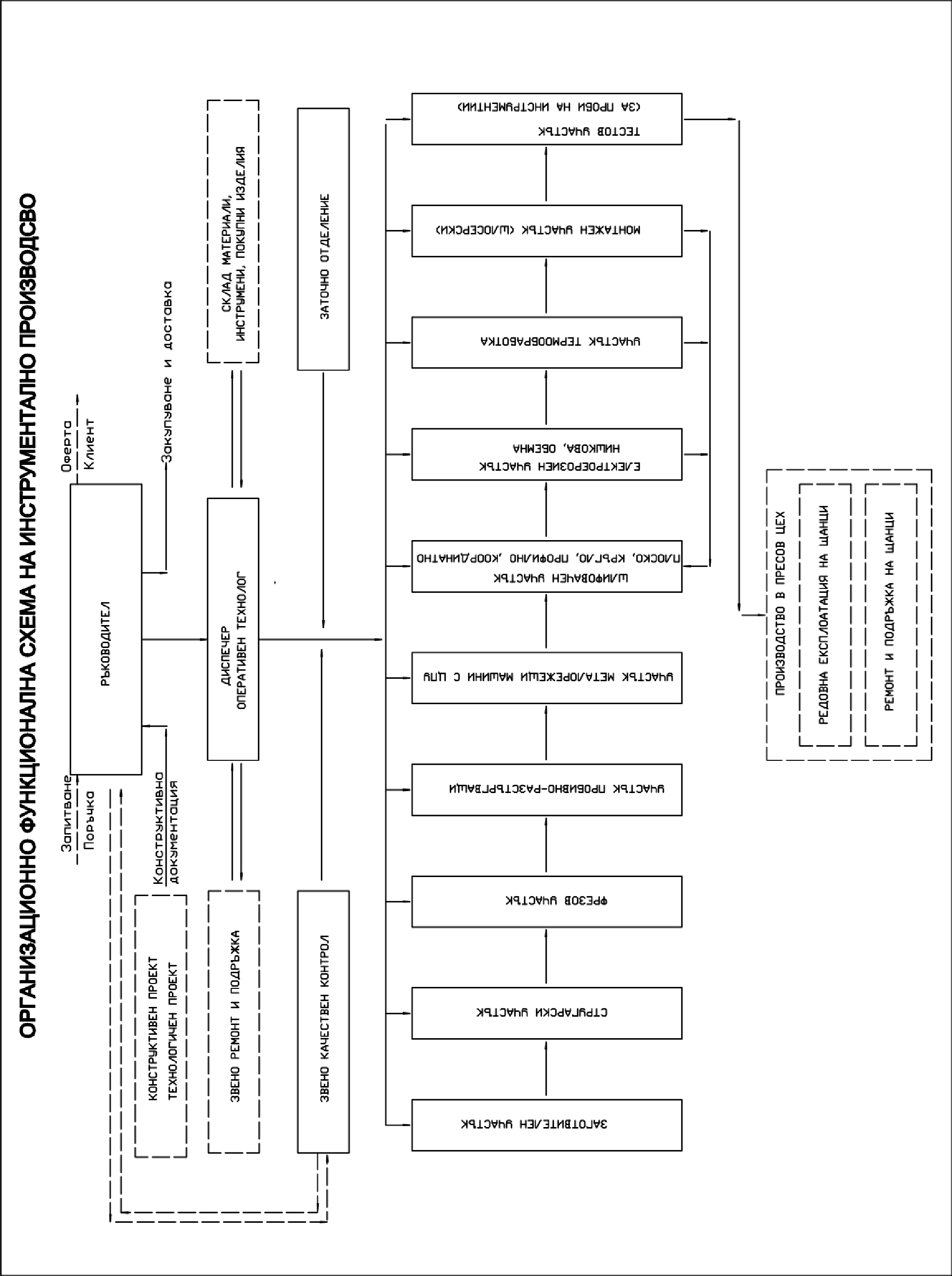
Фиг.12-1
От нея се виждат основните дейностите, които трябва да се изпълнят при изработката на щанцови инструменти – осигуряване на материали, покупни изделия, конструктивно-технологична документация, изпълнение на различните технологични операции върху различни металообработващи машини, монтаж, контрол, проба на иструментите, поддръжка на машините и необходимите взаимодействия между тях и управлението. Разбира се, не всички показани звена и участъци са необходими – възможно е да няма голяма част от обработващите участъци (например електроерозиен участък, участък с металорежещи машини с ЦПУ, тестов участък и други). За част от тях може да се използва коопериране, външен под изпълнител, или да не са включени в структурата на инструменталното призводство – на пример звено за ремонт и поддръжка, конструктивен отдел, склад за материали и инструменти, пресов цех (показани с прекъсната линия). Главната ерархична структура обаче, остава неизменна: ръководство – диспечиране – изработка – проба – пускане в производство. Технологичните възможности на най-използваните машини бяха разгледани по-горе. Физическото разделяне на участъци по видове машини е направено за удобство и не е задължително. Във всички случаи обаче, трябва да се отчита вида на извършваните операции на конкретните машини – недопустимо е, на пример до универсална фреза, използвана за зачистване на газоплазмено отрязани плочи, да се разположи прецизна шлифоваща или нишково електорозийна машина, защото възникналите вибрации и сружките ще оказват влияние на нейната точност при работа. Необходимо е да се отчете, че някои машини (електроерозийни, шлифоващи) трябва да се отделят в самостоятелно помещение за експлоатация в термоконстантна среда. Колкото по-малко е инструменталното производство, толкова повече ще се различава от показаната схема.
Необходимостта от квалифицирана работна сила бе коментирана не еднократно. Работниците не само трябва да познат машините, с които работят и да разчитат информация от чертежа, но и да са запознати с особеностите при изработката на щанци. За това е много важно обучението на място, което се подценява у нас. Работникът трябва да знае до какви последствия могат да доведат неговите неправилни действия и как да ги избегне, защото единичния характер на инструменталното производство не позволява да се контролират напълно всички операции. Важна роля изпълнява контрола на качеството. Препоръчително е, всички активни части да се контролират преди и след термообработка или преди окончателн монтаж. Тук трябва да се спази основния принцип за независимост на контролиращото звено, за да се осиури неговата безпристрастност. Наличието на качествен контрол позволява да се реагира навреме и да се решат потенциалните проблеми за инструмента.
Основното при изграждането на инструментално производство, е начина на организиране на ефективно управление и контрол. Рационалните управленски решения могат да се вземат само на база достоверна и актуална информация за хода на производствения процес. Събирането на тази информация и контрол за изпълнението на самите решения, се извършва от диспечер. В малките инструментални диспечерските функции и тези на оперативен технолог се изпълняват от организатор на производсво, бригадир, отговорник или дори от самия ръководител. Важната информация за хода на производсвото на щанцов инструмент, е свързана с доставката на всички материали, местоположението и изпълнението на технологичните операции за всеки детайл, незавършените детайли, техните срокове и необходимия машинен капацитет, резултатите от проведен контрол на качеството, допуснати отклонения и предприети мерки, необходимост от промени в технологията за изработка или конструкцията на щанцата. Оперативните технологични решения се взимат за всички операци при самата машина. Винаги има непредвидени трудности, пречещи на точното изпълнение на предписаната технология, а при малки инструментални често няма такава в писменна форма и необходима намеса на компетентно лице, запознато с целия процес на изработка, конструкцията на инструмента и последиците от различнте отклонения.
2. Управление и планиране на инструменталното производство.
Ефективното управление на инструментално производство се нуждае освен от точна информация за моментното състояние и от планиране изработката на новите щанци. На базата на попълнените маршрутни технологични карти и обобщаването на целия технологичен процес в таблиците за разпределение на времето за изработка по операции (виж Фиг.11-14 и Фиг.11-15), може да се изработи график за производство на всеки инструмент. За да е реалистичен графика, изработката на нови щанци трябва се разгледа едновременно с произвежданите в момента инструменти. Всяко производство разполага със съответен ресурс от машини, работници и време (смени), които определят капацитетните възможности за изработка. Оценката се прави по операции, едновременно за всички изработвани инструменти за определен период, например месец - Фиг.12-2.
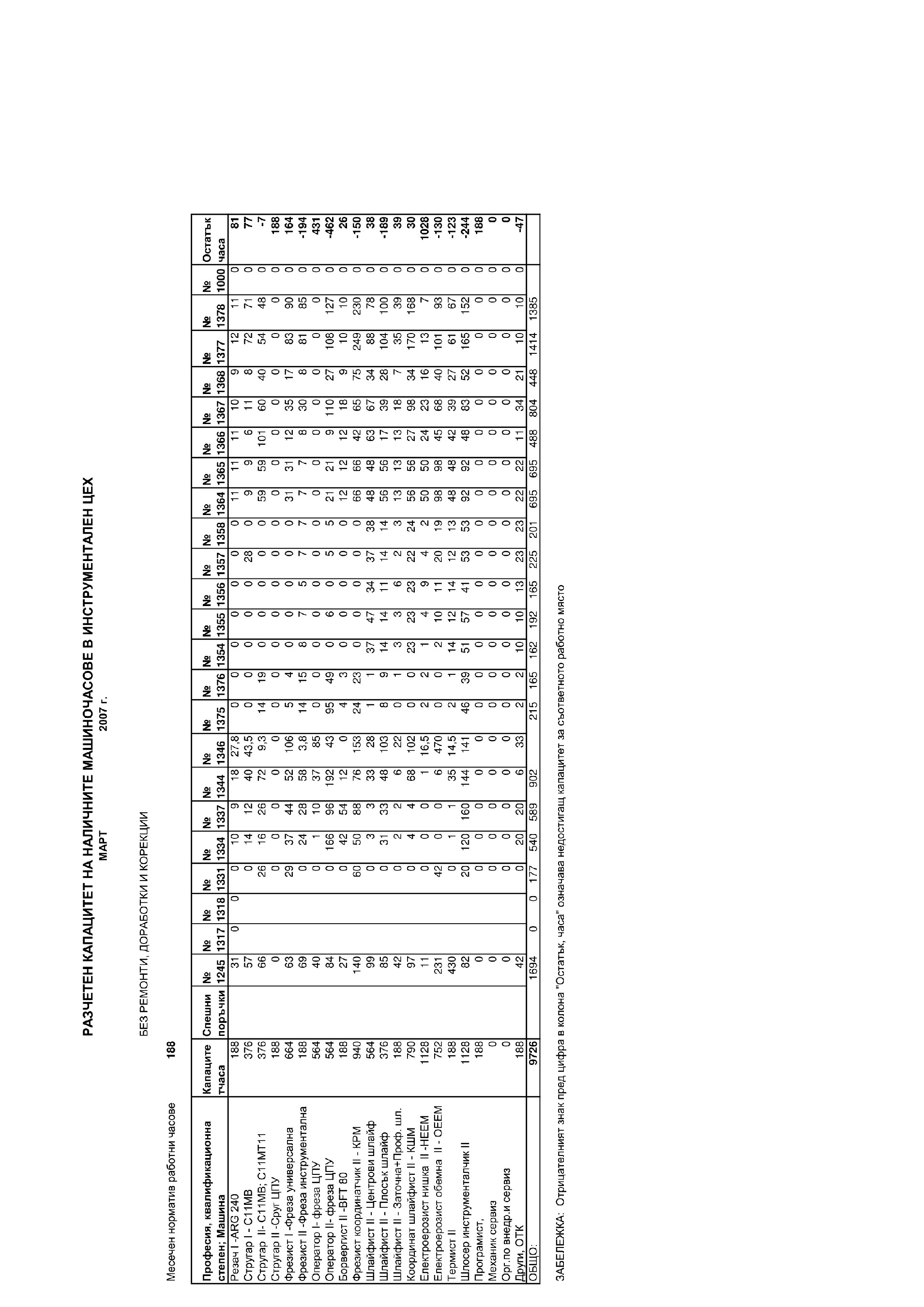
Фиг.12-2
Целия разполагаем ресурс от време (капацитета) се вижда на най-долния ред от втора колона. Той зависи от броя машини, смените на които работят и тяхната продължителност. Срещу всяка операция в крайната колона е остатъчния ресурс от време. Възможността за изпълнение на която и да е технологична операция върху всички инструменти е реална само, ако тази стойност не е отрицателно число, което означава недостиг от време. Такива операции са тясно място и са възможни два подхода за решаване:
– изнасяне на тези опеации при външен под изпълнител;
– увеличаване на натоварването на тези машината (броя смени и тяхната продължителност), ако това е възможно. Често този подход влиза в конфликт с националното законодателство и причинява повече проблеми, отколкото ползи.
Ако капацитетните възможности са достатъчни, необходимо е да се подготви линeен график за изработката на щанцата по дни (виж Фиг.5-51). За тази цел са необхдими подобни графици за останалите инструменти и реда на изпълнение на поръчките (тяхната спешност).
Контролът за изпълнението на всяка операция за произволен детайл от щанцата и актуална информация за неговото местоположение в разглеждан момент от време, изисква попълване на маршрутен лист за всеки инструмент. Пример на такъв за Щанца огъваща №02943 е показан на Фиг.12-3.

Фиг.12-3
При него в първата колона са включени всички работни места за технологични операции, а в първия хоризонтален ред всички позиции на оригинални детайли от щанцата. Под всяка позиция са маркирани операциите, през които трябва да премине, като оцветяването показва изпълнените към разглеждания момент. След като дадена операция е оцветена, то детайла в момента се намира при следващата по ред, неоцветена операция. Така проблемът с „изчезващи“ детайли отпада.
Важен момент за бъдещо планиране е събирането на актуална информация за времето на изработка. Причините за отклонения са много – субективни грешки на технолога или работника, по-големи от необходимите прибавки, неподходящо избрани инструменти и режими, неясноти в чертежите и много други. Основната причина обаче е, че не се изчисляват необходимите времена, поради характера на единично производство, а се задават от технолога по интуиция на база натрупания опит. Добра практика е, реалното време за операцията да се съобщи на диспечера, който да го впише в съответната графа на маршрутния лист, след което да я оцвети. Тази информация по късно може да се сравни със заложената в технологията и за в бъдеще да се изработват много по-точни прогнози.
3. Особености на изработката, монтажа, и контрола на щанцови инструменти.
Инструменталната екипировка за щанцоване винаги включва разделителни операции, като пробиване, изрязване, отрязване, просичане, зарязване. Те изискват строго определена хлабина между матрица и поансон, чиято равномерност и големина определя трайността (живота) на щанците. При това, процесът на щанцоване е динамичен, което означава допълнителна промяна на хлабината под действието на възникващите сили при работа. Затова, от решаващо зачение е, тя да се осигури в процеса на изработка. Типично оборудване, използвано при изработка на щанците, са нишково електоерозийна машина, координатно шлифоваща машина, профилно (оптична) шлифоваща машина. Те позволяват при правилна последователност на операциите да се постигне условието за равномерна хлабина. На база на нарупания през годините опит, може да се препоръча следната технологична последователност при изработка на щанците:
– Изработка на поансони;
– Изработка на поансонодържачи (когато отворите им са с хлабина спрямо поансоните);
– Изработка на матрици;
– Изработка на притискачи в комплект с водещи плочи (ако са с еднаква хлабина);
– Пробен монтаж и проверка на режещите поансони за необходимата хлабина;
– Извеждане на центроващи отвори за щифтове или отвори за водещи колонки и втулки при сглобени матрици, притискачи, водещи и долни плочи, поансони (проникнали в отворите на матрицата с работния ход).
Много операционните щанци с последователно действие и голямо габаритните щанци имат вложкова или секционна конструкция. За пример са показани типични ленти от такива щанци на Фиг.6-68, Фиг.12-4, Фиг.12-5, Фиг.12-6, Фиг.12-7 и детайли на Фиг.12-8.
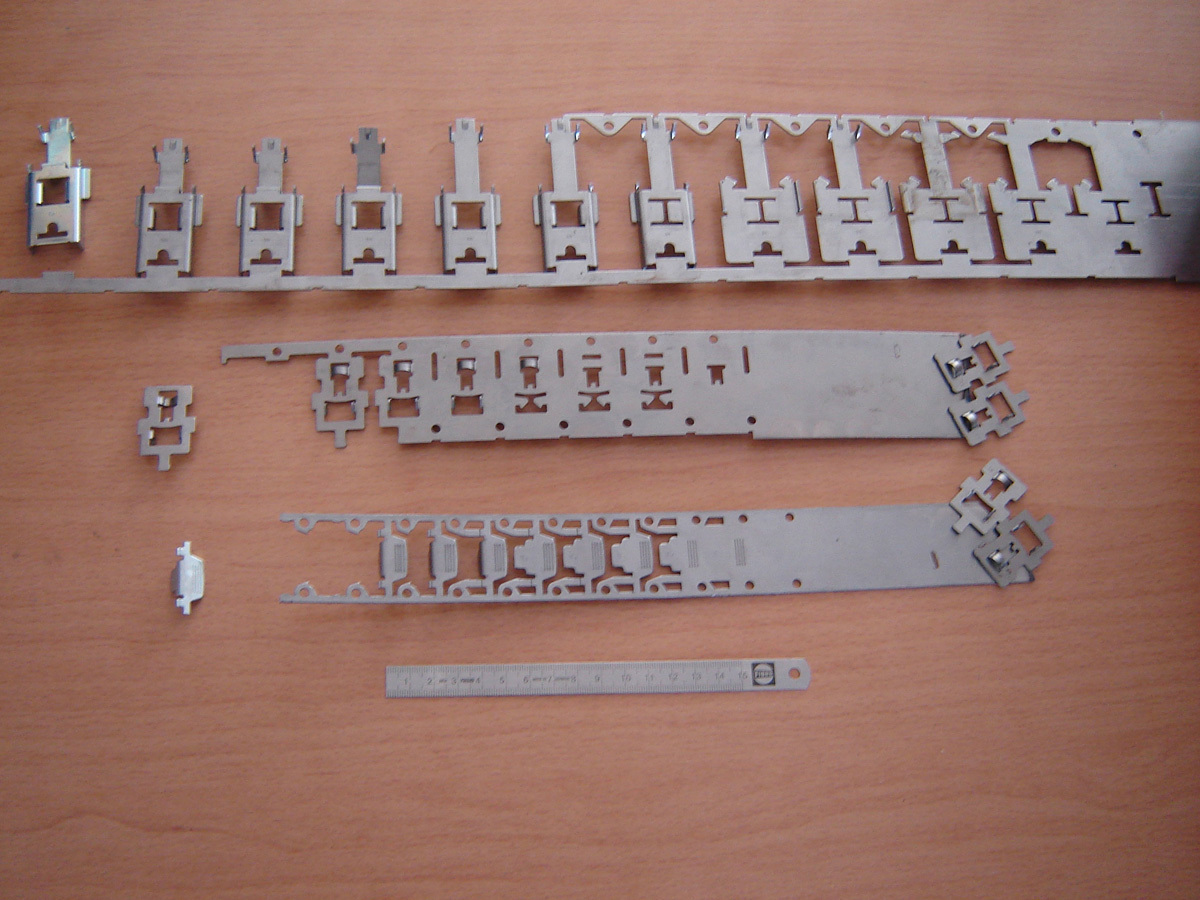
Фиг.12-4
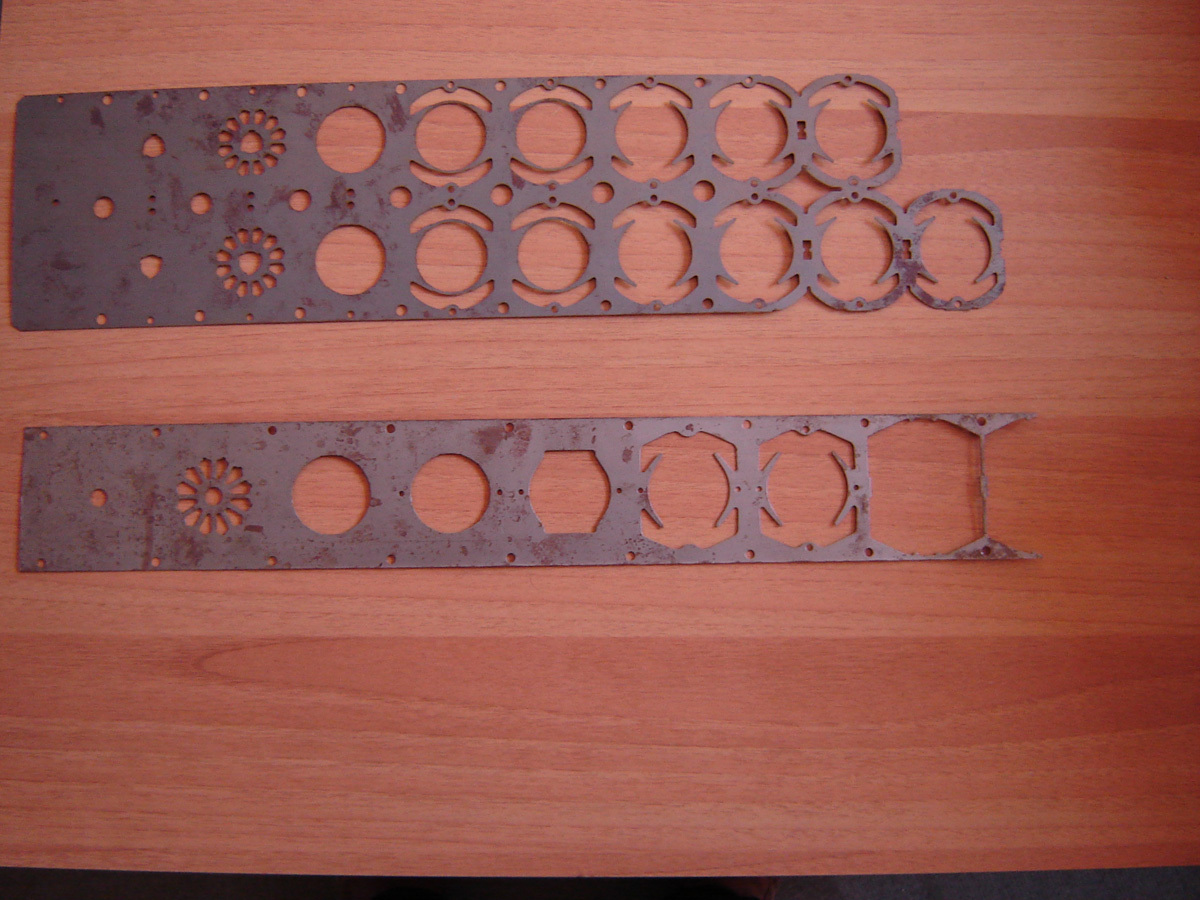
Фиг.12-5
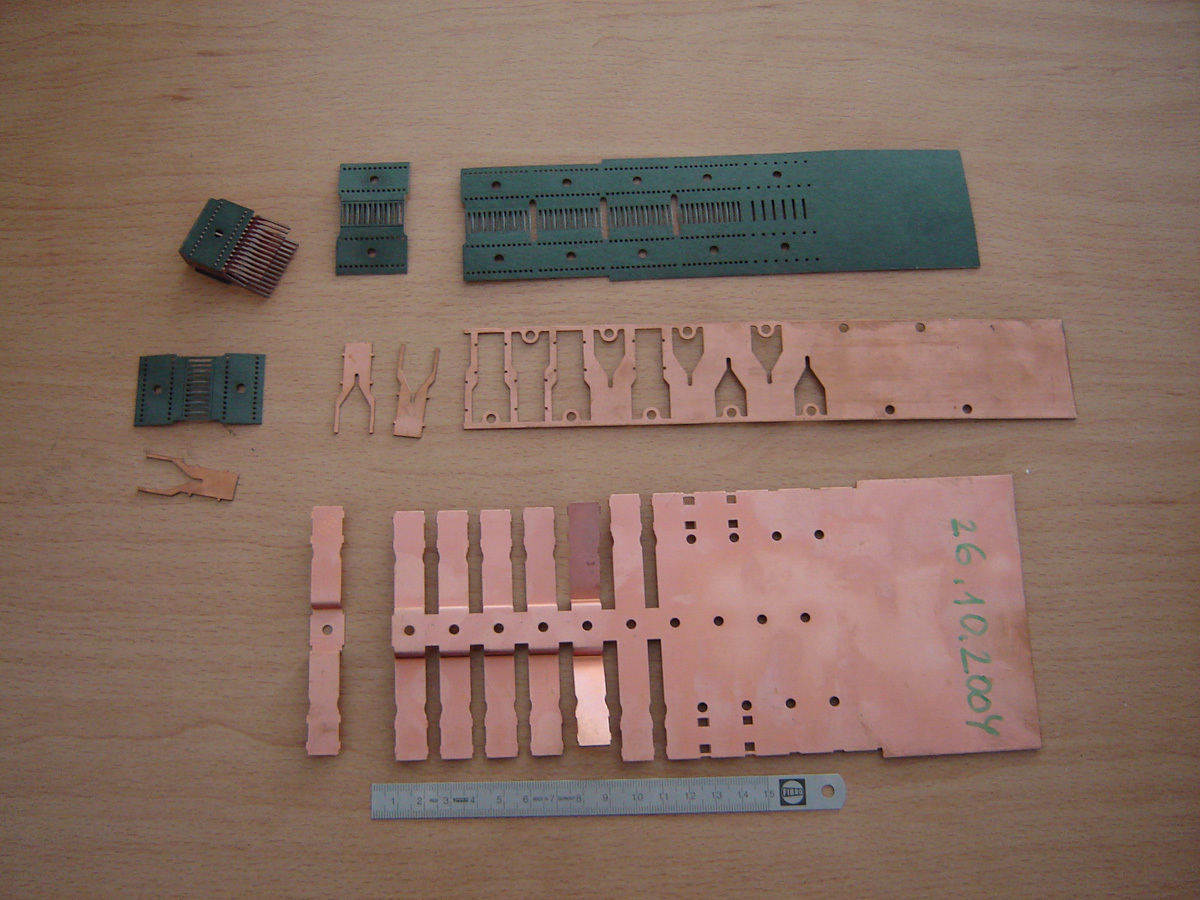
Фиг.12-6
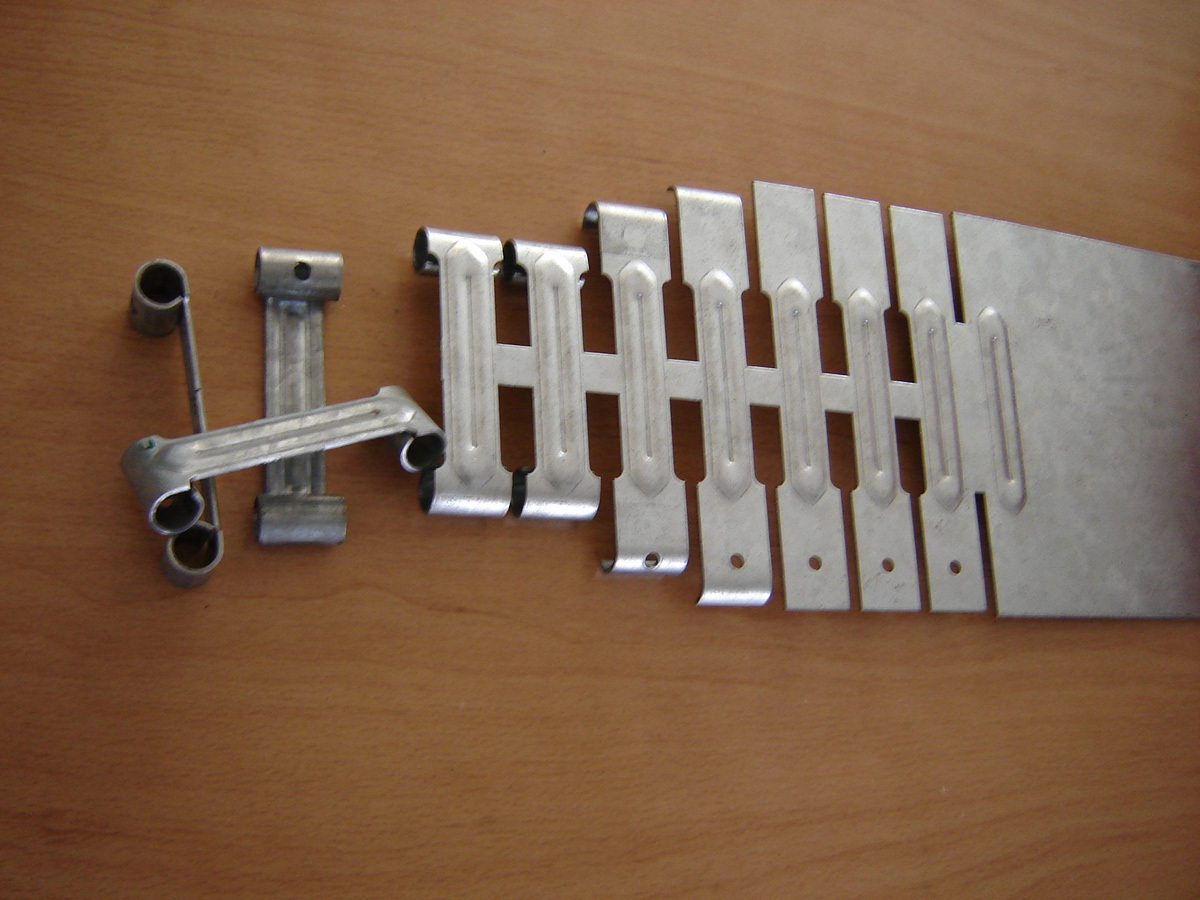
Фиг.12-7
Фиг.12-8
В тези случаи, технологична последователност при изработка на щанците се усложнява:
– Изработка на поансони;
– Изработка на матрични вложки;
– Изработка на вложки за притискач;
– Изработка на поансонодържачи (когато отворите им са с хлабина спрямо поансоните);
– Изработка на матрицодържачи по размерите на готовите матрични вложки;
– Изработка на притискачите по размерите на готовите вложки за притискач;
– Изработка на притискачи в комплект с водещи плочи (ако са с еднаква хлабина) или само на водещи плочи с увеличена хлабина;
– Пробен монтаж и проверка на режещите поансони за необходимата хлабина;
– Извеждане на центроващи отвори за щифтове или отвори за водещи колонки и втулки при сглобени матрици, притискачи, водещи и долни плочи, с поансони, проникнали в отворите на матрицата на дълбочина, предписана от работения ход.
Вложковите и секционите поансони и матрици трябва да се напасват и полират в сглобено състояние - Фиг.12-9 и Фиг.12-10
Фиг.12-9
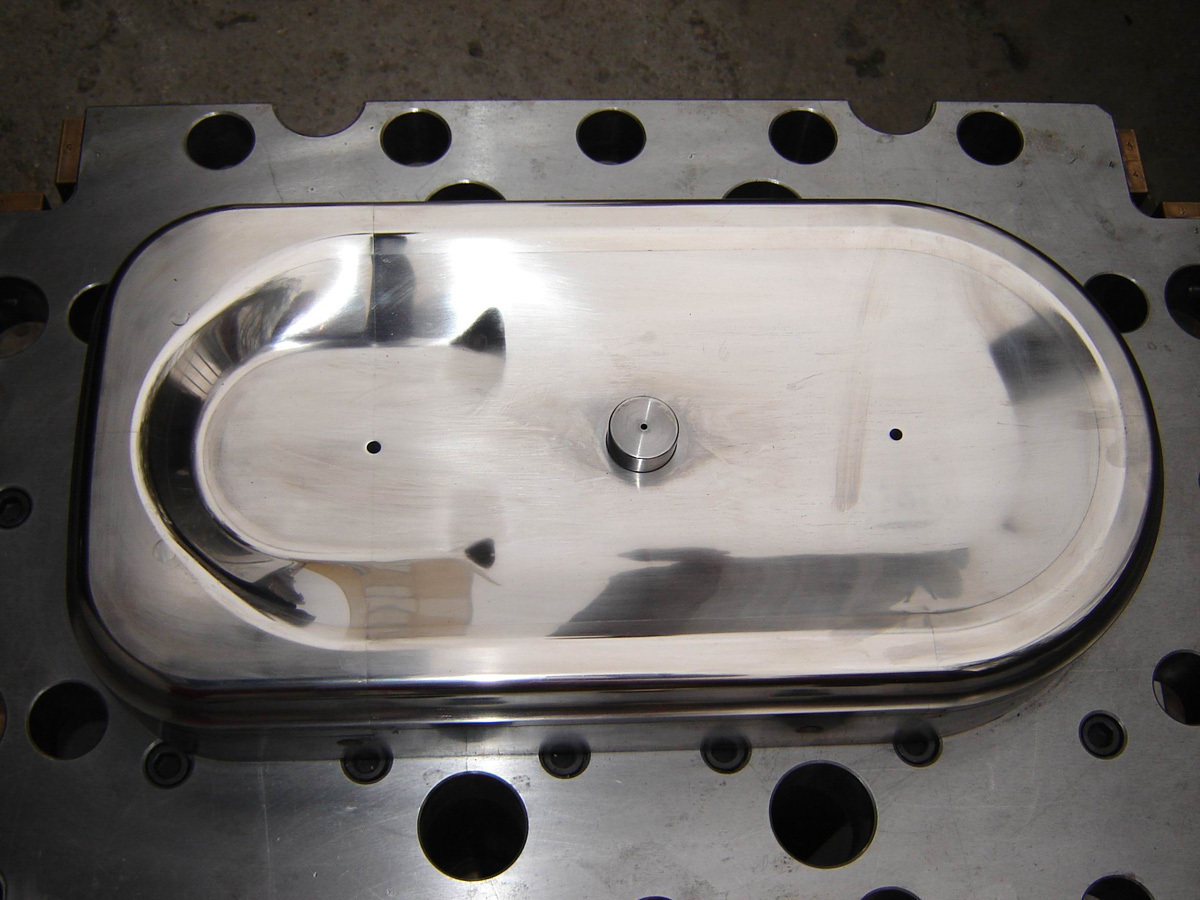
Фиг.12-10
В противен случай са възможни малки разминавания между вложките, които остават отпечатък на изработвания детайл.
Важна особеност при изработката на инструментална екипировка за щанцоване на листов материал е свързана с нелинейния характер на деформаците. Те се разпределят неравномерно и по различен начин при огъващите и изтеглящи операции. Изчисленията показват само приблизителната големина на деформациите. Точната стойност обикновено се определя опитно. По тази причина, когато има точно разположени отвори върху огънати рамена, изрязващата щанца се изработва след проба на огъващите инструменти с лазерно или нишково електроерозирана заготовка. На пример, разгъвката на детайл „ПЛАНКА“ Фиг.3-5 е изработена чрез нишково електроерозиране и е изпробвана на изработените огъващи щанци за следващи операции от Фиг.4-6. След проба е проверена съосността на отворите и е определена стойност за корегиране на разгъвката, след пружиниране от Фиг.5-27, за да се получи в зададените граници размера на процепа 6.4 mm. По уточнената разгъвка е изработена изрязващата щанца.
Монтажните операции при щанците се изпълняват с последователно монтиране от долна плоча към горна плоча. Първоначално се сглобява неподвижния пакет (долна плоча, подложна плоча, матрица или матрицодържач с вложки, лентоводачи, водещи колони или втулки) - Фиг.12-11.
Фиг.12-11
При по-големите инструменти, отворите за главите на винтовете трябва да са разположени в матрицата или матрицодържача, за да не се налага повдигане и обръщане на пакета. Изключение от това правило се прави при малки щанци с тегло на неподвижния пакет под 20 кг. Следва сглобяване на водеща плоча с монтиран притискач към водещите колони, последвано от поставяне на поансонодържача и монтиране на поансоните в него и водещата плоча. Между поансонодържача и водещата плоча се поставят дистанциони подложки, за да може той лесно да се повдигне. Накрая се поставят опорна плоча и горна плоча, която се центрова по водещите колони. Всички пружини в горна плоча са поставени предварително и ако не са предвидени конструктивно с предварителен ограничител на дължината, по малко и симетрично се притягат винтовете. Следи се да не се получи еднострано изкривяване на плочите от пружините сили. Щифтовете в горната плоча и поансонодърча се поставят накрая за да не пречат на монтажа. Препоръчително е в поансонодържача те да са с хлабина (ако поансоните не се центроват от самия поансонодържач). По някога в матрицата също има пружинни повдигачи, пречещи на лесния монтаж. Желателно е те да бъдат максимално разхлабени при сглобяването.
Монтажа на сачмени или ролкови сепаратори за триене при търкаляне има определени правила – никога не се чука по сепаратор, когато е в контакт едновремено с колонка и втулка. Така може да се наруши безхлабинната връзка и да предизвика откъртване на парченца от търкалящи тела или надиране на колонките. Вместо това, системата се разглобява и при сглобяването сепараторите се нагласят на дистанция, повече от половината ход на щанцата, преди контакта им с втулките или колонките. Работното положение на сепараторите се постига чрез възвратно постъпателно движение на подвижния спрямо неподвижния пакет, имитиращо работата на щанцата на пресата. След 2-3 повдигания и спускания, сепараторите заемат необходимото за правилна експлоатация разположение спрямо втулките. Обикновенно, в сепараторите има зегерки, които не позволяват пропадането им във втулките и облекчават монтажа – между зегерките и втулката се поставя дистанионнен елемент, който впоследствие се изважда преди затваряне на щанцата до край. Това е много удобно при инструменти с повече от 4 колонки.
Контролът на хлабината при щанци за разделителни операции се прави в зависимост нейната големина. При щанци с хлабина под 0,02 mm може да се използва PVC фолио или найлон за опаковане. Неговата дебелина обикновено е същия порядък – рядко е повече от 0,03 mm. Иделно заточените ръбове с равномерно разпределена хлабина ще откъснат участък с формата на контура на поансона. По-голяма хлабина или лошо заточване ще предизвика само разтегляне, без скъсване в съответния участък. Много шлосери инструменталчици прилагат друг практически метод – те използват тънък лист хартия за същата цел. Трябва обаче, много да се внимава хартията да е суха и да не се омасли, защото тогава се изкривяват резултатите (влажна и омаслена хартия се разтегля, а не се къса и създава илюзия за голяма хлабина). Този метод обаче, също е приложим за малка хлабина (до 0,03 mm).
Често след проба се наблюдават малки деформации, белези или други проблеми по лентата или детайла. Тяхното откриване става най-лесно чрез наслагване на получената лента върху неподвижния пакет - Фиг.12-12
Фиг.12-12
или върху подвижния пакет, в зависимост от проблемната страна на лентата. Дори, когато белезите или деформацията е на готовия детайл, връщайки се назад по работни позиции и разглеждайки внимателно кога за първи път възниква проблема в лентата, бързо се открива причината. Затова изваждането, маркирането и запазването на лентата от първа проба е много важна част от организацията на работата в инструментална за изработка на щанци.
4. Анализ на натрупания опит от изработката на щанцови инструменти.
Натрупания опит и наблюдения върху производството на инструментална екипировка за обработка на листов материал, позволява да се извърши анализ и да се отделят основните параметри за неговата оценка. Липсата на точни изчислителни методи, правила и време, са наложили в практиката определянето на времената и сроковете по преценка на технолога, организатора на производството или ръководителя по усет или в най-добрия случай, по аналогия с вече произведени щанци. Беше посочено, че дори за еднакви инструменти, условията за дублиране никога не са едни и същи (различни прибавки, режещи инструменти и така на татък). Необходимостта от събиране на подобни дани се засилва от факта, че производствените условия в две инструментални не са еднакви, следователно сроковете за изработка и цените за една и съща щанца ще се различават. Проблемът при оценката на сроковете за изработка и цената е, че обективни стойности могат да се посочат след завършване на процесите на конструиране и подготовка на маршрутен технологичен процес на щанцата. Практически, такова време никога не се отпуска, а резултата се очаква до няколко дни след поставяне на задачата. При сложни последователни щанци, този срок не достаъчен за пълното изпълнение на идеен проект. Следва залагане на субективно определен срок, който подобно на бумеранг се връща обратно като уговорен с клиента, под форма на график за изработка, пък бил той и нереален или невъзможен. Това налага да се разгледат данните за различни видове щанци (особено за много позиционни щанци с последователно действие, където почти никога няма еднакво съчетание на операции).
4.1. Реално разпределение на времето за изработка на щанците по операции.
За да се отделят важните данни, са разгледани практическите времена за изработка на щанци с различна конструкция и размери, предназначени за производство на различни детайли - Фиг.12-13.
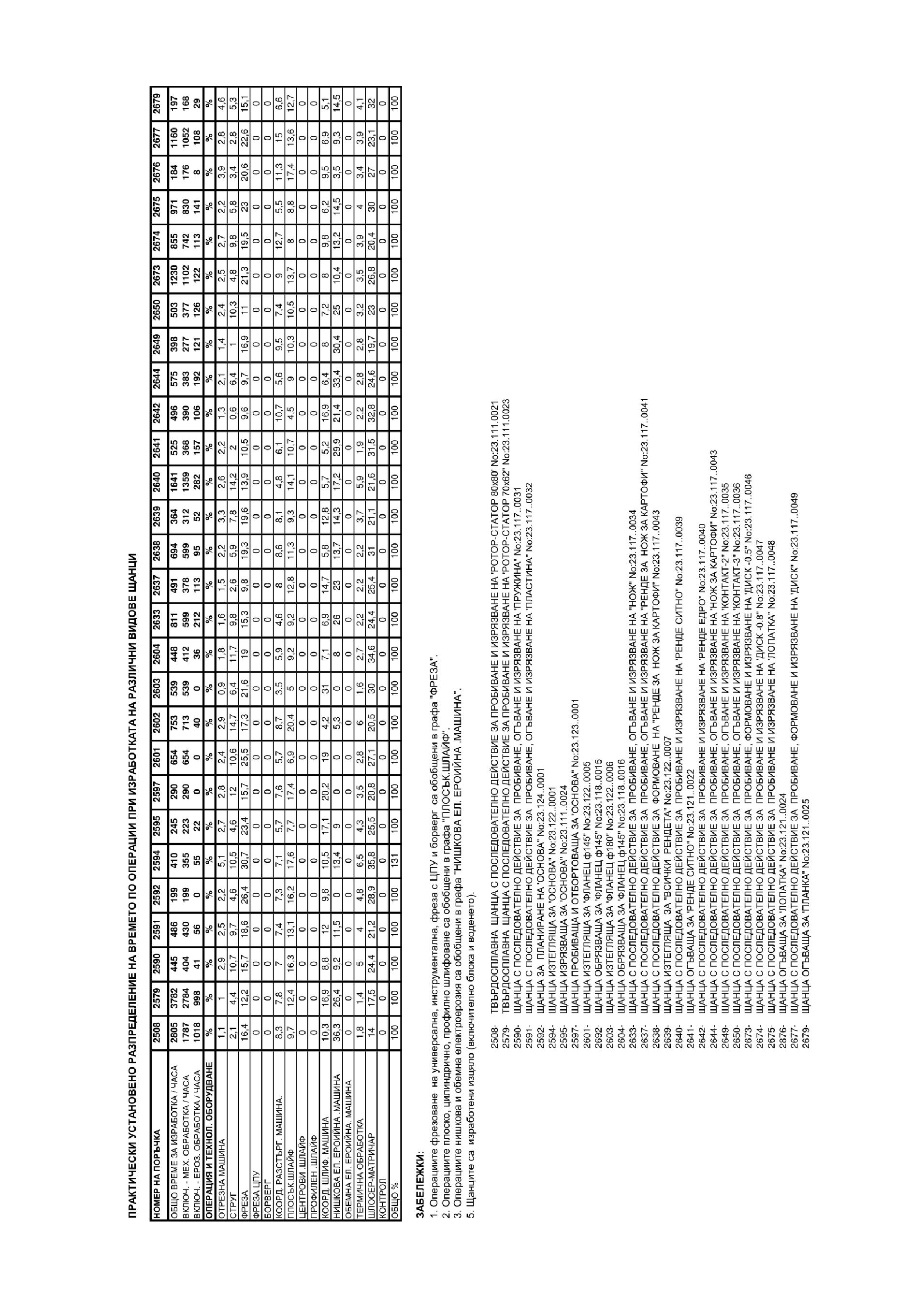
Фиг.12-13
Времената за изпълнение на отделните операции са представени като процент от общото време на изработка. Оказва се, че електроерозийната обработка при всички инструменти е тясно място, поради малкия брой машини и липса на алтернативен метод. Затова общото време е разделено на механична обработка и електроерозия.
4.2. Сравнение на прогнозирани и реални разходи за материали и труд за щанци.
Важен момент за обективността на анализа, е сравнението на заложените по технология времена с реално отчетените. Освен времето за изработка, влияещо върху цената за труда и срока за изпълнение, цената на вложените материали също влияе върху крайната цена на инструмента. Сравнение на разходите за материали и трудоемкостта по технологии (прогноза) и реално отчетените при изработка е показано на Фиг.12-14.
Оценка на отклоненията на прогнозите спрямо действителните е направена чрез изчисление на процентната относителна грешка на прогнозната спрямо реалната стойност. Като цяло, таблицата показва, че разходите за материали се завишават с 12%, а вложения труд с 1.6%. Разглеждайки подробно таблицата ред по ред се вижда, че отклонения от 50% до 300% са фактически възможни както в „подценяване“, така и в „надценяване“. И за двете има практическо обяснение. В случай на надценяване, технологичното време и разходите за материали са по-големи от действителните. Тогава стойността на отклонението е отрицателна. За материалите обяснението е просто – намерени са по-евтини материали или са изолзвани остатъчни количества, вече изписани за други инструменти. При времето за изработка съществуват две вероятности:
– неправилна преценка на технолога, което е напълно възможно в рамките на 20-30%;
– неотчетено изцяло реално време, което е най-често срещаната причина.
При обратния случай на подценяване, стойностите на отклонението са положителни. Тук за материала е възможно да е доставен по-скъп, но е възможно също така, да е доставено по-голямо количество за покриване загуби от брак при изработката. Времето за изработка може да е по-голямо по две причини:
– неправилна преценка на технолога, което е възможно в рамките на 30%;
– оставени по-големи прибавки, възникнала необходимост от повторна изработка на отделни части поради грешки в изпълнението или корекции в инструмента, изискващи допълнителен труд, който не може да се предвиди при подготовката на технологичните карти.
4.3. Сравнение на прогнозирани и реални разходи за материали и труд по видове щанци.
Анализът на разгледаните по-горе данни, са позволили щанците да бъдат разделени по вид в следните групи:
– Щанци с последователно действие с твърдосплавни режещи части - Фиг.12-15.
Тук са обединени най-сложните инструменти с вложкова конструкция, сепараторно водене на втулки и колонки, трудно обработваеми активни части и високи изисквания за надеждност.
– Щанци с последователно действие - Фиг.12-16.
В тази група са включени сложни последователни инструменти за разделителни и формоизменящи операции, с вложкова конструкция за формоизменящите позиции, най-често със сепараторно водене на втулки и колонки, с активни части от високолегирана инструментална стомана и високи изисквания за надеждност.
– Щанци със съвместно действие - Фиг.12-17.
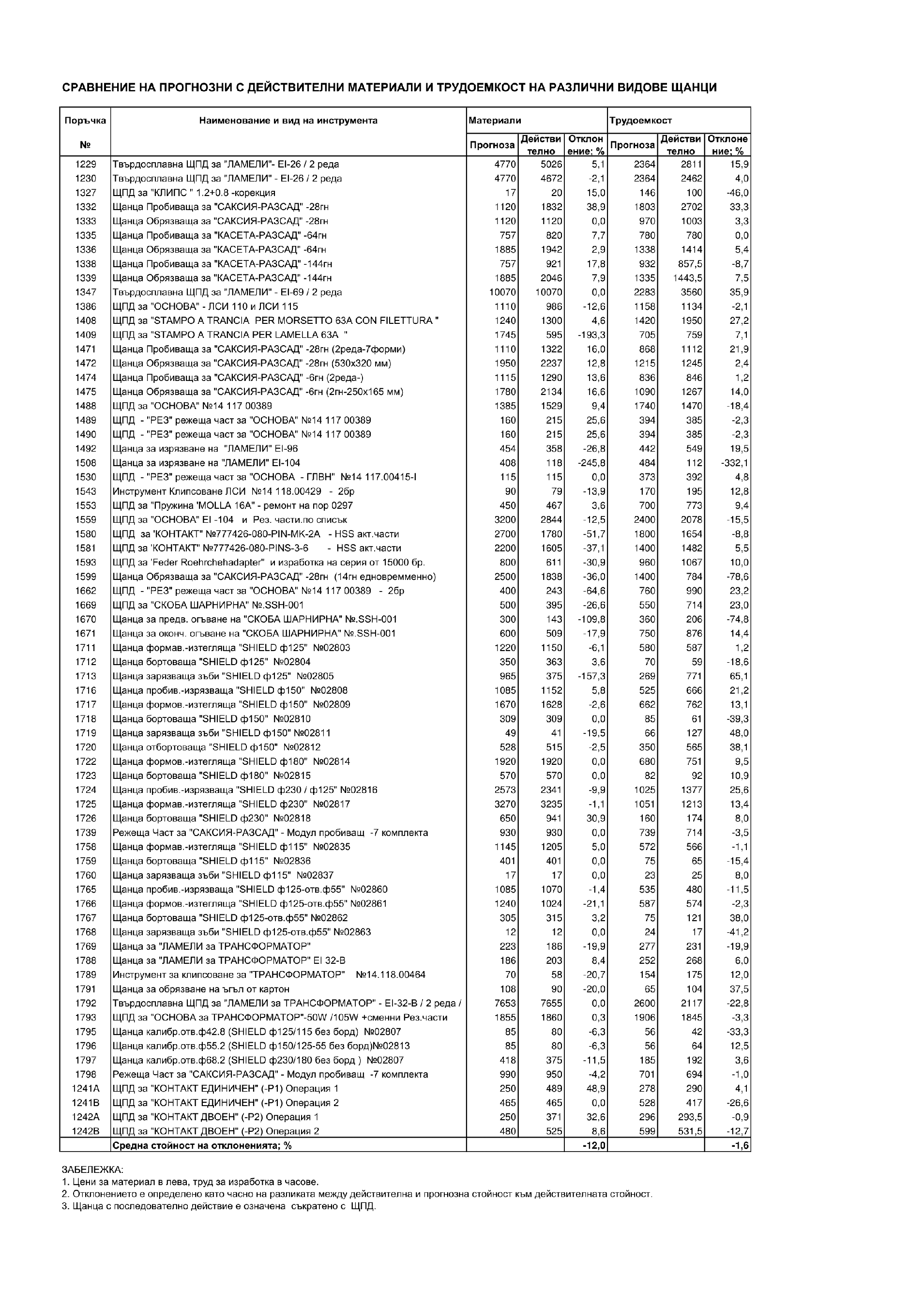
Фиг.12-14
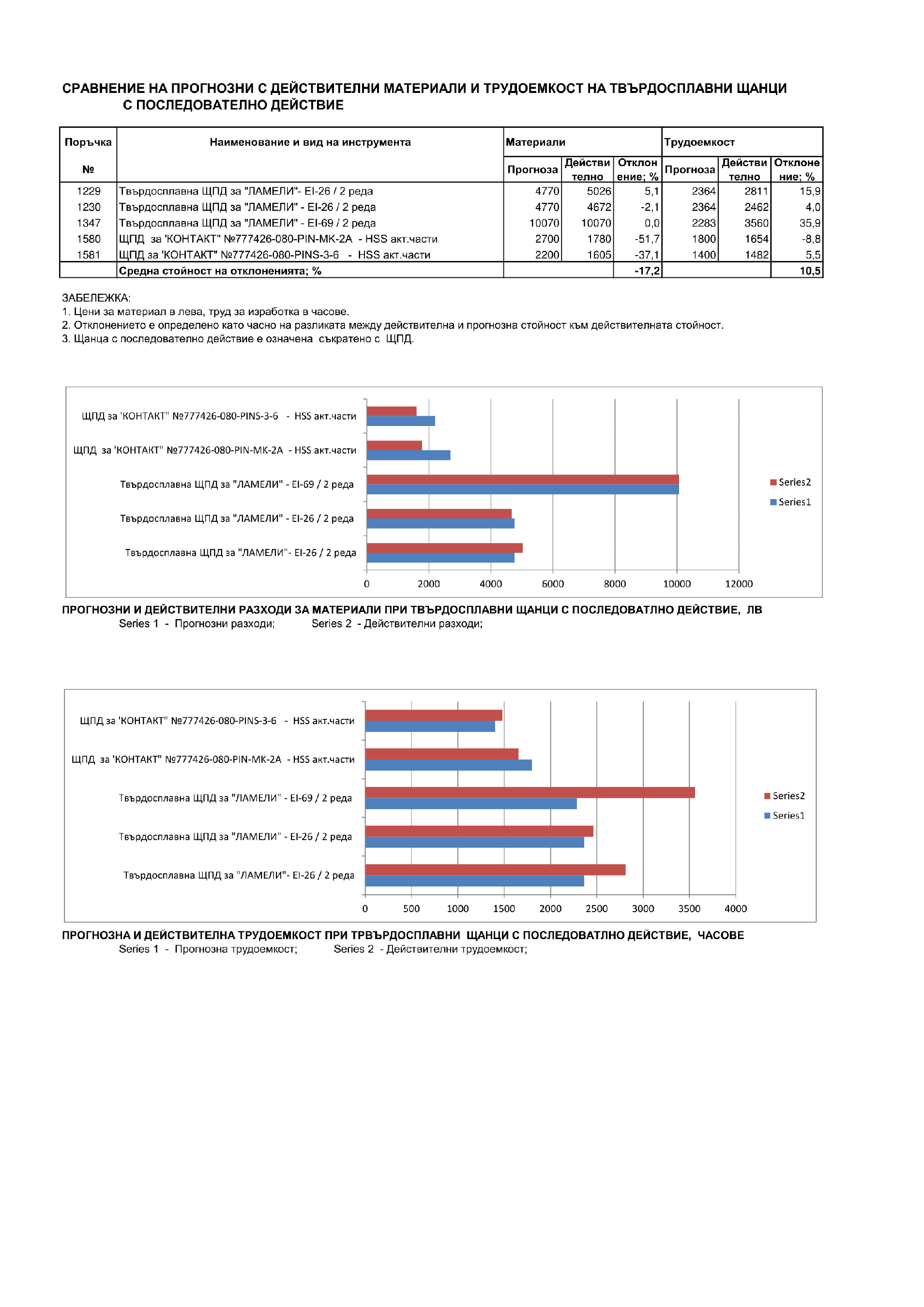
Фиг.12-15
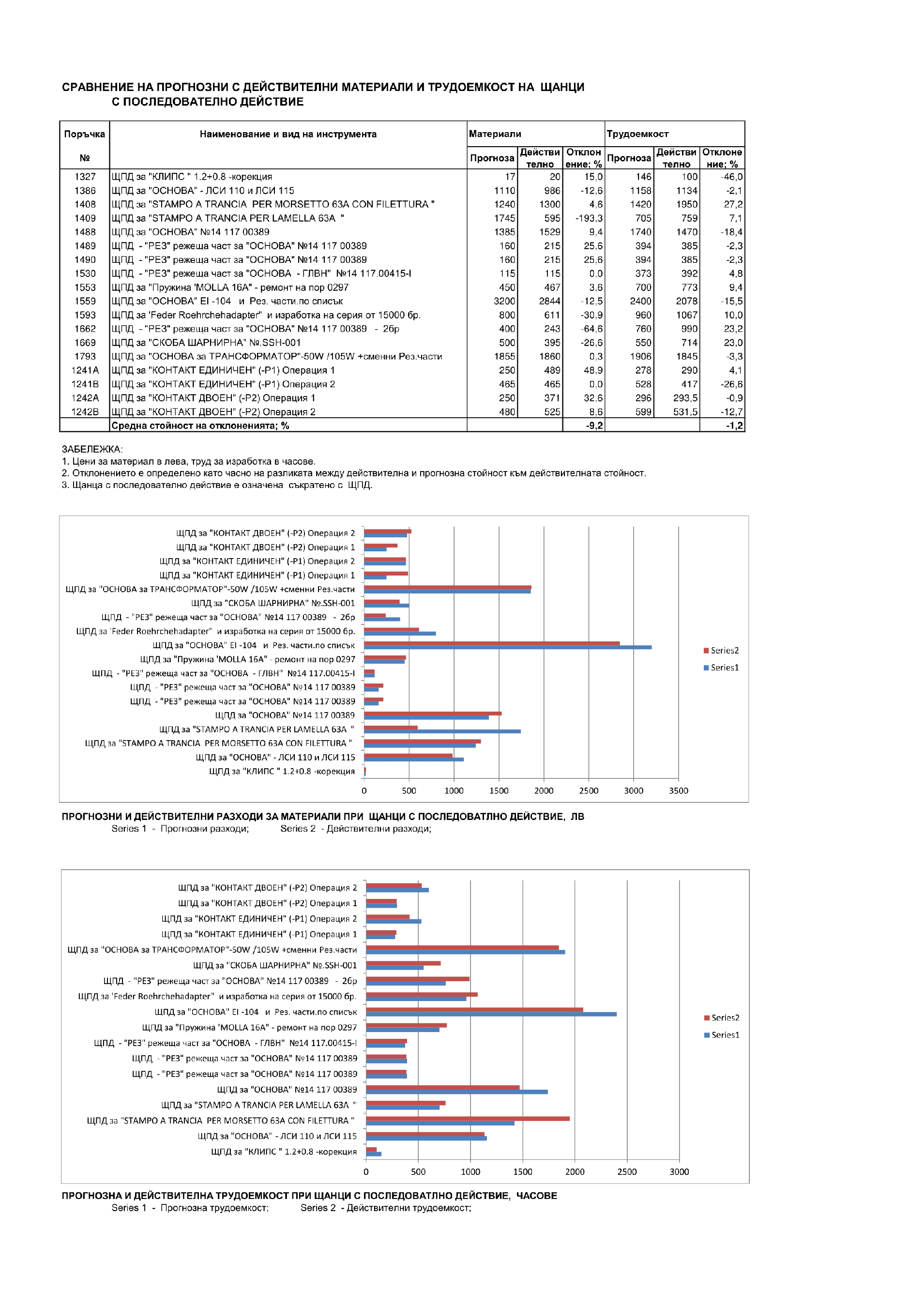
Фиг.12-16
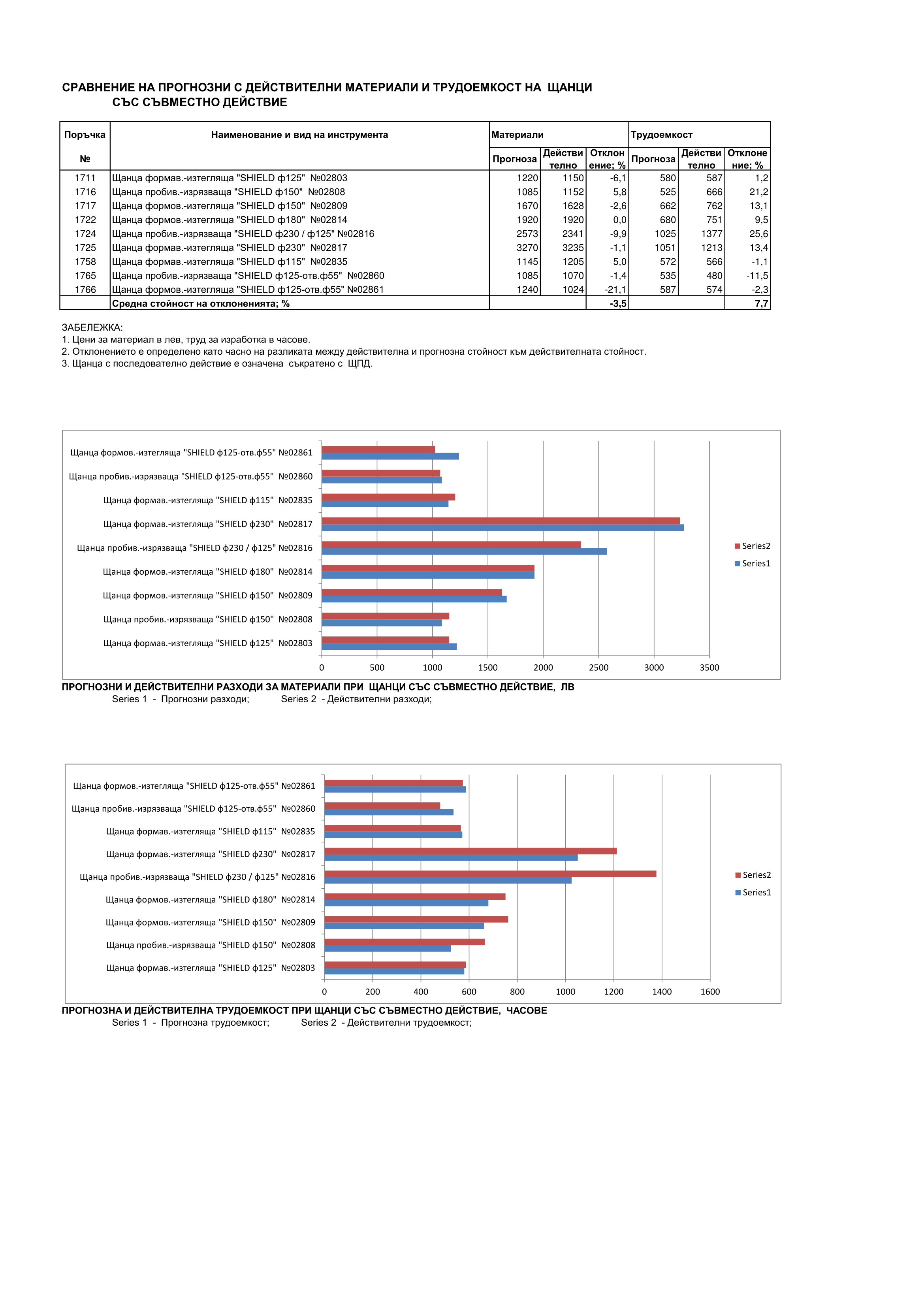
Фиг.12-17
В тази група са включени инструменти за две и повече разделителни и / или формоизменящи операции, извършени в рамките на работния ход на щанцата, често с вложкова конструкция, рядко със сепараторно водене на втулки и колонки, с активни части от високолегирана инструментална стомана и високи изисквания за надеждност.
– Едно операционни щанци за еднотипни операции - Фиг.12-18.
В тази група са обединени едно операционни инструменти за разделителни или формоизменящи операции (изрязване, огъване, изтегляне), често с вложкова конструкция, обикновенно с водене на втулки и колонки с триене при плъзгане, с активни части от високолегирана инструментална стомана.
– Щанци за производство на неметални детайли - Фиг.12-19.
В групата са включени инструменти за разделителни операции (пробиване, изрязване, отсичане) на неметални детайли (различни пластмаси, картон, текстолит), често с вложкова конструкция, обикновено със сепараторно водене на втулки и колонки, с активни части от високолегирана инструментална стомана и високи изисквания за надеждност.
От всички разгледани групи, най-големи отклонения се наблюдават при най-простите едно операционни щанци. Тук обяснението е с начина на оценка на инструментите – запазен е подхода на оценка за сложните последователни или съвместни щанци, което е довело да надценяване материалните разходи с 23% и времето за труд с 12,6%.
5. Прогнози и оценки за изработката на щанцови инструменти.
Разгледаните данни позволяват да се определят основните параметри, определящи производствения процес – вида и големината на щанцата, площта или обема на нейните активни части. По долу ще бъдат разгледани модели за прогнозиране трудоемкоста и цената на щанците, ориентировъчното разпределение на времето по операции, най-краткия календарен срок за изработка (без да се отчита влиянието на фактическото натоварване на инструменталното оборудване). Технологичната схема и тези модели са достатъчни за обосновано определяне на разгледаните величини в етапа на идеен проект на инструмента.
5.1.Процентно разпределение на времето по операции за различни видове щанци.
От всички разгледани групи, това разпределение, позволяващо точно определяне на цените, е изпълнено за най-сложните инструменти. На Фиг.12-20-A и Фиг.12-20-B е показано процентното разпределение за твърдосплавна щанца с поледователно действие, а на Фиг.12-21-A и Фиг.12-21-B
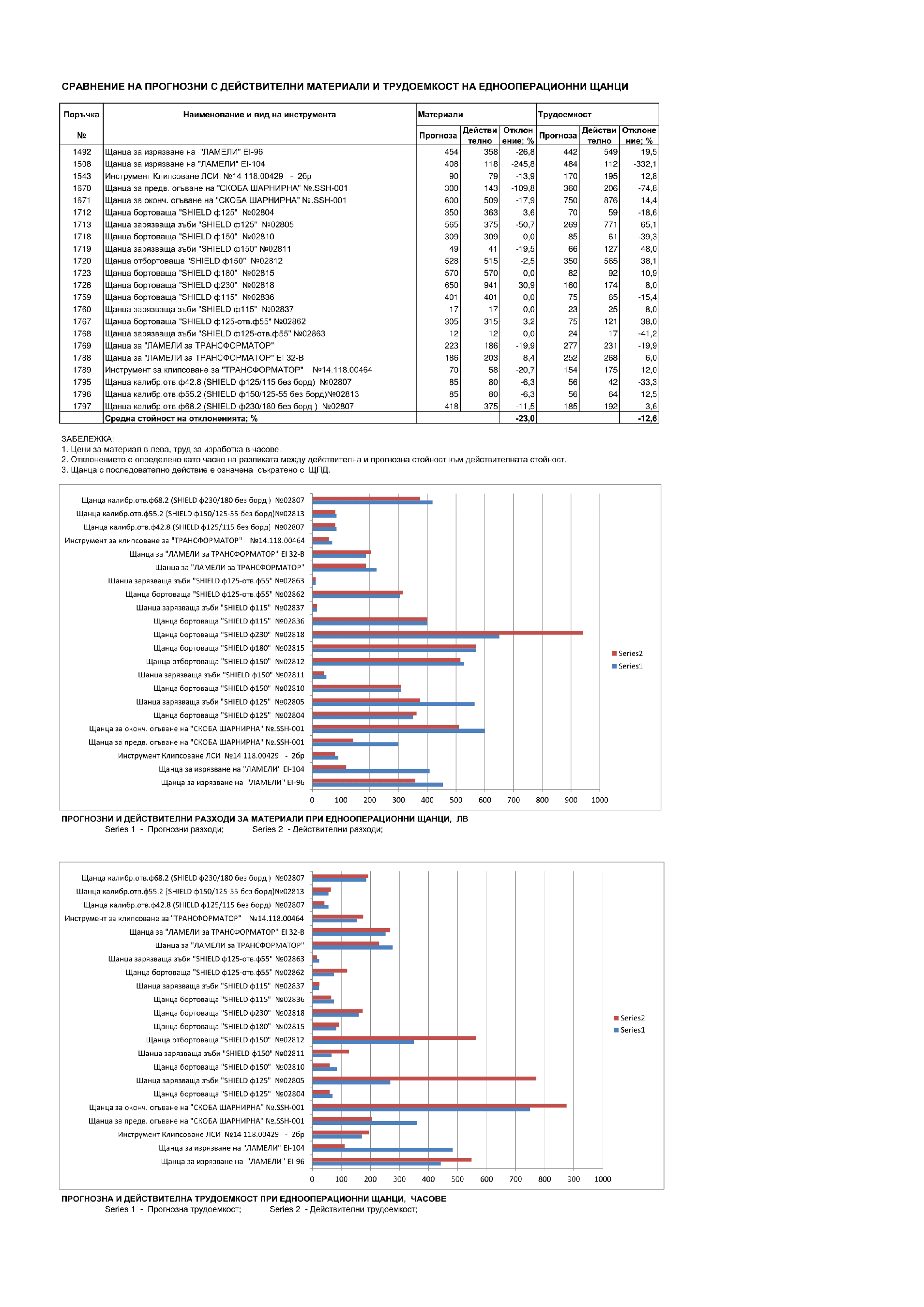
Фиг.12-18
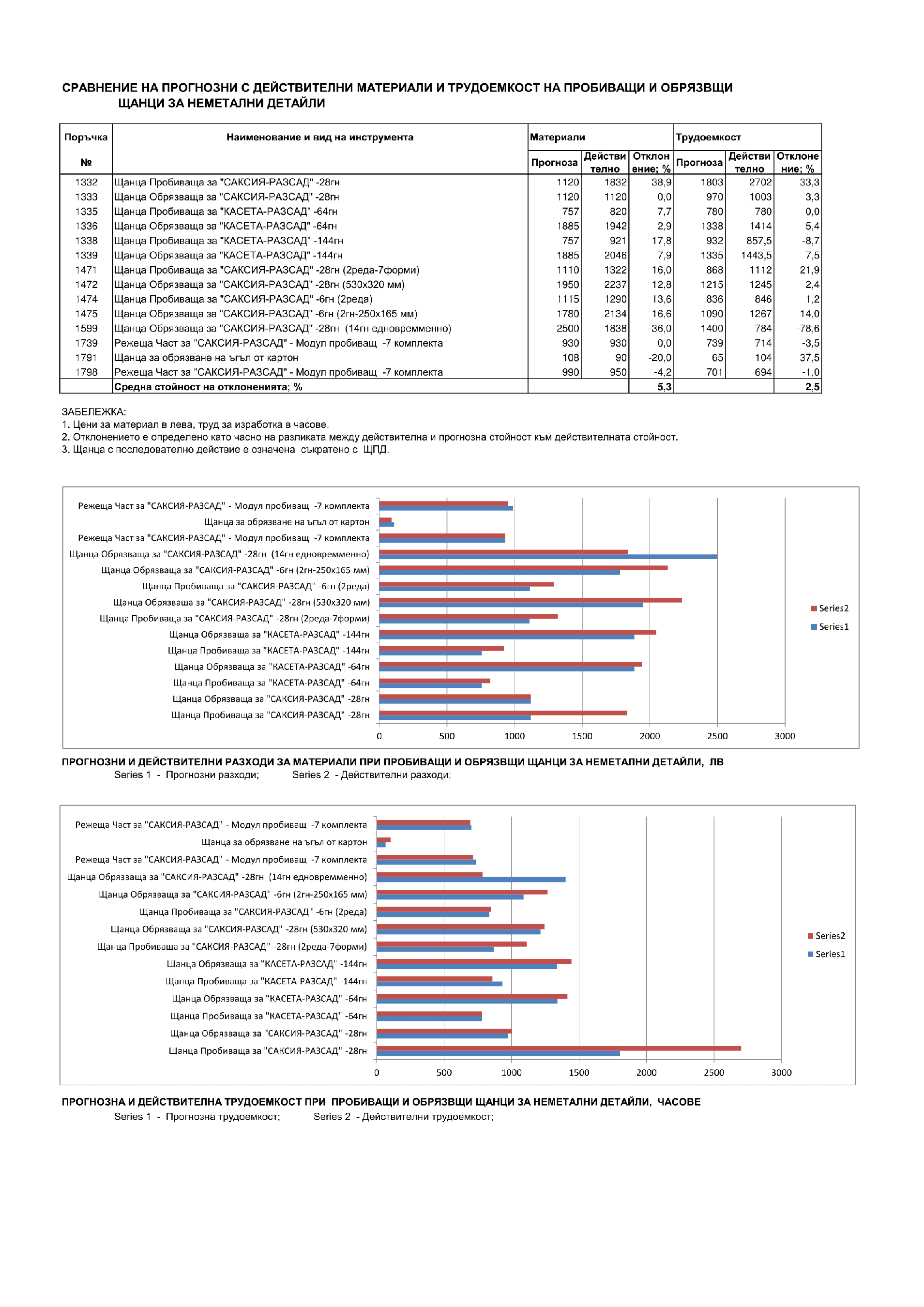
Фиг.12-19
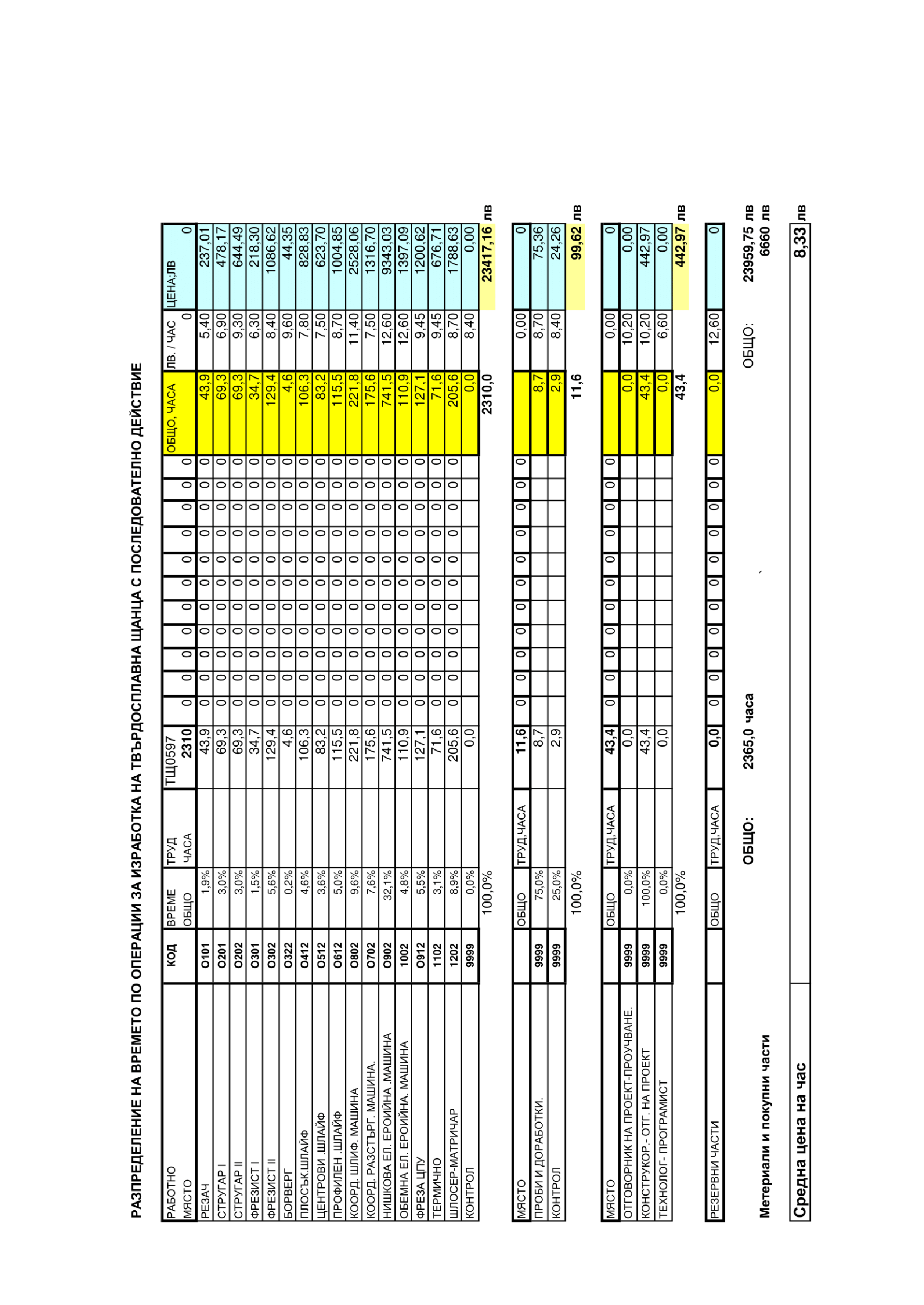
Фиг.12-20-A
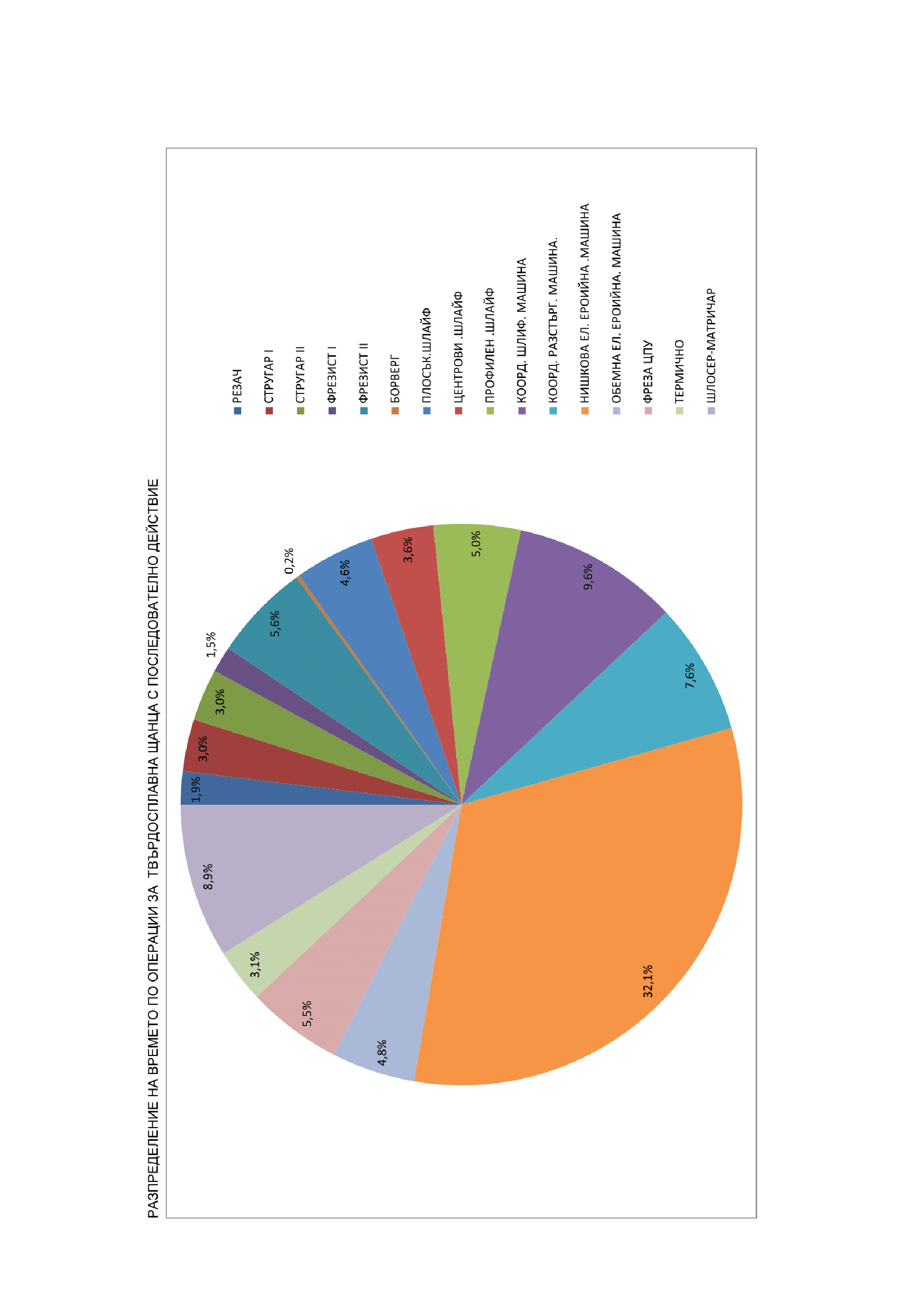
Фиг.12-20-B
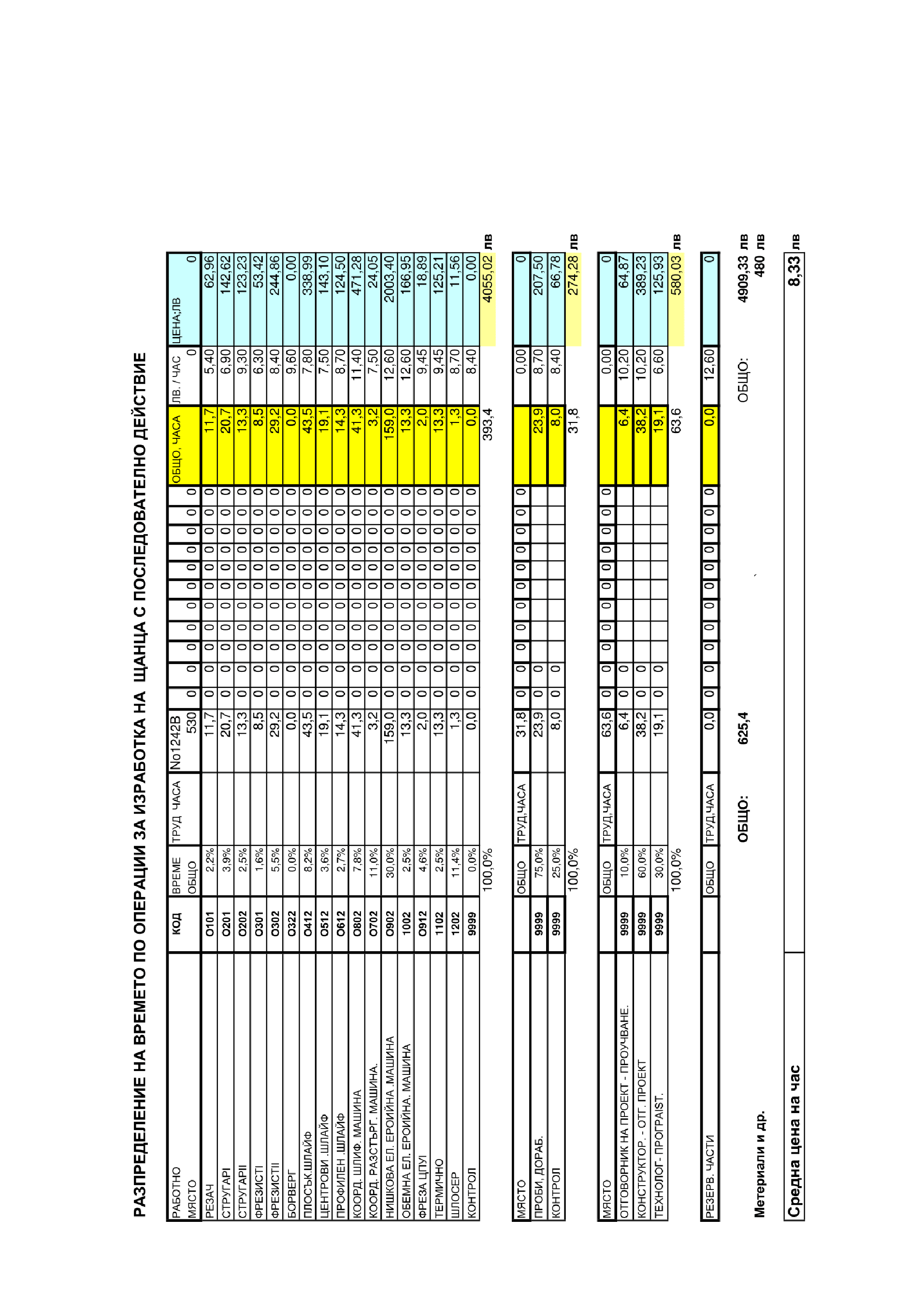
Фиг.12-21-A
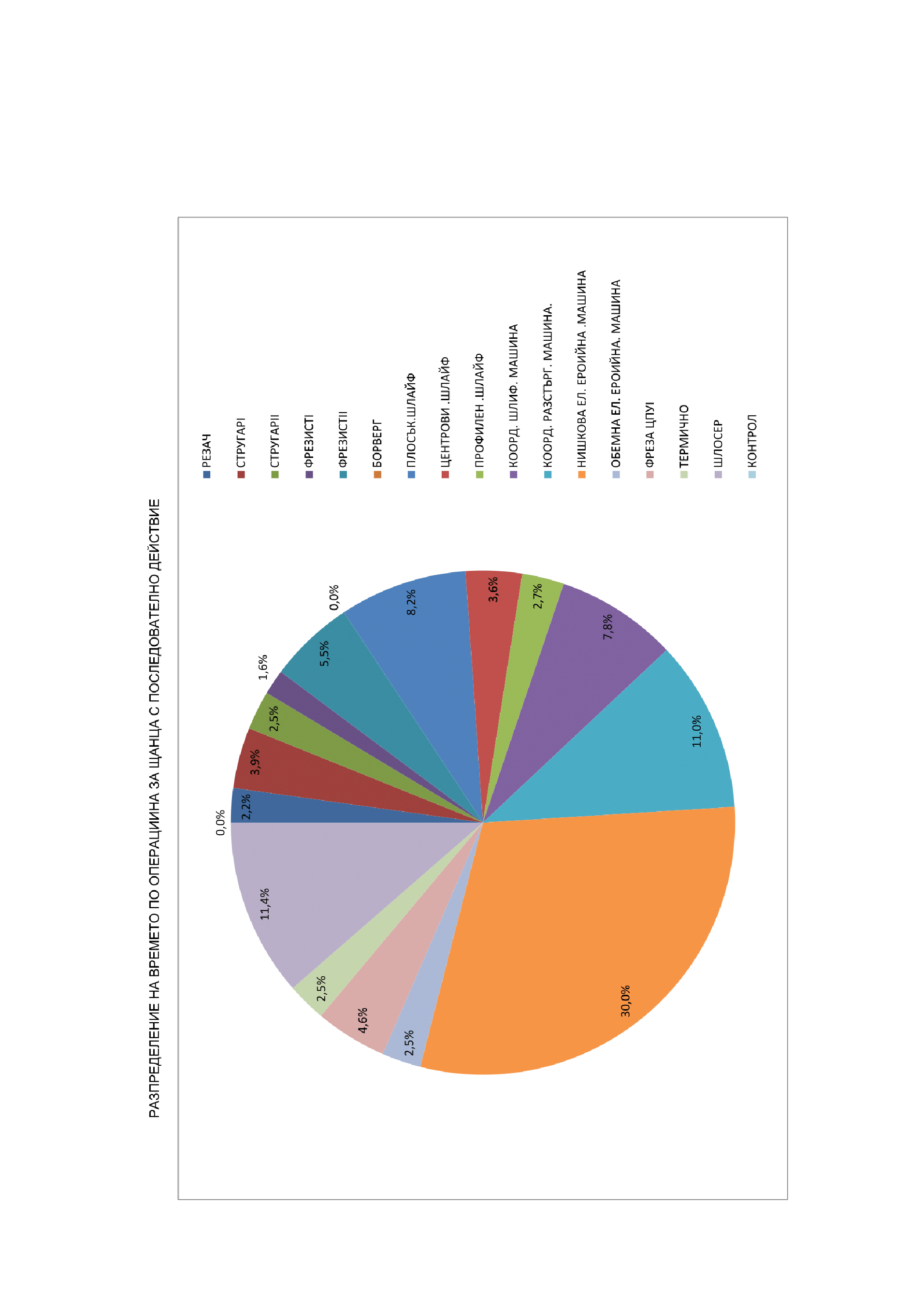
Фиг.12-21-B
на щанца с последователно действие с активни части от закалена високолегирана инструментална стомана. Анализът показва, че за дадения вид щанца с последователно действие, процентното разпределение се колебае в тесни граници, независимо от вида на технологичните операции, броя преходи и тяхната последователност.
5.2.Сравнение и модел на средната трудоемкост и цената за различни видове щанци.
За целите на моделирането са обособени няколко различни групи на щанци, различаващи се по вид на конструкцията, габаритни размери и ерозирана повърхност, зависеща от активните части. Щанците с последователно действие с твърдосплавни активни части са разделени на 3 подгрупи, според габаритните размери и конструкцията. Типични представители на първата подгрупа са инструменти за роторни и статорни листове за електродвигатели, на втората подгрупа са инструменти за ламели от магнитопроводи, а на третата подгрупа инструменти за различни контакти или дребни детайли от масовото производство. Щанците с последователно действие със закалени активни части от инструментална легирана стомата са разделени на 2 подгрупи, според габаритните размери. При тяхната конструкция, обикновено вложки се използват за формоизменящите позиции, за разделителните позиции това е изключение. Едно операционните щанци са разделени на две подгрупи – огъващи, изряваващи (или пробиващи). Резултатите, правилата за прилагане на модела и ограниченията са показани на Фиг.12-22-A и Фиг.12-22-B.
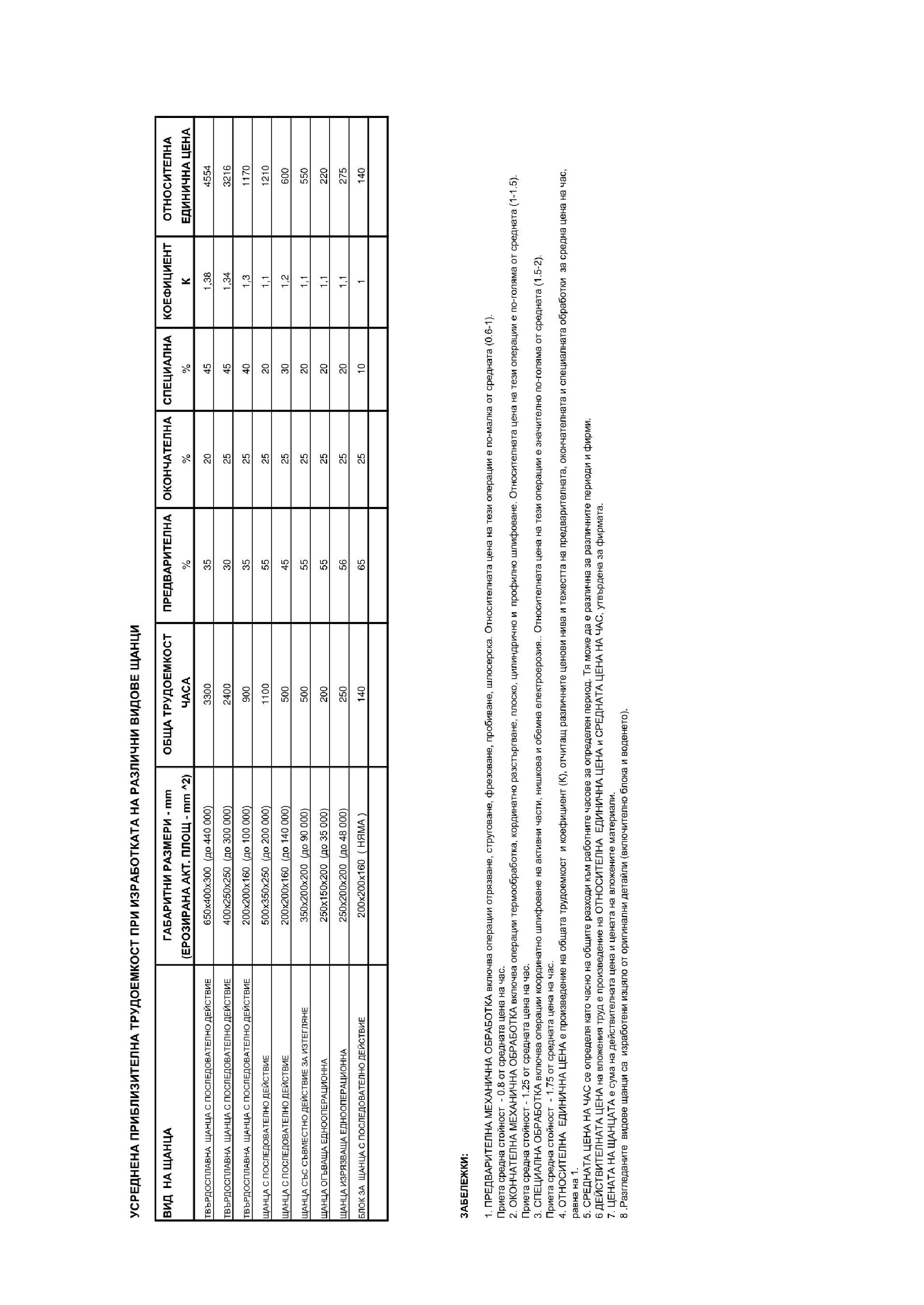
Фиг.12-22-A
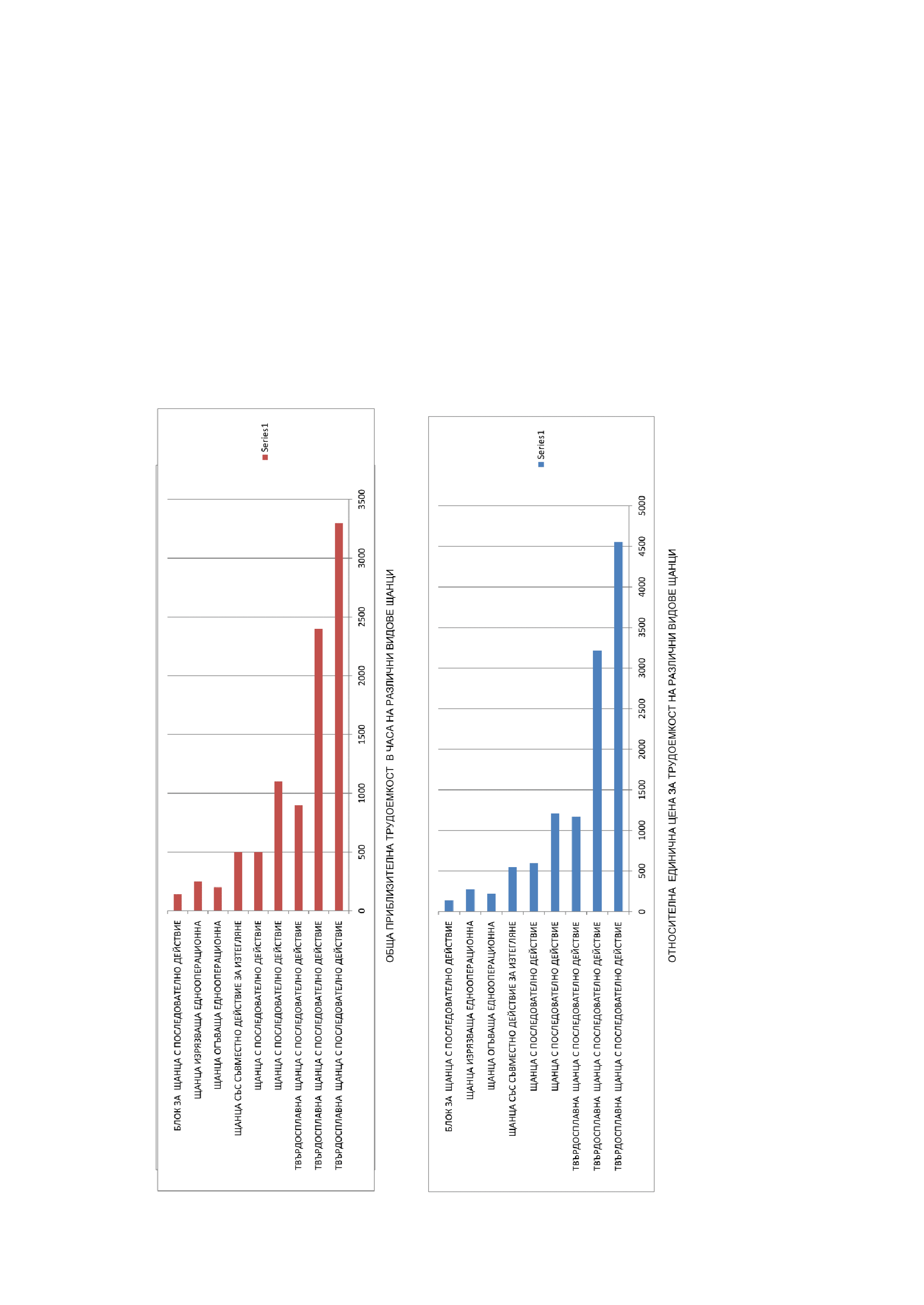
Фиг.12-22-B
За удобство и сравнение, е направен и модел на блок за щанца с последователно действие. Така лесно може да се оцени влиянието на не свързаните с формата и размерите на детайла части от конструкцията, върху общата цена на щанцата при еднакви габаритни размери.
5.3.Пример за приложение на модела на трудоемкостта и цената.
От всички разгледани групи, тук в качеството на пример ще се формират трудоемкост и относителна единична цена за твърдосплавна щанца с последователно действие за „Лист Роторен – Лист статорен“ с чертежи, показани на Фиг.6-74 (поглед отгоре), на Фиг.6-75 (надлъжен разрез А-А), на Фиг.6-76 (напречен разрез В-В), на Фиг.6-77 (напречен разрез С-С), и за щанца с последователно действие с вложки от HSS (1.3343) за „Пластина контактна” с чертежи от Фиг.11-6 (неподвижен пакет), от Фиг.11-7 (напречен разрез А-А), от Фиг.11-8 (напречен разрез В-В), от Фиг.11-9 (подвижен пакет).
Твърдосплавна щанца с последователно действие за „Лист Роторен – Лист статорен“ се класифицира в подгрупа „ТВЪРДОСПЛАВНА ЩАНЦА С ПОСЛЕДОВАТЕЛНО ДЕЙСТВИЕ“ с габаритни размери (дължина, ширина, височина) 600х400х300 mm и активна ерозирана повърхност до 440 000 квадратни милиметра. Приблизителната обща трудоемкост за модела е 3300 часа, която включва 1155 часа предварителна механична обработка, 660 часа окончателна механична обработка и 1485 часа специална обработка (стойности са изчислени като посочен процент от общата трудоемкост). Габаритните размери оказват непосредствено влияние върху предварителната и окончателна обработки. Времето за тези обработки е право пропорционално на големината – по-големите инструменти изискват повече труд за механична обработка и обратно. За разглежданата щанца, габаритните размери (дължина, ширина, височина) са 640х480х326,7 mm. Лесно може да се определи средната стойност на мащабен коефициент за отношенията на всички габаритни размери към модела, който в случая е около 1,29. Линейната връзка с модела означава, че времената за предварителната и окончателна обработки ще бъдат 1,29 пъти по-големи или 1490 часа предварителна механична обработка, 851 часа окончателна механична обработка. Меджу габаритните размери и сложността на детайла няма пряка връзка. Такава обаче, съществува между ерозираната активна площ на модела и тази на разглежданата щанца. Колкото по сложен е детайла, толкова повече работни позиции със съответните контури за обработка ще има, за които ще е необходимо повече време. Ако разполагаме с чертежи, общата ерозирана площ лесно може да се изчисли. На практика обаче, трудоемкостта и относитената единична цена са необходими на етап идеен проект. При него разполагаме само с технологична схема от Фиг.5-10. По нея се изчисляват дължините на контурите за всички поансони и вложки и общата дължина се умножава по сумарната височина на поансони, поансонодържач, водеща плоча, матрица, опорна плоча и долна плоча, а за вложките общата дължина се умножава по височината на матрицата. Приблизителен резултат може да се получи при умножаване на общата дължина на контурите с 80% от височинаа на блока. За разглеждания случай, ерозираната активна площ е около 661000 квадратни милиметра, или около 1,5 пъти по-голяма от модела. Това означава около 2228 часа специална обработка. Следователно, общата трудоемкост за разглеждаата щанца е 4569 часа, а относителната единична цена е 6325,22. Физическото обяснение се вижда с просто око от Фиг.6-68, където са показани детайли и ленти за модела и разглежданата щанца. Ясно е, че щанцата трябва да е по-скъпа, но отговор с колко, може да се даде едва след изпълнения на горните изчисления.
Щанцата с последователно действие с вложки от HSS (1.3343) за „Пластина контактна” се класифицира в подгрупа „ТВЪРДОСПЛАВНА ЩАНЦА С ПОСЛЕДОВАТЕЛНО ДЕЙСТВИЕ“ с габаритни размери (дължина, ширина, височина) 200х200х160 mm и активна ерозирана повърхност до 100 000 квадратни милиметра. Приблизителната обща трудоемкост за модела е 900 часа, която включва 270 часа предварителна механична обработка, 225 часа окончателна механична обработка и 405 часа специална обработка. Габаритните размери на разглежданата щанца са средно с 28% по-големи. Линейната връзка с модела означава, че времената за предварителната и окончателна обработки ще бъдат 1,28 пъти по-големи или 346 часа предварителна механична обработка, 284 часа окончателна механична обработка. Изчислената активната електроерозийна площ с вложките е 159 000 квадратни милиметра, или 1.59 пъти по-голяма от модела, следователно специалната обработка е 644 часа. В случая общата трудоемкост за разглежданата щанца е 1274 часа, а относителната единична цена е 1656,2.
Общите продажни цени за двете щанци ще се получат като произведение на относителните единични цени и средната цена за час и добавяне на прогнозните разходи за материали. Ако се попълнят изчислените общи трудоемкости в модела от Фиг.12-23 ще се прогнозира минималният календарен срок за тяхната изработка. Като следваща стъпка, след попълване на общото време в Фиг.12-20, може да се прогнозира разпределението на времето по видове операции и на тази база да се направи анализ за натоварването и наличието на тесни места в изработката, изискващи своевремено намиране и договаряне с подизпълнител. Ако цените за отделните операции са актуални, то в най-дясната колона ще се изчислят разходите за всяка от тях.
5.4.Прогнозиране на срока за изработка.
Прогнозния срок за изработка е определен на база на линеен календарен график със зависимост „начало – край“ със застъпване (препокриване) между началото на следващата операция и края на предходната. Това означава, че следващата операция може да започне върху част от партидата, за която е завършена предходната операция. Цялата партида обаче, не е завършена и застъпането е възможно само при повече от 3 заготовки в нея. В разгледаният случай, времената за изпълнение на операциите са разделени според взаимната им зависимост на ротационни, призматични и общи за всички. Така са формирани два независими пътя за протичане на изработката (ротационни и призматични детайли), по-дългия от които е критичен за определяне на срока за изработка. Към него се добавят общите времена и се получава необходимия срок за изработка в работни дни, който се трансформира в календарен при 5 дневна работна седмица.
Моделът за определяне на прогнозния календарен срок за изработка на двуредна твърдосплавна щанца за пробиване и изрязване на „Ламела EI-26“ поръчка ТЩ0597 е показан на Фиг.12-23.
На практика, коефициентите на застъпване рядко приемат стойности 0 или по-високи от 0,4.
Модел за определяне на прогнозния календарен срок за изработка на щанца с последователно действие за пробиване, огъване, изрязване за „Контакт двоен“ поръчка 1242В е показан на Фиг.12-24.
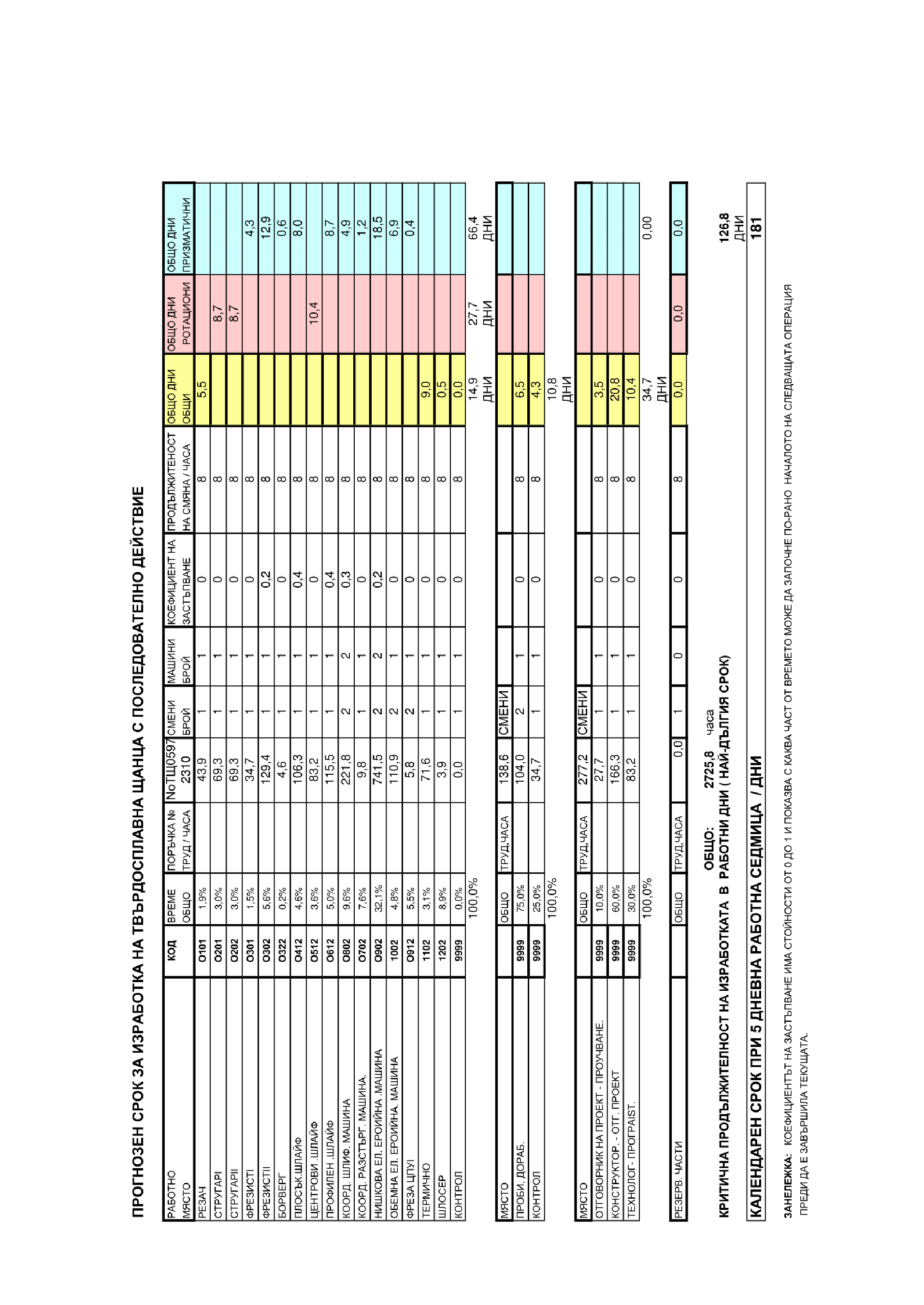
Фиг.12-23
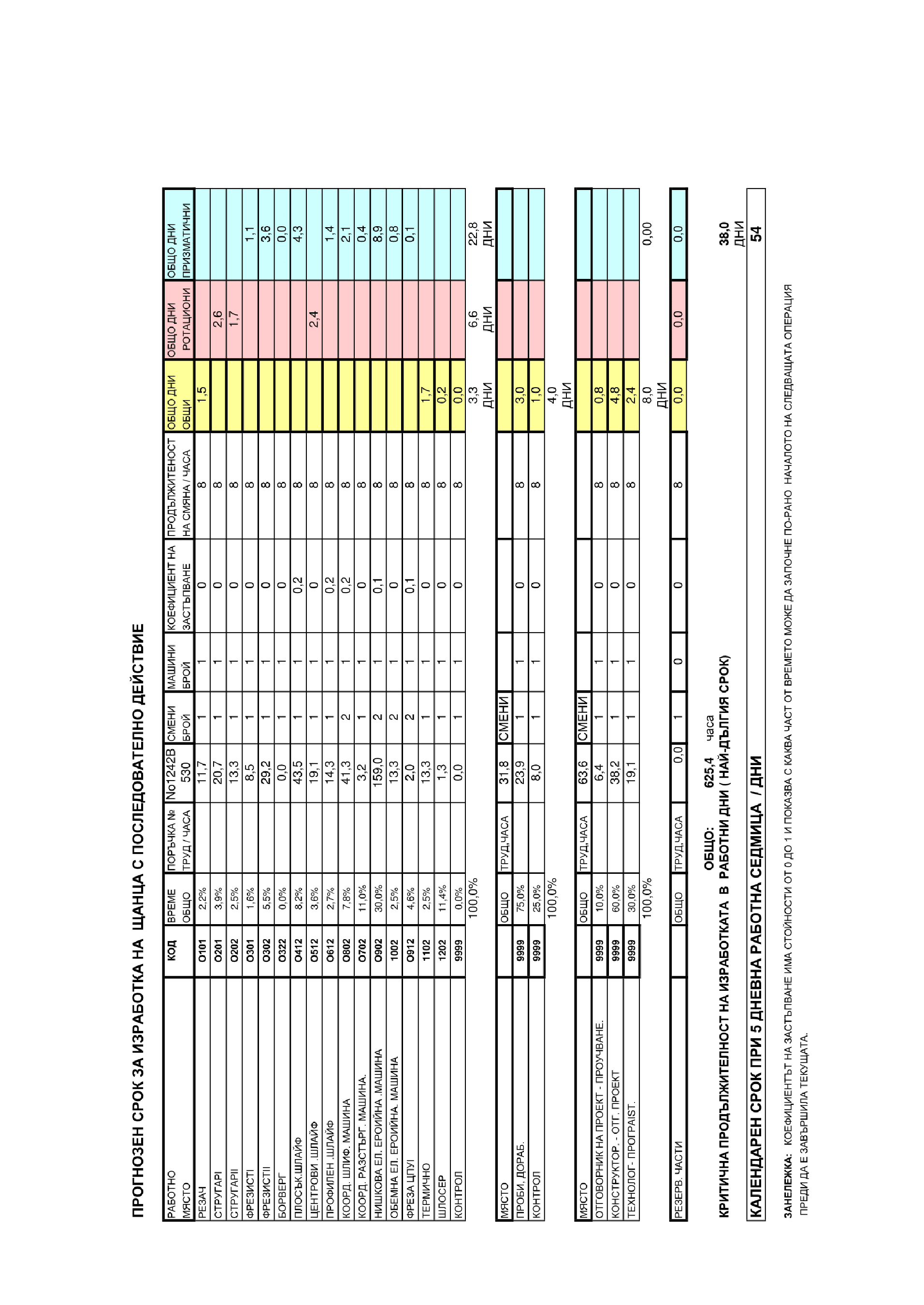
Фиг.12-24
За разгледаните типове щанци е достатъчно да се промени общата трудоемкост на изработка (в часове) в графата под номера на поръчка и ако е необходимо броя на работни смени или коефициента на застъпване за някои операции. След това програмата автоматично ще генерира календарния срок. Разбира се, тук се дава идеалния вариант, който не отчита заетостта на машини (тесни места) и изоставане от срока по тази причина.
ГЛАВА 13. НАСТРОЙКА И ПРОБА (ТЕСТ) НА НОВИ ИНСТРУМЕНТИ ЗА ЩАНЦОВАНЕ – ОЦЕНКА НА КОНСТРУКЦИЯТА, КАЧЕСТВОТО НА ТЯХНАТА ИЗРАБОТКА И ТОЧНОСТТА НА ПРОИЗВЕДЕНОТО ИЗДЕЛИЕ
Производственият процес на специални нестандартни инструменти, включително щанци, задължително изисква проба на инструмента при производителя или при клиента, като завършващ етап на проектиране и изработка. Целта на тази проба е да се получи отговор на два изключително важни въпроса:
– Произведените пробни детайли с инструмента, отговарят ли на изискванията на клиента и чертежа?
– Изработката на инструмента и неговата конструкция, ще гарантират ли надежна работа и лесна поддръжка?
Отговорът на първия въпрос ще определи приемането на щанцата от клиента, а отговорът на втория въпрос ще подскаже, каква гаранция може да се предложи (ако е уговорена предварително, може ли да се изпълни).
Първоначалната проба е много важна, защото имено при нея се откриват скрити дефекти или други проблеми на конструкцията и качеството на изработка. Някои от тях са видими още след първите няколко удара на пресата (например липса на освобождение в матрица или притискач за огъната част от детайла и нежелани деформации). Други стават факт след работа за определен период от време (например задръстване на малки отвори с отпадък и вероятност за счупване на поансон). Трети се появяват или изчезват периодично и също изискват определен период на работа и наблюдение (например вдигане на отпадък над матрицата). На базата на практическия опит от проби на нови щанци, може да се препоръча, винаги да се изпълнява пробна серия при производителя, преди пускане в експлоатация при клиента. Нейната големина е различна в зависимост от размерите на детайла, вида на щанцата, серийността и други условия. При прости огъващи, изтеглящи, пробиващи или изрязващи щанци, са достатъчни 30 детайла, но при сложни последователни щанци с много работни позиции и малки отвори, не са достатъчни дори 600 броя. Най-големи пробни серии (обикновено от 5000 до 10000 детайла) са необходими за твърдосплавните инструменти. Често пресата, за която е прeдназначена щанцата, не е тази, на която ще се извърши първоначалната проба. Това трябва да се вземе в предвид още при конструирането на инструмента и да се предвидят допълнителни държачи, закрепващи отвори или други части за проба на наличната преса. Обикновено, спестяването на тези „консумативи“ за проба, излиза много по-скъпо, ако се отиде за проба направо при клиента – вероятността всичко да се изпълни с първата проба при по-сложни щанци е под 1% . При това, пробата задължително се изпълнява на два етапа – първият цели настройка на пресата и инструмента, а втория етап е за производство на пробна серия годни детайли и може да започне едва след окачествяване на детайлите. Важно изискване е използването на точно предписания материал и ленти, които ще се прилагат при клиента. Често същия материал, отрязан от лист, вместо от по-скъпата лента, показва разлики в пружинирането след операцията и напасването на щанцата за него води до проблеми при работа с предписаната лента (особено при точни огъвки, изтеглени, формовани, отбортовани участъци). Следователно, пробата на нов инструмент трябва да се планира минимум за три етапа:
1. Първоначална проба с настройка на преса, инструмент и процес.
Тук трябва да се настроят хода и закритата височина на пресата, дължината на подаване на лентата и разстоянието на подаващите челюсти (за автоматични преси с подаващо устройство), в някои случаи и момента на начало на подаването на лентата и нейната височина спрямо масата на пресата, подложки под щанцата (ако са необходими), улеи за отделяне на готови детайли или отпадъка, гилотини за нарязване на отпадъка от лентата, намотаващи и размотаващи устройства (ако са предвидени), междинни лентоводачи за лентата, защитни датчици на пресата и инструмента, система за смазване на лентата (ако има такава), пневматична система за издухване на детайли или отпадъци (ако са предвидени), буфери на пресата (ако са предвидени), палети за готови детайли и отпадък.
По щанцата трябва да се проверят всички отвори и части за закрепване към пресата, нивото на матрицата спрямо подаващото устройство, без проблемното подаване и движение на лентата между работните позиции, гарантирано повдигане и събуване на лентата или детайла от поансони и матрица, правилно и навременно центроване на лентата, сигурното отделяне на отпадъка или готовите детайли от работната зона, действието на защитни системи (ако е предвиден защитен ловител), да се уточнят височините на ограничителите на хода за постигане на необходимата точност на детайла, да се регулира положението на поансони или да се изберат и заменят подложките под тях, да се настроят буферни пружини в щанцата (ако е предвидено).
1.1. Настройката на пресата – извършва се в следната последователност:
– Смяна на хода (ако е необходимо и възможно) за ексцентър пресите. При хидравличните преси е достатъчно да се настроят изключвателите на хидравличните разпределители;
– Приблизителна настройка на закритата височина за ексцентър пресите чрез винта на мотовилката – тя трябва да е по-голяма от необходимата за щанцата и да позволява лесно монтиране;
– Сваляне или качване на подщанцова или допълнителна плоча към масата на пресата;
– Настройка на буфери на пресата (ако са предвидени). Някои преси имат такива пружинни буфери и те могат да се монтират на пресата, ако не е качен инструмент. При хидравличните преси с двойно действие и хидравличен буфер, разположен под нивото на масата, е необходимо той да се приведе в долно положение и в съответните отвори да се поставят междинни предаващи силата пръти - Фиг.13-1.
Фиг.13-1
При тях може също предварително да се регулира налягането (да намали силата) - Фиг.13-2
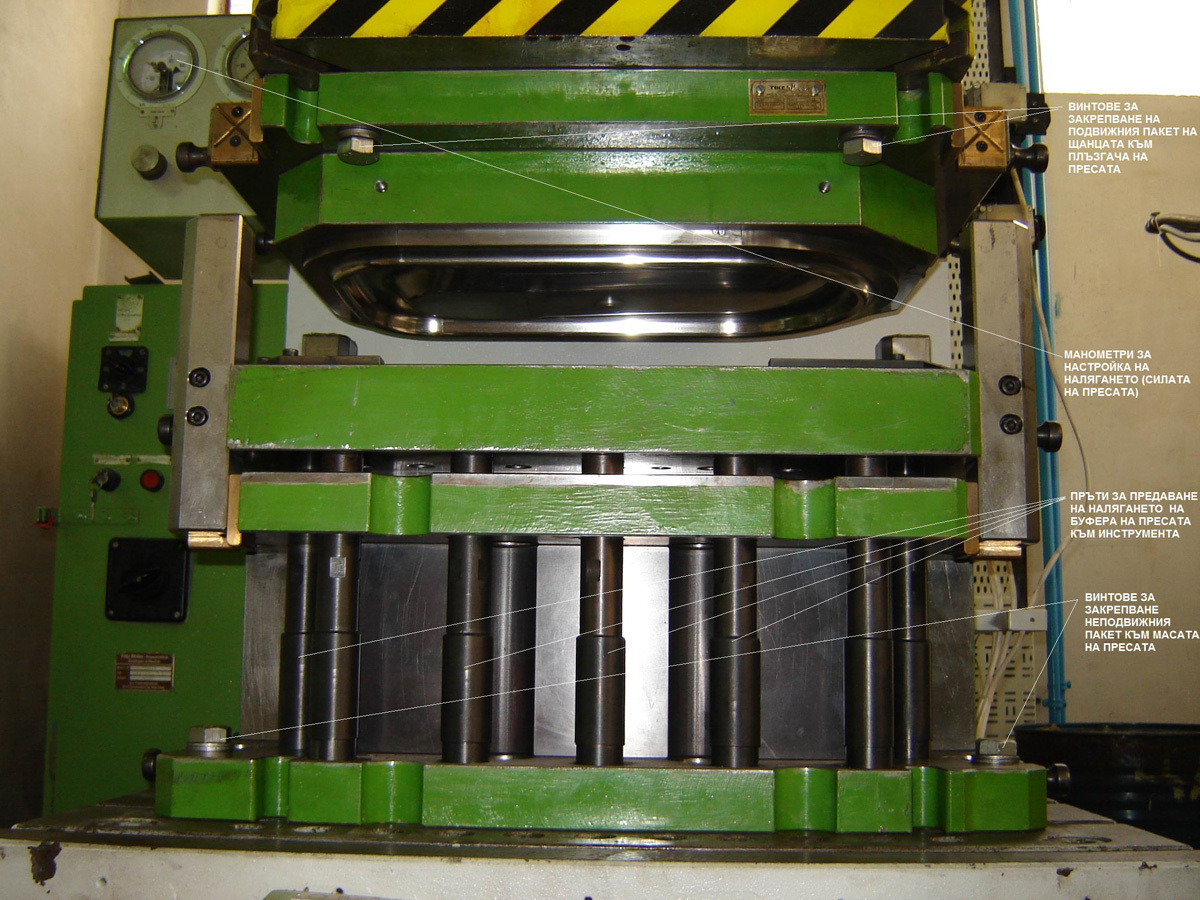
Фиг.13-2
за да се предотврати опасност от повреда на щанцата при първия работен удар;
– При автоматични преси трябва да се настрои подаващото устройство за необходимата дебелина и стъпка на подаване, да се подготви размотаващото устройство и необходимите лентоводачи и улеи.
1.2. Настройката на щанцата – извършва се в следната последователност:
– Поставяне на дистанционни планки върху масата на пресата (ако е необходимо и не са включен в самата конструкция на инструмента) за режещи щанци, за които не е осигурено свободно падане на отпадъка или готовия детайл през отвора в масата на пресата - Фиг.13-3.
Фиг.13-3
Те трябва да са разположени максимално близо до отворите за отпадък, но да не ги затварят дори частично - Фиг.13-4.
Фиг.13-4
Важно е да се знае, че инструментът трябва да се мести заедно с тях, като се избягват удари, които могат да предизвикат местна деформация по плочите и да влошат необходимия контакт между тях. Идеалният вариант е планките да са предвидени в конструкцията на щанцата - Фиг.13-5;
Фиг.13-5
– Центроване и закрепване на щанците – при ексцентър пресите за центроване се използва цилиндричния държач на щанцата, който влиза в полуотвори на плъзгача на пресата и се затяга с гайки и шпилки - Фиг.13-6.
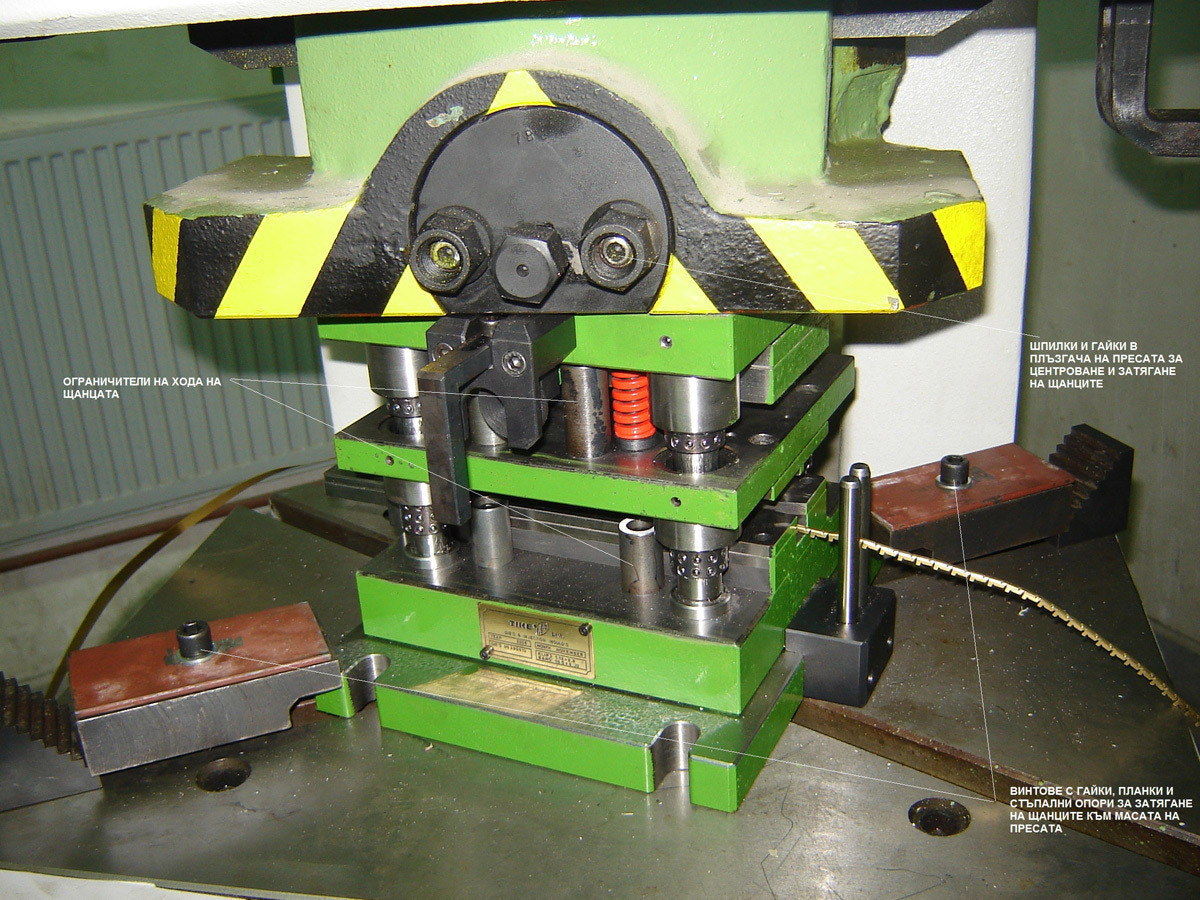
Фиг.13-6
За малки щанци това е напълно достатъчно - Фиг.13-7,
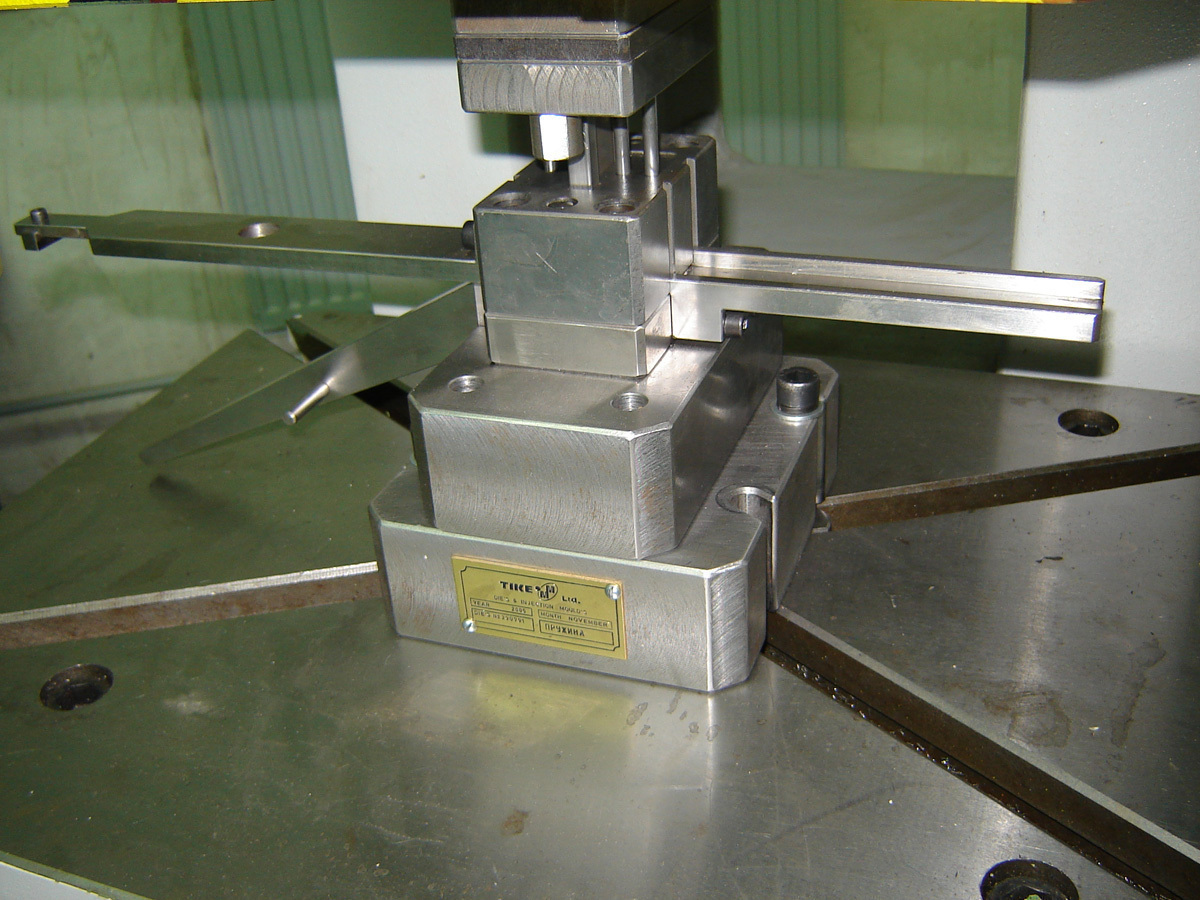
Фиг.13-7
но при голямо габаритни инструменти или при големи сили за събуване на лентата от поансоните, е необходимо допълнително закрепване с винтове или винтове и планки на подвижния пакет - Фиг.13-5 и Фиг.13-8.
Фиг.13-8
За автоматичните преси, това е начина на закрепване (с винтове). При тях държача служи единствено за центроване на щанцата. Обикновено, щанците за автоматични преси са снабдени допълнително с призматичен клин (за надлъчно центроване по канал в плъзгача на пресата) или цилиндричен щифт, разположен по надлъжната ос на инструмента на разстояние от държача. Това е необходимо за точно разполагане на щанцата спрямо подаващото устройство и трябва да се гарантира при центроване и закрепване на инструмента. При хидравличните преси с двойно действие, центроването се извършва до съвпадане на отворите за предаване на силата чрез междинни пръти от буфера от Фиг.13-1, но закрепването остава с винтове. Закрепване на неподвижната част на щанците към масата на пресата става с винтове в предвидени канали на долната плоча от Фиг.13-1, или с шпилки, гайки, стъпалнни опори и затягащи планки от Фиг.13-6. При използването на затягащи планки трябва да се знае, че опората в другия край на планката трябва да е висока точно колкото е плочата на инструмента или по-висока с не повече от 0,2-0,3 mm. Не се препоръчва тя да е по-ниска, защото възниква хоризонтална сила от затягането, която се стреми да измести инструмента. Разположението на затягащите шпилка или винт, трябва да е максимално близко до инструмента, за да бъде най-голяма приложената сила. Изключително важно е местоположението на точките на затягане да е близо до водещите колони на щанцата, за да се намали динамичното въздействие върху тях от еластично деформиране на плочата при удар на пресата;
– Последователност на затягане на щанците – винаги първо се затягат винтовете на подвижния пакет (горна плоча). Затягането се извършва близо до долно положение на инструмента, за да се свият пружините и оберат хлабините. Извършва се постепенно, на кръст. Преди затягане на неподвижния пакет (долна плоча) към масата, се извършват един или два хода в режим на настройка или ръчно задвижване (за малки преси), за да го нагласят водещите части към закрепения за плъзгача подвижен пакет. Стягането се извършва на кръст, постепено, за да не се създаде допълнително напрежение в системата;
– Настройка на долната точка на инструмента – при ексцентър пресите се извършва чрез регулиращия винт на мотовилката постепено, като при всяко намаляване на височината се проверява дали подвижния пакет преминава през долна мъртва точка чрез следене за наличие на хлабина между ограничителите на хода - Фиг.13-9.
Фиг.13-9
Изключително важно е, да не се подаде повече от необходимото, защото пресата с инструмента ще се заклинят и са възможни повреди. Ако все пак това се случи, необходимо е реверсиране на посоката на въртене на коляновия вал (ако е възможно) или при по-малки преси да се освободи пневматичната спирачка на вала и ръчно да се завърти в обратна посока маховика на пресата. Успехът на това действие е възможен само при незначителни стойности на подминаване на критичната височина. Трябва да се знае, че това е само приблизителна настройка за първата проба. След няколко удъра на пресата е много вероятно, да е необходимо още малко скъсяване на височината, за да се компенсират еластичните деформации и хлабините в пресата. Всички действия се извършват в режим за работа на пресата „настройка“ и „единичен удар“. За хидравлична преса трябва точно да се настроят изключвателите за край на хода и тези за ускорен ход (ако пресата разполага с такива). При настройката на височината в двата или четирите края на матрицата се поставят парченца от лентата, които да гарантират необходимото разстояние при работа;
– Пробни удари с инструмента – при ексцентър пресите се изпълняват единични удъри и след всеки, лентата се проверява (ако е възможно се изважда) на всяка стъпка на подаване за деформации, вдигнат отпадък от матрицата - Фиг.13-10,
Фиг.13-10
плавно движение в лентоводача и точно фиксиране на позиция - Фиг.13-11.
Фиг.13-11
При хидравличните и ексцентър пресите за ръчна работа е препоръчително да се прилага режим „работа с две ръце“, който не позволява задействане на плъзгача до момента на едновременно натискане на двата бутона, разположени извън работната зона. Така се повишава безопасността и се отстранява възможността за травми на оператора на пресата. След получаване на готов детайл, той се оглежда и се измерват някои размери, за да се оцени настройката на пресата и инструмента;
– Измерване на първите детайли от пробата – същността на тези измервания е да се оцени настройката и необходимите корекци в нея или в инструмента, а не окачествяване и заключение за детайла. Разбира се, понякога още на този фаза се откриват грешки и пропуски. При сложни щанци с последователно действие, тъкостта на тези измерванията се състои в определяне, кои точно размери зависят от настройката и трябва да се измерят. Добре подготвената конструктивна документация е комлектована с технологична схема на лентата или заготовката, от които става ясно какво да се провери. Правилото е, че при няколко последователни формоизменящи прехода (огъване, изтегляне, отбортоване, оребряване, формоване на маркировка или фаски), само един зависи от пресата и се приема за базов. Останалите трябва да се регулират в щанцата спрямо него (ако са предвидени регулиращи механизми за тяхната височина) или да се напасват чрез избор и уточняване на височината на компенсиращи подложки. Не се препоръчва да се отнема от поансоните, защото при следващата неуспешна настройка е невъзможно да се възстанови предишната. По тази причина, няма общо правило за избор на контролен размер, без да се познават особеностите на съответната конструкция;
– Корекции на ограничители и поансони – отклоненията на първите детайли от очакваното е нормално явление, защото преднамерено не са постигнати необходимите настройки, като целта е предпазване на инструмента. След измерване на контролните размери на детайла се взема решение, кои поансони или компенсиращи подложки трябва да се корегират. Обикновено, следващата настройка изисква по-силен удар и планиране, които се извършват за сметка на намаляване на закритата височина. За тази цел трябва да се намали височината на ограничителите на хода от Фиг.13-5 и от Фиг.13-6, което изисква точно измерване с гранични плоско паралелни пластини точните размери в техните места. Препоръчително е, ограничителите да се демонтират и монтират, без да е необходимо сваляне от пресата и разлобяване на инструмента. По този начин лесно се установява на какъв размер трябва да се корегират. На базата на този размер и текущо използваните компенсиращи подложки, се уточнява кои трябва да се намалят или увеличат и с каква стойност. Ако пресата има уред за отчитане на височината, неговите показания се записват и могат да се използват при следваща настройка (виж Фиг.9-6 - червения брояч на плъзгача). Използването на компенсиращи подложки обаче, изисква сваляне на инструмента от пресата. Правилната конструкция на щанците позволява изваждане на формоващи поансони и подложки, само с изваждане на подвижния от неподвижния пакети и развиване на закрепващите винтове, без необходимост от допълнително разглобяване. Пресата остава в настроено положение, готова за работа с щанцата, след изпълнение на разгледаните корекции. Ако е необходимо, процедурата с корекции се повтаря толкова пъти, колкото са необходими за постигане на очаквания резултат.
2. Пробна серия от инструмента.
Пробната серия се изпълнява след като са приключили всички необходими корекции по щанцата. Броя пробни детайли обикновено се уговаря с клиента. Ако няма такава уговорка, препоръчва се като ориентировъчна големина за серията да се прилагат: 30-50 детайла за прости щанци; 600-1000 детайла за щанци с последователно действие за автоматични преси (горната граница е за малки детайли); над 5000 броя за твърдосплавни щанци на автоматични преси. Преди стартиране на пробната серия, инструментът трябва да сработи на празен ход най-малко още толкова работни цикъла, като предварително се смажат всички подвижни части. След преключване на фазата за сработване, матриците, поансоните и притискачите се почистват от изличното масло и се прекарва лентата стъпка по стъпка в режим „настройка“ или „единичен удър“ до излизане от инструмента. Включват се всички защити и може да започне изпълнението на пробната серия в автоматичен режим (ако е предвидена работа в него). През това време инструмента се наблюдава и оператора трябва да има готовност да спре пресата при откриване на нередност. Добра практика е, поне веднъж да се спре и огледа щанцата за вдигнати отпадъци или други отклонения от процеса. Периодично се извършва визуален контрол, дали падат редовно отпадъците от малките отвори. В началото, средата и края на серията трябва да се отделят по няколко детайла за контрол заедно с щанцованата лента - Фиг.13-12, Фиг.13-13, Фиг.13-14.
Фиг.13-12
Фиг.13-13
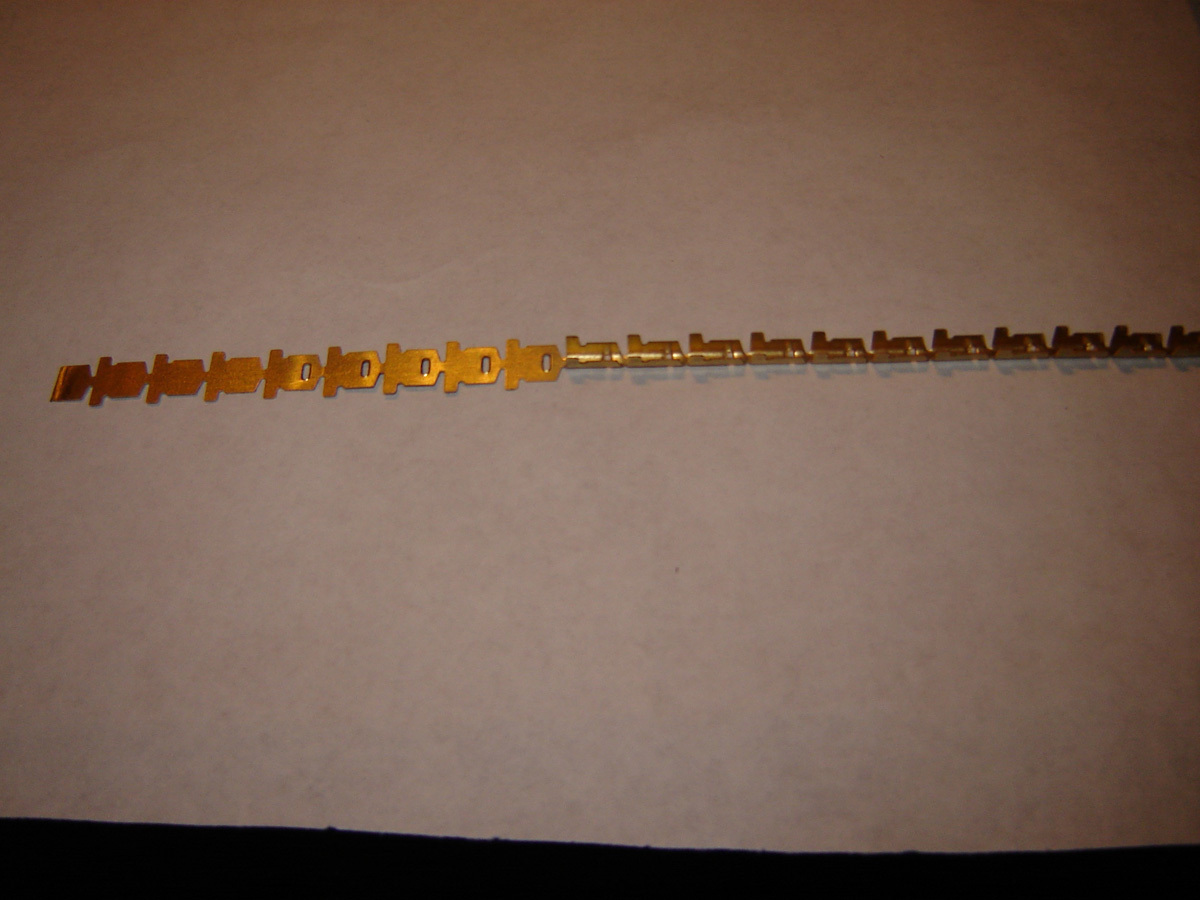
Фиг.13-14
След успешно приключване на пробната серия, щанцата се разглобява и преглежда за натрупани стружки, износване на режещи или формоващи части, пружини и ловители, задиране на поансони (предимно тези с голямо напречно сечение) или водещи колонки, задръстване на отвори с отпадък. Особено внимателно трябва да се огледат режещите ръбове на твърдосплавните щанци за микро откъртвания. Ако всичко е наред, може да се даде оценка за надеждност на инструмента и да се поемат определените гаранции пред клиента. Тази проба дава много висок процент на сигурност, че пускането в редовна експлоатация при клиента, ще протече успешно.
3. Окачествяване на произведените детайли с новия инструмент.
Отделените от пробната серия детайли за контрол се подлагат на измерване и оценка за съответствието с чертежа и други документи, регламентиращи изискванията на клиента. Всички размери от чертежите условно могат да се разделят на две групи – важни функционални размери за работоспособността и безопасността на изделието и размери без специални изисквания. В професионално подготвените чертежи на детайлите, важните функционални размери са означени, често са посочени точно и формите на контрол при тяхното приемане. В много случаи най-простото указание за важността на размера, е наличие на означен допуск на чертежа, различен от общия. Самия факт, че конструктора си е направил труда да означи допуск на размера или отклонение от форма и разположение, подсказва косвено за неговата важност. Принципно, тези размери подлежат на контрол като стойности и като разсейване от очаквата величина. За такава оценка са необходими не по-малко от 5-6 детайла (колкото е по важен размера, толкова повече детайли трябва да се проверят). Все пак, в случая има едно изключение – ако размера е от разделителна операция (изрязване, пробиване), неговото вариране ще е в тесни граници и ще се дължи по-скоро на грешките при измерване, затова едва ли ще са неободими повече от 5 мостри за измерване. Макар и рядко, важни функционални размери могат да се вместват в общите допуски на чертежа. В този случай, ако няма подсказващо обозначение, трябва да се отправи запитване към клиента (особенно, ако този размер се отклонява от общите предписани допуски). Размерите без специални изисквания попадат в общо предписаните допустими отклонения. В повечето случаи, това са технологично необходими размери (на пример радиуси на закръгления на ъгли, фаски, размери на освобождаващи канали, някои отвори или габаритни размери, ребра за усилване на здравината на огъвки). За тези размери допуските са по-широки. При тях не е задължително да се контролират 5-6 детайла (освен ако те варират в широки граници и е необходима оценка за средната стойност). При отклонения на тези размери от зададените общи допуски, клиентите често приемат фактически получената стойност и променят чертежа или вмъкват забележка, че стойностите не важат за конретния инструмент. Всички тези дейности по измерване, заедно с оценка за годността и надежостта на инструмента, трябва да се документират в протокол или доклад за контрол, който да се съгасува с клиента преди предаването на инструмента. Този подход ще предотврати много от възможните спорове в бъдеще между производител и клиент.
За пример е показан попълнен измервателен протокол за CAN PLATE SUBD, произведен с щанца с последователно действие, чиято лента е показана на Фиг.13-15.
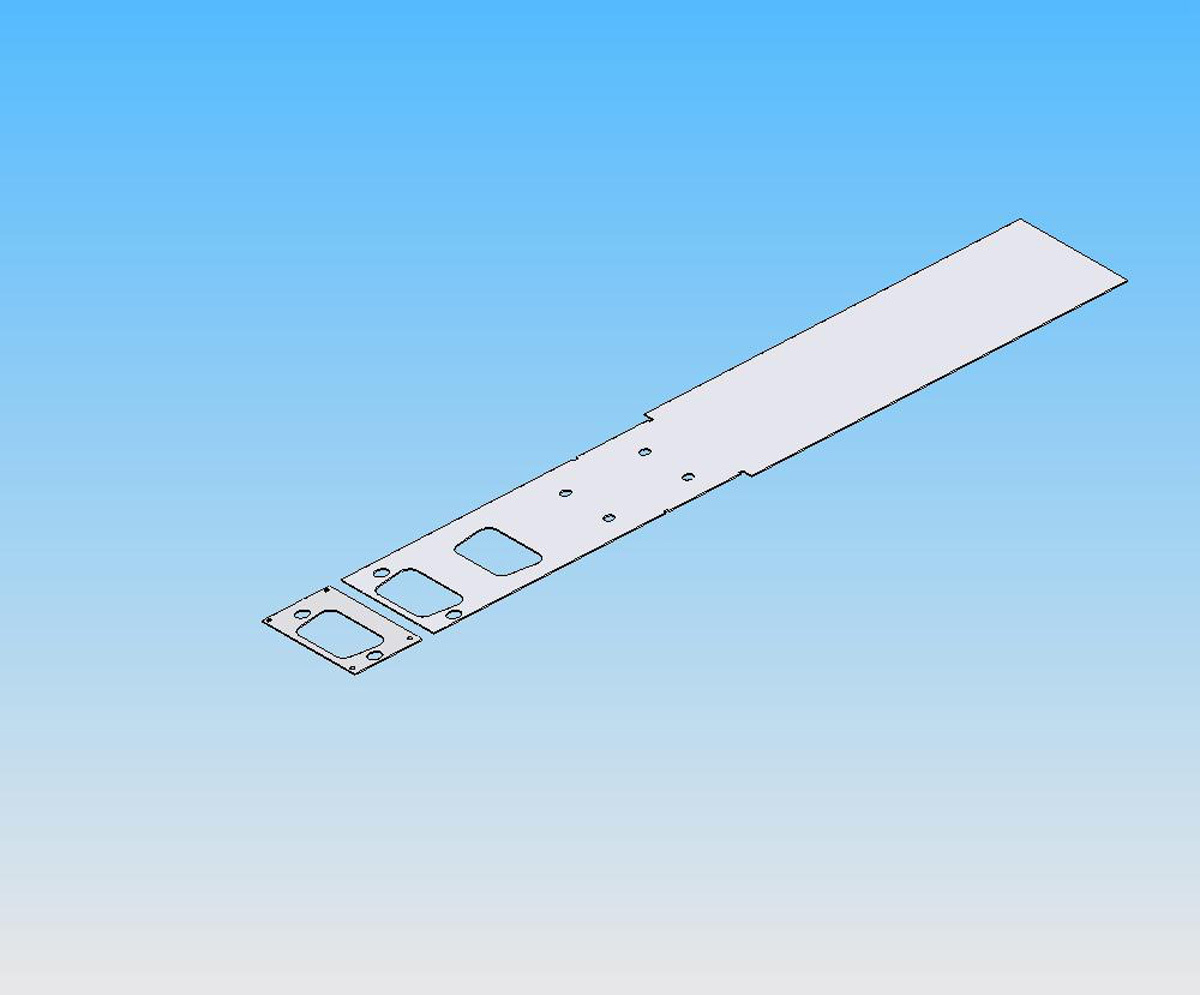
Фиг.13-15
Първата страница съдържа общите условия за инструмента, щанцования материал, модел преса, режим на работа, изпълнител на пробата, брой измерени детайли, контрольор и заключение за годност (приемане от клиента) - Фиг.13-16. На втората страница е показана оценката за работата на функционалните системи на щанцата и участвалия в нея персонал - Фиг.13-17. На третата страница са отделени резултатаите от измерване на функционалните размери - Фиг.13-18. За детайла те са дебелина на материала, диаметър и разстояние между отворите, по които ще се центрова детайла за точково електро съпротивително заваряване към друга част. Тук трябва да се обърне внимание на математическата обработка на резултатите от измерване. Извършена е оценка на математическото очакване (средната стойност) и дисперсията на размерите, като на тази база са оценени вероятните граници на процеса. Малкия брой измерени детайли обаче, не позволява да се даде сигурна оценка за надежността на процеса и неговите граници. За тази цел, от фирмата „Telemechanic” са предложили стеснение на заложения в чертежа производствен допуск до 63%. Това стеснение компенсира до някъде малкия брой детайли, защото математически най-висока плътност на размерите при нормално разпределение на случайно измерените величини, е в средната зона (над 50%), а с отдалечаване плътността рязко намалява. С това е отчетена и вероятността за поява на такива размери. Крайната оценка за даден размер е положителна (1), тоест процеса за неговото получаване е стабилен, ако математическите граници са в интервала от 63% от допуска. Ако излизат извън тях, оценката за размерът е отрицателен (0) и процесът се оценява като нестабилен. Все пак, крайното решение се взима от клиента между следните възможности: приема или отказва, като при отказ се препоръчват възможни въздействия – ново измерване, корекция на инструмента, приемане на отклонението само за този инструмент, ще се корегира чертежа на детайла. На четвъртата страница са размерите, без специлни изисквания - Фиг.13-19. Подхода за оценка е същия, възможните граници обаче, се разполагат в 100% от зададения допуск по чертеж. На клиента обикновено се изпращат контролираните мостри заедно с лента от инструмента и доклад с резултатите от извършения контрол.
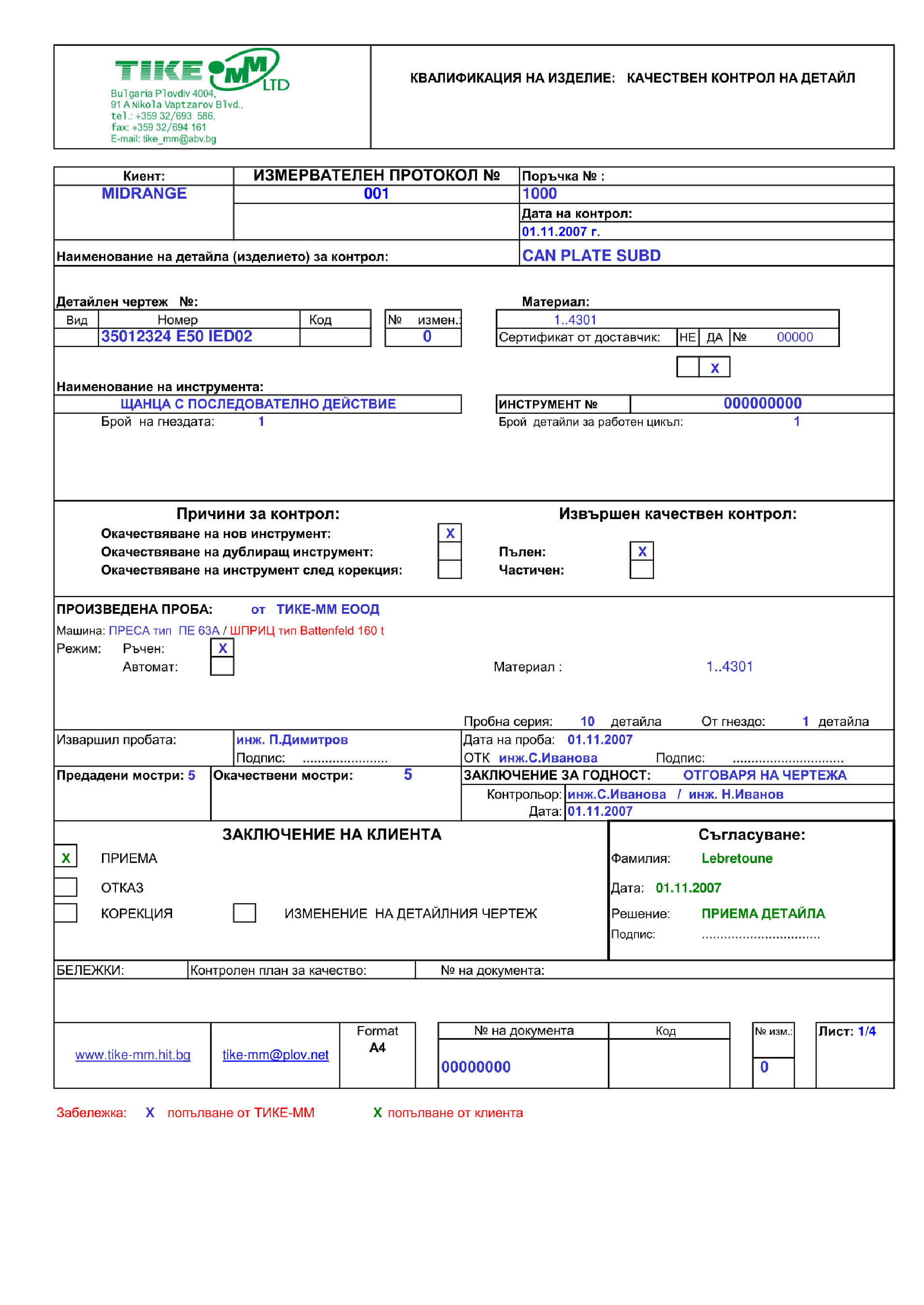
Фиг.13-16
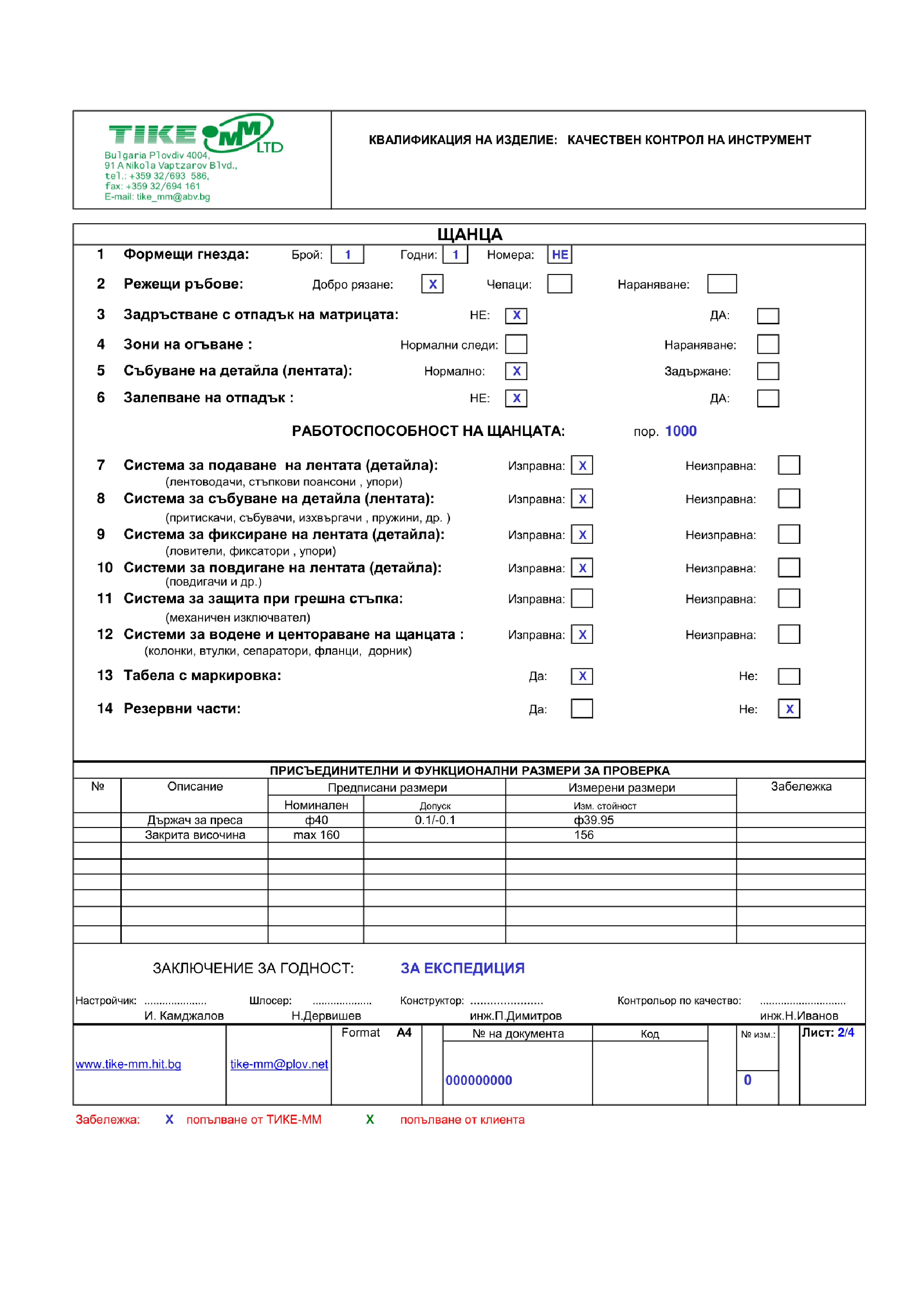
Фиг.13-17
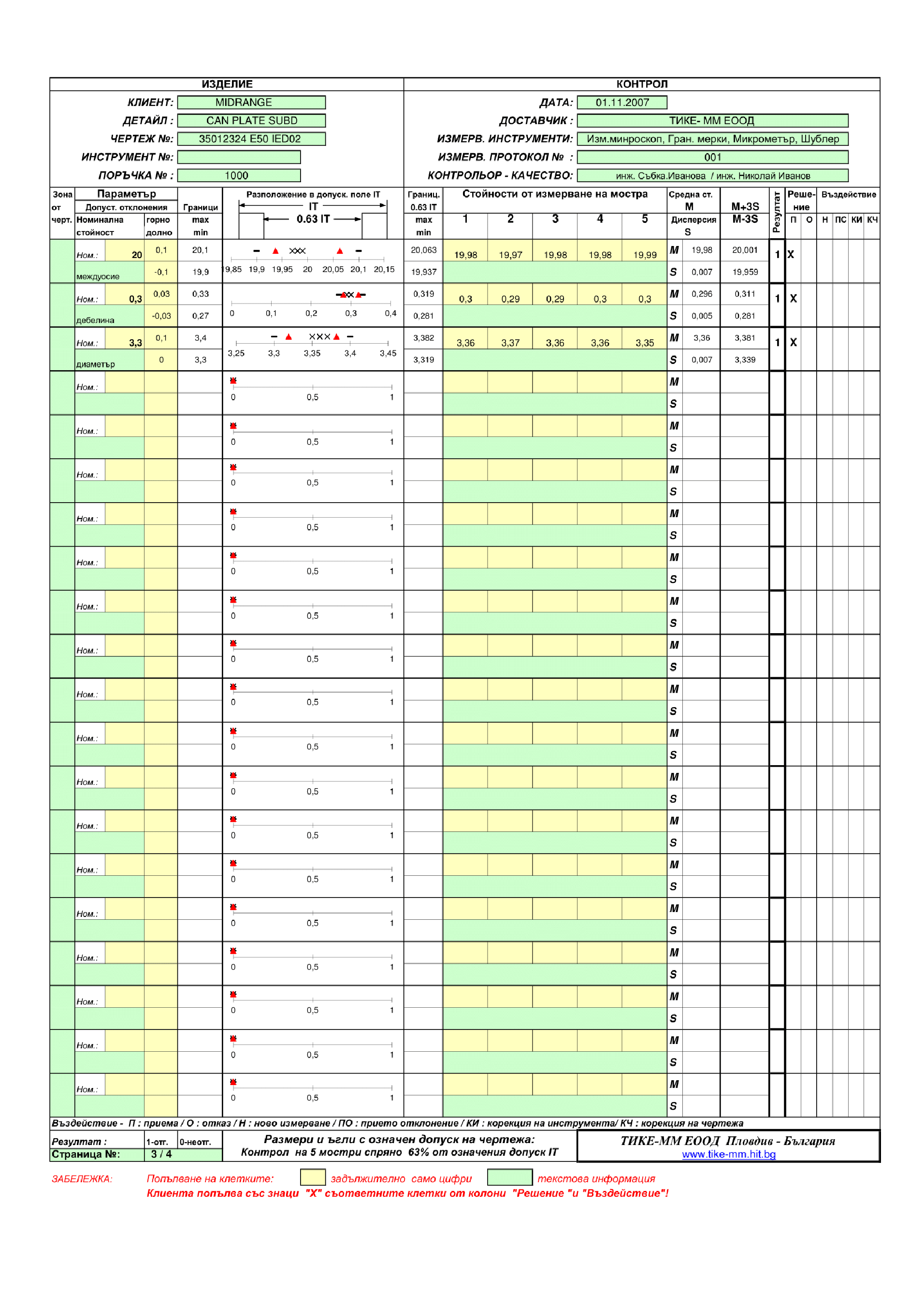
Фиг.13-18
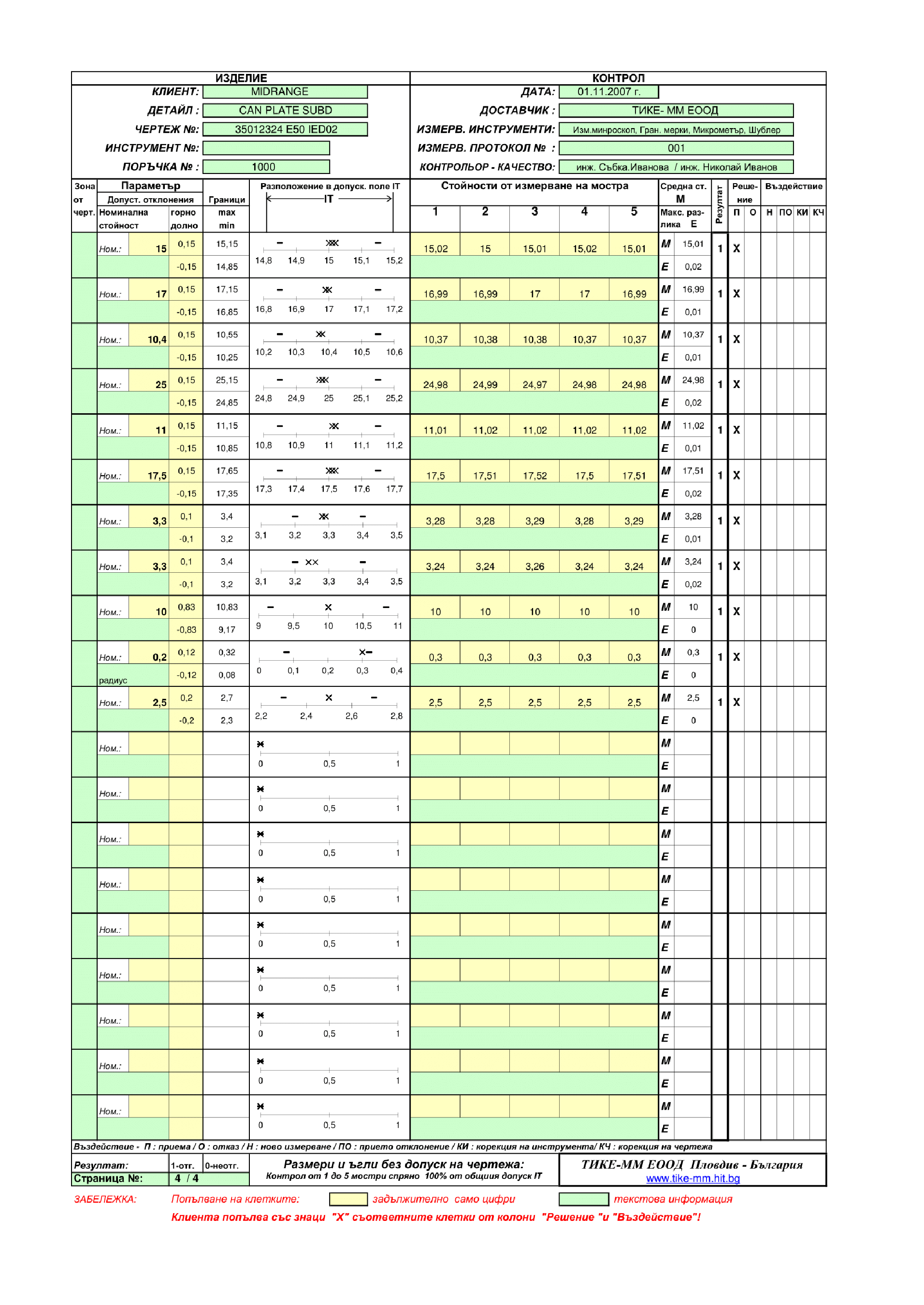
Фиг.13-19
Препоръчва се няколко мостри от пробата с още една лента и копие на измерванията да се съхраняват поне за периода на гаранция на инструмента, за решаване на възникнали спорове в този срок.
ГЛАВА 14 . БЕЗОПАСНА ЕКСПЛОАТАЦИЯ, ПОДДРЪЖКА И РЕМОНТ НА ИНСТРУМЕНТАЛНАТА ЕКИПИРОВКА ЗА ЩАНЦОВАНЕ
Успешната експлоатация на новите инструменти за щанцоване е свързана с правила за безопасна работа с тях, за необходимата подръжка и ремонт.
1. Общи правила за безопасна работа с инструменти за щанцоване.
Тук трябва ще се посочат някои документи и стандарти, регламентиращи безопасната работа с щанци и пресово оборудване, без претенции за всебхватност.
Най-напред това е българският стандарт БДС 16640-87 „Охрана на труда. Щампи за листово щамповане. Общи изисквания за безопасност“. В него са заложени някои основни изисквания към конструкцията на щанците, за да се предпазят работещите от възможни травми по крайниците.
– Първото изскване въвежда елементи за транспорт, повдигане и монтаж за щанците на всички части (плочи, матрици, поансони), чието тегло е равно или по-голямо от 20 килограма. По този начин може да се използва повдигаща техника и ще се намали вероятността от изпускане и травми по крайниците на обслужващия персонал. Минималното изискване към конструкцията е, да са предвидени съответни отвори за закрепване на такива елементи при необходимост в случай, че пречат на нормалната работа на щанците. Елементарни устройства за повдигане, са закрепени в предвидените отвори болтове, които позволяват повдигане със закачени за тях въжета или вериги с помоща на телфер, кран, мотокар или друга техника. Професионалните варианти изискват специални транспортни палци от Фиг.13-8, болт с халка по DIN 580 - Фиг.14-1
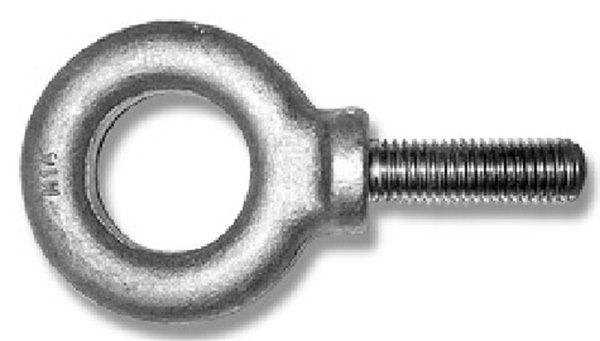
Фиг.14-1
или други подобни конструкции - Фиг.14-2, Фиг.14-3, Фиг.14-4, Фиг.14-5.
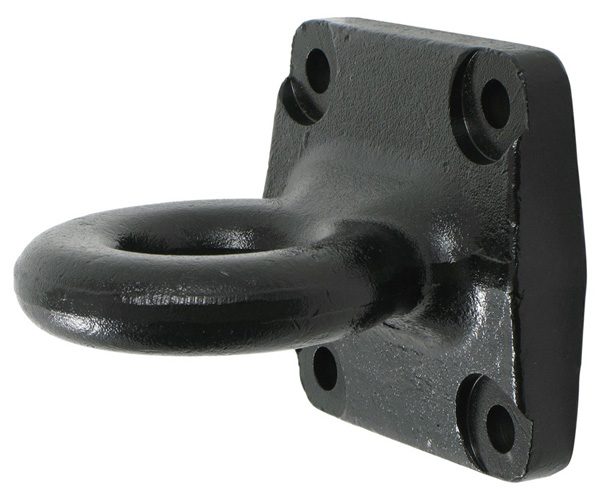
Фиг.14-2
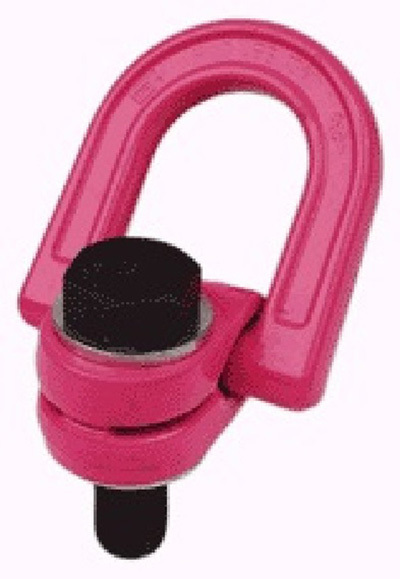
Фиг.14-3
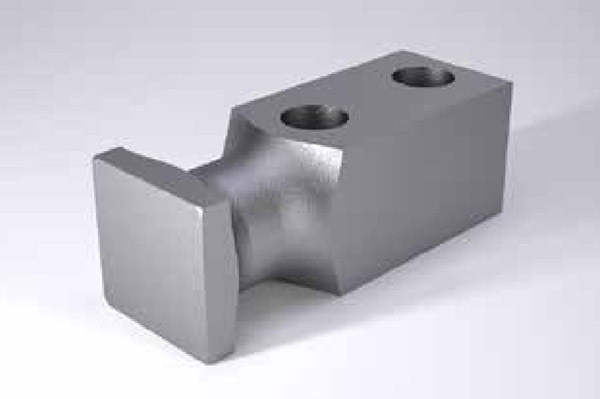
Фиг.14-4
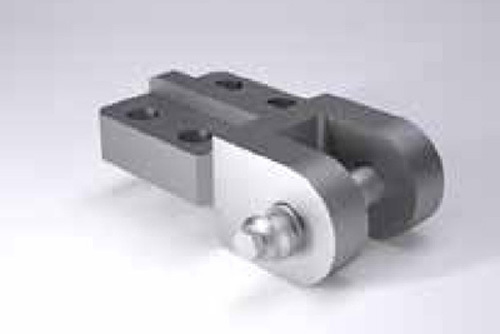
Фиг.14-5
– Друго изискване към конструкцията на щанците е минималното разстояние между подвижните плочи, където рaботника може да постави по невнимание пръста си, да е повече от 25 mm. Така може да се спести травма на ръката му при невнимание и случаен работен ход на пресата. Такова опасно място е дистанцията между горна и водеща плоча в зоната на ограничителите на хода, където при настройка се поставя хартия с ръка Фиг.13-5, а често трябва и да се придържа при работения ход, за да не падне. Разбира се, не винаги може да се осигури това изисквание, защото се намесват стандартни покупни дължина на поансони, особености на процеса и различни конструкции на инструментите.
– Щанците с ръчно подаване на лента (ако се използва непрекъснат цикъл на хода, а не единичен удър на преса), трябва да са затворен тип с процеп между матрицата и водача до 8 mm, който не позволява на оператора да пъхне пръстите си в работната зона (например Фиг.6-14).
– Ако това условие е невъзможно, на пример има притискач с подпружинена водеща плоча, препоръчва се поставяне на защитни ограждения или прегради, пречещи на попадане на ръцете на работника в работната зона при невнимание. Тези прегради не бива да нарушават видимостта, затова най-често са от перфорирана ламарина, мрежа или прозрачен материал. В много случаи обаче (например огъващи или изтеглящи щанци), заготовките се поставят и изваждат една по една от щанцата. Това е характерно за еднооперационната технология. В този случай е невъзможно да се постави защитна преграда, защото ще пречи на работата. Тогава се препоръчва да се изполват пинцети, куки, клещи или други приспособления, вместо да се поставя или изважда заготовката с гола ръка.
– В матриците и притискачите на щанци за ръчно поставяне и снемане на заготовката с пинцети трябва да има съответни освобождения за тях, за да се гарантира, че при аварийна ситуация, те няма да предизвикат спукване на активни части и нараняване на работника чрез откъртени и изхвърлени парчета. Като принцип, всички подвижни части в щанцата, създаващи опасност, трябва да имат защитни ограждения при работа. Добра практика е те да се боядисат в червен или оранжев цвят.
– Почти всички преси разполагат със специален режим за работа с единично поставяни заготовки – „работа с две ръце“ (виж Фиг.13-1, Фиг.13-5). При него стартиране на работния ход на плъзгача е възможен едва след едновременно натискане на достатъчно отдалечени един от друг бутони, които не могат да се задействат с една ръка.
– Още едно изискване към конструкцията е защита на щанците, работещи на преси с автоматично подаване. Те трябва да имат защитно устройство, изключващо пресата при неправилно подаване, например изключвател за пресата, задействан от контролен ловител при грешно подаване лентата на стъпка (виж Фиг.5-21). Отсъствието на такава защита може да доведе до задръстване на инструмента, заклинване на пресата, откъртване на парчета от активните части и с това нараняване на обслужващия персонал.
Важен документ, който трябва да се познава, е „Наредба №3 от 23 март 2004 г. за осигуряване на здравословни и безопасни условия на труд при механично (студено) обработване на металите“, по специално приложение №2 към член 6, относно специфичните изисквания към пресовото обработване на метали, детайли и изделия. Приложение 2 обобщава част от разгледаните изисквания и добавя допълнителни такива към пресовото оборудване, закрепването на инструментите, хидравличните и механични преси. Всички разгледани изисквания за безопасност в документите обаче, са с общ характер. Те трябва да намерят конкретната си форма в попънения паспорт или инструкция за правилна експлоатация (виж Фиг.5-53). Към нея може да се включи формуляр от стандарта БДС 16640-87 (Бланка №2), в която за всяка щанца да се конкретизират взетите предпазни мерки. При ръчно подаване или сваляне на заготовка се препоръчва указания за безопасност да са включени в техническите изисквания на сборния чертеж. Всички мерки за безопасност обаче ще са напразни, ако не се извършва необходимия инструктаж на персонала преди допускане за работа с нов инструмент.
2. Нормална експлоатация на инструментална екипировка за щанцоване.
Щанците са инструменти за серийна работа. Обичайната им експлоатация преминава през следните фази:
– Подготовка на пресата;
– Монтиране и настройка на предвидената щанца;
– Производство на заложената партида щанцовани детайли;
– Сваляне, почистване и прибиране на щанцата за съхранение.
В паспорта или инструкция за правилна експлоатация на щанците, тези фази трябва да намерят конкретно описание на особеностите за всяка от тях, като визуални и други проверки преди работа, смазване на определени части, особености и проверки на закрепването към пресата, периодичност на смазване на необходимите възли при работа, препоръчителни наблюдения и проверки върху определени части, период за спирания и почистване, препоръчани действия при възникнали отклонения по време на работа, начини и регулировки (ако са необходими), смазвне на лентата, следене за нормалното отделяне на отпадъците и готовите детайли, почистването и проверки на щанцата след приключване на партидата и сваляне от пресата, условията за транспорт и съхранение.
Годността на инструмента за производство се оценява пряко по точността на размерите на щанцования детайл и косвено по състоянието на неговите активни части. Важна задача за правилната експлоатация на инструменталната екипировка за щанцоване е задаване на обосновани критерии за годност. Под обосновани се разбира действително необходими, чието неспазване има неблагоприятни последици за произвежданите детайли или самия инструмент. Най-разпространения критерий за годност е броят на изработените детайли до ремонт, или както се нарича в практиката „удари до ремонт“. На пръв поглед, това е лесен за изпълнение критерий, достатъчно е просто да се попълва редовно посочения в паспорта или инструкцията за правилна експлоатация от Фиг.5-53-D формуляр. Тук обаче се крие основния проблем – този критерий за нови инструменти е изцяло субективен. Ако се изключат случаите, в които той лесно се свързва с измерване на определен размер, който в процеса на експлоатация се променя поради износване на матрици и поансони (например точен отвор), най-често той се задава по аналогия с подобни инструменти. Не може и дума да става за предварително съобразяване с огромния брой фактори, влияещи по различен начин на конкретния инструмент, защото такава оценка изисква достатъчно натрупани практически наблюдения, анализ и препоръки, каквито няма. Опитът е показал, че назначени по такъв начин „удари до ремонт“ са надвишавали оптималните и са довели до счупване на вложка, вследствие на по-ускорено затъпяване на режещи ръбове след определен момент и увеличаване на натоварването. След намаляването им с около 25%, такъв проблем повече не е възниквал при този инструмент, за което обаче са били необходими три цикъла за наблюдение и за заточване (без цикъла с авария). При други инструменти, заложеният брой на изработените детайли до ремонт, може да е значително по-малък от оптималния (презастраховка) и да настъпи обратния ефект – по-рано заточване от необходимото и намаляване на общото количество на произведените детайли с щанцата.
Физически броят на изработените детайли до ремонт за разделителните и формоизменящите операции е свързан с два различни параметъра.
– При разделителните операции това е чепакът от износване на режещите ръбове, което настъпва значително по-рано от намаляване на размерите на матриците и поансоните, определящи точността.
– При формоизменящите операции, това е износването на работните повърини на матрици или поансони, което води до промяна на размерите на щанцования детайл, но поради по-голямата площ, натоварванията са по-ниски и процесът настъпва по-бавно от образуването на чепак. Най-вероятните проблеми при тях са попадане на прах или налепване на метал от заготовката по работните повърхини, вследствие на което смазвнето е недостатъчно и се появяват местни драскотини или откъртвания. Те влошават качеството на щанцованите детайли и трябва внимателно да се следи за тяхното възникване и навременно почистване.
Височината на чепака може да се използва като обективен критерий за изработените детайли до необходим ремонт на щанците за разделителни операции. Характерна особеност при тези инструментите е възможността за възстановяване нормалната работа чрез челно заточване на режещите матрици и поансони. От тази гледна точка, заточването на режещите щанци е планов ремонт. Тук обаче, също е възможно субективно определяне на допустимата височина на чепака, ако няма специални и обосновани изисквания, каквито се прилагат при листовете за ротори и статори на електродвигатели или ламели за трансформатори. Чепаците и изтънените остри ръбове от скъсване на материала са присъщи на разделителните процеси при заточени или затъпени режещи ръбове – разликата е във формата и големината. Следователно, дори с износени режещи ръбове щанците могат да произвеждат годни детайли, когато чепакът не от значение. На практика, това прави нееднозначна зависимостта между произведени детайли до ремонт („удари до ремонт“), определящи трайността до заточване, и височината на чепака. Напълно вероятно е една и съща щанца при определен чепак да бъде оцена както за годна, така и за негодна, според субективната оценка на наблюдателя за допустим чепак. Най-разпространеното мнение в практиката за допустимия чепак и нужда от заточване, е за стойност около 7% от дебелината на материала при стомана, но не повече от 0,15 mm (при дебелина над 2 mm). Ако анализираме тази стойност и я сравним с хлабината между матрица и поансон при рязане, ще се убедим, че съответства приблизително на максимално допустимата хлабина за мека стомана. Височината на чепака е право пропорционална на износването на поансона, показано на Фиг.14-6.
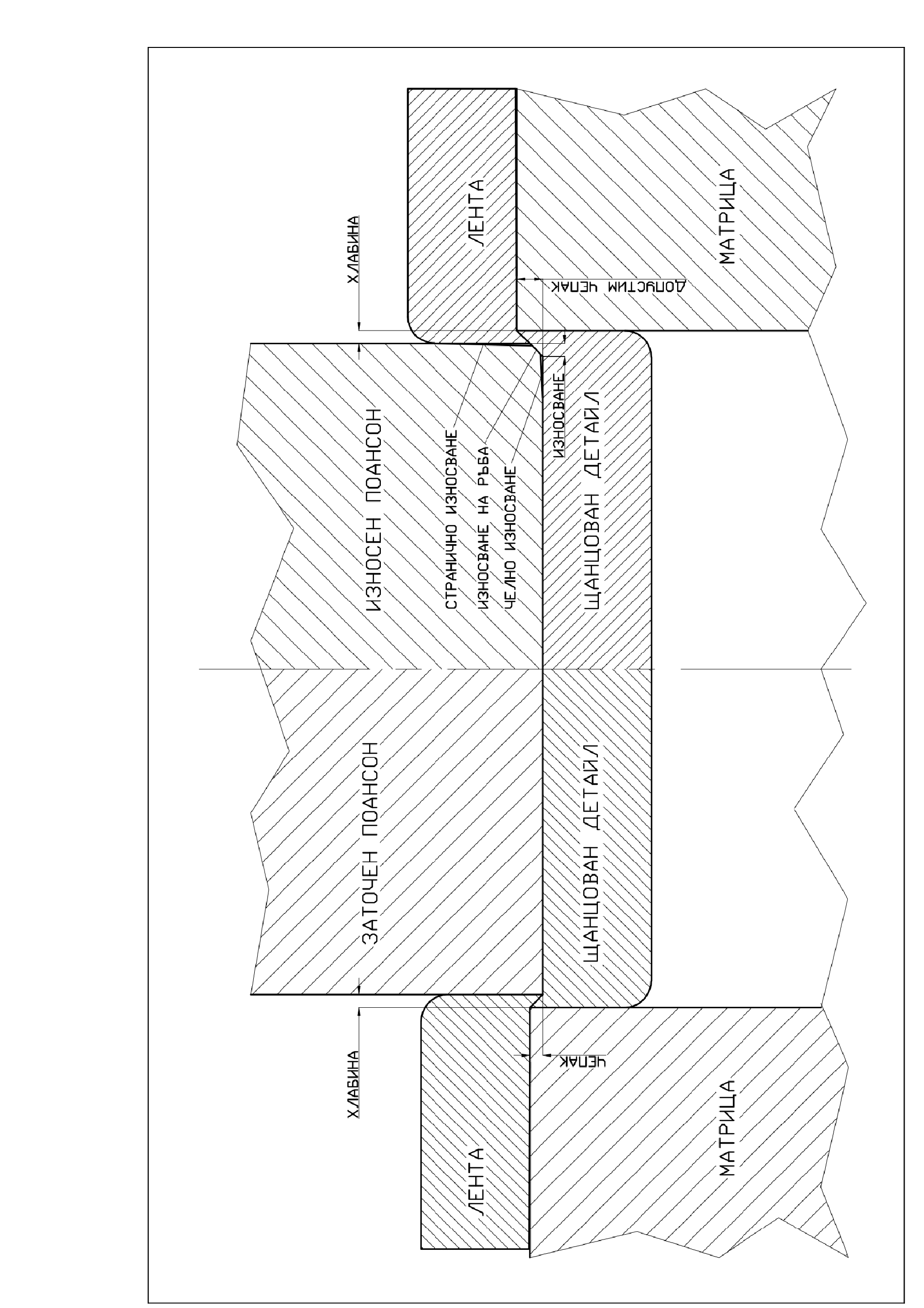
Фиг.14-6
От нея се вижда, че височината на чепака е приблизително сума на хлабината и износването на режещия ръб. Поансонът освен по режещия ръб се износва челно и странично. Колкото по-голямо е износването на ръба, толкова повече материал за чепака ще попада в тази част и ще предизвика по-големи натоварвания и странично износване. Имайки в предвид, че за една и съща дебелина, хлабината за различните материали не е еднаква,а в литературата [3], [4], [5] се посочва първа и втора оптимална хлабина, при определянето на допустима височина на чепака се препоръчва тя да е определящ фактор, вместо дебелината.
За практическо приложение може да се използва простото правило – допустимата височина на чепака е удвоената оптимална хлабина на щанцата. При нормална експлоатация, на основата на контролиране на допустимата височина на чепака и произведеното количество детайли, може обосновано да се посочи възможния брой на произведените детайли до планов ремонт – заточване на режещите ръбове на матриците и поансоните. Този брой отговаря на трайността на инструмента между заточване, която умножена с максималния брой възможни заточвания, определя общата трайност на щанцата до физическа амортизация и количеството произведени детайли през целия жизнен цикъл на инструмента. След произвеждането на това количество, щанцата се бракува и заменя с нова.
За приблизителна предварителна оценка на трайността на щанците с матрици и поансони от закалена до HRC 56-62 инструментална стомана Х12М, може да се използва таблицата от Фиг.14-7,
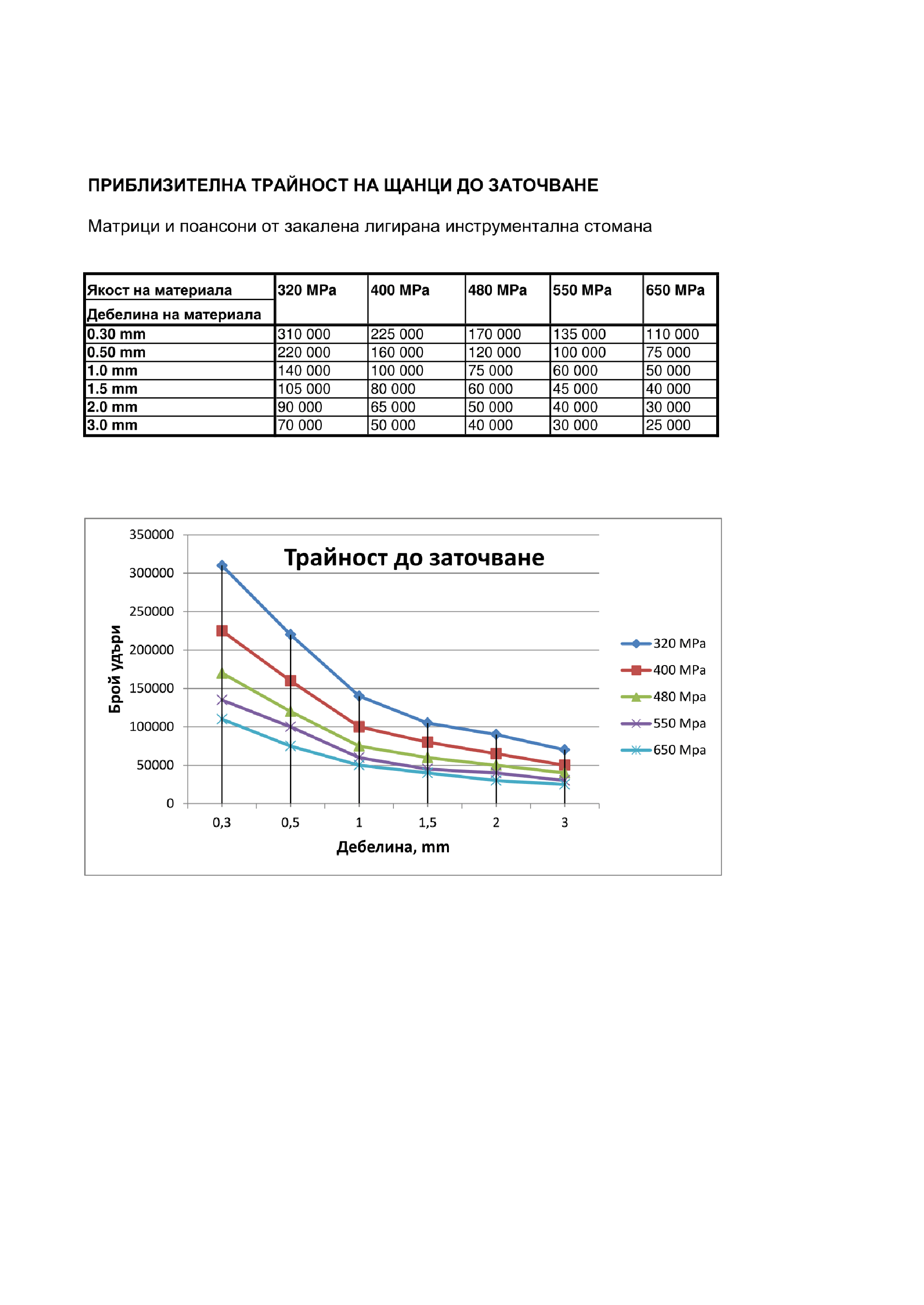
Фиг.14-7
построена по данни на [1]. Таблицата се отнася за щанцоване на стомана с прости по форма поансони и отчита влиянието само на два фактора – якостта на материала и неговата дебелина. Вижда се, че увеличението на якостта и дебелината на листа, водят до намаляване на броя на щанцованите детайли до ремонт (заточване), което е напълно логично. Двата фактора предизвикват увеличение на натоварването и свързаното с него износване. Тези стойности трябва да се използват много предпазливо, само като отправна точка за максимална трайност до заточване, защото не отчитат влиянието на относителната дебелина на детайла S/d и хлабината, които могат да доведат до 4 кратно нарастване на натоварването на режещите ръбове и намаляване на трайността, на качеството на изработка на режещите ръбове (грапавостта и твърдостта), на сложността на формата на контура и наличието на малки радиуси в ъглите, на равномерността на хлабината, наличието на смазващи вещества, на вида конструкция и използваната преса. За критерий е използван чепак с височина около 0,1- 0,15 mm. При малка дебелина до 0.5 mm, височина на чепака от 0,1 mm е голяма и табличните стойности може да са завишени. За другите видове щаннци могат да се посочат следните ориентировъчни количества щанцовани детайли до заточване:
– Твърдосплавни щанци с последователно действие за роторни и статорни листове от силициева ламарина 0,50 mm (на пример от Фиг.6-74, Фиг.6-75, Фиг.6-76, Фиг.6-77) с трайност до заточване от около 1 600 000 комплекта от двата детайла;
– Твърдосплавни щанци с последователно действие за „Е“ и „I“ пластини за трансформатор от силициева ламарина 0,50 mm (на пример от Фиг.6-73) с трайност до заточване от около 7 500 000 комплекта от двата детайла при подходящо смазване на лентата;
– Щанци със стоманени активни части за пробиване или изрязване на не метални детайли от пластмаси тип PP и PS с дебелина 0,3 – 0,8 mm (на пример от Фиг.6-79) с трайност до заточване от около 2 500 000 детайла.
3. Поддръжка и ремонт на инструменти за щанцоване.
Поддръжката на екипировката за щанцоване се състои от планови или аварийни ремонти. Плановите ремонти са заложени в паспортите под форма на трайност между заточване за режещите щанци или профилактичен ремонт (полиране) на активните части на огъващи, изтеглящи и формоващи щанци. Аварийните ремонти възникват непредвидено не само по активните части, но често по водещи втулки и колони, лентоводачи, буферни устройства.
Вероятността за авария по активните части е най-висока при поансони с малко напречно сечение с размер, близък до дебелината на материала и при твърдосплавни вложки и поансони, поради тяхната крехкост. Основния проблем на малките пробиващи поансони обикновено е задръстване на отвора, смачкване на поансона и излизането му от строя, а при твърдосплавните части преобладават местни откъртвания на участъци от режещите ръбове. По някога, аварийни ремонти възникват и при поансони с голямо напречно сечение, които са водят в притискача или водеща плоча. Техният проблем най-често е задиране в притискача и блокиране на движението на плочите. Ако не се вземат навреме мерки, може да се стигне до спукване на притискач и последващо откъртване на режещ ръб на матрица. В тези случаи вида на материала (стомана или твърда сплав) е без значение и вероятността за поява съществува и при двата вида материал. Разбира се, отстраняване на аварията при твърдосплавен поансон е много по-скъпо. При изтеглящите матрици и поансони най-често срещаните аварийни ситуации възникват поради вкарване на откъснати парчета материал от заготовката и задиране, последвано от заклинване на инструмента. Подобни случаи на заклинване се наблюдават и при силно натоварени огъващи поансони, но те обикновенно са закрепени с винтове, и следствието е тяхното скъсване. Най-честата причина за аварийна ситуация при огъващи, изтеглящи, отбортоващи, формоващи, калиброващи вложки и поансони, е по-голяма дебелина на материала, което довежда до спукване на вложката или поансона в зависимост от конструкцията. Затова, непрекъснатата проверка и измерване на дебелината на щанцования материал, е важно условие за без аварийната експлоатация на щанците.
Плановите ремонти обхващат следните дейности:
– Заточване на режещите ръбове – последователността и начина на заточване се уточняват в инструкцията за експлоатация. Важно изискване е, да се отнеме определена прибавка от челните повърхности на матрицата и поансоните, която е препоръчана в паспорта за нормални условия на работа (без аварийни износвания и откъртване). Ако такава стойност не е посочена, но е определена максимално допустима височина на чепак, при заточването може да се отнеме 1,5-2 пъти тази стойност. Обикновенно при твърдосплавните щанци се шлифова 0,05-0,08 mm, а при щанците от инструментална стомана от 0,05-0,3 mm в зависимост от дебелината на материала. В щанците конструктивно се оставя от 2 до 5 mm ресурс за заточване на матриците и от 3 до 8 mm ресурс за заточване на поансоните, следователно, колкото по-малко материал се отнема при заточване, толкова повече заточвания могат да се изпълнят и толкова по-висока обща трайност (жизнен цикъл) ще има инструмента. Опасността е, да не останат ръбовете частично заточени, защото тогава износването ще настъпи преждевременно;
– Заточване на компенсиращи елементи – в щанците най-често са въведени части, за които е предвидено шлифоване след всяко заточване. Типичен пример за такива части при щанците с последователно действие за разделителни и формоизменящи операции са формоващите вложки и поансони. Тяхната дължина е свързана с режещите части и тяхното заточване изисква нейното скъсяване. За удобство, в конструкцията на такива щанци са включени компенсиращи или дистанционни подложки, които се шлифоват и намаляват с големината на отнетата от режещите части прибавка. Понякога освен тях трябва да се шлифоват и различни упори и ограничители на хода. Изключително рядко, но все пак възможно, е изискване за шлифоване на противоположната страна на работната част от вложки или поансони;
– Полиране и почистване на формоващи (огъващи, изтеглящи, бортоващи) поансони – достатично е да се почистят и полират от налепване на материал от заготовките само работните профили. В случаи на използване на повърхностни покрития и твърди сплави е достатъчно само почистване;
– Почистване и проверка на всички центроващи части – това са ловители, фиксатори, ограничители, упори, лентоводачи, които влизат в контакт със заготовката. Вследствие на относителното движение между тях и заготовката, тези части също се износват и трябва периодично да се проверят техните размери, за да не се влоши точността на щанците. На пример, цилиндричен ловител от стомана HSS се износва с около 0,02 mm (колкото е заложената хлабина за центроване) след около 3 000 000 работни цикъла и трябва да се смени, защото намалява два пъти точността. Дори при твърдосплавни армиращи вложки на лентоводачите, след 8 000 000 работни цикъла е настъпило износване от движението на лентата от над 0,3 mm. Допустимото износване за частите трябва да се посочи в инструкцията за експлоатация;
– Проверка и почистване на воденето на щанците – отнася се за втулки, колонки, сепаратори и други водещи части. В зависимост от техния вид, начина на смазване, условията за експлоатация и натоварване, водещите колони и втулки с триене при плъзгане издържат от 1 000 000 до 10 000 000 работни цикъла, без да е необходима замяна. Правилно експлоатирани, водещите колони и втулки с триене при търкаляне издържат от 10 000 000 до 30 000 000 работни цикъла, без забележимо износване. Проверката на воденето с триене при плъзгане се извършва чрез измерване на диаметрите на отвора и колонката, и изчисляване на хлабината, която не трябва да превишава максимално допустимата. Тя също трябва да е посочена от производителя, но зависи главно от вида на щанцата и хлабината между матрицата и поансона (при огъване е много по-голяма от допустимата за рязане на тънък материал). Най-простата проверка при воденето с триене при търкаляне е сепараторите да не пропадат под собствената си тежест в монтирано положение. Последното подсказва за износване, защото принципно те се изработват с малка стегнатост. Новото сепараторно водене не позволява самостоятелно предвижване на сепараторите спрямо втулките и колоните без прилагане на значителна сила;
– Проверка на буферите в щанците – отнася се за всички пружини и други буферни елементи. Производителите залагат определен жизнен период, в зависимост от натоварванията и условията на работа. В повечето случаи, за винтови пружини по ISO 10243, той не надвишава 1 500 000 – 3 000 000 работни цикъла. При по-високо натоварване от препоръчваното или не добро водене, може да е дори под 100 000 цикъла. Проверката се състои в измерване на свободната дължина и визуален преглед за пукнатини на пружините и износване, смачкани или откъртени краища. Полиуретановите и гумени буфери имат значително по-ниска трайност. В редки случаи издържат до 500 000 работни цикъла, но това зависи главно от натоварването. Проверката им също се свежда до измерване на свободната височина. Нейното намаляване е свидетелство за умора и необходимост от смяна. Останалите видове буфери трябва да се проверяват според изискванията на производителя.
– Проверка на плочи и други части в щанците – отнася се за горни и долни плочи и проверката обхваща откриване и отстраняване на подбити и деформирани от удари зони и почистване на корозирали участъци. Необходимо е да се огледат и други части от инструмента и при откриване на нередности, те да се отстранят.
Изискването за професионална поддръжката на щанците е да се прилагат оригинални резервни части, изработени и доставени от производителя. В практиката обаче, това изискване рядко се изпълнява. Всеки потребител изработва някакви резервни части под предлог, че са спешно необходими, които използва в инструмента, но те рядко отговарят на всички изисквания към тях. По такъв начин се скъсява жизнения цикъл на щанците. Оптималния вариант е такива части (изключение са аварийните ремонти) да се поръчват заедно с новия инструмент при неговата изработка. Така те ще се напасват и пробват от производителя и ще се гарантира тяхната трайност и тази на щанцата като цяло.
ПРИЛОЖЕНИЕ 1. СПИСЪК НА ПРОЕКТИРАНИ И ВНЕДРЕНИ ИНСТРУМЕНТАЛНИ ЕКИПИРОВКИ ЗА ЩАНЦОВАНЕ, СРЕД КОИТО СА ИЗБРАНИ ИЗПОЛЗВАНИТЕ ПРИМЕРИ
- “Проектиране и изработка на Автоматична технологична линия за монтаж и щанцоване на съединители тип ЕВРОКАРД” - гнезда, внедрена в “ЗСЕМЕ София” - ръководител на проект, автор на идеен проект и технологични модули Преси и Щанци.
- “Проектиране и изработка на заварочна глава за многосупортен настроеваем пресавтомат МПА-1П”, внедрена в “ТИКЕ Пловдив” - ръководител на проект и автор.
- “Проектиране и изработка на технологична екипировка за щанцоване на детайл КЛИПС за нуждите на АВТОЕЛЕКТРОНИКА Пловдив на многосупортен настроеваем пресавтомат МПА-1П”, внедрена в “ТИКЕ Пловдив” – режеща щанца, огъващ център, гърбично задвижване, контролиращ датчик, комплект водачи - ръководител на проект и автор.
- “Проектиране и изработка на инструментална екипировка за щанцоване на КАПАЧКА тип ТУИСТ-ОФ”, дог.Е18/93 за “ПРИСОЕ” - съавтор.
- “Проектиране и изработка на инструментална екипировка за щанцоване на детайли за домакински електроуреди - РЕНДЕТА - 10 щанци”, дог.Е20/93 за “ОЛИМЕКС Пловдив” - ръководител на проект и автор.
- “Проектиране и изработка на инструментална екипировка за щанцоване на детайли за ТЯЛО и СТРАНИЦА - 3 щанци”, дог.Е21/93 за “ОЛИМЕКС Пловдив” - ръководител на проект и автор.
- “Проектиране и изработка на твърдосплавна щанца за детайл ЛОСТ за контактор”, дог.Е26/93 за “ЕАЗ Перущица” - ръководител на проект и съавтор.
- “Проектиране и изработка на технологична екипировка за щанцоване на детайли за домакински електроуреди - НОЖОВЕ и БЪРКАЛКИ - 7 щанци”, дог.Е27/93 за “ОЛИМЕКС Пловдив” - ръководител на проект, автор и съавтор.
- “Проектиране и изработка на технологична екипировка за щанцоване на детайли за сешоар - КОНТАКТИ, ЛАМЕЛИ, ПРУЖИНА - 17 щанци”, дог.Е28/93 за “ОЛИМЕКС Пловдив” - ръководител на проект, автор и съавтор.
- “Проектиране и изработка на технологична екипировка за щанцоване на детайл за домакински електроуреди - ПАНЕЛ - 3 щанци”, дог.Е29/93 за “ОЛИМЕКС Пловдив” - ръководител на проект, автор.
- “Проектиране и изработка на технологична екипировка за щанцоване на детайли КОНТАКТНИ ПЛАСТИНИ - 12 щанци”, дог.Е36/93 за “КРАСКО - КО СОФИЯ” - ръководител на проект и автор.
- “Проектиране и изработка на технологична екипировка за щанцоване на детайли за превключвател - КОНТАКТИ и ПЛАТКИ - 5 щанци”, дог.И2/94 за “ОЛИМЕКС Пловдив” - ръководител на проект, автор и съавтор.
- “Проектиране и изработка на технологична екипировка за щанцоване на детайли - КАБЕЛНИ НАКРАЙНИЦИ - 4 щанци”, дог.И4/94 за “ОЛИМЕКС Пловдив” - ръководител на проект и автор.
- “Проектиране и изработка на технологична екипировка за щанцоване на комплект детайли - КЛЮЧАЛКА ЗА БРАВА - 7 щанци”, дог.И6/94 за “КОДКИ София” - ръководител на проект и автор.
- “Проектиране и изработка на твърдосплавни щанци за детайли РОТОРНА И СТАТОРНА ПЛАСТИНИ за елдвигател: №23.111.0021 и №23.111.0023 - 2 щанци “, дог.И25/94 за “СЕНУР Турция” - ръководител на проект и автор.
- “Проектиране и изработка на технологична екипировка за щанцоване на комплект детайли - ЕЛЕКТРОННА ВЕЗНА - 7 щанци”, дог.И35/94 за “ОЛИМЕКС Пловдив” - ръководител на проект, автор и съавтор.
- “Проектиране и изработка на технологична екипировка за щанцоване на комплект детайли - ФЛАННЦИ ЗА ЕЛЕКТРОУРЕДИ - 4 щанци”, дог.И36/94 за “МИКРОАК Ботевград” - ръководител на проект и автор.
- “Проектиране и изработка на технологична екипировка за щанцоване на комплект детайли за домакински електроуреди - РЕНДЕТА и КОНТАКТИ - 19 щанци”, дог.К4/95 за “СЕНУР Турция” - ръководител на проект, автор и съавтор.
- “Проектиране и изработка на технологична екипировка за щанцоване на комплект детайли за прахосмукачка - ТУРБИНА и КОРПУС - 12 щанци”, дог.К9/95 за “СЕНУР Турция”- ръководител на проект, автор и съавтор.
- “Проектиране и изработка на твърдосплавни щанци за РОТОРНА и СТАТОРНА ПЛАСТИНА 80Х80 мм и 70х62 мм за електромотор - 2 щанци”, дог.К10/95 за “СЕНУР Турция” - ръководител на проект и автор.
- “Проектиране и изработка на твърдосплавна щанца за РОТОРНА и СТАТОРНА ПЛАСТИНА за електромотор “, дог.К12/95 за “БАЛКАН МОТОР Турция” - ръководител на проект и съавтор.
- “Проектиране и изработка на твърдосплавна щанца за РОТОРНА и СТАТОРНА ПЛАСТИНА за електромотор на прахосмукачка “, дог.К14/95 за “СЕНУР Турция” - ръководител на проект и автор.
- “Проектиране и изработка на технологична екипировка за щанцоване на комплект детайли - КАПАЧКИ “В” и “Т”- 2 щанци”, дог.К19/95 за “КАРАС Гърция” - ръководител на проект и автор.
- “Проектиране и изработка на технологична екипировка за щанцоване на детайли - КАБЕЛНИ НАКРАЙНИЦИ - 4 щанци”, дог.К20/95 за “ЕЛЕКТРОСТАРТ Вършец” - ръководител на проект и съавтор.
- “Проектиране и изработка на технологична екипировка за щанцоване на комплект детайли за електроуреди - ТЯЛО, ФЛАНЕЦ, РЕНДЕ, ЧЕТКОДЪРЖТЕЛ и др. - 13 щанци”, дог.Л6/96 за “СЕНУР Турция” - ръководител на проект, автор и съавтор.
- “Проектиране и изработка на технологична екипировка за щанцоване на комплект детайли КОНТАКТИ - 4 щанци”, дог.Л12/96 за “СЕНУР Турция” - ръководител на проект, автор и съавтор.
- “Проектиране и изработка на технологична екипировка за щанцоване на детайл ПЕРКА - 1 щанца”, дог.Л14/96 за “СЕНУР Турция” - ръководител на проект и автор.
- “Проектиране и изработка на технологична екипировка за щанцованена комплект детайли за електроуреди - ТЯЛО, КОНТАКТИ и РЕНДЕТА - 12 щанци”, дог.Л17/96 за “СЕНУР Турция” - ръководител на проект, автор и съавтор.
- “Проектиране и изработка на твърдосплавна технологична екипировка за щанцоване на комплект детайли за електроуреди БЛЕНДЕР - 5 щанци”, дог.Л19/96 за “СЕНУР Турция” - ръководител на проект, автор и съавтор.
- “Проектиране и изработка на технологична екипировка за щанцоване на комплект детайли за ТУРБИНА от прахосмукачка - 3 щанци и приспособление за занитване”, дог.М3/97 за “СЕНУР Турция” - ръководител на проект и автор.
- “Проектиране и изработка на технологична екипировка за щанцоване на комплект детайли за МАКАРА от прахосмукачка - 6 щанци “, дог.М14/97 за “СЕНУР Турция” - ръководител на проект, автор и съавтор.
- “Проектиране и изработка на технологична екипировка за щанцоване на комплект детайли за ПРАХОСМУКАЧКА - 11 щанци “, дог.М15/97 за “СЕНУР Турция” - ръководител на проект, автор и съавтор.
- “Проектиране и изработка на инструментална екипировка за щанцоване на комплект детайли за електроуреди - РЕНДЕТА - 2 щанци “, дог.М18/97 за “СЕНУР Турция” - ръководител на проект и съавтор.
- “Проектиране и изработка на технологична екипировка за щанцоване на детайли за електроуреди ШАСИ, КОНТАКТИ, ТЕРМИНАЛ - 6 щанци “, дог.М30/97 за “СЕНУР Турция” - ръководител на проект и автор.
- “Проектиране и изработка на технологична екипировка за щанцоване на детайл за електромотор - КОНЗОЛА ЗА ЛАГЕР на многопозиционна преса AIDA 250 тона - 12 щанци, 4 хващача и носеща конструкция “, дог.С4/98 за “СЕНУР Турция” - ръководител на проект и автор.
- “Проектиране и изработка на технологична екипировка за щанцоване на детайл „КОНТАКТ ЗА КАБЕЛ” за многосупортен пренастроевам гърбичен пресов автомат - режеща щанца, огъващ център, централен поансон, гърбично задвижване, гъбично-лостов подщанцови задвижващ модул, комплект лентоводачи “, дог. за “БЕТА МАКИНА Турция”, изпълнен в “БЕТА МАКИНА Турция” - автор.
- “Проектиране и изработка на технологична екипировка за щанцованена детайл ДИСК ПРОФИЛЕН №133-01-03-03 за турбина на прахосмукачка – 1 щанца №23.117.0078.00А”, договор с “Senur” Турция - автор.
- “Проектиране и изработка на технологиченпроцес за изтегляне и екипировка за на детайли EMBASEBRUTE, CUVE, COLLERETTE за автомобилен филтър - 7 щанци №.0037, №0038, №0039, №0040, №0040А, №0041, №0042”, договор пор. 0037, 0038, 0039, 0040, 0040А, 0041, 0042 с “Sinfa” Мароко - ръководител на проект и автор.
- “Проектиране и изработка на технологична екипировка за щанцованена детайл ДИСК РАВНИНЕН №133-01-03-02, ДИСК ПРОФИЛЕН №133-01-03-01, ЛАМЕЛА №133-01-03-03 за турбина на прахосмукачка – 3 щанци №0044, №0045, №0046 и приспособление за занитване на турбината, договор пор. 0044, 0045, 0046 с “Senur” Турция - ръководител на проект, автор и съавтор.
- “Проектиране и изработка на технологична екипировка за щанцоване на детайл ЧЕТКОДЪРЖАЧ №133-01-04-02 за електродвигател – 1 щанца №0047, договор пор. 0047 с “Senur” Турция - ръководител на проект, съавтор.
- “Проектиране и изработка на технологична екипировка за щанцованена детайл ПЕРКА №133-01-00-10 за електродвигател – 2 щанци №0048, №0049, договор пор. 0048 и 0049 с “Senur” Турция - ръководител на проект, автор и съавтор.
- “Проектиране на технологичен процес за изтегляне на многопозиционна преса AIDA 250 тона и изработка на инструментална екипировка за щанцоване на детайл - ФЛАНЕЦ ДОЛЕН №133-01-00-02 за електродвигател - 8 щанци, 4 хващача, 3 улея, буферни фланци и носеща конструкция №117С.00.00 “, договор пор. 0077 до 0086 с “Senur” Турция - ръководител на проект и автор.
- “Проектиране на технологичен процес за изтегляне на многопозиционна преса AIDA 250 тона и изработка на инструментална екипировка за щанцоване на детайл - КОРПУС ГОРЕН №133-01-00-01 за електродвигател - 9 щанци, 4 хващача, 3 улея, буферни фланци, 3 комплекта буферни устройства и носеща конструкция №117В.00.00 “, договор пор. 0067 до 0076 с “Senur” Турция - ръководител на проект и автор.
- “Проектиране и изработка на технологична екипировка за щанцоване (пробиване) на детайл КОРПУС ГОРЕН №133-01-00-01 за електродвигател – 3 щанци №0087, №0088, №0089, договор пор. 0087, 0088, 0089 с “Senur” Турция - ръководител на проект, автор и съавтор.
- “Проектиране и изработка на технологична екипировка за щанцоване на детайли MOTOR ARKA AYAK №300-94-05 и MOTOR ON AYAK №300-94-06 за електродвигател – 2 щанци №0101, №0102, договор пор. 0101, 0102 с “Balkanmotor” Турция - ръководител на проект, автор и съавтор.
- “Проектиране и изработка на твърдосплавна щанца за детайли ROTOR SACI №TR.P.02.024 и STATOR SACI №TR.P.02.025 за електродвигател - 1 щанца №0105”, договор пор. 0105 с “Balkanmotor” Турция - ръководител на проект и автор.
- “Проектиране и изработка на технологична екипировка за щанцоване на детайл MOTOR AYAK №FR.32.05.06 за електродвигател – 1 щанца №0169”, договор пор. 0169 с “Balkanmotor” Турция - ръководител на проект и съавтор.
- “Проектиране и изработка на твърдосплавна щанца за детайл CARCASSE №908413AE за автоматичен електропрекъсвач - 1 щанца №0170”, договор пор. 0170 с “Шнайдер-Електрик - България” - ръководител на проект, автор.
- “Проектиране и изработка на технологична екипировка за щанцованена детайл ШАСИ №HR126-00-00-04 за топъл робот – 5 щанци №0188, №0189, №0190,№0191, №0192”, договор пор. 0188, 0189, 0190, 0191, 0192 с “Senur” Турция - ръководител на проект, автор.
- “Проектиране и изработка на технологична екипировка за щанцоване(пробиване) на детайли ГОЛЯМ СЪД №HR126-00-00-22 и МАЛЪК СЪД №HR126-05-00-05 за топъл робот – 4 щанци №0193, №0194, №0195, №0196”, договор пор. 0193, 0194, 0195, 0196 с “Senur” Турция - ръководител на проект, автор и съавтор.
- “Проектиране и изработка на технологична екипировка за щанцоване на детайл КОНТАКТ №HR126-04-00-06 за топъл робот – 1 щанца №0197”, договор пор. 0197 с “Senur” Турция - ръководител на проект, автор.
- “Проектиране и изработка на двуредна твърдосплавна щанца за детайли ЛИСТ КОТВЕН №113274 и ЛИСТ СТАТОРЕН №112984 за електродвигател - 1 щанца №0204”, договор пор. 0204 със “СПАРКИ ЕЛТОС -АД” Ловеч - ръководител на проект, автор.
- “Проектиране и изработка на технологична екипировка за щанцованена детайл КРАК за електродвигател за топъл робот – 2 щанци №0208, №0209”, договор пор. 0208 и 0209 с “Senur” Турция - ръководител на проект, автор.
- “Проектиране и изработка на твърдосплавна щанца за детайл CONTACT HOLDER №908276BE за автоматичен електропрекъсвач - 1 щанца №0242”, договор пор. 0242 с “Шнайдер-Електрик - България” /Перущица/ - ръководител на проект, автор.
- “Проектиране на технологичен процес за изтегляне и изработка на инструментална екипировка за щанцоване на детайл КУПА №HR126-05-00-06 за топъл робот – 9 щанци №0263, №264, №0265, №0266, №0267, №268, №0269, №0270, №0271 и комплектовка за хидравлична преса (маси, закрепващи части, буферно устройство)”, договор пор. 0263, 0264, 0265, 0266, 0267, 268, 0269, 0270, 0271 с “Senur” Турция - ръководител на проект, автор.
- “Проектиране и изработка на технологична екипировка за щанцоване на детайли MOTOR ARKA AYAK, MOTOR ON AYAK и YATAK BASKI YAYI за електродвигател – 3 щанци №0287, №0288, №0289”, договор пор. 0287, 0288, 0289 с “Balkanmotor” Турция - ръководител на проект, автор и съавтор.
- “Проектиране и изработка на технологична екипировка за щанцованена детайл MOLLA (ПРУЖИНА) за електроизолциони фланци – 1 щанца №0297”, договор пор. 0297 с “АБИ “ (POWER) Италия - ръководител на проект, автор.
- “Проектиране и изработка на технологична екипировка за щанцоване на детайли MOTOR ARKA AYAK, MOTOR ON AYAK за електродвигател – 2 щанци №0319, №0318 “, договор пор. 0319 и 0318 с “Balkanmotor” Турция - ръководител на проект, съавтор.
- “Проектиране и изработка на едноредна твърдосплавна щанца за детайли ЛИСТ КОТВЕН №152527 и ЛИСТ СТАТОРЕН №152528 за електродвигател - 1 щанца №0335”, договор пор. 0335 със “СПАРКИ ЕЛТОС -АД” Ловеч - ръководител на проект и автор.
- “Проектиране и изработка на едноредна твърдосплавна щанца за детайли ЛИСТ КОТВЕН №100335 и ЛИСТ СТАТОРЕН №152714 за електродвигател - 1 щанца №0349”, договор пор. 0349 със “СПАРКИ ЕЛТОС -АД” Ловеч - ръководител на проект и автор.
- “Проектиране и изработка на технологична екипировка за щанцоване на ПРУЖИНА за електроизолционни фланци – 1 щанца №0376”, договор пор. 0376 с “ POWER “ Италия - ръководител на проект и съавтор.
- “Проектиране и изработка на твърдосплавна щанца за детайл MOVING CONTACT №908258AH за автоматичен електропрекъсвач - 1 щанца №0398”, договор пор. 0398 с “Шнайдер-Електрик - България” - ръководител на проект и автор.
- “Изработка на двуредна твърдосплавна щанца за детайли Ш и І ЛАМЕЛА №Д9.301210.044 за дросел - 3 щанци №14 112.00354”, договори пор. 0400, Щ0448 / Щ0449 със “ЕЛЕКТРОСТАРТ-АД” Вършец - ръководител на проект, съавтор.
- “Адаптиране и изработка на щанца за детайл BILAME №1636537 за автоматичен електропрекъсвач - 1 щанца №1534526”, договор пор.0415 с “Шнайдер-Електрик “ - Dijon, Франция - ръководител на проект.
- “Проектиране и изработка на едноредна твърдосплавна щанца за детайли ROTOR SACI №TR.P.64А.013 и STATOR SACI №TR.P.64А.015 за електродвигател - 1 щанца №Щ0420”, договор с “Balkanmotor” Турция пор. ТЩ0420 - ръководител на проект и автор.
- “Проектиране и изработка на едноредна твърдосплавна щанца за детайли ЛИСТ РОТОРЕН №678067.05.01 и ЛИСТ СТАТОРЕН №678067.02.01 за електродвигател - 1 щанца №ТЩ0426”, договор със “ЕЛПРОМ ЕМС-АД” Тетевен - ръководител на проект и автор.
- “Адаптиране и изработка на щанца за детайл BILAME №1725551 за автоматичен електропрекъсвач - 1 щанца №1534621”, договор пор. Щ0477 с “Schneider-Electric” - Dijon, Франция - ръководител на проект.
- “Проектиране и изработка на твърдосплавни щанци за детайл SUPPORT PLATE №908410 и SHIELD PLATE №720358 за автоматичен електропрекъсвач - 2 щанци №M1001, №M1001 “, договор с “Шнайдер-Електрик - България” - ръководител на проект, съавтор.
- “Проектиране и изработка на твърдосплавна щанца за детайл AILETTE №1723564 – GVT4 за искрогасителна камера на автоматичен електропрекъсвач - 1 щанца “, договор пор. Щ0480 с “ Schneider-Electric “ - Dijon, Франция - ръководител на проект и автор.
- “Проектиране и изработка на твърдосплавна щанца за детайл FIBRE №1723565 – GVT4 за искрогасителна камера на автоматичен електропрекъсвач - 1 прототипна и 1 твърдосплавна щанца “, договор пор. Щ0481 с “ Schneider-Electric “ - Dijon, Франция - ръководител на проект и автор.
- “Проектиране и изработка на монтажна щанца за детайл BLOC AILETTE №1723563 – GVT4 за искрогасителна камера на автоматичен електропрекъсвач - 1 щанца “, договор пор. Щ0482 с “ Schneider-Electric “ - Dijon, Франция - ръководител на проект и автор.
- “Проектиране и изработка на щанца с последователно действие за детайл DEFLECTEUR №1723562 – GVT4 за искрогасителна камера на автоматичен електропрекъсвач - 1 щанца “, договор Щ0483 с “ Schneider-Electric” - Dijon, Франция - ръководител на проект и автор.
- “Проектиране и изработка на едноредна твърдосплавна щанца за детайли ROTOR SACI №R.A.L.98.150/ №120-01-01-04 и STATOR SACI №R.M.L.98.075 за електродвигател на прахосмукачка - 1 щанца №ТЩ0540”, договор с “Senur Motorlari San ve TIC. AS” Турция “ пор.ТЩ0540 - ръководител на проект и автор.
- “Проектиране и изработка на протитипна щанца за детайл РОТОР -24 КАНАЛА за електродвигател - 1 щанца № Щ0541”, договор с “Senur Motorlari San ve TIC. AS” Турция “ пор. Щ0541 – ръководител на проект и автор.
- “Корегиране, проектиране и изработка на щанца с последователно действие за детайл „ПАНТА” №0097” и щанца за калиброване, поръчка от “АРП – ООД” Пловдив пор. Щ0093 - ръководител на проект и автор.
- “Адаптиране и изработка на щанца за детайл ‘BILAME CLIO RELAIS T3 №1725758 за автоматичен електропрекъсвач - 1 щанца №1534638”, договор Щ0566 с “ Schneider-Electric “ - Dijon, Франция пор. Щ0566 - ръководител на проект.
- “Проектиране и изработка на прототипна екипировка за детайл ‘CLIQUET -GVT4 №1723567 за искрогасителна камера на автоматичен електропрекъсвач” и производство на 100 прототипа, договор с “ Schneider-Electric “ - Dijon, Франция пор. П0483 - ръководител на проект и автор.
- “Проектиране и изработка на прототипна екипировка за детайл ‘VERROU -GVT4 №1723566 за искрогасителна камера на автоматичен електропрекъсвач” и производство на 100 прототипа, договор с “ Schneider-Electric” - Dijon, Франция пор. П0484 - ръководител на проект и автор.
- “Проектиране и изработка на двуредна твърдосплавна щанца за детайли Ш и І ЛАМЕЛА №Д9.301210.069 за дросел – 1+1 щанци №ТЩ0578”, договори с “ЕЛЕКТРОСТАРТ-АД” Вършец пор. ТЩ0578, пор.ТЩ0597 - ръководител на проект и автор.
- “Адаптиране, корегиране и изработка на комбинирана щанца за детайли „ОСНОВА” №Д9.301220.039 за дросел – 1 щанца №14 117 00389.”, договор с “ЕЛЕКТРОСТАРТ-АД” Вършец пор. Щ0579 - ръководител на проект, съавтор.
- “Проектиране и изработка на щанца с последователно действие за детайл ‘CLIQUET GVT4 №1723567 за искрогасителна камера на автоматичен електропрекъсвач” – 1 щанца №1534623, договор с “ Schneider-Electric” - Dijon, Франция, пор. 0290642 - ръководител на проект и автор.
- “Проектиране и изработка на щанца с последователно действие за детайл ‘VERROU -GVT4 №1723566 за искрогасителна камера на автоматичен електропрекъсвач”– 1 щанца №1534622, договор с “ Schneider-Electric” - Dijon, Франция, пор. 0290641 - ръководител на проект и автор.
- “Създаване на 3D модел, проектиране и изработка на щанца за изтегляне на детайл ‘КАПАК ЗА ЛЮК №:CAESpA003 за винарска промишленост” – 1 щанца №1534622, договор с “C.A.E. S.p. A.” - Торино, Италия, пор. 0290657 - ръководител на проект и автор.
- “Проектиране и изработка на щанца с последователно действие за детайл “VERROU - RELAIS TAILLE 3” №1725754” – 1 щанца №1534637, договор с “Schneider-Electric” - Франция, пор. 0290690 - ръководител на проект и автор.
- “Създаване 3D модел, проектиране и изработка на щанца с последователно действие, щанца за първо огъване и щанца за второ огъване на детайл “KONTAKT GEWISS – Крайна връзка” – 3 щанци, договор с “ЕХІМ” - Италия, пор. №0290671, № 0290672 и № 0290673, - водещ ръководител на проект и автор.
- “Създаване 3D модел, проектиране и изработка на щанца с последователно действие за детайл “KONTAKT GEWISS – Пружина плоска” – 1 щанца, договор с “ЕХІМ “ - Италия, пор. №0290666 - ръководител на проект иавтор.
- “Създаване 3D модел, проектиране и изработка на щанца с последователно действие, щанца за огъване на детайл “KONTAKT GEWISS – Централна неутрална връзка” – 2 щанци, договор с “ЕХІМ “ - Италия, пор. №0290667 и № 0290668 - ръководител на проект и съавтор.
- “Проектиране и изработка на щанца с последователно действие, за детайл “ПЛОСКА ПРУЖИНА” – 1 щанца, за ТИКЕ-ММ ЕООД във връзка с договор за серийно производство с “ПИРИНПЛАСТ” ООД – гр. Гоце Делчев, пор. №0290791 - ръководител на проект и автор.
- “Проектиране и изработка на РАЗМОТАВАЩО УСТРОЙСТВО за детайл “ПЛОСКА ПРУЖИНА “ – за ТИКЕ-ММ ЕООД във връзка с договор за серийно производство с “ПИРИНПЛАСТ” ООД – гр. Гоце Делчев, пор. №0290791 - ръководител на проект и автор.
- “Създаване 3D модел, проектиране и изработка на щанца с последователно действие за детайл “КЛИПС 1.12+0.8” – 1 щанца, договор с “ЕЛЕКТРОСТАРТ-АД” гр. Вършец, пор. №0290813 - ръководител на проект и автор.
- “Проектиране и изработка на УЛЕИ И ПАКЕТИРАЩО УСТРОЙСТВО ЗА ПРЕСА Schuler 80t за детайли “AILETTE №1723564 – GVT4 “ – за ТИКЕ-ММ ЕООД във връзка с договор за серийно производство на искрогасителна камера с “ Schneider-Electric” - Dijon, Франция”, вътрешна поръчка към пор. Щ0480 - ръководител на проект и автор.
- “Проектиране и изработка на щанца с последователно действие, за детайл “ВИНКЕЛ-PR” – 1 щанца, за ТИКЕ-ММ ЕООД във връзка с договор за серийно производство с “ПРОФИЛ” ООД – гр. Пловдив, пор. №11 1001 001 - ръководител на проект и автор.
- “Проектиране и изработка на щанца с последователно действие, за детайл “ЪГЪЛ № PR8215” – 1 щанца, за ТИКЕ-ММ ЕООД във връзка с договор за серийно производство с “ПРОФИЛ” ООД – гр. Пловдив, пор. №11 1004 001 - ръководител на проект и автор.
- “Проектиране и изработка на щанца с последователно действие за детайли “SHIELD BKP 4 №35008872”; “SHIELD BKP 6 №35008872”; “SHIELD BKP 8 №35008872”; “SHIELD BKP 12 №35008872” - 1 пренастроеваема щанца, договор с “ Schneider-Electric “ – Sophie-Antipolis, Франция, пор. 11 1221 017 - ръководител на проект и автор.
- “Проектиране и изработка на щанци за огъване и пробеване на детайли “SHIELD BKP 4 №35008872”; “SHIELD BKP 6 №35008872”; “SHIELD BKP 8 №35008872”; “SHIELD BKP 12 №35008872” - 4 двупозиционни щанци, договор с “ Schneider-Electric “ – Sophie-Antipolis, Франция, пор. 11 1222 017; 11 1223 017; 11 1224 017; 11 1225 017 - ръководител на проект и автор.
- “Проектиране и изработка на щанци за изрязване и пробеване със сменяеми поансони на „SHIELD CPU MB –CAN+ETH-CAN №35009663-Е50-000-04”; ” SHIELD CPU ETH MB №35009664-Е50-000-03”; ” SHIELD ETH (RST)+2 SL №35009665-Е50-000-03”; ” SHIELD ETH C30 (NOE) №35012284-Е50-000-02”; - 4 щанци, договор с “ Schneider-Electric “ – Sophie-Antipolis, Франция, пор. 11 1263 017; 11 1264 017; 11 1265017; 11 1266 017 - водещ проектa, автор и съавтор.
- “Проектиране и изработка на щанца за залепване на изолатори ”LEFT SHIELD INSULATOR №35010956-Е50-000-02”, ”RIGHT SHIELD INSULATOR №35010957-Е50-000-02” КЪМ „SHIELD CPU MB –CAN+ETH-CAN №35009663-Е50-000-04”; ” SHIELD CPU ETH MB №35009664-Е50-000-03”; ” SHIELD ETH (RST)+2 SL №35009665-Е50-000-03”; ” SHIELD ETH C30 (NOE) №35012284-Е50-000-02”; - 1 щанца, договор с “ Schneider-Electric “ – Sophie-Antipolis, Франция, пор. 11 1267 017 - ръководител на проект и автор.
- “Проектиране и изработка на щанца за формоване на страничен изпъкнал профил на ” SHIELD CPU MB –CAN+ETH-CAN №35009663-Е50-000-04”; ” SHIELD CPU ETH MB №35009664-Е50-000-03”; ” SHIELD ETH C30 (NOE) №35012284-Е50-000-02” и отбортоване на последния - 1 щанца, договор с “ Schneider-Electric “ – Sophie-Antipolis, Франция, пор. 11 1268 017 - ръководител на проект и автор.
- “Проектиране и изработка на щанци за огъване със сменяеми поансони на “ASSY SHIELD CPU ETH-MB №35011174-Е53-000- 02 ”; “ ASSY SHIELD CPU NOE №35012285-Е53-000- 01”; “ASSY SHIELD CPU DUAL SERIAL №35011176-Е53-000- 02 ”; ” ASSY SHIELD CPU MB –CAN+ETH-CAN №35012325-Е53-000- 02 - 4 щанци, договор с “ Schneider-Electric “ – Sophie-Antipolis, Франция, пор. 11 1269 017; 11 1270 017; 11 1271017; 11 1272 017 - ръководител на проект и съавтор.
- “Проектиране и изработка на щанца с последователно действие за отрязване на “ CAN PLATE SUBD №35012324-Е50-000- 02” - 1 щанца, договор с “ Schneider-Electric “ – Sophie-Antipolis, Франция, пор. 11 1273 017 - ръководител на проект и автор.
- “Проектиране и изработка приспособление за електросъпротивително заваряване на “ CAN SHIELD ASSЕМBLY №35012325-Е53-000- 02” - 1 брой, договор с “ Schneider-Electric “ – Sophie-Antipolis, Франция, пор. 11 1273 017 - ръководител на проект и автор.
- “Проектиране и изработка на щанца с последователно действие за отрязване на “ SHIELD FOR ANALOG MODULE №35009841-Е50-000- 03” - 1 щанца, договор с “ Schneider-Electric “ – Sophie-Antipolis, Франция, пор. 11 1282 017 - ръководител на проект и автор.
- “Проектиране и изработка на щанца за залепване на изолатори ”LEFT BASIC SHIELD INSULATOR №35011370-Е50-000-02”, ”RIGHT BASIC SHIELD INSULATOR №35011371-Е50-000-02” КЪМ „ASSY SECOND PCB SHIELD I / O №35011376-Е53-000-02”; „ASSY FIRST PCB SHIELD I / O №35011375-Е53-000-02”- 1 щанца, договор с “ Schneider-Electric “ – Sophie-Antipolis, Франция, пор. 11 1283 017 - ръководител на проект и автор.
- “Проектиране и изработка на ПРИСПОСОБЛЕНИЕ ЗА ОТРЯЗВАНЕ И ПАКЕТИРАНЕ на детайл “ЛЪЖИЦА МАЛКА 24 гнезда “ – за договор с “ПИРИНПЛАСТ” ООД – гр. Гоце Делчев, пор. №11 1293 003 -, ръководител на проект и автор.
- “Създаване 3D модел, проектиране и изработка на ПРЕСФОРМА ЗА ИЗДУВАНЕ НА САКСИЯ ЗА РАЗСАД -28 гн,(за автоматична потчна линия)” – за договор с “ДЖЕТТА” ООД – Тула, Русия, пор. №41 1331 023 - ръководител на проект.
- “Създаване 3D модел, проектиране и изработка на ЩАНЦА ЗА ПРОБИВАНЕ НА САКСИЯ ЗА РАЗСАД -28 гн,(7 гнездна за автоматична поточна линия)” – за договор с “ДЖЕТТА” ООД – Тула, Русия, пор. №11 1332 023 - ръководител на проект и автор.
- “Създаване 3D модел, проектиране и изработка на ЩАНЦА ЗА ОТРЯЗВАНЕ НА САКСИЯ ЗА РАЗСАД -28 гн,(7 гнездна за автоматична поточна линия)” – за договор с “ДЖЕТТА” ООД – Тула, Русия, пор. №11 1333 023 - ръководител на проект и автор.
- “Създаване 3D модел, проектиране и изработка на ПРЕСФОРМА ЗА ИЗДУВАНЕ НА КАСЕТА ЗА РАЗСАД -64 гн,(за автоматична потчна линия)” – за договор с “ДЖЕТТА” ООД – Тула, Русия, пор. №41 1334 023 - ръководител на проект.
- “Създаване 3D модел, проектиране и изработка на ЩАНЦА ЗА ПРОБИВАНЕ НА КАСЕТА ЗА РАЗСАД -64 гн,(16 гнездна за автоматична поточна линия)” – за договор с “ДЖЕТТА” ООД – Тула, Русия, пор. №11 1335 023 - ръководител на проект и автор.
- “Създаване 3D модел, проектиране и изработка на ЩАНЦА ЗА ОТРЯЗВАНЕ НА КАСЕТА ЗА РАЗСАД -64 гн,(1 гнездо за автоматична поточна линия)” – за договор с “ДЖЕТТА” ООД – Тула, Русия, пор. №11 1336 023 - ръководител на проект и автор.
- “Създаване 3D модел, проектиране и изработка на ПРЕСФОРМА ЗА ИЗДУВАНЕ НА КАСЕТА ЗА РАЗСАД -144 гн,(за автоматична потчна линия)” – за договор с “ДЖЕТТА” ООД – Тула, Русия, пор. №41 1337 023 - ръководител на проект
- “Създаване 3D модел, проектиране и изработка на ЩАНЦА ЗА ПРОБИВАНЕ НА КАСЕТА ЗА РАЗСАД -144 гн,(36 гнездна за автоматична поточна линия)” – за договор с “ДЖЕТТА” ООД – Тула, Русия, пор. №11 1338 023 - ръководител на проект и автор.
- “Създаване 3D модел, проектиране и изработка на ЩАНЦА ЗА ОТРЯЗВАНЕ НА КАСЕТА ЗА РАЗСАД -144 гн,(1 гнездо за автоматична поточна линия)” – за договор с “ДЖЕТТА” ООД – Тула, Русия, пор. №11 1339 023 - ръководител на проект и автор.
- “Създаване 3D модел, проектиране и изработка на щанцa с последователно действие (Операция 1-пробиване и формоване); щанца с последователно действие (Операция 2-огъване и отрязване след заваряване на сребърна пъпка) за детайл “KONTAKT Р1 – изделие INTERUTTORE “ – 2 щанци за автоматична линия за производство на контакти със заварени сребърни пъпки в Италия, договор с “ТIКЕ-MR “ Ltd - България, пор. №1241A и № 1241B - ръководител на проект и автор.
- “Създаване 3D модел, проектиране и изработка на щанцa с последователно действие (Операция 1-пробиване и формоване); щанца с последователно действие (Операция 2-огъване и отрязване след заваряване на сребърна пъпка) за детайл “KONTAKT Р2 – изделие INTERUTTORE “ – 2 щанци за автоматична линия за производство на контакти със заварени сребърни пъпки в Италия, договор с “ТIКЕ-MR “ Ltd - България, пор. №1242A и № 1242B -. ръководител на проект и автор.
- “Създаване 3D модел, проектиране и изработка на ПРЕСФОРМА ЗА ИЗДУВАНЕ НА КАСЕТА ЗА РАЗСАД -28 гн,(за автоматична потчна линия)” – за договор с “ДЖЕТТА” ООД – Тула, Русия, пор. №41 1470 023 - ръководител на проект.
- “Създаване 3D модел, проектиране и изработка на ЩАНЦА ЗА ПРОБИВАНЕ НА КАСЕТА ЗА РАЗСАД -28 гн, (14 гнездна за автоматична поточна линия)” – за договор с “ДЖЕТТА” ООД – Тула, Русия, пор. №11 1471023 - ръководител на проект и автор.
- “Създаване 3D модел, проектиране и изработка на ЩАНЦА ЗА ОТРЯЗВАНЕ НА КАСАТА ЗА РАЗСАД -28 гн, (1 гнездо за автоматична поточна линия)” – за договор с “ДЖЕТТА” ООД – Тула, Русия, пор. №11 1472023 - ръководител на проект и автор.
- “Създаване 3D модел, проектиране и изработка на ПРЕСФОРМА ЗА ИЗДУВАНЕ НА КАСЕТА ЗА РАЗСАД -6 гн, -2 реда по широчина на лентата (за автоматична потчна линия)” – за договор с “ДЖЕТТА” ООД – Тула, Русия, пор. №41 1473 023 - ръководител на проект.
- “Създаване 3D модел, проектиране и изработка на ЩАНЦА ЗА ПРОБИВАНЕ НА КАСЕТА ЗА РАЗСАД -6 гн, -2 реда по широчина на лентата (12 гнездна за автоматична поточна линия)” – за договор с “ДЖЕТТА” ООД – Тула, Русия, пор. №11 1474023 - ръководител на проект и автор.
- “Създаване 3D модел, проектиране и изработка на ЩАНЦА ЗА ОТРЯЗВАНЕ НА КАСЕТА ЗА РАЗСАД -6 гн, -2 реда по широчина на лентата (2 гнезда за автоматична поточна линия)” – за договор с “ДЖЕТТА” ООД – Тула, Русия, пор. №11 1475.023 - ръководител на проект и автор.
- “Проектиране и изработка на Блок с плочи за водене на вертикална преса за щанци за пробиване на КАСЕТИ от автоматична поточна линия” – за договор с “ДЖЕТТА” ООД – Тула, Русия, пор. №1482 - ръководител на проект и автор.
- “Проектиране и изработка на щанца с последователно действие за детайли „ЛАМЕЛА ГЛВН ЕІ 104”; №Д9.301210.124– 1 щанца №11. 1508.009 +1 щанца №11. 1492.009. за ЕІ-96 “, договор с “ЕЛЕКТРОСТАРТ-АД” Вършец пор. 1508 - ръководител на проект и автор.
- “Създаване 3D модел, проектиране и изработка на комбинирана щанца с последователно действие за детайли „ОСНОВА ГЛВН ЕІ 104”; №Д9.301220.045; №Д9.301220.046; №Д9.301220.047 за дросел – 1 пренастроеваема щанца №11. 1559.009.”, договор Q-3/2008 с “ЕЛЕКТРОСТАРТ-АД” Вършец пор. 1559 - ръководител на проект и автор.
- “Проектиране и изработка на щанца с последователно действие за детайли „FEDER ROEHRCHENADAPTER”;– 1 щанца №11. 1593.037 “, договор Q-5/2008 с “АРТ-КОЛЕНТА БЪЛГАРИЯ” –ЕООД, София пор. 1593 - ръководител на проект и автор.
- “Създаване 3D модел, проектиране и изработка на ЩАНЦА ЗА ПРОБИВАНЕ НА САКСИЯ ЗА РАЗСАД -28 гн,(14 гнездна за автоматична поточна линия)” – за договор с “ДЖЕТТА” ООД – Тула, Русия, пор. №111599 023 - ръководител на проект и автор.
- “Проектиране и изработка на щанци с последователно действие за детайли „КОНТАКТ №777426-080-PIN-MK-2A” и „КОНТАКТ №777426-080-PINS-3-6”; №11.1580.035 и №11. 1581.035– 2 щанци, договор Q-4/2008 с СД „ОКТО-7 Цолев и сие”, Ботевград, пор. 1580 и пор. 1581 - ръководител на проект и автор.
- “Проектиране и изработка на щанци с последователно действие за детайл „ГАЙКА – 63А” (STAMPO A TRANCIA PER MORSETTO 63A CON FILETTURA) и cъздаване 3D модел за „ГАЙКА – 63А; №11.1408.029, договор R-01/2007 с “ROSI-SNC” Italy, пор. 1408 - ръководител на проект и автор.
- “Създаване 3D модел, проектиране и изработка на инструментална екипировка за детайли „Скоба шарнилна ”; №SSH-001 за сушилка – 3 щанци: Щанца с последователно действие №11. 1669.040; щанца за предварително отъване №11. 1670.040; щанца за окончателно огъване №11. 16719.040 “, поръчка потвърждение №332/01.07.2009 с “ПАРМАШ-АД” гр. Сливен - пор.1669; пор. 1670; пор.1671 - ръководител на проект и автор.
- “Създаване технолотичен процес, проектиране и изработка на инструментална екипировка за детайли „ПРЕДПАЗИТЕЛ ф125” за ъглошлайф №178774 – 4 щанци: Щанца изрязваща №02816-00 (обща с Предпазител ф230); Щанца формоваща и изтеляща №02803-00; Щанца бортоваща №02804-00; .Щанца зарязваща 4 зъба №02805-00, дог. 2008-1/10.12.2008 -спецификация №2 с “СПАРКИ-ЕЛТОС АД” гр. Ловеч - пор.1724; пор. 1711; пор.1712; пор.1713 - ръководител на проект и автор.
- “Създаване технолотичен процес, проектиране и изработка на инструментална екипировка за детайли „ПРЕДПАЗИТЕЛ ф150” за ъглошлайф №178536 – 4 щанци: Щанца изрязваща №02808-00; Щанца формоваща и изтеляща №02809-00; Щанца бортоваща №02810-00; .Щанца зарязваща 4 зъба №02811-00, дог. 2008-1/10.12.2008 -спецификация №2 с “СПАРКИ-ЕЛТОС АД” гр. Ловеч - пор.1716; пор. 1717; пор.1718; пор.1719 - ръководител на проект и автор.
- “Създаване технолотичен процес, проектиране и изработка на инструментална екипировка за детайли „ПРЕДПАЗИТЕЛ ф180” за ъглошлайф №178751 – 4 щанци: Щанца изрязваща №02816-00 (обща с Предпазител ф230 –пробива отвор); Щанца формоваща и изтеляща №02814-00; Щанца бортоваща №02815-00; .Щанца зарязваща 4 зъба №02819-00 (обща с Предпазител ф230-сменяеми части), дог. 2008-1/10.12.2008 -спецификация №2 с “СПАРКИ-ЕЛТОС АД” гр. Ловеч - пор.1724; пор. 1722; пор.1723; пор.1727 - ръководител на проект и автор.
- “Създаване технолотичен процес, проектиране и изработка на инструментална екипировка за детайли „ПРЕДПАЗИТЕЛ ф230” за ъглошлайф №177352 – 4 щанци: Щанца изрязваща №02816-00; Щанца формоваща и изтеляща №02817-00; Щанца бортоваща №02818-00; .Щанца зарязваща 4 зъба №02819-00, дог. 2008-1/10.12.2008 -спецификация №2 с “СПАРКИ-ЕЛТОС АД” гр. Ловеч - пор.1724; пор. 1725; пор.1726; пор.1727 - ръководител на проект и автор.
- “Създаване технолотичен процес, проектиране и изработка на инструментална екипировка за детайли „ПРЕДПАЗИТЕЛ ф115” за ъглошлайф №176398 – 3 щанци: Щанца формоваща и изтеляща №02835-00; Щанца бортоваща №02836-00; .Щанца зарязваща 4 зъба №02837-00, дог. 2008-1/10.12.2008 -спецификация №3 с “СПАРКИ-ЕЛТОС АД” гр. Ловеч - пор. 1758; пор.1759; пор.1760 (заготовка излязана от лазер - ръководител на проект и автор.
- “Създаване технолотичен процес, проектиране и изработка на инструментална екипировка за детайли „ПРЕДПАЗИТЕЛ ф125 за отвор ф55” за ъглошлайф №156041– 4 щанци: Щанца изрязваща №02860-00; Щанца формоваща и изтеляща №02861-00; Щанца бортоваща №02862-00; .Щанца зарязваща 4 зъба №02863-00, дог. 2008-1/10.12.2008 -спецификация №4 с “СПАРКИ-ЕЛТОС АД” гр. Ловеч - пор.1765; пор. 1766; пор.1767; пор.1768 - ръководител на проект и автор.
- “Проектиране и изработка на щанца с посл. действие за детайли „ЛАМЕЛА ЗА ТРАНСФОРМАТОР”; №Д9.301210.126 – 1 щанца №11.1769.009 “, договор с “ЕЛЕКТРОСТАРТ-АД” Вършец пор. 1769 - ръководител на проект и автор.
- “Проектиране и изработка на щанца с посл. действие за детайли „ЛАМЕЛА ЗА ТРАНСФОРМАТОРИ - 32B”; №Д9.301210.126 – 1 щанца №11.1788.009”, договор с “ЕЛЕКТРОСТАРТ-АД” Вършец пор. 1788- ръководител на проект и автор.
- “Създаване технолотичен процес, проектиране и изработка на инструментална екипировка за детайли „ПРЕДПАЗИТЕЛ ф115/ ф125/ ф125- ф55/ ф150/ ф180/ ф230 ” за ъглошлайф – 3 щанци: Щанца калиброваща ф42,8-№02807-00; Щанца калиброваща №02813-00-ф55,2; Щанца калиброваща ф68,2 -№02820-00, дог. 2008-1/10.12.2008 -спецификация №3 с “СПАРКИ-ЕЛТОС АД” гр. Ловеч - пор. 1795; пор.1796; пор.1797 - ръководител на проект и автор.
- “Проектиране и изработка на двуредна твърдосплавна щанца за детайли Е І -32-В ЛАМЕЛА №Д9.301210.128 за трансформатор – 1 щанцa №11.1792.009.000”, договор S-02/2010г с “ЕЛЕКТРОСТАРТ-АД” Вършец пор. 1792, - ръководител на проект и автор.
- “Създаване 3D модел, проектиране и изработка на комбинирана щанца за детайли „ОСНОВА за трансформатор 50W-155 mm ” №Д9.301220.050; „ОСНОВА за трансформатор 50W-175 mm ” №Д9.301220.04; „ОСНОВА за трансформатор 105W-235 mm”; №Д9.301220.049; – 1 пренастроеваема щанца №11.1793.009.00, договор S-02/2010г с “ЕЛЕКТРОСТАРТ-АД” Вършец пор. 1793 - ръководител на проект и автор.
- “Проектиране и изработка на инструментална екипировка за детайли „ЧАША 13.5 ” №157334, „ЧАША 12 ” №157337, „УПЛЪТНЕНИЕ ФИЛЦЕВО 13.5 ” №157335, „УПЛЪТНЕНИЕ ФИЛЦЕВО 12 ” №157338 – 6 щанци: Щанца с последователно действие за Чаша 13.5 №02894-00; Щанца изтеляща Чаша 13.5 №02878-00; .Щанца за огъване на Уплътнение филц. 13.5 №02879-00, Щанца с последователно действие за Чаша 12 №02880-00; Щанца изтеляща Чаша 12 №02881-00; .Щанца за огъване на Уплътнение филц. 12 №02887-00 по дог. 2008-1/10.12.2008 -спецификация №5 с “СПАРКИ-ЕЛТОС АД” гр. Ловеч - пор.1834; пор. 1835; пор.1836; пор.1837; - пор.1838; пор.1839 ръководител на проект и автор.
- “Проектиране и изработка на инструментална екипировка за детайли „ПЛАНКА №157809”; „ПЛАНКА №157811”; „ПЛАНКА №157800”; - 3 щанци- Щанца с последователно действие за изрязване №02891-00; Щанца за огъване №02892-00; Щанца с последователно действие за изрязване №02893-00 по дог. 2008-1/10.12.2008 -спецификация №6 с “СПАРКИ-ЕЛТОС АД” гр. Ловеч - пор.1853; пор.1854; пор.1855 - автор.
- “Проектиране и изработка на инструментална екипировка за детайли „ВИЛКА ” №1132773 и „ГРЕБЕН” №132763; Щанца огъваща Вилка №02900-00; Щанца с последователно действие за ГРЕБЕН №02901-00 по дог. 2008-1/10.12.2008 -спецификация №6 с “СПАРКИ-ЕЛТОС АД” гр. Ловеч - пор.1863; пор. 1862; - автор.
- “Проектиране и изработка на щанци с посл. действие за детайл „INCISIVO” (16A); №11.1880.000, договор от 2011 с “ROSI-SNC” Italy, пор. 1880 - автор.
- “Създаване 3D модел, проектиране и изработка на ЩАНЦА ЗА ПРОБИВАНЕ НА КАСЕТА ЗА РАЗСАД -6 гн, №111904.023 -2 реда по широчина на лентата (12 гнездна за автоматична поточна линия)” – за договор с “ДЖЕТТА” ООД – Тула, Русия, пор. №1904 -автор.
- “Създаване 3D модел, проектиране и изработка на ЩАНЦА ЗА ОТРЯЗВАНЕ НА КАСЕТА ЗА РАЗСАД -6 гн №111905.023., -2 реда по широчина на лентата (2 гнезда за автоматична поточна линия)” – за договор с “ДЖЕТТА” ООД – Тула, Русия, пор. №1905 - автор.
- “Проектиране и изработка на инструментална екипировка за детайл „КУЛИСА №159021” чертеж №278479; Щанца за изрязване №02914-00; Щанца за огъване №02915-00 по дог. 2008-1/10.12.2008 -спецификация №6 с “СПАРКИ-ЕЛТОС АД” гр. Ловеч - пор.1923; пор. 1924; -автор.
- “Проектиране и изработка на инструментална екипировка за автомаатична преса за детайли „Пластина реверсатор 1 ” №107372, „Пластина реверсатор 2” №107373, „Пластина 2” №107387, „Пластина контактна ” №107349 – 4 щанци: Щанца с последователно действие за „Пластина реверсатор 1 ” №02921-00; Щанца с последователно действие за „Пластина реверсатор 2 ” №02922-00; Щанца с последователно действие за „Пластина 2 ” №02925-00, Щанца с последователно действие за „Пластина контактна” №02920-00 по дог. 2008-1/10.12.2008 -спецификация №7 с “СПАРКИ-ЕЛТОС АД” гр. Ловеч - пор.1930; пор. 1931; пор.1933; пор.1929; - ръководител на проект и автор.
- “Проектиране и изработка на инструментална екипировка за автомаатична преса за детайли „Пластина1 ” №107364, „Пластина 3” №107389, „Планка 1” №107409, „Планка 2 ” №107410 – 4 щанци: Щанца с последователно действие за „Пластина 1 ” №02924-00; Щанца с последователно действие за „Пластина 3” №02926-00; Щанца с последователно действие за „Планка 1 ” №02930-00, Щанца с последователно действие за „Планка 2” №02931-00 по дог. 2008-1/10.12.2008 -спецификация №7 с “СПАРКИ-ЕЛТОС АД” гр. Ловеч - пор.1932; пор. 1934; пор.1935; пор.1936; - ръководител на проект и съавтор .
- ” Проектиране и изработка на инструментална екипировка за детайл „ПЛАНКА №132813”;- 3 щанци- Щанца с последователно действие за изрязване №02942-00; Щанца за огъване №02943-00; Щанца за огъване №02944-00 по дог. 2008-1/10.12.2008 -спецификация №7 с “СПАРКИ-ЕЛТОС АД” гр. Ловеч - пор.1957; пор.1958; пор.1959, - автор.
- “Проектиране и изработка на инструментална екипировка за детайл „ВТУЛКА №12030-00-06” - 1 щанца - Щанца изтегляща с последователно действие №120030-00-06-00; по договор на „МЕТАЛПРЕС” ЕООД Пловдив и „КОМПАС-ИНЖЕНЕРИНГ” ООД гр. Асеновград с “БЪДЕЩНОСТ” АД гр. Черпан - автор.
ЗАБЕЛЕЖКА: Всички инструментални екипировки за щанцоване, с изключение на №36 и №151, са изработени и внедрени в “ТИКЕ-ММ” ЕООД, гр. Пловдив
ИЗПОЛЗВАНА ЛИТЕРАТУРА:
- Романовский В. П., „Справочник по холодной штамповке”, Ленинград, Машиностроение, 1979.
- Рудман Л. И., „Справочник коструктора штампов”, Москва, Машиностроение, 1988.
- Семенов Е. И., „Ковка и штамповка”, том 4, Листовая штамповка, Москва, Машиностроение, 1985.
- Фишеков Н. Д., “Щанци с твърдосплавни режещи части”, София, Техника, 1983.
- AIDA engineering Ltd, „Aida Press Handbook”, JAPAN, 1992.